УЧЕБНО-ИССЛЕДОВАТЕЛЬСКАЯ ЛАБОРАТОРНАЯ РАБОТА №1
ФЕДЕРАЛЬНОЕ АГЕНТСТВО ПО ОБРАЗОВАНИЮ
ГОСУДАРСТВЕННОЕ ОБРАЗОВАТЕЛЬНОЕ УЧРЕЖДЕНИЕ
ВЫСШЕГО ПРОФЕССИОНАЛЬНОГО ОБРАЗОВАНИЯ
ДОНСКОЙ ГОСУДАРСТВЕННЫЙ ТЕХНИЧЕСКИЙ УНИВЕРСИТЕТ
Кафедра «Технология машиностроения»
Учебно-исследовательские
лабораторные работы по курсу
«Физико-технологические основы
методов обработки»
Ростов-на-Дону 2008
Составители: к.т.н., доцент Т.Н. Рысева
д.т.н., профессор М.Е. Попов
к.т.н., доцент А.А. Жуков
к.т.н., доцент Ю.П. Анкудимов
доцент А.А. Тихонов
Учебно-исследовательские лабораторные работы по курсу «Физико-технологические основы методов обработки» - Ростов н/Д: Издательский центр ДГТУ. 2008. - 44 с.
Настоящие методические указания к лабораторным работам по курсу «Физико-технологические основы методов обработки» предназначены для студентов инженерных специальностей очной и заочной форм обучения.
Печатается по решению методической комиссии факультета "Технология машиностроения"
Рецензент д.т.н., профессор А.П. Бабичев
Научный редактор д.т.н., профессор М.А. Тамаркин
ã Издательский центр ДГТУ, 2008
ДОСТИЖЕНИЕ ТОЧНОСТИ ИЗГОТОВЛЕНИЯ ДЕТАЛИ
|
|
Для обеспечения заданной точности деталь обрабатывается на металлорежущих станках. При обработке деталь включается в размерные цепи системы СПИД в качестве замыкающего звена. Процесс достижения точности, при этом, состоит из трех этапов: установка заготовки на станке, статическая и динамическая настройка системы СПИД. Соответственно, погрешность обработки детали складывается из погрешностей установки, статической и динамической настройки:
Эти погрешности состоят из большого количества составляющих, которые можно разделить на три группы: случайные, систематические постоянные и систематические переменные. Случайными называются такие погрешности, момент появления и степень воздействия которых на процесс получения размера предсказать невозможно. Систематические постоянные погрешности остаются постоянными в течение времени обработки всей партии деталей. Систематические переменные погрешности изменяются по мере обработки деталей партии в соответствии с законами, которые могут быть теоретически или экспериментально выявлены. Если при образовании размера доминируют случайные погрешности, то кривая распределения размеров в партии получается близкой к кривой Гаусса (нормальный закон распределения). При появлении в процессе обработки партии деталей постоянных систематических погрешностей кривая нормального распределения искажается и приобретает многовершинный характер. При одновременном действии случайных и систематических переменных погрешностей - искажается и становится либо плосковершинной, либо асимметричной. Наличие таких связей позволяет по форме кривых распределения анализировать структуру погрешностей, действующих в конкретном исследуемом случае.
|
|
Установкой называется процесс базирования и закрепления заготовки. При этом образуется размер установки Ау, равный расстоянию между технологической базой детали (ТБ) и установочными элементами (УЭ) приспособления. В ряде случаев номинальных размер Ау может быть равным нулю. Отклонение фактически достигнутого положения заготовки от требуемого называется погрешностью установки. Погрешность установки состоит из погрешности базирования и погрешности закрепления заготовки.
Погрешность базирования складывается из нескольких составляющих:
Погрешности технологических баз деталей образуются в процессе обработки поверхности детали, выбранной в качестве ТБ, и носят случайный характер.
|
|
Погрешности установочных элементов приспособления образуются в процессе изготовления приспособления (систематическая постоянная погрешность), а также в результате износа УЭ при эксплуатации (систематическая переменная погрешность).
