Исходные данные для выполнения работы
Н.В. Панишев, С.К. Сибагатуллин
Практикум по дисциплине
«Новые процессы в металлургии»
Магнитогорск, 2014
УДК 669.1:622.788(075)
ББК 34.323я7
П 162
Рецензенты:
Кафедра экстракции и рециклинга чёрных металлов
ФГАОУ ВПО «Национальный исследовательский
технологический университет МИСиС»
(заведующий кафедрой
кандидат технических наук, профессор, Г.С. Подгородецкий)
Менеджер группы инвестиционных программ дирекции по развитию бизнеса и управлению эффективности ОАО «ММК»
кандидат технических наук, В. В. Арцибашев
Практикум по дисциплине “Новые процессы в металлургии»: учеб. пособие/ Н.В. Панишев, С.К. Сибагатуллин,Магнитогорск: Изд-во Магнитогорского государственного технического университета им. Г.И. Носова, 2014. 93 с.
ISBN
Изложена сущность наиболее важных явлений и логическая связь основных этапов процесса подготовки сырых материалов к металлургическому переделу, влияние качественных характеристик исходного сырья на технико-экономические показатели работы металлургических агрегатов и качество конечного продукта.
Пособие предназначено для студентов, обучающихся по направлению 150400.62 “Металлургия”, профилю подготовки “Металлургия черных металлов", полезно инженерно-техническим работникам предприятий черной металлургии.
|
|
УДК 669.1:622.788(075)
ISBN © Магнитогорский государственный
технический университет
им. Г.И. Носова, 2014
© Панишев Н.В.,
Сибагатуллин С.К., 2014
Оглавление
Введение 4
1. Минералогический тип руды 4
2. .Дробление и измельчение, грохочение и классификация сырых материалов 8
|
|
3. Оценка гранулометрического состава смеси фракций 12
4. Обогащение руд 17
5. Оценка однородности сырых материалов 23
6. Металлургическая оценка сырых материалов 26
7. Окускование руд 31
8. Качество окускованного железорудного сырья 37
9. Металлизация 50
10. Литература 54
11. Приложение 55
Введение
Целью настоящего пособия является акцентирование внимания студентов на узловых моментах специальной дисциплины «Новые процессы в металлургии», а также на вопросах, нуждающихся в изложении с позиции современных теоретических представлений. Пособие охватывает основные вопросы, поднимаемые программой дисциплины, и не повторяет известные пособия.
|
|
В разделах пособия изложена сущность наиболее важных явлений, показана логическая связь основных этапов процесса подготовки сырых материалов к металлургическому переделу. Кроме необходимого объема теоретических сведений каждый раздел содержит подробное решение типовых примеров и необходимый справочный материал для студентов двух академических групп.
Введение, разделы 1-7,9-11 написаны Н.В.Панишевым, раздел 8 – С.К.Сибагатуллиным.
Содержание и методика изложения пособия, основанные на многолетнем опыте преподавания специальных дисциплин на кафедре металлургии черных металлов ФГБОУ ВПО МГТУ, продиктованы стремлением закрепления знаний по важнейшим вопросам изучаемой дисциплины путем активизации самостоятельной работы студентов на практических занятиях при решении задач сравнительно небольшого объема.
1. МИНЕРАЛОГИЧЕКИЙ ТИП РУДЫ
Знание минералогического типа руды необходимо при проектировании дробильных и обогатительных фабрик, при проектировании и прогнозировании работы фабрик окускования и агрегатов для получения металлизованной продукции.
|
|
Мощности и виды дробильных агрегатов, способы обогащения определяются соответствующими свойствами перерабатываемых руд. В зависимости от типа руды задаются содержанием углерода и влаги в агломерационной шихте (табл. 1.1) [1]., а также содержанием углерода в шихте для получения металлизованного продукта [2].
Таблица 1.1
Содержание углерода в шихте, ее влажность и насыпная плотность
Минералогический тип руды | Рудный минерал | Насыпная плотность, т/м3 | Содержание в шихте, % | |
углерода | влаги | |||
Магнитный железняк | Fe3O4 | 1,75-2,0 | 3,5-4,5 | 6,0-8,0 |
Красный железняк | Fe2O3 | 1,48-1,6 | 4,5-5,0 | 8,0-10,0 |
Бурый железняк | Fe2O3; * n H2O | 0,55-0,6 | 6,0-8,0 | 14,0-18,0 |
Шпатовый железняк (сидеритовые руды)* | FeCO3 | 0,5-1,7 | - | - |
*- Сидеритовые руды обычно спекаются в смеси с другими рудами, чаще с бурыми железняками. Поэтому в расчетах следует задаваться содержанием углерода и влаги в шихте, близким для случая бурых железняков. Концентраты обогащения сидеритов после восстановительного обжига спекаются при тех же условиях, что и магнитные железняки.
Красный железняк является самым распространенным типом руды. Характеризуется высоким содержанием железа и чистотой от вредных примесей.
Магнитные железняки менее распространены, чем красные железняки, характеризуются высоким содержанием железа, пониженной восстановимостью, часто сопровождаются серой.
Водные окислы железа в зависимости от значения «n» образуют разные минералы, но все образуемые ими руды называются бурыми железняками. Выделяются следующие основные минералы:
n<1 – гидрогематит, содержит 62-69% железа;
n=1 – гетит, содержит 62,9% железа;
n=1-1,5 – гидрогетит (лимонит), содержит 59,8-63% железа.
Лимонит отвечает формуле 2Fe2O3*3H2O, т.е. n=1,5. Бурые железняки характеризуются пониженным содержанием железа, рыхлостью, часто сопровождаются марганцем, фосфором, обладают высокой пористостью и восстановимостью.
Шпатовые железняки распространены меньше, чем другие руды, характеризуются высокой восстановимостью, низким содержанием железа. Под воздействием влаги и кислорода атмосферы сидериты переходят в бурые железняки, так как закись железа в формуле FeO*CO2 окисляется и поглощает влагу. Поэтому месторождения, в которых верхние слои руды являются бурыми железняками, в нижних, коренных слоях содержат сидериты.
Меньший расход углерода на процесс спекания шихты из магнетитовых руд обусловлен выделением тепла за счет экзотермической реакции окисления магнетита в гематит, выгорания сульфидной серы. Высокие затраты тепла на разложение гидратов и карбонатов железа объясняют повышенное содержание углерода при окусковании соответственно бурых железняков и сидеритов. Развитие восстановительных процессов оксидов железа требует дополнительного тепла при спекании гематитовых руд.
В расчетах производительности обжиговых и агломерационных машин, а также емкостей штабелей на усреднительных складах и емкости бункеров в шихтовом отделении фабрик окускования учитывают насыпную плотность руд, зависящую от их минералогического типа. Определить минералогический тип руды можно, пользуясь данными табл. 1.2.
Таблица 1.2
Неполный химический состав руд различного минералогического типа, %.
Тип руды | Feобщ | FeO | П.п.п. |
Магнитный железняк | 40-65 | 15-28 | до 5,0 |
Красный железняк | 50-60 | до 2,5 | до 5,0 |
Бурый железняк | 35-50 | до 2,0 | 10-12 |
Шпатовый железняк | 25-35 | >28,0 | 28-33 |
Обычно принимают, что в основном в потери при прокаливании (п.п.п.) в сидеритах входит CO2, в остальных материалах - гидратная влага. При отсутствии данных о соединениях серы в материалах условно принимают, что вся сера в магнетитовых и полумартитовых рудах связана в пирит FeS2; в других типах железных руд, а также в марганцевых рудах, известняке, колошниковой пыли – в сернистый ангидрит SO2.
Тип руды в зависимости от степени окисления магнетита можно определить, следуя рекомендациям академика М.А. Павлова (табл. 1.3) [3].
В некоторых случаях минералогический тип исходной руды существенно отличается от минералогического типа концентрата обогащения этой руды. Например, в результате восстановительного обжига бурых железняков, сидеритов, железистых кварцитов (при этом снижаются п.п.п.) и последующего магнитного обогащения продукта обжига получают концентраты с характеристиками магнитных железняков. Другой причиной изменения типа руды может быть различная магнитная восприимчивость оксидов железа в исходной магнетитовой руде, приводящая к снижению общей степени окисления железа в концентрате магнитного обогащения этой руды вследствие уноса с хвостами части слабомагнитных с повышенной окисленностью железа рудных минералов.
Таблица 1.3
Определение минералогического типа руды в зависимости от степени окисления магнетита
Тип руды | Feобщ /FeFeO |
Магнетитовая | < 3,5 |
Полумартитовая | 3,5-7,0 |
Мартитовая | > 7,0 |
В связи с истощением запасов магнетитовых руд все в большей степени вовлекаются в передел руды, содержащие титаномагнетиты FeTiO3 Fe3O4, которые, как и магнетитовые руды, отличаются высокой плотностью, низкой восстановимостью. Часто эти руды содержат ванадий. Подготовка этих руд к металлургическому переделу аналогична магнетитовым рудам, но участие их в доменном переделе ограничено содержанием в них оксидов титана (см. раздел 8).
Установление минералогического типа руды необходимо при подготовке исходных данных для составления материального и теплового балансов доменного процесса и процессов окускования и металлизации. Как правило, данные химического состава материалов отражают не все, а только основные компоненты, представляющие для металлургов интерес. Часто в химических составах содержание некоторых элементов указывается в свободном состоянии.
Понятно, что в таких случаях сумма компонентов химического состава будет меньше 100%. Обеспечить же сводимость материального баланса металлургических процессов можно лишь при равенстве суммы всех составляющих химического состава 100 %.
Пример
Аглофабрика работает на концентрате следующего химического состава, %: Fe - 52,0; Mn - 0,4; P - 0,04; S - 1,2; SiO2 - 8,8; Al2O3 - 4,0; CaO – 5,6; MgO – 0,4; FeO – 20,0; п.п.п. – 1,8.
Проверить сумму компонентов химического состава на 100 %. Принять влажность шихты и содержание в ней углерода.
Решение:
Поскольку отношение Feобщ / FeFeO = 52 72 / 20 56 <3,5, п.п.п. не превышает 5 %, рассматриваемый концентрат является магнетитовым, в котором сера связана в пирит FeS2.
С серой связано железа 1,2 56 / 64 = 1,05 %.
В концентрате содержится пирита 1,05 120 / 56 = 2,25 %.
В FeO связано железа 20·56 / 72 = 15,56 %.
Количество железа в Fe2 O3 52 - 1,05 - 15,56 = 35,39 %.
В концентрате содержится гематита (Fe2 O3) 35,39 · 160 / 112 = 50,56 %.
В концентрате содержание MnO и P2 O5 составит соответственно
MnO 0,4 *71 / 56 = 0,52 %. P2 O5 0,04 * 142 / 62 = 0,09%.
После выполненных расчетов сложим содержание всех компонентов химического состава
2,25 + 50,56 + 20,0 + 0,52 + 0,09 + 8,8 + 4,0 + 5,6 + 0,4 + 1,8 = 94,02 % .
Неравенство суммы компонентов 100 % может быть вследствие неточности проведения химического анализа или ошибочно принятого распределения элементов по соединениям.
Пересчитаем химический состав концентрата на 100 % согласно выражению
K i100 = 100 · Ki исх / ∑ Ki исх;
где Ki исх - содержание компонента в исходном химическом составе, %;
K i100 - то же после перерасчета на 100 %;
∑ Ki исх - сумма содержаний компонентов в исходном химическом
составе, %.
Fe2 O3100 = 50,56 *100 / 94,025 = 53,78 %0
Fe O100 = 20 *100 / 94,02 = 21,27 %
Fe S2100 = 2,25 *100 / 94,02 = 2,39 %
P2 O5100 = 0.09 *100 / 94.02 = 0,1 %
Mg O100 = 0,4 100 */ 94,02 = 0,43 %
Si O2100 = 8,8 *100 / 94,02 = 9,36 %
Mn O100 = 0,52 *100 / 94,02 = 0,55
Са O100 = 5,6 *100 / 94,02 = 5,96 %
Al2 O3100 = 4,0 *100 / 94,02 = 4,25 %
п.п.п. 100 = 1,8 *100 / 94,02 = 1,91 %
Просуммируем новые значения содержания компонентов:
53,78 + 2,39 + 0,1 + 0,55 + 9,36 + 5,96 + 0,43 + 4,25 + 1,91 = 100 %.
Рассчитаем содержание в концентрате Fe, Mn, P и S в виде свободных элементов, исходя из пересчитанного содержания их соединений.
Fe = 53,78 *112 / 160 + 21,27 *56 / 72 +2,39 *56 / 120 = 55,31 %.
Mn = 0,55 *56 / 71 = 0,43 %.
P = 0,1 *62 / 142 = 0,044 %.
S = 2,39 *64 / 120 = 1,27 %.
Поскольку спеканию подвергается магнетитовый концентрат, принимаем (см. табл. 1.1) содержание углерода в шихте 4,0 %, влаги 7,5 % и насыпную плотность шихты 2,0 т/м3 .
Задание к работе 1
Оперируя данными, представленными в табл. П.1, определить минералогический тип руды и концентрата, проверить сумму составляющих компонентов на 100 %. Принять содержание влаги и углерода в агломерационной шихте и ее насыпную плотность.
2. ДРОБЛЕНИЕ И ИЗМЕЛЬЧЕНИЕ, ГРОХОЧЕНИЕ И КЛАССИФИКАЦИЯ
СЫРЫХ МАТЕРИАЛОВ
Дробление и измельчение сырых материалов производят с целью доведения их крупности до размеров кусков (зерен), приемлемых для доменной плавки, обогащения, окускования или металлизации, поскольку куски руды могут достигать до 1,5 м в поперечнике при открытом способе добычи руды и до 0,8 м – при подземной добыче.
Верхний предел крупности для богатых руд, загружаемых в доменные печи, определяется их характеристиками и составляет:
-30-50 мм для магнитных железняков;
-50-80 мм для красных железняков;
-80-100 мм для бурых железняков.
Нижний предел для всех руд составляет 10-12 мм, поскольку отсев фракций менее 5 мм затруднен.
Под дроблением понимают операцию разрушения кусков до 5 мм. Дальнейшее уменьшение размеров кусков называют измельчением.
Дробление и измельчение являются энергоемкими процессами. Поэтому весьма важно соблюдать принцип «не дробить ничего лишнего», т.е. не загружать в дробилки куски, крупность которых меньше ширины выпускной щели дробилки. Отделение таких кусков производится грохочением материалов (см. ниже) перед загрузкой их в дробилки.
Дробление подразделяют на:
-крупное от 1500 до 100-400 мм;
-среднее от 100-400 до 30-50 мм;
-мелкое от 30-50 до 5 мм.
Стадии уменьшения размера кусков (зёрен) характеризуются степенью дробления (измельчения) i, т.е. отношением размера максимального куска (зерна) руды Dmax до дробления (измельчения) к размеру максимального куска (зерна) в продукте после дробления (измельчения) dmax, т.е.
i = Dmax / dmax (2.1)
Иногда среднюю степень дробления (измельчения) определяют как отношение средних диаметров
i = Dср / dср . (2.2)
Общая степень дробления (измельчения) будет равна произведению частных степеней дробления (измельчения) в каждой стадии, т.е.
i= i1 *i2 *i3*in. (2.3)
Разделение или сортировка материалов по крупности на механических ситах называют грохочением, а разделение материалов при падение в воде или на воздухе - гидравлической или воздушной классификацией. Грохочением разделяются материалы на классы до крупности 1-3 мм, а более мелкие фракции – классификацией. В результате грохочения сыпучие материалы разделяются на классы – продукты, имеющие определённые размеры кусков (зёрен).
Отверстия на рабочей поверхности грохота могут быть круглыми, квадратными или прямоугольными. Крупность продуктов принято выражать в миллиметрах или микрометрах. Размер отверстий тканых сит и соответственно рассеваемого материала в зарубежной, а иногда и в отечественной практике характеризуется числом меш – количество отверстий, приходящимся на один линейный дюйм сетки, т.е. на 25,4 мм.
По технологическому назначению различают четыре вида операций разделения материала по крупности [4]:
1) самостоятельное грохочение - для выделения классов, представляющих собой готовые, отправляемые потребителю продукты;
2) подготовительное грохочение – для разделения материала на несколько классов крупности, предназначенных для последующей разделительной обработки;
3) вспомогательное грохочение – операция для выделения мелких классов, не подлежащих дроблению (измельчению);
4) обезвоживающее грохочение – операция обезвоживания на грохотах продуктов обогащения или обесшламливания материалов перед дальнейшим обогащением.
Материалы, поступающие на грохочение, называют исходным, оставшийся на сите – надрешётным, просыпавшийся через отверстия сита – подрешётным продуктом.
2.1. Определение основных технологических параметров процесса разделения материалов по крупности
2.1.1. Выход подрешётного продукта
На Рис.1.1 приведена схема односитового грохота с показателями грохочения [4].
Рис.1.1.Схема односитового грохота (к определению показателей грохочения)
При установившемся режиме работы грохота соблюдается равенство
Q = P + S, (2.4)
где Q – масса исходного материала, подаваемого на грохот в единицу времени, т/ч;
P, S – масса соответственно подрешётного и надрешётного продуктов в единицу времени, т/ч.
Уравнение баланса расчётного мелкого класса имеет вид
Q·α0 = P·β + S·υ, (2.5)
где α0, β, υ – содержание мелкого класса соответственно в исходном, подрешётном и надрешётном продуктах, %.
После подстановки значения S из предыдущего равенства, уравнение баланса получит вид
Q·(α0 - υ) = P·(β - υ). (2.6)
Отсюда выход подрешётного продукта, равный отношению масс подрешётного и исходного (γ = 100·P/Q), %:
γ = 100(α0 - υ) / (β - υ) (2.7)
Если расчёт ведётся по классу, верхний предел крупности которого равен ширине (диаметру) ячеек сита, то содержание расчётного класса в определённом продукте составит 100% (т.е. β = 100%). В этом частном случае выход подрешётного продукта составит
γо = 100(α0 - υ) / (100 - υ). (2.8)
2.1.2. Извлечение мелкого класса в подрешётный продукт
Извлечение (ε) мелкого класса в подрешётный продукт представляет собой выраженное в процентах отношение массы данного класса в подрешётном продукте к общему количеству этого же класса в исходном материале. Оно определяется по уравнению
ε = β γ / α0 (2.9)
Подстановка в равенство (2.9) значения γ из формулы (2.7) даёт
ε =100 β (α0 - υ)/ α (β - υ) (2.10)
В частном случае, когда β = 100 % подставленная формула принимает вид
ε =10000 (α0 - υ)/ αо (100 - υ) (2.11)
2.1.3. Эффективность разделения
Эффективность разделения (грохочения, классификации) по классу мельче отверстий сита представляет отношение массы этого класса в подрешётном продукте к массе этого класса в исходном материале. Это отношение равно разности между извлечением (ε) расчётного мелкого класса в подрешётный продукт и извлечением (ε+ ) в него крупного класса [4]
Е = ε – ε+ (2.12)
Первый член правой части находится по формуле (2.10). Второй член, т.е. извлечение (ε+) в подрешётный продукт крупных классов, определяется как произведение выхода γ подрешётного продукта на отношение содержаний крупного класса в подрешётном (100 - β) и в исходном (100 – α0):
ε+= γ (100- β) / (100- α) (2.13)
или
Е =100 γ (β- α0/) / (100- α0) (2.14)
На основе предыдущих соотношений общая формула эффективности грохочения может быть записана в различных, но и в равнозначных вариантах.
Е = ε – ε+=100 γ (β- α0) / α0 (100- α0) =100(ε - γ)/ (100- α0) =
=10000(β- α0)( α0 – υ) / α0 (100- αо) (β - γ) (2.15)
В частном случае, когда β = 100 %, т.е. расчётным считается весь класс мельче размеров ячеек сита, формула (2.15) упрощается:
Ео = ε0 = 100 γ/ α0 = 10000(α0 - υ) / α0 (100 - υ). (2.16)
т.е. эффективность грохочения (Е0) по всему мелкому классу (верхний предел которого равен размеру отверстий сита) равна извлечению этого класса в подрешётный продукт (в этом частном случае эффективность (Е0) иногда называют точностью грохочения).
Если же расчёт ведётся по классу меньшему, чем отверстие сита, то содержание его в подрешётном продукте будет меньше 100 % и эффективность (Е) будет отличаться от измельчения (ε).
2.1.4. «Замельчённость»
Вследствие вероятностного характера процесса грохочения в надрешётном продукте неизбежно остаётся некоторое количество подлежащих отсеву мелких классов. Содержащие их (υ) в надрешётном продукте характеризует степень его засорённости, или «замельчённость».
Она зависит от эффективности грохочения (Е0,равного извлечению ε0) и начального содержания (α0) отсеваемых мелких классов в исходном материале. Решение уравнения (2.16) относительно (υ) даёт [4]:
υ =( β - ε0 ) / (β / α0- ε0/100) (2.17)
где β = 100 %.
Непосредственно по выходу (γ) подрешётного продукта «замельчённость» надрешётного продукта может быть вычислена по формуле
υ =100(αо- γ)/(100- α ) (2.18)
Таким образом, качество процесса грохочения необходимо характеризовать двумя параметрами – эффективность грохочения (Е0) и «замельчённостью» υ надрешётного продукта, так как высокая эффективность ещё не гарантирует хорошего качества надрешётного продукта.
Пример 1
Из возврата крупностью 0-15 мм требуется выделить «постель» (класс 8-15 мм) грохочением возврата на сетке с ячейками 8х8 мм. «Замельчённость» «постели» υ не должна превышать 10 %. Грохочение ведётся с очень высокой эффективностью Е0 = ε0 = 98 %.
Решение
«Замельчённость» надрешётного продукта («постели») классом 0-8 мм согласно формуле (2.17) составит
υ =( β - ε0 )/ (β / α0- ε0/100) =(100-98)/(100/90-98/100)=15,3 %.
Для обеспечения требуемой предельной «замельчённости» «постели» υ, равной 10 %, в соответствии с формулой (2.16) необходимо проводить грохочение с более высокой эффективностью отсева, а именно:
Ео = ε0 = 100 γ/ α0 = 10000(α0 - υ)/ α0 (100 - υ) =
=10000 (90-10)/90(100-10)=98,77%,
что достижимо только при понижении нагрузки грохота.
Пример 2
По современным представлениям содержание класса 0-5 мм в агломерате перед загрузкой в доменную печь не должно превышать 5 %. Найти необходимую эффективность грохочения при различном содержании класса 0-5 мм α0 в годном агломерате.
Решение
Согласно формуле (2.16) для получения υ = 5 % необходимая эффективность грохочения должна составить
Ео = 100(α0 - 5)/0,95 α0 (2.19)
Отсюда при α0 равном, например, 10, 20 и 30 % эффективность грохочения Е0 будет соответственно равна 52,5; 79,0 и 87,5 %, т.е. эффективность должна быть тем выше, чем больше содержится подлежащего отсеву мелкого класса α0 в исходном материале. Это правило сохраняет свою силу при любом значении υ.
Задание к работе 2
Используя данные табл.П.2, рассчитать основные технологические параметры разделения материалов по крупности.
3. ОЦЕНКА ГРАНУЛОМЕТРИЧЕСКОГО СОСТАВА СМЕСИ ФРАКЦИЙ
Развитие тепломассообменных процессов, являющихся решающими в доменной плавке и в процессах окускования и металлизации, определяется теплофизическими свойствами и крупностью сырья [5], зависит от газопроницаемости слоя шихтовых материалов.
В свою очередь газодинамические характеристики слоя определяются распределением компонентов полидисперсной смеси по крупности. В практических расчётах важно уметь производить оценку гранулометрического состава материалов.
Размер частицы шарообразной формы однозначно характеризуется диаметром того шара, к которому близка по размеру рассматриваемая частица. В этом случае номинальный диаметр частицы совпадает с диаметром (d) наименьшего круглого отверстия, через которое шарообразная частица способна проходить.
В большинстве случаев минеральные частицы имеют неправильную форму и при определении номинального размера частицы её условно заменяют в каком-либо отношении эквивалентным телом правильной формы.
Номинальным диаметром кусков и частиц, выделенных при ситовом анализе, считается сторона квадратного отверстия, определяющего размеры наибольших проходящих через него кусков.
Для тонкого материала (мельче 0,045 мм) крупность частиц устанавливается в результате шламового (седиментационного) анализа; для них условным диаметром считается диаметр правильного шара, падающего в воде с той же конечной скоростью, что и данная частица, и имеющего одинаковую с ней плотность. Крупность самых тонких частиц (менее 0,005 мм) определяется под микроскопом [4].
Помимо определения крупности по номинальному (условному) диаметру крупность частиц неправильной формы оценивают одним линейным измерителем – «средним диаметром», заменяющим все три измерения. В этом случае частицы заменяется эквивалентным ей телом правильной геометрической формы.
Понятие «средний диаметр» становится определённым лишь, если указано, в каком отношении устанавливается эквивалентность между измеряемой частицей и телом правильной геометрической формы.
Для того, чтобы термин “средний диаметр зерна” имел физический смысл, необходимо всякий раз оговаривать, каким образом достигнуто полученное усреднение.
Например, чтобы кратко охарактеризовать близкую по форме к параллелепипеду частицу длиной (d), шириной (b), и толщиной (h), используют все её размеры или часть из них.
За диаметр (d) частицы принимают:
- ширину параллелепипеда
d = b; (3.1)
- среднее арифметическое из длины и ширины
d = (b +l) / 2; (3.2)
- то же, из длины, ширины и толщины
d = (b +l + h) / 3; (3.3)
- среднее геометрическое из длины и ширины
; (3.4)
- ребро куба, равновеликого параллелепипеду по объему
; (3.5)
- ребро куба, равновеликого параллелепипеду по поверхности
; (3.6)
- ребро куба, эквивалентного параллелепипеду по удельной поверхности
d = 3 · b · l · h / (b l + l h + b h ). (3.7)
С помощью сит можно получить один размер частицы (зерна). В этом случае приходится пользоваться формулой (3.1). С помощью микроскопа определяют два размера, что делает возможным применение формул (3.2) и (3.4). Для крупных зерен (кусков) можно получить три размера и применить остальные формулы, если потребуется охарактеризовать линейный размер, объём, поверхность или удельную поверхность соответственно.
Определение величины среднего диаметра в практических задачах, связанных с гранулометрическим составом смеси зерен, обусловлено удобством оперирования одной величиной, нежели со всей гранулометрической характеристикой. Средний диаметр при этом должен давать упрощенное суммарное представление о крупности исследуемой смеси зерен.
Средний диаметр может быть заранее рассчитан на отображение какого-нибудь одного определенного свойства. Характер этого свойства и вид функциональной зависимости его от гранулометрического состава определяет вид искомой формулы, которая в этом случае приобретает и физический смысл. В работе [6] для удобства обозрения формул для исчисления среднего диаметра разбиты на две категории.
В первую категорию отнесены формулы математической статистики, по которым величина среднего диаметра исчисляется с учетом данных гранулометрического анализа исследуемого материала.
Во вторую категорию отнесены формулы, по которым величина среднего диаметра определяется по значениям крайних, ограничивающих усредняемую фракцию, диаметров, без учета внутреннего грансостава, что снижает ценность усреднения и ограничивает применение формул.
Обе категории содержат значения среднего диаметра по соответствующим формулам при равномерном распределении фракций в диапазоне изменения крупности от 2 до 60 мм.
В этих формулах:
D – средний диаметр зерен всех зерен;
d1 и d2 – крайние, ограничивающие фракцию диаметра;
d =( d1+d2 ) / 2- средний диаметр i–х более или менее узких фракций (при модуле
классификации d2 / d1 = = 1,414 или более 1,414);
n – число зерен отдельных фракций (числовой выход);
γi - масса зерен в i–й фракции (массовый выход).
Для простоты вычислений, полагая, что если все зерна имеют правильную кубическую форму и равную плотность, будем иметь
n = γi /δ d3i; (3.8) γi = n δ d3i; (3.9)
V= n d3i; (3.10) S = 6 n d2i; (3.11),
а в случае шарообразной формы зерен
n = 6 γi / δ π d2i; (3.12) γi = = n δ d3i /6; (3.13)
V = = n π d3i /6; (3.14) S = n π d2i, (3.15)
где δ – плотность материала зерен;
V, S– соответственно объём и площадь поверхности зерен в отдельных фракциях;
Средний диаметр (среднемассовый) в большей степени учитывает крупные зерна, относительная масса которых большая, а поверхность мала. Диаметры, в той или иной степени учитывающие количество зерен, характеризующих в основном содержание мелких фракций с развитой поверхностью, имеют свои значения заниженными.
Анализ значений среднего диаметра различного рода усреднения показывает, что пользоваться по произволу готовыми формулами, не обосновывая их надлежащим определяющим свойством, нельзя.
Если установлено определяющее свойство, которое необходимо сохранить при усреднении, то задачу определения среднего диаметра зерна можно решить следующим образом [6].
Выбранное определяющее свойство выражают функцией f(d) переменного от фракции к фракции диаметра зерна d и той же функцией f(D) искомого среднего диаметра зерен D, который является величиной постоянной для всех фракций. Определяющее свойство при усреднении должно остаться неизменным, следовательно
f(d) = f(D) (3.16)
Например, по роду исследования выясняется, что определяющим свойством служит удельная поверхность, т.е. отношение поверхности ∑ 6 n d2i к объему ∑ n d3i то определяющая функция будет иметь вид
ƒ (d ) =∑ 6 n d2i; / ∑ n d3i. (3.17)
Исходное уравнение
∑ 6 n d2i; / ∑ n d3i = ∑ 6 n D2 /∑ n D3. (3.18)
Или, по сокращении
∑ n d2i / ∑ n d3i = 1/D. (3.19)
Отсюда величина соответствующего диаметра определится формулой
D = ∑ n d3i / ∑ n d2i =D1. (3.20)
Или по массовому выходу
D1 = ∑ γi / ∑ γi / di (3.21)
Следовательно, при определении величины удельной поверхности средний диаметр необходимо исчислять по формулам (3.20-3.21). Рассуждая аналогичным образом, можно показать, что для нахождения среднего диаметра по объему зерен, следует использовать формулу
D2 = ∑ γi · di / ∑ γi (3.22)
Средний диаметр D1 широко используется для усреднения по удельной поверхности. При этом полагают, что у зерна с эквивалентным диаметром отношение площади поверхности к объему равно средней удельной поверхности всех зерен. Однако не учитывается диапазон фракций, т.е. разность между максимальным диаметром (d)2 и минимальным диаметром зерен в каждой фракции, ее удельная плотность (химический состав).
