Углеродистая сталь У8 после закалки и отпуска. Опешите превращения, которые происходят при выбранных режимах термической обработки и окончательную структуру
Для каких целей применяются неполные отжиги? Как выбрать режим такого отжига? Опешите структурные превращения.Приведите примеры. Неполный отжиг. Этот отжиг отличается от полного тем, что сталь нагревают до более низкой температуры (немного выше точки Ас. Для доэвтектоидных сталей неполный отжиг применяют для улучшения обрабатываемости резанием. Однако при неполном отжиге происходит частичная перекристаллизация стали только вследствие превращения перлит — аустенит. Избыточный феррит лишь частично превращается в аустенит, и поэтому значительная его часть не подвергается перекристаллизации. В связи с этим неполный отжиг доэвтектоидных сталей применяют в том случае, если горячая механическая обработка их была выполнена правильно и при этом не было получено крупного зерна такой структуры, как, например, видманштеттова. Для заэвтектоидных сталей применяют только неполный отжиг. В этих сталях нагрев несколько выше точки Ас1 (обычно на 10 — 30°С) вызывает практически полную перекристаллизацию и позволяет получить зернистую структуру перлита (см. рис. 1, и) вместо пластинчатой (рис. 1, ж и з). Такой отжиг называют сфероидизацией. Рис. 1. Микроструктура стали в зависимости от содержания углерода ; а – 0,06%С; б – 0,01%С; в – 0,22%С; г – 0,3%С; д – 0,4%С; е – 0,55%С; ж – 0,8%С; з – 1,3%С; и – 1,1%С. Частицы цементита, не растворившегося при нагреве, и микрообъемы с повышенной концентрацией углерода в аустените, из-за недостаточно полной его гомогенизации, служат центрами кристаллизации для цементита, выделяющегося при последующем охлаждении ниже точки /1t и принимающего в этом, случае зернистую форму. В результате нагрева значительно выше точки Ас1 и растворения большей части цементита и более полной гомогенизации аустенита последующее выделение его ниже точки Ас1 происходит в пластинчатой форме. Если избыточный цементит находился в виде сетки (см. рис. 1, з), что является дефектом, то перед этим отжигом предварительно нужно провести нормализацию с нагревом выше Аст для растворения сетки из вторичного цементита с последующим охлаждением на воздухе или в воздушной струе для предупреждения выделения этого цементита по границам аустенита. Нормализацию нередко проводят с прокатного (ковочного) нагрева. Стали, близкие к эвтектоидному составу, имеют узкий интервал температур нагрева (750 —760°С) для отжига на зернистый цементит, для заэвтектоидных углеродистых сталей интервал расширяется до 770 —790°С. Легированные заэвтектоидные .стали для получения зернистых карбидов можно нагревать до более высоких температур и в более широком интервале (770- 820°С). Охлаждение при сфероидизации медленное. Оно должно обеспечить распад аустенита на ферритно-карбидную структуру, сфероидизацию и коагуляцию образовавшихся карбидов, при охлаждении до 620 —680°С. Чаще применяют изотермический отжиг, требующий меньше времени. В этом случае сталь медленно охлаждают (30 — 50°С/ч) до 620 — 680°С. Выдержка при постоянной температуре, необходимая для распада переохлажденного аустенита и коагуляции карбидов, составляет 1 — 3 ч в зависимости от массы отжигаемого металла. Последующее охлаждение производят на воздухе. Сталь с зернистым перлитом имеет более низкую твердость, предел прочности и соответственно более высокие значения относительно удлинения и сужения. Например, эвтектоидная сталь с пластинчатым перлитом имеет твердость НВ 228, а с зернистым перлитом — НВ 163; соответственно предел прочности 82 и 63 кгс/мм2 и относительное удлинение .15 и 20%. После отжига на зернистый перлит эвтектоидные и заэвтектоидные стали обладают наилучшей обрабатываемостью резанием, т. е. возможно применение больших скоростей резания и достигается высокая чистота поверхности. Отжигу на зернистый перлит подвергают также тонкие листы и прутки из низко и среднеуглеродистой стали перед холодной штамповкой или волочением для повышения пластичности. Вследствие ускоренного охлаждения после прокатки или другой горячей обработки легированные стали получают неравномерную структуру: сорбит, троостит, бейнит или мартенсит и, как следствие этого, высокую твердость. Для снижения твердости на металлургических заводах сортовой прокат подвергают высокому отпуску при 650 — 680°С (несколько ниже точки Ах). При нагреве до указанных температур происходят процессы распада мартенсита, коагуляции карбидов и в итоге снижение твердости.
