Основные свойства металлов и их определение
Свойства металлов
Все свойства металлов и сплавов можно разделить на четыре группы: физические, химические, технологические и механические.
К физическимсвойствам металлов и сплавов относятся цвет, плотность, плавкость, электро- и теплопроводность, теплоемкость, магнитные и другие свойства.
Плотность металлов имеет большое значение для выбора материалов при проектировании машин, аппаратов. Использование легких металлов и сплавов (алюминиевые, магниевые, титановые, бериллиевые) снижает общую массу аппарата, сооружении, что особенно важно, в таких отраслях, как авиапромышленность, ракетостроение, автомобильное и тракторное машиностроение.
Плавкость металлов определяется температурой их плавления. Легкоплавкие металлы и сплавы используют для отливки типографических матриц, изготовления подшипников и др.
Металлы с высокой электропроводностью (медь, алюминий) используют для устройства линий электропередач; сплавы, обладающие высоким электросопротивлением, для ламп накаливания и нагревательных приборов и др. Металлы и сплавы, обладающие магнитными свойствами, применяют при изготовлении динамо-машин, электродвигателей, трансформаторов; для изготовления приборов связи: телефонных, телеграфных и других видов аппаратов и машин.
Металлы и сплавы, обладающие высокой теплопроводностью, равномерно нагреваются при горячей обработке, их легко сваривать и паять. Их широко применяют для изготовления теплообменных аппаратов.
|
|
Коэффициент линейного расширения — величина, на которую изменяются линейные размеры тела при изменении температуры. Этот коэффициент должен учитываться при конструировании аппаратуры. Детали, изготовленные из металлов с разным коэффициентом линейного расширения и соединенные между собой, могут разрушаться или дать изгиб при нагревании. Сплавы, имеющие очень малый коэффициент линейного расширения, используются при изготовлении точных приборов.
К химическимсвойствам металлов, и сплавов относятся их окисляемость, растворимость, коррозионная стойкость.
К технологическим —жидкотекучесть, ковкость, свариваемость, обрабатываемость режущим инструментом. Технологические свойства металлов и сплавов имеют исключительное значение при выполнении тех или иных операций в производстве и в частности, при выборе приемов и методов получения деталей машин.
Ковкость — способность металлов и сплавов подвергаться обработке давлением. Это свойство металлов и сплавов связано с их пластической деформацией, особенно при нагревании. С ковкостью связаны такие важнейшие виды обработки, как прокатка, прессование, волочение, ковка и штамповка.
|
|
Жидкотекучесть — способность металлов и сплавов легко растекаться и заполнять полностью литейную форму. Медь даже при перегреве расплава густа и, не растекается, поэтому из нее нельзя готовить изделия методом литья, тогда как сплавы ее (бронзы и латуни) и многие другие металлы (чугун, сталь, магниевые и алюминиевые сплавы) достаточно жидкотекучи.
Свариваемость — способность металлов и сплавов давать прочные неразъемные соединения изготовленных из них деталей. Сварку применяют для изготовления сварных конструкций взамен литых, клепанных, восстановления поломанных деталей, исправления брака литья и т. д. Сварные конструкции легче, прочнее и дешевле клепанных.
Металлы и сплавы подвергаются обработке резанием. Это свойство широко используется в технике, несмотря, на большие отходы (стружка), металлов. Объясняется это тем, что получить обработкой резанием нужную форму, точные размеры и чистоту поверхности детали намного рациональнее по сравнению с другими методами.
Механическиесвойства металлов и сплавов характеризуют их прочностное, пластическое и вязкое состояния.
Прочность — способность металла или сплава сопротивляться действию прилагаемых внешних сил, не разрушаясь. При конструировании учитывают это свойство, так как по нему определяются допускаемые напряжения и ведется расчет аппаратуры. Чем прочнее металл или сплав, тем меньше размер детали, ее масса и тем меньше расход металла на ее изготовление.
|
|
Вязкость — способность металла оказывать сопротивление ударным нагрузкам.
