Рудин М.Г., Арсеньев Г.А., Васильев А.В. Общезаводское хозяйство нефтеперерабатывающего завода
СНАБЖЕНИЕ ИНЕРТНЫМ ГАЗОМ
Снабжение установок нефтеперерабатывающей промышленности инертными газами является неотъемлемой частью общезаводского хозяйства предприятия.
Все НПЗ оснащены системами снабжения инертным газом (азотом). Инертный газ первоначально применялся для регенерации катализаторов риформинга и гидроочистки; появление на НПЗ крупных производств, вырабатывающих инертный газ, связано с широким внедрением в нефтепереработку этих процессов. В дальнейшем инертный газ начал все шире использоваться в целях, не связанных с регенерацией катализатора. В настоящее время он применяется для создания «подушек» в резервуарах, в которых хранятся легкоокисляемые продукты, для продувки аппаратуры и оборудования перед ремонтом, при проведении пневматических испытаний на прочность и испытаний трубопроводов на плотность.
При регенерации алюмоплатинового катализатора установок каталитического риформинга инертный газ используется для следующих (проходящих последовательно) операций: продувка системы «на свечу», промывка системы при низкой (ниже 100 °С)температуре путем многократного заполнения ее инертным газом с последующим сбросом давления; промывка системы при температуре в реакторах 250 °С; собственно регенерация катализатора, во время которой инертный газ в смеси с воздухом проходит по схеме сырьевого цикла, а избыточные газы, образующиеся при горении кокса, сбрасываются «на свечу»; прокалка катализатора; промывка системы сухим инертным газом до снижения содержания кислорода не более 0,5% (об.). Если система в период регенерации сообщалась с атмосферой, проводится опрессовка аппаратуры инертным газом высокого давления.
|
|
При газовоздушной регенерации катализаторов гидроочистки инертный газ используется в операциях продувки, заполнения системы, выжига кокса и серы, прокалки катализатора, продувки системы.
При паровоздушной регенерации этих же катализаторов сначала вся система продувается инертным газом, а затем он заменяется водяным паром и в ходе операций выжига кокса и прокалки катализатора не потребляется. После прокалки водяной пар вновь заменяется инертным газом и система продувается до тех пор, пока из нее не будут полностью удалены водяные пары. Затем подготовленная к работе система испытывается на герметичность инертным газом высокого давления.
Потребление инертного газа так же, как и воздуха, носит ступенчатый характер. Например, при регенерации алюмоплатинового катализатора на укрупненных установках каталитического риформинга необходимо подать 15 000 м3инертного газа для продувки системы, 15 000 м3 для заполнения системы перед регенерацией, 15 000 м3 для промывки системы после регенерации. Если в процессе регенерации произошло разуплотнение системы риформинга, а также после замены катализатора, проводится испытание системы на герметичность. С этой целью подается 76 000 м3 инертного газа (4000 м3 × 19) высокого давления.
|
|
На современных установках каталитического риформинга жесткого режима и других установках, где осуществляется осушка газов цеолитами, инертный газ применяется для регенерации цеолитов.
На установках депарафинизации циркуляция инертного газа обеспечивает вакуум в системе фильтрования, уменьшает потери растворителя при испарении, предотвращает образование взрывчатой смеси, которая могла бы возникнуть в системе в присутствии кислорода воздуха. Под давлением инертного газа с поверхности барабана вращающегося вакуум-фильтра отделяется парафиновая лепешка. В составе установок депарафинизации имеются две системы инертного газа: дыхательная, которая находится под давлением 2 кПа, и вакуумная. В эти системы инертный газ подается из газгольдера, заполняемого из общезаводской сети.
На НПЗ инертный газ получают одним из двух способов:
|
|
- сжиганием топливного газа в токе атмосферного воздуха при минимальном избытке последнего с последующей очисткой образовавшегося дымового газа от окислов углерода и осушкой;
- разделением воздуха на азот и кислород при высоких давлениях и низких температурах.
Установки получения инертного газа методом сжигания построены почти на всех заводах, где имеются установки платформинга и гидроочистки. Первая типовая установка инертного газа была запроектирована в 1957 г. Расчетным сырьем для нее был принят топливный газ из общезаводской сети, имеющий теплоту сгорания 40 000 кДж/м3 (9500 ккал/м3). Для снижения калорийности газа к нему перед подачей в печь подмешивается холодный дымовой газ. Производительность установки составляла 2000 м3/ч.
Поскольку требования, которые предъявлялись в период проектирования этой установки к качеству газа, состояли в том, чтобы он был сухими не содержал более 0,5% (об.) кислорода, в схеме установки была предусмотрена очистка от кислорода на платиновом катализаторе и осушка на бокситах.
По проекту предполагалось, что в составе инертного газа будет содержаться 18% (об.) С02 и что окиси углерода в составе газа не будет. Как показал опыт пуска этих установок на ряде заводов, инертный газ содержал повышенное количество окиси углерода—в среднем 2,6% (об.), а в отдельных случаях — до 5% (об.). Поскольку в дальнейшем.было выдвинуто требование о снижении содержания окислов углерода (СО и С02) в инертном газе, разработанный в 1960 г. проект модернизированной установки производства инертного газа включал реакторы, в которых СО окисляется в С02 на катализаторе — гопкалите (смеси окислов марганца и меди). Для удаления двуокиси углерода предусматривались скрубберы щелочной промывки.
|
|
В связи с созданием и широким внедрением новых модификаций алюмоплатинового катализатора возникла необходимость дальнейшего снижения содержания окиси углерода, которая является сильнейшим ядом алюмоплатиновых катализаторов (адсорбция СО на поверхности катализаторов приводит к их необратимой дезактивации), до 0,1% (об.). Это было учтено при разработке в 1966—1968 гг. проектов новых установок инертного газа производительностью 300—360 и 1500 м3/ч.
При проектировании был детально изучен вопрос о выборе сырья. Поскольку, как показал опыт эксплуатации установок инертного газа, топливные газы нефтеперерабатывающих заводов отличаются непостоянством состава, сильными колебаниями теплоты сгорания, повышенным содержанием тяжелых бензиновых компонентов, в проектах этих установок в качестве сырья был применен сжиженный газ. В зависимости от конкретных условий работы предприятия могут использоваться либо индивидуальные пропан и бутан, либо их смесь. Расход сжиженного газа на производство инертного газа составляет 156 кг/ч (1250 т/год). Это не превышает 1% от общей выработки сжиженных газов на НПЗ.
