Теория и факторы, влияющие на критерии циклической прочности
Характер усталостного разрушения существенно зависит от уровня циклически изменяющихся напряжений. Так, при максимальных напряжениях цикла, меньших предела упругости материала, усталостное разрушение имеет хрупкий характер и происходит вследствие накопления повреждений и развития магистральной трещины без заметной пластической деформации всей детали. В связи с различными физическими процессами разрушения материала при высоких и низких уровнях максимальных напряжений цикла, принято различать два вида усталости – многоцикловая, малоцикловая. Многоцикловая усталость - усталость материала, при которой усталостное повреждение или разрушение происходит в основном при упругом деформировании. Малоцикловая усталость - усталость материала, при которой усталостное повреждение или разрушение происходит при упругопластическом деформировании. Характер разрушения в области малоцикловой усталости существенно зависит от способности материала к накоплению пластических деформаций при циклическомнагружении. Интенсивность процесса накопления пластических деформаций при циклическомнагружении зависит также от с Малоцикловое разрушение может быть вызвано не только действием переменных нагрузок, но и повторными тепловыми воздействиями. Если температурные расширения в детали стеснены опорными устройствами или окружающими частями детали с неизменной температурой, то в такой детали возникнут температурные напряжения, которые могут достигнуть предела текучести. В результате появятся пластические деформации, скорости нагружения и разгрузки и времени выдержки. Циклическая прочность зависит от перегрузок, которым деталь подвергается перед нагружением. Циклическая прочность зависит от большого числа факторов, из которых решающее значение имеют структура и напряженное состояние поверхностного слоя, качество поверхности и воздействие коррозионной среды. Наличие на поверхности остаточных напряжений сжатия затрудняет образование и развитие трещин усталости и, как следствие, способствует увеличению предела выносливости.
|
|
Лекция 12
Деградационные процессы оборудования и материалов, виды предельных состояний
При эксплуатации технологического оборудования в той или иной мере, в зависимости от условий и режимов работы, происходит деградация конструкционных материалов. Деградация — явление, наблюдающееся в материалах с течением длительного времени и выражающееся в соответствующем снижении способности конструкции сопротивляться воздействию на нее различных нагрузок и, соответственно, снижающее остаточный ресурс оборудования.
|
|
Диагностирование технического состояния оборудования и прогноз его изменения при дальнейшей эксплуатации осуществляется на основе анализа деградационных процессов и выявления определяющих параметров технического состояния. Определяющие параметры технического состояния (ПТС) — это параметры, изменение которых в отдельности или в некоторой совокупности приводит оборудование в неработоспособное состояние.
В нефте- и газодобывающей и перерабатывающей промышленности выделяют следующие деградационные процессы, приводящие к потере работоспособности технологического оборудования:
• изменение геометрии конструкции или отдельных ее элементов;
• поверхностное изнашивание или коррозийное повреждение;
• образование и развитие макродефектности;
• деградация (старение) механических свойств материалов.
В зависимости от действующего механизма деградационного процесса различают следующие виды предельных состояний:
• вязкое, усталостное или кратковременное хрупкое разрушение элемента или всей конструкции;
• предельная пластическая деформация металлоконструкции, обусловленная прогибом или нарушением устойчивости несущих элементов, образованием «пластических шарниров» или явлениями ползучести, определяющая необходимость прекращения ее эксплуатации;
|
|
• разгерметизация или течь конструкции.
Определяющими параметрами, приводящими к перечисленным видам предельных состояний, являются напряженно-деформированное состояние элементов конструкции, механические свойства конструкционных материалов, степень поражения коррозией, количество и размеры повреждений и дефектов.
Процессы зарождения и развития макродефектности в элементах конструкций определяются следующими факторами:
• величиной эксплуатационных нагрузок;
• величиной остаточных напряжений после сварки;
• химическим составом и структурой материала.