|
|
|
|
|
|
Углеродистая сталь У8 после закалки и отпуска. Опешите превращения, которые происходят при выбранных режимах термической обработки и окончательную структуру.
Цементацией называется процесс насыщения поверхностного слоя стали углеродом. Различают два основных вида цементации: твердыми углеродсодержащими смесями (карбюризаторами) и газовую. Целью цементации является получение твердой и износостойкой поверхности, что достигается обогащением поверхностного слоя углеродом и последующей закалкой с низким отпуском. Цементация и последующая термическая обработка одновременно повышают и предел выносливости.
|
|
Для Цементации обычно используют низкоуглеродистые стали (0,12 — 0,23% С). Выбор таких сталей необходим для того, чтобы сердце вина изделия, не насыщающаяся углеродом при цементации, сохраняла высокую вязкость после закалки.
Для цементации детали поступают после механической обработки с припуском на шлифование 0,05 — 0,10 мм или после окончательной обработки (например, автомобильные шестерни). Во многих случаях цементации подвергается только часть детали; тогда участки, не подлежащие упрочнению, защищают тонким слоем меди (0,02 — 0,05 мм), которую наносят электролитическим способом, или изолируют специальными обмазками, состоящими из смеси огнеупорной глины, песка и асбеста или окиси алюминия и талька, замешанных на жидком стекле и др.
Цементация твердым карбюризатором.
В этом процессе насыщающей средой является древесный уголь (дубовый или березовый) в зернах поперечником 3,5 —10 мм или каменноугольный полукокс и торфяной кокс, к которым добавляют активизаторы: углекислый барий (ВаСОэ) и кальцинированную соду (Na2C02) в количестве 10 — 40% от массы угля.
Широко применяемый карбюризатор состоит из древесного угля, 20 — 35% ВаСОэ и ~ 3,5% СаС03 . Рабочую смесь, применяемую для цементации, составляют из 25 — 35% свежего карбюризатора и 65 — 75% отработанного. Содержание ВаС03 в такой смеси 5 — 7%, что обеспечивает требуемую толщину слоя и исключает образование грубой цементитной сетки па поверхности.
Изделия, подлежащие цементации, после предварительной очистки укладывают в ящики: сварные стальные или, реже, литые чугунные прямоугольной или цилиндрической формы. При упаковке изделий на дно ящика насыпают и утрамбовывают слой карбюризатора толщиной 20 — 30 мм, на который укладывают первый ряд деталей, выдерживая расстояния между деталями и до боковых стенок ящика 10—15 мм. Затем засыпают и утрамбовывают слой карбюризатора толщиной 10—15 мм, на него укладывают другой ряд деталей и т. д. Последний (верхний) ряд деталей засыпают слоем карбюризатора толщиной 35 — 40 мм с тем, чтобы компенсировать возможную его усадку. Ящик накрывают крышкой, кромки которой обмазывают огнеупорной глиной или смесью глины и речного песка. После этого ящик помещают в печь.