Технологическая схема установки инертного газа мощностью 1500 м3/ч приведена на рисунке 1. [1]
Рисунок 1 - Технологическая схема установки инертного газа
1— испаритель; 2—топка; 3—скруббер; 4, 7, 9—адсорберы; 5—компрессор низкого давления;' 6—печь; 8 — холодильник; 10—компрессор высокого давления; 11 — сепаратор;
I — сжиженный газ; II — неочищенный и неосушенный инертный газ без давления; III—очищенный от СО, неосушенный инертный газ;
IV—очищенный от С02 осушенный инертный газ (0,8 МПа); V—очищенный от CO2 и СО осушенный инертный газ (0,8 МПа); VI—инертный газ (6,4 МПа); VII—углекислый газ;
VIII —Моноэтаноламин; IX—‘Вода; X — пар.
Сырье через промежуточную емкость поступает в испаритель, откуда пары углеводородов подаются в топку инертного газа 2, работающую под небольшим избыточным давлением. Из топки дымовой газ (после охлаждения в непосредственно соединенном с топкой скруббере 3, орошаемой водой) направляется в адсорбер 4 на очистку от С02 раствором моноэтаноламина. Очищенный от С02 газ сжимается до 0,8 МПа компрессором 5, охлаждается и подвергается осушке в адсорберах 7. В качестве адсорбента используется синтетический цеолит NaA. Адсорберы работают по сменно-циклическому графику с продолжительностью цикла, равной 24 ч. Цикл состоит из трех фаз — осушки газа, регенерации адсорбента и охлаждения адсорбера, каждая из которых продолжается 8 ч.
Инертный газ, поступивший да осушку, подогревается в печи 6 до 400—440 °С и подается в тот из адсорберов, в котором в данный момент проводится регенерация цеолита — удаление поглощенной при осушке влаги. Затем газ охлаждается в холодильнике 8 до 35 °С, отделяется от влаги и поступает в тот адсорбер, который в этот момент работает как осушитель. Осушенный газ используется затем для охлаждения третьего адсорбера.
После осушки газ подвергается очистке от СО в адсорбере 9,заполненном гопкалитом.
По проекту очищенный .и осушенный газ имеет следующий состав (в % (об.)): N2— 98,6; С02 — до 1,0; СО—до 0,1; 02 — до 0,3. Влажность газа равна 0,04 г/м3, что соответствует точке росы минус 35 °С.
В установках мощностью 300—360 м3/ч сохранен основной принцип получения инертного газа — сжигание испаренного сжиженного газа. Однако сжигание проводится не в печи со скруббером, а на специальной установке ЭК- 125М03, разработанной Всесоюзным научно-исследовательским институтом электротермического оборудования (ВНИИЭТО). Агрегат ЭК-125М03 состоит из камеры сжигания с охлаждаемым водой газоотводом, водяного холодильника, влагоотделителя, гидрозатвора и воздуходувки.
Дымовой газ с температурой 40 °С подается из агрегата на очистку от СО, С02 и осушку. Для подогрева газа, поступающего на регенерацию осушителя, вместо печи используется электроподогреватель.
Недостатком описанных установок является присутствие в инертном газе заметных количеств окиси углерода, поскольку примененный катализатор не позволяет полностью удалить СО. За рубежом на установках получения инертного газа для удаления СО используетсяалюмопалладиевый катализатор, с помощью которого можно добиться снижения содержания окиси углерода в газе до 20%. Для удаления влаги из газа часто используется метод вымораживания.
261 |
Азот высокой чистоты (99,9% и выше) может быть получен на установках разделения воздуха, которые широко применяются в различных отраслях народного хозяйства, испытывающих потребность в чистом кислороде и азоте.
Установки разделения воздуха отличаются по типу технологической схемы: способу получения холода (холодильному циклу), способу очистки воздуха от двуокиси углерода и влаги и т. д. Эксплуатируется большое количество стационарных и передвижных воздухоразделительных установок производительностью от 15 до 35 000 м3/ч по кислороду и от 20 до 48 000 м3/ч по азоту. В зависимости от вида получаемой продукции установки разделения воздуха подразделяются на азотные, азотно-кислородные и кислородные. Установки первого типа в качестве товарной продукции выпускают только азот, второго — азот и кислород, третьего — только кислород.
На НПЗ строятся азотные и азотно-кислородные установки. Кислород, вырабатываемый одновременно с азотом может быть использован в некоторых процессах окисления, для очистки сточных вод, для сварки в ремонтно-механическом цехе завода. На некоторых НПЗ рядом с азотно-кислородными установками сооружаются цехи наполнения баллонов, и кислород в баллонах реализуется как товарная продукция.
На ряде НПЗ в последние годы построены азотно-кислородные установки типа 2АК-0,6. Такая воздухоразделительная установка вырабатывает 1200 м3/ч азота чистотой 99,999% и 170 м3/ч кислорода чистотой 99,7%. Поскольку установка состоит из двух блоков, периодически останавливающихся на ремонт, указанная производительность обеспечивается только в течение 7700 ч в год. В остальное время, когда работает только один блок, она снижается в два раза.
При эксплуатации установок разделения воздуха особое внимание следует уделять технике безопасности, предотвращению взрывов на этих установках. Основной причиной взрывов азотно-кислородных станций может быть накопление взрывоопасных примесей, присутствующих в малых количествах в перерабатываемом воздухе. Наиболее опасные из примесей — ацетилен, кислородсодержащие органические соединения, углеводороды, сероуглерод, а также масло, попадающее в воздухоразделительный блок вместе с воздухом.
Основные способы защиты аппаратов воздухоразделительных установок:
применение для переработки воздуха, не загрязненного вредными примесями или загрязненного ими в малой степени:
- очистка перерабатываемого воздуха от взрывоопасных примесей;
- организация технологического процесса разделения воздуха таким образом, чтобы снизить содержание взрывоопасных примесей в жидком обогащенном воздухе и жидком кислороде.
На территории НПЗ содержание вредных примесей в воздухе, как правило, превышает допустимое. Поэтому организовать забор воздуха в непосредственной близости от азотно-кислородной станции не представляется возможным и сооружаются дальние воздухозаборы, имеющие одну, две или несколько ветвей. При двух и более ветвях воздухозаборы переключаются в зависимости от направления ветра так, чтобы забор воздуха осуществлялся из наименее загрязненной зоны. Для переключения используются поворотные шиберы или электрозадвижки. Воздухозаборные шахты или трубы на всасывающих концах воздухозабора имеют высоту до 30 м. Сопротивление головного сооружения и воздухопровода не должно превышать 3 кПа (300 мм вод.ст.), поэтому приходится сооружать воздухопроводы большого диаметра, уделять особое внимание защите от подсосов воздуха, нагрева солнечными лучами и т. д.