Пластичность — свойство металла деформироваться без разрушения приложениями внешних сил. Пластичность и вязкость не влияют на массу изготовляемых изделий, но при малой пластичности и вязкости изделие при высоких прочностных, свойствах становится хрупким и при случайных перегрузках (при ударном приложении нагрузок) будет разрушаться. При понижении прочностных свойств изделия повышаются его пластичность и вязкость. Следовательно, при определенной прочности изделие должно обладать необходимой (минимумом) пластичностью, и вязкостью. На механические свойства металлов и сплавов влияют химический состав, структура и факторы, связанные с эксплуатацией изделий.
Упругость — свойство металла восстанавливать свою форму после действия приложенных внешних сил.
Твердость — способность одного тела противостоять проникновению в него другого тела, более твердого.
|
|
Таким образом, металлы (сплавы) используемые в качестве конструкционных, должны обладать определенными свойствами и выбор металла или сплава для изготовления изделия зависит от всего комплекса этих свойств.
Определение свойств металлов
Пластическая деформация и рекристаллизация.Приприложении к металлу или сплаву нагрузки он подвергается деформации, которая может быть упругой, т. е. исчезающей после снятия нагрузки, и сохраняющейся пластичной или остаточно пластичной или остаточной. Пластическая деформация связана со сдвигом части кристаллитов по отношению к другой его части по плоскостям скольжения. Упругая деформация прямо пропорциональна напряжению.
Рассмотрим поведение образца металла при испытании его на растяжение. Для этих испытаний готовятся круглые или плоские (для листовых материалов) образцы из испытуемого металла (рис. 6.4) стандартных размеров: диаметр рабочей части 20 мм, рабочая длина образца 200 мм. Для испытаний можно применять образцы и других размеров. Испытания проводятся на разрывных машинах различного типа. На рис. 13 приведен общий вид и кинематическая схема разрывной машины типа ИМ-4Р.
Машина состоит из нагружающего и силоизмеряющего механизмов. Испытуемый образец закрепляется головками в зажимах, после чего приводятся в действие рабочие механизмы машины и перо автоматически записывает на бумаге диаграмму в координатах нагрузка - деформация, где по оси ординат отложена нагрузка Р, по оси абсцисс — удлинение образца Δl. Рассмотрим диаграмму растяжения, мягкой стали (рис. 6.5), полученную при постепенном увеличении растягивающего усилия вплоть до разрыва испытуемого образца.
Зная прилагаемую нагрузку (усилие) Р и площадь поперечного сечения F0, можно определить напряжение о в любой точке диаграммы, т. е. σ= Р/F0. Анализ диаграммы оказывает, что участок ОА является отрезком прямой линии и характеризует жесткость металла. Удлинение образца до точки А строго пропорционально усилию. Такое изменение деформации (удлинения) металла от приложенного усилия называется законом пропорциональности или законом Гука, а наибольшее напряжение, которое выдерживает образец без отклонения от этого закона, - пределом пропорциональности σПЦ, который определяется по уравнению σПЦ = РПЦ/F0.
Точка А соответствует моменту появления пластической деформации и при дальнейшей нагрузке образца до точки В, нарушается закон пропорциональности и на диаграмме появляется криволинейный участок. Возникающие деформации образца от точки А до В являются упругими, если они полностью исчезают при снятии нагрузки. Условное, напряжение, соответствующее появлению первых признаков оставшейся после снятия нагрузки образца деформации, 0,05% (или еще меньше) от первоначальной длины образца, называется пределом упругости σУП:
σУП = РУП/F0.
Для стали предел упругости принимается равным пределу пропорциональности, что видно из диаграммы (точки А и В близки друг к другу).
В точке С образец начинает удлиняться без увеличения нагрузки. Минимальное напряжение, при котором происходит такое удлинение образца, называется физическим пределом текучести:
σТ = РТ/F0.
Большинство металлов и, в частности, средне- и высоко углеродистые стали не обнаруживают горизонтального участка на диаграмме растяжения, и поэтому для таких материалов определяется условный предел текучести σ0,2:
σ0,2 = Р0,2/F0.