Нагрев до температуры цементации (910 —930°С) составляет 7 — 9 мин па каждый сантиметр минимального размера ящика. Продолжительность выдержки при температуре цементации для ящика с минимальным размером 150 мм составляет 5,5 —6,5 ч для слоя толщиной 0,7 —0,9 мм и 9 — 11 ч для слоя толщиной 1,2 —1,5 мм. При большем размере ящика (минимальный размер 250 мм) для получения слоя толщиной 0,7 —0,9 мм продолжительность выдержки равна 7,5 —8,5 ч, а при толщине 1,2 —1,5 мм — И — 14 ч.
После цементации ящики охлаждают на воздухе до 400 — 500°С и затем раскрывают.
Цементацию стали производят атомарным углеродом. При цементации твердым карбюризатором атомарный углерод образуется следующим образом. В цементационном ящике имеется воздух, кислород которого при высокой температуре взаимодействует с углеродом карбюризатора, образуя окись углерода. Окись углерода в присутствии железа диссоциирует по уравнению 2СО -> С02 + Сат.
Углерод, выделяющийся в результате этой реакции в момент его образования, является атомарным и диффундирует в аустенит. Добавление углекислых солей активизирует карбюризатор, обогащая атмосферу в цементационном ящике окисью углерода:
ВаСОэ + С -► ВаО + 2 СО.
Газовая цементация.
Этот процесс осуществляют нагревом изделия в среде газов, содержащих углерод. Газовая цементация имеет ряд преимуществ по сравнению с цементацией в твердом карбюризаторе, поэтому ее широко применяют на заводах, изготовляющих детали массовыми партиями.
В случае газовой цементации можно получить заданную концентрацию углерода в слое; сокращается длительность процесса, так как отпадает необходимость прогрева ящиков, наполненных малотеплопроводным карбюризатором; обеспечивается возможность полной механизации и автоматизации процессов и значительно упрощается последующая термическая обработка изделий, так как можно производить закалку непосредственно из цементационной печи.
Наиболее качественный цементованный слой получается при использовании в качестве карбюризатора природного газа, состоящего почти полностью из метана (СН4) и пронапбутановых смесей, подвергнутых специальной обработке, а также жидких углеводородов. Основной реакцией, обеспечивающей науглероживание при газовой цементации, является диссоциация окиси углерода и метана:
2С0-тС02 + Сат
или
СН4->2Н2 + Сат, Сат-»Геу = аустенит Fev(C).
Процесс ведут при 910 — 930°С, 6—12 ч (толщина слоя 1,0—1,7 мм)
В серийном производстве газовую цементацию обычно проводят в шахтных муфельных печах серии Ц (рис. 150). Шахтные печи серии Ц (Ц-35Б, Ц-60Б, Ц-75Б, Ц-105Б) имеют рабочую температуру 950°С, единовременную загрузку 185 — 1100 кг, диаметр рабочего пространства 300 — 600 мм и высоту 600 — 1200 мм . Изделия в печь загружают на специальных подвесках и приспособлениях, которые помещают в реторте. Необходимая для газовой цементации атмосфера создается при подаче (с помощью специальной капельницы) в камеру печи жидкостей, богатых углеродом (керосин, синтин, спирты и т. д.). Углеводородные соединения при высокой температуре разлагаются с образованием активного углерода и водорода.
На предприятиях с серийным масштабом производства также применяют камерные универсальные печи с герметизированной форкамеройи закалочным баком (см. рис. 2). В таких печах исключается контакт нагретых деталей с воздухом, предотвращается образование дефектов на поверхности изделий, снижающих прочность.
Рис. 2. Механизированная камерная электропечь ( типа СНЗА):
1 – заколоченный бак; 2 – заколоченная камера; 3 – стол для загрузки и выгрузки деталей; 4 – вентилятор; 5 – нагревательная камера; 6 – цепной механизм для передвижения поддона с деталями.
Укажите структуру металлической основы серого чугуна и форму графита, наиболее пригодные для обеспечения износостойкости вкладышей подшипников. Перечислите примерные механические свойства.
Серый чугун.
