Исходные данные для выпускной квалификационной работы
Исходными данными для выполнения ВКР являются материалы преддипломной практики. К ним могут относиться:
Ø технологические процессы производств;
Ø планы расположения оборудования;
Ø схемы, сборочные чертежи конструкторской документации изделий, выпускающихся на базовом предприятии, предназначенных для модернизации;
Ø годовая трудоемкость работ, выполняемых на участке (цехе);
Ø режим работы проектируемого участка или цеха (обычно принимается двухсменный режим);
Ø техническое задание на разработку комплексов механизации или автоматизации производства;
Ø постановка задач для проведения исследований.
Задание на выпускную квалификационную работу
После утверждения темы вместе с руководителем студент составляет задание на выполнение дипломного проекта. Оно подписывается студентом, преподавателем-руководителем ВКР, утверждается зам директора по НМР.
В задании указываются:
- название темы дипломного проекта (дипломной работы);
- фамилии руководителя, консультанта и нормоконтролёра;
- исходные данные;
- указания по выполнению отдельных разделов проекта;
- перечень графических материалов;
Задание оформляется на бланке установленной формы. Составляется в двух экземплярах: первый выдается студенту перед преддипломной практикой, среди задач которой сбор данных для дипломного проекта и обобщение информации по избранной теме; второй остается у руководителя и вместе с дипломным проектом представляется к защите.
|
|
Содержание и объем выпускной квалификационной работы
Состав выпускной квалификационной работы
Выпускная квалификационная работа, как правило, оформляется в виде пояснительной записки, комплекта технологической документации и графической части. Требования к содержанию, объему и структуре выпускной квалификационной работы определяются образовательной организацией.
Пояснительная записка состоит из следующих основных частей:
Ø технологической (включая проектирование участка);
Ø конструкторской;
Ø исследовательской;
Ø экономической;
Ø безопасность жизнедеятельности;
Ø охрана окружающей среды.
В зависимости от тематики дипломного проекта некоторые перечисленные разделы могут отсутствовать.
При необходимости к ВКР могут быть приложены разработанные и изготовленные в процессе выполнения проекта натурные образцы приборов, устройств, механизмов, пакеты прикладных программ и др.
Пояснительная записка является основным документом, в котором излагаются исчерпывающие сведения о выполненной работе. Примерный объем пояснительной записки в компьютерном варианте 40 - 60 страниц.
|
|
В записке излагается содержание работы, делаются выводы и приводятся рекомендации. Пояснительная записка должна полно раскрывать сущность дипломного проекта, содержать все необходимые пояснения, расчеты, должна быть изложена грамотно, техническим литературным языком в предельно сжатой форме.
Пояснительная записка должна включать следующие структурные элементы:
Ø титульный лист (Приложение А);
Ø задание на проектирование (Приложение Б);
Ø реферат;
Ø содержание;
Ø перечень листов графических документов;
Ø введение;
Ø технологическую часть;
Ø конструкторскую часть*;
Ø исследовательскую часть*;
Ø расчетную часть;
Ø экономическую часть*;
Ø безопасность жизнедеятельности;
Ø охрана окружающей среды
Ø заключение;
Ø используемые источники информации;
Ø спецификации чертежей, схем;
Ø приложения.
Разделы отмеченные (*), в зависимости от темы дипломного проекта могут отсутствовать. При этом общий объем пояснительной записки должен соответствовать установленным нормам. Пример оформления листа «Содержание» см. Приложение Д.
|
|
Комплект технологической документации на изготовление сварного изделия (узла), оформленный в виде альбома, в который входят следующие технологические документы:
– титульный лист;
– карта эскизов;
– комплектовочные карты;
– маршрутные карты;
– карты технического контроля.
Разработанный технологический процесс оформляется в соответствии с требованиями Единой системы технологической документации (ЕСТД) на бланках в программе Microsoft Excel, подписан дипломником и руководителем.
Графическая часть должна содержать не менее 3-4 чертежей формата А1, выполненных карандашом, или с использованием современных графических пакетов «Компас», AutoCAD и др. Состав технологической, конструкторской и исследовательской частей дипломного проекта является примерным. Он может быть дополнен и несколько видоизменен для различных категорий выпускных квалификационных работ. По согласованию с руководителем методического объединения требования к составным частям пояснительной записки на конкретную тему устанавливает руководитель проекта с оформлением этих требований в задании на дипломный проект.
Примерный состав чертежей выпускных
квалификационных работ
|
|
– сборочный узел;
– рабочие чертежи деталей;
– план участка;
– средства технологического оснащения (специальное технологическое оборудование, приспособления, средства механизации и автоматизации);
– технико-экономические показатели.
Реферат
В реферате излагаются краткие сведения о выполненной работе и выводы. Он строится по следующей схеме:
Ø цель работы;
Ø текст реферата;
Ø сведения об объеме работы, количестве иллюстраций, рисунков, таблиц и т.д.
В тексте реферата отражается сущность выполненной работы, приводятся конкретные достигнутые результаты, краткие выводы, эффективность разработки, возможности применения полученных результатов.