Вклад химсостава и структуры в образование макродефектности особенно весом для таких опасных явлений, как коррозийное растрескивание под напряжением, стресс-коррозия, сульфидное растрескивание и т.д.
Наличие крупнозернистой и неоднородной структуры также способствует возникновению и развитию межзеренного разрушения и образованию трещин. Данный эффект в большей степени встречается в околошовной зоне сварных соединений — зоне термического влияния (ЗТВ). Практика технического диагностирования показывает, что в элементах конструкций, имеющих крупнозернистую структуру (с размером ферритных зерен 100...300 мкм и более), доля межзеренного разрушения достигает 35...40%, что облегчает зарождение и развитие трещин под воздействием остаточных сварочных, а также эксплуатационных напряжений.
|
|
Деградация (старение) материалов, включая и конструкционные стали, с течением времени проявляется в ухудшении механических свойств, определяющихся в первую очередь их химическим составом и микроструктурой, и обусловлена термодинамической неравновесностью исходного состояния материала и постепенным приближением его структуры к равновесному состоянию в условиях диффузной подвижности атомов.
Анализ эксплуатационных факторов, действующих на металл, позволяет выделить следующие процессы, приводящие его к старению:
• разупрочнение — проявляется в том, что прочностные характеристики металла (временное сопротивление или условный предел текучести) отличаются от исходных (нормативных) более чем на 5 % в меньшую сторону. Может быть следствием длительного пребывания металла при высокой температуре, например во время пожара;
• циклическое воздействие нагрузок — вызывает микропластические деформации в зонах концентрации напряжений в результате накопления дислокаций, ускоряющих развитие повреждаемости металла;
• охрупчивание — является наиболее опасным следствием изменения физико-механических свойств материала (применительно к сталям, имеющим объемно-центрированную кубическую решетку: углеродистым и малолегированным). Охрупчивание сдвигает область хрупкого разрушения в область положительных температур, резко снижает трещиностойкость и приводит к внезапному разрушению конструкции.
Изменение механических свойств, обусловленных развитием процессов охрупчивания, выражается, с одной стороны, в увеличении твердости материала и предела его текучести, с другой — в снижении вязкопластических показателей, показателей ударной вязкости и трещиностойкости.
Различают технологические и эксплуатационные факторы охрупчивания сталей. Первые возникают в процессе изготовления, транспортировки и монтажа конструкции, вторые — в процессе ее эксплуатации.
К эксплуатационным факторам относят все виды механических, тепловых, коррозийных и химических воздействий на металл в период эксплуатации конструкции. К их числу относят:
• длительное воздействие повышенных температур (250...500 °С), приводящих к укрупнению зерна феррита и развитию обратной отпускной хрупкости;
• появление закалочных крупнозернистых структур в зоне сварных швов при нарушении технологии сварки в процессе ремонта (попадание влаги в сварочную ванну) или при ускоренном охлаждении сварного соединения (например, при сварке в зимний период без предварительного подогрева свариваемого металла);
• наводороживание металла сварных швов (при попадании влаги в сварочную ванну или при использовании непросушенных электродов и сварочных материалов);
• коррозийное растрескивание под напряжением, обусловленное воздействием механических нагрузок и электрохимических процессов коррозии;
• сезонную подвижку фундаментов опор машины и примыкающих трубопроводов, кратковременные перегрузки в период пуска или испытаний под нагрузкой и др.
Дата добавления: 2018-04-05; просмотров: 339; Мы поможем в написании вашей работы! |
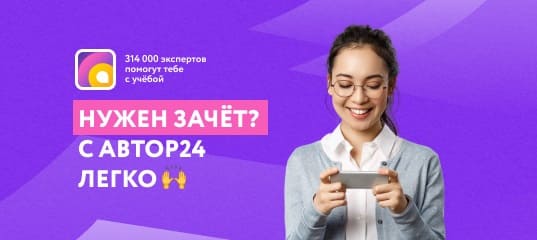
Мы поможем в написании ваших работ!