Серый чугун (технический) представляет собой по существу сплав Fe — Si — С, содержащий в качестве неизбежных примесей Mn, Р и S. В структуре серых чугунов большая часть или весь углерод находится в виде графита. Характерная особенность структуры серых чугунов, определяющая многие его свойства, заключается в том, что графит имеет в поле зрения микрошлифа форму пластинок. Наиболее широкое применение получили доэвтектоидные чугуны, содержащие 2,4 —3,8% С. Чем выше содержание в чугуне углерода, тем больше образуется графита и тем ниже его механические свойства. В связи с этим количество углерода в чугуне обычно не превышает 3,8%. В то же время для обеспечения высоких литейных свойств (хорошей жидкотекучести) углерода должно быть не меньше 2,4%.
Кремний, содержание которого в серых чугунах находится в пределах 1,2 — 3,5%, оказывает большое влияние на строение, а следовательно, и на свойства чугунов, поэтому при изучении структурообразования в техническом чугуне нужно пользоваться не диаграммой состояния Fe — С, а тройной диаграммой Fe — Si — С.
Охлаждение чугуна в реальных условиях вносит существенные отклонения отусловий равновесия, поэтому по равновесной диаграмме состояния нельзя судить о процессе затвердевания и получающихся при этом фазах в структурах. Структура чугуна в отливках зависит в первую очередь от химического состава (содержания углерода и кремния) и скорости кристаллизации.
Кремний способствует процессу графитизации, действуя в том же направлении, что и замедление скорости охлаждения. Путем изменения, с одной стороны, содержания в чугуне углерода и кремния и, с другой стороны скорости охлаждения, можно получить различную структуру металлической основы чугуна. Структурная диаграмма для чугунов, показывающая, какой должна быть структура в отливке с толщиной стенки 50 мм в зависимости от содержания в чугуне кремния и углерода показана на рис. 3, а. При данном содержании углерода, чем больше в чугуне кремния, тем полнее протекает процесс графитизации. Чем больше в чугуне углерода, тем меньше требуется кремния для получения заданной структуры.
В зависимости от содержания углерода, связанного в цементит, различают несколько видов чугуна:
1.Белый чугун; весь углерод находится в виде цементита Fe3C. Структура чугуна (рис. 4, а) —перлит и ледебурит (область I на рис. 3).
2.Половинчатый чугун; большая часть углерода (свыше 0,8%) находится в виде Fe3C. Структура чугуна — перлит, ледебурит и пластинчатый графит 1 (область II на рис. 3).
3.Перлитный серый чугун; структура (рис. 4,б) —перлит и пластинчатый графит (область III на рис. 3). В этом чугуне 0,7 —0,8% С находится в виде Fe3C, входящего в состав перлита.
Рис. 3. Структурные диаграммы для чугунов:
а – влияние С и Si на структуру чугуна; б – влияние скорости охолождения (толщины отливки) и суммы С + Si на структуру чугуна; Ⅰ – белый чугун; ⅠⅠ – V – серые чугуны.
|
Рис. 4. Микроструктуры серого чугуна ( 500):
а – белый чугун; б – перлитный серый чугун; в – ферритно – перлитный серый чугун; г – ферритный серый чугун.
4.Ферритно-перлитный серый чугун; структура (рис. 4,в) — перлит, феррит и пластинчатый графит (область /Кна рис. 3). В этом чугуне о зависимость от степени распада :эвтектоидного цементита в связанном со-стоянии находится от 0,7 до 0,1% С.
5.Ферритный серый чугун; структура (рис. 4, г,) феррит и пластинчатый графит (область Гна рис. 3). В этом случае весь углерод, находится в виде графита.
При данном содержании углерода и кремния процесс графитизации протекает тем полнее, чем медленнее охлаждение. В производственных условиях скорость охлаждения удобно характеризовать по толщине стенки отливки. Чем тоньше отливка, тем быстрее охлаждение и в меньшей, степени протекает процесс графитизации (см. рис. 3,б). Следовательно, содержание кремния надо увеличивать в отливке небольшого сечения, охлаждающейся ускоренно, или в чугуне с меньшим содержанием углерода. В толстых сечениях отливок, охлаждающихся медленно, процесс графитизации протекает полнее и содержание кремния может быть меньше.