Помимо сооружения дальних воздухозаборов предложен ряд других способов защиты воздухоразделительных агрегатов от накопления в них вредных примесей:
- адсорбция ацетилена силикагелем из кубовой жидкости (обогащенного жидкого воздуха);
- ацетилена силикагелем ив воздуха в газовой фазе при низких температурах;
очистка воздуха цеолитами.
- каталитическая очистка воздуха от ацетилена и других углеводородов путем окисления примесей на серебряно-марганцевом катализаторе.
Адсорбционными блоками очистки жидкого воздуха оборудованы установки типа КтА-12-2, Кт-5-2, АКт-16-1, АКт-17-1, Бр-14 и т. д. На установках КтА-33, КАр-30 имеются адсорберы на газовом потоке.
Применение цеолитов (молекулярных сит) позволяет осуществить комплексную очистку воздуха от примесей — двуокиси углерода,, паров воды, ацетилена и других углеводородов. Разработаны типовые проекты блоков очистки и осушки воздуха цеолитами. Такими блоками дооборудуются действующие воздухоразделительные установки. Вновь разрабатываемые блоки разделения воздуха также имеют в своем составе узлы очистки воздуха с применением цеолитов.
Каталитическая очистка воздуха на серебряно-марганцевом или палладиево-марганцевом катализаторах позволяет наиболее эффективно очистить воздух от микропримесей. Метод прошел опытную и промышленную проверку на Руставском металлургическом комбинате и Салаватском нефтехимическом комбинате. Взрывобезопасность воздухоразделительных агрегатов с, каталитической очисткой обеспечивается даже при содержании в воздухе ацетилена до 10 мг/м3.
Схема блока каталитической очистки воздуха для установки 2АК-0.6 приведена на рисунке 2.
Рисунок 2 - Схема блока каталитической очистки воздуха
Т-1, Г-2 —теплообменники;
Э-1 — электроподогреватель;
Х-1, Х-2—холодильники; Р-1—контактный аппарат;
I — воздух после первой ступени компрессора воздухоразделительной установки; II —воздух на вторую ступень; III — воздух после четвертой ступени компрессора; IV— воздух в агрегат разделения воздуха; К —охлаждающая вода.
Воздух на очистку поступает после четвертой ступени компрессора под давлением 5,0—5,4 МПа с температурой 35 °С. Затем он нагревается в теплообменнике Т-1 до 240—250 °С и подается в контактный аппарат Р-1, где происходит окисление (сгорание) углеводородных примесей на катализаторе. Очищенный воздухиз Р-1 проходит через трубное пространство теплообменника Т-2, где охлаждается до 90 °С, и водяной холодильник Х-1, где температура его снижается до 35 °С, после чего поступает для очистки на существующий цеолитовый блок азотно-кислородной станции.
В качестве теплоносителя в теплообменниках применяется воздух после первой ступени компрессора, последовательно нагревающийся в теплообменнике Т-2 и электроподогревателеЭ-1до 300 °С. Затем он отдает теплоту воздуху, поступающему на очистку, в теплообменнике Т-1. В холодильнике Х-1 воздух-теплоноситель охлаждается до 35 °С, после чего поступает на вторую ступень компрессии.
Потребление инертного газа на НПЗ имеет неравномерный характер. Так для создания азотной «подушки» инертный газ расходуется равномерно, а в момент регенерации катализатора, проведения продувок, опрессовок, испытаний трубопроводов на прочность расход азота резко возрастает. Известно, что при проведении газовоздушной регенерации алюмокобальтмолибденового катализатора на установку гидроочистки типа Л-24-6 в сравнительно короткий срок должно быть подано 66 тыс. м3 инертного газа. В период регенерации алюмоплатинового катализатора и цеолитов в секции каталитического риформинга установки ЛКза 150 ч расходуется 165 тыс. м3 азота. Необходимый для быстрого проведения регенерации катализатора часовой расход азота составляет 1500 м3 и более.
Для покрытия пиковой потребности в азоте на НПЗ сооружаются газгольдерные парки, состоящие из мокрых или сухих газгольдеров. Объем парка определяется исходя из необходимости обеспечить потребность в инертном газе в период регенерации катализатора (с учетом выработки инертного газа в этот период на существующих производствах).
Для НПЗ мощностью 12—18 млн. т/год необходимы газгольдерные парки инертного газа на объем 40—50 тыс. м3.
Газгольдер состоит из стального резервуара и подвижных звеньев. У резервуаров объемом 100—6000 м3 подвижным звеном является колокол, у резервуаров объемом 10 000, 15 000, 20 000 и 30 000 м3 — колокол и телескоп.
Корпус колокола, резервуар и днища газгольдера транспортируются к месту монтажа свернутыми в рулоны.
По технологической схеме газгольдер может быть подключен на «тупик» или «проход» газа, со сбросом избыточного газа в атмосферу и без сброса газа. Подача газа, воды и пара осуществляется через газовый ввод, состоящий из утепленной будки — камеры, внутреннего заглубленного приямка и тоннеля под газгольдером. Газгольдер в районах с расчетной зимней температурой выше минус 20 °С сооружается без утепляющей стенки, а в более холодных районах — с утепляющей стенкой.
Общий вид газгольдера приведен на рисунке 3.
Рисунок 3 - Мокрый газгольдер
1 — гидравлический затвор;
2 — клапанная коробка;
3 — подъемно-клапанное устройство;
4 — газосбросная труба; 5 —колокол;
6—телескоп; 7 —резервуар;
8 — утепляющая стенка.
На многих НПЗ были смонтированы мокрые газгольдеры объемом 10 000 м3. Недостатком мокрых газгольдеров является то, что они занимают много места, хранимый газ выходит из них увлажненным.
Гораздо более эффективны сухие газгольдеры, которые представляют собой вертикальные емкости высокого давления.
Резервуарный парк объемом 45 тыс. м3г состоящий из трех мокрых газгольдеров инертного газа объемом 15 тыс. м3 каждый, занимает площадь 9600 м2, а парк аналогичного объема из пяти сухих газгольдеров объемом 160 м3 — 500 м2, т. е. в 19 раз меньше.
