Порошки для наплавки и напыления.
В соответствии с ГОСТ 21448-75 (в ред. 1991 г.) выпускают порошки из сплавов: крупный (К) с размером частиц 1,25 ... 0,8 мм, средний (С) - 0,8 ... 0,4 мм, мелкий (М) -0,4 ... 0,16 мм и очень мелкий (ОМ) - менее 0,16 мм. ГОСТом предусмотрено 8 марок порошков: ПГ-С27 (тип ПН-У40Х28Н2С2ВМ), ПГ-С1 (тип ПН-У30Х28Н4С4), ПГ-УС25 (тип ПН-У50Х38Н), ПГ-ФБХ6-2 (тип ПН-У45Х35ГСР), ПГ-АН1 (Тип ПН-У25Х30СР), ПГ-СР2 (тип ПН-ХН80С2Р2), ПГ-СРЗ (тип ПН-ХН80СЗРЗ), ПГ-СР4 (тип ПН-ХН80С4Р4) для наплавки и напыления износостойкого слоя на детали машин и оборудования, работающие в условиях воздействия абразивного изнашивания, коррозии, эрозии при повышенных температурах или в агрессивных средах. Порошки поставляют в металлических банках массой до 50 кг.
Неплавящиеся электроды.
В зависимости от материала, из которого они изготовлены, электроды могут быть угольными, графитовыми, вольфрамовыми, циркониевыми, гафниевыми. Все эти материалы относятся к группе тугоплавких. Неплавящиеся электроды служат только для поддержания горения дуги и поэтому должны обладать высокой стойкостью при воздействии высоких температур (расход их должен быть минимальным).
Графитовые и угольные электроды различаются строением углерода. В графитовых электродах углерод имеет кристаллическое строение, в угольных - аморфное. Для угольного электрода электрическое сопротивление кубика с ребром в 1 см составляет 0,0032 Ом, для графитового 0,0008 Ом. Температура начала окисления на воздухе угольного электрода 500 °С, графитового 640 °С. Следовательно, по этим показателям предпочтительнее применение графитовых электродов.
|
|
Уменьшить диаметр электродов, исключить опасность науглероживания металла шва можно при применении электродов из тугоплавких металлов. Наиболее широкое применение для сварки имеют вольфрамовые электроды диаметрами 1 ... 6 мм, с высокой механической прочностью и сравнительно небольшим электрическим сопротивлением. Температура плавления вольфрама 3377 °С, температура кипения 4700 °С. Вольфрамовые стержни изготовляют из порошка (чистотой 99,7 %), который прессуют, спекают и проковывают, в результате чего отдельные его частицы свариваются. Заготовки подвергают волочению для получения стержней необходимых диаметров.
ГОСТ 23949-80 "Электроды вольфрамовые сварочные неплавящиеся" распространяется на электроды из чистого вольфрама марки ЭВЧ, вольфрама с присадкой оксида лантана марки ЭВИ-1, ЭВИ-2 и ЭВИ-3 и вольфрама с присадкой двуокиси тория марки ЭВТ-15. Эти электроды предназначены для дуговой сварки неплавящимся электродом в среде инертных газов, а также для плазменных процессов сварки, резки, наплавки и напыления. В ГОСТе приводится химический состав электродов, требования к поверхности и методы испытаний. Электроды диметром 0,5 мм выпускают в мотках, а электроды диаметром 1 ... 10 мм выпускают прутками длиной 75, 150, 200 и 300 мм.
|
|
Пример условного обозначения электрода длиной 150 мм:
Электрод вольфрамовый ЭВЛ-2-150 - ГОСТ 23949-80.
Циркониевые и гафниевые электроды используют в плазмотронах при термической резке металлов.
Флюсы сварочные
Сварочными флюсами называют специально приготовленные неметаллические гранулированные порошки с размером отдельных зерен 0,25 ... 4 мм (в зависимости от марки флюса). Флюсы, расплавляясь, создают газовый и шлаковый купол над зоной сварочной дуги, а после химико-металлургического воздействия в дуговом пространстве и сварочной ванне образуют на поверхности шва шлаковую корку, в которую выводятся окислы, сера, фосфор, газы.
