СТАНДАРТНЫЕ И СПРАВОЧНЫЕ ДАННЫЕ
ПРИМЕР ВЫПОЛНЕНИЯ РАБОТЫ Исходные данные: Рисунок 1 – Схема машинного агрегата Исходные данные для проектирования механической передачи: 1 Передаточное отношение и = 4; 2 Зубчатое зацепление – косозубое; 3 Расположение зубчатых колес в редукторе – вертикальное. Рисунок 2 – Кинематическая схема технологического механизма Примечание: частота вращения кривошипа n1 на рисунке 2 соответствует частоте вращения ведомого вала редуктора n2 на рисунке 1. Исходные данные для анализа технологического механизма приведены в таблице 1. Таблица 1 – Исходные данные для анализа технологического механизма м м м м м м x1 м y1 м y2 м q кг/м n1 0,23 0,69 0,31 0,5 0,77 0,925 0,695 0,46 0,08 21 245 1/45 Рисунок 3 – Диаграмма силы полезного сопротивления Выполненная работа должна иметь следующие разделы: 1 Структурный анализ технологического механизма. 2 Кинематический анализ механизма. 2.1 Построение плана положений. 2.2 Построение планов скоростей и ускорений для исследуемых положений механизма. 3 Динамический анализ механизма. 3.1 Расчет приложенных к звеньям механизма активных сил и инерционных нагрузок. 3.2 Определение величины уравновешивающей силы методом Н. Е. Жуковского. 3.3 Определение момента инерции махового колеса и потребной мощности двигателя. 4 Определение основных параметров зубчатой механической передачи и выбор электродвигателя. 5 Выбор материалов для изготовления деталей передачи и определение допускаемых напряжений. 6 Определение основных геометрических параметров зубчатой передачи. 6.1 Расчет величины межосевого расстояния. 6.2 Определение геометрических параметров зубчатых колес. 7. Проверочный расчет зубчатой передачи на прочность по контактным напряжениям. 8. Расчет и проектирование валов и корпуса редуктора. Выбор подшипников. 9. Выбор посадок и расчет допусков гладких цилиндрических соединений. Приложение А Графическая часть анализа технологического механизма на листе формата А1. Приложение В Эскизная компоновка редуктора на листе формата А2. 1 Структурный анализ технологического механизма Механизм состоит из пяти подвижных звеньев и одного неподвижного звена (стойки), соединенных между собой шестью вращательными (О1, О2, А, В, С, D) и одной поступательной (Е) кинематическими парами. Степень подвижности механизма определяется по формуле Чебышева W = 3n – 2 pн – pв , (1) Где n – число подвижных звеньев механизма, n = 5; pн – число низших кинематических пар, pн = 7 (О1, О2, А, В, С, D, Е); pв – число высших кинематических пар, pв = 0. . Механизм имеет одну степень подвижности, что соответствует одному ведущему звену. Ведущим звеном механизма является стержень О1А. Кроме того, механизм имеет в своем составе два шатуна – звенья 2 и 4, представляющие собой тонкие однородные стержни АВ и CD. Коромысло (звено 3) представляет собой треугольник O2BC, образованный посредством неподвижного соединения стержней O2B, O2C и BC. Звено 5 является ведомым звеном механизма и представляет собой ползун, или, в данном случае, резцовую призму. Образован механизм последовательным присоединением к группе Ассура I класса 1 вида (ведущему звену со стойкой) группы Ассура II класса 1 вида(звенья 2 и 3, кинематические пары А, В, О2), а затем группы Ассура II класса 2 вида (звенья 4 и 5, кинематические пары С, D, Е). Составляющие механизм группы Ассура представлены в графической части курсовой работы. Формула строения механизма: ГА I (1) + ГА II (1) + ГА II (2). Наивысший класс присоединенных групп – второй, поэтому механизм по классификации академика Артоболевского следует отнести к механизмам II класса. 2 Кинематический анализ механизма 2.1 Построение плана положений механизма и круговой циклограммы движения ползуна Построение начинаем с вычерчивания 12 положений ведущего звена. Принимаем масштаб плана положений . Масштаб принят таким, чтобы план положений занял все отведенное для него место на чертеже. В соответствии с выбранным масштабом определяем длины звеньев механизма на чертеже, а также координаты шарниров и положение направляющей. Дальнейший расчет сводим в таблицу. Таблица 2 – Расчет длин звеньев и координат неподвижных шарниров механизма на плане положений Звенья и стержни механизма x1 y1 y2 Действительная длина, м 0,23 0,69 0,31 0,5 0,77 0,925 0,695 0,46 0,08 Длина на плане, мм 57,5 172,5 77,5 125 192,5 231 174 115 20 Все построения на плане положений выполняем сплошными тонкими линиями. Одно произвольно выбранное положение выделяем сплошной толстой основной линией. Для составления круговой циклограммы движения ползуна предварительно вычерчиваем диаграмму силы полезного сопротивления движению ползуна . Примечание: Диаграмма силы полезного сопротивления вычерчивается обычно рядом с направляющей (над ней или под ней, если направляющая горизонтальна, справа или слева, если вертикальна). В том случае, когда непосредственно рядом с направляющей диаграмму разместить