Количество марганца в чугуне не превышает 1,25 — М%. Марганец препятствует процессу графитизации, т. е. затрудняет выделение графита и повышает способность чугуна к отбеливанию (к появлению, особенно в поверхностных слоях, структуры белого или половинчатого чугуна).
Сера является вредной примесью, ухудшающей механически и литейные свойства чугуна, поэтому ее содержание ограничивают до 0,1—0,12%. В сером чугуне сера образует сульфиды (FeS, MnS) или их твердые растворы (Fe, Mn) S.
Содержание фосфора в сером чугуне приблизительно 0,2%, но иногда допускается даже до 0,5%. При повышенном содержании фосфора в структуре чугуна образуются твердые включения фосфидной эвтектики: в серых чугунах,— двойной Fe3P — аустенит, а в белых тройной Fe3C — Fe3P — аустенит. Образование эвтектики улучшает литейные свойства чугуна (повышает жидкотекучесть), при этом увеличивается хрупкость отливок.
Механические свойства чугуна обусловлены его структурой, главным образом графитной составляющей. Чугун можно рассматривать как сталь, пронизанную графитом, который играет роль надрезов, ослабляющих металлическую основу структуры. В этом случае механические свойства будут зависеть от количества, величины и характера распределения включений графита.
Чем меньше графитовых включений, чем они мельче и больше степень изолированности их друг от друга, тем выше прочность чугуна. Чугун с большим количеством прямолинейных крупных графитовых выделений, разделяющих его металлическую основу, имеет грубозернистый излом и низкие механические свойства. Чугун с мелкими и завихренными графитными выделениями обладает более высокими свойствами.
Пластинки графита уменьшают сопротивление отрыву, предел прочности, и особенно пластичность чугуна. Относительное удлинение при растяжении серого чугуна независимо от свойств металлической основы практически равно нулю (0,5%). Графитовые включения мало влияют на снижение предела прочности при сжатии и твердости, величина которых определяется главным образом структурой металлической основы чугуна. При сжатии чугун претерпевает значительные деформации, и разрушение имеет характер среза под углом 45°. Разрушающая нагрузка при сжатии, в зависимости от качества чугуна и его структуры, в 3-5 раз больше, чем при растяжении, поэтому чугун рекомендуется использовать преимущественно для изделий, работающих на сжатие.
Пластинки графита менее значительно, чем при растяжении, снижают прочность и при изгибе, так как часть изделия испытывает сжимающие напряжения. Предел прочности при изгибе имеет промежуточное значение между пределом прочности на растяжение и пределом прочности на сжатие. Твердость чугуна в зависимости от металлической основы НВ 143 — 255.
Графит, нарушая сплошность металлической основы, делает чугун малочувствительным к всевозможным внешним концентраторам напряжений (дефектам поверхности, надрезам, выточкам и т. д.). Вследствие этого серый чугун имеет примерно одинаковую конструктивную прочность в отливках простой формы или с ровной поверхностью, и сложной формы с надрезом или плохо обработанной поверхностью. Графит повышает износостойкость и антифрикционные свойства чугуна вследствие собственного «смазывающего» действия и повышения прочности пленки смазки. Очень важно, что графит улучшает обрабатываемость резанием, делая стружку ломкой.
Металлическая основа в сером чугуне обеспечивает наибольшую прочность и износостойкость, если она имеет перлитную структуру (рис. 4, б). Присутствие в структуре феррита, не увеличивая пластичности и вязкости чугуна, снижает его прочность и износостойкость. Наименьшей прочностью обладает ферритный серый чугун.