При одинаковых диаметрах объем шара меньше объема куба, что видно из формул (3.10) и (3.14).
Считается [7], что средний диаметр D1 дает наилучшее обобщения при расчете газодинамического сопротивления полидисперсного материала, а D2 - при расчете тепло- и массообменных процессов.
Удельную поверхность зерен, отнесенную к массе и объему, можно оценить соответственно по формулам
Sмуд= 6 / δ D1 (3.23) SVуд = 6 / D1 (3.24).
Пример.
Используя данные табл. 3.1, рассчитать средние диаметры зерен смеси по формулам (3.21-3.22), удельное определяющее свойство смеси.
Таблица 3.1
Влияние грансостава аглошихты на характеристики слоя [7]
Показатели | Составы | ||||
а | б | в | г | ||
Содержание фракций по размерам, % |
| ||||
25-100 мм | 37,5 | 42,9 | 50 | 60 | |
16-25 мм | 12,5 | 14,3 | 16,7 | 20 | |
10–16 мм | 12,5 | 14,3 | 16,7 | 20 | |
6-10 мм | 12,5 | 14,3 | 16,7 | - | |
3-6 мм | 12,5 | 14,3 | - | - | |
0-3 мм | 12,5 | - | - | - | |
Насыпная плотность, кг/м3 | 1760 | 1625 | 1460 | 1420 | |
Относительная газопроницаемость, % | 38,1 | 61,2 | 79,6 | 100 | |
| |||||
Решение:
Среднеарифметический диаметр, взвешенный по поверхности зерен аглошихты «а»
D1=(37,5+12,5+12,5+12,5+12,5+12,5) / (37,5/62,5+12,5/20,5+12,5/13+12,5/4,5+12,5/1,5)=6,76 мм
Среднеарифметический диаметр, взвешенный по объему зерен аглошихты «а»
D2=(37,5 62,5+12,5 20,5+ 12,513+ 12,5 4,5+12,5 1,5) / (37,5+12,5+12,5+12,5+12,512,5)=29,38 мм.
Удельная поверхность зерен аглошихты «а», отнесенная к объему
SVуд = 6 / 6,76= 0,89 мм2.
Аналогичные вычисления выполнены и для других составов. Результаты вычисления средних диаметров приведены в табл. 3.2.
Таблица 3.2
Результаты вычислений
Составы шихт | D1 | D2 | SVуд |
а | 6,76 | 29,38 | 0,89 |
б | 13,46 | 33,39 | 0,45 |
в | 20,12 | 39,17 | 0,3 |
г | 28,82 | 44,2 | 0,21 |
Задание к работе 3
Оперируя данными табл. П.3, рассчитать средние диаметры по формулам (3.21-3.22) и удельное определяющее свойство смесей. Дать анализ влияния полидисперсности смеси на результаты вычислений.
4. ОБОГАЩЕНИЕ РУД
В природе общая концентрация железа составляет 4,2%, кислорода -49,7%, кремния -26%, алюминия -7,45%.
В России сосредоточено 24,2% мировых запасов и прогнозных ресурсов железных руд. Однако по содержанию железа в них 36% доля России составляет 14% (среднее содержание железа в рудах Бразилии составляет 58%, Австралии -62%, Индии -60%). Поэтому в нашей стране около 80% добываемых руд подвергают обогащению. При этом подземным способом добывается 7,5% руд. Считается, что месторождения железных руд отрабатывать выгодно, если запасы месторождения превышают 100 млн.т.
К общим требованиям, предъявляемым к рудам, можно отнести: высокое содержание железа и полезных примесей (Mn, Ni, V, W, Mo, V, Cr), низкое содержание вредных примесей (S, P, As, Zn, Pb), повышенное содержание основных оксидов (CaO, MgO), постоянство химического состава, высокая восстановимость и газопроницаемость (кусковатость, прочность). Важными характеристиками руд являются также их твердость, дробимость, истираемость, грансостав, влажность. Однако эти требования могут не относиться к рудам, подвергающимся обогащению и последующему окускованию, поскольку эти характеристики могут коренным образом изменяться перед проплавкой в доменной печи.
Практикой установлено, что увеличение содержания железа в доменной шихте на 1 % снижает удельный расход кокса на 0,8-1,2 % и повышает производительность доменных печей на 1,5-2,5%.
Обогащение - совокупность технологических процессов обработки руды, позволяющая удалить из нее в большей или в меньшей степени пустую породу (а иногда и вредные примеси) и вследствие этого повысить в руде содержание полезного компонента.
Из общего количества разведанных запасов железных руд России -17,4 % представлено рудами, которые могут использоваться без обогащения, 63,8 % - рудами, обогащаемыми по простым схемам, и 13,8 % -рудами, требующими сложных методов обогащения.
В результате обогащения руды получают: концентрат с преобладающим содержанием в нем рудного минерала; хвосты, состоящие в основном из пустой породы и незначительного количества полезных компонентов, извлечение которых на современном этапе технологии и техники обогащения экономически невыгодно; промежуточный продукт (промпродукт), который по содержанию рудных минералов занимает промежуточное положение между концентратом и хвостами и должен подвергаться дальнейшему обогащению.
Технология обогащения представляет собой совокупность отдельных частных процессов - подготовительных, основных и вспомогательных.
Подготовительное процессы предназначены для подготовки руды к обогащению: уменьшение крупности кусков руды, раскрытие сростков рудных и нерудных минералов и др. К этим процессам относятся дробление и измельчение руды, грохочение, классификация, магнетизирующий обжиг.
Основными являются процессы собственно обогащения руды.
Минералогический состав рудной части железных руд определяет технологию их обогащения. Методы обогащения основаны на использовании различий в физических и физико-химических свойствах разделяемых при обогащении компонентов (минералов) руды - цвете и блеске, промываемости, плотности, магнитной восприимчивости, смачиваемости поверхности и др. Различают следующие методы обогащения руд: рудоразборка, промывка, гравитационное обогащение, магнитная сепарация, обжигмагнитный способ и флотация.
Рудоразборка основана на различии в цвете (блеске) пустой породы и минералами, содержащими полезный компонент в руде.
Промывкой называется процесс обогащения руд в промывочных машинах путем размывания водой, механического разрушения, диспергирования и удаления вместе с водой песчаных и глинистых пород, входящих в состав руда.
Промывке подвергаются бурые железняки, валунчатые глинистые и песчано-глинистые руды (мартитовые, гематитовые магнитные железняки), марганцевые руды, известняки. Промывка может быть либо самостоятельным либо подготовительным процессом, после которого мытая руда направляется на обогащение другим методом.
Гравитационные методы обогащения (статические и динамические) основаны на различии плотности минералов пустой породы и минералов, содержащих полезный компонент, плотность которых в 2 раза выше.
Статические методы проводят в тяжелых суспензиях, плотность которых (около 3 г/см3) имеет промежуточное значение между плотностью пустой породы и плотностью рудных минералов. Обогащению подвергают породы крупнее 3 мм. В такой системе пустая порода всплывает, а рудные минералы тонут. Суспензии готовят из тонкоизмельченного Fe-Si (0,4-0,5 кг/т руды). Этот способ нашел применение при обогащении марганцевых и хромовых руд и в незначительном количестве красных железняков.
Динамические методы основаны на различии скоростей движения в жидкости твердых частичек различной массы. Для осуществления сепарации необходимо, чтобы самые маленькие частички окислов железа, например, имели скорость осаждения больше, чем самые большие частички пустой породы. Это достигается разделением измельченной руды на ряд фракций с определенным соотношением максимальных и минимальных частичек в каждой фракции. Обогащению подвергаются руды крупностью 3-35 мм в отсадочных машинах под воздействием вертикального потока воды переменного направления. Слой руды на решетке пронизывается потоком воды, скорость которого выше скорости падения частиц. Удаления с решета верхнего слоя хвостов происходит через сливной порог аппарата потоком воды. Отсадкой в основном обогащаются марганцевые руды и в незначительном количестве бурые и красные железняки.
Магнитное обогащение основано на использовании различий в магнитных свойствах разделяемых минералов. Преимущественно разделение осуществляется в постоянном магнитном поле. Магнитная сепарация наиболее широко применяется при обогащения магнетитовых руд и титаномагнетитов. Если принять магнитные свойства железа за 100%, то магнитные свойства Fe3O4 и FeO*TiO2 соответственно составят 40,2 и 24,7%, а Fe2O3 – 1,3%. Для обогащения руд крупностью более 6 мм применяют сухую магнитную сепарацию. Руды крупностью менее 0,1 мм обогащаются только мокрой (для лучшего разделения) магнитной сепарацией. При переработке слабомагнитных руд по комбинированным схемам магнитной сепарации подвергаются, как правило, отдельные продукты крупностью менее 3-5 мм.
Обжигмагнитный метод обогащения руд состоит из магнетизирующего обжига и магнитной сепарации в поле низкой напряженности. Этим способом обогащаются бурые, красные и шпатовые железняки. В результате магнетизирующего обжига в восстановительной среде слабомагнитные минералы железа переходят в ферромагнитные в основном в форму магнетита Fe304, иногда с последующим окислением до маггемита γ -Fe2O3. Первоначально обжиг руд производился в окислительной среде и служил для удаления серы, гидратной влаги из бурых железняков и повышения их восстановимости. В настоящее время эта задача решается при агломерации, а окислительный обжиг применяется при подготовке шпатовых железняков для разложения карбонатов и удаления серы. В последнее время все большее значение приобретает обжиг окисленных руд (красных и бурых железняков) в восстановительной среде для перевода слабомагнитной окиси железа в магнетит и последующего обогащения эффективным магнитным способом. На практике обжиг ведут при температурах 800-1000оС в присутствии СО или Н2:
3Fe2O3 + CO = 2Fe3O4 + CO2;
3Fe2O3 + H2 = 2Fe3O4 + H2O.
Такой обжиг еще называют магнетизирующим. Обжиг должен быть организован таким образом, чтобы не допустить переход Fe3O4 в FeO, обладающей слабомагнитными свойствами. При этом оптимальные параметры находят опытным путем для каждого типа руды. Для получения продукта высокого качества требуется уменьшение размера кусков руды и однородность гранулометрического состава. Обжиг богатых руд ведут при температурах выше 1000оС с целью получения металлизованного продукта DRI (direct reduced iron). Обжиг ведут в трубчатых вращающихся печах или в печах кипящего слоя. Трубчатые печи имеют длину до 60 м, диаметром 3,5-4,0 м, футерованы изнутри огнеупорным кирпичем. Скорость вращения составляет 1-2 об/мин. Благодаря наклону к горизонту (до 5о), руда крупностью 0-25 мм перемещается к разгрузочному концу. За время пребывания в печи (около 2-ух часов) из руды испаряется влага, удаляются летучие, в нижней части печи происходит восстановление до Fe3O4 (или до Feмет в случае металлизации). Основным элементом печи кипящего слоя является горизонтальный под с большим количеством отверстий. Через слой мелкой руды, помещенной на такую решетку, снизу вверх продувается горячий восстановительный газ. При достижении его определенной скорости слой руды переходит во взвешенное состояние, сыпучий материал приобретает некоторые свойства жидкости. По внешнему виду из-за взаимного перемещения частичек слой напоминает кипящую жидкость. Большая поверхность контакта твердого материала и газа обусловливает высокую интенсивность протекания химических реакций и теплообмена.
Обогащение флотацией основано на различии свойств поверхности (смачиваемости) рудного минерала и пустой порода. Обычно пустая порода гидрофильна (хорошо смачивающаяся водой) и опускается на дно, а рудный минерал гидрофобен и выносится пеной на поверхность жидкости, продуваемой воздухом. Для усиления именно таких свойств поверхности обогащаемый материал проходит сложную предварительную обработку различными веществами, так называемыми флотационными реагентами. Флотации подвергаются окисленные железные кварциты, хвосты магнитной сепарации, марганцевые концентраты и сливы промывки марганцевой руды.
Доля магнитного обогащения железных руд в нашей стране составляет около 80 %, около 15 % приходится на промывку и отсадку, остальное – на другие методы.
Вспомогательные процессы применяются для обработки продуктов, получаемых в результате обогащения. К ним относят сгущение шламов и осветление моечных вод, обезвоживание продуктов обогащения.
Результаты обогащение руд характеризуются следующими показателями: содержанием металла в исходной руде и продуктах обогащения; извлечением металла в продукты обогащения; глубиной обогащения; степенью сокращения; степенью обогащения.
Содержание металла в исходной руде α0, в концентрате βк и в хвостах ν определяют по данным химических анализов проб руды и продуктов обогащения.
1) Выход продукта (в %) представляет собою отношение массы продукта к массе исходной руды [4]:
(4.1)
Выход (в %) концентрата может быть также определен расчетным путем, составлением баланса металла:
(4.2)
Отсюда выход концентрата составит
(4.3)
А выход хвостов
(4.4)
Результаты полученных вычислений должны удовлетворять равенству:
(4.5)
2) Извлечение – показатель, обозначающий, какая часть всего количества полезного компонента, содержащегося в обогащаемой руде, перешла в концентрат или другой продукт обогащения. Извлечение выражается в процентах и вычисляется как отношение массы компонентов в данном продукте к его массе в обогащаемой руде
(4.6)
(4.7)
или
(4.8)
= 100
(
) /
(
) (4.9)
Суммарное извлечение данного компонента во все полученные конечные продукты обогащения составляет 100%
Σ Ɛi = 100% (4.10)
Извлечение полезного компонента в тот или иной продукт обогащения не является исчерпывающей оценкой эффективности этого процесса, что можно показать в следующих примерах.
1.В результате обогащения вся масса полезного компонента перешла в концентрат, т.е. ʋ = 0. Тогда извлечение полезного компонента в концентратах по выражению (4.8) составит
2.Идеальный случай. Содержание полезного компонента в концентрате максимальное, т.е. равно его содержанию в чистом ведущем рудном минерале (βк = βм). Обогащение осуществляется без потерь полезного компонента, т.е. ʋ = 0. В этом случае извлечение полезного компонента в концентрат составит
Таким образом, результаты обогащения в этих примерах характеризуются одинаковым извлечением полезного компонента в концентрат, но при этом содержание этого компонента может быть различное.
Поэтому эффективность процесса обогащения следует оценивать двумя показателями: извлечением полезного компонента в концентрат, учитывающим потери ценного компонента с хвостами, и глубиной обогащения руды, показывающей резервы для достижения максимального содержания полезного компонента в концентрате обогащения. Глубину обогащения руды можно определить из выражения [8]
G = 100 · /
, (4.11)
где βм – содержание полезного компонента в чистом рудном минерале, %.
Концентраты с высоким содержанием полезного компонента называют суперконцентратами (концентратами глубокого обогащения). Например (см.табл.П.I), концентраты глубокого обогащения Лебединского ГОКа содержит 71.7% Fe при содержании его в ведущем рудном минерале – магнитите 100 · 168 / 232 = 72,41%, т.е. G = 99%
Получение таких концентратов определяется уровнем развития технологии и техники процессов обогащения, потерями полезного компонента с хвостами и, в конечном счете, экономической эффективностью их дальнейшего передела, например, в агрегатах для получения металлизованного продукта.
Существуют и другие показатели обогащения. Степень сокращения – величина, обозначающая, во сколько раз выход полученного концентрата ɣк меньше количества перерабатываемого полезного ископаемого. Степень сокращения R выражает количество тонн руды, которое нужно переработать, что бы получить 1 тонну концентрата
R = 100 / = (
) / (
). (4.12)
Степень обогащения, или степень концентрации, К – показатель, обозначающей, во сколько раз увеличилось содержание компонента в концентрате по сравнению с его содержанием в исходной руде:
К = βк / α0 (4.13)
Пример:
При обогащении магнетитовой руды, содержащей 31% Fe (αо = 31%), получен концентрат с содержанием Fe 67,5% (βк = 67,5%) и хвосты с содержанием Fe 9,6% (ʋ = 9,6%). Определить основные технологические показатели обогащения.
Решение:
Выход концентрата
= 100 (31 - 9,6) / 67,5 - 9,6) = 37%.
Выход хвостов
== 100 (67,5 – 31) / (67,5 – 9,6) = 63%
Проверка:
к +
хв = 37 + 63 = 100%
Извлечение железа в концентрат
= 67,5 · 37 / 31 = 80,55.
Извлечение железа в хвосты (потери с хвостами)
= 9,6 · 63 / 31 = 19,5%.
Проверка: Ɛк + Ɛхв = 80,5 + 19,5 = 100%
Глубина обогащения
G = 100 · /
, = 100 ·67,5 /72,41 = 93,2%.
Степень сокращения
R = 100 / = 100 / 37 = 2,7 раза.
Степень обогащения
R = 100 / = 67,5 / 31 = 2,2 раза.
Задание к работе 4
Определить возможный способ обогащения руды, химический состав которой представлен в табл. П.I. Определить показатели обогащения, используя результаты выполненной работы I и данные табл. П.4. В случае изменения в процессе обогащения минералогического типа руды за βм принимать содержание материала в ведущем минерале концентрата.
5. ОЦЕНКА ОДНОГОДНОСТИ СЫРЫХ МАТЕРИАЛОВ
Для того, чтобы не допустить чрезмерного похолодания печи при внезапных колебаниях химического состава шихты, доменный процесс ведут обычно с резервом тепла, перерасходуя кокс.
Усреднение имеет целью снижение флуктуации химического состава и физических свойств, загружаемых в доменную печь материалов, т.е. стабилизацию их количества, с тем, что бы уменьшить колебания нагрева доменной печи, обеспечить ровность ее хода и, тем самым, повысить ее производительность, снизить удельный расход кокса на выплавку чугуна и улучшить его качество.
Установлено, что при снижении колебаний железа в шихте от ± 1,0 до ± 0,5% производительность доменных печей повышается на 2,5%, а удельный расход кокса снижается на 1% [7].
Усреднение руды ведется на всех этапах ее переработки, начиная от карьера и кончая бункерами доменного цеха.
Наилучшие результаты достигаются при усреднении на специальных складах. Для осуществления хорошего усреднения на каждом складе должно быть два штабеля, один из которых формируется, а другой выбирается.
Оценка стабильности химического состава материалов ведется, как правило, по изменению содержания железа, кремнезема и индекса основности.
Методы оценки однородности материалов основаны на закономерностях математической статистики. Исходными данными для анализа являются разовые пробы.
Для аналитической характеристики однородности используется ряд показателей.
В основе большинства методик оценки однородности материала лежит определение среднего квадратического отклонения [8].
σ = (5.1)
где Хср – среднеарифметическое содержание контролируемого компонента в материале, %;
Хi – содержание данного компонента в разовых пробах, %;
n – число разовых проб.
Коэффициент вариации
η = (5.2)
обычно используют в тех случаях, когда одновременно с усреднением идут другие процессы, в результате которых изменяется абсолютное значение контролируемого параметра (например, при обогащении или обжиге руд).
Среднее абсолютное отклонение
ΔХср = (5.3)
характеризует наиболее вероятно-возможное отклонение от средней концентрации в ту или другую сторону.
Коэффициент однородности
Ко = (5.4)
представляющий отношение среднего минимального значения к среднему максимальному, при увеличении однородности материала приближается к I.
Эффективность работы усреднительных сооружений оценивают сравнением показателей однородности материала до и после усреднения и коэффициентом усреднения:
;
;
;
; (5.5)
где σ, ΔХср, η, Ко - показатели однородности до усреднения;
σ,’ ΔХ’ср, η’, Ко’ - то же после усреднения.
Качество усреднения оценивают значениями показателей однородности материала, а коэффициент усреднения показывает лишь степень выравнивания контролируемого параметра.
Пример:
Определить показатели усреднения руды по 14 пробам (табл. 5.1.)
Таблица 5.1
Содержание железа в пробах до и после усреднения
Номер пробы | Содержание железа, % | |
До усреднения | После усреднения | |
1 | 50,6 | 50,1 |
2 | 50,6 | 49,9 |
3 | 50,7 | 50,3 |
4 | 50,2 | 50,2 |
5 | 50,1 | 50,0 |
6 | 50,2 | 50,1 |
7 | 49,8 | 50,2 |
8 | 50,0 | 50,2 |
9 | 49,9 | 50,1 |
10 | 50,3 | 50,2 |
11 | 49,6 | 50,3 |
12 | 49,9 | 50,3 |
13 | 50,0 | 50,2 |
14 | 50,3 | 50,2 |
Решение:
Оценки однородности Оценки однородности
До усреднения После усреднения
1.Хср = = 50,17%; Х’ср = 50,16%
2.∆Хср = =
= 0.22% ∆Х’ср =
= 0,09%
3.σ = =
= 0,29 σ’ =
= 0,1
4.η = =
= 0,0058 η’=
= 0,002
5.Ко = =
= 0,99 К’о =
= 0,996
Коэффициенты усреднения
=
= 2,9;
=
= 2,44
=
= 2,9
=
= 0,99
Для графической характеристики однородности материала сгруппируем данные по количеству случаев, укладывающихся в выбранные пределы значений (табл.5.2).
Таблица 5.2
Распределение железа в пробах с учетом пределов его колебаний
Диапазон колебаний, % | Число случаев | |
До усреднения | После усреднения | |
![]() ![]() | 4/28,57* 3/21,43 4/28,57 - 3/21,43 | 1/7,15 4/28,57 9/64,28 - - |
*-в числителе – шт., в знаменателе - %.
В случае совпадения значения параметра с границей диапазона его колебания значение этого параметра заносят в интервалах, начало которого совпадает с этим значением. Например, значение параметра, равное 50%, следует занести в диапазон 50-50,2%.
Полученные результаты группировки представлены на рис. 5.1 в виде кривых распределения, с помощью которых можно построить графики, характеризующие количество случаев, укладывающихся в заданные пределы колебаний от среднего (рис. 5.2). для построения таких графиков составим табл. 5.3.
Таблица 5.3
Колебания содержания железа в пробах, %
Количество проб |
Хср | Пределы колебаний | |||
![]() | ![]() | ![]() | ![]() | ||
До усреднения После усреднения | 50,16 50,17 | 42,86 85,71 | 64,29 100 | 78,57 100 | 100 100 |
Чем однороднее материал, тем выше пик кривой распределения и уже интервал ее существования (см.рис.5.1-5.2).
Рис. 5.1. Частотные кривые распределения железа в руде: а –до усреднения; б –после усреднения.
Рис. 5.2. Укладка случаев в заданные пределы колебаний от среднего содержания железа до (1) и после (2) усреднения.
Задание к работе 5.
Найти аналитические характеристики однородности материалов по данным табл.П.5. Дать графическую интерпретацию однородности материалов до и после усреднения.
6. МЕТАЛЛУРГИЧЕСКАЯ ОЦЕНКА СЫРЫХ МАТЕРИАЛОВ
Металлургическая оценка сырых материалов производится с целью разработки правильных технологических решений для достижения наилучших технико-экономических показателей работы доменных печей и других металлургических агрегатов на конкретной сырьевой базе.
Сырые материалы оцениваются с целью установления выплавки из них возможной марки чугуна по количеству фосфора и марганца, вносимых сырыми материалами, поскольку эти элементы ведут себя определенно в доменной плавке и нельзя получить в чугуне содержание их ниже того, которое определяется количеством этих элементов в рудной сыпи и других материалах, т.е. технологический персонал вынужден выплавлять ту марку чугуна, которая определяется содержанием в шихте фосфора и марганца [1].
В условиях доменной плавки при выплавке передельных чугунов фосфор полностью переходит в чугун, в то время как коэффициент использования марганца ηMn составляет 0,55-0,75.
Поступление этих элементов можно оценить по ориентировочному расходу сырых материалов на выплавку 1 т чугуна.
Для определения расхода рудной сыпи на выплавку 1 т чугуна необходимо учесть количество железа, вносимого в чугун сырыми материалами, расход которых известен, и задаться содержанием железа в чугуне.
Учитывая вышеизложенное, расход рудной сыпи составит
Рс=100 (930- Q · FeА/100-М · Feм/100) / Feр (6.1)
где Рс - расход рудной сыпи на выплавку 1 т чугуна, кг;
Feр - содержание железа в рудной сыпи, %;
930 - ориентировочное количество железа в 1 т чугуна, кг;
Q - количество золы, вносимой коксом, кг;
FeА -содержание железа в золе кокса, %;
M - расход металлодобавок на выплавку 1 т чугуна, кг;
Feм -содержание железа в металлодобавках, %.
Количество золы, вносимой коксом, на 1 т чугуна можно определить из выражения
Q = K А (100-Wр) / 100, (6.2)
где K - расход влажного кокса на выплавку 1 т чугуна, кг;
Wр- содержание влаги в коксе, %;
A -содержание золы в коксе, %.
Содержание марганца или фосфора в чугуне без учета незначительного количества их, вносимого флюсами, золой коксика (в случае использование агломерата или рудно-топливных окатышей), составит
[x] =100 ηX (Рс · хP/100+Q· хA/100+M · xM/100) / 1000, (6.3)
где хP , хA , xM - содержание соответственного элемента в рудной сыпи, золе кокса и металлодобавках, %;
ηX - коэффициент перехода в чугун соответствующего элемента (ηMn =0,55-0,75; ηP =1), ед.
По содержанию фосфора и марганца в чугуне в соответствии с ГОСТ 4832-80, ГОСТ 805-80 (табл.П.6-П.9) выбирают марку чугуна, которую можно выплавить из исходных материалов.
Качество железной руды определяется не только содержанием железа, но и составом пустой породы, содержанием вредных и полезных примесей. Измерения показывают, что наиболее жидкоподвижным являются шлак, содержащий 10-15% Al2O3. Такому содержанию Al2O3 в шлаке соответствует отношение SiO2 / Al2O3 в руде, равное 3-4. При более низком отношении образуется шлак с повышенной концентрацией Al2O3, обладающей значительной вязкостью. Для выпуска подобных шлаков из доменной печи необходим их перегрев, следствием которого является перерасход кокса.
Значительно повышает вязкость доменных шлаков чрезмерно высокое содержание магнезии в пустой породе руды. Для необходимой обессеривающей способности шлака при выводе из шихты марганцевой руды содержания MgO в шлаке повышают до 7-12% в зависимости от конкретных условий.
Для снижения температуры плавления пустой породы шихтовых материалов и получения доменного шлака необходимого состава и физических свойств, обеспечиваюoих очистку чугуна от серы и нормальную работу печи, в доменную шихту и шихту для окускования руд или металлизации вводят флюсы.
Металлургическая ценность руд возрастает с увеличением в пустой породе отношения CaO / SiO2, так как при этом снижается потребность в соответствующем флюсе. В результате уменьшается выход шлака, пропорционально сокращается удельный расход кокса и увеличивается производительность доменной печи. При оценке состава пустой породы руд следует иметь в виду, что при обогащении некоторых из них отношение CaO / SiO2 или SiO2 / Al2O3 изменяется.
В зависимости от состава пустой породы рудных материалов используют основные, кислые или глиноземистые флюсы.
Кислые флюсы применяют редко. В большинстве случаев кислые флюсы используют из-за высокого содержания Al2O3 в руде, т.е с целью снижения содержания его в шлаке до допустимых пределов. В качестве такого флюса используется бедная железная руда с кремнистой пустой породой или кварциты.
Применение глиноземистых флюсов еще реже. Чистым видом такого флюса являются бокситы. В доменной плавке обычно применяют железные руды с глиноземистой пустой породой, когда необходимо повысить содержание глинозема в шлаке.
Чугун выплавляют из железных руд преимущественно с кислой пустой породой, поэтому чаще используют основные флюсы: известняк или доломитизированный известняк. Известняк представляет природную форму минерала кальцита – CaCO3. Чистый кальцит содержит 56% CaO и 44% CO2. В природном известняке всегда присутствуют кремнезем SiO2 и глинозем Al2O3 , которые не только уменьшают в нем содержание оснований до 50-54%, но и требуют их на свое ошлакование. Поэтому известняк, прежде всего, оценивают по его флюсующей способности, показывающей содержание в нем «свободных» оснований, которые могут участвовать в ошлаковании пустой породы железорудных материалов и золы кокса.
Флюсующую способность известняка (или доломитизированного известняка, отличающегося повышенным по сравнению с известняком содержанием MgO) определяют по уравнению
Физв = ROизв – Rизв b, (6.4)
где RОизв - содержание в известняке основных оксидов, %;
R- содержание в известняке кислых оксидов, %;
b- индекс основности шлака, ед.
Произведение Rизв*b показывает потребность в основных оксидах на ошлакование кислых оксидов известняка.
Основность шлака может выражаться одним из следующих соотношений основных и кислых оксидов в нем
b = CaO / SiO2, (6.5)
b = (CaO+MgO) / (SiO2+Al2O3), (6.6)
b = (CaO+MgO) / SiO2, (6.7)
В соответствии с выражением индекса основности шлака в уравнение (6.4) подставляют значения ROизв и Rизв b.
Анализ выражения (6.4) показывает, что флюсующая способность одного и того же известняка не является постоянной величиной, так как она зависит не только от химического состава известняка, но и от основности шлака, которая может целенаправленно изменяться технологами-металлургами. Например, увеличиваться или уменьшаться в соответствии с повышением или уменьшением содержания серы в шихте.
Основным поставщиком серы в доменную печь является кокс, даже в случае возможно низкого содержания серы в нем. Это видно из следующего примера.
Пусть удельный расход сухого кокса составляет 350 кг/т чугуна, а расход рудной сыпи, состоящей из агломерата, 1400 кг/т чугуна. Пусть содержание серы в коксе составляет 0,5%, т.е. вблизи минимально достигаемого в настоящее время, а в агломерате – 0,03%.