невозможно, диаграмма силы полезного сопротивления вместе с направляющей, на которой отмечены 12 положений ползуна, вычерчивается в любом удобном месте чертежа. Крайним левым положением ползуна на направляющей является положение D9, а положение D3 – крайним правым. Таким образом, полный ход ползуна . Учитывая, что сила полезного сопротивления в соответствии с заданием начинает действовать на ползун на расстоянии 0,05Н от его крайнего левого положения и заканчивает действие на расстоянии 0,05Н от крайнего правого положения, определяем величину рабочего хода ползуна: . Начало рабочего хода приходится на участок между положениями ползуна D9 и D10, поэтому дополнительно вычерчиваем механизм в положении , соответствующем началу рабочего хода. Конец рабочего хода приходится на положение ползуна D2. В качестве рабочего хода целесообразно принимать такую часть возвратно-поступательного движения ползуна, когда шатун CD будет работать на растяжение. Круговую циклограмму вычерчиваем в графической части курсовой работы, совмещая ее с планом положений ведущего звена. Выделяем следующие элементы движения: 1 Прямой ход – от положения кривошипа А9 до положения А3 ( рад); 2 Обратный ход – от положения кривошипа А3 до положения А9 ( рад); 3 Рабочий ход – от до А2 ( рад); 4 Передний перебег – от до ( рад); 5 Задний перебег – от А2 до А4 ( рад). 2.2 Построение планов скоростей и ускорений для исследуемых положений механизма При помощи круговой циклограммы определяем, что рабочему ходу ползуна соответствуют положения механизма № , 10, 11, 12 (0), 1, 2. Для этих шести положений механизма на отведенном месте чертежа необходимо построить планы скоростей. Угловая скорость ведущего звена рад/с. Скорость точки А кривошипа м/с. Длину отрезка Pa, соответствующего вектору на планах скоростей, принимаем равной 70 мм. Определяем масштаб планов скоростей . Для определения положения точки B на планах скоростей используем векторное уравнение , где . Кроме того, известно направление вектора скорости точки В: . Положение точки С на планах скоростей можно найти, применив теорему о подобии картины относительных скоростей перемещаемой фигуре (в нашем случае подобны на плане скоростей и на плане положений), или решив графически векторное уравнение ( ). При этом учитываем, что . Положение точки d на планах скоростей определяем путем графического решения векторного уравнения , где . При этом учитываем, что скорость ползуна всегда параллельна направляющей. Обозначения векторов скоростей точек и соответствующих им отрезков на плане скоростей представлены в таблице 3: Таблица 3 – Обозначения векторов скоростей точек и соответствующих им отрезков на плане скоростей скорость отрезок на плане Pa ba Pb Pc cb dc Pd План ускорений строим для одного из положений механизма, соответствующих рабочему ходу. Выбираем в качестве исследуемого положение механизма № 11. Определяем линейные скорости выделенных точек в 11-м положении механизма. ; ; ; ; ; . Определяем угловые скорости звеньев в 11-м положении механизма. рад/с; рад/с; рад/с; рад/с. В дальнейших расчетах используем среднее арифметическое от полученных значений: рад/с. рад/с. Определяем значения нормальных ускорений, необходимые для построения плана ускорений ; ; ; ; ; . Отрезок Pa на плане ускорений, соответствующий ускорению , принимаем равным 120 мм. Длина отрезка Pa принимается произвольно, исходя из того, какой величины план ускорений необходимо получить на чертеже. Определяем масштаб плана ускорений . Определяем длины отрезков нормальных ускорений на плане ускорений ; ; ; ; . Положение точки b на плане ускорений определяем, решив графически следующую систему векторных уравнений: ; . Положение точки с на плане ускорений определяем путем графического решения следующей системы векторных уравнений: , . Правильность построения плана ускорений необходимо проверить, дополнительно определив положение точки с методом, основанным на теореме о подобии картины относительных ускорений перемещаемой фигуре. В данном случае треугольник О2ВС на плане положений и треугольник Pbc на плане ускорений должны быть подобны. Составляем соответствующую пропорцию и определяем расстояния Pc и cb на плане ускорений. , мм, мм. Определяем численные значения ускорений центров масс звеньев, касательные ускорения, ускорение ползуна, а также угловые ускорения звеньев. Для расчетов линейных ускорений используем следующую формулу: , (2) где – отрезок на плане ускорений, соответствующий ускорению , мм. Для уменьшения объема пояснительной записки расчет линейных ускорений сводим в таблицу 4. Таблица 4 – Расчет величины линейных ускорений Ускорение Длина на плане, мм 42,5 58,5 34,8 53 87,5 68,5 175 15 9,5 6 92 48,5 модуль ускорения, м/с2 53,64 73,83 43,92 66,89 110,43 86,45 220,85 18,93 11,99 7,57 116,1 61,21 Угловые ускорения звеньев ; ; ; ; В дальнейших расчетах будем использовать среднее арифметическое от полученных значений рад/с2; . 