где 0,2 —.остаточное удлинение, равное 0,2% от первоначальной длины образца; Р0,2 — нагрузка, соответствующая условному пределу текучести.
Максимальная нагрузка, которую может выдерживать образец без разрушения, приложена в точке В. Напряжение, соответствующее, наибольшей нагрузке предшествующее разрушению образца, называется пределом прочности при растяжении или временным сопротивлением разрыву σВ:
σВ=РВ/F0.
Истинное сопротивление разрыву SК определяется по уравнению
SК= РК/FК.
где Рк — нагрузка в момент разрыва образца; FК — площадь поперечного сечения образца в шейке после разрыва.
Из диаграммы видно, что до точки D удлинение Δ1 образца (соответственно и сужение его поперечного сечения) происходит по всей длине его рабочей части равномерно, но по достижении точки D удлинение сосредотачивается в месте наименьшего сопротивления и дальнейшее удлинение Δ12 образца протекает за счет того места, где образуются шейка, и разрыв его при нагрузке Рк.
Пластичность металлов характеризуется относительным удлинением δ и сужением площади поперечного сечения ψ, которые выражаются в процентах и определяются по уравнению
и
где lK — длина образца после разрыва, мм.; 10 — расчетная длинна образца, мм; Fк — площадь поперечного сечения образца после разрыва, мм; F0 первоначальная площадь его поперечного сечения, мм.
У ряда металлов относительное удлинение и относительное сужение близки к нулю. Такие металлы являются хрупкими, тогда как у пластичных металлов эти характеристики велики (десятки процентов).
Пластическую деформацию металлов и сплавов учитывают при выборе материала для изготовления изделий и, в частности, при получении проволоки, операциях, гибки, вытяжки, высадки, штамповки и т. д. Пластическая деформация обеспечивает конструктивную прочность металлических конструкций, аппаратов и других изделий. Если же металл не способен к пластической деформации, то он склонен к так называемым хрупким разрушениям, т.е. к разрушениям, происходящим при пониженных напряжениях.
В результате пластической деформации происходит упрочнение металла, которое получило название наклепа или нагартовки, при этом пластичность металла резко падает. При большой деформации в результате процессов скольжения зерна меняют свою форму, вытягиваясь в направлении действующих сил, происходит дробление зерен, кристаллическая решетка искажается, структура металла находится в, неустойчивом, напряжен- ном состоянии. Для снятия наклепа изделия нагревают при определенной температуре, при этом атомы металла приобретают способность к перемещениям, что ведет к устранению искажений кристаллической решетки, образованию новых центров кристаллизации и росту кристаллитов. При этом прочность металла понижается, а пластические свойства повышаются. Такой процесс называется рекристаллизацией.
Между абсолютной температурой рекристаллизации Трек и абсолютной температурой плавления Тпл существует простая зависимость Трек= а*Тпд, где коэффициент а определяется степенью чистоты металла.
Для химически чистых металлов а равно от 0,1 до 0,2, металлов технической чистоты 0,3 —:0,4, а для сплавов а может достигать величины, равной 0,8. Так, при нагревании изделия, находящегося в стадии наклепа выше Трек, ему возвращают пластичность. Если пластическую деформацию металла проводят при температуре выше Трек то достигнутое в процессе деформирования упрочнение (наклеп) устраняется при рекристаллизации, протекающей при этих температурах. Такой вид обработки называется горячей обработкой давлением в отличие от холодной, когда обработка давлением проводится при температуре, ниже Трек.
Для некоторых металлов Трек ниже комнатной (для свинца 30°С, олова — 70°С), поэтому при пластической деформации при комнатной температуре (+20°С) образовавшийся наклеп после обработки будет самопроизвольно устраняться. Поэтому деформация таких металлов, как свинец и олово, при комнатной температуре будет являться для, них горячей обработкой давлением. Для такого металла, как вольфрам (температура рекристаллизации 1200 С), обработка давлением даже при 1000 — 1100°С. является холодной пластической деформацией.
