Тема 1.2. Ультразвуковая сварка
СПЕЦИАЛЬНЫЕ МЕТОДЫ СВАРКИ
Конспект лекций
Введение
Сварка в настоящее время является одним из ведущих технологических процессов современного промышленного производства, от степени развития которого непосредственно зависит и уровень технологии, как в промышленности, так и во всех отраслях хозяйства страны. Сварка является, пожалуй, единственным способом создания высококачественных неразъёмных соединений. Сварка может подвергаться широкой механизации и автоматизации. Применение автоматов, полуавтоматов, и разнообразных специализированных машин позволяет существенно снизить долю ручного труда в сварочном производстве.
Требование развития сварочных процессов заставляет ускорять создание совершенных систем автоматического управления сварочным оборудованием с применением компьютерных технологий. Применение сложного современного компьютерного обеспечения в сварочном производстве требует значительного повышения инженерных и научных знаний у всего обслуживающего персонала.
Создание высокоэкономичных сварных конструкций из специальных металлов и сплавов невозможно без специально разработанных современных технологий и методов сварки. Применение редких металлов и сплавов и широкое освоение их как конструкционных материалов играет важнейшую роль в деле технического прогресса.
Таким образом, постоянно возникающие всё новые и новые задачи по совершенствованию технологий при применении новых материалов требуют модернизации существующих и создание новых более совершенных методов сварки. Следует добавить, что при изучении данной дисциплины нельзя ограничиться использованием только приведённой литературы, необходимо использовать другую литературу и журналы по сварочному производству.
|
|
Специальные методы сварки в твёрдой фазе
Раздел 1. Методы сварки механического класса
К методам сварки механического класса относятся такие методы (способы) сварки, в которых основным фактором, влияющим на создание неразъёмного соединения, является механический – внешнее силовое воздействие. Повышение температуры в месте соединения, является следствием сварочного процесса, а не привнесённым фактором. Обычное представление о процессе создания неразъёмного соединения связано с нагревом металла до высоких температур. Исследование природы металлических межатомных связей показали возможность использования этого механизма для соединения металлов в твёрдом состоянии.
Создание сварных соединений в твёрдом состоянии значительно расширяет область применения сварки. Позволяет соединять между собой разнородные металлы, металлы с неметаллическими материалами, пластмассы и тому подобное. Данный раздел включает в себя четыре темы, непосредственно относящиеся к сварке в твёрдой фазе: холодная сварка; ультразвуковая сварка; сварка взрывом; сварка трением.
|
|
Для закрепления теоретического материала в конце каждой темы представлены вопросы для самопроверки. Для творческого подхода к усвоению материала дисциплины студентам предлагаются тесты текущего контроля, представленные в конце УМК.
Тема 1.1. Холодная сварка
Тема «Холодная сварка» относится к разделу – сварка в твёрдой фазе. Для контроля качества усвоения изученного материала в конце данной темы предлагаются вопросы для самопроверки, а в виде текущего контроля тест №1 в блоке текущего контроля освоения дисциплины.
Холодная сварка, как метод создания неразъёмного соединения используется применительно к пластически деформируемым металлам (сплавам). В сварочной практике длительное время применяются процессы сварки с использованием высокотемпературных источников теплоты, при этом металл изделия в местах сварки доводится до плавления или тестообразного состояния. В последнее время показано, что металлы можно сваривать и при комнатных температурах без нагрева металла до высоких температур. Соединение металлов происходит в твердом состоянии вследствие образования металлических связей на свариваемых поверхностях при их совместном деформировании.
|
|
Для идеального случая процесс образования металлического соединения при холодной сварке можно представить следующим образом. Предположим, что имеются два куска металла с абсолютно гладкими и чистыми поверхностями. Так как металлы представляют собой конгломерат из положительно заряженных ионов и электродов, то взаимодействие между облаками электронов и ионами, находящимися в узлах кристаллической решетки, определяет монолитность и прочность кусков металла. При сближении двух металлических поверхностей происходит коллективизация электронов, вылетающих из поверхностей, в результате чего возникают силы взаимодействия между поверхностями, образуется общее электронное облако и, следовательно, единый агрегат. Из приведенных выше рассуждений следует, что при сближении идеально гладких и чистых поверхностей между ними самопроизвольно возникают межатомные силы взаимодействия, т. е. происходит образование прочного соединения.
|
|
Геометрия реальной металлической поверхности определяется ее волнистостью и шероховатостью. Геометрию поверхности можно представитьв виде двух кривых: кривой волны (рис. 1, а)и частотной кривой шероховатостей (рис. 1, б), которая накладывается на кривую волны.