3. Динамический анализ механизма 3.1 Расчет приложенных к звеньям механизма активных сил и инерционных нагрузок На свободном месте чертежа изображаем механизм в 11-м, исследуемом положении. Масштаб выбираем произвольно. В данном случае выбран масштаб . Для исследуемого положения механизма определяем действующие на звенья активные силы и инерционные нагрузки. Масса звена определяется по формуле , (3) где q – удельная масса звена, кг/м. В соответствии с заданием q = 21 кг/м. Силу тяжести, приложенную в центре масс звена, определяем по формуле , (4) где g – ускорение свободного падения, g = 9,81 м/с2. Главный вектор сил инерции звена, приложенный в его центре масс и направленный в сторону, противоположную направлению ускорения центра масс, определяется по формуле , (5) Момент инерции массы звена относительно центра масс , (6) Момент сил инерции звена , (7) Момент инерции массы звена 3 относительно его центра масс, находящегося в точке пересечения медиан, определяем при помощи теоремы Гюйгенса – Штейнера. , (8) где – момент инерции массы стержня, входящего в состав звена, относительно оси, проходящей через его центр масс, ; m – масса звена, кг; d – расстояние между центром масс входящего в состав звена стержня и центром масс всего звена, м. Расстояние между центром масс стержня и центром масс всего звена определяем при помощи построенной схемы механизма в исследуемом его положении. м, м, м. Для уменьшения объема пояснительной записки расчет приложенных к звеньям механизма активных сил и инерционных нагрузок сводим в таблицу 5. Таблица 5 – Расчет приложенных к звеньям механизма активных сил и инерционных нагрузок Звенья Звено 1 Звено 2 Звено 3 Звено 4 О1А АВ О2В О2С СВ CD , м 0,23 0,69 0,5 0,77 0,31 1,58 0,925 , м/с2 75,72 53,64 43,92 66,89 110,43 73,83 86,45 , рад/с2 0 320,1 24,3 24,3 24,3 24,3 125,5 , кг 4,83 14,49 10,5 16,17 6,51 33,18 19,425 , Н 47,4 142,1 103 158,6 63,9 325,5 190,6 , – 0,575 0,219 0,8 0,052 1,72 1,385 , Н – 777,24 – – – 2449,68 1679,3 , – 184,1 – – – 41,8 173,8 Моменты инерции массы стержней, входящих в состав звена, относительно осей, проходящих через их центры масс, были определены следующим образом: , , . 3.2 Определение величины уравновешивающей силы методом Н. Е. Жуковского На свободном месте чертежа вычерчиваем повернутый на план скоростей для 11-го положения механизма. В соответствующих точках повернутого плана скоростей прикладываем действующие на звенья механизма силы тяжести, уравновешивающую силу и силу полезного сопротивления. Для уменьшения объема построений и расчетов действующие на каждое звено механизма главный вектор и главный момент сил инерции заменяем одной силой. При этом используем лемму Пуансо о параллельном переносе силы. Выполним необходимые расчеты для звена 2. Плечо переноса силы м. Масштаб, согласующий действительный размер звена и размер звена на рычаге Жуковского м/мм. Плечо переноса силы на рычаге Жуковского мм. Главный вектор сил инерции переносим параллельно прямой, проходящей через центр масс звена 2 на расстояние мм таким образом, чтобы при его переносе направление момента перенесенной относительно центра масс звена силы совпадало с направлением момента сил инерции этого звена на рычаге Жуковского. Для правильного определения направления момента сил инерции звена на рычаге Жуковского, которое может не совпадать с направлением этого же момента на схеме механизма, необходимо заменить момент парой сил , . Эту пару сил необходимо показать на схеме механизма, а при определении направления момента на рычаге Жуковского достаточны мысленно приложить силы и к соответствующим точкам на повернутом плане скоростей. Таким образом, определяем, что на рычаге Жуковского должен быть направлен против хода стрелки часов. Вследствие этого главный вектор сил инерции перемещаем параллельно своему первоначальному направлению вверх относительно центра масс звена 2 на расстояние мм. Выполним необходимые расчеты и построения для звена 3. м. Масштаб приведения м/мм. Плечо переноса силы мм. При параллельном переносе главного вектора сил инерции звена 3 на расстояние мм его момент относительно центра масс звена должен быть направлен по ходу стрелки часов. Аналогичные расчеты и построения выполняем и для звена 4. м, м/мм, мм. Момент параллельно перенесенного на расстояние мм главного вектора сил инерции звена 4 должен быть направлен против хода стрелки часов (не смотря на то, что на схеме механизма направлен по ходу стрелки часов). При помощи диаграммы силы полезного сопротивления определяем величину силы полезного сопротивления в 11-м положении механизма. Н. В соответствии с методикой Н.