Поступление серы в процесс из кокса составит
350 · 0,5/100 = 1,75 кг/т чугуна,
из рудной сыпи 1400 · 0,03/100 = 0,42 кг/т чугуна.
То есть, несмотря на то, что расход рудной сыпи выше расхода кокса в 3,5 раза, она вносит в доменную печь в 2,1 раза меньше серы. Поэтому основность шлака главным образом зависит от содержания серы в коксе.
Понижение содержания серы в коксе уменьшает потребность в CaO на перевод серы из чугуна в шлак в виде CaS, что предоставляет возможность в этом случае уменьшать основность шлака, а отсюда и расход известняка на выплавку чугуна.
В этой связи для обеспечения достаточной обессеривающей способности шлака при плавке на коксе из донецких углей, содержащем до 1,7-1,8% серы, основность шлака по отношению CaO / SiO2 поддерживают в пределах 1,17-1,3. Использование кокса из кузнецких углей, содержащего серы в пределах 0,4-0,65%, позволяет успешно вести плавку на шлаках с основностью b = 0,85-1,15. Установлено, что снижение содержание серы в коксе на 0,1% дает возможность увеличить производительность печей на 0,8-1,5% и снизить удельный расход кокса на 1-1,5% [9].
Современный доменный процесс характеризуется уменьшением числа компонентов доменной шихты, что обеспечивается развитием процессов окускования мелкой богатой руды и железорудных концентратов и различного рода добавок, в том числе и флюсов, используемых в доменной плавке.
Вывод 100 кг сырого известняка из доменной шихты приводит к росту производительности печей на 3-5% и экономии кокса на 20-30 кг/т чугуна [9].
В случае получения агломерата расход известняка (И) на выплавку 1 т чугуна может быть определен через индекс основности доменного шлака согласно выражению
И = [Pc (SiO2р·b-CaOр) + Q (SiO2·b-CaOк) + q (SiO2q·b-CaOq)] / Физв (6.8)
где q- количество золы коксовой мелочи, приходящейся на 1 т чугуна (при использовании окатышей этого члена может не быть);
SiO2р,-CaOр- содержание соответствующих соединений в рудной сыпи, %;
SiO2к,-CaOк - то же в золе кокса, %;
SiO2q,-CaOq- то же, в золе коксовой мелочи (твердого топлива) в случае использования агломерата или рудно-топливных окатышей, %.
Таким образом, под металлургической ценностью железной руды понимают совокупность ее металлургических свойств и качеств, которая определяет технико-экономические показатели доменной плавки или другого металлургического процесса.
При полной оценке железной руды учитывают также ее кусковатость, прочность, пористость, восстановимость, географическое расположение месторождения, его размеры и глубину залегания рудного тела. Однако в настоящее время кусковатость, пористость и восстановимость руд утрачивают былое значение, поскольку почти все руды подвергаются обогащению и последующему окускованию, в результате которых эти свойства коренным образом могут меняться. Зато более важными характеристиками становятся прочность, определяющая расход энергии на дробление и измельчение, и способность руд к обогащению.
Пример
Найти расход материалов на выплавку 1 т чугуна, используя данные табл. 6.1. и результаты расчетов в примере раздела 1 настоящего пособия. Выбрать марку чугуна, которую можно выплавить из заданных материалов.
Таблица 6.1
Исходные данные для расчета
Материал | Расход, кг/т чугуна | Содержание в материале, % | Неполный химический состав золы, известняка, % | |||||||
влаги | золы | Fe | P | Mn | C* | S* | CaO | SiO2 | ||
Кокс | 400
- - | 3,8
11,0 - | 10,5
15,3 - | 8,3
9,7 0,008 | 0,001
- - | 0,1
- - | -
80,5 - | 0,55
0,8 0,001 | 0,9
0,8 53,2 | 49,7
49,9 1,5 |
Коксовая мелочь | ||||||||||
Известняк |
* Содержание серы и углерода приведено из данных технического анализа на сухую массу
Решение
Ориентировочный расход концентрата на выплавку 1 т чугуна составит согласно выражениям (6.1) и (6.2)
Рс = 100 [(930-К (100-WР) А FeA / 1000000] / Feр = 100 [930-400(100-3,8) 10,5 8,3 / 1000000] / 55,31= 1675 кг.
Содержание марганца и фосфора в чугуне согласно выражению (6.3) соответственно составит
[Mn] = 0,6 ·100 (1675 ·0,43 /100 + 40,404· 0,1 / 100) / 1000 = 0,435 %,
[P] = 1 ·100 (1675· 0,044 / 100 + 40,404 ·0,001 / 100) / 1000 = 0,072 %.
В соответствии с данными таблицы П.6 из концентрата можно выплавить чугун, химический состав которого представлен в таблице 6.2.
Таблица 6.2
Химический состав чугуна, %
Марга чугуна по ГОСТ 805-80 | Si | Mn | P | S | C | Fe |
П1(группа 1, класс А, категория П) | 0,51-0,9 | ≤0,5 | ≤0,1 | ≤0,02 | 3,8-4,8 | до 100 |
Принято | 0,8 | 0,44 | 0,08 | 0,02 | 4,5 | 94,16 |
Исходя из содержания серы в коксе, принимаем индекс основности доменного шлака 0,9 по отношению CaO/SiO2 Тогда флюсующая способность известняка составит
Физв = 53,2 – 0,9 ·1,5 =51,85 %.
Поскольку содержание углерода в аглошихте составляет 4 %, расход коксовой мелочи ориентировочно составит
1675* 4 / (80,5 -4)= 87,6 кг/т чугуна,
где 80,5 – содержание углерода в коксовой мелочи (см. табл. 6.1),%.
В коксовой мелочи содержится золы
q = 87,6* 15,3 / 100 = 13,4 кг/т чугуна.
где 15,3 – содержание золы в коксовой мелочи (см. табл. 6.1),%.
Согласно выражению (6.8) ориентировочный расход известняка составит
И = [1675*(9,36·0,9 - 5,96) + 40,404*(48,7 ·0,9 – 0,9) + 13,4*(49,9 – 0,8)] / 51,85 = 125,2 кг/т чугуна.
Дополнительный расход коксика на известняк составит
125,2 ·4 /(80,5 – 4) = 6,5 кг.
Дополнительный расход известняка на ошлакование золы дополнительного расхода коксика составит
Ид = 6,5 *15,3 *(49,9 *0,9 – 0,8) / 100*·51,85 = 0,84 кг.
Таким образом, расход сухих материалов на выплавку 1 т чугуна составит ориентировочно: концентрата – 1675 кг, известняка – 126,04 кг, кокса – 384,8 кг, коксовой мелочи ~ 94,1 кг.
Задание к работе 6
Из концентрата, представленного в таблице П.1 (см. результаты работы 1), и других сырых материалов, представленных в таблице П.10. выплавляется чугун. Выбрать марку чугуна, которую можно выплавить. Из исходных материалов производится офлюсованный агломерат. Найти расходы материалов на выплавку 1.т чугуна.
7. ОКУСКОВАНИЕ РУД
Железорудные концентраты, руды мельче 5 мм и такие железосодержащие материалы, как колошниковая пыль, окалина, циритные огарки и др., непригодны для непосредственного использования в доменной печи из-за малых размеров частичек. Для обеспечения необходимой газопроницаемости столба доменной шихты они должны быть предварительно превращены в кусковой материал с размером зерен не менее 5-10 мм. Уменьшение количества мелочи (0-5 мм) в агломерате, например, на 1 % дает 0,4 – 0,7 % экономии кокса и 0,4 – 0,7% прироста производительности доменных печей [9]. Существуют следующие способы окускования:
-агломерация (1887 г, Англия, Ф. Геберлейн и Т. Хантингтон);
-получение окатышей, как правило, окисленных (1912 г., Швеция, А. Андерсен);
-брикетирование - получение брикетов экструзией либо с использованием пресс-машин-валков (1911 г., Грендаль).
Выбор способа окускования определяется конкретной ситуацией в том или ином регионе: емкостью рынка потребления продукции металлургического производства, удаленностью месторождений руд от металлургических предприятий, наличием энергетических и трудовых ресурсов, инфраструктуры. В связи с постоянным ростом доли руды, подвергающейся обогащению, в металлургический передел вовлекается железорудное сырье, содержащее значительное количество фракций мельче 0,05-0,07 мм. При агломерации такого сырья резко падает скорость спекания и производительность агломашин из-за снижения газопроницаемости спекаемого слоя. Как правило, в настоящее время горно-обогатительные предприятия находятся на значительном расстоянии от металлургических предприятий. Транспортировать концентраты обогащения на далекие расстояния невыгодно из-за издержек, связанных с перевозкой влаги и затруднений из-за смерзания концентрата в зимнее время (возникают затраты, связанные с размораживанием сырья). Производство же агломерата непосредственно на горно-обогатительных предприятиях нецелесообразно из-за его недостаточной прочности. Удачным решением проблемы является производство окатышей. Окатыши не теряют прочности при хранении, транспортировке и перегрузках. Брикетирование не нашло широкого применения в черной металлургии из-за низкой производительности соответствующих агрегатов для производства брикетов и высокой стоимости последних
Агломерации могут подвергаться сырые материалы крупностью 0-8 мм. Основными компонентами агломерационной шихты являются: железорудное сырье (концентрат, аглоруда), возврат (некондиционный по крупности агломерат) -20-40%, коксовая мелочь -4 - 6%, флюсующие добавки (известняк, известь, доломитизированный известняк) -10%, добавки (окалина, колошниковая пыль и др.) -5%. Крупность коксовой мелочи и флюсов составляет 0-3 мм, остальных компонентов – не более 8-10 мм. В зависимости от минералогического типа спекаемого железорудного сырья влажность шихты находится в пределах от 7 до 12%, а содержание в ней углерода от 4,0 до 8,0%. С целью интенсификации агломерационного процесса используют предварительный нагрев шихты перед зажиганием, введение извести в аглошихту, накатывание твердого топлива на предварительно окомкованную шихту, обогащение кислородом воздуха, просасываемого через спекаемый слой, вывод из топлива класса менее 0,5 мм.
Высоким газодинамическим сопротивлением в спекаемом слое обладает зона переувлажнения за счет размывания в процессе конденсации паров воды комочков шихты, сминания этой части спекаемого слоя. Переувлажнение усиливается с возрастанием исходной влажности шихты и понижением ее начальной температуры. Если переувлажнение за счет содержания исходной влажности ограничено, то любой подогрев исходной шихты снижает негативное влияние на газопроницаемость спекаемого слоя зоны переувлажнения (1949 г., В.В.Виноградов). Максимальный эффект достигается подогревом шихты до температуры точки росы (50-70оС), когда пары воды проходят транзитом через спекаемый слой, не конденсируясь. Подогрев осуществляют горячим возвратом или известью, паром (в смесителях, окомкователях), сжиганием газа в окомкователях. В зависимости от минералогического типа спекаемого железорудного сырья, содержания в шихте тонких концентратов предварительный подогрев шихты может дать прирост производительности агломашин от 10 до 70%.
Аглопроцесс существенно интенсифицируется накатыванием части топлива в конце окомкования. При этом частички топлива располагаются на поверхности комочков шихты, ускоряется горение топлива, увеличивается скорость спекания. Наилучшие результаты достигаются при накатывании 70-80% топлива: прирост производительности агломашин на НЛМК составил 8%, прочность агломерата улучшилась на 6-8% при сокращении расхода коксовой мелочи на 6%. При одновременном накатывании топлива и извести производительность аглоустановки увеличивается на 15-20%, а прочность – на 9-10%.
Использование извести при производстве офлюсованного агломерата значительно увеличивает производительность агломашин за счет роста скорости спекания и выхода годного продукта. Скорость спекания увеличивается за счет улучшения газодинамических характеристик всего спекаемого слоя. При увлажнении шихты идет гидратация извести с выделением тепла
СаО + Н2О = Са(ОН)2.
Са(ОН)2, как связующее, благоприятно влияет на газопроницаемость исходной шиты, а выделяющееся при гидратации тепло снижает количество конденсирующихся паров, уменьшая негативное влияние зоны переувлажнения на газопроницаемость спекаемого слоя шихты. Выходящая из зоны горения СО2 может участвовать во вторичной карбонизации СаО
Са(ОН)2 + СО2 = СаСО3 + Н2О.
Образованный вторично СаСО3, являясь цементирующим веществом, способствует упрочнению комочков шихты, пребывающих в зонах сушки и интенсивного подогрева спекаемого слоя, снижая, тем самым, газодинамическое сопротивление этих зон.
Каждый процент кислорода в пределах от 21 до 95% в просасываемом через спекаемый слой воздухе увеличивает производительность агломашин на 1-2% за счет роста скорости спекания (горения углерода).
По данным Е.Ф.Вегмана частички топлива мельче 0,5 мм сгорают слишком быстро и не могут создавать вокруг себя блоков агломерата. Обладая повышенной реакционной способностью, такие частицы топлива воспламеняются при более низкой температуре, расширяя зону высоких температур, не обеспечивающих достаточного количества расплава для образования прочного агломерата, но снижающих газопроницаемость спекаемого слоя. Снижение содержания в топливе класса менее 0,5 мм на 1%, повышает производительность агломашин на 1-2% при росте прочности агломерата. Для снижения содержания этого класса в твердом топливе следует отсеивать фракцию 0-3 мм перед дроблением во избежание переизмельчения всей массы топлива.
Известно, что агломерат теряет прочность в период его охлаждения под воздействием напряжений, обусловленных значительным градиентом температур в куске (термические напряжения), существенным различием коэффициентов термического расширения отдельных фаз (структурные напряжения), протеканием в офлюсованном агломерате полиморфного превращения β2СаО*SiO2 в γ2СаО*SiO2, идущего при 675оС с увеличением объема на 11% (фазовые превращении). Для повышения прочности агломерата используют следующие приемы: спекание шихты в высоком слое (450-500 мм и выше); двухслойное спекание с различным содержанием углерода; спекание агломерата с различной основностью; использование доломитизированного известняка вместо части обычного известняка;.термическая обработка – повторный нагрев агломерата газовыми горелками (1100-1150оС) над хвостовой частью агломашины, снижение крупности известняка; стабилизация прочности агломерата.
С повышением высоты спекаемого слоя усиливается регенерация тепла по мере перемещения зоны формирования агломерата вниз. Увеличивается время воздействия высоких температур на спекаемый материал, благодаря чему получается хорошо раскристаллизованная структура агломерата с небольшим количеством стекла (5%), ослабляется действие факторов, ведущих к возникновению внутренних напряжений и появлению микротрещин. Чем выше спекаемы слой, тем меньше оказывается доля малопрочного агломерата верхней части слоя. При увеличении слоя с 250 до 500 мм выход годного агломерата растет с 62,5 до 84,%.
Для достижения максимальной производительности и исключения перегрева нижних слоев агломерата необходимо, чтобы шихта по высоте имела переменное содержание углерода (предложение Х.Г.Торульфа, 1911 г). По этому методу на агломашину укладывают двумя питателями две шихты, из которых нижняя содержит на 1-1,5% коксовой мелочи меньше, чем верхняя. Такая технология позволяет экономить 10% коксовой мелочи при улучшении прочности агломерата.
Спекание агломерата с основностью менее 0,4-0,5 и более 1,3-1,5 снижает содержание в агломерате 2СаО*SiO2, , а, следовательно, устраняет влияние его негативного фазового превращения.
В 1940 г Н.М.Якубцинер (ММК) установил, что на прочность агломерата благоприятно влияет добавки в шихту доломитизированного известняка В процессе кристаллизации MgO входит в решетку ларнита (2СаО*SiO2) и предотвращает, таким образом, его полиморфное превращение. Ввод в агломерат 3% MgO снижает выход мелочи с 22-25 до 17-20% после испытания в барабане. Ограничением является содержание MgO в доменных шлаках (не более 10-12%). Превышение этого предела приводит к образованию «коротких» шлаков (резко теряющих свою подвижность при снижении их температуры).
Снижение крупности известняка способствует полному усвоению СаО расплавом, что, в свою очередь, устраняет гидратирование извести влагой воздуха, сопровождающееся увеличением объема и разрушением агломерата.
Современная технология обработки агломерата способствует стабилизации его прочности и гранулометрического состава (дробление агломерата с отсевом горячего возврата, охлаждение агломерата в специальных агрегатах с последующим отсевом мелочи, отсев мелочи менее 5 мм перед загрузкой в доменные печи). В процессе отмеченных операций идет реализация трещин, возникших за счет внутренних напряжений, в результате достигается стабилизация прочностных и гранулометрических характеристик агломерата.
Нехватку регенерируемого тепла в верхней части спекаемого слоя можно компенсировать повторным нагревом (термической обработкой) газовыми горелками агломерата в хвостовой части агломашины либо подачей нагретого в кауперах воздуха на 1/3 части по длине агломашины. С той целью устанавливают удлиненные зажигательные горны. Такие технологии способствуют раскристаллизации стекла, снижают внутренние напряжения.
Окатыши же можно получить только из материалов мельче 0,1 мм. Схемы получения окатышей представляют собой комбинацию двух этапов путем окомкования влажной шихты в специальных аппаратах и упрочнения их (обжиговым или безобжиговым способами) для придания окатышам прочности, необходимой для хранения, транспортировки к металлургическим агрегатам. Сырые окатыши получают в барабанных или чашевых (тарельчатых) грануляторах. Легко комкующиеся материалы гранулируются в чашевых грануляторах, трудно комкующиеся шихты окомковываются в барабанных окомкователях. Сырые окатыши должны выдерживать, не разрушаясь, не менее 15 сбрасываний с высоты 300 мм и сопротивляться раздавливанию под нагрузкой 45-55Н для окатышей диаметром 25 мм и 9Н для окатышей диаметром 9,5 мм. В основном упрочнение окатышей производят обжиговым способом. Для этого используют конвейерные машины, шахтные печи и комбинированные установки типа «решетка-трубчатая печь». Наиболее распространенным агрегатом для упрочнения окатышей является конвейерная машина, состоящая из следующих зон: сушки (одна или две секции), подогрева, обжига (от одной до трех секций), рекуперации, охлаждения (одна или две секции). Процесс упрочнения окатышей идет за счет спекания частиц, самопроизвольным процессом приближения дисперсной системы к равновесию. К причинам отклонения от равновесия, кроме избыточной поверхностной энергии, относится наличие микродефектов (пор), концентрационной неоднородности, микродефектов кристаллической решетки. При обжиге идет высокотемпературное спекание в двух режимах: с отсутствием жидкой фазы (твердофазное спекание) и при наличии расплава (жидкофазное спекание). Для достижения теоретической плотности окатыша необходимо 25-50% (объемн.) расплава. Практика показывает, что наилучшие свойства окатышей соответствуют 12-20% расплава. Предполагая, что в расплаве образуются силикаты железа по реакции
2Fe3O4 + 3SiO2 = 3Fe2SiO4 + O2,
Получаем, что для получения 12-14% расплава необходимо с учетом других соединений пустой породы 3,5-4,0% SiO2. Эти значения могут служить ориентиром для выбора глубины обогащения железных руд.
В ходе агломерации и обжига окатышей происходит выгорание сульфидной серы шихты. Пирит FeS2 и пирротин FeS начинают окисляться с 250-280оС по реакциям:
4FeS2 + 11О2 = 2Fe2O3 + 8SO2;
4FeS + 7O2 = 2Fe2O3 + 4SO2.
Выше 1383оС в воздушной атмосфере гематит диссоциирует с образованием магнетита:
3FeS2 + 8O2 = Fe3O4 + 6SO2;
3FeS + 5O2 = Fe3O4 + 3SO2.
Степень удаления сульфидной серы может достигать 95-99%. Поскольку при окислении сульфидной серы выделяется значительное количество тепла, 1 кг пирита в шихте по теплотворной способности заменяет 0,3 кг коксовой мелочи.
Удалению сульфидной серы способствует окислительная атмосфера, умеренные температуры (низкий расход коксика), а также снижение крупности компонентов, содержащих серу. Окускование офлюсованных шихт снижает степень удаления серы до 85-90%, так как Ca связывает серу в CaS.
Сульфатная сера гипса (CaSO4*2H2O), барита (BaSO4) удаляется всего на 60-70%, так как диссоциация сульфатов требует длительного воздействия высоких температур (>1000оС). Поэтому для удаления сульфатной серы требуются повышенные расходы коксовой мелочи.
Для промышленного производства агломерата и окатышей обычно используются конвейерные машины, отличающиеся высокой производительностью, которую можно определить по одному из следующих выражений.
П = 60 В Н V γ Г, (7.1)
П = 60 S C γ Г, (7.2)
где В – ширина машины, м;
Н – высота слоя шихты (окатышей), м;
V – скорость передвижения паллет, м/мин;
γ – насыпная плотность шихты (окатышей), т/м3;
Г – относительный выход годного продукта окускования из шихты, доли ед.;
S – рабочая площадь машины, м2;
С – вертикальная скорость спекания (обжига), м/мин.
Во время термической обработки шихты идут процессы разложения карбонатов, диссоциации оксидов железа, получают развитие окислительных либо восстановительных процессов в зависимости от минералогического типа железорудного сырья.
Для определения температуры начала разложения карбоната кальция можно воспользоваться следующей формулой [11]:
T = 906858,75 / (763,99 - lg РСО2), (7.3)
а для определения температуры начала диссоциации гематита
Т = 3120810 / (1813,7 - lg РО2)), (7,4)
где РСО2 и РО2 - соответственно парциальное давление СО2 и О2, кПа;
Т – температура, К.
Пример
Окатыши из концентрата (см. пример раздела 1 настоящего пособия) обжигаются на конвейерной машине шириной 4 м. Скорость передвижения обжиговых тележек 1,5 м/мин. Выход годного продукта 85%. Расход известняка определен ранее (см. пример раздела 6). В качестве добавки используется бентонит в количестве 1,0% (5% Fe2O3, остальное - пустая порода). Готовые окатыши содержат 3% FeO и 0,02% S. Окатыши обжигаются продуктами горения природного газа (СН4 – 100%) с коэффициентом избытка воздуха α = 1,5. Давление в слое 100 кПа. Подсосами пренебречь. Н = 0,4 м.
Определить производительность обжиговой машины, содержание железа в окатышах, температуру начала диссоциации карбоната кальция и гематита, расход воздуха на сжигание 1 м3 природного газа
Решение
1.Производительность обжиговой машины согласно выражению (7.1) составит
П = 60 В Н V γ Г = 60 ·4 ·0,4 ·1,5 ·2 ·0,85 = 244,8 т/ч.
2.Для определения содержания железа в окатышах расчет будем вести на 100 кг концентрата [11].
Приход железа из концентрата – 55,3 кг;
из 1 кг бентонита (с пересчетом из Fe2O3 на Fe)
0,05 ·112 / 160 = 0,035 кг.
Всего железа в окатышах
55,3 + 0,035 = 55,335 кг.
К 100 кг концентрата добавляется
бентонита – 1 кг;
известняка после удаления СО2 остается
100 ·126,04 (53,2 + 1,5) / 100 ·1675 = 4,1 кг;
при окислении закиси железа (со снижением ее с 21,37 до 3%)
2FeO + 0,5O2 = Fe2O3, на каждый килограмм из окисляющейся FeO добавляется 16 / 144 = 0,111 кг кислорода; добавится кислорода всего
(21,37 – 3) 0,111 = 2,04 кг.
Удаляется серы
1,27 – 0,02 = 1,25 кг.
Итого получается окатышей
100 +1 + 4,1 + 2,04 - 1,25 = 105,89 кг.
Содержание железа в офлюсованных окатышах составит
100 ·55,335 / 105,89 = 52,26 %.
В расчете ради простоты вычислений принят ряд допущений (расход известняка вычислен с учетом золы коксовой мелочи, не учитывается железо, вносимое золой коксика и известняком и т.д.), которые не дают большой погрешности.
3.Реакцию горения природного газа при сжигании его атмосферным сухим воздухом можно записать следующим образом:
CH4 + 1,5 ·2 O2 + 1,5 ·2 ·3,762 N2 = CO2 + 2 H2O + O2 + 11,286 N2.
В продуктах горения содержатся молей газа
1 + 2 + 1 + 11,286 = 15, 286.
Доля СО2 в них
1 / 15,286 = 0,065.
Отсюда парциальное давление СО2 будет равно
PCO2 = 0,065 ·100 = 6,5 кПа.
Парциальное давление О2 будет в нашем случае таким же, т.е.
РО2 = 6,5 кПа.
Температура начала диссоциации СаСО3
T = 906858,75 / (763,99 - lg РСО2) = 906858,75 / (763,99 -0,813) = 1188 K или 915оС.
Температура начала диссоциации Fe2O3
Т = 3120810 / (1813,7 - lg РО2 ) =3120810 / (1813,7 – 0,813 ) = 1721 К или 1448оС.
4.Расход воздуха на сжигание 1м3 природного газа при α = 1,5 составит
СН4 + 2 О2 = СО2 + 2 Н2О,
1,5 ·2 ·100 / 21 =14,3 м3.
Задание к работе 7
Используя результаты работы 1 и 6, а также данные таблицы П.2, определить производительность обжиговой машины, содержание железа в готовых окатышах, температуру начала диссоциации кальцита и гематита, количество воздуха на сжигание 1 м3 природного газа (СН4 = 100%) для обогрева горна. Оценить влияние кислородного потенциала газовой фазы и давления в слое на температуру начала диссоциации кальцита и гематита. Подсосами пренебречь. Содержание бентонита 0,8%. В нем содержится 3% Fe2O3, остальное – пустая порода. В готовых окатышах содержится FeO – 2,5%, S – 0,015%.
При низком содержание закиси железа в концентрате (< 2,5%) учесть убыль массы окатышей за счет кислорода, выделившегося при диссоциации гематита. Содержание серы в окатышах принимать, равным содержанию ее в концентрате, если сернистость последнего не превышает 0,015%.
8 КАЧЕСТВО ОКУСКОВАННОГО ЖЕЛЕЗОРУДНОГО СЫРЬЯ
На результаты работы доменной печи по удельному расходу кокса, производительности и качеству чугуна, на ровность хода процессов существенно влияет качество шихтовых материалов [12]. Оно характеризуется тремя группами показателей:
- химическим составом;
- физико-механическими свойствами;
- физико-химическими свойствами.
По показателям, характеризующим эти свойства, имеются оптимальные и предельно допустимые значения. Для определения показателей качества разработаны и используются соответствующие устройства и методики. Знание этих показателей и влияния их на работу доменной печи позволяет, как совершенствовать технологию доменной плавки, так и формировать рациональные требования к поставщикам сырья.
Химический состав относится к наиболее важным показателям качества шихтовых материалов. По химическому составу сырьевых материалов производится корректировка шихты и технологии плавки.
Составляющими химического состава железорудного сырья являются (табл. 8.1): Fe преимущественно в виде FeO и Fe2O3, SiO2, Al2O3, CaO, MgO, P в виде Р2О5, S в виде FeS, СаS (в агломерате) FeS2 (в магнетитовых рудах), СаSO4 (преимущественно в окатышах), MnO (в агломерате и окатышах), Zn в виде ZnO и ZnS, TiO2, V2O5, Cr в виде Cr2O3, Ni в виде NiO, Na2O, K2O, Cu в виде CuO, As в виде As2O3, пмп (потери массы при прокаливании).
Таблица 8.1
Примеры химического состава компонентов железорудного сырья, %
Материал | Fe | FeO | SiO2 | Al2O3 | CaO | MgO | S | P | TiO2 | Zn | MnO | Cr |
Агломерат Окатыши 1 Окатыши 2 Магнитный продукт Руда | 56,2 65,6 62,2 66,2 41,3 | 11,6 1,80 3,09 11,3 5,6 | 6,1 5,3 6,1 6,4 35,0 | 2,09 0,39 1,90 1,64 0,26 | 9,9 0,21 1,43 10,6 1,56 | 1,94 0,39 0,96 4,25 0,31 | 0,051 0,012 0,020 0,005 0,155 | 0,029 0,012 0,017 0,1085 0,022 | 0,28 <0,1 0,33 0,36 0,10 | 0,040 0,007 0,007 0,020 0,017 | 0,32 0,04 0,22 1,50 0,06 | 0,020 0,007 0,013 0,20 0,005 |
Кроме этого содержатся микропримеси [13]. Составляющими пмп являются СО2 карбонатов и гидратная влага. Оксиды, сульфиды, сульфаты и другие соединения связаны в минералы. В магнитном продукте и металлизованном материале часть железа находится в металлическом состоянии.
Основными показателями, характеризующими физико-механические свойства, являются:
- крупность;
- механическая прочность;
- плотность;
- порозность;
- пористость;
- углы откоса, внешнего и внутреннего трения;
- коэффициенты внешнего и внутреннего трения;
- газопроницаемость;
- температура.
Основными показателями, характеризующими физико-химические свойства, являются:
- восстановимость;
- температура начала размягчения и температурный интервал размягчения компонентов железорудного сырья;
- увеличение объёма при восстановлении;
- газопроницаемость и усадка слоя при восстановлении;
- предложенные ИЧМ НАН Украины показатели, уровень которых должен соответствовать табл. 8.2.
Таблица 8. 2
Требования к физико-химическим свойствам агломерата и окатышей
(оф – офлюсованные, нф – неофлюсованные)
Показатель | Вид сырья | |
агломерат | окатыши | |
Температура резкого уменьшения газопроницаемости слоя при нагреве, °С Температура начала фильтрации жидких фаз, 0С, не менее Температура максимальной фильтрации, °С Содержание FeO в первичном шлаке, %, не более Остаток шлака в слое кокса при 1600°С, %, не более | 1260-1280 1380 1500-1540 12 18 | 1230-1250 1350оф 1380нф 1500 30оф 60нф 8 |
Железо и его оксиды
В агломерате (табл. 8.1) значительная часть железа содержится в виде магнетита (Fe3O4) и гематита (Fe2O3) при небольшом количестве однокальциевого феррита (СаО·Fe2O3), двукальциевого феррита (2СаО·Fe2O3) и фаялита (2FeO·SiO2). Указанное в анализе FeO находится преимущественно в виде Fe3O4 (FeO·Fe2O3), а частично в виде 2FeO·SiO2. Поэтому содержание его характеризует степень окисленности железа, то есть долю кислорода, приходящуюся на единицу железа. Более высокое содержание FeO свидетельствует о поступлении меньшего количества кислорода, которое необходимо удалить из железа проведением доменного процесса. Кроме того, содержание FeO в агломерате характеризует качество проведения агломерации, так как оно тем выше, чем выше был температурно-тепловой режим процесса при других неизменных условиях (основность агломерата, высота спекаемого слоя и др.)