Инертный газ подается потребителям под давлением 0,8 МПа. Это давление обеспечивается компрессорами, установленными на большинстве установок производства инертного газа и воздухоразделительных установках. На азотно-кислородной станции 2АК-0.6 имеется компрессор, сжимающий азот до более высокого давления, но производительность его невелика — всего 20 м3/ч.
В ряде случаев потребителям необходим азот более высокого, чем 0,8 МПа, давления. Так, если продувка системы установок гидроочистки до и после регенерации осуществляется инертным газом низкого давления, то для проведения собственно газо-воздушной регенерации требуется газ давлением 2,2 МПа. Газ высокого давления требуется и для опрессовки систем риформинга и гидроочистки после окончания регенерации. В этом случае давление инертного газа должно быть равно 4,4—4,9 МПа.
Инертный газ более высокого, чем 0,8 МПа, давления необходим также при испытаниях трубопроводов на прочность и плотность.
На тех заводах, где имеются установки каталитического риформингаJ1-35-11/300 и гидроочистки дизельного топлива J1-24-6, инертный газ сжимается до давления 7,0 МПа размещенными на этих установках компрессорами типа 5ВП-16/70. Компрессоры предназначались для того, чтобы последовательно сжимать воздух и инертный газ в период регенерации. От этих установок проложены коллекторы к установкам, не имеющим в своем составе компрессоров высокого давления, но нуждающимся в инертном газе высокого давления. По коллекторам воздух и инертный газ передаются попеременно. Такое решение нельзя признать правильным, поскольку объединять коллекторы, транспортирующие воздух и инертный газ (особенно, содержащий заметные количества окиси углерода) нежелательно. Известен случай, когда по линии попеременной подачи инертного газа и воздуха в операторную технологической установки попал инертный газ, в результате чего произошел несчастный случай.
Более целесообразно иметь в общезаводском хозяйстве компрессоры инертного газа высокого давления. Эти компрессоры могут использоваться также для заполнения сухих газгольдеров инертного газа.
Схема компрессорной инертного газа высокого давления приведена на рисунке 4.
Рисунок - 4 Схема компрессорной инертного газа высокого давления
А-1—установка инертного газа или воздухоразделительный агрегат;
Г-1, Г-2—гидрозатворы;
Е-1, Е-2 —сепараторы;
ПК-1. ПК-2—компрессоры;
Х-1, Х-2 — холодильники;
МО-1, МО-2 — маслоотделители;
Б-1—ресивер; Б-2, Б-3 — газгольдеры;
I — азот (0,8МПа); II—азот (6,4 МПа);
III—вода холодная; IV — вода теплая;
V—сброс масла.
Азот поступает на всасывающую линию компрессора с азотно-кислородной станции (установки инертного газа) или из газгольдерного парка. Сжатый азот подается потребителям, а в межрегенерационный период направляется на заполнение газгольдеров. Для сжатия азота наиболее пригоден компрессор типа 305ГП-16/70 производительностью 960 м3/ч, обеспечивающий сжатие газа до 7,0 МПа. ■
Чтобы сократить территорию и уменьшить штат обслуживающего персонала целесообразно создать единый блок, состоящий из объединенной компрессорной воздуха и инертного газа, азотно-кислородной станции и газгольдерного парка.
СНАБЖЕНИЕ ВОДОРОДОМ
В связи с внедрением в нефтепереработку гидрогенизационных процессов на НПЗ создана система снабжения водородом, организован сбор и распределение газов, содержащих в том или ином количестве водород, между потребителями.
Расход водорода (в пересчете на 100%) при различных гидрогенизационных процессах составляет (в % от массы сырья): гидроочистка прямогонных бензинов (сырья риформинга)—0,1; глубокая гидроочистка вторичных бензинов—1,2; гидроочистка керосиновых фракций — 0,3; гидроочистка прямогонных дизельных фракций — 0,4—0,5; одноступенчатый гидрокрекинг вакуум- дистиллята— 0,8; двухступенчатый гидрокрекинг вакуум-дистиллята — 2,4—4,0; гидроочистка масел — 0,3; гидродеалкилирование толуола — 2,5.
Основным источником водорода на современном НПЗ являются установки каталитического риформинга — платформинга. Выход водорода зависит от углеводородного состава, пределов кипения риформируемогосырья, давления процесса, типа применяемого катализатора и увеличивается при риформировании сырья, содержащего больше нафтеновых углеводородов, понижении давления процесса, повышении температуры начала кипения бензиновой фракции. На отечественных установках каталитического риформинга выход водорода составляет около 1,0% в расчете на перерабатываемое сырье.
Концентрация водорода в водородсодержащем газе главным образом зависит от типа применяемого катализатора и режима процесса. На установках, работающих в так называемом «мягком» режиме с использованием катализатора АП-56, содержание водорода в водородсодержащем газе, выдаваемом в общезаводскую сеть составляет 85—90% (об.). На установках «жесткого» режима, где применяется катализатор типа АП-64, в водородсодержащем газе содержится 70—75% (об.) водорода. При использовании полиметаллических катализаторов серии Кр концентрация водорода составляет 80—85% (об.) По мере отработки катализатора (снижения его активности) происходит падение концентрации водорода в водородсодержащем газе.
На НПЗ с неглубокой переработкой нефти количество водорода, получаемого при каталитическомриформинге, достаточно для обеспечения потребности установок гидроочистки прямогонных фракций — бензиновой и средних дистиллятов; имеется даже избыток водородсодержащего газа, который составляет 10— 15% от суммарной выработки. Избыточный водородсодержащий газ сбрасывается в топливную сеть.
Водородное хозяйство на НПЗ с неглубокой переработкой нефти создается для обеспечения начального и последующих пусков установок каталитического риформинга.
Как известно, в состав установок каталитического риформинга входит блок предварительной гидроочистки сырья. В реакторы блока риформинга должно подаваться сырье, очищенное от сернистых и азотистых соединений. Для предотвращения отравления катализатора блока риформинга при пуске установки сначала выводится на режим блок гидроочистки с использованием водородсодержащего газа, поступающего со стороны, а затем гидроочищенное сырье подается на блок риформинга.
Возможен и другой вариант — начальный пуск блока риформинга на негидроочищенном сырье при пониженной температуре реакции с последующим выводом на режим блока гидроочистки с применением собственного водородсодержащего газа. Однако практика 'последних лет показала серьезные недостатки этого варианта. В результате частых пусков установок риформинга в период их освоения на негидроочищенном сырье катализатор, содержащий драгоценные металлы, быстро выходит из строя.