Объем реферата должен составлять не более 0,5-0,7 страниц машинописного текста.
Введение
Даётся краткий обзор данной отрасли в общей системе народного хозяйства, отмечается актуальность проекта, указываются задачи, роль сварки и её развитие, состояние перспективы совершенствование сварочных процессов в данной отрасли.
Во введении обосновывается выбор темы, определяемый ее актуальностью, формируются проблема и круг вопросов, необходимых для ее решения; определяется цель работы с ее расчленением на взаимосвязанный комплекс задач, подлежащих решению, для раскрытия темы; указываются объект исследования, используемые методы анализа и литературные источники.
Во введении необходимо кратко изложить:
• предполагаемый объём использования высокопроизводительных современных методов сварки и возможность комплексной механизации и автоматизации производства по изготовлению данного изделия;
• мероприятия, обеспечивающие повышение производительности труда сварочных работ при производстве проектируемого изделия.
Писать «введение» следует не пространно, а применительно только к теме проекта - данной отрасли, отразить взаимное влияние и развитие данной отрасли и сварочной техники используя при этом более свежие материалы из журнальных и газетных статей, материалы заводы.
Использование устаревших материалов, например, книг и журналов более двух трёх летней давности недопустимо; тоже и заводских материалов.
Технологическая часть
Технологическая часть включает обоснование решений, принятых по этапам проектирования технологического процесса, выполнение расчетов по его разработке, оформление технологической документации.
В этой части пояснительной записки приводятся результаты по проектированию технологии изготовления сварного узла; обосновываются изменения, внесенные в технологию по сравнению с базовым вариантом; выбор оборудования, оснастки, материалов; проектирование участка (цеха).
Технологическая часть должна содержать перечисленные ниже разделы.
6.4.1. Конструкция, назначение и условия работы сварного изделия (сборочной единицы)
Кратко изложить назначение, техническую характеристику, условия работы изделия с указанием основных сборочных единиц и деталей, их габаритных размеров.
Данный материал рекомендуется подбирать будучи на преддипломной практике, где имеются соответствующие источники по отрасли, как, например, для описания общих сведений и устройств.
6.4.2. Характеристика материала, применяемого для изготовления изделия
Приводятся данные о материале изделия, его химическом составе, физико-механических свойствах, условиях поставки.
Следует обосновать возможности данного материала для использования при производстве сварных конструкций.
6.4.3. Анализ технологичности конструкции
Анализ технологичности конструкции имеет конечной целью предложение по повышению производительности труда, снижению затрат и сокращение времени на технологическую подготовку производства, изготовление, техническое обслуживание и ремонт оборудования.
Качественная оценка технологичности конструкции должна включать:
1. Возможность расчленения ее на отдельные сборочные единицы, которые могут быть собраны и сварены на отдельных рабочих местах с применением высокопроизводительного сварочного оборудования.
2. Возможность применения универсальной сборочно-сварочной оснастки.
3. Возможность применения механизированных и автоматических способов сварки, в том числе и роботизированных.
4. Доступность выполнения сварных швов.
5. Обосновать предлагаемые конструктивные изменения, направленные на улучшение технологичности проектируемого изделия или сборочной единицы.
На основании оценки технологичности конструкции разрабатываются, если это целесообразно, предложения по изменению конструкции, технологии изготовления, способа сварки и т.д.
6.4.4. Разработка технологического процесса
Технологическая часть проекта основная и наиболее трудоёмкая часть дипломного проекта.
При проектировании технологических процессов студент должен:
а. Определить рациональную степень механизации и автоматизации сборочно-сварочных работ, которая зависит от габаритов и веса изготавливаемых изделий, их конструкций, сечения, длины и конфигурации сварных швов, а так же от типа производства. Этим определяется применение видов сварки: ручной, механизированной, автоматической, сборки в стационарных либо в передвижных приспособлениях и т.д.;
б. Выбрать наиболее целесообразный приём выполнения сборочно-сварочных операций с целью повышения производительности труда, снижения трудоёмкости работ;
в.Определить рациональные режимы сварки, термической обработки, зависящие главным образом, от свойств свариваемых материалов, толщины последних и конструктивных форм сварных соединений;
г. Предусмотреть организацию производства;
д.Выбрать сварочные материалы с учетом способа сварки и состава свариваемого материала;
е. Подобрать сварочное и другое оборудование;
ж. С учётом требований технологического процесса установить профессии, разряды работ на каждом рабочем месте;
з. Предусмотреть в технологических картах контрольные и транспортные операции, расположив их в должной последовательности с новыми технологическими операциями и описать в пояснительной записке методику контроля продукции.
Разработка технологического процесса изготовлений изделий начинается с анализа заводского технологического процесса.
6.4.4.1. Анализ существующего технологического процесса
Анализ производится с целью изыскания возможностей совершенствования технологии изготовления, повышения производительности и обеспечения качества сварки.