В окатышах большая часть железа представлена гематитом, меньшая – магнетитом. В магнитном продукте, полученном из сталеплавильного шлака, железо в основном находится в металлическом состоянии, частично в виде Fe3O4. Гематитовые руды содержат железо преимущественно в виде Fe2O3, магнетитовые – Fe3O4, бурые железняки – mFe2O3 · nН2О. В карбонатной руде (сидерите, шпатовом железняке) железо находится в виде FeCO3, который в условиях доменной печи разлагается по реакции 3FeCO3 = Fe3O4 + СО + 2СО2.Таким образом, для получения чугуна необходимо восстановить железо в основном из Fe2O3 и Fe3O4.
Для работы доменной печи имеют значение величина содержания железа в шихте и постоянство его во времени
На основе обобщения результатов выполненных исследований получены данные, представленные в табл. 8.3 [13]. Они широко используются в настоящее время.
Таблица 8.3
Влияние увеличения содержания железа
на производительность доменной печи и удельный расход кокса [13]
Условия повышения содержания железа | Снижение удельного расхода кокса, % | Повышение производительности, % |
Повышение содержания железа на 1 % во всей шихте без кокса и СО2 флюса: до 50 % от 50 до 55 % от 55 до 60 % | 1,4 1,2 1,0 | 2,4 2,0 1,7 |
Наряду с этим справочная информация содержит данные, показывающие зависимость влияния богатства от вида железорудного сырья (табл. 8.4, 8.5) [14].
Таблица 8.4
Влияние увеличения содержания железа в агломерате
на производительность доменной печи и удельный расход кокса [14]
Условия повышения содержания железа | Снижение удельного расхода кокса, % | Повышение производительности, % |
Повышение содержания железа на 1 % в офлюсованном агломерате: от 50 до 52 % от 52 до 54 % от 54 до 56 % от 56 до 58 % от 58 до 60 % | 1,3 1,2 1,1 1,0 0,9 | 2,2 2,1 2,0 1,8 1,7 |
Увеличение содержания железа до 59 – 60 % обеспечивает, как правило, улучшение результатов работы печи без компенсации его отрицательного влияния на отдельные стороны доменного процесса, а выше – необходимыми становятся дополнительные мероприятия (по аналогии, например, с совместным использованием природного газа и технологического кислорода).
Таблица 8.5
Влияние увеличения содержания железа в окатышах на производительность доменной печи и удельный расход кокса [14]
Условия повышения содержания железа | Снижение удельного расхода кокса, % | Повышение производительности, % |
Повышение содержания железа на 1 % в офлюсованных окатышах: от 56 до 58 % от 58 до 60 % от 60 до 62 % | 1,0 0,9 0,8 | 1,9 1,8 1,7 |
Кроме абсолютной величины содержания железа имеет значение интервал его колебания и укладка в этот интервал . В настоящее время допустимым считается интервал колебания равный ± 0,5 %. Однако по разработанным современным требованиям он должен составлять ± 0,25 %.
Укладка показывает долю поставленного потребителю сырья, в котором содержание соответствующего компонента (например, железа) находится в заданных пределах от установленной средней величины. По справочнику технолога-доменщика уменьшение укладки от 100 % до соответствующих величин увеличивает удельный расход кокса и снижает производительность печи:
укладка ∆К, % ∆П, %
90 0,5 0,6
80 1,0 1,1
70 1,6 1,8
60 2,4 2,8
50 3,5 4,2
Выполнение требований по интервалу колебания содержания железа одновременно обеспечивает стабилизацию во времени других показателей качества железорудного сырья.
Наряду с этим в качестве показателя варьирования применяют интервал изменения содержания железа между максимальным и минимальным значениями. В современных условиях максимальные пределы отклонения железа в руде, поступающей на усреднительные склады, превышают ± 2,5 % от среднемесячного. Вследствие сегрегации руды при формировании штабеля колебания содержания железа по сечению его достигают ± 4 %. Разработка штабеля экскаваторами обеспечивает снижение этого интервала до ±1,5 %. Применение специального оборудования позволяет достигнуть ± 0,25 %.
Постоянство состава и других свойств исходных шихтовых материалов является одним из важных факторов, определяющих эффективность металлургического производства на всех его стадиях. Результаты расчётов по влиянию усреднения железорудного сырья показывают, что удельная производительность агломашин можно повысить до 8 % по бункерному и до 10 % по скиповому агломерату. Расход твёрдого топлива при получении агломерата снижается на 8 – 10 %. Содержание мелочи 5 – 0 мм в бункерах снижается на 2 %, в скипах – на 1,4 %.
При колебаниях в составе железорудной шихты ухудшение технических показателей доменной плавки происходит, главным образом, из–за уменьшения степени использования газов–восстановителей – монооксида углерода и водорода, и вынужденного повышения нагрева печи. Понижение интервала изменения содержания железа с ± 1,5 % до ± 0,25 % повышает производительность доменной печи на 5,8 %, и снижает удельный расход топлива (кокса и природного газа) на 8,8 %, существенно улучшает постоянство состава чугуна, прежде всего по содержанию кремния. Интервалам содержания железа ± 1,5 и ± 0,25 % соответствуют интервалы изменения содержания кремния в чугуне ± 0,4 и ± 0,1 % соответственно.
Изменения постоянства состава чугуна существенно влияют на показатели производства стали. Как показывает опыт передовых отечественных и зарубежных предприятий, устойчивая и высокопроизводительная работа конвертерных цехов может быть обеспечена при снижении колебаний содержания кремния в чугуне до ± 0,05 – 0,1 %.
Работе конвертеров при колебаниях содержания кремния в чугуне ± 0,4 % приводит к необходимости введения дополнительных операций (по сравнению с использованием чугуна с колебаниями по кремнию до ± 0,05–0,1 %): додувка плавок для корректировки температуры или содержания углерода, взятие пробы и ожидание анализа. Указанные операции приводят к удлинению продолжительности плавок в конвертерах и снижению производительности примерно на 10 %.
Изменение содержания кремния в чугуне на 0,1 % в связи с изменением потребного расхода извести вызывает либо недостаток её, либо перерасход в размере 10 кг/т чугуна. Увеличение расхода извести приводит к дополнительным затратам на него, увеличению количества шлака, угару железа, снижению количества годного примерно на 0,3 %.
Таким образом, переход от железорудного сырья с колебаниями по содержанию железа ± 1,5 % на сырьё с колебаниями ± 0,25 % обеспечивает повышение производительности агломашин примерно на 10 %, доменных печей на 5,8 %, конвертеров по производству стали на 10 %. Снижение расхода энергоносителей составляет: коксика в агломерационном производстве 8 %, кокса и природного газа в доменном производстве 8,8 %. Расход флюсов на доменную плавку сокращается на 3 %, расход извести в сталеплавильном производстве – на 17,5 %.
Задание 1 к работе 8
Используя результаты расчётов в разделе 6, определить ориентировочное содержание железа в агломерате. В агломерат переходят руды, концентраты, зола коксика, известняк, за вычетом его СО2. В используемом для агломерации известняке СаО содержится в виде СаСО3.
Оксиды кремния и кальция
Наибольшее значение имеет соотношение между этими оксидами вследствие проведения доменной плавки на шлаках заданной основности по отношению CaO/SiO2. В ОАО “ММК”, например, заданная основность шлака находится в пределах 0,95 – 1,10, но в каждых конкретных условиях задают более точную величину и в более узких пределах. Поэтому необходимое содержание этих оксидов в сырьевых материалах взаимосвязано. Её величину в агломерате и в окатышах регулируют изменением расхода известняка. Оперативное регулирование основности шлака осуществляют изменением соотношения разноосновных материалов (агломерата и окатышей), применением кускового известняка и кварцита в доменной шихте.
При работе с использованием офлюсованных окатышей ССГПО основностью 1,07 с долей в шихте 35,5 % величина основности агломерата ОАО “ММК”составляла в среднем 1,55. С переходом на неофлюсованные окатыши ССГПО основностью 0,18 – 0,20 с долей в шихте 35 – 41 % она стала равняться 1,80 – 2,0. При доле окатышей 21 % она составила 1,4, а при доле 8 % основностью 0,26 – близкой к 1,35.
Основность железорудных материалов выбирают с учётом влияния на их физико-механические и физико-химические свойства. Некоторой основности (критической величине) соответствуют наихудшие свойства. При этом существенное значение имеет содержание минералов, включающих Al2O3 (обозначенное далее как A), SiO2 (S), CaO (C), ферриты кальция (F).
По исследованиям университета “МИСиС” для условий ОАО “ММК” интервалу критической прочности агломерата соответствует основность от 1,4 до 1,8. Минимальную прочность имеет агломерат основностью 1,6. В минералогическом составе их распространена композиция игольчатых алюмосиликокальциевых ферритов ASCF2 в ассоциации с Ca2SiO4. С ростом основности с 1,6 до 1,9 количество таких композиций снижается, что благоприятно отражается на прочности агломерата. При повышении основности от 1,9 до 2,3 в составе агломерата постепенно уменьшается ASCF2 и начинают образовываться алюмосиликоферритные фазы с более высоким содержанием СаО: сначала на основе однокальциевого феррита CaFe2O4, а затем на основе двухкальциевого феррита Ca2Fe2O5. При основности 2,6 в агломератах основной связкой становятся алюмосиликоферриты на основе однокальциевого и двухкальциевого ферритов в ассоциации с трёхкальциевым силикатом (алитом) Ca3SiO5.
На доменных печах могут создаваться условия для применения совместно с агломератом окатышей в офлюсованном или неофлюсованном виде. При сильно выраженной определяющей роли силового взаимодействия потоков шихты и газа в нижней части печи и ускоренном износе футеровки шахты, распара, заплечиков целесообразен переход с неофлюсованных окатышей на офлюсованные. При сильно выраженной определяющей роли силового взаимодействия потоков шихты и газа в верхней части печи и регулярном формировании настылей на футеровке шахты целесообразен переход от офлюсованных окатышей на неофлюсованные.
При повышении основности агломерата вследствие поставки на предприятие неофлюсованных окатышей возрастают потребности во флюсе для введения в агломерат и работы по его подготовке. Некачественная подготовка флюса, например, из-за недостатка помольного оборудования, ведёт к ухудшению качества агломерата по прочности и содержанию мелочи.
Необходимо также обеспечение постоянства основности материалов во времени. В современных условиях считается допустимым интервал варьирования основности агломерата ±0,05 ед., окатышей ±0,025 ед. Уменьшение укладки в пределы (±0,05 ед.) повышает удельный расход кокса (∆К, %) и снижает производительность печи (∆П, %) в соответствии со следующими величинами:
укладка ∆К ∆П
90 0,5 0,5
80 1,0 1,0
70 1,5 1,7
60 2,1 2,6
50 3,0 4,0
Задание 2 к работе 8
Используя результаты расчётов в разделе 6, определить ориентировочную величину основности агломерата. В агломерат переходят руды, концентраты, зола коксика, известняк, за вычетом его СО2. В используемом для агломерации известняке СаО содержится в виде СаСО3.
Оксид алюминия
Имеется оптимальное отношение SiO2 к Al2O3, находящееся в пределах 2,5 – 5,0. Оптимальному соотношению соответствуют низкие величины вязкости и температуры плавления шлака, высокая величина коэффициента распределения серы между чугуном и шлаком. В каждых конкретных условиях SiO2/Al2O3 должно быть в более узких пределах. При заданной основности по CaO/SiO2 это означает ограничение содержания Al2O3 в сырьевых материалах. В связи с поступлением в ОАО “ММК” материалов с повышенным содержанием Al2O3 приходилось устанавливать технологические параметры работы печи применительно к минимальному отношению SiO2/Al2O3, то есть к максимальному содержанию Al2O3 в шлаке. В отдельные периоды они были равны 2,75 – 2,80 и 13,3 – 13,5 %, соответственно. С коксом поступало Al2O3 около 15 кг/т чугуна. Примерно такое же количество SiO2 расходовалось на восстановление Si, переходящего в чугун. С учётом этого отношение SiO2/Al2O3 в сырьевых материалах должно было быть не менее 2,90. В таких условиях использование материала с меньшей величиной этого отношения необходимо компенсировать применением другого материала с более высокой его величиной.
Основными железорудными материалами, имеющими повышенное содержание Al2O3, среди поступающих в ОАО “ММК”, являлись Коршуновский и Ковдорский концентраты.
В практике ОАО “ММК” имелся период работы длительностью около двух лет на железорудном сырьё КМА с низким содержанием Al2O3 (в виде концентратов и окатышей). Ход процессов и свойства шлака позволяли плавить малосернистый чугун. На доменной печи № 1 средний состав чугуна с содержанием серы менее 0,01 % был следующим:
компоненты Si Mn S Ti P Cr C
содержание, % 0,79 0,11 0,008 0,036 0,05 0,019 4,72
Ему соответствовал шлак состава:
компоненты SiO2 Al2O3 CaO MgO TiO2 S FeO MnO Na2O K2O
содержание, % 38,8 7,9 42,1 8,1 0,33 0,85 0,25 0,12 0,54 0,98
Отношение SiO2/Al2O3 составило 4,9.
Задание 3 к работе 8
Используя результаты расчётов в разделе 6, определить отношение SiO2/Al2O3 в агломерате. В агломерат переходят руды, концентраты, зола коксика, известняк, за вычетом его СО2. В используемом для агломерации известняке СаО содержится в виде СаСО3. Оксиды SiO2 и Al2O3 переходят в агломерат полностью.
Оксид магнияОксид магния улучшает свойства шлака в определённых пределах его содержания. В современных условиях работы ОАО “ММК” наилучшему ходу процессов в доменной печи соответствует содержание MgO шлаке в пределах 7 – 10 %. Оно обеспечивается при содержании MgO в сырье, равном 1,6 – 1,8 %. Имеет значение источник MgO. Оксид магния, поступающий в агломерацию, а затем в доменную плавку с Коршуновским и Ковдорским концентратами, связан в шпинель Al2O3·MgO и он не улучшает свойства шлака. Оксид магния, поступающий с доломитом, улучшает качество чугуна по содержанию серы. Это проявилось в ОАО “ММК” при работе печей на сырье КМА. От увеличения содержания доломита во флюсе агломерационной шихты на 10 % содержание серы в чугуне снижалось на 0,002 %. Зависимость его от модуля (MgO/Al2O3)/[Ti] имела вид:
[S] = 0,022 – 0,0002(MgO/Al2O3)/[Ti]
с коэффициентом детерминации 0,84 в интервале [S] = 0,013 – 0,022 %; Al2O3/MgO = 1,0 – 1,07; (MgO/Al2O3)/[Ti] = 5 – 35; MgO/[Ti] = 70 – 250.
Снижение содержания серы в чугуне изменением состава шихты и доведением модулей до выявленных оптимальных уровней сопровождалось улучшением результатов плавки по производительности и удельному расходу кокса. По результатам исследований доломит, содержащийся в агломерате, снимая диффузионный барьер, способствует более полному и интенсивному восстановлению оксидов марганца и железа.
В связи с повышенным содержанием MgO в ряде сырьевых материалах, особенно в сидерите Бакальского месторождения (поступающих в агломерационную шихту), и неблагоприятным видом содержащего его минерала в ОАО “ММК” часто устанавливают технологические параметры доменной плавки применительно к максимально допустимому содержанию MgO в шлаке. Ограничивают содержание MgO в шлаке.
Задание 4 к работе 8
Используя результаты расчётов в разделе 6, определить ориентировочное содержание MgO в агломерате. В агломерат переходят руды, концентраты, зола коксика, известняк, за вычетом его СО2. В используемом для агломерации известняке СаО содержится в виде СаСО3. Оксид MgO переходит из компонентов шихты в агломерат полностью.
Фосфор
В доменную печь фосфор поступает из железорудного сырья и минеральной части кокса (золы) в составе минералов, включающих оксид P2O5. При выплавке чугуна в основном переходит в чугун, а из него в сталь. По новым данным “МИСиС” коэффициенты перехода фосфора в металл, шлак и газ составляют:
в металл в шлак в газ
при выплавке передельного чугуна 0,9 – 0,94 0,01 – 0,02 0,04 – 0,06
при выплавке литейного чугуна 0,9 – 0,92 0,01 – 0,02 0,06 – 0,08
при выплавке ферромарганца 0,75 – 0,8 0,03 – 0,05 0,15 – 0,20
При выплавке феррофосфора около 13 % фосфора уносится с колошниковом газом. Из оставшегося количества около 80 % переходит в металл и, соответственно, около 20 % в шлак.
Фосфор снижает пластичность стали, особенно ударную вязкость при низких температурах, то есть придаёт металлу хладноломкость. Кроме того, повышенное содержание фосфора ухудшает прочность и свариваемость нагретого металла (придаёт красноломкость). Он совместно с серой и кислородом повышает анизотропию прочностных свойств проката со снижением прочности в поперечном направлении по сравнению с продольным направлением. Сталь с высоким содержанием фосфора имеет особо выраженную хрупкость при температурах 500 – 600 0С (синеломкость).
Только в некоторых видах металла фосфор является полезной примесью: чугун для художественного литья, некоторые виды конструкционных сталей (автоматные, атмосферостойкие и др.).
В процессах окускования мелких руд и концентратов он практически не удаляется. В ходе доменной плавки его содержание не поддаётся управлению. Поэтому содержание фосфора в исходных материалах определяет качество чугуна по этому компоненту. По справочным данным снижение содержания фосфора в чугуне на 0,1 %абс. за счёт меньшего его поступления с шихтовыми материалами обеспечивает сокращение удельного расхода кокса и повышение производительности печи на 1,2 %.
В доменные печи ОАО “ММК” поступает сырьё с относительно низким содержанием фосфора и поэтому в чугуне его содержание получается также невысоким, составляя около 0,05 – 0,065 %. Передельный чугун с таким содержанием фосфора по ГОСТу 805 – 80 относится к классу А.Задание 5 к работе 8
Используя результаты расчётов в разделе 6, определить ориентировочное содержание фосфора в агломерате. Руководствуясь ГОСТ 805-80 (табл. П.6) указать виды чугунов, которые можно выплавлять при заданных условиях по шихте. В агломерат переходят руды, концентраты, зола коксика, известняк, за вычетом его СО2. В используемом для агломерации известняке СаО содержится в виде СаСО3. Фосфор переходит из компонентов шихты в агломерат полностью.
Сера
Значительная часть серы, поступающей в доменную печь, переходит в шлак и, благодаря этому, удаляется. Однако некоторая часть её остаётся в чугуне и поступает в сталеплавильное производство.
В стали сера является вредной примесью вследствие снижения её механической прочности при температурах более 1000 0С (красноломкость) и менее – 30 0С (хладноломкость), ухудшения свариваемости, электротехнических, антикоррозийных и других свойств. Значительным является отрицательное влияние повышения содержания серы на величину ударной вязкости стали и на её анизотропию в поперечном и продольном направлениях. Поэтому целесообразно, во первых, минимальное поступление её в доменную печь с шихтовыми материалами, во вторых, максимальный перевод поступившей серы в шлак.
Содержание серы в сырьевых материалах доменных печей ОАО “ММК” низкое – в агломерате составляет около 0,05 %, в неофлюсованных окатышах ССГПО – около 0,02 % и находится в основном в виде сульфидов, частично в виде сульфатов. Низкое содержание серы обеспечивается, благодаря значительному удалению из руд в процессах окускования.
Основным поставщиком серы в печь является кокс, так как только часть её удаляется при коксовании углей. В коксе основная часть серы представлена органическими соединениями, меньшая находится в элементном виде, а также в виде сульфатов и сульфидов. По результатам проведенных исследований, элементная и органическая сера кокса переходит в газ, сульфатная, разложившись, переходит в сульфидную, а сульфидная, в свою очередь, распределяется между чугуном и шлаком. Газификация серы кокса происходит преимущественно при горении его у фурм (выше горизонта фурм переходит в газ 20 – 25 % серы). В последующем из газа она в процессе движения вверх в основном поглощается компонентами железорудного сырья, а из них распределяется между чугуном и шлаком.
Возможности снижения содержания серы в чугуне после поступления её с компонентами шихты определяются поведением сернистых соединений по высоте доменной печи. При выплавке передельного чугуна из печи уносится газами 1-3 % серы от общего поступления, литейного – 10-15 %. Поглощающими серу компонентами сырья являются Fe, FeO, MnO, CaO, MgO. Образование карбидов (Fe3C, Mn3C и др.), силицидов (FeSi и др.), фосфидов (Fe2P и др.) уменьшает растворимость серы в металле.
Распределение серы между составляющими чугуна и шлака происходит почти по всей высоте печи. До заплечиков серу поглощают материалы, находящиеся в твёрдом и размягчённом состояниях, ниже – в расплавленном. В жидкофазном распределении участвует 27 – 33 % серы, в твёрдофазном и промежуточном (выше зоны образования жидкого металла и шлака) – 67 – 73 % [2]. Из этого следует важность для выплавки качественного по сере чугуна не только свойств шлака и чугуна, но и состояния материалов до горизонта фурм, происходящих там процессов. При выплавке передельного чугуна в него переходит 3-12 % поступившей в печь серы, литейного – 1-3 %. По справочным данным [12] для снижения содержания серы в чугуне на 0,01 %абс. необходимо увеличить удельный расход кокса на 1,0 % и это сопровождается снижением производительности печи на 1,0 %.
Задание 6 к работе 8
Используя результаты расчётов в разделе 6, определить ориентировочное содержание серы в агломерате и в передельном чугуне. В агломерат переходят руды, концентраты, зола коксика, известняк, за вычетом его СО2. В используемом для агломерации известняке СаО содержится в виде СаСО3. Степень удаления сульфидной серы (в магнетитовых концентратах) при агломерации может достигать 95 – 99 %; сульфатная сера (СаSО4, ВаSО4 в гематитовых концентратах и рудах, в бурых железняках и сидеритах) удаляется на 60 – 70 % [12]. Сера в доменную печь поступает с железорудными материалами и коксом.
Мышьк
Мышьяк, образуя оксиды и сульфиды, содержится в некоторых железных рудах (Керченском, Аятском, бурых железняках регионов Сибири). В Керченском месторождении имеется в среднем 0,11 % As. Из руд практически полностью переходит в агломерат и окатыши, где он представлен оксидом Аs2O3, а из них в чугун. Далее поступает в сталеплавильное производство, в котором при окислительном рафинировании не удаляется. Переходя в сталь образует арсенат железа Fe2Аs. Вредное влияние аналогично фосфору, но выражено слабее. Вызывает хладноломкость (снижение вязкости стали при низких температурах), особенно при содержаниях в стали более 0,1 – 0, 15 %.
Мышьяк может быть удалён из жидкого железа введением в него кальция, который образует прочные и практически нерастворимые в металле арсениды кальция переменного состава СаmAsn, наиболее прочными из которых являются Са2As3 и Са2As.
В некоторых случаях мышьяк может быть использован в качестве легирующего элемента, так как при содержании его 0,1 – 0, 15 % в углеродистой и низколегированной стали наблюдается повышение коррозионной стойкости в воздухе и морской воде.
В чугуне ОАО “ММК” по результатам единичных анализов содержалось 0,02 – 0,04 % As.
Цинк
Цинк, содержащийся в сырьевых материалах доменных печей, относится к вредным примесям, так как способствует образованию настылей на поверхности футеровки шахты и в газоотводах, разрушению футеровки и к разрыву кожуха. Содержание его в агломерате ММК составляет 0,02 – 0,04 %, в окатышах ССГПО – около 0,007 – 0,012 %. Находится в основном в виде ZnO, частично образует ZnS.
В доменной печи цинк почти полностью восстанавливается при температурах более 900 0С. Имеет температуру плавления 419 0С и температуру испарения 906 0С, поэтому образует жидкую и парообразную фазу. Поднимаясь с газами, окисляется и переходит в твёрдое состояние, оседает на поверхности частиц шихты и вместе с ней возвращается в зону повышенных температур. Таким образом, частично циркулирует в объёме доменной печи и накапливается. Но основная масса ZnO уносится из печи газовым потоком.
Часть парообразного цинка проникает вместе с газом в швы и трещины огнеупорной футеровки, где конденсируется и окисляется, вызывая увеличение объёма, что ведёт к разрушению футеровки и разрыву кожуха доменной печи.
Образование жидкой фазы цинка с последующим окислением и переходом в твёрдое состояние способствует формированию настылей. Максимальные отложения цинка соответствовали по результатам исследований зоне максимального разрушения футеровки в нижней части шахты и зоне цинковых настылей вверху шахты под защитными плитами колошника. При работе доменных печей ОАО “ММК” на горячем агломерате без использования окатышей значительными были отложения цинкита на внутренней поверхности большого конуса и в газоотводах. Накапливание на конусе, не уравновешенной контргрузами, приводило к самопроизвольному его открытию, а в газоотводах – к ускоренному износу футеровки и нарушению распределения газов в слое шихты.
В доменных печах комбината настыли образовывались и при содержании цинка в агломерате около 0,025 %. Переход от офлюсованных окатышей ССГПО на неофлюсованные ослабил негативное влияние цинка на работу доменных печей.
По результатам выполненных исследований со шлаком удаляется 2-7 % цинка, с чугуном – 8-12 %. Остальной цинк выносится из печи с пылью, относительно крупные частицы которой образуют колошниковую пыль, мелкие и тонкие, улавливаемые в системе мокрой газоочистки, – шлам. Повышенное содержание в них железа и наличие углерода кокса обуславливают целесообразность повторного использования путём введения в агломерационную шихту. Для решения проблемы вредного влияния цинка при этом целесообразно предварительное удаление цинка из пыли. Примерное содержание цинка, железа и углерода в пыли, выносимой из доменных печей ОАО “ММК”, например, следующее (%):
Zn Fe C
колошниковая пыль 0,53 45,3 18,0
шлам 1,10 52,1 10,4
Медь
Медь образует оксиды CuO и Cu2O с низким сродством к кислороду. В условиях доменной печи полностью восстанавливается и переходит в чугун. Из чугуна также практически полностью поступает в сталь, так как удаление её в ходе проведения сталеплавильного производства затруднено. В стали чаще всего медь относится к примесям, ухудшающим свойства металла, так как снижает его пластичность и придаёт красноломкость. В некоторых видах сталей медь относится к полезным примесям, так как придаёт металлу коррозионную стойкость, повышает прочность и твёрдость.
В большинстве конструкционных сталей, предназначенных для изготовления товарной продукции без обработки давлением (штамповкой), положительное действие меди до содержания 0,25 – 0,30% существеннее, чем отрицательное.
В сталях, предназначенных для изготовления товарной продукции глубокой вытяжкой, в которых основным требованием является высокая пластичность в холодном состоянии, содержание меди не должно превышать 0,05 %. Таким же является требование к стали, поступающей на изготовление канатов.
В коррозионностойких литейных чугунах содержание меди доводят до 1,0 – 1,5 %.
В чугуне ОАО “ММК” по результатам единичных анализов содержалось 0,02 – 0,04 % Cu.
Оксид титана
Повышенное содержание оксида титана в шихтовых материалах вызывает осложнения в работе доменной печи: ухудшение дренажа продуктов плавки в горн, затруднения по выпуску их из печи, неполное разделение чугуна и шлака. В условиях ОАО “ММК” отрицательное действиеTiO2 заметно усиливается при содержании его в сырьевых материалах более 0,3 – 0,35 %. При этом содержание титана в чугуне составляет около 0,1 %, его оксида в шлаке – около 1 %. При выплавке обычного передельного чугуна в него переходит 20 – 30 % титана, специального (ванадиевого) “холодного” – 7 – 12 %.
Увеличение содержания TiO2 становится целесообразным на период формирования гарнисажа при появлении угрозы прорыва горна.
Важнейшие минералы титана входят в состав пяти характерных групп – рутила, ильменита, перовскита, лопарита, сфена. Наибольшее практическое значение имеют группы рутила и ильменита.
Рутил представляет собой оксид титанаТiO2, обычно содержащий оксиды двух- и трехвалентного железа (до 10 %). В месторождениях обычно находится вместе с ильменитом, цирконом, гематитом и магнетитом.
Ильменит представляет собой сложный твердый раствор на основе решетки метатитаната железа FеО · ТiO2. Его стехиометрический состав: 52,63 % ТiO2 и 47,37 % FеО. В чистом виде ильменит встречается редко, обычно в нем содержатся примеси оксидов железа, магния, марганца, ванадия, хрома, алюминия и др. Большая часть примесей находится в изоморфно связанном состоянии с ильменитом. Как правило, в ильменитах содержится переменное количество диоксида титана. Это обусловлено наличием примеси рутила, который находится в тонком прорастании с ильменитом, и лейкоксенизацией, т.е. изменением первичного ильменита под действием атмосферного воздуха, когда при длительном выветривании часть двухвалентного железа окисляется в трехвалентное и за счет выноса последнего происходит обогащение титаном. В результате длительного процесса лейкоксенизации кристаллическая решетка ильменита как самостоятельная фаза исчезает, уступая место рутилу. Поры, освободившиеся в ильмените в ходе выветривания и выщелачивания из него оксидов железа, постепенно заполняются другими оксидами, например кварцем, о чем свидетельствует, в частности, его тонкое прорастание в зернах лейкоксена. В связи с этим в процессе лейкоксенизации ильменита происходит изменение соотношения не только основных компонентов минерала (оксидов титана и железа), но и связанных с ними оксидов других металлов. Как правило, лейкоксен обогащается глиноземом, кремнеземом, оксидами магния, марганца, фосфора, хрома. Для ряда ильменитов характерно повышенное содержание оксидов железа, преимущественно магнетита, иногда и гематита. Смесь ильменита с магнетитом (FеО · ТiO2 – Fе3O4), представляющая собой твердый раствор ильменита в магнетите, известна под названием титаномагнетитов, а с гематитом – под названием гематитоильменитов (FеО· TiO2 – Fе2О3).