Рис. 1 - Схема образования размера детали Ад при обработке на станке
Погрешность, вызванная неопределенностью базирования, заключается в том, что детали партии при неизменной схеме базирования занимают различное положение относительно УЭ приспособления из-за попадания стружки на УЭ, а также из-за наличия зазоров между базирующими отверстиями и жесткими пальцами, оправками и т.д. Погрешность случайная.
Погрешность закрепления складывается из следующих составляющих:
Объемные деформации детали и приспособления под влиянием сил закрепления. На данную погрешность оказывают влияние как систематические факторы (например, жесткость элементов системы СПИД), так и случайные (например, выборка зазоров в стыках деталей приспособления);
Контактные деформации ТБ детали и УЭ приспособления. На данную погрешность оказывают влияние как систематические факторы (например, упругость материала детали и УЭ), так и случайные (например, смятие шероховатостей ТБ детали).
|
|
Случайная смена баз под влиянием сил закрепления может иметь место только при существенных ошибках при конструировании приспособления, поэтому на стадии проектирования должны быть приняты меры к недопущению этой погрешности.
Статической настройкой системы СПИД называется подведение без рабочих нагрузок исполнительных поверхностей (ИП) инструмента в такое положение относительно УЭ приспособления, которое было установлено при наладке (первоначальной настройке) системы СПИД. Расстояние между ИП и УЭ является размером статической настройки Асн. Статическая настройка системы СПИД повторяется при обработке деталей и в большинстве случаев производится относительно направляющих станка и описывается размерной цепью «В» (рис.1).
Погрешность статической настройки складывается из следующих составляющих:
Погрешность наладки системы СПИД – это погрешность первоначальной настройки, которая выполняется один раз перед началом обработки партии деталей. При применении приспособлений с кондукторными втулками функция наладки выполняется изготовлением приспособления. Погрешность систематическая постоянная, образуется в сечении I-I и остается постоянной по величине как для всех сечений данной детали, так и для всех деталей партии.
Погрешность процесса статической настройки. Статическая настройка повторяется столько раз, сколько деталей надо обработать, и может выполняться по лимбу, по упору, по индикатору, по копиру, с помощью автоматических остановов, с помощью кондукторных втулок приспособления. В последнем случае точность статической настройки повышается, так как она выполняется непосредственно относительно УЭ. Погрешность образуется в сечении I-I, остается постоянной о величине для всех сечений данной детали, но случайно изменяется для деталей партии. Имеет наибольший удельный вес в погрешности статической настройки, так как остальные составляющие являются систематическими и лучше поддаются управлению.
Смещение в направлении получаемого размера ИП инструмента из-за накопленных погрешностей. Такими погрешностями являются размерный износ инструмента и температурные деформации системы СПИД, накопленные за время предыдущей обработки, то есть к моменту выполнения статической настройки на данную деталь. Погрешность систематическая переменная, образуется в сечении I-I, остается постоянной для всех сечений данной детали, но закономерно изменяется для деталей партии. Может быть уменьшена путем своевременного выполнения подналадки.
Смещение в направлении получаемого размера УЭ приспособления (ИП инструмента) при перемещении приспособления (инструмента) в направлении подачи. Погрешность является переменной в пределах обработки одной детали, так как ее величина различна для каждого I–го сечения. Однако в партии деталей величина этой погрешности и характер изменения остаются неизменными, так как вызываются такими факторами, как погрешность установки приспособления и инструмента на станке, деформации и износ направляющих и т.д.
Динамической настройкой системы СПИД называется выполнение обработки со всеми присущими ей явлениями.
Силы резания, возникающие при этом, вызывают упругое отжатие детали и инструмента на величину Адн, которую называют размером динамической настройки. При номинальных значениях твердости материала, величины припуска, нормальной заточке инструмента и т.д. образуется номинальное значение Адн. Изменения Адн в процессе обработки представляют погрешность динамической настройки системы СПИД.