Рис. 1. Профилограмма волнистой и шероховатой поверхности
После механической зачистки поверхности металла в атмосфере сухого воздуха на ней образуется окисная пленка.
Слой окислов сохраняет на границе с металлом отрицательный потенциал против положительного потенциала самого металла. Наружная поверхность слоя окислов имеет положительный потенциал и они адсорбируют кислород, имеющий отрицательный потенциал. Таким образом, поверхность металла (рис. 2) покрывается двумя двойными электрическими слоями. Окисные пленки обычно очень хрупкие и обладают высокой твердостью.
Рис. 2. Строение поверхности металла в воздушной атмосфере
А - глубинный слой металла, не затронутый пластическими деформациями;
Б - поверхностный слой полностью разориентированных кристаллитов
с прослойкам окислов;
В - окисный слой, характерная полярность внутренних и внешних границ, а также
полярность верхних слоев металла показана знаками «+» и «-»;
Г - адсорбированный слой кислородных анионов и нейтральных молекул воздуха;
Д - слой водяных молекул;
Е - слой жировых молекул;
Ж - ионизированные пылевые частицы
Образование прочного сварного соединения реальных металлов при сварке в твердой фазе совместным деформированием происходит в три условных этапа:
1) сближение свариваемых поверхностей;
2) возникновение металлического контакта;
3) создание прочного сварного соединения.
Первый этап определяет сближение свариваемых поверхностей, характеризуется деформацией как микрошероховатостей, так и волнистостей.
Второй этап начинается в процессе сближения и деформирования поверхностных слоев и неровностей. Этот этап характеризуется увеличением площади металлического контакта свариваемых поверхностей и возникновением общих кристаллов на них.
Третий этап характеризуется различного рода перемещениями на определенные расстояния относительно больших масс частиц вследствие диффузии, этот процесс требует значительного времени.Эти процессы имеют отношение к холодной и диффузионной сварке и к сварке трением.
Процесс сварки при действии импульсных давлений — сварка взрывом, электромагнитным импульсом, ультразвуковаябудет проходить в те же три этапа, однако отличия состоят в том, что отдельные этапы в этих методах сварки трудно различимы вследствие малого времени образования сварного соединения.
Для осуществления холодной сварки необходимо удалить со свариваемых поверхностей окислы и загрязнения и сблизить соединяемые поверхности на расстояние параметра кристаллической решетки. На практике создают значительные пластические деформации. Холодной сваркой можно получать соединения встык, внахлестку и в тавр. Перед сваркой, поверхности, подлежащие сварке, очищают от загрязнений обезжириванием, обработкой вращающейся проволочной щеткой, шабрением. При сварке встык проволок обрезают только торцы. Листы толщиной 0,2 - 15 мм сваривают внахлестку путем вдавливания в толщу металла с одной или с двух сторон пуансонов (рис. 3). Соединения выполняют в виде отдельных точек или непрерывного шва. Ширину или диаметр пуансона выбирают в зависимости от толщины δ свариваемого материала, r - (1÷З) δ.
Рис. 3. Схемы холодной сварки внахлестку:
а — вдавливанием, одного пуансона; б — вдавливанием двух пуансонов;
в — вдавливанием пуансонов с заплечиками;
г — вдавливанием пуансонов с предварительным зажатием изделия
Основной параметр, определяющий процесс холодной сварки, величина деформации металла в месте соединения, которая зависит от свойств металла, его толщины, типа соединения и способов подготовки поверхностей.
Степень, необходимой деформации при сварке разнородных металлов определяется свойствами того из свариваемых металлов, при сварке которого требуется меньшая деформация. Этим пользуются при сварке малопластичных металлов, применяя прокладки из пластичных металлов.
Герметичное шовное соединение может быть достигнуто вдавливанием пуансона по всей длине шва или путем прокатывания ролика (рис. 4).