Если на заводе имеется несколько установок риформинга, то пуск одной из них после ремонта или проведения регенерации катализатора осуществляется на водороде, подаваемом с другой (работающей) установки. Если установка риформинга на заводе только одна (что, в частности, характерно для вновь строящихся заводов, где пущены только объекты первой очереди строительства), то для хранения водорода необходимо иметь газгольдеры. В газгольдеры направляют часть водорода, вырабатываемого на установке риформинга в межрегенерационный период, и за счет этого создается необходимый запас.
Водород хранится в мокрых и сухих газгольдерах. При использовании мокрых газгольдеров существует опасность попадания водорода в канализацию — вместе с водой, сбрасываемой из газгольдеров.
Сухие газгольдеры используются для хранения запаса водорода на вновь строящихся предприятиях. Существуют проекты сухих газгольдеров водорода объемом 100 и 160 м3 на давление 6 МПа.
Объем газгольдерного парка водорода определяется исходя из необходимости обеспечить пуск одной установки риформинга. Применительно к укрупненным установкам типа Л-35-11/1 ООО и ЛК-6у этот объем равен 25—30 тыс. м3.
Особую проблему представляет обеспечение водородом установок или блоков риформинга в период пуска первой очереди завода. На многих заводах для решения этой задачи одновременно со строительством первых установок риформинга были построены электролизные установки производительностью 12—24 м3/ч водорода по типовому проекту ГИАПа.
Водород на этих установках производится электролизом 30%- го раствора КОН в электролизере, состоящем из 50—100 ячеек. Электролизные установки имеют малую мощность; чтобы обеспечить пуск укрупненной установки риформинга их пришлось бы эксплуатировать для наработки водорода не менее 1000 ч.
Существуют проекты более крупных электролизных установок. Водородно-кислородная станция (типовой проект 405-4-41) имеет производительность 120—160 м3/ч по водороду и 60—80 м3/ч по кислороду. Для получения водорода применяется электролизер СЭУ-40 (в качестве электролита используется 30%-ный раствор КОН или 25%-ный раствор NaOH). Для подпитки системы применяется деионизированная вода. Для деионизации обычную воду пропускают через электродистиллятор марки ЭД-90М и финишную ионообменную установку УФ-250. Станция выдает потребителям газы под давлением 0,3—1,0 МПа. Схемой станции предусмотрена очистка и осушка газа. Чистота водорода и кислорода— 99,9999%. Газы осушаются до точки росы минус 50°С.
Возможен другой вариант снабжения завода водородом на пусковой период — накопление в газгольдерах водорода из баллонов, разряжаемых на специальной рампе. Такой способ, однако, широко не применяется ввиду его трудоемкости. Для обеспечения начального пуска потребовалось бы доставить и разрядить несколько тысяч баллонов.
При опорожнении сухих газгольдеров или подаче водорода из мокрых газгольдеров необходимо обеспечить повышение давления водорода до величины, с которой он должен поступать на установки риформинга (порядка 4,0 МПа). Поэтому в состав водородного хозяйства включается специальная компрессорная. Для сжатия водорода целесообразно применять компрессоры производительностью 300 м3/ч и давлением в нагнетательной линии до 7,0 МПа.
При углублении переработки нефти и внедрении ряда новых гидрогенизационных процессов (гидроизомеризация, изориформинг, термическоегидродеалкилирование) компенсировать потребность в водороде только за счет водородсодержащего газа риформинга не удается.
Потребность в дополнительных источниках водорода компенсируется за счет строительства специальных установок. Промышленно освоены два метода производства водорода из нефтезаводских газов:
1) каталитическая конверсия в присутствии водяного пара в трубчатых печах; 2) каталитическая высокотемпературная конверсия в присутствии кислорода в шахтных печах.[2]
В условиях НПЗ процесс паровой конверсии экономически' более эффективен, поскольку нет необходимости в дополнительных затратах на получение кислорода разделением воздуха.
За рубежом разработан и промышленно освоен метод получения водорода парокислородной газификацией нефтяных остатков.
Несомненный интерес представляет возможность использования водорода, содержащегося в сухих газах установок риформинга и гидроочистки, направляемых в настоящее время в топливную сеть. Выделить водород из этих газов можно с помощью метода низкотемпературного концентрирования. В сухих газах каталитического риформинга, выход которых колеблется от 2 до 9% (масс.) в расчете на сырье, содержится в зависимости от схемы и режима риформирования — 2—10% (масс.) водорода. В сухих газах гидроочистки его еще больше (до 14%), однако выход этих газов невелик — не более 0,3—0,4% (масс.) в расчете на сырье.
На НПЗ мощностью 15—18 млн. т/год, где все бензиновые фракции подвергаются риформированию, а средние дистилляты (керосиновый и дизельный) — гидроочистке, можно получить из отходящих газов риформинга и гидроочистки до 5 тыс. т/год и более водорода.
В состав установки концентрирования входят блоки предварительного охлаждения, очистки от сероводорода, осушки газа на цеолитах, аммиачного охлаждения, низкотемпературного разделения. Как показали расчеты, применительно к установке мощностью 5 тыс. т/год себестоимость производства водорода низкотемпературным концентрированием в 8 раз дешевле, чем конверсией.
Водородсодержащий газ с установок каталитического риформинга поступает в общезаводской коллектор, из которого подается потребителям. Давление в сети водородсодержащего газа поддерживается равным 2—2,2 МПа.
Для водорода высокой концентрации, получаемого на специальных установках, предусматриваются самостоятельные трубопроводы.
СНАБЖЕНИЕ ВОЗДУХОМ
Для различных нужд, нефтеперерабатывающего завода (НПЗ) в значительных количествах расходуется сжатый воздух. Воздух используется для пневматических систем автоматического регулирования и контроля, применяется для разнообразных технологических целей и т. д.
Потребление сжатого воздуха приборами автоматического регулирования составляет в среднем 0,5—1,0 м3/ч на каждый прибор. В зависимости от сложности технологической схемы установки по переработке нефти и, следовательно, от количества приборов на этой установке расход воздуха на ней колеблется в пределах от 1 до 8 м3/мин. На комбинированных установках, в которых совмещается пять-семь различных процессов, расход воздуха в 1,5- 2 раза выше.