При анализе студент должен обратить внимание на следующий примерный перечень вопросов:
• оптимальность расчленения изделия на сварные узлы (подузлы);
• правильность выбора видов сварки;
• целесообразность применяемого сварочного оборудования;
• обоснованность рассчитанных режимов сварки;
• обоснованность выбора сборочно-сварочных приспособлений и инструментов;
• соответствие марок электродов, флюсов и электродной проволоки, газов;
• рациональность организации рабочих мест;
• эффективность использования транспортных средств;
• правильность выбора методов контроля.
Результаты анализа существующего технологического процесса должны быть изложены в пояснительной записке. Далее студент должен обосновать внесенные им изменения в технологические операции, техническую, экономическую, социальную целесообразность этих изменений.
6.4.5. Выбор способа сварки
Дать анализ существующего способа сварки, его преимущества и недостатки.
На основании анализа конструкции, ее назначения, технических условий изготовления, материала, из которого она должна быть изготовлена, программы выпуска и условий производства необходимо выбрать оптимальный способ сварки, обеспечивающий минимальную себестоимость изготовления.
При выборе путём сравнений известных и новых способов сварки предпочтение следует отдавать тому, который обеспечивает для данных условий:
1. Более высокую производительность (автоматические и механизированные способы сварки).
2. Более высокое качество.
3. Снижает металлоемкость.
4. Улучшает санитарно-гигиенические условия.
5. Дает более высокую маневренность в получении швов высокого качества во всех пространственных положениях.
6.4.6. Методы и способы сборки
Сборка - процесс последовательного соединения и скрепления деталей между собой для образования узла, подузла или изделия.
Операция сборки является наиболее трудоемкой среди других операций по изготовлению и зависит в первую очередь от сложности, массы и размеров конструкции и типа производства (единичное, мелкосерийное, серийное, крупносерийное, массовое).
По форме сборки различают: индивидуальную; бригадную; конвейерную.
По методу сборки различают: стационарную; подвижную.
Способы сборки:
· По разметке - с помощью различных универсальных лёгких приспособлений с последующей их прихваткой. Этот способ применяется в индивидуальном производстве.
· В универсальных приспособлениях, например, в позиционерах или плитах с пазами, в которых могут быть установлены упоры фиксаторы или зажимы соответственно конструкции изделия. Способ применяется при серийном и массовом производстве.
· С помощью лёгких шаблонах накладываемых на детали или собираемых вместе с ними на время прихватки. Способ применяется в серийном и массовом производстве.
· С помощью специальных приспособлений - применяется в массовом производстве и серийном производстве.
6.4.7. Выбор сварочных материалов
Выбор сварочных материалов непосредственно вытекает из принятого способа сварки.
В зависимости от принятого способа сварки следует сделать и соответствующий выбор сварочных материалов:
• Для ручной дуговой сварки – тип и марку покрытого металлического электрода;
• Для автоматической и механизированной сварки под флюсом - сварочную (электродную) проволоку и флюс;
• Для аргонодуговой сварки - вольфрамовый неплавящийся электрод и инертный газ;
• Для сварки в углекислом газе - сварочную проволоку и углекислый газ.
6.4.8. Выбор сварочного оборудования
Выбор источников питания и сварочного оборудования непосредственно вытекает и определяется способом сварки, сварочным материалом и режимом сварки. Рекомендуется эти вопросы решать одновременно.
Технологические показатели и техническую характеристику следует занести в пояснительную записку (можно в виде таблицы).
Предварительно следует последовательно установить род тока, систему питания, режим сварки и основные параметры источника питания (напряжение холостого хода, рабочее напряжение, номинальный режим работы, внешняя характеристика).
К показателям сварочного оборудования: систему регулирования дуги, регулирование скоростей подачи электродной проволоки и сварки, и область применения.
6.4.9. Расчёт и выбор режимов сварки
Под режимом сварки понимают совокупность параметров, при которой обеспечивается требуемое качество, форма и размеры сварного соединения (шва) при высокой производительности. Эти параметры для способов сварки различны. При выполнении дипломного проекта режим сварки рекомендуется выполнять расчётным методом.
1. Параметрами режима ручной дуговой сварки является:
2. Диаметр электрода
3. Тип и марка электрода.
4. Величина сварочного тока.
5. Напряжение на дуге (обычно указывается в паспорте электрода)
6. Скорость сварки (при ручной дуговой сварке является условной, т.к. перемещение дуги зависит от квалификации сварщика).
7. Число слоев.
8. Положение шва в пространстве.
Основными параметрами режима автоматической и полуавтоматической сварки под флюсом является:
1. Величина сварочного тока
2. Диаметр электродной проволоки.
3. Число слоев.
4. Напряжение на дуге.
5. Скорость сварки.
6. Скорость подачи электродной проволоки.
7. Расход флюса.
8. Вылет электрода.
При сварке плавящимся электродом в углекислом газе параметры режима в основном те же, что и при сварке под флюсом. Установленного расчётного метода расчёта режима сварки нет. На практике обычно пользуются апробированными таблицами и графиками.
К основным параметрам сварки плавящимся электродом в углекислом газе относятся:
1. диаметр электродной проволоки;
2. сила сварочного тока;
3. напряжение на дуге;
4. скорость сварки;
5. скорость подачи электродной проволоки;
6. расход углекислого газа;
7. вылет электрода.