Рис.4. Схема холодной шовной сварки с деформированием:
односторонним (а), двусторонним (б)
Прочность стыковых соединений обычно выше прочности основного металла. Это объясняется тем, что в местах соединения металл упрочняется вследствие наклепа.
Холодную сварку можно осуществлять путем сдавливания соединяемых изделий с одновременным их тангенциальным относительным смещением. Этот способ сварки получил название сварки сдвигом. При сварке сдвигом механизм образования сварного соединения иной.
При приложении тангенциальной силы начинается перемещение поверхностей в процессе чего окисные пленки и загрязнения сдираются и образуются отдельные мостики контакта. Тангенциальное смещение соединяемых изделий дает возможность получить сравнительно большие площади очищенных от пленок поверхностей при небольшом растекании каждой из них. Наличие тангенциальной силы уменьшает сопротивление металла пластическим деформациям и при данной нормальной силе позволяет получить большую площадь контакта. Это ведет к тому, что при точечной сварке сдвигом схватывание происходит при малых деформациях и усилиях
Достаточная площадь сцепления поверхностей, обработанная напильником, возникнет после сдвига на 5÷7 мм.
Вопросы для проверки
1. В чём существенное отличие холодной сварки от сварки плавлением?
2. Что представляет собой идеальная поверхность?
3. Как выглядит в реальности поверхность металла?
4. Какие этапы предполагаются для проведения холодной сварки?
5. Какими способами можно создать неразъёмное соединение в процессе холодной сварки?
6. Какие машины используются для проведения холодной сварки?
7. Какими преимуществами и недостатками обладает процесс холодной сварки?
Тема 1.2. Ультразвуковая сварка
Метод ультразвуковой сварки широко применяется в современной промышленности. Использование силового ультразвука в сварочном производстве вызвано возросшими требованиями к качеству соединений, скорости их выполнения, сохранению физико-химических свойств соединяемых материалов и т. п.
Изучение данной темы позволяет студенту – будущему инженеру изучить не только один из перспективных современных методов сварки, но и углубить свои знания в области материаловедения.
Вопросы для самопроверки, находящиеся в конце темы, позволяют закрепить полученные знания сразу по прочтении материала. В помощь освоения дисциплины предлагается тест №2 блока текущего контроля. По материалу данной темы необходимо выполнить лабораторную работу №1, показывающую возможности применения технического силового ультразвука в промышленности.
Ультразвук находит широкое применение в науке для исследования некоторых физических явлений и свойств веществ, В технике ультразвуковые колебания используют для обработки металлов и в дефектоскопии. В сварочной технике ультразвук может быть использован в различных целях. Воздействуя им на сварочную ванну в процессе кристаллизации, можно улучшить механические свойства сварного соединения благодаря измельчению структуры металла шва и удалению газов. Ультразвук может быть источником энергии для создания точечных и шовных соединений.
Ультразвуковые колебания активно разрушают естественные и искусственные пленки, это позволяет сваривать металлы с окисленной поверхностью, покрытые слоем лака и т. п. Ультразвук снижает или снимает собственные напряжения и деформации, возникающие при сварке. Им можно стабилизировать структурные составляющие металла сварного соединения, устраняя возможность самопроизвольного деформирования сварных конструкций со временем.
В качестве источника энергии при сварке металлов ультразвук еще не нашел широкого применения, хотя этот способ имеет ряд преимуществ и особенностей по сравнению с контактной и холодной сваркой. При сварке ультразвуком неразъемное соединение металлов образуется при совместном воздействии на детали механических колебаний высокой частоты и относительно небольших сдавливающих усилий. В принципе этот метод сварки имеет много общего с холодной сваркой сдвигом.
Для получения, механических колебаний высокой частоты обычно используется магнитострикционный эффект, состоящий в изменении размеров некоторых металлов и сплавов под действием переменного магнитного поля. Для ультразвуковых преобразователей обычно используют чистый никель или железо-кобальтовые сплавы. Изменения размеров магнитострикционных материалов очень малы: так, для никеля магнитострикционное удлинение составляет 40·10-6. Поэтому для увеличения амплитуды смещения и концентрации энергии колебаний, а также для передачи механических колебаний к месту сварки используют волноводы или концентраторы, которые в большинстве случаев имеют сужающуюся форму.