Поэтому холодную и горячую обработку давлением следует различать в зависимости от отношения температуры деформации к температуре рекристаллизации.
Определение твердости.При определении твердости применяемые приборы несложны по устройству и просты в обращении, не требуется изготовления образцов для испытаний (можно испытывать заготовки изделия). Для определения твердости (вдавливание, царапание, упругая отдача, магнитный метод) наиболее широко применяются методы, основанные на способности тела (металла) противостоять проникновению в, него другого более твердого тела.
![]() |
По методу Бринелля твердость определяют вдавливанием в, изделие закаленного стального шарика определенного диаметра (10; 5; 2,5 мм.) (рис. 6.6). Число твердости по Бринеллю НВ характеризуется отношением нагрузки, действующей на шарик, к поверхности отпечатка: где Р — нагрузка на шарик, Н (кгс); F — поверхность отпечатка, мм. 2, D — диаметр вдавливаемого шарика, мм.; d — диаметр отпечатка, мм.
Для определения твердости применяют рычажные, и гидравлические прессы. Образец, установленный на столике при помощи винта, прижимают к шарику так, чтобы сжать пружину. Затем при помощи электродвигателя приводится в движение эксцентрик, при вращении которого шатун опускается, и грузы создают давление через систему рычагов. Эксцентрик, вращаясь, поднимает шатун и таким образом снимается давление грузов с образца. При нахождении шатуна в верхнем положении автоматически происходит отключение электродвигателя. Затем освобождают образец, определяют с помощью специальной лупы диаметр отпечатка, по которому вычисляют твердость по приведенной формуле, что требует много времени. В практике пользуются специальной таблицей, в которой каждому диаметру отпечатка соответствует число твердости НВ. Диаметр шарика и нагрузку устанавливают в зависимости от испытываемого металла, твердости и толщины его. При испытании стали и чугуна P=30D2 (например, D=10 мм, P=30000 Н (3000 кгс)]; при испытании меди P=10D2 (например, D =10 мм, Р=10 000 Н (1000 кгс)); при испытании алюминия Р=2,5D2 (например, D=10 мм, P=2500 Н (250 кгс)]. По методу Бринелля нельзя испытывать металлы с твердостью выше НВ 450, так как шарик будет деформироваться, и результат получится неправильным.
Для многих материалов, определив твердость НВ, можно найти предел прочности σВ=КНВ, где К — величина, зависящая от материала, например, для мягкой стали К=О,34, литой стали К=О,3 — 0,4, меди и ее сплавов К=0,55 и т. д. По методу Роквелла твердость определяют вдавливанием в изделие стального шарика -диаметром 1,59 мм при твердости определяемого металла не более 2200 МН/м2 (220 кгс/м2) [нагрузка 1000 Н (100 кгс)] или алмазного конуса с углом 120° при испытании более твердых материалов (нагрузка 1500 Н (150 кгс) и при испытании сверхтвердых сплавов (нагрузка 600 Н (60 кгс)]. Вдавливание в образец шарика или конуса на приборе происходит под действием двух нагрузок: предварительной Р, равной, всегда 100 Н (10 кгс), и основной Р при вдавливании шарика силой 900 Н (90 кгс) (шкала В), силой 1400 Н (140 кгс) (шкала С) и 500 Н (50 кгс) (шкала А). Общая нагрузка Р (рис. 6.7) является суммой этих нагрузок: Р=Р0+Р1.
![]() |
В зависимости от того, применяют стальной шарик или алмазный конус, и нагрузки, при которых проводят испытание (т. е. по какой шкале — В, С или А), число твердости обозначают HRB, HRC, HRA.