Е. Жуковского составляем уравнение моментов всех сил, действующих на повернутый план скоростей, относительно полюса P. , . Итого Уравновешивающий момент Потребная мощность двигателя в исследуемом положении механизма 3.3 Определение момента инерции массы махового колеса и потребной мощности двигателя Приведенный момент силы полезного сопротивления в i-том положении механизма определяется по формуле , (9) где – сила полезного сопротивления в i-том положении механизма, , Н; – скорость ползуна в i-том положении механизма, м/с; – косинус угла между направлениями векторов силы полезного сопротивления и скорости ползуна. Так как данный угол для всех положений механизма равен , то . Знак « – » указывает на то, что данные векторы противоположны друг другу. Таким образом, формула для определения приведенного момента силы полезного сопротивления в i-том положении механизма принимает вид , (10) где – длина вектора скорости точки D на соответствующем плане скоростей, мм; – длина вектора скорости точки A. Для всех планов скоростей Pa = 70 мм. Для уменьшения объема пояснительной записки расчет приведенных моментов сил полезного сопротивления сводим в таблицу 6. Таблица 6 – Расчет приведенных моментов сил полезного сопротивления Положение механизма 10 11 12, 0 1 2 , мм 10 10 16 30 31 21 , Н 1400 1400 2240 4200 4340 2940 , мм 60 71 120 108 73 38 , 276 326,6 883,2 1490,4 1041 367 , мм 20,5 24 65 110 77 27 Для построения диаграммы приведенных моментов силы полезного сопротивления заранее был определен масштаб диаграммы . Приняв максимальную ординату мм, определили масштаб . По построенной ранее круговой циклограмме было определено, что сектор является одной восьмой частью сектора . Следовательно, ордината, соответствующая положению на оси абсцисс диаграммы приведенных моментов, должна быть проведена на расстоянии мм от положения 10. На ординатах, проведенных из положений , 10, 11, 12(0), 1, 2 откладываем рассчитанные ранее значения . Для удобства построений отрицательные значения откладываем вверх от оси абсцисс. Полученные точки соединяем плавной кривой. В результате получен график функции на протяжении рабочего хода ползуна. Масштаб диаграммы по оси абсцисс , (11) где – длина отрезка на оси абсцисс, соответствующего одному полному обороту кривошипа, =180 мм. рад/мм. Под диаграммой строим диаграмму работ . Для обеспечения оптимальной высоты диаграммы работ принимаем полюсное расстояние Н = 50 мм. Масштаб диаграммы по оси ординат , . Графическим интегрированием при полюсном расстоянии Н = 50 мм строим диаграмму работы сил полезного сопротивления . Приведенный момент движущих сил можно считать постоянным во всех положениях кривошипа, т. е. графиком на диаграмме приведенных моментов будет прямая линия, параллельная оси абсцисс. Ординату этой прямой линии получаем графическим дифференцированием графика функции при том же полюсном расстоянии Н = 50 мм. Учитывая, что при установившемся движении механизма за период одного оборота кривошипа работа движущих сил равна работе сил сопротивления, график получаем, соединяя прямой линией начало и конец графика . В результате выполненных построений получаем ординату графика приведенных моментов движущих сил мм. Момент движущих сил . Потребная мощность двигателя При помощи полученных графиков и на диаграмме работ определяем работу движущих сил за период одного оборота кривошипа Адв и работу движущих сил на протяжении рабочего хода . , . Определим величину момента движущих сил вторым способом. Расхождение результатов . Момент инерции маховика определим по следующей формуле: , (12) где – работа сил сопротивления за период одного оборота кривошипа, ; – коэффициент неравномерности хода, в соответствии с заданием ; – средняя угловая скорость вращения кривошипа, . . Потребная мощность двигателя Максимальная угловая скорость кривошипа рад/с, рад/с. 4 Определение основных параметров зубчатой механической передачи и выбор электродвигателя. Частота вращения ведущего вала редуктора: , Потребная мощность электродвигателя , (13) где – коэффициент полезного действия (КПД) передачи. Коэффициент полезного действия передачи определяется по формуле , (14) где – КПД зубчатой передачи. Принимаем ; – КПД одной пары подшипников. Принимаем . По формуле 14 определяем КПД передачи: . По формуле 13 определяем потребную мощность электродвигателя: кВт. По каталогу электродвигателей выбираем двигатель асинхронный трехфазный закрытого обдуваемого исполнения с короткозамкнутым ротором серии АО2-61-6. Синхронная частота вращения электродвигателя 1000 , мощность 10 кВт. Фактическая частота вращения ротора электродвигателя с учетом скольжения по данным каталога электродвигателей . Допускается отклонение действительной частоты вращения ротора от потребной не более 4 %. – условие выполняется. Угловые скорости валов: , . Крутящие моменты на валах редуктора: , . 