Автоматическая дуговая сварка
Основными характеристиками производительности автоматической дуговой сварки являются: коэффициент наплавки, коэффициент расплавления и коэффициент потерь.
Коэффициент наплавки численно выражает количество металла в граммах, наплавленного в течение одного часа силой тока в один ампер,
, г/А·ч, (10)
где Qn – количество наплавленного металла в граммах;
I – сила тока в амперах;
t – время в часах.
Величина an зависит от материала стержня, рода и полярности тока.
Коэффициент расплавления – количество металла в граммах, расплавляемого в течение одного часа силой тока в один ампер,
, г/А·ч, (11)
где Qr – количество расплавленного металла в граммах.
Коэффициент расплавления так же, как и коэффициент наплавки, определяется опытным путем и зависит от материала стержня, а также от рода и полярности тока. Расплавленный металл электрода не весь полезно переносится в шов.
Часть расплавленного металла в процессе горения дуги теряется на разбрызгивание, испарение и угар.
Чем больше разница в ar и an, тем больше потеря металла. Поэтому производительность сварки рассчитывают исходя из an, а не ar.
ar = (1,1 – 1,3)an. (12)
Потери характеризуются коэффициентом ψ, который определяется в процентах по формуле:
. (13)
Производительность автоматической сварки (дуговой) под слоем флюса намного выше производительности ручной дуговой сварки.
|
|
При сварке под флюсом дуга горит в газовом пузыре, ограниченном снизу жидкой сварочной ванной, а сверху пленкой расплавленного флюса. Потери металла на разбрызгивание практически отсутствуют; возможно, применять при сварке большие плотности тока. Уменьшаются также потери тепла в окружающую атмосферу, и большая часть тепла полезно используется на расплавление электродной проволоки, основного металла и флюса.
Так как потери металла при сварке под флюсом составляют
не более 2%, то можно считать, что коэффициент наплавки an при автоматической сварке под слоем флюса равен коэффициенту расплавления ar.
Описание установки
Перед выполнением работы студенты должны ознакомиться с автоматической сваркой под слоем флюса на автоматах АДС – 500 и АДС – 1000.
При автоматической сварке механизированы следующие основные процессы: зажигание дуги, подача электродной проволоки к дуге по мере ее расплавления, поддерживание постоянства длины дуги и перемещение дуги вдоль свариваемого шва.
Первые три операции выполняются специальным механизмом, называемым сварочной головкой.
Перемещение дуги вдоль наплавленного валика осуществляется либо установкой сварочной головки на специальную самодвижущуюся тележку (сварочные тракторы), либо перемещением головки при помощи специального механизма по направляющим (подвижные сварочные головки), либо перемещением изделия относительно неподвижной сварочной головки.
|
|
В зависимости от назначения и условий работы сварочные головки оборудуются рядом вспомогательных устройств, например механизмом для подачи и отсоса флюса, направляющими роликами для выпрямления проволоки, корректировочным механизмом для правильного ведения дуги (конца проволоки) относительно сварного шва.
Принципиальная схема автоматической сварочной головки дана на
рисунке 2.2
Рисунок 2.2 – Принципиальная схема автоматической сварочной головки: 1 – электродвигатель; 2 – редуктор; 3 – ведущий ролик; 4 – ведомый ролик; 5 – сварочная проволока; 6 – кассета; 7 – мундштук
Электродвигатель 1 через редуктор 2 передает вращение ролику 3. Сварочная проволока 5 сматывается с барабана, помещенного в кассете 6, зажимается между ведущим роликом 3 и ведомым роликом 4.
При вращении роликов проволока получает поступательное движение к изделию через мундштук 7, к которому подводится сварочный ток.
|
|
Автоматическая сварочная головка должна обеспечивать постоянство режима сварки, то есть поддерживать в процессе сварки неизменяемые по величине: сварочный ток и напряжение.
При заданном токе для постоянства напряжения необходимо поддерживать неизменной длину дуги ld = const. Длина дуги будет постоянной, если скорость подачи электродной проволоки Vel будет равна скорости ее плавления Vpl.
Равенство Vel=Vpl в процессе сварки практически нарушается по разным причинам (колебание напряжения в питающей сети, пробуксовывание проволоки между роликами механизма подачи).
Автоматическая головка при нарушении равенства должна быстро и точно его восстанавливать.
В зависимости от способа поддержания постоянства длины дуги сварочные головки делятся на два типа:
1. Головки с постоянной скоростью подачи проволоки.
2. Головки с переменной скоростью подачи проволоки, регулируемой в зависимости от напряжения на дуге.
В головках с постоянной скоростью подачи проволоки поддержание постоянной длины дуги происходит автоматически, за счет явления «саморегулирования» дуги. Это явление сводится, в основном, к следующему: так как скорость плавления электродной проволоки тем больше, чем больше сварочный ток, то при укорочении дуги ток должен возрастать, а скорость плавления проволоки соответственно увеличиваться и, наоборот, при удлинении дуги ток должен падать, а скорость плавления уменьшаться.
|
|
Все это должно приводить к восстановлению исходной длины дуги.
В лабораторной работе используется автомат-трактор АДС – 1000
(рисунок 2.3) с переменной скоростью подачи проволоки, регулируемой в зависимости от напряжения на дуге. Автомат АДС – 1000 состоит из головки, укрепленной на передвигающейся тележке, сварочного трансформатора и распределительного устройства.
Сварочные автоматы, на которых головка крепится на тележке, передвигающейся вдоль изделия, называются сварочными тракторами.