Иногда к ильменитам относят также титансодержащие минералы, в которых другое соотношение между высшими оксидами железа и титана – минералы типа Fе2О3 · ЗTiO2. Это аризониты, отличающиеся от типичного ильменита меньшей плотностью, повышенным содержанием диоксида титана (62 – 66 %).
Титаномагнетиты, гематитоильмениты, ильмениты, содержащие ванадий являются комплексным сырьём, из которых возможно извлечение железа, титана и ванадия.
Действие ТiO2 на работу доменной печи имеет особое значение при выплавке ванадиевого чугуна из содержащих ванадий титаномагнетитовых руд.
Задание 7 к работе 8
Используя результаты расчётов в разделе 6, определить ориентировочное содержание ТiO2 в агломерате. В агломерат переходят руды, концентраты, зола коксика, известняк, за вычетом его СО2. В используемом для агломерации известняке СаО содержится в виде СаСО3. Оксид ТiO2 переходит из компонентов шихты в агломерат полностью.
Оксиды натрия и калия
Основными источниками их являются железорудное сырьё и кокс: 72 – 76 % вносится c сырьём, 24 – 28 % с коксом. В доменной печи при высоких температурах переходят в газ, охлаждаясь в составе газов, переходят в шихту и таким образом циркулируют. Оксиды щелочных элементов ухудшают “горячую” прочность агломерата, окатышей, кокса. Участвуют в формировании настылей, разрушении футеровки и разрыве кожуха доменной печи аналогично цинку.
От 85 до 92 % оксидов щелочных элементов выводятся из доменной печи со шлаком, около 4 % выносятся с пылью и примерно столько же в составе колошникового газа. Шлак печей ОАО “ММК” содержит около 2,0 % (К2О + Nа2О). В современных требованиях к качеству подготовленного железорудного сырья допустимое их содержание установлено не более 0,15 %.
Задание 8 к работе 8
Используя результаты расчётов в разделе 6, определить ориентировочное содержание К2О+Na2О в агломерате. В агломерат переходят руды, концентраты, зола коксика, известняк, за вычетом его СО2. В используемом для агломерации известняке СаО содержится в виде СаСО3. Оксиды К2О и Na2О переходит из компонентов шихты в агломерат полностью.
Марганец
Марганец относится к полезным примесям, как для процесса выплавки чугуна, так и для процесса выплавки стали. Содержится в рудах обычно в виде оксидов MnO2, Mn2O3, Mn3O4 и MnO и карбоната MnCO3. В агломерате и окатышах марганец находится в оксидной форме.
В доменной печи марганец распределяется между чугуном и шлаком. Он имеет неограниченную растворимость в жидком железе. Повышение содержания MnO в доменном шлаке снижает его вязкость и температуру плавления, делает шлак более “коротким”, повышает его серопоглотительную способность. Поступление оксидов марганца в печь обеспечивает промывку её от “спели” и мелочи кокса.
Это положительное влияние оксида марганца на ход доменной плавки имеет большое значение при использовании титаномагнетитовых руд.
При выплавке обычного передельного чугуна в него переходит 50 – 70 % марганца, а остальное количество в шлак. Железорудное сырьё, применяемое в ОАО “ММК” имеет низкое содержание марганца (табл. 1.1). Поэтому при необходимости увеличения содержания его в шихте применяют железомарганцевую или марганцевую руду.
По соотношению Mn/Fe различают следующие виды руд:
1. Марганцевые руды. В лучших рудах соотношение Mn/Fe доходит до 30.
2. Железомарганцевые руды. В них Mn/Fe находится в пределах 1 – 7;
3. Марганцовистые руды, в которых соотношение Mn/Fe менее 1, а содержание марганца составляет 5 – 10 %.
Руды, содержащие марганца менее 5 %, не относят к марганцевым. Эти руды с повышенным содержанием Fe относят к железным. Для промывки горна пригодны как марганцевые, так и марганцовистые и железные руды с повышенным содержанием марганца.
В сталеплавильном производстве поступление марганца обеспечивает уменьшение угара железа. Переходя частично в сталь, улучшает его качество, является раскислителем и легирующим элементом. Переходя в шлак, уменьшает его вязкость и температуру плавления, ускоряет растворение извести, что также благоприятно для сталеплавильного процесса. Устанавливаемое содержание марганца в стали зависит от назначения. При необходимости его увеличения проводят легирование ферромарганцем.
Основным положительным влиянием марганца на свойства стали является уменьшение вредного влияния серы за счёт образования сульфида MnS взамен FeS. Оно проявляется наиболее полно при достаточно высоком соотношении содержаний марганца и серы в стали: [Mn] / [S] ≥ 20 – 22.
Марганец значительно уменьшает критическую скорость закалки, поэтому марганцовистая сталь прокаливается глубже, чем простая углеродистая. Растворяясь в феррите, он повышает прочность стали (пределы прочности и текучести), но несколько снижает пластичность (относительное удлинение и вязкость). Повышает износостойкость и упругость стали. Марганец в легированных сталях снижает расход дорогого и дефицитного никеля.
В некоторых видах стали содержание марганца ограничивают из-за снижения пластичности её вследствие образования прочных карбидов. В низкоуглеродистой стали, используемой для глубокой штамповки без нагрева (например, автомобильные кузова), желательно относительно низкое содержание, составляющее 0,2 – 0,3 %. В углеродистой инструментальной стали оно близко к тем же значениям.
Задание 9 к работе 8
Используя результаты расчётов в разделе 6, определить ориентировочное содержание марганца в агломерате и в передельном чугуне. Руководствуясь ГОСТ 805-80 (табл. П.6) указать виды чугунов, которые можно выплавлять при заданных условиях по шихте. В агломерат переходят руды, концентраты, зола коксика, известняк, за вычетом его СО2. В используемом для агломерации известняке СаО содержится в виде СаСО3. Марганец переходит из компонентов шихты в агломерат полностью. Он в доменную печь поступает с железорудными материалами и коксом.
Ванадий
Ванадий, образующий устойчивые оксиды V2O5, V2O3, VO, содержится в сырьевых материалах доменных печей. При выплавке чугуна в него переходит 70 – 85 % ванадия, а остающаяся часть представлена в шлаке. Он имеет неограниченную растворимость в жидком и твёрдом железе. Оксид ванадия хорошо растворяется в шлаке, снижая при этом его температуру плавления. Передел чугуна в сталь сопровождается переходом значительной части ванадия в шлак (до 80 % и более в основных процессах и до 20 % в кислых). Оставшийся в металле ванадий является ценным легирующим элементом.
Ванадий образует прочные тугоплавкие карбиды и нитриды, выделяющиеся (выпадающие) в виде мелких неметаллических включений, служащих центрами кристаллизации металла, а потому способствующих измельчению первичного (аустенитного) и вторичного зерна, что повышает прочность, износоустойчивость и твёрдость стали, а также снижает анизотропию ей свойств вдоль и поперёк прокатки. Растворяясь в феррите (матрице) повышает его прочность (предел текучести), упругость, ударную вязкость, свариваемость. Выделение из жидкого металла карбидов, нитридов и карбонитридов устраняет явление старения стали во время холодной деформации её и службы в готовых изделиях.
Особое значение имеет содержание ванадия в сырьевых материалах при выплавке ванадиевого чугуна. В современных условиях доменная плавка является одной из стадий извлечения ванадия из руд. Россия обладает большими запасами титаномагнетитовых руд, содержащих ванадий. Предназначенные для производства ванадиевого чугуна агломерат и окатыши Качканарского ГОКа, например, содержат 0,5 – 0,55 % V2O5. Выплавленный чугун с содержанием 0,4 – 0,5 % ванадия перерабатывают дуплекс-процессом, применяя, в частности, технологию “конвертер – конвертер”. При этом в одном конвертере проводят деванадацию чугуна с получением ванадиевого шлака (содержащего 15 – 20 % V2O5), а в другом, оставшийся полупродукт переделывают в сталь.
Из ванадиевого шлака извлекают V2O5 химической переработкой. Далее из технического V2O5 производят феррованадий, содержащий 35 – 45 % V пирометаллургическим способом и используют для легирования стали.
Расширяется сфера применения ванадия при изготовлении труб нефтегазопроводов, строительных конструкций для мостов, высотных зданий, широкопролётных сооружений, железнодорожных рельсов. Удаётся улучшить показатели прочности стали на 20 – 40 %, хладостойкость на 20 – 50 %, коррозионную стойкость в 1,5 – 2 раза; уменьшить массу конструкций на 20 – 30 %. Улучшается качество литейных изделий из чугуна и стали. Положительное влияние проявляется и при низком содержании ванадия в стали (0,05 – 0,12 %). Целесообразным считается производство 100 г ванадия на тонну стали.
Хром
Хром содержится в железорудных материалах доменных печей в виде Cr2O3, а в магнитном продукте, производимом из сталеплавильных шлаков, в основном в металлическом состоянии. Особенно повышенным является содержание хрома в рудах Халиловского месторождения, составляя 1,2 – 1,8 %. При выплавке чугуна в него переходит 90 – 95 % хрома.
Хром имеет неограниченную растворимость, как в жидком, так и в твёрдом железе и во многих марках стали оказывает положительное влияние на его свойства. Относится к полезным примесям при производстве жаропрочного чугуна.
В некоторых сталях хром является нежелательной примесью. В канатной стали, например, его содержание не должно превышать 0,05 – 0,10 %. В передельном чугуне содержание хрома ограничивается также в случае поступления производимой далее стали на прокатку листового металла.
Переход части хрома в шлак в виде CrO приводит к увеличению вязкости шлака. Для условий ОАО “ММК” приемлемым является содержание хрома в чугуне 0,03 – 0,045 %.
Никель
Никель образует оксиды Ni2O3, Ni3O4, NiO. Сопровождает хром в рудах Халиловского месторождения с содержанием в пределах 0,3 – 0,55 %. В ходе доменной плавки полностью переходит в чугун, а из него в сталь. Относится к полезным примесям, так как повышает прочность и пластичность стали, а совместно с хромом придаёт антикоррозионные свойства. В чугуне ОАО “ММК” по результатам единичных анализов содержалось 0,1 – 0,2 % Ni.
9. МЕТАЛЛИЗАЦИЯ
Доменная печь, как агрегат высокой производительности и весьма экономичный, не имеет конкурентов. Однако, доменное производство имеет недостатки: необходимость применения каменноугольного кокса; использование железорудного сырья в виде прочного кускового материала (окатышей, агломерата). Кроме того, доменное производство сопряжено с коксохимическим и агломерационным производствами, отличающимися высокой экологической нагрузкой на окружающую среду.
В этой связи возможность организации процесса прямого получения железа из руды, минуя агло-коксо-доменный передел, представляет интерес и из других соображений. Развитие глубокого обогащения руд сопровождается не только получением концентратов с высоким содержанием железа, но и снижением в нем содержания вредных примесей (Cu, S, P, Zn, Pb и др.). Такие материалы незаменимы в производстве сталей ответственного назначения.
На современном этапе получение железа внедоменным путем осуществляется следующими способами:
1) восстановление железа с помощью твердых или газообразных восстановителей по реакциям
Fe2O3 + (C; CO; Н2; СН4) = Fe + (CO; СО2; Н2О)
2)-восстановление железа в кипящем железистом шлаке (жидкофазное восстановление) по реакции (FeO) + (C; CO) = Fe + (СО;CO2)
3) получение карбида железа из руд по реакции
3Fe2O3 + 5Н2 + 2СН4 = 2Fe3C + 9H2O
В мире имеются мощности для производства 80 млн. т/г металлизованной продукции. При этом по первому способу (процессу твердофазного восстановления при температурах до 1350оС)) получают более половины металлизованного продукта – «губчатого железа». За рубежом этот продукт принято называть DRI (Direct Reduced Iron), а после обжатия его в брикеты в горячем состояния (во избежание повторного окисления) - HBI (Hot Briquetted Iron). Для получения DRI используют вращающиеся трубчатые печи (процессы Wealz, SL-RN), печи с вращающимся подом (процессы Fastmet, Inmetco, Dryiron) и печи шахтного типа (процессы Midrex, HyL). В последних агрегатах в качестве восстановителя используется конвертированный природный газ (жидкое топливо), коксовый газ или газообразные продукты газификации твердого топлива. Основным видом газообразного топлива для производства восстановительного газа является природный газ, в результате конверсии которого образуются водород и оксид углерода. В соответствии с типом окислителя различают кислородную, воздушную, паровую и углекислотную конверсию природного газа:
CH4 + 0,5O2 = CO + 2H2;
CH4 + H2O = CO + 3H2;
CH4 + CO2 = 2CO + 2H2.
Конверсию проводят в специальных агрегатах (реформерах) на никелевом катализаторе либо непосредственно в металлургических печах с применением кислорода и участием свежевосстановленного железа в качестве катализатора.
В первых двух разновидностях агрегатов в качестве восстановителя используются некоксующиеся марки углей.
Продукт со степенью металлизации до 85% используют в доменной плавке, со степенью металлизации 85-95% - в сталеплавильном процессе, а со степенью металлизации более 98% - в производстве железного порошка. Степень металлизации определяют соотношением 100 Feмет / Fe общ.
По второму способу работают процессы Romelt, Hismelt, Ausmelt и в комбинированном варианте (с предварительным восстановлением) – процессы Corex, Finex, Dios, Fastmelt, Redsmelt и др. По этому способу в мире производят не более 10 млн. т/г чугуна.
По третьему способу работает одна промышленная установка. Процесс протекает при температуре 600оС и давлении 4 атм, получают частицы крупностью 0,1-1,0 мм с содержанием Fe более 90%.
В последнее время в мире продвигается передовая технология ITmk3 (Ironmaking Technology mark 3 – технология получения чугуна 3-го поколения), позволяющая получать напрямую гранулированный металл (чугун) из рудно-топливных окатышей за 9-12 мин [2] (в доменной печи за 6-8 часов). Аналогично процессу «Fastmet», технология реализуется в печах с вращающимся подом, но при температурах выше 1350оС. Гранулированный металл и шлак крупностью 0-20 мм легко отделяются друг от друга на магнитном сепараторе. Металл может заменять часть металлолома в сталеплавильном переделе, а шлак может использоваться в дорожном строительстве и в строительной индустрии для производства цемента или в качестве наполнителя бетонов. Другими преимуществами этой технологии являются:
-снижение вредных выбросов в окружающую среду на 30% по сравнению с агрегатами аналогичной мощности в агло-коксо-доменном производстве;
-отсутствие затрат на обслуживание огненно-жидких шлаков;
-возможность переработки комплексного труднообогатимого сырья и отходов, вызывающих осложнения в доменном производстве;
-снижение удельных капитальных и эксплуатационных затрат на 20-30% по сравнению с традиционными технологиями.
Технико-экономические показатели технологии ITmk3 зависят от состава шихты для изготовления рудно-топливных окатышей. При этом расход твердого топлива должен обеспечить потребности в углероде на восстановление Fe (потребность в тепле на протекание эндотермических реакций реализуется за счет внешнего нагрева в печи с вращающимся подом), а состав пустой породы железосодержащего материала, золы твердого топлива и флюса (при необходимости) должны обеспечить условия формирования шлака с температурой плавления не выше 1400оС.
Пример
Восстановлению подвергается концентрат обогащения титаномагнетитовой руды месторождения Малый Куйбас, который содержит, %:
FeO Fe2O3 TiO2 V2O5 SiO2 CaO Al2O3 MgO
31,0 41,8 10,9 0,67 5,1 1,0 4,69 3,05
В известняке, %: СаО – 51,3; SiO2 – 0,2; MgO – 2,9; Al2O3 -0,03.
В качестве твердого топлива используется угольный концентрат с характеристиками, %: содержание золы (А) – 9,9, углерода (С) – 80,96.
Зола топлива содержит, %:
SiO2 CaO Al2O3 MgO
54,92 3,85 23,88 3,05
Расход твердого топлива определяем, исходя из стехиометрической потребности углерода на прямое восстановление
FeO + C = Fe + CO С/Fe=0,214
Fe2О3 + 3C = 2Fe + 3CO С/Fe=0,321
V2O5 + 5С= 2V + 5СО С/V=0,589
С целью упрощения расчет ведем на 10 г титаномагнетитового концентрата.
Тогда Fe в FeO составит 31*56/72=24,1% или в 10 г концентрата 2,41 .г, Fe в Fe2O3 -41,8*112/160=29,26% или 2,93 г, а V в V2O5 -0,67*102/182=0,38% или 0,038 г.
На восстановление Fe V потребуется 0,214*2,41+0,321*2,93+0,589*0,038=0,516+0,941+0,022=1,479 г С или 1,479/0,8096=1,8 г угольного концентрата.
Материалы на 10 г концентрата вносят, г (табл.9.1)
Таблица 9.1
Вклад в шлакообразование компонентов шихты
Материал | Шлакообразующие компоненты |
Tпл,оС | ||||
SiO2 | CaO | Al2О3 | MgO | сумма | ||
Концентрат, г | 0,51 | 0,1 | 0,469 | 0,305 | ||
Зола (0,18 г) | 0,10 | 0,01 | 0,043 | 0,005 | ||
Сумма, г | 0,61 | 0,11 | 0,512 | 0,310 | 1,542 | |
39,6 | 7,1 | 33,2 | 20,1 | 100% | >1400оC | |
Известняк (2,0) г) | 0,004 | 1,026 | 0,058 | |||
Сумма, г | 0,614 | 1,036 | 0,512 | 0,368 | 2,53 | |
24,3 | 40,9 | 20,2 | 14,6 | 100% | 1400оС |
Температуру плавления пустой породы и золы твердого топлива находим с помощью диаграмм состояния системы SiO2-CaO-Al2O3-MgO [15].
Выводы:
-на восстановление 1 т титанованадиевого концентрата потребуется 180 кг угольного концентрата;
-снизить температуру плавления до необходимого уровня возможно присадкой в шихту 200 кг известняка.
Задание к работе 9
Оперируя данными, представленными в табл. П.1 и табл. П.10, определить расход коксовой мелочи, обеспечивающий стехиометрическую потребность в углероде на прямое восстановление Fe и Mn. Используя диаграммы состояния системы SiO2-CaO-Al2O3-MgO (приложение - Рис. П.9-1-П.9-.4), оценить состав пустой породы концентрата, золы коксовой мелочи с точки зрения температуры плавления шлака. При необходимости выбрать флюс и его расход для достижения температуры плавления шлака не выше 1400оС.
ЛИТЕРАТУРА
1. Неясов А.Г. Расчеты шихты, материального и теплового балансов агломерационного процесса: Учеб. пособие.–Свердловск: изд.УПИ, 1983. – 68 с.
2. Panishev N.V., Dubrovsky B.A., Starikov A.I., Redin E.V. and Knyazev E.V., «Direct reduction of Ti-V magnetite via ITmk3 technology», pp. 45-48 in 4th International Symposium on High-Temperature Metallurgical Processing, San Antonio, Texas, USA, March 3-7, 2013
3. Павлов М.А. Металлургия чугуна: В 3-х ч. – 6-е изд. – М.: Металлургиздат. 1949. – Ч.2. Доменный процесс. - 628 с.
4. Справочник по обогащению руд: Подготовительные процессы/Под ред. О.С. Богданова, В.А. Олевского. – 2-е изд., перераб. и доп. – М.: Недра, 1982. – 366 с.
5. Вегман Е.Ф., Панишев Н.В., Борисов В.М. Эффективность прогрева компонентов агломерационной шихты в зоне интенсивного подогрева // Изв. вузов. Черная металлургия. – 1979. -№5. – с.16-19
6. .Андреев С.Е., Товаров В.В, Перов В.А. Закономерности измельчения и исчисления характерности гранулометрического состава. – М.: Металлургиздат, 1959. – 437 с.
7. Теплотехника окускования железорудного сырья/ Братчиков С. Г., Берман Ю.А., Белоцерковский Я.Л. и др. – М.: Металлургия, 1970. – 344 с.
8. Панишев Н.В. Практикум по курсу «Теория и технология подготовки сырья к доменной плавке»: Учеб. пособие.-Свердловск: Изд. УПИ. 1987. – 84 с.
9. Вегман Е.Ф. Краткий справочник доменщика. – М.: Металлургия, 1981. – 240 с.
10. . Коротич В.И. Сборник примеров и задач по курсу «Теория и технология подготовки сырья к доменной плавке»: Учеб. пособие. – Свердловск: Изд. УПИ, 1978. – 122 с.
11. Юсфин Ю.С., Доброскок В.А. Подготовка руд к плавке и металлургия чугуна: Задачник. – М.: Изд. МИСиС, 1980. – 76 с.
12. Стефанович М.А., Сибагатуллин С.К., Гущин Д.Н. Закономерности движения шихты и газов в доменной печи: монография. Магнитогорск: Изд-во Магнитогорск. гос. техн. ун-та им. Г.И. Носова, 2011. 161 с.
13. Металлургия чугуна / Е.Ф. Вегман, Б.Н. Жеребин, А.Н. Похвиснев, Ю.С. Юсфин и др. М.: Академкнига, 2004. 774 с.
14. Бабарыкин Н.Н. Теория и технология доменного процесса. Магнитогорск: ГОУ ВПО “МГТУ”, 2009. 257 с
15. Жило Н.Л. Формирование и свойства доменных шлаков. – М., Металлургия, 1974. 120 с.
