Закалка сплавов с переменной растворимостью
(без полиморфного превращения)
состоит из нагрева до температур растворения избыточной фазы и получения однородного твердого раствора с быстрым охлаждением для фиксации пересыщенного твердого раствора и получения структурно неустойчивого состояния.
Этот вид закалки характерен для сплавов алюминия с медью – дюралюминия.
![]() | ![]() |
«Алюминиевый» угол диаграммы состояния алюминий - медь | Схема изменения строения сплава алюминия, содержащего 4 % Сu (после закалки): а - исходное состояние; б - после закалки |
Дюралюминий содержит 3,8-4,8 % меди. В отожженном (исходном) состоянии структура – твердый раствор атомов меди в решетке алюминия и частицы CuAl2. Механические свойства такой структуры: предел прочности sВ=21 кг/мм2, относительное удлинение d=15 %.
Нагрев проводят выше температуры, соответствующей линии предельной растворимости для того, чтобы растворились частицы CuAl2 и атомы меди внедрились в решетку алюминия. При быстром охлаждении (при закалке) атомы меди не успевают «покинуть» решетку алюминия. Так как, судя по диаграмме, при комнатной температуре в алюминии может раствориться не более 0,5 % меди, а на самом деле там содержится
~4 %, то полученный раствор является очень пересыщенным. При закалке прочность несколько повышается, sВ=25 кг/мм2.
Такая структура термодинамически очень нестабильна, поэтому уже при комнатной температуре спустя несколько минут начинаются изменения, а сам процесс называется старением. При комнатной температуре – естественное старение, а при нагреве – искусственное старение.
|
|
При старении происходят процессы в три стадии:
I стадия – атомы меди в результате диффузии концентрируются в определенных местах кристаллической решетки, образуя зоны Гинье-Престона.
II стадия (при 100-200 °С) – концентрация меди в этих местах достигает 50 %, соответствующего соединению CuAl2. Образуется это соединение, решетка которого когерентно связана с решеткой твердого раствора (т.е. у них есть общие атомы).
При этих двух стадиях создаются высокие напряжения, в результате чего значительно повышаются твердость и прочность (sВ=42 кг/мм2).
III стадия – происходит разрыв когерентности, напряжения снимаются, твердость и прочность уменьшаются.
IV стадия – коагуляция (рост) частиц CuAl2, дальнейшее понижение свойств.
![]() | ![]() | |
I стадия | II стадия | III стадия |
Сочетание закалки со старением практически всегда предполагает получение более высокого уровня свойств (твердости, характеристик прочности, коэрцетивной силы, удельного электросопротивления и др.) по сравнению с отожженным состоянием.
|
|
Отпуск и старение – термическая обработка, в результате которой в предварительно закаленных сплавах происходят фазовые превращения, приближающие их структуру к равновесной. В большинстве сплавов после закалки получают пересыщенный твердый раствор (или смесь твердых растворов); в этом случае основной процесс, происходящий при отпуске или старении, - распад пересыщенного твердого раствора.
Термин "отпуск" используют обычно применительно к сталям и другим сплавам, испытывающим при закалке полиморфное превращение (двухфазные алюминиевые бронзы, некоторые сплавы на основе титана; термин "старение" – применительно к сплавам, не претерпевающим при закалке полиморфного превращения (сплавы на основе алюминия, аустенитные стали, никелевые сплавы и др.).
Поверхностная закалка
Поверхностная закалка состоит в нагреве поверхностного слоя стали выше Ас3 с последующим охлаждением для получения высокой твердости и прочности в поверхностном слое детали в сочетании с вязкой сердцевиной.
Для поверхностной закалки применяют обычно углеродистые стали, содержащие около 0.4 % С. Глубокая прокаливаемость при этом методе не используется, поэтому легированные стали обычно не применяют.
|
|
После закалки проводят низкий отпуск 200°С или самоотпуск.
После закалки и отпуска твердость стали на поверхности – 45-55 HRC, в сердцевине – 25-30 HRC.
Нагрев под закалку проводят:
– в расплавленных металлах или солях,
– пламенем газовых или кислород-ацетиленовых горелок,
– лазерным излучением,
– токами высокой частоты (ТВЧ).