Эксперименты показывают, что для сварки металлов достаточно иметь волноводы с коэффициентом усиления около 5, при этом амплитуда на конце волновода при холостом ходе должна быть 20 - 30 мкм. Магнитострикционный преобразователь и волноводы должны быть рассчитаны и изготовлены на заданную частоту ультразвукового генератора.
Основной узел машины для выполнения точечных соединений с помощью ультразвука - магнитострикционный преобразователь (рис. 5), его обмотка питается током высокой частоты от ультразвукового генератора.
Рис. 5. Схема установки для точечной сварки ультразвуком.
1— магнитострикционный преобразователь; 2 —диафрагма;
3 — механизм нажатия; 4 — выступ; 5 — маятниковая опора;
6 — волновод; 7 — кожух водяного охлаждения; 8 — изделие
Охлаждаемый водой магнитострикционный преобразователь 7 изготовлен из пермендюра (К49Ф2), он служит для превращения энергии тока высокой частоты в механические колебания, которые передаются волноводу 6. На конце волновода имеется рабочий выступ 4. При сварке изделие 8 зажимают между рабочим выступом 4 и механизмом нажатия 3, к которому прикладывают усилие, необходимое для создания давления в процессе сварки.
Сварка происходит при включенном преобразователе. Высокочастотные упругие колебания передаются через волновод на рабочий выступ 4 в виде горизонтальных механических перемещений высокой частоты. Длительность процесса сварки зависит от свариваемого металла и его толщины, для малых толщин она исчисляется долями секунды.
Основные узлы машины для выполнения шовных соединений при помощи ультразвука (рис. 6): вращающийся магнитострикционный преобразователь 1 и волновод 2. Конец волновода имеет форму ролика 3. Изделие 5, подлежащее соединению, зажимают между вращающимся роликом 3 волновода и холостым роликом 4. Высокочастотные упругие колебания передаются через волновод на ролик, который вращается вместе с волноводом. Изделие, зажатое между роликами, перемещается, и одновременно создается герметичное соединение.
Рис. 6. Схема установки для роликовой сварки ультразвуком:
1— магнитострикционный преобразователь; 2 —волновод; 3 — сваривающий
ролик; 4 — прижимной ролик; 5 —.изделие; 6 — кожух преобразователя;
7 — подвод тока от ультразвукового генератора; .8 — привод;
9 — подвод охлаждающей воды
Имеющийся опыт сварки ультразвуком выявил следующие преимущества этого способа:
1. Сварка ультразвуком происходит в твердом состоянии без существенного нагрева места сварки, что позволяет соединять химически активные металлы или пары металлов, склонные образовывать хрупкие интерметаллические соединения в зоне сварки.
2. Возможны соединения тонких и ультратонких деталей, приварка тонких
листов и фольги к деталям большей толщины, сварка пакетов из фольги.
3. Снижены требования к чистоте свариваемых поверхностей, в связи, с чем возможна сварка плакированных и оксидированных поверхностей и вообще сварка металлических изделий, поверхности которых покрыты различными изоляционными пленками.
4. Небольшие сдавливающие усилия [10 - 250 кгс (98 - 2450 Н) ] вызывают незначительную деформацию поверхности деталей в месте их соединения (вмятина, как правило, не превышает 5 - 10%).
5. Применяется оборудование малой мощности и несложной конструкции (если, например, для контактной точечной сварки алюминия толщиной 1 мм необходима машина мощностью 100 - 150 кВА, то при сварке ультразвуком аналогичного соединения - всего 5 - 2,5 кВА).
Ультразвуковая сварка нашла достаточно широкое применение для соединения тонких деталей из однородных и разнородных материалов.
В дальнейшем можно ожидать, что этот метод будет использован при сварке металлов, образующих хрупкие интерметаллические соединения, для приварки тонких обшивок к несущей конструкции (в авиационной промышленности, автомобилестроении и ряде других отраслей промышленности).
Вопросы для проверки
1. Что такое ультразвуковые волны и каков их диапазон частот?
2. Что такое понятие магнитострикция?
3. Какие металлы относятся к магнитострикционным?