Погрешность динамической настройки системы СПИД складывается из следующих составляющих:
Размерный износ инструмента. Систематическая переменная погрешность, влияющая на размеры данной детали. Особенностью размерного износа является то, что он не исчезает при прерывании процесса резания. И, таким образом, накопленный за время обработки «n» деталей размерный износ превращается в погрешность статической настройки для (n+1) детали, оказывая таким образом влияние и на размеры деталей в партии.
Изменения температурных деформаций системы СПИД. Систематическая переменная погрешность, аналогично размерному износу, накапливается в процессе обработки и превращается в погрешность статической настройки для (n+1) детали.
Изменение упругих деформаций системы СПИД. Погрешность, вызываемая как случайными причинами - изменением усилия резания из-за неравномерной твердости материала заготовки и неравномерного припуска, так и систематическими - неравномерной жесткостью системы СПИД и изменением усилия резания из-за затупления инструмента.
Деформация детали в результате перераспределения внутренних напряжений. Случайная погрешность, в большой степени зависит от величины снимаемого на черновых операциях припуска.
Погрешности, вызываемые вибрациями системы СПИД, обусловлены большим количеством причин, в комплексе придающих случайный характер данной погрешности.
УЧЕБНО-ИССЛЕДОВАТЕЛЬСКАЯ ЛАБОРАТОРНАЯ РАБОТА №1
ИССЛЕДОВАНИЕ ПРОЦЕССА ДОСТИЖЕНИЯ ЗАДАННОЙ ТОЧНОСТИ ДЕТАЛИ ПУТЕМ ЕЕ ПОСЛЕДОВАТЕЛЬНОГО УТОЧНЕНИЯ
1.1. Цель работы
Изучение явления копирования погрешностей при обработке деталей на металлорежущих станках.
Исследование возможностей обеспечения заданной точности детали путем ее последовательного уточнения.
1.2. Задачи работы
Расчет возможности обеспечения заданной точности детали в один и два прохода.
Экспериментальная проверка теоретических выводов.
Оценка вариантов обеспечения точности по трудоемкости.
1.3. Подготовка к проведению работы
Назначение механической обработки состоит в том, чтобы превращать неточные заготовки в гораздо более точные, соответствующие техническим условиям, детали. При этом в большинстве случаев бывает невозможно обеспечить заданную точность детали за один проход, так как в процессе обработки действует большое количество факторов, вызывающих погрешность обработки. Один из таких факторов носит название копирования погрешностей. Сущность копирования заключается в том, что погрешность заготовки копируется (повторяется) на детали в виде одноименной погрешности меньшей величины. Например, при точении из конусной заготовки получается конусная деталь, из бочкообразной заготовки – бочкообразная деталь и т.д.
Объясняется это тем, что погрешность заготовки Δзаг. обуславливает неравномерность припуска Z и соответственно изменение глубины резания
t при обработке. Изменение глубины резания обусловливает изменение усилия резания
Ру, а изменение усилия резания, в свою очередь, вызывает изменение упругих деформаций в системе СПИД -
, которые непосредственно превращаются в погрешность детали
дет (составляющая погрешность динамической настройки).
Следовательно, копирование погрешностей происходит по следующей схеме:
Отношение называется уточнением. Величина уточнения, обусловленная только копированием, может быть рассчитана аналитически, исходя из параметров процесса обработки и жесткости системы СПИД:
(1)
где у1 и у2 - величины упругих отжатий соответственно при первом и втором положениях инструмента вдоль обрабатываемой детали;
Ру1 и Ру2 - величина радиальной составляющей силы резания соответственно при первом и втором положениях инструмента;
jСПИД - жесткость системы СПИД;
Сру - коэффициент, величина которого зависит от условий обработки (наличие или отсутствие смазочно-охлаждающей жидкости, величины углов резания, материал режущей части инструмента и т.д.);
S - подача инструмента;
НВ - твердость материала заготовки по Бринелю;
t1 и t2 - величина глубины резания соответственно при первом и втором положениях инструмента;
у,n,x - показатели степени.