В зависимости от свариваемых металлов и требований, предъявляемых при этом к металлургическим процессам, флюсы могут иметь самые различные композиции. Флюсы принято разделять в зависимости от способа их изготовления, назначения и химического состава. По способу изготовления флюсы разделяют на неплавленые (керамические) и плавленые.
Керамические флюсы. Технология их изготовления сходна с технологией изготовления покрытий электродов. Сухие компоненты шихты замешивают на жидком стекле, полученную массу измельчают путем продавливания ее через сетку на специальном устройстве типа мясорубки, сушат, прокаливают при тех же режимах, что и электродные покрытия, и просеивают для получения частиц зерен определенного размера. Частицы сухой смеси компонентов могут скрепляться спеканием при повышенных температурах без расплавления. Полученные комки гранулируют до необходимого размера (так называемые спеченные флюсы).
|
|
Неплавленые флюсы могут быть приготовлены и в виде простой механической смеси (флюсы - смеси). Из группы неплавленых флюсов наибольшее распространение получили керамические флюсы, состав которых близок к составу покрытий электродов основного типа. Легирование металла такими флюсами достигается введением в них необходимых ферросплавов. Флюсы при изготовлении не подвергаются операции расплавления, поэтому количество и сочетание ферросплавов и других легирующих элементов может быть различным, что позволяет легко получать любой требуемый состав металла шва.
Эта особенность керамических флюсов является главным их преимуществом. Однако при использовании таких флюсов химический состав металла шва сильно зависит от режима сварки. Изменение величины сварочного тока, и особенно напряжения дуги, изменяет соотношение масс расплавленных флюса и металла, а следовательно, и состав металла шва, который может быть неоднородным даже по длине шва.
|
|
Керамические флюсы обладают и другим серьезным недостатком - легко разрушаются вследствие малой механической прочности его частиц, что делает их разными по размерам.
Основная область их использования - сварка высоколегированных специальных сталей и наплавочные работы.
Плавленые флюсы представляют собой сплавы оксидов и солей металлов. Процесс изготовления их включает следующие стадии: расчет и подготовку шихты, выплавку флюса, грануляцию, сушку после мокрой грануляции и просеивание. Предварительно измельченные и взвешенные в заданной пропорции компоненты смешивают и загружают в дуговые или пламенные печи. После расплавления и выдержки, необходимой для завершения реакций, жидкий флюс при температуре около 1400 °С выпускают из печи.
Грануляцию можно осуществлять сухим и мокрым способами. При сухом способе флюс выливают в металлические формы, после остывания отливку дробят в валках до крупки размерами 0,1 ... 3 мм, затем просеивают. Сухую грануляцию применяют для гигроскопичных флюсов (содержащих большое количество фтористых и хлористых солей). Преимущественно это флюсы для сварки алюминиевых и титановых сплавов. При мокром способе грануляции выпускаемый из печи тонкой струей жидкий флюс направляют в бак с проточной водой. В некоторых случаях струю флюса дополнительно над поверхностью воды разбивают сильной струей воды.
Высушенную при температуре 250 ... 350 °С массу дробят и пропускают через два сита с 16 и 400 отверстиями на 1 см2. Остаток на втором сите представляет собой готовый флюс. Обычно это неровные зерна от светло-серого до красно - бурого или коричневого цвета (в зависимости от состава).
Хранят и транспортируют флюсы в стальных бочках, полиэтиленовых мешках и другой герметичной таре.
Принципиальное отличие плавленого флюса от керамического состоит в том, что плавленый флюс не может содержать легирующих элементов в чистом виде, в процессе выплавки они неизбежно окислятся. Легирование плавлеными флюсами происходит путем восстановления элементов из окислов, находящихся во флюсе.
В основу классификации флюсов по химическому составу положено содержание в них оксидов и солей металлов. Различают окислительные флюсы, содержащие в основном оксиды МnО и SiО2. Для получения необходимых свойств флюса в него вводят и другие составляющие, например плавиковый шпат, а также весьма прочные оксиды CaO, MgO, A12О3, которые в сварочных условиях практически не реагируют с металлом.
Чем больше содержится во флюсе МnО и SiО2, тем сильнее флюс может легировать металл кремнием и марганцем, но и одновременно тем сильнее он окисляет металл. Поэтому окислительные флюсы преимущественно применяют при сварке углеродистых и низколегированных сталей. Безокислительные флюсы практически не содержат оксидов кремния и марганца или содержат их в небольших количествах. В них входят фториды CaF2 и прочные оксиды металлов. Их преимущественно используют для сварки высоколегированных сталей.