4. Какие ещё материалы обладают свойством магнитострикции?
5. С каким видом сварки можно сравнить ультразвуковую сварку?
6. Для сварки каких материалов применяется УЗС в промышленном производстве?
7. Где ещё, кроме сварки можно применить ультразвуковую технологию?
Тема 1.3. Сварка взрывом
В последнее время в технике все более широкое распространение находит процесс сварки с использованием энергии взрыва. Метод сварки взрывом применяется при сварке изделий из разнородных материалов, сварке труб, приварке отводов и других заготовок.
В помощь закрепления изучаемого материала предлагаются вопросы для самопроверки, а также тест №3 из блока текущего контроля освоения дисциплины. Для лучшего восприятия в тексте присутствуют рисунки графически представляющие процесс создания неразъёмного соединения. Необходимо заметить, что использование данного метода (способа) возможно только для пластически деформируемых материалов.
Схема сварки металлов взрывом представлена на рис. 7. На жесткое основание 5 (земляной грунт, дерево, металл и т. п.) устанавливают одну из свариваемых пластин 4. Вторую пластину 3 помещают над первой на расстоянии h от ее поверхности. На всю поверхность пластины 3 укладывают заряд 2 взрывчатого вещества (ВВ) слоем одинаковой толщины Н. Заряд взрывают при помощи детонатора /, находящегося в одном из концов или углов пластины 3. В качестве взрывчатого вещества используют гранулированные аммониты и гранулиты, имеющие плотность около 1,0 г/см3 и скорости детонации D порядка 3 - 4 тыс. метров в секунду. Заряды ВВ взрывают с помощью электродетонаторов. После инициирования заряда ВВ детонатором вдоль слоя ВВ распространяется плоская детонационная волна. Позади фронта детонационной волны образуются продукты взрыва, которые в течение очень короткого промежутка времени по инерции сохраняют прежний объем, находясь под давлением 100 - 200 тыс. атм., а затем со скоростью 0,5 - 0,75 D разлетаются в стороны по нормалям к свободным поверхностям заряда.
Рис. 7. Схема сварки взрывом плоских параллельно
расположенных элементов
При установившемся процессе сварки метаемая пластина на некоторой длине дважды перегибается и, если соединяемые поверхности перед сваркой были установлены параллельно друг другу, ее наклонный участок со скоростью vк, равной D, движется за фронтом детонационной волны, а участок на котором находится непродетонированная часть заряда ВВ, под действием сил инерции остается в исходном состоянии (рис. 8).
Рис. 8. Схема установившегося процесса соударения свариваемых пластин:
/ — фронт детонационной волны; 2 — фронт разлета продуктов взрыва ВВ; 3 — фронт волны разрежения; D — скорость детонации ВВ; v — скорость соударения пластин; vк — скорость перемещения «динамического угла встречи» соударяющихся пластин в направлении сварки; δ — толщина метаемой (верхней) пластины; δН — толщина неподвижной пластины; H — толщина слоя ВВ
При этом они сообщают находящемуся за фронтом детонации участку металла импульс, под действием которого его элементарные объемы последовательно с ускорением движутся к поверхности неподвижной части металла и со скоростью v соударяются с ней.
Соударение свариваемых металлов, происходящее под некоторым углом γ, вызывает давление в десятки тысяч атмосфер. В местах прикосновения пластин появляется тангенциальная составляющая скорости соударения в направлении движения фронта детонационной волны, вследствие этого происходит совместное деформирование поверхностных слоев свариваемых листов. Окисные пленки и другие поверхностные загрязнения дробятся и рассредоточиваются со слоями деформирующего металла аналогично явлению при холодной сварке и частично уносятся в виде тонкой пыли под действием кумулятивного эффекта.
При сварке металлов взрывом происходит образование металлических связей.
Особенности процесса сварки взрывом следующие:
1. Сварное соединение образуется в течение миллионных долей секунды, т. е. практически мгновенно. Сварное соединение возникает вследствие образования металлических связей при совместном пластическом деформировании свариваемых поверхностей металла. Малая продолжительность сварки предотвращает возникновение диффузионных процессов. Эта особенность процесса позволяет сваривать металлы, которые при обычных процессах сварки с расплавлением металлов образуют хрупкие интерметаллические соединения, делающими непригодными швы к эксплуатации.