ПРИЛОЖЕНИЕ
Таблица II.I – Химический состав железных руд и концентратов
Вариант | Месторождение железных руд | Материал | Содержание, % | |||||||||||
![]() | ![]() | ![]() | ![]() | ![]() | ![]() | ![]() | ![]() | ![]() | ![]() | ![]() | ![]() | |||
1 | Рудногорское | Руда | 38,40 | 0,09 | 0,44 | 0,05 | 6,70 | 12,40 | 5,80 | 9,90 | 8,40 | – | – | 1,30 |
Концентрат | 58,00 | 0,15 | 0,30 | 0,01 | 18,00 | 4,60 | 2,20 | 3,20 | 2,80 | 0,20 | 0,33 | 4,72 | ||
2 | Атасуйское | Аглоруда | 45,00 | 1,07 | 0,04 | 0,92 | 15,10 | 20,78 | 4,38 | 0,37 | – | – | – | 2,09 |
Концентрат | 50,00 | 0,60 | 0,04 | 0,47 | 23,40 | 17,57 | 3,60 | – | – | – | – | 3,50 | ||
3 | Аятское | Руда | 37,10 | 0,88 | 0,40 | 0,35 | 1,30 | 16,00 | 8,60 | 1,80 | 1,02 | – | – | 17,30 |
Концентрат | 52,00 | 1,16 | 0,41 | 0,10 | 25,00 | 14,60 | 8,50 | 1,60 | 0,90 | – | – | – | ||
4 | Лисаковское | Руда | 36,40 | – | 0,48 | 0,03 | – | 31,00 | 4,67 | 0,73 | – | – | – | 11,70 |
Концентрат | 47,46 | 0,29 | 0,61 | 0,05 | 0,66 | 10,94 | 4,96 | 0,65 | 0,59 | 0,25 | – | 12,77 | ||
5 | Абаканское | Руда | 45,50 | 0,07 | 0,19 | 2,30 | 7,10 | 13,80 | 4,20 | 4,10 | 2,20 | – | – | 3,50 |
Концентрат | 62,52 | 0,19 | 0,11 | 0,29 | 17,90 | 6,20 | 1,36 | 2,30 | 1,20 | 0,20 | – | 0,70 | ||
6 | Коршуновское | Руда | 34,50 | 0,05 | 0,26 | 0,04 | 11,30 | 23,40 | 5,70 | 9,00 | 9,70 | – | – | 9,70 |
Концентрат | 61,00 | 0,13 | 0,11 | – | 22,00 | 4,20 | 3,39 | 1,50 | 4,00 | 0,38 | – | 1,23 | ||
7 | Сарбайское | Руда (доменная) | 58,20 | 0,07 | 0,10 | 0,23 | 26,10 | 5,95 | 1,26 | 3,17 | 1,33 | 0,21 | – | 2,52 |
Концентрат | 66,10 | 0,10 | 0,05 | 0,33 | 27,05 | 3,86 | 1,25 | 1,12 | 0,89 | 0,24 | 0,15 | 1,39 |
Продолжение таблицы II.I
Вариант | Месторождение железных руд | Материал | Содержание, % | |||||||||||
![]() | ![]() | ![]() | ![]() | ![]() | ![]() | ![]() | ![]() | ![]() | ![]() | ![]() | ![]() | |||
8 | Качарское | Руда | 59,10 | 0,19 | 0,03 | 0,06 | 27,10 | 8,70 | 2,90 | 1,80 | 3,10 | – | – | 2,30 |
Концентрат | 65,00 | 0,19 | 0,02 | 0,10 | 28,68 | 4,50 | 2,00 | 0,90 | 1,00 | 0,08 | – | 0,40 | ||
9 | Михайловское (КМА) | Аглоруда | 57,28 | 0,05 | 0,04 | 0,22 | 13,10 | 10,42 | 1,69 | 0,32 | – | – | – | 4,46 |
Концентрат | 66,30 | 0,015 | 0,015 | 0,03 | 26,00 | 6,32 | 0,26 | 0,39 | – | – | 0,14 | 0,88 | ||
10 | Стойленское (КМА) | Аглоруда | 51,96 | 0,18 | 0,026 | 0,036 | 5,14 | 13,40 | 5,30 | 1,07 | 0,44 | – | – | 5,75 |
Концентрат | 65,60 | 0,046 | 0,016 | 0,049 | 27,50 | 7,50 | 0,45 | 0,22 | 0,50 | – | – | 0,55 | ||
11 | Соколовское | Аглоруда | 55,43 | 0,11 | 0,11 | 0,13 | 22,82 | 9,95 | 2,18 | 4,02 | 2,42 | 0,25 | 0,10 | 2,80 |
Концентрат | 66,20 | 0,09 | 0,04 | 0,34 | 27,10 | 4,00 | 0,99 | 1,10 | 0,85 | 0,23 | 0,11 | 1,40 | ||
12 | Лисаковское | Руда | 35,80 | 0,10 | 0,50 | 0,03 | – | 20,00 | 4,80 | 0,66 | – | – | – | 12,00 |
Концентрат | 60,00 | 0,23 | 0,74 | 0,02 | 20,00 | 7,86 | 5,26 | 0,60 | 0,50 | 0,10 | – | – | ||
13 | Лебединское (КМА) | Руда | 33,51 | – | 0,091 | 0,065 | 13,10 | 42,95 | 1,86 | 1,62 | 1,34 | 0,24 | – | – |
Концентрат | 58,00 | – | 0,009 | 0,02 | 26,50 | 4,50 | 0,15 | 0,30 | 0,40 | – | – | 0,30 | ||
14 | Криворожское | Руда | 33,00 | – | 0,035 | ,011 | – | 42,00 | 0,60 | 1,40 | 1,80 | – | – | – |
Концентрат | 65,00 | 0,09 | 0,004 | 0,01 | 20,84 | 8,19 | 0,22 | 0,55 | 0,35 | – | – | – | ||
15 | Ковдорское | Руда | 31,50 | – | 2,86 | 0,16 | 11,90 | 9,00 | 2,70 | 8,40 | 10,50 | 0,40 | – | – |
Концентрат | 63,48 | 0,44 | 0,09 | 0,20 | 23,48 | 0,72 | 0,65 | 0,53 | 4,73 | 1,25 | – | 1,30 | ||
16 | Керченское | Руда | 38,30 | 1,99 | 0,98 | 0,13 | – | 19,00 | 5,00 | 1,90 | 1,10 | – | – | 12,00 |
Концентрат | 46,07 | 2,12 | 1,16 | 0,097 | – | 10,77 | 3,30 | 1,34 | 0,74 | 0,11 | – | 11,55 | ||
17 | Дашкесанское | Руда | 36,00 | – | 0,10 | 0,066 | 13,00 | 20,03 | 4,70 | 14,00 | 1,30 | – | – | 1,20 |
Концентрат | 60,50 | – | 0,044 | 0,025 | 20,80 | 6,73 | 1,90 | 4,90 | 0,58 | – | – | 0,80 |
Продолжение таблицы II.I
Вариант | Месторождение железных руд | Материал | Содержание, % | |||||||||||
![]() | ![]() | ![]() | ![]() | ![]() | ![]() | ![]() | ![]() | ![]() | ![]() | ![]() | ![]() | |||
18 | Рудняны (Словакия) | Руда | 33,07 | 2,04 | 0,02 | 0,92 | 38,89 | 10,68 | 2,59 | 0,83 | 4,55 | – | – | 28,89 |
Концентрат | 46,96 | 2,25 | 0,21 | 0,03 | 18,09 | 11,05 | 1,83 | 2,57 | 3,86 | – | – | 4,03 | ||
19 | Лисаковское | Руда | 43,55 | – | 0,61 | – | – | 20,34 | 4,67 | 0,37 | 0,50 | – | – | 10,20 |
Концентрат | 48,34 | – | 0,68 | 0,02 | – | 11,10 | 4,66 | 0,39 | 0,41 | – | – | 11,42 | ||
20 | Лебединское (КМА) | Руда | 33,51 | – | 0,08 | 0,07 | 13,10 | 40,50 | 1,67 | 1,40 | 1,43 | – | – | – |
Концентрат | 66,34 | – | 0,009 | 0,02 | 24,00 | 7,24 | 0,25 | 1,40 | 0,30 | – | – | – | ||
21 | Коршуновское | Руда | 27,54 | 0,07 | 0,222 | 0,034 | 10,57 | 27,08 | 5,33 | 12,74 | 10,59 | 0,45 | – | 5,52 |
Концентрат | 62,30 | 0,05 | 0,13 | 0,008 | 22,80 | 4,06 | 2,69 | 2,12 | 3,13 | 0,33 | – | 1,24 | ||
22 | Ковдорское | Руда | 27,48 | 0,07 | 75 | 0,275 | 11,35 | 9,53 | – | 16,88 | 14,33 | 0,53 | – | 8,12 |
Концентрат | 63,48 | 0,004 | 0,09 | 0,305 | 23,48 | 0,72 | – | 0,53 | 4,73 | 1,25 | – | – | ||
23 | Запорожское | Руда | 52,00 | 0,016 | 0,021 | 0,005 | 1,00 | 23,20 | 1,00 | 0,11 | 0,18 | 0,048 | 0,23 | 0,75 |
Концентрат | 61,20 | 0,031 | 0,023 | 0,008 | 1,20 | 9,96 | 1,40 | 0,14 | 0,25 | 0,064 | 0,24 | 0,80 | ||
24 | Дашкесанское | Руда | 55,85 | 0,32 | 0,07 | 0,09 | 18,50 | 14,80 | 2,50 | 6,24 | 0,92 | 0,05 | – | 0,30 |
Концентрат | 60,50 | 0,31 | 0,04 | 0,08 | 23,00 | 8,60 | 1,70 | 3,90 | 0,90 | 0,04 | – | 0,21 | ||
25 | Ружнява (Словакия) | Руда | 37,02 | 1,96 | 0,02 | 0,26 | 45,40 | 14,06 | 2,23 | 0,99 | 3,52 | – | – | 27,00 |
Концентрат | 46,04 | 1,99 | 0,06 | 0,47 | 11,47 | 10,82 | 2,56 | 0,95 | 5,70 | – | – | 5,63 | ||
26 | Бакальское | Руда | 28,86 | 0,90 | 0,01 | 0,15 | 16,75 | 6,88 | 2,59 | 2,96 | 8,92 | – | – | 31,07 |
Концентрат | 40,77 | 0,50 | – | 0,189 | 8,02 | 10,82 | 2,56 | 4,50 | 13,02 | – | – | – | ||
27 | Высокогорское | Руда | 53,88 | 0,93 | 0,11 | 0,05 | 19,20 | 8,56 | 3,89 | 4,10 | 2,41 | – | – | 4,41 |
Концентрат | 58,07 | 0,77 | 0,074 | 0,05 | 20,00 | 8,08 | 2,30 | 3,10 | 1,80 | – | – | 3,00 |
Продолжение таблицы II.I
Вариант | Месторождение железных руд | Материал | Содержание, % | |||||||||||
![]() | ![]() | ![]() | ![]() | ![]() | ![]() | ![]() | ![]() | ![]() | ![]() | ![]() | ![]() | |||
28 | Оленегорское | Руда | 32,07 | 0,02 | 0,023 | 0,033 | 9,53 | 47,72 | 1,76 | 1,62 | 2,10 | – | – | 3,10 |
Концентрат | 65,08 | 0,01 | 0,014 | 0,052 | 22,39 | 8,09 | 0,10 | 0,11 | 0,13 | – | – | 2,70 | ||
29 | Криворожское | Руда | 48,40 | 0,016 | 0,026 | 0,07 | 0,93 | 28,90 | 0,61 | 0,12 | 0,06 | 0,036 | 0,19 | 0,78 |
Концентрат | 55,81 | 0,016 | 0,026 | 0,08 | 0,78 | 18,10 | 0,75 | 0,13 | 0,09 | 0,025 | 0,25 | 0,91 | ||
30 | Абаканское | Аглоруда | 44,90 | 0,09 | 0,20 | 1,90 | 6,90 | 13,30 | 4,10 | 4,00 | 2,20 | – | – | 3,30 |
Концентрат | 60,45 | 0,15 | 0,11 | 0,52 | 20,00 | 7,38 | 1,50 | 2,28 | 1,40 | 0,13 | – | 1,30 | ||
31 | Криворожское | Руда | 47,26 | 0,016 | 0,015 | 0,008 | 1,26 | 31,10 | 0,414 | 0,12 | 0,08 | 0,022 | 0,26 | 0,35 |
Концентрат | 56,81 | 0,016 | 0,026 | 0,008 | 0,78 | 18,10 | 0,85 | 0,13 | 0,09 | 0,025 | 0,25 | 0,91 | ||
32 | Лебединское (КМА) | Руда | 35,60 | 0,06 | 0,06 | 0,07 | 12,90 | 41,60 | 1,90 | 1,50 | 1,30 | 0,20 | – | 0,30 |
Концентрат | 71,70 | 0,01 | 0,03 | 0,01 | 27,30 | 0,35 | 0,15 | 0,10 | 0,10 | 0,01 | – | 0,12 | ||
33 | Южно-Коробковское (КМА) | Руда | 33,20 | 0,015 | 0,007 | 0,008 | 11,50 | 44,00 | 3,90 | 2,30 | 2,19 | – | – | 0,50 |
Концентрат | 68,20 | 0,016 | 0,023 | 0,03 | 28,00 | 4,80 | 0,25 | 0,30 | 0,29 | – | – | 0,30 | ||
34 | Керченское | Руда | 39,10 | 2,00 | 0,97 | 0,17 | – | 18,80 | 5,10 | 1,20 | 1,70 | – | – | 11,90 |
Концентрат | 55,10 | 1,78 | 1,49 | 0,16 | 16,30 | 10,09 | 4,15 | 0,20 | 2,00 | – | – | 2,10 | ||
35 | Качканарское | Руда | 21,00 | 0,09 | 0,01 | 0,02 | 3,75 | 32,30 | 11,70 | 19,70 | 13,30 | – | – | 1,30 |
Концентрат | 63,00 | 0,16 | 0,01 | 0,02 | 25,30 | 4,39 | 1,54 | 1,73 | 2,39 | – | – | 0,70 | ||
36 | Соколовское | Руда | 52,30 | 0,12 | 0,04 | 0,34 | 20,10 | 10,10 | 2,10 | 4,00 | 2,30 | 0,20 | – | 0,60 |
Концентрат | 64,08 | 0,09 | 0,03 | 1,01 | 26,09 | 4,00 | 1,65 | 1,35 | 1,09 | 0,22 | – | 1,98 | ||
37 | Лисаковское | Руда | 33,80 | 0,10 | 0,45 | 0,03 | – | 21,40 | 7,90 | 5,20 | 0,55 | 0,40 | – | 13,00 |
Концентрат | 47,46 | 0,29 | 0,61 | 0,05 | 1,00 | 10,94 | 4,96 | 0,65 | 0,69 | – | – | 12,75 |
Продолжение таблицы II.I
Вариант | Месторождение железных руд | Материал | Содержание, % | |||||||||||
![]() | ![]() | ![]() | ![]() | ![]() | ![]() | ![]() | ![]() | ![]() | ![]() | ![]() | ![]() | |||
38 | Криворожское | Руда | 5,70 | 0,04 | 0,015 | 0,01 | – | 16,10 | 1,15 | 0,12 | 0,10 | – | – | 1,00 |
Концентрат | 65,00 | 0,01 | 0,01 | – | – | 8,41 | 0,27 | 0,04 | 0,25 | – | – | 1,01 | ||
39 | Оленегорское | Руда | 33,90 | 0,03 | 0,023 | 0,03 | 10,00 | 45,80 | 1,80 | 1,60 | 2,00 | – | – | 3,10 |
Концентрат | 65,00 | 0,08 | 0,01 | 0,05 | 22,10 | 8,19 | 0,20 | 0,55 | 0,35 | – | – | 0,16 | ||
40 | Коршуновское | Руда | 28,30 | 0,07 | 0,22 | 0,05 | 11,00 | 25,40 | 5,60 | 1,06 | 10,50 | 0,50 | – | 5,10 |
Концентрат | 61,30 | 0,13 | 0,11 | 0,21 | 23,10 | 4,15 | 3,35 | 1,45 | 4,00 | – | – | 1,15 | ||
41 | Криворожское | Руда | 56,30 | 0,05 | 0,03 | 0,02 | 0,80 | 17,10 | 0,95 | 0,15 | 0,12 | – | – | 0,90 |
Концентрат | 68,00 | 0,05 | 0,01 | 0,02 | 0,90 | 5,30 | 0,08 | 0,14 | 0,25 | – | – | 0,20 | ||
42 | Лебединское (КМА) | Руда | 34,70 | 0,05 | 0,07 | 0,07 | 9,90 | 40,10 | 1,37 | 1,33 | 1,41 | – | – | – |
Концентрат | 71,70 | 0,03 | 0,003 | 0,01 | 25,10 | 0,34 | 0,15 | 0,10 | 0,10 | – | – | 0,12 | ||
43 | Лебединское (КМА) | Руда | 35,10 | 0,08 | 0,08 | 0,07 | 11,70 | 41,20 | 1,50 | 1,42 | 1,43 | – | – | – |
Концентрат | 68,00 | 0,10 | 0,012 | 0,02 | 25,10 | 4,10 | 0,17 | 0,30 | 0,40 | – | – | 0,30 | ||
44 | Губкинское (КМА) | Руда | 57,30 | 0,05 | 0,035 | 0,03 | 14,70 | 10,50 | 0,06 | 1,69 | 0,35 | – | – | 4,30 |
Концентрат | 69,00 | 0,02 | 0,02 | 0,02 | 27,90 | 3,70 | 0,04 | 0,22 | 0,25 | – | – | 0,30 | ||
45 | Коробковское (КМА) | Руда | 35,10 | 0,02 | 0,01 | 0,007 | 9,90 | 45,10 | 3,80 | 2,10 | 2,20 | – | – | 0,45 |
Концентрат | 63,40 | 0,08 | 0,03 | 0,13 | 27,50 | 9,92 | 0,53 | 0,57 | 0,86 | – | – | 0,23 | ||
46 | Ено-Ковдорское | Руда | 31,80 | 0,21 | 2,50 | 0,09 | 11,30 | 8,80 | 2,50 | 8,50 | 10,40 | 0,30 | – | 2,00 |
Концентрат | 62,50 | 0,45 | 0,16 | 0,07 | 22,90 | 1,64 | 2,35 | 0,85 | 5,70 | – | – | 1,80 | ||
47 | Качарское | Руда | 57,30 | 0,20 | 0,03 | 0,07 | 25,30 | 8,90 | 3,00 | 1,90 | 3,00 | – | – | 2,20 |
Концентрат | 64,30 | 0,31 | 0,02 | 0,12 | 27,70 | 4,32 | 2,10 | 1,10 | 1,00 | 0,07 | – | 0,40 |
Продолжение таблицы II.I
Вариант | Месторождение железных руд | Материал | Содержание, % | |||||||||||
![]() | ![]() | ![]() | ![]() | ![]() | ![]() | ![]() | ![]() | ![]() | ![]() | ![]() | ![]() | |||
48 | Аятское | Руда | 36,90 | 0,90 | 0,40 | 0,35 | 1,10 | 17,00 | 8,90 | 1,70 | 1,00 | – | – | 18,00 |
Концентрат | 51,80 | 1,20 | 0,40 | 0,20 | 24,30 | 13,90 | 8,30 | 1,40 | 0,70 | – | – | 0,70 | ||
49 | Абаканское | Руда | 43,00 | 0,07 | 0,19 | 2,10 | 6,90 | 13,80 | 4,20 | 3,90 | 2,30 | – | – | 3,30 |
Концентрат | 63,00 | 0,20 | 0,15 | 0,30 | 17,80 | 6,30 | 1,40 | 2,50 | 1,20 | 0,20 | – | 0,60 | ||
50 | Абаканское | Руда | 45,40 | 0,09 | 0,20 | 2,30 | 11,20 | 13,60 | 4,10 | 4,10 | 2,20 | 0,10 | – | 3,40 |
Концентрат | 60,45 | 0,15 | 0,11 | 0,52 | 20,00 | 7,38 | 1,50 | 2,28 | 1,40 | 0,13 | – | 1,30 |
Таблица П.2
Сходные данные и условия для выполнения работы 2
Вариант | Формулировка задачи | Исходные данные | |||||
![]() | ![]() | ![]() | ![]() | ![]() | E, % | ||
1 | Сырые окатыши, полученные в барабанном окомкователе, подвергаются грохочению на сите с ячейками 12х70 мм с целью отделения некондиционных окатышей крупностью менее 12 мм, которые вновь используют в процессе окомкования в качестве зародышей. Рассчитать основные показатели грохочения, если дано содержание окатышей меньше 12 мм в исходном ( | 66 | 100 | 65 | - | - | - |
2 | 70 | 98 | 65 | - | - | - | |
3 | 73 | 99 | 70 | - | - | - | |
4 | 58 | 97 | 55 | - | - | - | |
5 | 50 | 100 | 49 | - | - | - | |
6 | 52 | 99 | 48 | - | - | - | |
7 | 60 | 100 | 58 | - | - | - | |
8 | 65 | 98 | 63,5 | - | - | - | |
9 | 67 | 99 | 66 | - | - | - | |
10 | Из коксовой мелочи после измельчения в валковых дробилках грохочением на сите 3х3 мм отделяется фракция крупнее 3 мм для повторного измельчения. По технологическим условиям содержание фракции крупнее 3 мм в топливе для агломерации не должно превышать 5 %. Определить содержание в готовом топливе фракции 0-3 мм, если известны эффективность разделения (E), содержание этой фракции в топливе после измельчения ( | 65 | - | 64 | - | - | 95 |
11 | 60 | - | 60 | - | - | 97 | |
12 | 70 | - | 70 | - | - | 96 | |
13 | 90 | - | 75 | - | - | 80 | |
14 | 66 | - | 64 | - | - | 95 | |
15 | 80 | - | 75 | - | - | 90 | |
16 | 75 | - | 74 | - | - | 96 | |
17 | 68 | - | 67 | - | - | 98 | |
18 | 78 | - | 76 | - | - | 90 | |
19 | 50 | - | 49 | - | - | 85 |
Продолжение табл.П.2
Вариант | Формулировка задачи | Исходные данные | |||||
![]() | ![]() | ![]() | ![]() | ![]() | E, % | ||
20 | Для формирования донной и бортовой "постели" используют обожженные окатыши крупнее 5мм. Определить необходимую эффективность отсева из окатышей мелочи 0-5 мм, если известно её содержание в окатышах ( | 11 | 100 | - | - | - | - |
21 | 9,5 | 100 | - | - | - | - | |
22 | 5 | 100 | - | - | - | - | |
23 | 6,5 | 100 | - | - | - | - | |
24 | 7,0 | 100 | - | - | - | - | |
25 | Для интенсификации процесса спекания тонких железорудных концентратов в шихту вводят аглоруду, которую получают путём отсева мелких фракций 0-8 мм из богатых руд. В то же время руды крупнее 8 мм спекаются плохо и дают легко разрушающийся агломерат, поэтому содержание фракций крупнее 8 мм ограничивают в аглоруде до 2,5%. При известном содержании фракции 0-8 мм в исходной руде ( | 40 | - | - | 12 | - | - |
26 | 55 | - | - | 15 | - | - | |
27 | 30 | - | - | 18 | - | - | |
28 | 28 | - | - | 9 | - | - | |
29 | 32 | - | - | 7 | - | - | |
30 | 37 | - | - | 11 | - | - | |
31 | После пребывания в охладителе агломерат перед транспортировкой в доменный цех подвергается грохочению на самобалансном грохоте, на котором установлены сита с ячейками 5х5 мм. Определить "замельчённость" агломерата фракцией 0-5 мм, содержание которой не должно превышать 5%. Грохочение ведётся с известной эффективностью (E). Содержание мелочи в исходном материале ( | 30 | 100 | - | - | - | 85 |
32 | 20 | 100 | - | - | - | 98 | |
33 | 15 | 100 | - | - | - | 96 | |
34 | 18 | 100 | - | - | - | 96 | |
35 | 21 | 100 | - | - | - | 80 | |
36 | 18 | 100 | - | - | - | 92 | |
37 | 16 | 100 | - | - | - | 93 | |
38 | 16 | 100 | - | - | - | 95 | |
39 | 19 | 100 | - | - | - | 90 | |
40 | 17 | 100 | - | - | - | 94 |
Окончание табл.П.2
Вариант | Формулировка задачи | Исходные данные | |||||
![]() | ![]() | ![]() | ![]() | ![]() | E, % | ||
41 | В зимнее время для предупреждения примерзания сыпучих железорудных материалов днище железнодорожных вагонов посыпают возвратом агломерационного производства. Перед засыпкой из возврата отсеивают фракции мельче 10 мм. Известно извлечение мелких фракций в подрещётный продукт на сите 10х10 мм, а также содержание мелочи 0-10мм в исходном возврате. Найти "замельчённость" продукта. Содержание мелочи в нём не должно превышать 15%. Если требуется, дать рекомендации | 85 | 100 | - | - | 94 | - |
42 | 80 | 100 | - | - | 90 | - | |
43 | 90 | 100 | - | - | 96 | - | |
44 | 86 | 100 | - | - | 92 | - | |
45 | 82 | 100 | - | - | 98 | - | |
46 | 86 | 100 | - | - | 95 | - | |
47 | 90 | 100 | - | - | 99 | - | |
48 | 95 | 100 | - | - | 96 | - | |
49 | 88 | 100 | - | - | 90 | - | |
50 | 86 | 100 | - | - | 96 | - |
Таблица П.3
Гранулометрический состав сырых материалов
Вариант | Материал | Содержание классов, % | |||||||||||||
0-0,045 | 0,045-0,074 | 0,074-0,1 | 0,1-0,5 | 0,5-1,0 | 1,0-3,0 | 3,0-5,0 | 5,0-8,0 | 8,0-12,0 | 12,0-15,0 | 15,0-25,0 | 25,0-40,0 | 40,0-60,0 | 60,0-80,0 | ||
1 | Коксовая мелочь | - - - | - - - | - - - | 15,3 20,8 31,9 | 16,4 23,5 33,0 | 62,0 51,2 33,6 | 6,2 4,5 1,5 | - - - | - - - | - - - | - - - | - - - | - - - | - - - |
2 | Аглоруда | - - - | - - - | - - - | 10,0 14,8 18,3 | 6,2 21,3 16,8 | 12,9 45,2 17,5 | 15,7 15,3 18,1 | 50,0 2,1 14,9 | 3,5 1,2 14,4 | 1,7 - - | - - - | - - - | - - - | - - - |
3 | Кокс | - - - | - - - | - - - | - - - | - - - | - - - | - - - | - - - | - - - | 1,0 - - | 1,5 6,0 0,8 | 13,3 49,7 67,3 | 22,9 43,6 24,2 | 61,3 0,7 7,7 |
4 | Известняк | - - - | - 7,5 - | 2,5 11,3 17,6 | 15,7 56,2 24,2 | 23,6 14,3 33,3 | 52,1 8,8 18,0 | 5,2 1,9 6,9 | 0,9 - - | - - - | - - - | - - - | - - - | - - - | - - - |
5 | Известняк | 3,7 81,7 21,7 | 27,5 7,7 28,3 | 63,3 3,5 29,1 | 3,8 7,1 20,9 | 1,7 - - | - - - | - - - | - - - | - - - | - - - | - - - | - - - | - - - | - - - |
6 | Агломерат | - - - | - - - | - - - | - - - | 1,7 - 1,9 | 2,1 - 1,9 | 6,3 - 2,8 | 17,2 4,0 65,2 | 23,2 5,3 12,9 | 14,6 1,7 11,1 | 17,9 3,3 3,7 | 14,1 37,9 - | 2,9 41,9 0,5 | - 5,9 - |
Продолжение табл.П3
Вариант | Материал | Содержание классов, % | |||||||||||||
0-0,045 | 0,045-0,074 | 0,074-0,1 | 0,1-0,5 | 0,5-1,0 | 1,0-3,0 | 3,0-5,0 | 5,0-8,0 | 8,0-12,0 | 12,0-15,0 | 15,0-25,0 | 25,0-40,0 | 40,0-60,0 | 60,0-80,0 | ||
7 | Концентрат обогащения железной руды | 70,0 73,6 5,2 | 5,6 9,7 6,7 | 8,1 7,7 36,1 | 10,1 9,0 50,3 | 6,2 - 1,7 | - - - | - - - | - - - | - - - | - - - | - - - | - - - | - - - | - - - |
8 | Аглошихта | - - - | - - - | - - - | - - - | 8,1 - 2,5 | 43,3 0,6 16,3 | 30,9 14,7 48,5 | 9,7 25,2 4,0 | 4,3 38,7 12,2 | 3,7 17,7 14,6 | - 3,1 1,9 | - - - | - - - | - - - |
9 | Бентонит | 89,3 77,9 90,5 | 7,8 18,6 4,9 | 2,6 3,5 1,7 | 0,3 - 2,9 | - - - | - - - | - - - | - - - | - - - | - - - | - - - | - - - | - - - | - - - |
10 | Колошниковая пыль | 3,5 21,7 48,5 | 2,9 38,6 26,7 | 17,6 36,5 17,5 | 50,6 3,2 4,8 | 25,2 - 2,5 | - - - | - - - | - - - | - - - | - - - | - - - | - - - | - - - | - - - |
11 | Кокс | - - - | - - - | - - - | - - - | - - - | - - - | - - - | - - - | - - - | 16,2 - - | 5,6 3,7 0,7 | 47,8 36,3 17,0 | 15,1 26,9 13,9 | 15,3 33,1 68,4 |
12 | Окалина | - - - | - - - | - 2,8 - | 6,1 21,3 38,3 | 47,9 20,8 23,6 | 36,6 17,6 19,5 | 4,2 30,6 18,6 | 3,7 6,9 - | 1,5 - - | - - - | - - - | - - - | - - - | - - - |
13 | Коксовая мелочь | 1,7 - - | 3,9 5,2 2,7 | 22,2 13,8 21,7 | 56,3 19,7 34,5 | 14,8 61,3 11,3 | 1,1 - 19,1 | - - 10,7 | - - - | - - - | - - - | - - - | - - - | - - - | - - - |
Продолжение табл.П.3
Вариант | Материал | Содержание классов, % | |||||||||||||
0-0,045 | 0,045-0,074 | 0,074-0,1 | 0,1-0,5 | 0,5-1,0 | 1,0-3,0 | 3,0-5,0 | 5,0-8,0 | 8,0-12,0 | 12,0-15,0 | 15,0-25,0 | 25,0-40,0 | 40,0-60,0 | 60,0-80,0 | ||
14 | Концентрат обогащения железной руды | 50,3 61,8 17,3 | 13,9 14,3 28,6 | 21,7 18,2 34,3 | 12,8 5,7 15,4 | 1,3 - 4,4 | - - - | - - - | - - - | - - - | - - - | - - - | - - - | - - - | - - - |
15 | Аглошихта | - - - | - - - | - - - | - - - | 12,9 5,8 - | 23,8 16,3 22,7 | 13,5 21,9 38,5 | 13,7 23,7 19,6 | 20,8 30,8 10,1 | 15,3 1,5 9,1 | - - - | - - - | - - - | - - - |
16 | Кокс | - - - | - - - | - - - | - - - | - - - | - - - | - - - | - - - | - 0,3 - | 0,8 2,1 - | 1,5 3,3 1,5 | 37,9 29,1 26,3 | 40,5 41,6 25,9 | 19,3 23,6 46,3 |
17 | Агломерат | - - - | - - - | - - - | - - - | - - - | 0,5 1,7 - | 4,5 5,8 1,4 | 16,7 17,9 5,6 | 22,7 20,2 10,6 | 7,8 31,8 17,9 | 16,3 20,6 23,8 | 13,2 2,0 40,7 | 7,9 - - | 10,4 - - |