Расход воздуха на нужды КИП в целом по заводу зависит от количества технологических установок и глубины переработки нефти. Он составляет 0,4—1,0 м3/т перерабатываемой нефти. Воздух, подаваемый к приборам автоматического контроля, должен быть очищен и осушен.
Сжатый воздух применяется также при очистке змеевиков трубчатых печей от кокса, при регенерации катализаторов, на окислительных установках, в ремонтных целях (для пневматического инструмента).
Для очистки труб печей от коксовых отложений используются два способа — пневматический и паровоздушный. При пневматической очистке в очищаемую трубу вставляется воздушная турбинка, которая шарниром соединена с чугунным бойком. В турбинку подают сжатый воздух. Средний расход воздуха на одну турбинку составляет 4,2 м3/мин. Число турбинокN,работающих одновременно можно рассчитать по формуле:
N = (m×l×a)/T
где т — продолжительность чистки 1 м трубы;l— длина трубы, м; а — число труб в печи, шт.; Т — продолжительность чистки всего змеевика.
Расход воздуха на установках каталитического крекинга составляет 10—15 м3/кг кокса. Поскольку при каталитическом крекировании образуется 3—5% (масс.) кокса в расчете на сырье, расход воздуха равен 300—500 м3/т перерабатываемого сырья. На установках каталитического риформинга и гидроочистки обрабатываемое сырье пропускается через неподвижный слой алюмоплатинового или алюмо-кобальтмолибденового (алюмоникельмолибденового) катализатора. В процессе эксплуатации активность катализатора постепенно уменьшается. Снижение активности катализатора компенсируется изменением технологического режима — повышением температуры процесса, подачей промотора, увеличением расхода водорода и т. п. Если изменением режима не удается компенсировать снижение активности катализатора, необходимо провести регенерацию катализатора.
Периодичность регенерации зависит от свойств данной партии катализатора, состава сырья, типа катализатора и, наконец, от того, насколько точно соблюдают технологический режим. По рекомендациям научно-исследовательских институтов межрегенера-ционный период для катализаторов риформинга АП-56 и АП-64 составляет 3—6 месяцев, для полиметаллических катализаторов серии Кр — 12 месяцев, для алюмокобальтмолибденовых катализаторов гидроочистки средних дистиллятов — 6 месяцев. Однако на практике во многих случаях межрегенерационный период оказывается гораздо большим.
Регенерация катализатора на установках каталитического риформинга сводится к выжигу кокса, отложившегося на алюмопла-тиновом катализаторе и проводится при строго контролируемой температуре с использованием инертного газа, содержащего определенное количество кислорода. Кислород поступает вместе с воздухом, подаваемым при регенерации в линию нагнетания циркуляционных компрессоров, которыми в этот период перекачивается инертный газ.
Количество воздуха, подаваемого на разных стадиях регенерации, неодинаково. На первой стадии воздух поступает в таком количестве, чтобы его содержание в газе на входе в реакторы составляло 0,5—0,6% (об.). Во время второй стадии регенерации расход воздуха поддерживается таким, чтобы содержание кислорода в смеси сначала составляло 0,5—0,6% (об.). Затем расход воздуха увеличивается и содержание кислорода доводится до 1,0% (об.). После окончания второй стадии регенерации осуществляется прокалка катализатора, во время которой содержание кислорода на входе в первый реактор повышается до 1,5% (об.), а затем до 3% (об.).
Воздух на установках каталитического риформинга необходим также при пассивации катализатора (окислении сорбированных на поверхности катализаторов углеводородов, способных самовоспламеняться при соприкосновении катализатора с воздухом). Пассивация осуществляется инертным газом, содержащим до 5% (об.) кислорода.
Регенерация катализатора на установках гидроочистки проводится паровоздушным или газовоздушным методом.
Процесс паровоздушной регенерации состоит из трех стадий: начальный период, собственно регенерация, выжиг глубинного кокса. В первый период воздух подается в постепенно увеличивающихся количествах. Сначала во избежание «вспышки» кокса и быстрого подъема температуры воздух подается в количестве, не превышающем 1% (об.) от расхода водяного пара. В период установившегося режима расход воздуха составляет 5—8% (об.) от расхода водяного пара, а при операции выжига глубинного кокса доводится до 8—12% (об.). Регенерация считается законченнойкогда концентрация кислорода в отходящих дымовых тазах повышается до 15—18% (об.).
При газовоздушной регенерации катализатора выжиг кокса ведется смесью инертного газа и воздуха. В начальный период регенерации расход воздуха должен быть таким, чтобы содержание кислорода в смеси составляло 0,2% (об.), а в конце регенерации — 1,2% (об.). После окончания регенерации проводится операция прокалки кокса, во время которой содержание кислорода в циркулирующем газе должно составлять 2% (об.).
Расход воздуха за период регенерации катализатора на установках риформинга и гидроочистки достигает 50—100тыс. м3. Следует иметь в виду, что количество воздуха, подаваемого в различные периоды регенерации, изменяется. Например, при регенерации катализатора в секции риформинга воздух расходуется в продолжение 36 ч, начиная с 67-го часа регенерации, по 16 м3/ч. Затем после 5-часового перерыва (нагрев катализатора до более высокой температуры) воздух расходуется по 2400 м3/'ч в течение 12 ч и после трехчасового перерыва (нагрев катализатора до еще более высокой температуры) вновь подается в количестве 2400 м3/ч в течение 4 ч.
К окислительным процессам, наиболее распространенным на НПЗ, относятся получение битума, производство синтетических жирных кислот (СЖК) из нефтяных парафинов, получение серной кислоты и элементарной серы из сероводорода.
На битумных установках расход воздуха составляет 100— 150 м3/т получаемого продукта, на установках производства СЖК около 50 м3/т сырья.
Расход сжатого воздуха на ремонтные нужды зависит от количества подключаемых во время ремонта инструментов и принимается равным 1,5 м3/мин на каждый инструмент. Кроме того, технологический воздух потребляется ремонтно-механической базой, цехом металлической тары и разливочной масел.
Потребители предъявляют различные требования к давлению подаваемого воздуха. Нормы технологического проектирования требуют, чтобы давление сжатого воздуха общего назначения (технологического) у источника давления составляло 0,8 МПа, а у потребителя— не ниже 0,6 МПа. Сжатый воздух для приборов контроля и автоматизации у источника давления должен иметь давление 0,7—0,8 МПа, а у потребителя — не ниже 0,6 МПа. Температура воздуха должна быть равна 30—40 °С. На установках каталитического крекинга давление в регенераторах не превышает 0,06—0,08 МПа, поэтому воздух можно подавать при небольшом избыточном давлении.