2. Можно получать соединения неограниченной площади. При этом процесс сварки осуществляется тем легче, чем больше отношение площади соединения к толщине метаемой части металла. Осуществлены соединения площадью 15 - 20 м2.
На рис. 9, а - д представлены технологические схемы сварки взрывом:
а - сварка трех и многослойных плоских соединений одновременно одним зарядом ВВ; б - приварка двух наружных слоев к листу взрывом из одной точки двух зарядов ВВ; в - наружная облицовка цилиндрических тел кольцевым зарядом ВВ; г - сварка биметаллических цилиндрических заготовок переменного диаметра для изготовления из разнородных металлов бесступенчатых трубных переходников; д - приварка труб к трубным решеткам теплообменников.
Рис. 9. Технологические схемы сварки взрывом соединений различного типа:
1 - детонатор; 2 - заряд ВВ; 3 - метаемые пластины; 4 - неподвижная пластина;
5 - подложка; 6 - грунт; 7 - металлическая призма или конус для центрирования заготовок и направления фронта детонационной волны; 8 -облицовываемый
цилиндр; 9 -метаемая труба; I0 - центрирующая шайба; 11 - трубная решетка;
12 - трубка; 13 - буферная пластмассовая цилиндрическая вставка
Подготовка изделий под сварку.Заготовки не должны иметь значительного прогиба. Допускается прогиб не более 2—3 мм на 1 м длины. Поверхности свариваемых металлов должны быть зачищены до металлического блеска, для титана и сталей аустенитного класса допускается травление свариваемых поверхностей.
Непосредственно перед сваркой соединяемые поверхности обезжиривают, так как наличие следов масел препятствует образованию сварного соединения. Зазоры между плоскими свариваемыми заготовками устанавливаются с помощью проволочных штырей, для цилиндрических заготовок используются специально выточенные центрирующие конусы и шайбы (рис. 9, в). Для зарядов ВВ, обычно насыпных, из картона делают контейнеры заданных размеров.
Сварку осуществляют на открытых полигонах, если масса заряда достигает десятков и сотен килограммов, либо в специальных производственных помещениях в вакуумных камерах, если масса заряда ВВ не превышает нескольких килограммов. Использование вакуумных камер предотвращает разрушающее действие и даже звуковой эффект.
Сварные соединения обладают достаточно высокими свойствами; так, предел прочности соединений при срезе сталей 12Х18Н9Т и СтЗ равен 54 - 57 кгс/мм2 (52,9 - 558 МН/м2), стали 12Х18Н9Т и меди МЗ - 16,8 кгс/мм2 (164,5 МН/м2), стали 12Х18Н9Т и алюминия АДН - 7,2 кгс/мм2 (70,5 МН/м2). При испытаниях разрушение образцов, как правило, происходило по наименее прочному металлу пары на некотором расстоянии от плоскости соединения.
Измерением микротвёрдости сварных соединений выявлено упрочнение зон соединения шириной 10 - 100 мкм.
Малая продолжительность процесса сварки, которая длится микросекунды, даже при некотором повышении температуры поверхностных слоев металла, вызванном соударением и деформацией пластин, явно недостаточна для протекания диффузионных процессов. Вследствие этого в соединениях между разнородными металлами (Сu+Ti; Fe+Al; Fe+Си) отсутствуют интерметаллические составляющие. Таким образом, сварка взрывом позволяет получать, сварные соединения в твердой фазе без образования промежуточных химических составляющих между разнородными металлами и сплавами.
Разработка процесса сварки взрывом находится в начальной стадии и поэтому трудно определить области применения этого метода в будущем. Сварку взрывом используют при изготовлении заготовок для проката биметалла, при плакировке поверхностей конструкционных сталей металлами и сплавами с особыми физическими и химическими свойствами, а также при сварке заготовок и некоторых деталей из разнородных металлов. Перспективным представляется сочетание сварки взрывом со штамповкой и ковкой.
Вопросы для проверки
1. Какой физический принцип заложен в процесс сварки взрывом?
2. Какие металлы рекомендуется сваривать данным методом?
3. Какая энергия используется в способе сварки взрывом?