Бескислородные флюсы целиком состоят из фторидных и. хлоридных солей металлов, а также других составляющих, не содержащих кислород. Их используют для сварки химически активных металлов (алюминия, титана и др.).
В связи с широким применением плавленых флюсов на основные марки флюсов существует ГОСТ 9087-81 (в ред. 1990 г.) "Флюсы сварочные плавленые", в котором регламентирован химический состав 21 марки плавленых флюсов, указаны цвет, строение и размеры зерна и даны рекомендации по области их применения (табл. 2.8).
Для двух марок флюсов АН-20 и АН-26 сделано разделение не только по размеру зерна, но и в зависимости от строения зерен флюса - стекловидного или пемзовидного характера. Строение зерен флюса зависит от состава расплава флюса, степени перегрева в момент выпуска в воду, в связи с чем флюс может получиться плотным, с прозрачными зернами -"стекловидный", либо пористым, рыхлым - "пемзовидным". Пемзовид-ный флюс при том же составе имеет в 1,5 ... 2 раза меньший удельный вес. Эти флюсы хуже защищают металл от действия воздуха, но обеспечивают лучшее формирование швов при больших силах тока и скоростях сварки.
Флюсы различают также и по размеру зерен. Так, флюсы АН-348-А, ОСЦ-45, АН-20С, АН-26П имеют размер зерен 0,35 ... 3 мм; флюсы АН-348-АМ, ОСЦ-45-М, ФЦ-9, АН-20С 0,25 ... 1,6 мм; флюсы АН-8, АН-22 и АН-26С - 0,35 ... 4 мм и флюс АН-26-СП - 0,25 ... 4 мм. Стекловидные флюсы с размером зерен не более 1,6 мм предназначены для сварки электродной проволокой диаметром не свыше 3 мм.
В обозначении марки флюса буквы означают: М - мелкий, С - стекловидный, П - пемзовидный, СП - смешанный.
Пример условного обозначения флюса по стандарту:
флюс АН-348-АМ - ГОСТ 9087-81.
Для электрошлаковой сварки применяют флюсы общего назначения АН-348-А, АН-22 (см. табл. 2.8), 48-ОФ-6, АНФ-5 (табл. 2.9) и флюсы, предназначенные именно для данного процесса (АН-8 и АН-25). Содержание в этих флюсах окислов титана обеспечивает высокую электропроводность их в твердом состоянии, что важно в начале процесса, при возбуждении дуги для создания начального объема шлаковой ванны. Лучшим с технологической точки зрения является флюс АН-8.
При механизированной сварке меди и ее сплавов успешно используют обычные марки флюсов ОСЦ-45, АН-348-А, АН-20, АН-26, т.е. флюсов, широко применяемых для сварки сталей. Для сварки алюминия и его сплавов по слою флюса разработаны две основные марки бескислородных флюсов: АН-А1 и АН-А4 (табл. 2.10).
Эти флюсы изготовляют сплавлением входящих в их состав солей или механическим их смешиванием. Для электрошлаковой сварки алюминия также разработаны специальные флюсы.
При сварке титана используют бескислородные флюсы типа АН-Т1, АН-ТЗ и др., в состав которых в основном входят фтористые и хлористые соединения. Фтористые соединения могут реагировать с оксидами титана и растворять их, но для обеспечения необходимых технологических свойств флюса в них вводят хлористые соединения.
Защитные газы.
Защитные газы делятся на две группы: химически инертные и активные. Газы первой группы с металлом, нагретым и расплавленным, не взаимодействуют и практически не растворяются в нем. При использовании этих газов дуговую сварку можно выполнять плавящимся или неплавящимся электродом. Газы второй группы защищают зону сварки от воздуха, но сами либо растворяются в жидком металле, либо вступают с ним в химическое взаимодействие.
Ввиду химической активности углекислого газа по отношению к нагретому вольфраму (окисление и разрушение вольфрама) для дуговой сварки в углекислом газе используют плавящиеся электроды или неплавящиеся (угольные или графитовые).