Определение твердости проводят на приборе Роквелла (рис. 6.8). Установленный на столике 2 образец, вращением маховика 1 доводят до соприкосновения его со стальным шариком или алмазным конусом 3. Затем продолжают вращение, маховика до тех пор, пока малая стрелка 4 на циферблате дойдет до красной точечки, а большая стрелка циферблата установится при этом в вертикальном положении. Этим создается предварительная нагрузка 100 Н (10 кгс). Далее на образец при помощи рукоятки 5 прилагается основная нагрузка. По окончании определения (вдавливание длится 5 — 6 с) снимается основная, нагрузка обратным поворотом рукоятки 5 и по показаниям большой стрелки циферблата определяется твердость, которая является условной величиной, характеризующей разность глубин отпечатков. Для перевода значений твердости, по Роквеллу в значения твердости по Бринеллю пользуются переводной таблицей.
![]() |
Метод испытания вдавливанием алмазной пирамиды (метод Виккерса) используется для определения твердости деталей малой толщины и тонких поверхностных слоев, имеющих высокую твердость. При испытании в, металл вдавливают четырехгранную пирамиду (с углом при вершине 136°) под нагрузкой от 50 Н (5 кгс) до 1000 Н (100 кгс). Величину диагонали отпечатка определяют с помощью микроскопа, укрепленного на приборе, и по полученным показаниям определяют число твердости, обозначаемое, по формуле HV=P/F,
где Р — нагрузка на пирамиду, Н (кгс); F — площадь отпечатка, мм2.
Обычно для определения числа твердости по величине диагонали отпечатка пользуются специальными таблицами.
Определение выносливости.Выносливость (усталость) — способность металла сопротивляться разрушению (усталости) от периодически повторяющегося действия сил. При перемененном воздействии сил (переменных деформациях и напряжениях) могут образовываться микротрещины и трещины, которые концентрируются, в местах больших напряжений. Но разрушение металла не произойдет, если напряжение будет меньше определенного значения. Наибольшее напряжение, которое при, переменном действии сил не вызывает образования трещин, называется пределом выносливости. Его определяют на специальных машинах, испытанием изгибом при вращении, растяжении, сжатии, кручении. Предел выносливости для конструкционной стали обычно составляет 10 млн. циклов, а для цветных металлов 20млн. циклов.
Кроме названных методов применяют испытания на срез, кручение, сжатие, изгиб, свариваемость, загиб, осадку, выдавливание, обжатие и др.
Основные сведения о сплавах
Общее понятие о сплавах
В связи с отсутствием у большинства чистых металлов технически полезных свойств в технике наибольшее применение находят их сплавы. Сплав — вещество, содержащее два и более компонентов. Сплав, состоящий из металлических элементов и обладающий металлическими свойствами, называется металлическим сплавом.
Сплавы в настоящее время получают несколькими способами, например, взаимодействием элементов в жидком состоянии (сплавлением); спеканием и диффузией в твердом состоянии; осаждением нескольких элементов на катоде при электролизе водных растворов. По количеству компонентов, содержащихся в сплаве, их делят на двойные, тройные и т. д. Вещества, входящие в состав сплава, при затвердевании могут находиться в виде отдельных частиц, зерен обоих компонентов (механическая смесь), или в виде образующихся химических соединений (химическое соединение), или взаимно растворяющихся друг в друге компонентов (твердые растворы).
Сплавы типа механической смеси образуются из веществ, не растворяющихся и не вступающих в химическое взаимодействие между собой в твердом состоянии с образованием соединений. Такие сплавы состоят из смеси кристаллитов веществ, сохраняющих свои кристаллические решетки. Свойства сплава будут определяться соотношением компонентов, входящих в его состав. Чем больше компонентов входит в состав сплава, тем его свойства ближе к свойствам чистого компонента.
Сплавы типа химического соединения образуются при взаимодействии между собой компонентов, входящих в состав сплава, причем содержание компонентов должно быть, строго определенным, Они имеют решетку, отличную от кристаллических решеток компонентов, поэтому обладают и другими механическими, физическими и химическими свойствами.
Сплавы типа твердых растворов бывают трех видов: твердые растворы замещения, твердые растворы внедрения и твердые растворы вычитания.