18 | Аглоруда | - - - | - - - | - 2,8 8,7 | 12,0 3,4 11,3 | 18,8 5,3 12,1 | 24,7 2,8 16,3 | 22,3 24,0 3,7 | 17,9 43,3 28,5 | 2,6 7,9 9,3 | 1,7 10,5 9,6 | - - 0,5 | - - - | - - - | - - - |
19 | Коксовая мелочь | 2,8 - 1,3 | 30,7 - 5,8 | 15,3 1,7 16,7 | 14,8 4,9 3,9 | 16,3 13,8 18,8 | 13,9 72,7 38,2 | 5,7 6,9 5,3 | 0,5 - - | - - - | - - - | - - - | - - - | - - - | - - - |
20 | Аглоруда | 15,5 - - | 20,3 10,0 - | 15,3 7,7 3,8 | 8,7 15,8 40,5 | 13,5 22,0 7,7 | 8,3 16,5 3,7 | 2,7 7,9 17,1 | 11,5 13,7 20,9 | 3,2 4,3 6,3 | - 2,1 - | - - - | - - - | - - - | - - - |
Продолжение таблицы II.3
Вариант | Материал | Содержание классов, % | |||||||||||||
0-0,045 | 0,045-0,074 | 0,074-0,1 | 0,1-0,5 | 0,5-1,0 | 1,0-3,0 | 3,0-5,0 | 5,0-8,0 | 8,0-12,0 | 12,0-15,0 | 15,0-25,0 | 25,0-40,0 | 40,0-60,0 | 60,0-80,0 | ||
21 | Аглошихта | – | – | – | – | 0,7 | 13,1 | 21,8 | 40,5 | 16,1 | 7,8 | – | – | – | – |
– | – | – | – | – | 30,0 | 15,6 | 9,7 | 22,0 | 16,6 | 6,1 | – | – | – | ||
– | – | – | – | 1,3 | 16,0 | 16,0 | 19,0 | 11,1 | 25,3 | 11,3 | – | – | – | ||
22 | Окатыши | – | – | – | – | – | 3,3 | 5,0 | 17,3 | 10,0 | 20,0 | 44,4 | – | – | – |
– | – | – | – | 1,5 | 2,7 | 4,4 | 16,8 | 11,7 | 23,4 | 39,5 | – | – | – | ||
– | – | – | – | 2,5 | 6,0 | 0,7 | 18,1 | 9,9 | 19,2 | 43,6 | – | – | – | ||
23 | Известняк | 8,8 | 11,2 | 6,0 | 5,8 | 23,9 | 39,0 | 5,3 | – | – | – | – | – | – | – |
– | 7,1 | 23,7 | 56,0 | 3,9 | 5,2 | 3,3 | 0,8 | – | – | – | – | – | – | ||
5,8 | 16,0 | 28,2 | 41,8 | 8,2 | – | – | – | – | – | – | – | – | – | ||
24 | Окатыши | – | – | – | – | – | – | 16,5 | 15,6 | 39,6 | 26,2 | 2,1 | – | – | – |
– | – | – | – | – | – | 15,5 | 9,2 | 45,3 | 28,3 | 1,7 | – | – | – | ||
– | – | – | – | – | 4,8 | 3,7 | 7,2 | 15,7 | 65,3 | 3,3 | – | – | – | ||
25 | Аглоруда | 3,5 | 0,7 | 6,4 | 6,6 | 21,1 | 17,9 | 23,0 | 15,7 | 2,0 | 3,1 | – | – | – | – |
2,1 | 2,0 | 5,2 | 13,3 | 19,6 | 43,2 | 11,2 | 2,7 | 0,7 | – | – | – | – | – | ||
– | 2,5 | 27,8 | 24,2 | 13,9 | 7,5 | 9,6 | 7,5 | 5,7 | 1,3 | – | – | – | – | ||
26 | Колошниковая пыль | 20,7 | 19,9 | 38,5 | 12,1 | 6,2 | 2,6 | – | – | – | – | – | – | – | – |
17,6 | 11,3 | 16,3 | 40,5 | 13,8 | 0,5 | – | – | – | – | – | – | – | – | ||
7,5 | 16,8 | 29,7 | 30,0 | 3,9 | 12,1 | – | – | – | – | – | – | – | – | ||
27 | Агломерат | 0,7 | 1,5 | 1,5 | 0,9 | 2,0 | 3,1 | 0,9 | 16,1 | 11,2 | 8,4 | 13,7 | – | 40,0 | – |
– | 0,9 | 0,7 | 3,0 | 0,4 | 0,4 | 2,2 | 40,7 | 6,0 | 12,2 | 3,7 | 5,8 | 7,9 | 16,1 | ||
0,3 | 0,7 | 1,3 | 0,9 | 0,4 | 0,6 | 0,8 | 17,0 | 12,2 | 21,8 | 20,0 | 9,9 | 3,3 | 10,8 |
Продолжение таблицы II.3
Вариант | Материал | Содержание классов, % | |||||||||||||
0-0,045 | 0,045-0,074 | 0,074-0,1 | 0,1-0,5 | 0,5-1,0 | 1,0-3,0 | 3,0-5,0 | 5,0-8,0 | 8,0-12,0 | 12,0-15,0 | 15,0-25,0 | 25,0-40,0 | 40,0-60,0 | 60,0-80,0 | ||
28 | Бентонит | 70,6 | 28,0 | 1,3 | 0,1 | – | – | – | – | – | – | – | – | – | – |
50,4 | 47,3 | 0,8 | 1,5 | – | – | – | – | – | – | – | – | – | – | ||
20,5 | 76,9 | 1,8 | 0,8 | – | – | – | – | – | – | – | – | – | – | ||
29 | Окатыши | – | – | – | – | – | 1,5 | 2,0 | 3,7 | 30,5 | 52,5 | 9,8 | – | – | – |
– | – | – | – | – | 0,7 | 1,8 | 1,4 | 34,0 | 48,1 | 14,0 | – | – | – | ||
– | – | – | – | – | 0,6 | 1,7 | 1,3 | 28,4 | 54,3 | 13,7 | – | – | – | ||
30 | Коксовая мелочь | 0,5 | 6,5 | 15,0 | 40,5 | 13,3 | 17,6 | 5,1 | 1,5 | – | – | – | – | – | – |
0,1 | 0,4 | 6,7 | 1,5 | 25,2 | 60,3 | 5,0 | 0,8 | – | – | – | – | – | – | ||
0,3 | 0,9 | 9,3 | 15,2 | 50,8 | 17,5 | 3,0 | 3,0 | – | – | – | – | – | – | ||
31 | Концентрат обогащения железной руды | 17,5 | 59,3 | 13,7 | 8,2 | 1,3 | – | – | – | – | – | – | – | – | – |
61,2 | 30,3 | 7,0 | 1,5 | – | – | – | – | – | – | – | – | – | – | ||
40,6 | 50,1 | 5,5 | 3,0 | 0,8 | – | – | – | – | – | – | – | – | – | ||
32 | Агломерат | 0,2 | – | 0,5 | 1,5 | 0,3 | 1,5 | 1,0 | 23,0 | 17,9 | 21,6 | 13,3 | 11,7 | 7,2 | 0,3 |
– | – | – | – | 3,1 | 1,3 | 0,5 | 14,0 | 13,0 | 17,1 | 43,1 | 5,3 | 1,0 | 1,6 | ||
– | – | – | 2,7 | 3,0 | 1,0 | – | 40,5 | 26,7 | 14,5 | 11,0 | 0,6 | – | – | ||
33 | Аглошихта | – | – | – | 0,1 | 5,3 | 17,6 | 40,4 | 20,0 | 15,7 | 0,9 | – | – | – | – |
– | – | – | – | 3,5 | 15,0 | 25,5 | 38,6 | 17,3 | 0,1 | – | – | – | – | ||
– | – | 0,8 | 1,5 | 6,2 | 13,7 | 15,3 | 40,5 | 20,5 | 1,5 | – | – | – | – | ||
34 | Аглоруда | 0,7 | 0,5 | 1,5 | 4,7 | 28,7 | 8,0 | 33,0 | 17,2 | 4,8 | 0,9 | – | – | – | – |
– | 0,3 | 0,2 | 1,6 | 9,3 | 17,3 | 40,1 | 28,3 | 1,7 | 1,2 | – | – | – | – | ||
0,4 | 2,4 | 4,3 | 7,7 | 38,5 | 21,6 | 14,2 | 6,3 | 3,3 | 0,3 | – | – | – | – |
Продолжение таблицы II.3
Вариант | Материал | Содержание классов, % | |||||||||||||
0-0,045 | 0,045-0,074 | 0,074-0,1 | 0,1-0,5 | 0,5-1,0 | 1,0-3,0 | 3,0-5,0 | 5,0-8,0 | 8,0-12,0 | 12,0-15,0 | 15,0-25,0 | 25,0-40,0 | 40,0-60,0 | 60,0-80,0 | ||
35 | Кокс* | – | – | – | – | – | – | – | – | 0,3* | 1,5* | 3,0* | 11,2 | 40,7 | 43,3 |
– | – | – | – | – | – | – | – | 0,5 | 3,0 | 5,7 | 66,6 | 12,3 | 11,9 | ||
– | – | – | – | – | – | – | 1,7 | 0,9 | 3,1 | 4,1 | 29,7 | 46,0 | 14,5 | ||
36 | Концентрат обогащения железной руды | 28,6 | 50,1 | 20,3 | 0,7 | 0,3 | – | – | – | – | – | – | – | – | – |
66,5 | 12,3 | 17,2 | 2,3 | 1,5 | 0,2 | – | – | – | – | – | – | – | – | ||
70,1 | 13,3 | 11,6 | 5,0 | – | – | – | – | – | – | – | – | – | – | ||
37 | Концентрат обогащения железной руды | 60,1 | 31,3 | 3,9 | 4,7 | – | – | – | – | – | – | – | – | – | – |
55,6 | 38,3 | 6,0 | 0,1 | – | – | – | – | – | – | – | – | – | – | ||
58,3 | 28,2 | 6,1 | 6,2 | 1,2 | – | – | – | – | – | – | – | – | – | ||
38 | Бентонит | 70,6 | 23,8 | 5,6 | – | – | – | – | – | – | – | – | – | – | – |
69,3 | 25,1 | 3,5 | 2,0 | 0,1 | – | – | – | – | – | – | – | – | – | ||
65,3 | 30,7 | 4,0 | – | – | – | – | – | – | – | – | – | – | – | ||
39 | Окатыши | – | – | – | – | – | 0,2 | 0,8 | 6,3 | 40,6 | 46,3 | 5,8 | – | – | – |
– | – | – | – | – | 0,3 | 0,8 | 5,6 | 35,5 | 51,8 | 6,0 | – | – | – | ||
– | – | – | – | – | 0,3 | 0,9 | 4,8 | 42,1 | 49,3 | 2,6 | – | – | – | ||
40 | Окалина | – | 0,3 | 20,0 | 50,6 | 17,8 | 4,1 | 4,2 | 3,0 | – | – | – | – | – | – |
0,4 | 0,8 | 21,7 | 45,3 | 21,2 | 3,7 | 2,9 | 4,0 | – | – | – | – | – | – | ||
– | 1,3 | 10,3 | 16,0 | 23,7 | 43,8 | 3,7 | 1,2 | – | – | – | – | – | – | ||
41 | Коксовая мелочь | 15,0 | 17,3 | 40,5 | 15,1 | – | 4,6 | 6,0 | 1,5 | – | – | – | – | – | – |
7,5 | 11,8 | 20,6 | 23,0 | 24,0 | 5,1 | 6,5 | 1,5 | – | – | – | – | – | – | ||
1,7 | 2,3 | 11,9 | 16,4 | 11,9 | 50,3 | 5,1 | 0,4 | – | – | – | – | – | – |
Продолжение таблицы II.3
Вариант | Материал | Содержание классов, % | |||||||||||||
0-0,045 | 0,045-0,074 | 0,074-0,1 | 0,1-0,5 | 0,5-1,0 | 1,0-3,0 | 3,0-5,0 | 5,0-8,0 | 8,0-12,0 | 12,0-15,0 | 15,0-25,0 | 25,0-40,0 | 40,0-60,0 | 60,0-80,0 | ||
42 | Концентрат обогащения железной руды | 40,3 | 36,6 | 16,0 | 3,9 | 3,2 | – | – | – | – | – | – | – | – | – |
38,2 | 33,0 | 20,1 | 3,7 | 4,7 | 0,3 | – | – | – | – | – | – | – | – | ||
43,5 | 30,0 | 19,4 | 6,5 | 0,6 | – | – | – | – | – | – | – | – | – | ||
43 | Агломерат | 0,3 | 0,5 | 0,7 | 0,9 | 1,2 | 0,3 | 1,4 | 47,0 | 38,2 | 8,3 | 1,2 | – | – | – |
0,5 | – | – | 1,3 | – | 3,1 | 1,5 | 28,2 | 50,6 | 9,7 | 3,2 | 1,0 | 0,9 | – | ||
– | – | 1,7 | 1,5 | – | 0,6 | 2,1 | 16,3 | 32,3 | 43,5 | 1,5 | 0,2 | 0,3 | – | ||
44 | Колошниковая пыль | 11,7 | 16,0 | 7,7 | 23,0 | 40,1 | 1,5 | – | – | – | – | – | – | – | – |
40,7 | 23,0 | 16,3 | 9,0 | 11,0 | – | – | – | – | – | – | – | – | – | ||
22,2 | 39,9 | 27,4 | 8,1 | 2,4 | – | – | – | – | – | – | – | – | – | ||
45 | Окалина | 0,9 | 7,9 | 16,8 | 46,7 | 21,7 | 3,7 | 2,2 | 0,1 | – | – | – | – | – | – |
2,4 | 39,9 | 21,7 | 19,8 | 15,6 | 0,6 | – | – | – | – | – | – | – | – | ||
1,5 | 19,1 | 43,8 | 20,5 | 11,7 | 3,4 | – | – | – | – | – | – | – | – | ||
46 | Окатыши | – | – | – | – | – | – | 0,2 | 0,4 | 14,3 | 70,4 | 7,3 | 3,8 | 3,6 | – |
– | – | – | – | – | – | 0,5 | 0,6 | 13,7 | 65,0 | 13,8 | 2,9 | 3,5 | – | ||
– | – | – | – | – | – | 0,3 | 0,5 | 11,3 | 58,3 | 20,1 | 3,7 | 5,8 | – | ||
47 | Концентрат обогащения железной руды | 55,5 | 28,3 | 10,0 | 5,9 | 0,3 | – | – | – | – | – | – | – | – | – |
40,0 | 36,1 | 12,7 | 8,8 | 2,4 | – | – | – | – | – | – | – | – | – | ||
53,7 | 29,6 | 11,8 | 4,9 | – | – | – | – | – | – | – | – | – | – | ||
48 | Известняк | 30,7 | 26,6 | 27,1 | 8,1 | 5,2 | 2,3 | – | – | – | – | – | – | – | |
4,9 | 17,5 | 20,6 | 18,4 | 16,3 | 17,2 | 3,6 | 1,5 | – | – | – | – | – | – | ||
20,2 | 17,3 | 16,3 | 36,6 | 3,4 | – | 6,2 | – | – | – | – | – | – |
Продолжение таблицы II.3
Вариант | Материал | Содержание классов, % | |||||||||||||
0-0,045 | 0,045-0,074 | 0,074-0,1 | 0,1-0,5 | 0,5-1,0 | 1,0-3,0 | 3,0-5,0 | 5,0-8,0 | 8,0-12,0 | 12,0-15,0 | 15,0-25,0 | 25,0-40,0 | 40,0-60,0 | 60,0-80,0 | ||
49 | Агломерат | 1,8 | 2,3 | 0,9 | – | – | – | – | 40,4 | 26,1 | 13,7 | 11,8 | 2,1 | 0,9 | – |
0,3 | – | 1,6 | 2,1 | 0,7 | – | – | 25,5 | 38,1 | 14,8 | 14,1 | 2,8 | – | – | ||
– | 1,3 | 1,9 | 1,8 | – | – | – | 19,7 | 26,9 | 8,0 | 40,4 | – | – | – | ||
50 | Кокс* | – | – | – | – | – | – | – | – | 1,3* | 7,0* | 14,0* | 40,5 | 15,5 | 21,7 |
– | – | – | – | – | – | 2,2 | 1,7 | – | – | 12,7 | 9,7 | 50,3 | 23,4 | ||
– | – | – | – | – | – | – | 5,4 | 0,7 | – | 13,1 | 5,2 | 14,8 | 60,8 |
- Рассев скипового кокса ведется по стандарту на классы, мм: >80, >60, >40, >25, 60-80, 40-60, 25-40, 10-25, 0-10, 6-10, 0-6.
Таблица II.4
Исходные данные для выполнения работы 4
Вариант | ![]() | ![]() | ![]() | ![]() | Вариант | ![]() | ![]() | ![]() | ![]() |
1 | 90 | – | 250 | – | 26 | – | – | – | 9,7 |
2 | – | 80 | 230 | – | 27 | – | 15 | 100 | – |
3 | – | – | – | 23,1 | 28 | – | – | – | 16,0 |
4 | – | – | – | 18,6 | 29 | – | – | – | 22,5 |
5 | 120 | – | 210 | – | 30 | – | – | – | 21,9 |
6 | 83 | – | 225 | – | 31 | 170 | – | 210 | – |
7 | 165 | – | 210 | – | 32 | 60 | – | 240 | – |
8 | 113 | – | 150 | – | 33 | – | 150 | 230 | – |
9 | – | 30 | 180 | – | 34 | – | – | – | 19,6 |
10 | 140 | – | 180 | – | 35 | – | – | – | 6,1 |
11 | 170 | – | 230 | – | 36 | – | 40 | 190 | – |
12 | – | 165 | 250 | – | 37 | 170 | – | 210 | – |
13 | – | – | – | 16,1 | 38 | – | – | – | 28,7 |
14 | – | – | – | 15,7 | 39 | 80 | – | 230 | – |
15 | – | – | – | 14,9 | 40 | – | 140 | 220 | – |
16 | 111 | – | 150 | – | 41 | – | 40 | 250 | – |
17 | – | – | – | 15,9 | 42 | – | – | – | 17,3 |
18 | – | – | – | 19,0 | 43 | 50 | – | 180 | – |
19 | – | 30 | 210 | – | 44 | – | 43 | 165 | – |
20 | – | – | – | 16,2 | 45 | – | – | – | 16,2 |
21 | – | – | – | 11,3 | 46 | 80 | – | 230 | – |
22 | – | – | – | 14,3 | 47 | – | 34 | 200 | – |
23 | – | 20 | 190 | – | 48 | – | – | – | 18,6 |
24 | – | – | – | 21,3 | 49 | – | 100 | 150 | – |
25 | – | – | – | 20,8 | 50 | – | 132 | 180 | – |
Примечание. Ведущим рудным железосодержащим минералом в буром железняке принимать гётит ( )
Таблица П.5
Исходные данные для выполнения работы 5
Вариант | Параметр усреднения, (содержание компонента в материале), % | Номер | |||||||
1 | 2 | 3 | 4 | 5 | 6 | 7 | 8 | ||
1 | Железо в руде | ![]() | ![]() | ![]() | ![]() | ![]() | ![]() | ![]() | ![]() |
2 | Фракция +8 мм в агломерате | ![]() | ![]() | ![]() | ![]() | ![]() | ![]() | ![]() | ![]() |
3 | Са в руде | ![]() | ![]() | ![]() | ![]() | ![]() | ![]() | ![]() | ![]() |
4 | S в концентрате | ![]() | ![]() | ![]() | ![]() | ![]() | ![]() | ![]() | ![]() |
5 | Зола в коксовой мелочи | ![]() | ![]() | ![]() | ![]() | ![]() | ![]() | ![]() | ![]() |
6 | СаО в известняке | ![]() | ![]() | ![]() | ![]() | ![]() | ![]() | ![]() | ![]() |
7 | S в коксе | ![]() | ![]() | ![]() | ![]() | ![]() | ![]() | ![]() | ![]() |
8 | СаО в известняке | ![]() | ![]() | ![]() | ![]() | ![]() | ![]() | ![]() | ![]() |
9 | Влага в коксовой мелочи | ![]() | ![]() | ![]() | ![]() | ![]() | ![]() | ![]() | ![]() |
10 | Fe в концентрате | ![]() | ![]() | ![]() | ![]() | ![]() | ![]() | ![]() | ![]() |
11 | Зола в коксе | ![]() | ![]() | ![]() | ![]() | ![]() | ![]() | ![]() | ![]() |
12 | SiO2 в руде | ![]() | ![]() | ![]() | ![]() | ![]() | ![]() | ![]() | ![]() |
13 | Fe в концентрате | ![]() | ![]() | ![]() | ![]() | ![]() | ![]() | ![]() | ![]() |
14 | SiO2 в руде | ![]() | ![]() | ![]() | ![]() | ![]() | ![]() | ![]() | ![]() |
15 | Зола в коксе | ![]() | ![]() | ![]() | ![]() | ![]() | ![]() | ![]() | ![]() |
16 | СаО в известняке | ![]() | ![]() | ![]() | ![]() | ![]() | ![]() | ![]() | ![]() |
17 | SiO2 в концентрате | ![]() | ![]() | ![]() | ![]() | ![]() | ![]() | ![]() | ![]() |
18 | SiO2 в руде | ![]() | ![]() | ![]() | ![]() | ![]() | ![]() | ![]() | ![]() |
19 | Са в руде | ![]() | ![]() | ![]() | ![]() | ![]() | ![]() | ![]() | ![]() |
Продолжение Табл.5
пробы | |||||||||||
9 | 10 | 11 | 12 | 13 | 14 | 15 | 16 | 17 | 18 | 19 | 20 |
![]() | ![]() | ![]() | ![]() | ![]() | ![]() | ![]() | ![]() | ![]() | ![]() | ![]() | ![]() |
![]() | ![]() | ![]() | ![]() | ![]() | ![]() | ![]() | ![]() | ![]() | ![]() | ![]() | ![]() |
![]() | ![]() | ![]() | ![]() | ![]() | ![]() | ![]() | ![]() | ![]() | ![]() | ![]() | ![]() |
![]() | ![]() | ![]() | ![]() | ![]() | ![]() | ![]() | ![]() | ![]() | ![]() | ![]() | ![]() |
![]() | ![]() | ![]() | ![]() | ![]() | ![]() | ![]() | ![]() | ![]() | ![]() | ![]() | ![]() |
![]() | ![]() | ![]() | ![]() | ![]() | ![]() | ![]() | ![]() | ![]() | ![]() | ![]() | ![]() |
![]() | ![]() | ![]() | ![]() | ![]() | ![]() | ![]() | ![]() | ![]() | ![]() | ![]() | ![]() |
![]() | ![]() | ![]() | ![]() | ![]() | ![]() | ![]() | ![]() | ![]() | ![]() | ![]() | ![]() |
![]() | ![]() | ![]() | ![]() | ![]() | ![]() | ![]() | ![]() | ![]() | ![]() | ![]() | ![]() |
![]() | ![]() | ![]() | ![]() | ![]() | ![]() | ![]() | ![]() | ![]() | ![]() | ![]() | ![]() |
![]() | ![]() | ![]() | ![]() | ![]() | ![]() | ![]() | ![]() | ![]() | ![]() | ![]() | ![]() |
![]() | ![]() | ![]() | ![]() | ![]() | ![]() | ![]() | ![]() | ![]() | ![]() | ![]() | ![]() |
![]() | ![]() | ![]() | ![]() | ![]() | ![]() | ![]() | ![]() | ![]() | ![]() | ![]() | ![]() |
![]() | ![]() | ![]() | ![]() | ![]() | ![]() | ![]() | ![]() | ![]() | ![]() | ![]() | ![]() |
![]() | ![]() | ![]() | ![]() | ![]() | ![]() | ![]() | ![]() | ![]() | ![]() | ![]() | ![]() |
![]() | ![]() | ![]() | ![]() | ![]() | ![]() | ![]() | ![]() | ![]() | ![]() | ![]() | ![]() |
![]() | ![]() | ![]() | ![]() | ![]() | ![]() | ![]() | ![]() | ![]() | ![]() | ![]() | ![]() |
![]() | ![]() | ![]() | ![]() | ![]() | ![]() | ![]() | ![]() | ![]() | ![]() | ![]() | ![]() |
![]() | ![]() | ![]() | ![]() | ![]() | ![]() | ![]() | ![]() | ![]() | ![]() | ![]() | ![]() |
Вариант | Параметр усреднения, (содержание компонента в материале), % | Номер | |||||||
1 | 2 | 3 | 4 | 5 | 6 | 7 | 8 | ||
20 | Fe в концентрате | ![]() | ![]() | ![]() | ![]() | ![]() | ![]() | ![]() | ![]() |
21 | S в коксе | ![]() | ![]() | ![]() | ![]() | ![]() | ![]() | ![]() | ![]() |
22 | Зола в коксе | ![]() | ![]() | ![]() | ![]() | ![]() | ![]() | ![]() | ![]() |
23 | S в коксе | ![]() | ![]() | ![]() | ![]() | ![]() | ![]() | ![]() | ![]() |
24 | SiO2 в руде | ![]() | ![]() | ![]() | ![]() | ![]() | ![]() | ![]() | ![]() |
25 | Влага в коксовой мелочи | ![]() | ![]() | ![]() | ![]() | ![]() | ![]() | ![]() | ![]() |
26 | MgO в концентрате | ![]() | ![]() | ![]() | ![]() | ![]() | ![]() | ![]() | ![]() |
27 | СаО в руде | ![]() | ![]() | ![]() | ![]() | ![]() | ![]() | ![]() | ![]() |
28 | Fe в концентрате | ![]() | ![]() | ![]() | ![]() | ![]() | ![]() | ![]() | ![]() |
29 | Зола в коксе | ![]() | ![]() | ![]() | ![]() | ![]() | ![]() | ![]() | ![]() |
30 | Fe в руде | ![]() | ![]() | ![]() | ![]() | ![]() | ![]() | ![]() | ![]() |
31 | SiO2 в концентрате | ![]() | ![]() | ![]() | ![]() | ![]() | ![]() | ![]() | ![]() |
32 | Fe в концентрате | ![]() | ![]() | ![]() | ![]() | ![]() | ![]() | ![]() | ![]() |
33 | Влага в коксе | ![]() | ![]() | ![]() | ![]() | ![]() | ![]() | ![]() | ![]() |
34 | P в руде | ![]() | ![]() | ![]() | ![]() | ![]() | ![]() | ![]() | ![]() |
35 | S в коксовой мелочи | ![]() | ![]() | ![]() | ![]() | ![]() | ![]() | ![]() | ![]() |
36 | Зола в коксовой мелочи | ![]() | ![]() | ![]() | ![]() | ![]() | ![]() | ![]() | ![]() |
37 | CaO в известняке | ![]() | ![]() | ![]() | ![]() | ![]() | ![]() | ![]() | ![]() |
38 | SiO2 в известняке | ![]() | ![]() | ![]() | ![]() | ![]() | ![]() | ![]() | ![]() |
39 | S в коксовой мелочи | ![]() | ![]() | ![]() | ![]() | ![]() | ![]() | ![]() | ![]() |
Продолжение таблицы П.5
пробы | |||||||||||
9 | 10 | 11 | 12 | 13 | 14 | 15 | 16 | 17 | 18 | 19 | 20 |
![]() | ![]() | ![]() | ![]() | ![]() | ![]() | ![]() | ![]() | ![]() | ![]() | ![]() | ![]() |
![]() | ![]() | ![]() | ![]() | ![]() | ![]() | ![]() | ![]() | ![]() | ![]() | ![]() | ![]() |
![]() | ![]() | ![]() | ![]() | ![]() | ![]() | ![]() | ![]() | ![]() | ![]() | ![]() | ![]() |
![]() | ![]() | ![]() | ![]() | ![]() | ![]() | ![]() | ![]() | ![]() | ![]() | ![]() | ![]() |
![]() | ![]() | ![]() | ![]() | ![]() | ![]() | ![]() | ![]() | ![]() | ![]() | ![]() | ![]() |
![]() | ![]() | ![]() | ![]() | ![]() | ![]() | ![]() | ![]() | ![]() | ![]() | ![]() | ![]() |
![]() | ![]() | ![]() | ![]() | ![]() | ![]() | ![]() | ![]() | ![]() | ![]() | ![]() | ![]() |
![]() | ![]() | ![]() | ![]() | ![]() | ![]() | ![]() | ![]() | ![]() | ![]() | ![]() | ![]() |
![]() | ![]() | ![]() | ![]() | ![]() | ![]() | ![]() | ![]() | ![]() | ![]() | ![]() | ![]() |
![]() | ![]() | ![]() | ![]() | ![]() | ![]() | ![]() | ![]() | ![]() | ![]() | ![]() | ![]() |
![]() | ![]() | ![]() | ![]() | ![]() | ![]() | ![]() | ![]() | ![]() | ![]() | ![]() | ![]() |
![]() | ![]() | ![]() | ![]() | ![]() | ![]() | ![]() | ![]() | ![]() | ![]() | ![]() | ![]() |
![]() | ![]() | ![]() | ![]() | ![]() | ![]() | ![]() | ![]() | ![]() | ![]() | ![]() | ![]() |
![]() | ![]() | ![]() | ![]() | ![]() | ![]() | ![]() | ![]() | ![]() | ![]() | ![]() | ![]() |
![]() | ![]() | ![]() | ![]() | ![]() | ![]() | ![]() | ![]() | ![]() | ![]() | ![]() | ![]() |
![]() | ![]() | ![]() | ![]() | ![]() | ![]() | ![]() | ![]() | ![]() | ![]() | ![]() | ![]() |
![]() | ![]() | ![]() | ![]() | ![]() | ![]() | ![]() | ![]() | ![]() | ![]() | ![]() | ![]() |
![]() | ![]() | ![]() | ![]() | ![]() | ![]() | ![]() | ![]() | ![]() | ![]() | ![]() | ![]() |
![]() | ![]() | ![]() | ![]() | ![]() | ![]() | ![]() | ![]() | ![]() | ![]() | ![]() | ![]() |
![]() | ![]() | ![]() | ![]() | ![]() | ![]() | ![]() | ![]() | ![]() | ![]() | ![]() | ![]() |
Вариант | Параметр усреднения, (содержание компонента в материале), % | Номер | |||||||
1 | 2 | 3 | 4 | 5 | 6 | 7 | 8 | ||
40 | SiO2 в руде | ![]() | ![]() | ![]() | ![]() | ![]() | ![]() | ![]() | ![]() |
41 | S в коксовой мелочи | ![]() | ![]() | ![]() | ![]() | ![]() | ![]() | ![]() | ![]() |
42 | Fe в руде | ![]() | ![]() | ![]() | ![]() | ![]() | ![]() | ![]() | ![]() |
43 | Зола в коксовой мелочи | ![]() | ![]() | ![]() | ![]() | ![]() | ![]() | ![]() | ![]() |
44 | Влага в коксовой мелочи | ![]() | ![]() | ![]() | ![]() | ![]() | ![]() | ![]() | ![]() |
45 | Фракция < 25 мм в коксе | ![]() | ![]() | ![]() | ![]() | ![]() | ![]() | ![]() | ![]() |
46 | Фракция > 80 мм в коксе | ![]() | ![]() | ![]() | ![]() | ![]() | ![]() | ![]() | ![]() |
47 | Фракция > 8 мм в аглоруде | ![]() | ![]() | ![]() | ![]() | ![]() | ![]() | ![]() | ![]() |
48 | Выход летучих веществ в коксе | ![]() | ![]() | ![]() | ![]() | ![]() | ![]() | ![]() | ![]() |
49 | Фракция > 40 мм в коксе | ![]() | ![]() | ![]() | ![]() | ![]() | ![]() | ![]() | ![]() |
50 | Фракция > 25 мм в коксе | ![]() | ![]() | ![]() | ![]() | ![]() | ![]() | ![]() | ![]() |
Примечание: В числителе – до усреднения, в знаменателе – после усреднения.