Формула (1) справедлива для случая, когда показатель степени х при глубине резания равен 1. Из (1) может быть получено выражение для уточнения:
Фактическое уточнение обычно бывает меньше, чем вычисленное по этой формуле, так как в процессе обработки кроме копирования действует еще много других факторов и кроме изменения упругих деформаций имеют место другие погрешности.
Если выполняется «m» последовательных переходов, то общее уточнение равно произведению уточнений:
(2)
В конкретном случае, когда можно считать jспид = const для всех переходов, заданное общее уточнение можно получать, варьируя подачу и количество переходов. Уменьшая подачу и увеличивая таким образом уточнение
и можно уменьшать количество переходов и наоборот.
Для различных совокупностей подачи и жесткости системы СПИД составлена таблица 1 возможных уточнений .Используя eё данные с учетом поправочного коэффициента из таблицы 2, можно расчетным путем компоновать варианты обеспечения заданного
.
Окончательный выбор наилучшего варианта обеспечения заданной точности может быть сделан по производительности обработки. При этом надо стремиться к тому, чтобы чистовые проходы выполнялись с меньшей подачей.
Таблица 1
Уточнение в зависимости от жесткости системы jСПИД и подачи S при обработке стали (чугуна) с
Па (HB= 220) в один проход
(при ).
jСПИД, Н/мм | S, мм/рад (мм/об) | |||||
0,016 | 0,024 | 0,032 | 0,048 | 0,064 | 0,080 | |
(0,10) | (0,15) | (0,20) | (0,30) | (0,40) | (0,50) | |
1000 | 7,4 | 5,5 | 4,4 | 3,2 | 2,6 | 2,2 |
2000 | 14,8 | 10,9 | 8,8 | 6,4 | 5,2 | 4,4 |
3000 | 22,2 | 16,4 | 13,2 | 9,6 | 7,8 | 6,6 |
4000 | 29,6 | 21,8 | 17,6 | 12,8 | 10,4 | 8,8 |
5000 | 37,0 | 27,3 | 22,0 | 16,0 | 13,0 | 11,0 |
10000 | 74,0 | 54,6 | 44,0 | 32,0 | 26,0 | 22,0 |
15000 | 111,0 | 81,9 | 66,0 | 48,0 | 39,0 | 33,0 |
20000 | 148,0 | 109,2 | 88,0 | 64,0 | 52,0 | 44,0 |
25000 | 185,0 | 136,5 | 110,0 | 80,0 | 65,0 | 55,0 |
50000 | 370,0 | 273,0 | 220,0 | 160,0 | 130,0 | 110,0 |
100000 | 740,0 | 546,0 | 440,0 | 320,0 | 260,0 | 220,0 |
Таблица 2
Коэффициент , учитывающий механические свойства
обрабатываемых материалов
НВ | σв, Па | ![]() |
162 | 55·107 | 1,22 |
176 | 60·107 | 1,17 |
194 | 65·107 | 1,12 |
206 | 70·107 | 1,06 |
220 | 75·107 | 1,00 |
235 | 80·107 | 0,95 |
250 | 85·107 | 0,90 |
370 | 125·107 | 0,848 |
Пользуясь этими таблицами, можно определить ожидаемое уточнение для каждого прохода
(3)
1.4. Материальное обеспечение работы
1.4.1. Токарно-винторезный станок.
1.4.2. Микрометр с ценой деления 0,01.мм.
1.4.3. Штангенциркуль.
1.4.4. Заготовка.
1.4.5. Резец токарный проходной (рис. 2)
Рис. 2 - Параметры токарного проходного резца
1.5. Методика проведения исследования
1.5.1. Получить у преподавателя задание: величину вылета заготовки l, погрешность заготовки (рекомендуется
), допускаемую погрешность полностью обработанной детали (рекомендуется
).
1.5.2. Найти величину заданного общего уточнения:
,
где К = (2 3) - коэффициент запаса, учитывавший влияние остальных факторов процесса обработки (кроме копирования погрешностей).
1.5.3. Вычислить жесткость системы СПИД по формуле:
,
где jпб - жесткость передней бабки станка, Н/мм;
jсуп - жесткость суппорта станка, Н/мм;
jдет- жесткость детали, Н/мм.