Твердые растворы замещения образуются в тех случаях, когда атомы растворяемого вещества замещают в кристаллической решетке атомы растворителя (рис. 6.9, а). Это возможно в том случае, когда компоненты имеют одинаковую решетку, размеры их атомов должны мало, отличаться друг от друга (не более 15%).
Размеры атомов растворяемого вещества влияют на параметры решетки, увеличивая ее, если диаметр атома больше или уменьшая ее, если он меньше. Атомы растворяемого вещества могут занимать в кристаллической решетке растворителя строго определенное положение (упорядоченные твердые растворы) или располагаться в произвольном порядке (неупорядоченные твердые растворы).
а) б) в)
Рис. 6.9 Схема распределения атомов в решетках твердых растворов
Образование твердых растворов внедрения (рис. 6.9, б) происходит при растворении атомов растворяемого элемента в кристаллической решетке растворителя, т. е, когда атомы растворенного элемента внедряются в решетку растворителя в промежутках между атомами растворителя. Это возможно только в том случае, когда атомы растворяемого элемента по размерам невелики, т. е. когда отношение диаметра атома растворяемого элемента к диаметру атома растворителя меньше 0,59. Как правило, твердые растворы внедрения образуются с неметаллами, причем параметры кристаллической решетки всегда увеличиваются.
Твердые растворы вычитания (рис. 6.9, в) могут образовываться только в сплавах, содержащих химические соединения, когда избыточные атомы одного из компонентов занимают строго определенное положение в кристаллической решетке, а места, которые должны быть сняты атомами другого компонента, остаются частично свободными, например в решетках карбидов TiC, WC (места, принадлежащие углероду, остаются свободными). Растворы вычитания часто встречаются в полупроводниковых соединениях.
Помимо указанных типов сплавов металлы образуют электронные соединения и фазы внедрения. Электронные соединения характеризуются определенным соотношением числа валентных электронов к общему числу атомов химическом соединении, например, в соединении СuZn3. Указанное отношение будет равно 1/4. Каждому такому соотношению соответствует определенная кристаллическая решетка, например, отношению 3/2 — решетка гранецентрированного куба, 21/3— сложная кубическая решетка; 7/4 — гексагональная плотноупакованная решетка сплавы меди с цинком, меди с оловом, меди с кремнием, слеза с алюминием и т. д. содержат в своем составе электронные соединения. Фазы внедрения могут образовывать атомы железа, хрома, вольфрама, молибдена с элементами, имеющими малый атомный диаметр, например водородом, углеродом, азотом, бором. Они имеют вою кристаллическую решетку, отличающуюся от решеток обоих фаз. Фазы внедрения могут быть трех типов: MeX (WC, VC, TiN и др.); Ме2Х (W2С, Fe2N и др.); Me4Х (Fe4N и др.).
Состояние сплава в зависимости от концентрации и температуры изображают графически. Такое изображение состояния сплава получило название диаграмма состояния. Так как диаграмма состояния показывает устойчивое состояние системы (совокупность фаз, находящихся в равновесии), то она является диаграммой равновесия фаз, существующих при данных условиях. Состояние сплава, изображенного на диаграмме, относится к равновесным условиям без учета перегрева или переохлаждения, чего в действительности быть не может. Следовательно, рассматриваемые диаграммы состояния представляют собой теоретический случай. Математическое описание общих закономерностей существования устойчивых фаз, отвечающих условиям равновесия, было дано Гиббсом, именуемое правилом фаз, которое устанавливает количественную зависимость между степенью свободы системы С, количеством фаз Ф и компонентов К.
Компонентами К называют вещества, составляющие систему, способные переходить из одной фазы в другую т. е. если мы имеем химически чистый элемент, то он представляет собой однокомпонентную систему. Однокомпонентной системой является и химическое соединение, не разлагающееся на составные части в интервале температур изучаемой системы.
Фазой Ф называют однородную часть системы одинакового агрегатного состояния и состава, отделенную от других фаз системы поверхностью раздела, переход которой резко изменяет химический состав или структуру вещества. Например, расплавленный металл является однофазной системой, а механическая смесь - двухфазной и т.д.