Наиболее распространенным процессом поверхностной закалки в настоящее время является обработка токами высокой частоты (ТВЧ), основанная на скин-эффекте. Скин-эффект проявляется при взаимодействии электромагнитного поля с поверхностью электропроводящего материала и выражается в неравномерном распределении интенсивности (плотности) переменного электрического тока по сечению проводника.
При нагреве ТВЧ магнитный поток, создаваемый переменным током, проходящим по проводнику (индуктору), индуцирует вихревые токи в металле детали, помещенной внутри индуктора. Форма индуктора соответствует внешней форме изделия. Индуктор представляет собой медные трубки с циркулирующей внутри водой для охлаждения.
Скорость нагрева зависит от количества выделившегося тепла, пропорционально квадрату силы тока и сопротивлению металла.
|
|
На поверхности детали плотность тока значительно выше, чем в сердцевине, поэтому основное количество тепла выделяется в тонком поверхностном слое.
Глубина проникновения тока в металл зависит от свойств нагреваемого металла и обратно пропорциональна квадратному корню из частоты тока:
g – толщина слоя, м; r – электросопротивление, Ом×м;
m – магнитная проницаемость, Г/м; ¦ – частота тока, Гц.
Чем больше частота тока, тем тоньше получается закаленный слой.
Обычно применяют:
Машинные генераторы с частотой 500-15000 Гц для получения закаленного слоя толщиной 2-10 мм;
Ламповые генераторы с частотой 106 Гц для получения закаленного слоя толщиной от десятых долей мм до 2мм.
После нагрева в индукторе деталь охлаждают с помощью специального охлаждающего устройства. Через имеющиеся в нем отверстия на поверхность детали разбрызгивается охлаждающая жидкость.
![]() | Структура закаленного слоя – мартенсит; переходной зоны – мартенсит и феррит сердцевины – исходная (т.к. глубинные слои нагреваются до температур ниже критических и при охлаждении не упрочняются) |
Для повышения прочности сердцевины перед поверхностной закалкой деталь иногда подвергают нормализации или улучшению.
Преимущества обработки ТВЧ:
- регулируемая глубина закаленного слоя;
- высокая производительность и возможность автоматизации;
- отсутствие обезуглероживания и окалинообразования;
- минимальное коробление детали.
Недостатки:
- высокая стоимость индуктора (индивидуальная для каждой детали) и, следовательно, малая применимость ТВЧ к условиям единичного производства.
2) Термомеханическая обработка (ТМО) стали
ТМО заключается в пластическом деформировании аустенита с последующей закалкой на мартенсит и низким отпуском.
Причиной упрочнения при ТМО является то, что из предварительно деформированного аустенитного зерна образуются более мелкие пластины мартенсита. При дроблении зерна аустенита создается блочная структура, которая фиксируется при закалке.
При последующем отпуске до 200°С происходит выделение углерода из мартенсита в виде дисперсных карбидов.
В результате ТМО достигается высокая прочность при достаточной пластичности и вязкости.
В зависимости от температуры, при которой деформируется аустенит, различают:
- ВТМО – высокотемпературную термомеханическую обработку;
- НТМО - низкотемпературную термомеханическую обработку.
При ВТМО по сравнению с обычной термообработкой прочность повышается примерно на 40 % при одновременном увеличении характеристик пластичности в 2 раза. Возрастает сопротивление усталости, увеличивается ударная вязкость, уменьшается склонность к образованию трещин и порог хладноломкости.
При НТМО достигается еще большее упрочнение, но ее проведение более сложно по сравнению с ВТМО.
Дата добавления: 2018-04-05; просмотров: 275; Мы поможем в написании вашей работы! |
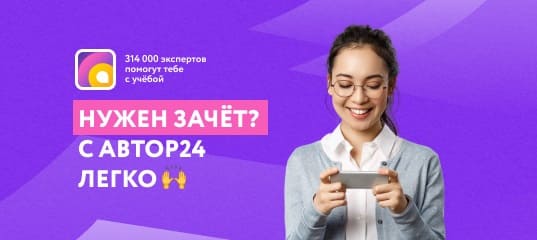
Мы поможем в написании ваших работ!