При регенерации катализатора установок гидроочистки и каталитического риформинга воздух подается в нагнетательную линию циркуляционных компрессоров, перекачивающих инертный газ. Поэтому давление воздуха должно быть не ниже давления, развиваемого этими компрессорами. На установки риформинга воздух должен поступать с давлением 2,2—2,4 МПа, а на установки гидроочистки, где проводится газовоздушная регенерация,— 4,0 МПа.
Снабжение воздухом осуществляется как от централизованных общезаводских воздушных компрессорных, так и от местных воздуходувных и компрессорных. Местные воздуходувные и компрессорные имеются в составе установок каталитического крекинга и производства битума.
Для централизованного снабжения потребителей сжатым воздухом на НПЗ сооружаются воздушные компрессорные. При определении числа компрессорных на заводе учитываются следующие факторы:
1) размер территории завода и расстояние от воздушной компрессорной до наиболее удаленного потребителя воздуха (необходимо, чтобы потери давления в сети до потребителя не превышали 0,2 МПа);
2) очередность ввода объектов завода в эксплуатацию.
Как правило, на НПЗ с большим числом установок малой единичной мощности, занимающих значительную площадь, сооружается и эксплуатируется не менее двух воздушных компрессорных. На современных заводах, территория которых благодаря применению укрупненных и комбинированных установок в несколько раз меньше, строится одна центральная заводская воздушная компрессорная.
Работа воздушных компрессорных и систем снабжения сжатым воздухом регламентирована «Правилами устройства и безопасной эксплуатации воздушных компрессоров и воздухопроводов», утвержденными ВЦСПС 22 июня 1963 г. В «Правилах» содержатся основные положения об установке компрессоров, системах смазки и забора воздуха, арматуре, контрольно-измерительных приборах и регулирующей аппаратуре воздушных компрессорных, устройстве и монтаже внешних воздухопроводов.
Число компрессоров выбирается в зависимости от потребности в воздухе, производительности серийно выпускаемых компрессоров, необходимости обеспечения бесперебойного снабжения воздухом постоянных потребителей. Предусматривается 100%-ный резерв для компрессоров, подающих воздух для приборов автоматического контроля.
На большинстве действующих НПЗ для сжатия воздуха применяются поршневые компрессоры с масляной смазкой цилиндров. Содержание масла в сжатом воздухе после таких компрессоров достигает 20—25 мг/м3, а иногда и еще выше, Удаление масла из сжатого воздуха — технически сложная задача, которую не всегда удается решить успешно. Поэтому более целесообразно для сжатия воздуха использовать компрессоры непоршневого типа (мембранные, центробежные и т. п.) и поршневые, работающие без смазки цилиндров. На некоторых НПЗ уже эксплуатируются воздушные компрессорные, оборудованные центробежными компрессорами типа К-250-61-2, ЦК-135/8.
Воздухозаборйые устройства располагаются вне производственного помещения — в зоне, которая защищена от солнечной радиации и тепловых выделений различных агрегатов. Воздух забирается на высоте не менее чем на 2—3 м выше уровня земли. Заборное устройство закрывается специальным колпаком, предотвращающим попадание в него атмосферных осадков.
Фильтры во всасывающей линии компрессора предназначаются для удаления из воздуха частиц пыли крупнее 5—6 мкм. Наиболее широко применяются пылевые фильтры, состоящие из' набора смоченных в свинцовом масле кассет или цилиндров (свинцовые фильтры), а также фильтры, изготавливаемые из стекловолокна, полиамидных и целлюлозных волокон.
Фильтры могут быть индивидуальными или общими для нескольких компрессоров, однако в последнем случае для каждого компрессора должна быть предусмотрена возможность отключения (при необходимости ремонта) от общего всасывающего трубопровода.
Для компрессоров малой производительности (до 360 м3/ч) с разрешения технической инспекции профсоюзов допускается осуществлять Забор воздуха из помещения компрессоров станции.
Все компрессорные установки снабжаются следующими контрольно-измерительными приборами и арматурой:
1) манометрами и предохранительными клапанами на компрессорах, холодильниках и воздухосборниках (ресиверах);
2) устройствами для измерения температуры сжатого воздуха на каждой ступени компрессора и после промежуточного и концевого холодильника, а для компрессоров производительностью более 3000 м3/ч — регистрирующими приборами;
3) приборами для сигнализации и автоматического отключения компрессора при повышении давления и температуры сжатого воздуха сверх допустимых норм, а также при прекращении подачи охлаждающей воды;
4) манометрами и термометрами для измерения температуры и давления масла.
Компрессорные станции, на которых эксплуатируется три и более машин оборудуются системой дистанционного контроля и сигнализации работы установки.
Смазка компрессоров проводится в соответствии с инструкцией завода-изготовителя. Разница между температурой вспышки масла и температурой сжатого воздуха должна быть не менее 75 °С. Масляные фильтры в системе принудительной циркуляции масла необходимо очищать не реже одного раза в два месяца, а масляный насос — не реже одного раза в месяц.
Сжатый воздух после компримирования содержит не только масло, но и влагу, пыль, продукты коррозии. Поэтому он нуждается в очистке и осушке. Для отделения водяных и масляных капель используются специальные аппараты — водомаслоотделители. Существуют водомаслоотделители инерционного, поверхностного и инерционно-контактного типа. Инерционное отделение капель происходит вследствие поворотов и резкого изменения скорости воздушного потока. В аппаратах поверхностного типа воздушный поток пропускают через слой насадки с развитой поверхностью (гофрированные сетки, кольца Рашига и т. п.), в аппаратах инерционно-контактного типа воздушный поток проходит между зигзагообразными листами или жалюзями.
Наивысшая степень отделения жидкости достигается в водо-маслоотделителях с насадкой из волокнистых фильтрующих материалов. В качестве фильтрующих материалов используются стекловолокно, капроновое волокно, асбест и т. п.
Помимо капель в сжатом воздухе после компрессоров содержатся пары масла. Для очистки воздуха от масляных паров применяются различные поглотители — активные угли, силикагель, активная окись алюминия.
Осушка воздуха на НПЗ осуществляется также адсорбционным методом. Другие существующие методы (охлаждение, абсорбция, хемосорбция) используются редко. Адсорбционный метод позволяет добиться очень низкого остаточного влагосодержания воздуха (соответствующего температуре точки росы минус 70°С и ниже).Схема воздушной компрессорной приведена на рисунке 5.