5 Выбор материалов для изготовления деталей передачи и определение допускаемых напряжений При отсутствии особых требований к габаритам редуктора для изготовления деталей зубчатой передачи наиболее целесообразно выбирать материалы со средними механическими характеристиками. Твердость материала должна при этом удовлетворять условию , что позволяет производить чистовое нарезание зубьев после термообработки. Для лучшей приработки зубьев шестерни и колеса и равномерного их износа твердость материала шестерни должна быть на 10 – 20 единиц Бриннеля выше твердости материала колеса: . Для изготовления шестерни выбираем сталь Ст45Х улучшенную с твердостью 250 HB, пределом прочности МПа, пределом текучести МПа. Для изготовления колеса принимаем сталь Ст45Х улучшенную с твердостью 230 HB, пределом прочности МПа, пределом текучести МПа. При таком выборе материалов шестерни и колеса обеспечивается выполнение условия . Для изготовления валов принимаем сталь Ст 45 нормализованную, предел прочности МПа, предел текучести МПа. Для изготовления деталей корпуса редуктора выбираем серый чугун марки СЧ 15, обладающий хорошими литейными свойствами. Величина допускаемого контактного напряжения определяется по формуле , (15) где – предел контактной выносливости поверхности зубьев. Для зубчатых колес при МПа; – коэффициент безопасности; – коэффициент долговечности. При нормализации, улучшении и объемной закалке зубьев (однородная по всему объему зуба структура) рекомендуется принимать коэффициент безопасности =1,1. При поверхностной закалке, азотировании, цементации, нитроцементации (неоднородная по объему структура) =1,2. Коэффициент долговечности учитывает влияние срока службы и режима нагрузки передачи. Принимается в пределах = 1…2,4. Пределы контактной выносливости материалов шестерни и колеса: МПа, МПа. Зубья шестерни и колеса будут иметь однородную по всему объему структуру (термообработка – улучшение), поэтому принимаем коэффициент безопасности =1,1. Редуктор рассчитывается на 30000 часов работы при постоянной нагрузке, в этом случае коэффициент долговечности = 1. Допускаемые контактные напряжения материалов шестерни и колеса: МПа, МПа. В качестве расчетного принимается среднее значение допускаемого напряжения по условию: , (16) где – допускаемое контактное напряжение зубьев шестерни, МПа; – допускаемое контактное напряжение зубьев колеса, МПа. Расчетное допускаемое контактное напряжение: МПа. Принимаем МПа. 6 Определение основных геометрических параметров зубчатой передачи 6.1 Расчет величины межосевого расстояния В современной методике расчета из двух напряжений (контактное) и (изгиба) в качестве основного принято контактное напряжение, так как в пределах заданных габаритов колес контактные напряжения остаются постоянными, а напряжения изгиба можно уменьшать путем изменения модуля. Величину межосевого расстояния определим по формуле, следующей из условия прочности зубьев по контактным напряжениям: , (17) где: k – постоянный коэффициент (для прямозубых передач 0,85, для косозубых – 0,75), в нашем случае k = 0,75; u – передаточное отношение, u = 4; – приведенный модуль упругости материалов шестерни и колеса, МПа. Приведенный модуль упругости материалов шестерни и колеса определяется по формуле , где и – модули упругости материалов шестерни и колеса. Так как в качестве материала для изготовления и шестерни и колеса принята сталь с модулем упругости МПа, то МПа; – крутящий момент на выходном валу, . =335,15 ; – коэффициент концентрации нагрузки при расчетах по контактным напряжениям; – коэффициент зависимости ширины колеса от величины межосевого расстояния; – допускаемое контактное напряжение, МПа. Концентрация нагрузки происходит вследствие изгиба или перекоса валов, в результате чего зубья колес контактируют не по всей длине. Коэффициент концентрации нагрузки при расчетах по контактным напряжениям определяется по графику на рисунке 1 приложения С, составленному на основе практики эксплуатации зубчатых колес, при помощи – коэффициента зависимости ширины колеса от величины делительного диаметра шестерни ( ). При проектном расчете коэффициент зависимости ширины колеса от величины делительного диаметра шестерни определяется по формуле , (18) где – коэффициент зависимости ширины колеса от величины межосевого расстояния ( ). Стандартные значения коэффициента = 0,315, 0,4, 0,5 (чем более тяжело нагружена передача, тем большие значения коэффициента принимаются). Принимаем коэффициент зависимости ширины колеса от величины межосевого расстояния = 0,4. Тогда коэффициент зависимости ширины колеса от величины делительного диаметра шестерни = = 1. По графику на рисунке 1 приложения С определяем коэффициент концентрации нагрузки при расчетах по контактным напряжениям: = 1,043. Полученные значения подставляем в формулу (17) и определяем величину межосевого расстояния: В результате расчета получили значение aw = 134,2 мм. Так как редуктор предназначен для мелкосерийного производства, то принимать стандартное межосевое расстояние не обязательно. Расчетное значение межосевого расстояния разрешается округлять по ряду нормальных линейных размеров Ra40:12, 13, 14, 15, 16, 17, 18, 19, 