Серый чугун маркируется буквами С — серый и Ч — чугун (ГОСТ 1412 — 70). После букв следуют цифры. Первые цифры указывают среднюю величину предела прочности при растяжении, а вторые — среднюю величину предела прочности при испытании на изгиб. Предел прочности при изгибе используют для оценки пластичности чугуна, так как относительное удлинение у всех серых чугунов практически равно нулю.
Серые чугуны по свойствам и применению можно распределить на группы, приведенные ниже:
Ферритные и ферритно-перлитные чугуны (СЧ 00, СЧ 12 — 28, СЧ 15 — 32, СЧ 18 — 36) имеют пределы прочности при растяжении 12—18 и при изгибе 28 — 40 кгс/мм2. Их примерный состав: 3,1 —3,6% С; 1,8 —2,5% Si; 0,6—1,2% Мп; <0,3 — 0,60% Р; <0,15% S (химический состав устанавливают в зависимости от толщины стенок отливки). Структура чугунов — перлит, феррит и графит грубой (СЧ 00, СЧ 12 — 28) или средней величины. Эти чугуны применяют для изготовления малоответственных деталей, испытывающих небольшие нагрузки в работе. Например, чугун СЧ 12 — 28 используют для строительных колон, фундаментных плит, а чугуны СЧ 15 — 32 и СЧ 18 —36 — для литых малонагруженных деталей сельскохозяйственных машин, станков, автомобилей и тракторов, арматуры и т. д.
Перлитные чугуны (СЧ 21-40, СЧ 24-44, СЧ 28-48, СЧ 32-52, СЧ 36 —56, СЧ 40 — 60) применяют для отливки станин мощных станков и механизмов, поршней, цилиндров, деталей, работающих на износ в условиях больших давлений (компрессорное, арматурное и турбинное литье, дизельные цилиндры, блоки двигателей, детали металлургического оборудования и т. д.). Структуры этих чугунов — мелкопластинчатый перлит (сорбит) с мелкими завихренными графитными включениями. К перлитным чугунам относятся так называемые сталистые и модифицированные чугуны.
Сталистые чугуны (СЧ 24-44, СЧ 28 — 48) получают выплавкой с добавлением в шихту 20 — 30% стального лома; чугуны имеют пониженное со-держание углерода, что обеспечивает получение более дисперсной перлитной основы с меньшим количеством графитных включений. Примерный состав: 2,9-3,3% С; 1,1 —1,8% Si; 0,8 —1,2% Мп; <0,2%Р; < 0Ь12% S. Содержание кремния в этих чугунах должно быть достаточным для предотвращения возможности отбеливания чугуна.
Модифицированные чугуны (СЧ 32 — 52, СЧ 36 — 56, СЧ 40 — 60 и СЧ 44 — 64) получают при добавлении в жидкий чугун перед разливкой специальных добавок — модификаторов. (75%-ный ферросилиций, силикокальций в количестве 0,3 —0,8% и т. д.). Модифицирование применяют для получения в чугунных отливках с различной толщиной стенок перлитной металлической основы с вкраплением небольшого количества изолированных пластинок графита средней величины. Модифицирование наиболее эффективно при использовании чугуна определенного состава и перегрева его перед модифицированием до 1400*0. Перегрев обеспечивает измельчение графитных включений и способствует получению более плотных отливок.
Модифицированию подвергают низкоуглеродистый чугун, содержащий сравнительно небольшое количество кремния и повышенное количество марганца и имеющий без введения модификатора структуру половинчатого чугуна, т. е. ледебурит, перлит и графит. Примерный химический состав чугуна: 2,5-3,0% С; 1,1-1,5% Si; 0,8-1,2% Мп; <0,2% Р и <0,12% S (СЧ 40-60 и СЧ 44-64).