Жесткость детали прутка при установке в патроне
,
где Е = 2,1·1011 Па - модуль упругости стали;
- момент инерции сечения заготовки;
l - свободный вылет заготовки, мм.
Значения жесткости передней бабки и суппорта станка получить у преподавателя.
1.5.4. Используя табл.1 и 2, подобрать подачи для обработки заготовки в один и два прохода. Учитывая формулу (2), следует стремиться к тому, чтобы
.
Если это неравенство выдержать невозможно, то выбрать такие подачи, которые обеспечивают наибольшие возможные для данной системы СПИД уточнения.
1.5.5. Выбранные подачи и ожидаемые уточнения, рассчитанные по формуле (3), занести в отчет.
1.5.6. В патроне токарного станка закрепить заготовку с заданным вылетом l. Проточить заготовку с небольшой глубиной резания для удаления биения.
1.5.7. На свободном конце заготовки проточить уступ длиной 5 10мм (рис.3), имитирующий погрешность заготовка
, заданную преподавателем.
Рис. 3 - Схема обработки заготовки с неравномерным припуском
1.5.8. Обработать заготовку с выбранной подачей в один проход. Обе ступени протачивать с одной установки резца при скорости резания 30÷40 м/мин.
Глубину резания для меньшего диаметра принять 0,5 мм.
1.5.9. Измерить после обработки диаметры обеих ступеней Di и di и результаты занести в таблицу протокола.
1.5.10. Вновь на свободном конце заготовки проточить уступ длиной (5÷10) мм, имитирующий погрешность заготовки , заданную преподавателем.
1.5.11. Обработать заготовку с выбранными подачами в два прохода. При каждом проходе оба диаметра обрабатываются с одной установки резца при скорости резания 30÷40 м/мин.
Глубина резания для меньшего диаметра - 0,5 мм.
1.5.12. Измерить после первого в второго прохода диаметры обеих ступеней Di и di и результаты занести в отчет.
1.5.13. Рассчитать погрешности детали для всех проходов по формуле:
1.5.14. Рассчитать уточнения для всех проходов. Для первого прохода:
Для каждого последующего прохода
1.5.15. Рассчитать общее фактические уточнение по формуле (2) для всех вариантов обработки.
1.5.16. Изтех вариантов обработки, которые обеспечивают заданное общее уточнение , выбрать наилучший по критерию минимальной трудоемкости. Для упрощения рассчитывается не штучное, а основное время для каждого прохода:
(мин),
где - длина рабочего хода, мм (принимается по указанию преподавателя);
- подача, принятая для i-го прохода, мм/рад (мм/об);
- частота вращения шпинделя для i -го прохода, об/мин.
Наилучшим будет вариант обработки, обеспечивающий:
1.6. Содержание выводов.
Сравнить, фактическое уточнение с заданным
. Оценить расхождение в процентах.
Объяснить, для чего применяется многопроходная обработка деталей на металлорежущих станках.
Оценить варианты обработки с точки зрения трудоемкости.
1.7 Контрольные вопросы
1.7.1. Что называется погрешностью динамической настройки и из каких составляющих она состоит?
1.7.2. В чем сущность явления копирования погрешностей при обработке на металлорежущих станках?
1.7.3. Что называется уточнением? Как определяется общее уточнение при многопроходной обработке?
1.7.4. За счет чего можно уменьшать копирование погрешностей (повышать уточнение) при обработке на металлорежущих станках?
Дата добавления: 2018-04-05; просмотров: 497; Мы поможем в написании вашей работы! |
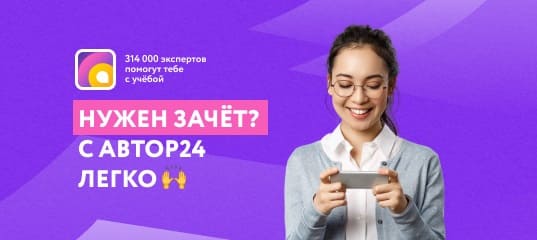
Мы поможем в написании ваших работ!