20, 21, 22, 24, 25, 26, 28, 30, 32, 34, 36, 38, 40, 42, 45, 48, 50, 53, 56, 60, 63, 67, 71, 75, 80, 85, 90, 95, 100, 105, 110, 115, 125, 130, далее через 10 до 260 и через 20 до 420 мм. Принимаем ближайшее большее значение aw = 140 мм. 6.2 Определение геометрических параметров зубчатых колес Ширина колеса . Полученное значение ширины колеса округляется в большую сторону по ряду Ra40. Принимаем мм. В данном случае расчетное значение сразу соответствовало ряду Ra40. Ширина шестерни должна быть на 3…5 мм больше ширины колеса: мм. Нормальный модуль зацепления принимаем в пределах: мм. Стандартные значения модулей приведены в таблице 1 приложения C. Принимаем стандартный модуль зацепления mn = 2 мм. При определении оптимального угла наклона зуба учитываем, что коэффициент осевого перекрытия должен соответствовать следующему условию: > 1,1. Предварительно принимаем = 1,6. Угол наклона зуба должен быть в пределах . Угол наклона зуба определяется по формуле , (19) Тогда угол наклона зуба . Суммарное число зубьев шестерни и колеса: . Принимаем целое число . Число зубьев шестерни . Необходимо учитывать, что по условию неподрезания зубьев . Принимаем . Число зубьев колеса . Уточняем передаточное отношение: . Определяем процент расхождения: . Допускается расхождение не более 4 %. Фактическая частота вращения ведомого (выходного) вала редуктора об/мин. Отклонение действительной частоты вращения ведомого вала от заданной не должно превышать 4 %. Уточняем величину угла наклона зуба: , . Делительные диаметры шестерни и колеса: мм; мм. Проверка: мм. Диаметры окружностей выступов шестерни и колеса: мм; мм. Диаметры окружностей впадин шестерни и колеса: , (20) где с – радиальный зазор, , мм. мм, мм. Примечание: При прямозубом зубчатом зацеплении расчет по пп. 6.1 и 6.2 выглядел бы следующим образом: Величина межосевого расстояния определяется по формуле 17: В результате расчета получили значение aw = 152,2 мм. Принимаем ближайшее значение по ряду Ra40: aw = 150 мм. Ширина колеса . Ширина шестерни должна быть на 3…5 мм больше ширины колеса: мм. Нормальный модуль зацепления принимаем в пределах: мм. Принимаем стандартный модуль зацепления mn = 2 мм. При расчете прямозубых передач следует величину модуля подбирать таким образом, чтобы суммарное число зубьев получалось при расчете целым числом. В этом случае сохраняется принятое значение межосевого расстояния. Определяем суммарное число зубьев шестерни и колеса: . Число зубьев шестерни . Расчетное значение округляется до ближайшего целого. В нашем случае целое число получили при расчете. Число зубьев колеса . Уточняем передаточное отношение: . Расхождение с заданным значением составило 0 %. Допускается расхождение не более 4 %. Делительные диаметры шестерни и колеса: мм, мм. Проверка: мм. Диаметры окружностей выступов шестерни и колеса: мм; мм. Радиальный зазор , мм. Диаметры окружностей впадин шестерни и колеса мм, мм. 7 Проверочный расчет зубчатой передачи на прочность по контактным напряжениям Условие прочности зубчатой передачи по контактным напряжениям: , (21) где – коэффициент, учитывающий повышение прочности косозубых колес по контактным напряжениям (для прямозубых колес =1); – стандартный угол зацепления, ; – коэффициент расчетной нагрузки. Определяется по формуле = , где – определенный ранее коэффициент концентрации напряжений, а – коэффициент, учитывающий динамический характер приложения нагрузки. Определяется коэффициент динамической нагрузки по графику на рисунке 2 приложения С в зависимости от окружной скорости и назначенного квалитета точности изготовления передачи. Коэффициент , учитывающий повышение прочности косозубых передач по контактным напряжениям, определяется по формуле , (22) где – коэффициент, учитывающий неравномерность нагрузки одновременно зацепляющихся пар зубьев. – коэффициент торцового перекрытия. определяемый по следующей формуле: Коэффициент торцового перекрытия определяется по формуле: (23) Значение коэффициента зависит от величины окружной скорости и назначенной степени точности (квалитета) изготовления передачи. Окружная скорость определяется по формуле . Степень точности назначается при помощи таблицы 2, а коэффициент определяется по таблице 3 приложения C. Окружная скорость м/с. Назначаем по таблице 2 приложения C 9 степень точности изготовления передачи. При помощи таблицы 3 приложения C определяем коэффициент , зависящий от окружной скорости и назначенной степени точности (квалитета): =1,13. Коэффициент торцового перекрытия определяем по формуле 23: . Коэффициент, учитывающий повышение прочности косозубых передач по контактным напряжениям определяем по формуле 22: . При помощи графика на рисунке 2 приложения С определяем коэффициент динамической нагрузки. Для 9 степени точности и м/с = 1,042. Коэффициент расчетной нагрузки = . По формуле 21 определяем напряжение, возникающее в линии контакта зубьев, и сравниваем