Рисунок 5 - Схема воздушной компрессорной:
ЦК 1, ЦК-2—центробежные компрессоры низкого давления; ЛК-1, ЛК-2—поршневые компрессоры высокого давления;
Ф-1, Ф-11— фильтры; Г-1, Г-4—теплообменники;
УОВ 1 — УОВ- 2 — установки осушки воздуха;
Е-1— Е-5 - емкости н сепараторы;
МО-1, МО-2—маслоотделители;
А-1 — воздухозаборная труба; Г-1 — гидрозатвор;
I — воздух на нужды КИП;II—воздух технологический; III — воздух высокого давления; IV— воздух к глушителям шума;
V — выхлоп в атмосферу; VI—слав масла.
Воздух забирается через воздухозаборную трубу А-1, проходит через воздушные фильтры Ф-1, Ф-2 и подается на компрессоры ЦК-1 и ЦК-2, которыми сжимается до 0,8 МПа. Для предотвращения превышения давления на нагнетательной линии компрессоров установлен предохранительный клапан. Сжатый воздух охлаждается в холодильниках Т-1, Т-2.
Охлажденный воздух проходит группу коксовых фильтров Ф-3 — Ф-10 типа ВМФ и поступает в отделение осушки. Для осушки используются установки типа УОВ, состоящие из автоматического блока осушки, блока фильтров для улавливания масла, блока для улавливания пыли, теплообменника и воздухосборника.
Блоки осушки воздуха имеют низкую единичную производительность. Серийно выпускаются установки на 10; 20; 30 и 100 м3/мин воздуха. При использовании даже наиболее крупной из установок УОВ в состав общезаводской компрессорной приходится включать несколько таких установок.
Недостатками установок осушки воздуха являются относительно низкая надежность (блоки и, в особенности, входящие в их состав воздухоподогреватели часто выходят из строя), отсутствие автоматического регулирования степени осушки в условиях переменных расходов и температур, низкая интенсивность использования оборудования. Осушенный воздух подается потребителям по трубопроводам. Коллекторы осушенного воздуха прокладываются по территории заводов без изоляции и спутника, а трубопроводы неосушенного (технологического) воздуха — с паровым или водяным спутником и в изоляции.
Целесообразно подвергать осушке также и технологический воздух, что позволит отказаться от расхода теплоты на обогрев трубопроводов. Кроме того, появляется возможность использования трубопроводов технологического воздуха для резервирования трубопровода воздуха КИП. «Правила устройства и безопасной эксплуатации воздушных компрессоров и воздухопроводов» требуют периодически, не реже одного раза в 6 месяцев, проводить промывку воздухопроводов для очистки от масляных отложений. Промывать воздухопроводы рекомендуется 5%-ным раствором едкого натра. После очистки воздухопровод должен быть промыт водой до полной нейтрализации едкого натра и просушен сжатым воздухом в течение не менее получаса.
После продувки проверяют, не произошло ли уменьшение толщины стенок воздухопровода вследствие коррозии. В период промывки коллектора воздуха КИП подача воздуха для приборов осуществляется по коллектору технологического воздуха.
В состав общезаводских компрессорных в ряде случаев включаются компрессоры высокого давления для подачи воздуха на регенерацию катализаторов риформинга и гидроочистки. На некоторых установках каталитического риформинга и гидроочистки, построенных в 1962—1970 гг. (Л-35-11/300, Л-24-6), имеются специальные компрессоры, сжимающие воздух до необходимого давления. Ряд заводов использует эти компрессоры для подачи воздуха высокого давления на другие установки.
Осушенный воздух низкого давления дросселируется до давления 3 кПа и через буферную емкость подается на сжатиекомпрессорами высокого давления ПК-1, ПК-2. Для защиты компрессоров от повышения давления во всасывающей линии предусмотрен гидрозатвор Г-1. Сжатый компрессорами воздух охлаждается в холодильниках Т-3, Т-4, отделяется от масла в маслосборниках с циклонными сепараторами МО-1, МО-2 и через емкость (ресивер) Е-5 выдается в сеть.
Недостаток описанной схемы — необходимость дважды сжимать воздух: сначала до 0,8 МПа, а затем (после дросселирования) до более высокого давления. Такое решение является вынужденным и связано с тем, что при регенерации катализаторов необходим осушенный воздух, а установки УОВ рассчитаны только на давление 0,8 МПа.
Система снабжения потребителей воздухом КИП должна обладать повышенной надежностью, поскольку прекращение подачи этого воздуха делает технологические производства неуправляемыми и может стать причиной крупных аварий. Для обеспечения гарантированной непрерывной подачи воздуха КИП, как уже указывалось выше, предусматривается 100%-ное резервирование компрессоров, подающих воздух для пневматических систем автоматизации.
На многих зарубежных НПЗ резервный компрессор имеет привод от паровой турбины или дизельного двигателя. Это позволяет обеспечить непрерывную подачу воздуха КИП даже при прекращении- поступления электроэнергии.
Важным элементом безаварийной системы снабжения воздухом приборов автоматики и контроля служат буферные емкости (ресиверы), которые размещаются на технологических установках и предназначаются для хранения запаса сжатого воздуха.
Буферными емкостями, рассчитываемыми на хранение часового запаса воздуха КИП, оснащаются все установки и объекты общезаводского хозяйства.
Таким образом, резюмируя все вышеизложенное следует, что инертные газы, водород и сжатый воздух занимают в производстве немаловажно положение. Без наличия данных оборотных средств невозможно организовать любое нефтеперерабатывающее производство.
СПИСОК ЛИТЕРАТУРЫ
Рудин М.Г., Арсеньев Г.А., Васильев А.В. Общезаводское хозяйство нефтеперерабатывающего завода
Дата добавления: 2018-04-05; просмотров: 2118; Мы поможем в написании вашей работы! |
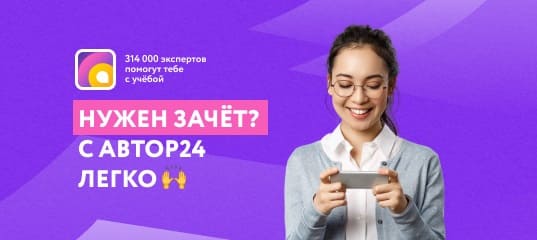
Мы поможем в написании ваших работ!