6.5. Расчетная часть
Для каждой операции технологического процесса определяют норму выработки, в записке приводится описание расчета технических норм времени.
Нормирование ведут по каждой операции в отдельности, учитывая условия её выполнения по справочным общемашиностроительным отраслевым и заводским нормам.
Результаты расчета заносят в технологические карты.
В результате нормирования получим укрупненные нормы времени для расчёта план участка.
6.5.1. Нормирование сборочных работ
Норма штучного времени на сборочные работы Тш определяется по формуле:
Тш =Туст + Ткр + Тприхв +Т пов + Тсн (мин), где
Туст - сумма времени на установку деталей (т 54 ) (4)
Ткр- сумма времени на крепление и открепление деталей
Тприхв - сумма времени на прихватки
Тпов - сумма времени на повороты деталей (узлов)
Тсн - сумма времени на снятие узла, изделия.
6.5.2. Нормирование сварочных работ
А. Ручная дуговая сварка
Норма штучного времени Тш определяется по формуле:
Тш = (То +t вш )l + tви, (мин),
То – основное время на 1 погонный метр шва в мин
То = 60Fш j \α I (м/мин)
Fш – площадь поперечного сечения сварного шва ( мм2)
α – коэффициент наплавки (г/А час)
Iсв - сварочный ток (А)
j - плотность металла (г\ см3)
tвш - вспомогательное время, связанное со швом (на 1 погонный метр шва, мин) табл.71 [15]
tви - вспомогательное время, связанное с изделием (мин) табл. 72 [15]
Б. Автоматическая и полуавтоматическая сварка под флюсом и в среде защитного газа
Норма штучного времени Тш определяется по формуле:
Тш = (То + t вш ) l + tви, (мин),
То – основное время на 1 погонный метр шва в мин
То = 60Fш j \α I (м/мин)
Fш – площадь поперечного сечения сварного шва ( мм2)
α – коэффициент наплавки (г/А час)
Iсв - сварочный ток (А)
j - плотность металла (г\ см3)
tвш - вспомогательное время, связанное со швом (на 1 погонный метр шва ; мин) табл.85 – 86 [15]
tви - вспомогательное время, связанное с изделием (мин) табл. 87 – 88 [15]
В. Нормирование кислородной резки
Норма штучного времени Тш определяется по формуле:
Тш = (t op Ko + t B1) l + t o под + t в2 к1,
top – основное время резки 1 погонного метра мин
ко – коэффициент учитывающий чистоту кислорода и состав разрезаемой стали табл. 44 [15]
tв1 - вспомогательное время, зависящее от длины реза табл. 45 [15]
tв2 - вспомогательное время , не зависящее от длины реза на одну деталь мин табл. 42 [15]
6.5.3.Определение массы изделия и расхода основных материалов
Масса деталей определяется по формуле:
Рд = V*J |1000 (кг), где
Рд – масса детали (кг)
V - объем детали (см3)
J – плотность материала (г/см3)
Расход основного материала определяется с учетом отходов по формуле:
Р = Рд * Z, где
Р – масса требуемого количества основного материала (кг)
Z – коэффициент отхода (В машиностроении Z = 1,02 – 1,08)
Результаты свести в таблицу.
Таблица 1- Расход основного материала
№ детали | Наименование детали | Количество деталей на изделие | Масса одной детали (кг) Рд | Масса деталей на изделие | Z | Масса основного материала на одно изделие |
ИТОГО: _____________
6.5.4. Расчет массы наплавленного металла
Производится по формуле:
PH =Fш*Lш*L*J (г), где
PH-масса направленного металла(г)
FШ- площадь поперечного сечения шва(мм2)
L-длина шва (м) (или FШ в см2 и L в см)
J- плотность металла (г\см3) для стали J= 7.85 г\см3
Масса наплавленного металла подсчитывается раздельно для каждой операции и для каждого сечения.
6.5.5. Определение расхода вспомогательных материалов
А. Расход электродов Рэ.
Производится по формуле:
Рэ = Рн\ Кн * (1+ Кэ) (кг), где :
Рэ – расход электродов (кг)
Рн – масса наплавленного металла (кг)
Кп – коэффициент перехода металла электрода в шов [15]
Кэ – Отношение массы электродного покрытия к массе электрода (кэ ≈ 0,4)
Таблица 2 - Расход электродов
№ операции | Наименование операции | Марка электрода | Диаметр электрода | Расход электродов |
ИТОГО: ______________
Б. Расход электродной проволоки Рпр
Определяется по формуле: Рпр = Рн /Кпр (кг),
Где Рн – масса наплавленного металла (кг)
Кпр - коэффициент перехода металла проволоки в шов( сварка под флюсом Кпр = 0, 98; сварка в среде СО2- Кпр =0,92)
Таблица 3 - Расход электродной проволоки
№ операции | Наименование операции | Марка проволоки | Диаметр проволоки | Расход проволоки |
ИТОГО: _____________
В. Расход флюса Рф
Определяется по формуле: Рф = (1,0 – 1,2)*Рн
Таблица 4 - Расход флюса
№ операции | Наименование операции | Марка флюса | Расход флюса |
ИТОГО: _____________
Г. Расход защитного газа (СО2 ) Рг
Определяется по формуле: Рг = Рг* tсв (литр), где Рг – расход газа на операцию (изделие); Рг – объемный расход газа (литр/ мин); tсв – время горения дуги tсв = То*l То – (мин/м) l- (метры)
Таблица 5 - Расход газа
№ операции | Наименование операции | Объемный расход газа л/мин | Время горения дуги, мин | Расход газа л/мин |
ИТОГО: _______________
6.5.5. Расход технологической электроэнергии.