Окончание таблицы П.5
пробы | |||||||||||
9 | 10 | 11 | 12 | 13 | 14 | 15 | 16 | 17 | 18 | 19 | 20 |
![]() | ![]() | ![]() | ![]() | ![]() | ![]() | ![]() | ![]() | ![]() | ![]() | ![]() | ![]() |
![]() | ![]() | ![]() | ![]() | ![]() | ![]() | ![]() | ![]() | ![]() | ![]() | ![]() | ![]() |
![]() | ![]() | ![]() | ![]() | ![]() | ![]() | ![]() | ![]() | ![]() | ![]() | ![]() | ![]() |
![]() | ![]() | ![]() | ![]() | ![]() | ![]() | ![]() | ![]() | ![]() | ![]() | ![]() | ![]() |
![]() | ![]() | ![]() | ![]() | ![]() | ![]() | ![]() | ![]() | ![]() | ![]() | ![]() | ![]() |
![]() | ![]() | ![]() | ![]() | ![]() | ![]() | ![]() | ![]() | ![]() | ![]() | ![]() | ![]() |
![]() | ![]() | ![]() | ![]() | ![]() | ![]() | ![]() | ![]() | ![]() | ![]() | ![]() | ![]() |
![]() | ![]() | ![]() | ![]() | ![]() | ![]() | ![]() | ![]() | ![]() | ![]() | ![]() | ![]() |
![]() | ![]() | ![]() | ![]() | ![]() | ![]() | ![]() | ![]() | ![]() | ![]() | ![]() | ![]() |
![]() | ![]() | ![]() | ![]() | ![]() | ![]() | ![]() | ![]() | ![]() | ![]() | ![]() | ![]() |
![]() | ![]() | ![]() | ![]() | ![]() | ![]() | ![]() | ![]() | ![]() | ![]() | ![]() | ![]() |
таблица П.6
Предельный чугун по ГОСТ 805-80, массовая доля, %
Марка | Si | Mn | P, не более | S, не более | |||||||
Группы | Класс | Категория | |||||||||
I | II | III | IV | А Б В | I | II | III | IV | V | ||
П1 | 0,51-0,9 | ≤0,5 | 0,51-1,0 | 1,01-1,5 | - | 0,1 0,2 | |||||
П2 | ≤ 0,5 | ≤0,5 | 0,51-1,0 | 1,01-1,5 | - | 0,1 0,2 0,3 | 0,01 | 0,02 | 0,03 | 0,04 | 0,05 |
ПЛ1 | 0,81-1,2 | ≤0,3 | 0,31-0,5 | 0,51-0,9 | 0,91-1,5 | 0.08 0,12 | |||||
ПЛ2 | 0,51-0,8 | ≤0,3 | 0,31-0,5 | 0,51-0,9 | 0,91-1,5 | 0,08 0,12 |
таблица П.7
Литейный чугун по ГОСТ 4832-80, массовая доля, %
Марка | Si | C | Mn | P | S, не более | ||||||||||
Группа | Класс | Категория | |||||||||||||
Не более | Г | Д | |||||||||||||
I | II | III | IV | А | Б | В | 1 | 2 | 3 | 4 | |||||
Л1 | 3,21-3,6 | 3,4-3,9 |
До 0,3 |
0,31-0,5 |
0,51-0,9 |
0,91-1,5 |
0,08 |
0,12 |
0,3 |
0,3-0,7 |
0,7-1,2 |
0,02 |
0,03 |
0,04 |
0,05
0,05
0,05
|
Л2 | 2,81-3,2 | 3,5-4,0 | |||||||||||||
Л3 | 2,41-2,8 | 3,6-4,1 | |||||||||||||
Л4 | 2,01-2,4 | 3,7-4,2 | |||||||||||||
Л5 | 1,61-2,0 | 3,9-4,4 | |||||||||||||
Л6 | 1,21-1,6 | 4,0-4,5 |
таблица П.8
Предельный фосфористый чугун по ГОСТ 805-80, массовая доля, %
Марка | Si | Mn, не более | S, не более | Класс | |||||||||
Группа | Категория | А | Б | В | |||||||||
I | II | III | I | II | III | P | As, не более | P | As, не более | P | As, не более | ||
ПФ1 ПФ2 ПФ3 | 0,91-1,2 0,51-0,9 ≤0,5 | 1 | 1,5 | 2,0 | 0,03 | 0,05 | 0,07 | 0,0-0,7 | 0,10 | 0,71-1,5 | 0,15 | 1,51-2,0 | 0,20 |
таблица П.9
Высококачественный ппредельный чугун по ГОСТ 805-80, массовая доля, %
Марка | Si | Mn | P | S | |||||||
Группа | Класс | Категория | |||||||||
I | II | III | А | Б | В | Г | I | II | III | ||
Не более | |||||||||||
ПВК1 ПВК2 ПВК3 | 0,91-1,3 0,51-,09 ≤0,50 | ≤0,50 | 0,51-1,0 | 1,01-1,50 | 0,02 | 0,03 | 0,04 | 0,05 | 0,015 | 0,020 | 0,025 |
Таблица П.10
исходные данные для выполнения работы
Вариант | Вид материала | Расход мат-ла, т/т чугуна | Содержится в материале | Неполный химический состав золы, топлива, известняка, % | |||||||
влаги | золы | Fe | Cao | SiO2 | Mn | P | S* | C* | |||
1 | Кокс Коксовая мелочь Известняк Металлодобавки | 405 - - 8,0 | 3,5 9,3 3,0 - | 9,5 13,5 - - | 8,0 8,2 - 90,5 | 8,0 7,2 54,0 - | 45,0 49,3 1,5 7,0 | 0,6 0,5 - 0,2 | 0,01 0,05 - 0,03 | 0,55 0,8 - - | - 80,0 - - |
2 | Кокс Коксовая мелочь Известняк | 410 - - | 1,6 13,0 3,5 | 12,4 15,6 - | 5,6 5,5 - | 4,4 4,2 54,0 | 49,6 49,6 1,00 | - - - | 0,2 0,25 - | 0,8 0,9 - | - 80,3 - |
3 | Кокс Коксовая мелочь Известняк Металлодобавки | 407 - - 9,05 | 3,7 13,0 4,0 - | 9,6 13,8 - - | 7,9 8,1 - 90,3 | 4,8 4,2 53,9 - | 49,3 49,5 1,01 8,1 | - - - 0,3 | 0,4 - - 0,02 | 0,76 - - - | - 80,4 - - |
4 | Кокс Коксовая мелочь Известняк | 410 - - | 2,1 11,8 4,0 | 12,6 16,1 - | 5,3 5,4 - | 4,3 4,1 53,8 | 49,3 49,7 1,02 | - - - | 0,5 0,4 - | 0,83 0,93 - | - 80,4 - |
5 | Кокс Коксовая мелочь Известняк Металлодобавки | 395 - - 9,01 | 3,4 12,7 4,1 - | 10,7 15,0 - - | 5,2 5,3 - 90,5 | 6,79 5,93 53,7 - | 48,44 49,1 2,28 8,3 | 0,05 0,04 - 0,3 | 0,48 0,6 - 0,08 | 0,4 0,6 - 0,02 | - 80,3 - - |
*Содержание углерода и серы в коксе и коксовой мелочи приведены из данных технического состава на сухую массу
Продолжение таблицы П.10
Вариант | Вид материала | Расход мат-ла, т/т чугуна | Содержится в материале | Неполный химический состав золы, топлива, известняка, % | |||||||
влаги | золы | Fe | Cao | SiO2 | Mn | P | S* | C* | |||
6 | Кокс Коксовая мелочь Известняк Металлодобавки | 390 - - 8,5 | 3,3 10,3 4,2 - | 10,6 13,8 - - | 5,0 5,3 - 91 | 6,7 6,8 51,5 - | 48,5 49,2 2,3 8,4 | 0,05 0,03 - 0,3 | 0,48 0,49 - 0,03 | 0,41 0,63 - 0,02 | - 80,5 - - |
7 | Кокс Коксовая мелочь Известняк | 407 - - | 3,8 9,9 8,1 | 12,2 14,8 - | 5,3 5,2 - | 4,3 4,0 54 | 49,7 49,9 0,98 | 0,2 0,2 - | 0,4 0,4 - | 1,74 1,8 - | - 80,6 - |
8 | Кокс Коксовая мелочь Известняк Металлодобавки | 400,6 - - 8,6 | 3,9 10,0 6,0 - | 12,3 6,3 - - | 5,4 5,3 - 91,0 | 4,4 4,5 53,9 - | 49,3 49,6 1,99 7,9 | 0,1 0,1 - 0,2 | 0,4 0,4 - 0,03 | 0,62 0,8 - 0,02 | - 80,3 - - |
9 | Кокс Коксовая мелочь Известняк Металлодобавки | 400 - - 7,0 | 0,5 18,0 3,0 - | 10,6 14,7 - - | 6,7 6,5 - 90,5 | 3,12 3,6 54,5 - | 53,36 53,4 0,79 8,1 | - - - 0,05 | - - - 0,01 | 0,81 0,9 - 0,015 | - 80,5 - - |
10 | Кокс Коксовая мелочь Известняк | 393 - - | 0,6 9,0 5,0 | 10,7 14,8 - | 6,4 6,5 - | 3,2 3,1 54,1 | 53,4 53,5 0,8 | - - - | - - - | 0,8 0,92 - | - 80,6 - |
11 | Кокс Коксовая мелочь Известняк Металлодобавки | 412 - - 5,0 | 3,2 11,7 7,0 - | 8,5 12,6 - - | 5,1 5,2 - 90,7 | 4,1 4,0 54,2 - | 49,3 49,6 0,92 8,0 | - - - 0,3 | 0,4 0,5 - 0,03 | 0,63 0,8 - 0,01 | - 80,2 - - |
Продолжение табл. П.10
Вариант | Вид мате-риала | Расход материала, кг/т чугуна | Содержится в материале | Неполный химический состав золы, топлива, известняка, % | |||||||
влаги | золы | Fe | CaO | SiO2 | Mn | P | S | C | |||
12 | Кокс Коксовая мелочь Известняк Металло-добавки | 420 - - 60 | 3,5 12,3 6,5 - | 12,4 14,6 - - | 6,2 6,0 - 90,6 | 4,0 3,9 54,0 - | 49,5 49,5 1,0 8,1 | - - - 0,2 | - 0,4 - 0,02 | 0,61 0,8 - 0,01 | - 80,4 - - |
13 | Кокс Коксовая мелочь Известняк Металло-добавки | 390 - - 7,0 | 0,58 9,0 5,0 - | 10,6 15,1 - - | 6,2 6,3 - 90,5 | 3,1 3,0 54,0 - | 53,2 53,5 0,9 8,6 | - - - 0,1 | - - - 0,01 | 0,6 0,92 - 0,01 | - 80,5 - - |
14 | Кокс Коксовая мелочь Известняк Металло-добавки | 430 - - 6,5 | 2,7 9,9 6,0 - | 9,6 13,7 - - | 10,5 10,7 - 90,4 | 2,8 2,0 54,0 - | 42,4 43,3 2,00 8,3 | - - - 0,05 | 0,05 0,05 - 0,02 | 1,74 1,8 - 0,02 | - 80,1 - - |
15 | Кокс Коксовая мелочь Извест-няк | 380 - - | 2,8 13,0 3,5 | 8,3 11,0 - | 4,03 4,05 - | 3,4 3,3 53,5 | 56,11 57,2 1,6 | 0,14 0,2 - | 0,14 0,14 - | 0,49 0,55 - | - 80,6 - |
16 | Кокс Коксо-вая мелочь Известняк Металло-добавки | 425 - - 9,0 | 3,18 11,0 4,0 - | 9,6 12,7 - - | 16,3 18,0 - 90,7 | 5,1 4,3 52,8 - | 38,0 39,5 2,0 8,1 | 0,2 0,25 - 0,03 | 0,2 0,25 - 0,03 | 1,79 1,95 - 0,02 | - 79,3 - - |
17 | Кокс Коксовая мелочь Известняк | 430 - - | 3,5 12,1 7,5 | 9,7 11,9 - | 16,1 17,3 - | 5,0 4,7 54,0 | 37,9 39,1 1,3 | 0,21 0,24 - | 0,25 0,23 - | 1,8 1,85 - | - 79,6 - |
Продолжение табл. П.10
Вариант | Вид мате-риала | Расход материала, кг/т чугуна | Содержится в материале | Неполный химический состав золы, топлива, известняка, % | |||||||
влаги | золы | Fe | CaO | SiO2 | Mn | P | S | C | |||
18 | Кокс Коксовая мелочь Известняк Металло-добавки | 425 - - 7,5 | 3,8 12,7 9,6 - | 9,8 12,2 - - | 15,4 15,8 - 90,6 | 4,3 5,1 54,0 - | 38,3 38,5 1,8 8,3 | 0,23 0,2 - 0,03 | 0,24 0,23 - 0,02 | 1,78 1,82 - - | - 79,8 - - |
19 | Кокс Коксовая мелочь Известняк | 410 - - | 2,2 13,3 7,0 | 12,8 15,7 - | 5,0 5,1 - | 4,7 4,3 54,0 | 49,5 49,7 1,00 | - - - | 0,4 0,45 - | 0,6 0,73 - | - 80,6 - |
20 | Кокс Коксовая мелочь Известняк Металло-добавки | 400 - - 9,5 | 3,0 8,8 7,6 - | 10,64 13,85 - - | 11,7 12,1 - 90,5 | 2,26 2,17 53,0 - | 43,61 44,3 1,5 8,6 | - 0,2 - - | - 0,2 - 0,02 | 1,44 1,56 - 0,02 | - 80,3 - - |
21 | Кокс Коксовая мелочь Известняк Металло-добавки | 380 - - 6,3 | 2,2 9,7 7,0 - | 10,0 13,8 - - | 3,6 3,7 - 90,3 | 4,29 4,15 54,0 - | 52,83 53,1 1,48 7,9 | 0,15 0,15 - 0,01 | 0,5 0,5 - 0,02 | 0,55 0,6 - 0,03 | - 80,7 - - |
22 | Кокс Коксовая мелочь Известняк Металло-добавки | 375 - - 7,8 | 1,8 5,6 7,1 - | 10,5 12,7 - - | 4,0 4,1 - 90,6 | 3,4 3,3 53,0 - | 56,2 56,3 1,4 8,3 | - 0,01 - 0,2 | 0,14 0,2 - 0,05 | 0,5 0,55 - 0,03 | - 80,8 - - |
23 | Кокс Коксовая мелочь Известняк Металло-добавки | 418 - - 8,3 | 3,18 8,15 8,3 - | 9,5 11,3 - - | 16,7 17,3 - 90,1 | 5,08 4,97 54,5 - | 36,27 37,5 0,79 8,5 | 0,2 0,25 - 0,3 | 0,15 0,18 - 0,03 | 1,85 1,9 - 0,02 | - 80,4 - - |
Продолжение табл. П.10
Вариант | Вид материала | Расход материала, кг/т чугуна | Содержится в материале | Неполный химический состав золы, топлива, известняка, % | |||||||
влаги | золы | Fe | CaO | SiO2 | Mn | P | S | C | |||
24 | Кокс Коксовая мелочь Известняк Металло-добавки | 435 - - 9,0 | 3,7 12,3 7,7 - | 9,5 12,2 - - | 16,3 17,1 - 90,7 | 5,2 4,8 54,1 - | 37,5 38,5 1,31 7,96 | 0,21 0,25 - 0,3 | 0,24 0,23 - 0,09 | 1,8 1,9 - 0,01 | - 80,1 - - |
25 | Кокс Коксовая мелочь Известняк Металло-добавки | 430 - - 9,5 | 3,5 21,0 7,9 - | 9,6 13,1 - - | 16,6 17,1 - 90,5 | 5,06 4,85 54,2 - | 36,31 37,7 1,4 8,8 | 0,21 0,23 - - | 0,15 0,24 - - | 1,84 1,9 - - | - 80,5 - - |
26 | Кокс Коксовая мелочь Известняк Металло-добавки | 390 - - 9,0 | 2,7 9,7 7,0 - | 11,0 13,5 - - | 4,8 4,9 - 90,0 | 6,06 6,0 54,77 - | 48,25 49,1 0,54 9,0 | 0,15 0,15 - - | 0,5 0,5 - - | 0,45 0,5 - - | - 80,8 - - |
27 | Кокс Коксо-вая мелочь Известняк Металло-добавки | 390 - - 6,0 | 2,2 11,0 8,1 - | 12,4 13,9 - - | 3,98 4,2 - 90,1 | 5,45 5,2 51,9 - | 56,21 57,00 1,41 9,1 | - - - - | 0,33 0,35 - - | 0,47 0,49 - - | - 80,7 - - |
28 | Кокс Коксовая мелочь Известняк Металло-добавки | 370 - - 3,5 | 2,8 9,7 5,1 - | 10,8 13,1 - - | 4,1 4,3 - 90,3 | 3,5 3,3 52,9 - | 56,4 57,2 1,35 8,8 | 0,01 0,02 - - | 0,14 0,17 - - | 0,49 0,53 - - | - 80,8 - - |
29 | Кокс Коксовая мелочь Известняк Металло-добавки | 425 - - 5,0 | 2,9 6,7 - - | 9,5 9,9 - - | 9,65 9,83 - 90,0 | 2,75 2,7 90,0 - | 42,5 43,3 2,3 7,0 | - 0,1 - - | 0,05 0,05 - - | 1,75 1,84 - - | - 80,0 - - |
Продолжение табл. П.10
Вариант | Вид мате-риала | Расход материала, кг/т чугуна | Содержится в материале | Неполный химический состав золы, топлива, известняка, % | |||||||
влаги | золы | Fe | CaO | SiO2 | Mn | P | S | C | |||
30 | Кокс Коксовая мелочь Известняк Металло-добавки | 370 - - 7,0 | 1,5 5,8 - - | 10,0 12,7 - - | 3,6 3,8 - 90,5 | 4,3 4,5 90,2 - | 52,8 53,1 1,0 8,0 | 0,12 0,13 - 0,5 | 0,52 0,5 - 0,13 | 0,4 0,43 - 0,01 | - 80,8 - - |
31 | Кокс Коксовая мелочь Известняк Металло-добавки | 435 - - 5,0 | 5,5 7,2 5,1 - | 9,7 11,9 - - | 12,1 12,0 - 90,3 | 2,9 3,3 54,0 - | 42,5 43,1 1,98 9,2 | - - - 0,3 | 0,06 0,07 - 0,03 | 1,75 1,79 - 0,03 | - 80,1 - - |
32 | Кокс Коксовая мелочь Известняк Металло-добавки | 395 - - 4,5 | 0,6 9,9 - - | 10,8 12,7 - - | 6,5 5,3 - 91,0 | 3,15 3,36 91,0 - | 53,5 52,9 2,3 7,5 | - - - 0,3 | - - - 0,03 | 0,8 0,85 - 0,02 | - 80,5 - - |
33 | Кокс Коксовая мелочь Известняк Металло-добавки | 390 - - 5,0 | 0,7 7,7 - - | 10,9 13,8 - - | 6,6 5,7 - 90,5 | 3,4 3,3 90,7 - | 53,8 54,0 2,7 7,9 | - - - - | - - - 0,3 | 0,78 0,82 - 0,03 | - 80,3 - - |
34 | Кокс Коксовая мелочь Известняк Металло-добавки | 423 - - 9,0 | 3,2 7,7 4,1 - | 9,8 13,5 - - | 16,7 17,1 - 90,2 | 5,0 4,5 53,0 - | 38,7 39,3 2,1 8,1 | 0,25 0,3 - 0,4 | 0,2 0,2 - 0,23 | 1,8 1,83 - 0,03 | - 80,3 - - |
35 | Кокс Коксовая мелочь Известняк Металло-добавки | 392 - - 2,5 | 2,1 7,1 7,0 - | 12,5 14,3 - - | 4,1 4,0 - 90,6 | 5,5 5,3 51,8 - | 56,3 56,5 1,38 8,5 | - - - 0,3 | 0,34 0,35 - 0,05 | 0,47 0,8 - 0,03 | - 80,7 - - |
Продолжение табл. П.10
Вариант | Вид мате-риала | Расход материала, кг/т чугуна | Содержится в материале | Неполный химический состав золы, топлива, известняка, % | |||||||
влаги | золы | Fe | CaO | SiO2 | Mn | P | S | C | |||
36 | Кокс Коксовая мелочь Известняк Металло-добавки | 390 - - 7,0 | 2,6 10,3 5,4 - | 11,0 14,4 - - | 4,9 4,9 - 90,5 | 6,0 6,0 64,8 - | 48,3 49,5 0,6 8,6 | 0,15 0,2 - - | 0,15 0,18 - - | 0,45 0,48 - - | - 80,9 - - |
37 | Кокс Коксовая мелочь Известняк Металло-добавки | 420 - - 9,0 | 3,3 7,0 5,2 - | 8,5 11,0 - - | 5,2 5,3 - 90,1 | 3,9 4,1 54,1 - | 49,5 49,6 0,9 7,9 | 0,05 0,05 - 0,5 | 0,4 0,43 - 0,35 | 0,61 0,66 - 0,03 | - 80,3 - - |
38 | Кокс Коксовая мелочь Известняк Металло-добавки | 440 - - 10,0 | 2,8 9,1 4,3 - | 9,6 13,0 - - | 10,4 11,0 - 90,7 | 2,75 2,6 54,1 - | 42,8 43,1 0,82 7,6 | - - - 0,3 | 0,05 0,06 - 0,2 | 1,85 1,91 - 0,02 | - 80,0 - - |
39 | Кокс Коксовая мелочь Известняк Металло-добавки | 370 - - 2,5 | 1,9 4,8 4,0 - | 10,8 13,1 - - | 4,05 5,01 - 90,5 | 3,35 3,18 53,6 - | 56,3 56,35 1,72 8,7 | 0,15 0,16 - 0,3 | 0,16 0,16 - - | 0,50 0,52 - 0,02 | - 81,0 - - |
40 | Кокс Коксовая мелочь Известняк Металло-добавки | 370 - - 15,0 | 1,5 8,8 7,1 - | 10,0 13,3 - - | 3,8 3,8 - 90,3 | 4,3 4,15 54,0 - | 52,8 53,6 1,53 8,1 | 0,13 0,15 - 0,01 | 0,5 0,61 - 0,02 | 0,40 0,47 - 0,03 | - 81,0 - - |
41 | Кокс Коксовая мелочь Известняк Металло-добавки | 432 - - 7,5 | 2,85 7,0 - - | 9,67 11,5 - - | 10,8 10,95 - 90,4 | 2,8 2,6 90,6 - | 42,9 43,7 2,3 9,0 | - - - 0,5 | 0,06 0,06 - 0,3 | 1,8 1,0 - 0,02 | - 80,5 - - |
Продолжение табл. П.10
Вариант | Вид мате-риала | Расход материала, кг/т чугуна | Содержится в материале | Неполный химический состав золы, топлива, известняка, % | |||||||
влаги | золы | Fe | CaO | SiO2 | Mn | P | S | C | |||
42 | Кокс Коксовая мелочь Известняк Металло-добавки | 390 - - 20,0 | 0,8 6,4 - - | 10,6 13,2 - - | 6,6 6,8 - 90,7 | 3,3 3,1 91,0 - | 53,8 54,1 0,8 7,9 | - - - 0,5 | - - - 0,3 | 0,8 0,86 - 0,01 | - 80,6 - - |
43 | Кокс Коксовая мелочь Известняк Металло-добавки | 385 - - 2,5 | 0,9 7,1 - - | 10,7 13,4 - - | 6,7 6,7 - 90,5 | 3,25 3,1 90,9 - | 54,1 54,2 0,95 8,1 | - - - 0,43 | - - - 0,35 | 0,8 0,85 - 0,01 | - 80,5 - - |
Продолжение табл. П. 10
Вариант | Вид материала | Расход материала, т/т чугуна | Содержание в материале | Неполный химический состав золы, топлива, известняка, % | |||||||
Влаги | Золы | Fe | CaO | SiO2 | Mn | P | S | C | |||
44 | Кокс Коксовая мелочь Известняк Металлодобавки | 390 - - 2,5 | 0,85 8,0 - - | 10,9 13,5 - - | 6,65 6,9 - 90,1 | 3,4 3,1 90,5 - | 53,6 54,2 0,86 9,2 | - - - 0,48 | - - - 0,37 | 0,75 0,8 - 0,01 | - 80,6 - - |
45 | Кокс Коксовая мелочь Известняк Металлодобавки | 400 - - 2,0 | 0,5 6,5 4,3 - | 10,64 13,7 - - | 11,2 11,8 - 90,3 | 2,3 2,1 54,0 - | 43,61 43,8 1,05 8,9 | - - - 0,47 | - - - 0,33 | 1,45 1,54 - 0,01 | - 80,4 - - |
46 | Кокс Коксовая мелочь Известняк Металлодобавки | 375 - - 15,0 | 1,95 6,3 4,2 - | 10,7 13,8 - - | 4,01 4,0 - 90,3 | 3,4 3,1 53,8 - | 56,4 56,8 1,84 9,2 | 0,15 0,16 - 0,3 | 0,15 0,18 - - | 0,50 0,55 - 0,02 | - 81,0 - - |
47 | Кокс Коксовая мелочь Известняк Металлодобавки | 395 - - 3,0 | 2,7 5,3 4,3 - | 11,0 14,3 - - | 4,9 5,1 - 90,5 | 6,2 5,9 54,9 - | 48,4 49,5 0,4 8,6 | 0,15 0,2 - 0,21 | 0,15 0,18 - 0,23 | 0,45 0,53 - 0,03 | - 80,8 - - |
48 | Кокс Коксовая мелочь Известняк Металлодобавки | 415 - - 10,0 | 3,8 7,0 3,8 - | 8,6 11,0 - - | 5,3 5,8 - 90,8 | 3,5 3,35 54,2 - | 49,5 50,1 0,8 7,9 | 0,06 0,1 - 0,5 | 0,4 0,6 - 0,4 | 0,61 0,85 - 0,03 | - 80,5 - - |
Окончание табл. П. 10
Вариант | Вид материала | Расход материала, т/т чугуна | Содержание в материале | Неполный химический состав золы, топлива, известняка, % | |||||||
Влаги | Золы | Fe | CaO | SiO2 | Mn | P | S | C | |||
49 | Кокс Коксовая мелочь Известняк Металлодобавки | 380 - - 10,0 | 2,2 12,1 3,4 - | 10,0 13,7 - - | 5,2 5,7 - 90,5 | 5,4 5,35 54,1 - | 42,5 54,2 1,35 7,0 | - - - 0,1 | - - - 0,3 | 0,40 0,45 - 0,02 | - 81,0 - - |
50 | Кокс Коксовая мелочь Известняк Металлодобавки | 370 - - 15,0 | 1,7 11,7 3,6 - | 10,1 15,1 - - | 5,1 5,5 - 90,6 | 1,6 1,7 54,0 - | 56,5 56,3 1,48 7,7 | - - - 0,1 | - - - 0,3 | 0,39 0,44 - 0,02 | - 81,1 - - |
Таблица П. 11
Исходные данные для выполнения работы 7
Вариант |
| Давление в слое, кПа | Коэффициент избытка воздуха, доли ед. | H, м | B, м | V, м/мин | S, м2 | C, м/мин | ||
P1 | P2 | ![]() | ![]() | |||||||
1 | 0,86 | 101,0 | 96,0 | 1,4 | - | - | - | - | 306 | 0,0084 |
2 | 0,89 | 95,0 | - | 1,04 | 1,2 | 0,3 | 3,0 | 2,5 | - | - |
3 | 0,87 | 90,0 | 98,0 | 1,15 | - | - | - | - | 108 | 0,00725 |
4 | 0,88 | 98,0 | - | 1,5 | 1,3 | 0,3 | 2,0 | 3,0 | - | - |
5 | 0,85 | 100,0 | 95,0 | 1,3 | - | - | - | - | 520 | 0,0083 |
6 | 0,86 | 100,01 | - | 1,05 | 1,25 | 0,4 | 4,0 | 2,75 | - | - |
7 | 0,85 | 89,0 | 92,0 | 1,4 | - | - | - | - | 306 | 0,008 |
8 | 0,84 | 92,0 | - | 1,6 | 1,2 | 0,25 | 3,0 | 2,75 | - | - |
9 | 0,86 | 99,5 | 93,5 | 1,5 | - | - | - | - | 108 | 0,0075 |
10 | 0,88 | 96,0 | - | 1,3 | 1,5 | - | - | - | 520 | 0,0078 |
11 | 0,85 | 94,0 | 97,5 | 1,55 | - | 0,3 | 2,0 | 3,2 | - | - |
12 | 0,87 | 97,5 | - | 1,42 | 1,37 | 0,42 | 4,0 | 2,7 | - | - |
13 | 0,85 | 100,0 | 98,5 | 1,3 | - | - | - | - | 306 | 0,0082 |
14 | 0,86 | 98,5 | - | 1,35 | 1,12 | 0,35 | 3,0 | 2,5 | - | - |
15 | 0,87 | 91,7 | 95,4 | 1,15 | - | - | - | - | 108 | 0,008 |
16 | 0,85 | 96,4 | - | 1,05 | 1,35 | 0,32 | 2,0 | 2,7 | - | - |
17 | 0,88 | 101,1 | 98,6 | 1,22 | - | - | - | - | 520 | 0,0087 |
18 | 0,86 | 101,0 | - | 1,42 | 1,3 | 0,42 | 4,0 | 3,0 | - | - |
19 | 0,87 | 98,6 | 100,1 | 1,3 | - | - | - | - | 306 | 0,009 |
20 | 0,85 | 97,0 | - | 1,25 | 1,4 | 0,42 | 3,0 | 3,0 | - | - |
21 | 0,84 | 98,4 | 96,5 | 1,1 | - | - | - | - | 108 | 0,009 |
22 | 0,83 | 89,0 | - | 1,3 | 1,1 | 0,38 | 2,0 | 3,0 | - | - |
23 | 0,85 | 98,0 | 100,2 | 1,2 | - | - | - | - | 520 | 0,01 |
24 | 0,79 | 90,0 | - | 1,12 | 1,24 | 0,42 | 4,0 | 3,1 | - | - |
25 | 0,89 | 99,0 | 96,0 | 1,15 | - | - | - | - | 123 | 0,007 |
26 | 0,84 | 101,1 | - | 1,6 | 1,3 | 0,25 | 1,83 | 2,8 | - | - |
27 | 0,85 | 98,3 | 99,7 | 1,55 | - | - | - | - | 94 | 0,0065 |
28 | 0,81 | 101,0 | - | 1,03 | 1,23 | 0,22 | 1,83 | 2,8 | - | - |
29 | 0,84 | 101,0 | 97,0 | 1,07 | - | - | - | - | 178 | 0,0065 |
30 | 0,87 | 100,0 | - | 1,2 | 1,02 | 0,2 | 2,43 | 2,7 | - | - |
31 | 0,85 | 90,0 | 100,0 | 1,08 | - | - | - | - | 110 | 0,007 |
32 | 0,80 | 95,0 | - | 1,08 | 1,25 | 0,3 | 2,5 | 2,8 | - | - |
33 | 0,88 | 96,7 | 94,5 | 1,25 | - | - | - | - | 120 | 0,0075 |
Окончание табл. П. 11
Вариант |
| Давление в слое, кПа | Коэффициент избытка воздуха, доли ед. | H, м | B, м | V, м/мин | S, м2 | C, м/мин | ||
P1 | P2 | ![]() | ![]() | |||||||
34 | 0,85 | 93,7 | - | 1,17 | 1,33 | 0,3 | 2,5 | 2,8 | - | - |
35 | 0,84 | 95,0 | 98,0 | 1,13 | - | - | - | - | 278 | 0,008 |
36 | 0,86 | 99,0 | - | 1,22 | 1.08 | 0,35 | 3,5 | 2,9 | - | - |
37 | 0,87 | 100,1 | 98,0 | 1,24 | - | - | - | - | 414 | 0,008 |
38 | 0,88 | 97,0 | - | 1,01 | 1,6 | 0,35 | 3,0 | 2,8 | - | - |
39 | 0,85 | 100,0 | 101,2 | 1,05 | - | - | - | - | 400 | 0,008 |
40 | 0,80 | 101,15 | - | 1,53 | 1,13 | 0,4 | 4,0 | 3,0 | - | - |
41 | 0,79 | 100,0 | 97,7 | 1,16 | - | - | - | - | 380 | 0,0075 |
42 | 0,81 | 99,9 | - | 1,14 | 1,56 | 0,4 | 3,5 | 2,0 | - | - |
43 | 0,89 | 93,5 | 99,8 | 1,47 | - | - | - | - | 520 | 0,008 |
44 | 0,90 | 94,4 | - | 1,62 | 1,08 | 0,41 | 4,0 | 3,0 | - | - |
45 | 0,87 | 98,1 | 96,5 | 1,34 | - | - | - | - | 305 | 0,0082 |
46 | 0,86 | 97,9 | - | 1,28 | 1,38 | 0,43 | 3,0 | 2,5 | - | - |
47 | 0,85 | 97,1 | 100,3 | 1,03 | - | - | - | - | 408 | 0,0072 |
48 | 0,84 | 100,4 | - | 1,47 | 1,05 | 0,38 | 2,0 | 3,0 | - | - |
49 | 0,85 | 100,5 | 95,5 | 1,61 | - | - | - | - | 520 | 0,009 |
50 | 0,86 | 98,3 | - | 1,09 | 1,49 | 0,45 | 4,0 | 3,0 | - | - |
Рис.П.9-1. [15] Проекция поверхности ликвидус четверной системы C–M–A–S при 5 % Al2O3
Рис.П9-.2. [15]Проекция поверхности ликвидус четверной системы C–M–A–S при 10 % Al2O3
Рис.П9-.3 [15]. Проекция поверхности ликвидус четверной системы C–M–A–S при 15 % Al2O3
Рис.П.9-4.[15] Проекция поверхности ликвидус четверной системы C–M–A–S при 20 % Al2O3
Дата добавления: 2018-04-15; просмотров: 318; Мы поможем в написании вашей работы! |
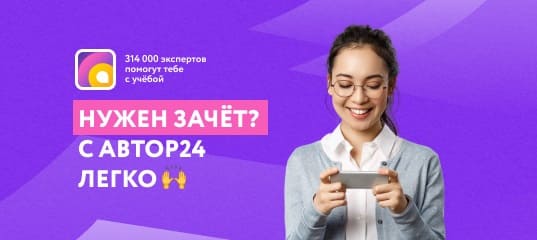
Мы поможем в написании ваших работ!