Для снятия литейных напряжений и стабилизации размеров чугунные отливки отжигают при 500 —570°С. В зависимости от формы и размеров отливки выдержка при температуре отжига составляет 3—10 ч. Охлаждение после отжига медленное, вместе с печью. После такой обработки механические свойства изменяются мало, а внутренние напряжения снижаются на 80 — 90%. Иногда для снятия напряжений в чугунных отливках применяют естественное старение чугуна — выдержку их на складе в течение 6—10 месяцев. Такая выдержка снижает напряжения на 40—50%.
Антифрикционные ч у г у н ы применяют для изготовления подшипников скольжения, втулок и других деталей, работающих при трении о металл, чаще в присутствии смазки. Эти чугуны должны обеспечивать низкое трение (малый коэффициент трения), т. е. антифрикционность. Антифрикционные свойства чугуна определяются соотношением перлита и феррита в основе, а также количеством и формой графита. Антифрикционные чугуны изготовляют следующих марок : АЧС — 1 (3,2 — 3,6% С, 1,3-2,0% Si; 0,6-1,2% Мп; 0,15-0,3% Р; <0,12% S; 0,2-0,4%. Сг; 1,5-2,0% Си), АЧС-2(3,2 —3,8% С; 1,4-2,2% Si; 0,4-0,7% Мп; 0.15-0,4% Р; <0,12% S; 0,2-0,4% Сг; 0,2-0,4% Ni; 0,03-0,1% Ti; 0,3-0,5% Си) и АЧС-3(3,2—3,8% С; 1,7-2,6% Si; 0,4-0,7% Мп; 0,15-0,4% Р; <0,12% S; 0,03-0,1% Ti).
Детали, работающие в паре с закаленными или нормализованными стальными валами, изготовляют из перлитных серых чугунов АЧС-1 и АЧС-2; для' работы в паре с термически не обработанными валами применяют перлитно-ферритный чугун АЧС-3.
Перлитный чугун, содержащий повышенное количество фосфора (0,3—0,5%), используют для изготовления поршневых колец. Высокая износостойкость колец обеспечивается металлической основой, состоящей из тонкого перлита и равномерно распределенной фосфидной эвтектики при наличии изолированных выделений пластинчатого графита.
Для изготовления копиров выбрана сталь 38ХМФА. Назначьте и обоснуйте режим термической и химико – термической обработки, если высокая износостойкость объясняется при твердости поверхностного слоя 750 – 1000 HV. Опишите микроструктуру и свойства копиров после термической и химико – термической обработки.
Технология процесса азотирования.
Технологический процесс предусматривает несколько операций, приведенных ниже:
1. Предварительная термическая обработка заготовки. Эта операция состоит из закалки и высокого отпуска стали для получения повышенной прочности и вязкости в сердцевине изделия.
Закалку стали 38Х2МЮА выполняют с нагревом до 930 — 950°С с охлаждением в воде или в масле. Отпуск проводят при высокой температуре 600 —675°С, превышающей максимальную температуру последующего азотирования и обеспечивающей получение твердости, при которой сталь можно обрабатывать резанием. Структура стали после этот отпуска — сорбит.
2.Механическая обработка деталей, а также шлифование, которое придает окончательные размеры детали.
3.Защита участков, не подлежащих азотированию, нанесением, тонкого слоя (0,01 — 0,015 мм) олова электролитическим методом или жидкого стекла. Олово при температуре азотирования расплавляется на поверхности стали в виде тонкой не проницаемой для азота пленки.
3.Азотирование.
5.Окончательное шлифование или доводка изделия.
Дата добавления: 2018-04-05; просмотров: 2391; Мы поможем в написании вашей работы! |
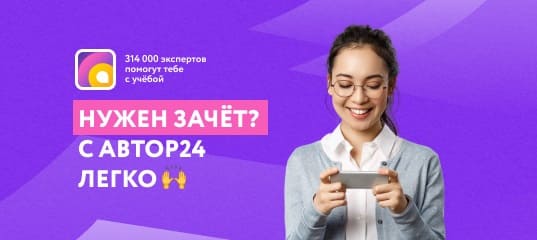
Мы поможем в написании ваших работ!