К химически инертным газам, используемым при сварке, относятся аргон и гелий (табл. 2.11). Из химически активных газов основное значение имеет углекислый газ.
Аргон - газообразный чистый поставляется по ГОСТ 10157-79 (в ред. 1998 г.) двух сортов: высшего и первого. Содержание аргона соответственно равно: 99,99 %; 99,98 %. Примесями служат кислород, азот и водяные пары.
Хранится и транспортируется аргон в газообразном виде в стальных баллонах под давлением 15 МПа, т.е. в баллоне находится 6,2 м газообразного аргона в пересчете на температуру 20 °С и давление 760 мм рт. ст. (0,1 МПа). Возможна также транспортировка аргона в жидком виде в специальных цистернах или сосудах Дьюара с последующей его газификацией. Баллон для хранения аргона окрашен в серый цвет, надпись зеленого цвета.
Аргон высшего сорта предназначен для сварки химически активных металлов (титана, циркония, ниобия) и сплавов на их основе. Аргон первого сорта рекомендуется для сварки неплавящимся электродом сплавов алюминия, магния и других металлов, менее чувствительных к примесям кислорода и азота.
Гелий - газообразный чистый поставляют по техническим условиям. Гелий для сварки марок А, Б и В содержит не менее 99,99 % чистого гелия, остальное примеси. Примеси: азот, водород, кислород, неон, влага. Хранят и транспортируют гелий так же, как и аргон, в стальных баллонах вместимостью 40 л при давлении 15 МПа. Цвет баллона коричневый, надпись белого цвета. В связи с тем, что гелий в 10 раз легче аргона, расход гелия при сварке увеличивается в 1,5 ... 3 раза.
Углекислый газ поставляется по ГОСТ 8050-85 (в ред. 1996 г.). Для сварки используют сварочную углекислоту высшего и первого сортов, которые отличаются лишь содержанием паров воды (соответственно 0,037 и 0,184 г/см3 при 20 °С и давлении 0,1 МПа). Углекислоту транспортируют и хранят в стальных баллонах или цистернах большой емкости в жидком состоянии с последующей газификацией на заводе, с централизованным снабжением сварочных постов через рампы. В баллоне вместимостью 40 л содержится 25 кг С02, дающего при испарении 12,5 м3 газа при давлении 0,1 МПа (760 мм рт. ст.). Баллон окрашен в черный цвет, надписи желтого цвета.
При применении углекислого газа вследствие большого количества свободного кислорода в газовой фазе сварочная проволока должна содержать дополнительное количество легирующих элементов с большим сродством к кислороду, чаще всего Si и Мn (сверх того количества, которое требуется для легирования металла шва). Наиболее широко применяется проволока Св-08Г2С.
При применении защитных газов следует учитывать технологические свойства газов (например, значительно больший расход гелия, чем аргона), их влияние на форму проплавления и форму шва, а также стоимость газов.
При сварке плавящимся электродом значительное влияние на характер переноса электродного металла, производительность расплавления электрода, разбрызгивание, и форму проплавления оказывает состав защитного газа, в котором горит дуга. Хорошие перспективы по улучшению этих показателей дает применение смесей газов. Улучшает перенос электродного металла и позволяет получать более плавную наружную поверхность шва применение смеси углекислого газа с 2 ... 15 % кислорода. Широко применяется при сварке сталей двойная смесь, состоящая из 80 % аргона и 20 % углекислого газа, позволяющая реализовать мелкокапельный и струйный перенос электродного металла. Применение многокомпонентных смесей, состоящих из аргона, углекислого газа, окиси азота, водорода и др. газов позволяет увеличить производительность расплавления и наплавки более чем в 2 раза при благоприятной форме проплавления и наружной поверхности шва.
Дата добавления: 2018-04-15; просмотров: 663; Мы поможем в написании вашей работы! |
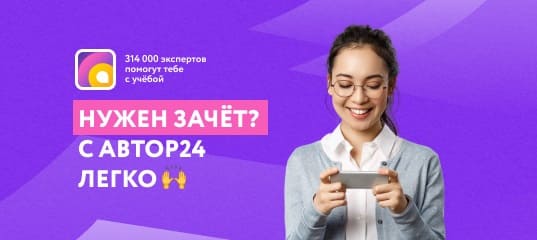
Мы поможем в написании ваших работ!