Расход технологической электроэнергии производится по формуле:
А = I св U д *t св + Wo(Тш – t св)(кВт ч.)
1000 n
Где: I св – сила сварочного тока, в А
U д – напряжение на дуге, в В
N – КПД источника питания
t св – время горения дуги, час
Wo – мощность холостого хода источника питания, вкт
Тш – штучное время на операцию, час
Таблица 6 - Значение n и W o
Вид источника | n | W o (кВт) |
Св.трансформатор | 0,8_0,9 | 0,3_0,5 |
Св.выпрямитель | 0,7_0,84 | 0,35_0,55 |
Св.генератор | 0,4_0,6 | 2,5_3 |
При наличии значения n и W o берутся по паспортным данным источника
T св = То * L (час), где
То – основное время на 1 литр шва в мин/м
L – длина шва в метрах
При сварке под флюсом на переменном токе и при многопостовой
Сварке расход эл.энергии Ао определяется по формуле:
Ао = А(кВт ч )
Ph кг
Где Ph – масса наплавленного металла в кг
Таблица 7 - Расхода электроэнергии
ИТОГО: ____________
6.5.6. Степень и уровень механизации сварочных работ
Степень механизации См определяется по формуле:
См = Е к Т м 100%
Е Тhm+E Ktm
Где: K – коэффициент приведения трудоемкости механизированных способов сварки К трудоемкости ручной дуговой сварки
Тм – трудоемкость механизированных работ
Тhm – трудоемкость немеханизированных работ
Тм и Thм равны соответствующим Е Тм
При отсутствии ручной дуговой сварки и выполнения прихваток электродами в Е Тhм входит время на выполнение всех прихваток
Е Thм = ЕТприхв.
Время, идущее на выполнение прихваток под ручную дуговую сварку, при определении
Е Тhм не учитывается.
Уровень механизации Yм определяется по формуле:
Yм = E KTm- Е Тм 100% или Yм = См (1 – 1 ) 100%
E Thм + Е КТм Кср
Кср – средний коэффициент приведения определяется по формуле:
Кср = Е КТм
Е Тм
Конструкторская часть
Эта часть является проектной. В ней студент разрабатывает предложения по совершенствованию технологического процесса производства, повышению результативности и качества работы данного предприятия (организации).
Студентом разрабатываются: схемы управления объектами, осуществляется выбор оборудования и его обоснование и т.д.
Задачи по проектированию также могут сводиться к модернизации существующих технологий на основе изучения их работы в производственных условиях в период прохождения преддипломной практики с целью повышения их производительности, снижения металлоемкости, трудоемкости или др.
Все предложения и рекомендации должны носить конкретный характер, быть доведены до стадии разработки, обеспечивающей их практическое применение. Базой для разработки конкретных мероприятий и предложений служит проведенный анализ исследуемой проблемы, а также имеющийся прогрессивный отечественный и зарубежный опыт.
Исследовательская часть
Дипломные проекты содержат исследовательскую (экспериментальную) часть. Данная часть должна быть увязана с планами организационно-технических мероприятий предприятий с тем, чтобы выполненная работа способствовала решению конкретных профессиональных задач.
Содержание исследовательской части должно быть направлено на решение конкретных технологических вопросов, связанных с темой дипломного проекта. Ее состав и объем определяется руководителем. Это может быть:
- сопоставление имеющегося и проектируемого технологического процесса;
- - исследование эффективности использования механизированных и автоматических средств производства;
- - эксперимент;
- и т.д.
Обязательными для дипломного проекта являются логическая связь между главами и последовательное развитие основной идеи темы на протяжении всей работы.
6.8. Организационная часть
6.8.1. Тип производства
В соответствии с запланированным объёмом выпуска продукции, номенклатуры, трудоёмкости и веса изделий нужно выбрать тип производства и охарактеризовать его. Существует 3 типа производства: единичное, массовое, серийное.
Единичное производство определяется, прежде всего, тем, что выпуск продукции производится по отдельным заказам единичными экземплярами или в очень небольших количествах, причём заказ на данное изделие обычно не повторяется. В сварочном производстве это крупные конструкции, например, котельных установок, сварных станин для тяжёлого машиностроения, строительных конструкций для специального назначения. Характерной чертой единичного производства является универсальность применяемого оборудования и сборочно-сварочных приспособлений. Сварку выполняют в ручную или на автоматах.