4. Какая подготовка поверхностей соединяемых металлов выполняется перед сваркой?
5. Какие связи образуются в результате сварки взрывом?
6. В течение какого времени происходит данный сварочный процесс?
7. Каковы перспективы развития сварки взрывом?
8. Какие взрывчатые вещества могут использоваться в данном сварочном процессе?
Тема 1.4. Сварка трением
Сварка трением является одним из методов сварки в твёрдой фазе. Здесь также теплота, влияющая на создание соединения, является не внешне прилагаемым фактором, а следствием механического процесса.
Метод сварки трением успешно применяется при удлинении различных тел вращения (валов, трубчатых изделий), удлинение хвостовиков режущего инструмента (свёрла, фрезы) и т. д. Способ сварки трением не является дорогостоящим и сложным процессом и поэтому находит довольно широкое применение для соединения разнообразных заготовок не требующих прецезионной точности.
Изучение материала данной темы способствует более глубокому пониманию студентами влияния изменения механических характеристик соединяемых материалов на процесс создания сварного соединения. Теоретический материал сопровождается рисунками, дающими наглядное представление изучаемого сварочного процесса. Для закрепления текущего материала предлагаются вопросы для самопроверки, а для контроля усвоения тест № 4 блока текущего контроля.
Сварка трением происходит в твердом состоянии при воздействии теплоты, возникающей при трении поверхностей свариваемого изделия. Трение поверхностей осуществляют вращением свариваемых деталей, сжимаемых усилием Р, как это показано на рис. 15. В процессе сварки наблюдаются значительные пластические деформации на свариваемых поверхностях. Прочное сварное соединение образуется в результате возникновения металлических связей между ювенильными (чистыми) контактирующими поверхностями свариваемых деталей. Препятствующие образованию этих связей различные включения и пленки, покрывающие металлические поверхности, разрушаются при трении и удаляются из зоны сварки в радиальном направлении вследствие значительной пластической деформации трущихся поверхностей.
Рис. 15. Принципиальные схемы сварки трением:
а — вращение одной детали, б — вращение обеих деталей.
Для получения требуемой деформации металл доводят до состояния повышенной пластичности с помощью теплоты, возникающей при трении. На поверхностях деталей, прижатых усилием Р, возникают силы трения. Работа, затрачиваемая на преодоление этих сил, превращается в теплоту, которая выделяется на поверхностях трения и вызывает интенсивный нагрев металла до температур, необходимых для образования сварного соединения применительно к сварке сталей эти температуры, в зависимости от режима процесса, составляют 950 - 1300 °С (1223 - 1573 К). По достижении требуемой температуры относительное движение деталей должно быть по возможности быстро (практически мгновенно) прекращено. Процесс образования сварного соединения завершают проковкой. Проковкой называется операция выдержки сваренных деталей под давлением, но уже без вращения. После проковки происходит естественное охлаждение сварных деталей.
Малый объем металла, нагреваемого при сварке трением, предопределяет и исключительно высокие энергетические характеристики процесса; расход энергии и мощность установок при сварке трением в 5 - 10 раз меньше, чем при контактной. При этом обеспечивается равномерная нагрузка фаз питающей сети, высокий коэффициент мощности (φ = 0,8 - 0,85).
Наиболее важным достоинством способа сварки трением, является высокое качество получаемых сварных соединений. Различные типы сварных соединений, выполненные сваркой трением, представлены на рис. 16. При правильно выбранном режиме сварки металл стыка и прилегающих к нему зон обладает прочностью и пластичностью, не меньшими, чем основной металл свариваемых деталей. Это объясняется следующим:
1. Все окисные и адсорбированные пленки и различные инородные частицы в процессе сварки трением удаляются из стыка в грат благодаря деформированию металла в радиальных направлениях. Плотный контакт между поверхностями трения препятствует образованию окислов в процессе сварки.
2. В стыке и прилегающих к нему зонах термического влияния металл приобретает структуру с равноосным измельчённым зерном; такая структура образуется в результате быстрого локального нагрева малых объемов металла и высоких скоростей их охлаждения в присутствии значительных давлений, достигающих 300 - 500 ат (29,4 - 49,0 МН/м2) и более того, имеет место механическое измельчение зёрен в процессе трения. Сварка трением позволяет получать прочные соединения не только из одноименных, но и из большого числа сочетаний разноименных металлов и сплавов, в том числе и таких, теплофизические характеристики которых резко различны.