его с допускаемым: Па. – условие прочности по контактным напряжениям выполняется. Примечание: При прямозубом зубчатом зацеплении расчет по п. 7 выглядел бы следующим образом: Определяем окружную скорость: м/с. Назначаем по таблице 2 приложения C 8 степень точности изготовления передачи. Для прямозубого зацепления коэффициент учитывающий повышение прочности косозубых передач по контактным напряжениям . При помощи графика на рисунке 2 приложения С определяем коэффициент динамической нагрузки. Для 8 степени точности и м/с = 1,12. Коэффициент расчетной нагрузки = . Определяем напряжение, возникающее в линии контакта зубьев, и сравниваем его с допускаемым напряжением: Па . Определим процент перенапряжения: . Допускаемым является перенапряжение до 4 %. 8 Расчет и проектирование валов и корпуса редуктора. Выбор подшипников Проектным расчетом определяется минимальный диаметр вала (диаметр выходного конца вала, предназначенного для установки муфты) из расчета на кручение по пониженным допускаемым напряжениям. Диаметры цапф должны быть согласованы с диаметрами внутренних колец подшипников, а всех остальных участков – с рядом нормальных линейных размеров Ra40. Определяем минимальные диаметры ведущего и ведомого валов редуктора из расчета на кручение по пониженным допускаемым напряжениям: , м (24) где – допускаемое касательное напряжение, МПа. Для стальных валов принимается в пределах 13…15 МПа; – крутящий момент на i-том валу, . На ведущем , на ведомом . Диаметр выходного конца ведущего вала: Выходной конец вала предназначен для установки муфты, поэтому его диаметр согласовываем с диаметром посадочного отверстия втулки полумуфты при помощи таблицы 4 приложения С. Для соединения валов применяем муфту упругую втулочно-пальцевую МУВП, смягчающую удары при передаче вращающих моментов благодаря наличию на пальцах муфты упругих резиновых втулок. Принимаем Минимальная разница диаметров вала одной ступени должна быть не менее 2 мм, поэтому назначаем, используя каталог подшипников и ряд нормальных линейных размеров, следующие диаметры участков ведущего вала: 35 мм – для установки уплотнительной манжеты и посадки внутренних колец подшипников, = 38 мм – для посадки зубчатого колеса. При выполнении следующего условия вал и шестерню целесообразно изготавливать в виде одной детали: . В нашем случае , поэтому вал и шестерню будем изготавливать не в виде одной детали «вал-шестерня», а каждую деталь отдельно. Диаметр выходного конца ведомого вала: Принимаем , диаметр для установки уплотнительной манжеты и посадки внутренних колец подшипников – 55 мм, для посадки зубчатого колеса – = 60 мм. Высота буртика – 5 мм. Длины участков валов определяются при выполнении эскизной компоновки редуктора. Определяем основные геометрические размеры корпуса редуктора. Толщина стенки корпуса редуктора (должна быть не менее 8 мм) мм. Принимаем толщину стенки корпуса редуктора мм. Толщина верхнего и нижнего поясов (фланцев) редуктора мм. Толщина нижнего пояса корпуса редуктора мм. Принимаем p = 19 мм. Толщина ребер мм. Принимаем мм. Зазор между торцом шестерни и внутренней стенкой корпуса редуктора мм. Принимаем мм. Минимальный допускаемый зазор от окружности вершин зубьев колеса до внутренней стенки корпуса редуктора мм. Определяем диаметр ступицы зубчатого колеса мм. Принимаем мм. Толщина обода колеса мм (должна быть не менее 8 мм). Принимаем мм. Толщина диска зубчатого колеса мм. Принимаем мм. Диаметр отверстий в диске принимаем исходя из следующего ориентировочного расчета: мм. Принимаем по ряду нормальных линейных размеров мм. При величине межосевого расстояния aw до 100 мм в качестве фундаментного болта принимается болт размером М12 (4 штуки), при величине aw свыше 100 до 200 мм – М16 (4 штуки), свыше 200 до 250 мм – М20 (4 штуки), до 355 мм – М24 (6 штук). В нашем случае принимаем dф = М16. Тогда диаметр фланцевых болтов, соединяющих основание корпуса с верхней его частью мм. Принимаем dфл = М12. Диаметр винтов, крепящих смотровые крышки , тогда мм. Принимаем dсм = М6. Определяем размеры подшипниковых гнезд ведущего и ведомого валов редуктора. Диаметр отверстия подшипникового гнезда D1H7 соответствует наружному диаметру наружного кольца подшипника, т. е. D1H7 = 72 мм для ведущего вала и D1H7 = 100 мм для ведомого. Наружный диаметр подшипникового гнезда D2, соответствующий диаметру подшипниковой крышки, осевой диаметр D3, диаметр винтов dп, их количество n, а также толщина подшипниковой крышки h определяются в зависимости от величины D1H7 при помощи таблицы 5 приложения С. Размеры гнезда подшипника ведущего вала: D1H7 = 72 мм, D2 = 108 мм, D3 = 88 мм, dп = М8, n = 4 шт., h = 7 мм. Размеры гнезда подшипника ведомого вала: D1H7 = 100 мм, D2 = 145 мм, D3 = 120 мм, dп = М10, n = 6 шт., h = 10 мм. Ширина K1 нижнего пояса (лапы) определяется в зависимости от величины фундаментных болтов, а ширина K верхнего пояса (фланца, соединяющего основание корпуса с крышкой корпуса) определяется в зависимости от величины болтов, соединяющих основание корпуса с крышкой по таблице 6 приложения С. Аналогично определяется расстояние c1 от наружной стенки корпуса до оси фундаментного болта и расстояние c от наружной стенки корпуса до оси фланцевого болта. По величине фундаментного болта dф = М16 при помощи таблицы 6 приложения С определяем K1 = 39 мм, c1 = 21 мм. По величине фланцевого болта dфл = М12 определяем K = 33 мм, c = 18 мм. Размеры K и c на компоновочном эскизе не отражены, они должны были бы быть использованы при вычерчивании видов сбоку и сверху на сборочном чертеже редуктора. Примечание: Объем данной курсовой работы не позволяет произвести расчет и выбор подшипников по динамической грузоподъемности. Поэтому подшипники выбираются из следующих соображений: для прямозубого зацепления выбираются радиальные шариковые или роликовые цилиндрические подшипники легкой или средней серии. Для косозубого зацепления выбираются радиально-упорные шариковые или роликовые конические подшипники легкой или средней серии. Подбирается подшипник таким образом, чтобы диаметр внутреннего кольца подшипника соответствовал диаметру вала в месте его посадки. В пояснительной записке указываются условный номер подшипника, внутренний диаметр внутреннего и наружный диаметр наружного колец, паспортная динамическая и статическая грузоподъемности. Проектируемая механическая передача имеет косозубые зубчатые колеса. В косозубом зацеплении возникают значительные осевые силы, поэтому для установки валов на опоры качения должны быть использованы радиально-упорные подшипники. Для ведущего вала выбираем шарикоподшипники радиально-упорные легкой серии условный номер 36207 со следующими характеристиками: внутренний диаметр внутреннего кольца d = 35 мм, наружный диаметр наружного кольца D = 72 мм, ширина подшипника В = 17 мм, статическая грузоподъемность С = 23,5 кН, динамическая грузоподъемность С0 = 17,8 кН. Для ведомого вала выбираем шарикоподшипники радиально-упорные легкой серии условный номер 36211 со следующими характеристиками: внутренний диаметр внутреннего кольца d = 55 мм, наружный диаметр наружного кольца D = 100 мм, ширина подшипника В = 21 мм, статическая грузоподъемность С = 41,1 кН, динамическая грузоподъемность С0 = 34,2 кН. 9 Выбор посадок и расчет допусков гладких цилиндрических соединений Для наружных колец подшипников с гнездом корпуса выбираем посадку Н7, обеспечивающую небольшой гарантированный зазор. Для соединения внутренних колец подшипников с цапфами валов выбираем посадку k6, обеспечивающую минимальный гарантированный натяг. Для соединения зубчатых колес с подступичными частями валов выбираем посадку , обеспечивающую небольшой гарантированный натяг. Рассчитаем при помощи таблиц Единой системы допусков и посадок (ЕСДП) величину образующихся в соединении зубчатого колеса с ведомым валом натягов, а также минимальные и максимальные значения диаметров подступичной части вала и отверстия в ступице колеса. Рассчитываемая посадка: 60 По таблице ЕСДП «Значения допусков для размеров до 500 мм» определяем величину допусков. Для 60 мм (интервал размеров свыше 50 до 80 мм) получаем допуск на изготовление отверстия в ступице зубчатого колеса: TD = 30 мкм. Допуск на изготовление подступичной части вала: Td = 19 мкм. Основные отклонения (ближайшие к нулевой линии) определяем по таблицам ЕСДП «Значения основных отклонений отверстий для размеров до 500 мм» и «Значения основных отклонений валов для размеров до 500 мм». Для основного отклонения H и размера 60 мм получаем нижнее отклонение поля допуска отверстия EI = 0 мкм. Для основного отклонения p и размера 60 мм получаем нижнее отклонение поля допуска вала ei = + 32 мкм. Предельное верхнее отклонение отверстия: ES = EI + TD = 0 + 30 = 30 мкм. Предельное верхнее отклонение вала: es = ei + Td = 32 + 19 = 51 мкм. По результатам расчетов изображаем схему полей допусков. Рисунок 4 – Схема полей допусков По расположению полей допусков убеждаемся, что в соединении получена посадка с гарантированным натягом. Определяем величину максимального, минимального и среднего натягов. Nmax = es – EI = 51 – 0 = 51 мкм, Nmin = ei – ES = 32 – 30 = 2 мкм, мкм. Предельные допускаемые размеры отверстия и вала: Dmax = D + ES = 60 + 0,03 = 60,03 мм, Dmin = D + EI = 60 + 0= 60 мм, dmax = d + es = 60 + 0,051 = 60,051 мм, dmin = d + ei = 60 + 0,032= 60,032 мм, Размеры, указываемые на рабочих чертежах: для отверстия 60+ 0,03 мм, для вала мм. Приложение А Графическая часть анализа технологического механизма на листе формата А1. Приложение В Эскизная компоновка редуктора на листе формата А2. ПРИЛОЖЕНИЕ С (обязательное)
СТАНДАРТНЫЕ И СПРАВОЧНЫЕ ДАННЫЕ
Дата добавления: 2018-04-05; просмотров: 321; Мы поможем в написании вашей работы! |
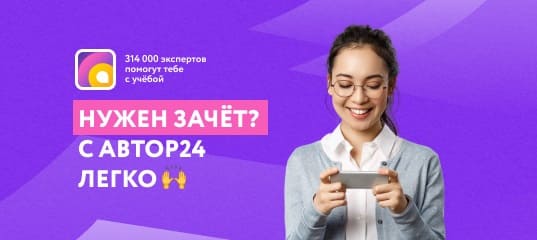
Мы поможем в написании ваших работ!