Серийное производство имеет место при достаточно большой номенклатуре изделий и значительном объёме программы, продукция изготовляется сериями или партиями. Примером серийного производства может служить изготовление стандартных цистерн, типовых котлов, сельскохозяйственных машин. В серийном производстве при надлежащей организации труда и современном материально-техническом обеспечении рабочих мест целесообразно применение специальных сборочно-сварочных приспособлений, внедрять автоматизированные способы сварки, а на отдельных участках организовать поточные и даже автоматические линии.
Массовое производство проектируется при большом объёме выпуска изделий небольшой номенклатуры. Массовое производство позволяет широко и эффективно использовать специальное высокопроизводительное оборудование и сборочно-сварочные приспособления, механизировать производственные процессы, создать поточные и автоматические автомобильные и другие предприятия.
В соответствии с характером применяемого оборудования, технологического процесса, объемом выпуска продукции, степени специализации нужно произвести выбор метода организации производственного процесса и охарактеризовать его. Наиболее эффективной формой организации является поточное производство. Поточные линии могут быть ручными, механизированными и автоматическими, необходимо дать полную характеристику применяемой поточной линии.
6.8.2. Организация рабочего места
Под рабочим местом понимается зона трудовой деятельности человека, оснащенная комплексом технических средств и вспомогательным оборудованием, необходимым для выполнения трудовых операций. Целью организации рабочего места является оптимизация условий трудовой деятельности, обеспечивающих максимальную эффективность и безопасность работы на проектируемом участке или оборудовании.
При компоновке оборудования рабочего места следует принимать во внимание многочисленные факторы, влияющие на человека, оборудование и окружающую среду.
При организации рабочих мест, прежде всего, необходимо руководствоваться действующим государственным стандартом, отражающим совокупность эргономических и инженерно - психологических показателей комплекса оборудования рабочих мест.
Эргономические показатели подразделяются на следующие группы: гигиенические, антропометрические, физиологические, психофизиологические и психологические.
К гигиеническим показателям относятся: микроклимат (температура, влажность, давление, скорость движения воздуха), освещенность, вентилируемость, запыленность, загазованность, напряженность, шум.
Антропометрические показатели определяют соответствие комплекса оборудования рабочего места форме и размерам тела человека, распределение его веса.
Физиологические и психофизиологические показатели характеризуют соответствие рабочего места, его оборудования и устройств энергетическим, скоростным слуховым и другим психологическим возможностям человека.
Психологические показатели отражают соответствие оборудования рабочего места приобретённым и вновь формируемым навыкам человека, а так же возможностям восприятия и переработки информации.
Организация рабочего места должна обеспечить:
а) целесообразное расположение рабочего по отношению к оборудованию в целях кротчайших путей движения рабочего по отношению к оборудованию, в процессе выполнения элементов операций, удобства обзора процесса управления механизмами передвижения изделия;
б) безопасность рабочего в процессе работы;
в) целесообразное расположение вспомогательного оборудования и транспортных средств;
г) охрана труда от вредных влияний процесса (температура, светоизлучение, вредные газы, пылеобразование и тд.).
При разработке организации рабочего места необходимо выполнить следующее:
1 Составить план рабочего места с размещением: оборудования механизмов управления, рабочего стола - шкафа, место самого рабочего, место полуфабрикатов, материалов и т.д.
2 Нанести на план схемы движения рабочего при выполнении
операции.
3 Составить схему рабочего стола - шкафа с указанием отделением и назначения их, а так же перечня содержимого отделений (приспособлений, документации и др.).
4 Порядок обслуживания рабочего места, обеспечивающего производительную работу рабочего.
5 Технику безопасности, охрану труда, и противопожарную защиту, охрану окружающей среды.
6 Механизацию вспомогательных работ рабочего.
Эскизы, схемы, зарисовки помещаются по тексту в данном разделе пояснительной записки.
6.8.3. Организация управления участком
Управление участком поясняется графической схемой управления. На этой схеме студенты показывает соподчиненность руководителей и исполнителей на участке. Ниже приводятся примерная схема. Далее учащийся должен описать права и обязанности руководителей участка. Пример схемы управления цехом см. в Приложении В.
6.8.4. Организация внутрицехового транспорта
В сварочных цехах и участках применяются различные и подъёмно-транспортные средства. Выбор транспортных средств зависит от типа производства объёма и веса транспортируемых грузов и принятой формы организации работ. При изготовлении тяжёлых конструкций на предприятиях с единичным и мелкосерийным характером производства, как правило, применяются краны грузоподъёмностью 5-350 тонн, кран-балки 1-10 тонн, тельферы 0,25-5 тонн, электрические тележки (электрокары) и т.д.
Электрические тележки грузоподъёмностью 0,75; 1; 1,5; 2; 3; и 5 тонн применяются для транспортировки заготовок, полуфабрикатов сварных узлов из промежуточных складов на рабочие места и вывоза готовых изделий. Наиболее удобны электрические тележки с подъёмной платформой или с подъёмным краном.
Для обслуживания одного или двух рабочих мест можно использовать поворотный кран, установленный на колонне и снабжённый ручной, талью или электрическим тельфером.