При сварке трением не предъявляются высокие требования в отношении загрязненности к чистоты обработки боковых поверхностей деталей, предназначенных для сварки, этим сварка трением выгодно отличается от контактной. На поверхностях трения недопустима окалина, ее присутствие может привести к образованию недоброкачественного соединения.
Рис. 16. Типы сварных соединений, выполненных с помощью сварки трением:
а - стержни встык; б - трубы встык; в–стержень и труба встык;
г - соединения стержня и трубы с плоской поверхностью детали
Возможность использования сварки трением ограничивается также и размерами сечения свариваемых деталей в месте их сопряжения. Расчеты показывают, что использовать этот процесс для сварки стержней сплошного сечения диаметром более 200 мм при современном уровне развития техники нецелесообразно. Нижний предел диаметра свариваемых трением деталей - стержни диаметром менее 6 мм. Диапазон площадей сечений деталей, которые целесообразно сваривать трением, составляет 30—8000 мм2.
Расширить возможности применения сварки трением крупных деталей, вращение и в особенности быстрое торможение которых в конце процесса сильно затруднено, можно путем вращения вспомогательной детали (третьего тела), зажатой между двумя невращающимися и подлежащими сварке деталями (рис. 17). Эта схема процесса позволяет также сварить две (крайние) детали.
Рис. 17. Сварка двух неподвижных деталей с помощью
вращающейся третьей детали
На рис. 18 показана схема процесса сварки вибротрением, отличительная особенность которого - сообщение одной из свариваемых деталей возвратно-поступательного движения в плоскости трения с относительно малыми амплитудами. В этом случае можно сваривать детали с различной формой поперечного сечения.
Рис. 18. Сварка вибротрением
(возвратно-поступательные движения в плоскости стыка
с относительно малыми амплитудами при звуковой частоте)
Тепловой режим определяет производительность процесса, прочность сварного соединения, параметры сварочного оборудования и т. п.
Вследствие обнажения участков чистого металла уже в начале проведения процесса сварки, на поверхностях трения появляется возможность образования очагов схватывания. В процессе продолжающегося относительного движения поверхностей эти мостики вслед за их образованием разрушаются. Энергия, затраченная на их деформацию, проявляясь в форме теплоты, способствует повышению температуры поверхности, что, в свою очередь, облегчает образование новых очагов схватывания, которые вновь разрушаются.
Экономический эффект, получаемый в результате использования сварки трением заготовок инструмента, обусловлен значительным снижением брака и затрат труда и весьма существенной экономией дефицитной быстрорежущей стали. Замена электрической контактной сварки встык заготовок инструмента сваркой трения дает большую экономию.
В ближайшие годы сварка трением должна быть широко внедрена в промышленность. Для этого предстоит выявить детали, которые целесообразно сваривать трением.
Вопросы для проверки
1. В каком состоянии происходит процесс сварки трением?
2. Какие связи возникают между контактирующими поверхностями?
3. Какие существуют типы сварных соединений, выполненных этим способом?
4. Какие основные параметры сварки трением?
5. В чём отличительная особенность сварки вибротрением в общем процессе сварки трением?
6. В чём физический смысл выделения тепла в процессе сварки трением?
7. Что такое деформация смятия и как она происходит в данном процессе?
8. Как рекомендуется проводить подготовку свариваемых поверхностей?
9. По какому принципу устроены машины для сварки трением?
Дата добавления: 2018-04-15; просмотров: 534; Мы поможем в написании вашей работы! |
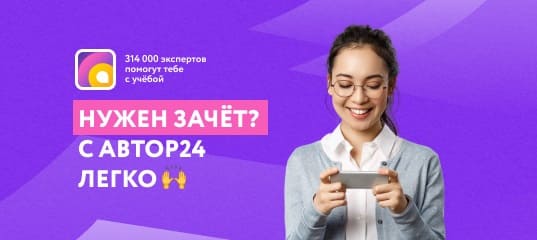
Мы поможем в написании ваших работ!