Основные части автомата-трактора АДС – 1000: самоходная тележка 1, колонка 2, пульт управления 3, кассета для электродной проволоки 4,
коромысло 5, бункер для флюса 6, сварочная головка 7 с мундштуком 8 и указателем 9.
Трактор может перемешаться по специальным направляющим в виде рельсов или непосредственно по изделию и производить сварку соединений различных типов.
|

Рисунок 2.3 – Общий вид автомата-трактора АДС – 1000
3 Оборудование и материалы
3.1 Ручная дуговая электросварка
1. Пластины из конструкционной стали (200×50×10 мм),
2. Электроды типа Э42АФ, Э46Т марок УОНИ – 13/45 и АНО – 4 или других марок.
3 Оборудование, приспособления, инструмент
1. Сварочный пост переменного или постоянного тока.
2. Штангенциркуль.
3. Линейка.
4. Весы с разновесом.
5. Секундомер.
6. Емкость с водой.
3.2 Автоматическая дуговая сварка
1. Сварочный автомат АДС – 500 или АДС – 1000.
2. Технические весы с разновесом.
3. Металлически щетка.
4. Секундомер.
5. Металлическая линейка.
6. Электродная проволока марки, диаметром мм.
7. Пластины из низкоуглеродистой стали (С245 – С255) размером 60×150×10 мм.
4 Указания по технике безопасности
К выполнению лабораторных работ допускаются только студенты, прошедшие инструктаж по технике безопасности. Зона выполнения лабораторных работ должна быть изолирована от учебной зоны аудитории. Нахождение посторонних лиц в рабочей зоне запрещается.
Все контактные соединения должны быть очищены и проверены на плотность затяжки; измерительные приборы должны быть исправлены. Пользование поврежденными предметами не допускается.
При перерывах в работе, а также после окончания работы, все приборы необходимо отключить. Запрещается оставлять без надзора электроприборы, подключенные к сети.
Запрещается включать без разрешения учебного мастера или преподавателя электросварочное оборудование.
Не смотреть на электрическую дугу незащищенными глазами.
При выполнении работ пользоваться щитком или маской, рукавицами, фартуком.
После выполнения сварочных работ убрать рабочее место.
При проведении работ должно быть смешанное освещение, то есть естественное и искусственное, что обеспечивает освещенность зоны работ в соответствии с требованиями норм.
5 Задания (указания по порядку выполнения работы)
5.1 Ручная дуговая электросварка
1. Для каждой марки и типа электродов определяют вес стержня электрода:
, (14)
где: d – диаметр металлического стержня, см;
γ – плотность металла, 7,8 г/см3;
l – длина стержня электрода, см.
2. Для каждой марки электродов подготавливают по 2 пластины стали под наплавки на ней валика. (Очистить от ржавчины и других загрязнений).
3. Взвешивают пластины на весах с точностью до 1 г.
4. В зависимости от de подбирается сила сварочного тока на дополнительной пластинке.
Ориентировочно Isv рассчитывается по формуле
Isv = (40 – 50) de, (15)
где: 40 – 50 – примерная сила тока на каждый мм диаметра электрода.
Действительную величину тока отмечают по амперметру. Величина тока в процессе наплавки может изменяться, поэтому для расчета необходимо определить среднее значение тока, полученное по 3 измерениям.
5. По выбранным режимам наплавить на пластины валики длиной
50 – 60 мм разными марками электродов.
На постоянном токе с различной полярностью (+; –).
При наплавке фиксируются величина тока (А) и время горения дуги
(в секундах).
6. После наплавки охладить пластины с наплавленным металлом, атакже огарки электродов. Очистить валики и пластины от шлака и брызг, высушить.
7. Взвесить пластины и огарки.
8. По формулам вычислить коэффициенты:
8.1 наплавки
,г/А·ч, (16)
где Qn=Ppl2-Рpl1, А,
Рpl1 – вес пластины до наплавки, г;
Ppl2 – вес пластины после наплавки, г;
t – время в секундах.
8.2 расплавление
, (17)
где Qr=(Qel1- Qоg)
Qel1 – вес электрода до сварки, г;
Qоg – вес огарка после сварки, г.
log – длина огарка, см.
8.3 потери
. (18)
Данные измерений и расчетов заносятся в таблицу 2.1.
5.2 Автоматическая дуговая сварка
Порядок выполнения работы следующий:
1. Взвесить пластины, на которые будет производиться наплавка;
2. В процессе наплавки замерить сварочный ток, напряжение на дуге, время горения дуги.
3. После наплавки зачистить валики от шлака и брызг и взвесить пластины.
4. Определить расход проволоки и ее вес.
Данные определений занести в таблицу 2.2. Произвести вычисления коэффициента расплавления ar по формуле (11) и коэффициента потерь ψ по формуле (13).
6 Содержание отчета
6.1 Ручная дуговая электросварка
1. Краткие сведения из теории и методика проведения работы.
2. Таблица измерений и результаты расчетов.
3. Выводы по работе.
Дата добавления: 2018-04-05; просмотров: 345; Мы поможем в написании вашей работы! |
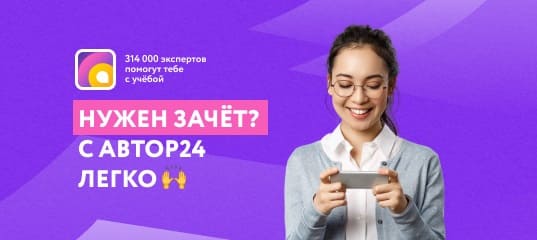
Мы поможем в написании ваших работ!