6.8.5.Организация технического контроля
Основным назначение технического контроля на промышленном предприятии является недопущение брака и систематическая проверка технических и технологических элементов производства, конструкторских и технологических параметров изделия, направленное на обеспечение точного соответствия этих элементов и параметров установленных стандартом и техническим условием выпускаемым предприятием продукции. В соответствии с этим необходимо на участке вести следующие мероприятия:
1. контроль сварочных материалов.
2. контроль в процессе изготовления изделий.
3. окончательный контроль и приемо-сдаточные испытания.
4. мероприятия по обеспечению высокого качества выпускаемой продукции.
5. мероприятия по устранения брака.
Необходимо описать вид контроля, применяемый на участке. Если применяется контроль внешним осмотром, то необходимо привести нормы контроля изделий.
6.9. Экономическая часть
В этой части дипломного проекта студент должен произвести полный расчёт сметы затрат на производство изделий, определить сумму экономии от снижения затрат на производство продукции, определить технико-экономические показатели работы сварочного участка.
Организационная часть
Таблица 8 - Исходные данные
№ п/п | Исходные данные | Ед. измерения | Показатели |
1. | Изделие | ||
2. | Масса основного материала | кг | |
3. | Цена 1 кг основного материала | руб. | |
4. | Масса вспомогательного материала | ||
- | кг | ||
- | кг | ||
- | кг | ||
5. | Цена 1 кг вспомогательного материала | ||
- | руб. | ||
- | руб. | ||
- | руб. | ||
6. | Расход технологической энергии | кВт | |
7. | Цена 1 кВт | руб. | |
8. | Трудоемкость по каждой операции отдельно | ||
- | мин (час) | ||
9. | Разряд работы по каждой операции отдельно | ||
- | разряд | ||
10. | Часовая тарифная ставка по каждой операции отдельно | ||
- | руб. | ||
11. | Процент премии | % | |
12. | Коэффициент транспортно-заготовительных расходов | - | |
13. | Режим работы | смены | |
14. | Расход на содержание и эксплуатацию оборудования | % | |
15. | Общепроизводственные расходы | % | |
16. | Общехозяйственные расходы | % | |
17. | Прочие расходы | % | |
18. | Коммерческие (внепроизводственные) расходы | % | |
19. | - |
6.9.1.1 Расчёт производственной мощности и программы выпуска
Дать понятие производственной мощности
Мощность рассчитывается по производительности ведущего оборудования или по трудоёмкости ведущей операции по формуле:
- трудоёмкость ведущей операции
Fдо - действительный годовой фонд времени работы оборудования, в часах
- коэффициент, учитывающий серийность производства и связанный с серийностью потери времени на переналадку оборудования (от 4% до 12%).
принимаем
шт.
Различают 3 фонда времени:
1) Календарный фонд, т.е. количество часов в году
час.
2) Номинальный фонд времени, т.е. количество рабочих часов в году
час.
- количество календарных дней в году
- количество выходных и праздничных дней
- длительность смены (8 часов)
- количество рабочих смен в сутках
- количество праздников с сокращенной сменой (смена 7 часов)
3) Действительный (эффективный) фонд времени, учитывающий плановые потери времени на переналадку и ремонт оборудования.
час.
- коэффициент, учитывающий серийность производства и связанный с серийностью потери времени на переналадку оборудования (от 4% до 12%).
принимаем
Дать понятие годовой производственной программы.
Расчёт годовой производственной программы:
- коэффициент использования мощности, норма от 70% до 90%.
М – мощность предприятия
Принимаем
шт.
Для дальнейших расчетов принимаем Nгод - _____________ шт.
6.9.1.2. Расчет партии
Определение годовой программы по детали-представителю:
Nгод – годовая производственная программа, шт.
Кзо – коэффициент закрепления операции зависит от типа производства (для серийного 11-20)
Средняя программа по детали-представителю определяется по формуле:
шт. Число наименований изделий определяется по формуле:
Nгод – годовая производственная программа, шт.
Nдп.ср. - средняя программа по детали-представителю
6.9.1.3. Расчёт количества оборудования и его загрузки
Дать понятие основным фондам предприятия, видам износа, повышению эффективности использования оборудования на предприятии.
После установления плана производства нужно рассчитать необходимое количество оборудования для выполнения требуемого объёма работ. Для этого расчёта исходными данными являются: план производства в натуральном выражении; норма времени на единицу продукции в часах; действительный фонд времени работы оборудования.
Расчётное количество оборудования рассчитывается по каждой операции отдельно по формуле:
Тшт.- штучное время по операции
Fдо – действительный годовой фонд времени работы оборудования с учетом потерь времени на ремонт оборудования
Nгод – годовая производственная программа, шт.
Рассчитанное значение числа оборудования округляется до большего целого числа.
- принятое число единиц оборудования. Загрузка оборудования рассчитывается
- расчетное число единиц оборудования
- принятое число единиц оборудования
Таблица 9 - Расчет количества оборудования и его загрузки
№ | Наименование операции | Годовая производственная программа |
Действительный годовой фонд времени | Штучное время | Расчет кол-ва оборудования | Количество оборудования | Расчет загрузки оборудования | Процент загрузки оборудования | |
Расчетное | Принятое | ||||||||
Nгод | Fдо | Тшт | ![]() | nр | nпр | ![]() | Кз | ||
1. | |||||||||
2. | |||||||||
3. | |||||||||
ИТОГО | * | * | * | ** |
* - суммировать значение в данной колонке
** -рассчитать среднее значение показателей в данной колонке
6.9.1.3. Расчёт численности основных производственных рабочих
Дать понятие классификации персонала предприятия, структуры кадров, кадровой политики предприятия.
Расчёт численности основных производственных рабочих определятся по каждой операции отдельно по формуле.
- плановый коэффициент перевыполнения норм выработки.
Для сборщиков и сварщиков Кв = 1,2.
Т шт.- штучное время по операции
Nгод – годовая производственная программа, шт.
- действительный годовой фонд времени рабочего, в часах:
час.
- номинальный фонд времени при односменном режиме
- плановый процент потерь времени рабочего из-за невыходов на работу по причине отпусков и болезней. Зависит от контингента работающих, определяется по фактическим данным табельного учёта прошлого года.
На ОАО «НПК «Уралвагонзавод»»
Таблица 10 - Расчет численности основных производственных рабочих
№ | Наименование операции | Профессия | Годовая производственная программа, шт. | Штучное время, мин. | Фонд времени работы рабочего, час. | Разряд работы | Кол-во оборудования | Расчет численности рабочих | Численность рабочих, чел. | Распределение по сменам | |||
Расч | Прин. | ||||||||||||
Nгод | Тшт. | Fдо | nпр | ![]() | Росн рас. | Росн.пр | 1 | 2 | 3 | ||||
1. | |||||||||||||
2. | |||||||||||||
3. | |||||||||||||
ИТОГО: | * | * | * | * | * | * | * |
* - суммировать значение в данной колонке
Экономическая часть
6.9.2.1 Расчёт стоимости основных материалов.
Дать понятие оборотным средствам. Классификация оборотных средств. Движение оборотных средств в производстве.
Расчёт стоимости основного материала на единицу изделия (указать марку материала)
Z – цена 1 кг основного материала
q – масса основного материала
Ктз – коэффициент транспортно-заготовительных расходов (1,01 – 1,16), принимаем Ктз -______
_______________ руб.
Расчёт стоимости основного материала на годовую программу
______________ руб.
Расчёт стоимости вспомогательного материала на единицу изделия (рассчитывается по каждому вспомогательному материалу отдельно) (указать марку материала)
Z – цена 1 кг вспомогательного материала
q – масса вспомогательного материала
Ктз – коэффициент транспортно-заготовительных расходов (1,01 – 1,16), принимаем Ктз -______
_______________ руб.
Расчёт стоимости вспомогательного материала на годовую программу
_______________руб.
Таблица 11 -Расчет потребности в материалах
Наименование материала | Годовая производственная программа, шт. | Цена за 1 кг материала, руб. | Расход материала, кг | Стоимость материала, руб. | ||
На деталь | На программу | На деталь | На программу | |||
Nгод | Z | q | q . N | z . q | z . q .N .Kтз | |
Основной материал | ||||||
ИТОГО: | ||||||
Вспомогательный материал | ||||||
ИТОГО: | ||||||
ВСЕГО: | * | * | * | * |
6.9.2.2. Расчёт технологической электроэнергии
Стоимость энергии затрачиваемой на изготовление одной конструкции рассчитывается по формуле:
Цэ – цена 1 кВт
Wэн – потребляемое количество электроэнергии
_______________ руб.
Расчёт стоимости энергии на годовую производственную программу
________________ руб.
6.9.2.3. Расчёт полного фонда заработной платы
Дать понятие заработной платы. Формы оплаты труда. Мотивация труда.
РАСЧЕТ сдельной заработной платы
- расценка сдельная
Т шт.- штучное время по операции
Сч – часовая тарифная ставка
Таблица 12 - Расчет сдельных расценок
№ | Наименование операции | Разряд работ | Часовая тарифная ставка | Штучно-калькуляционное время, мин | Расчет сдельной расценки | Сдельная расценка |
Сч | Тшт | ![]() | Рсд | |||
1 | ||||||
2 | ||||||
3 | ||||||
ИТОГО: | * | * |
РАСЧЕТ суммы премии
Дата добавления: 2018-04-15; просмотров: 8193; Мы поможем в написании вашей работы! |
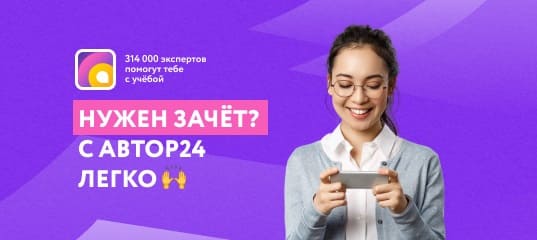
Мы поможем в написании ваших работ!