Железоуглеродистые сплавы
К сплавам железо — углерод относятся, стали, чугуны и ферросплавы, занимающие, но масштабам производства первое место, а по многообразию применения самое широкое распространение в технике. Чистое железо имеет две аллотропические модификации – α и β (см. аллотропические превращения железа). Чистое железо со многими элементами образует как химические соединения, Так и твердые растворы. Например, с углеродом оно образует химическое соединение цементит Fe3C, в котором содержится 6,67% С. Цементит, обладает высокой твердостью (НВ 800) и очень малой пластичностью.
Железо растворяет углерод с образованием твердых растворов. В зависимости от модификации железа растворимость углерода различна. Так, в γ-железе максимальная растворимость углерода при 1147° С составляет 2,14%, а минимальная растворимость при 727° С - 0,8%. Твердый раствор углерода в γ- Fe называется аустенитом по имени английского ученого Р. Аустена. Аустенит пластичен, твердость его НВ 160—200. В α - Fe растворимость углерода намного ниже. Так, максимальная растворимость углерода при 727°С составляет всего 0,02°/о, а минимальная — 0,006% при комнатной температуре. Твердый раствор углерода в α -Fe называется ферритом (от лат. слова ferrum—железо). Феррит имеет низкую твердость (НВ 80) и высокую пластичность.
Диаграмма состояния железо — цементит
Сплавы железо—углерод выше 6,67% С не применяются как конструкционные материалы, поэтому рассмотрим только диаграмму состояния сплавов железо—цементит (рис. 6.10).
Рис. 6.10 Диаграмма состояния системы Fe—Fe3C
Для упрощения диаграммы состояния железо—цементит структурные изменения, связанные с существованием δ- железа в области температур выше 14010С, рассматривать не будем.
На диаграмме точка А отвечает т. плавления, чистого железа 1539° С, в точке D т. плавления цементита около 16000 C. Область выше линии АСD (линия ликвидуса) характеризуйся жидким состоянием сплава. Полное затвердевание сплавов происходит по линии солидуса АЕСВ. Ниже линии АС до линии АЕС из жидкого расплава (Ж.) выделяются кристаллы аустенита (А). В области АСЕ сплав состоит из жидкого раствора (Ж) и аустенита (А). Ниже линии CD до линии СВ из жидкого расплава выпадают кристаллы цементита, называемого первичным (ЦI), и в области DCB находится смесь жидкого раствора (Ж) и цементита (ЦI). При содержании углерода в сплаве, равном 4,3% и 11470 С, в точке С одновременно кристаллизуется аустенит и цементит, образуя механическую смесь (эвтектику), называемую ледебуритом (Л). Во всех сплавах, содержащих от 2,14 до 6,67% углерода - чугунах, присутствует ледебурит. Сплавы, лежащие левее точки E, относятся к группе сталей.
Превращения в твердом состоянии в сплавах системы Fe—Fe3C связаны с переходом железа из одной модификации в другую и изменением растворимости углерода в железе в результате этого перехода.
В области диаграммы AESG находится аустенит. При снижении температуры ниже линии GS (критическая точка А3) из аустенита выделяется феррит (Ф), а ниже линии ES—цементит, называемый вторичным (ЦII). В области диаграммы GSP сплавы состоят из феррита и аустенита, а в области ниже линии SE (критическая точка Аст) - из цементита и аустенита. Сплавы, содержащие от 2,14 до 4,3% углерода, при температурах от 1147 до 7270 С состоят из аустенита, цементита и ледебурита, а содержащие углерода более 4,3% - из цементита и ледебурита.
При 727° С (линия PSK, критическая точка А1) аустенит распадается с образованием механической смеси феррита и цементита, которая называется перлитом (П). Ниже 7270 С железоуглеродистые сплавы имеют следующие структуры.
Стали, содержащие от 0,02 до 0,8% С феррит +перлит, - доэвтектоидные стали; 0,8% С перлит - эвтектоидная сталь; от 0,8 до 2,14%цементит + перлит—заэвтектоидные стали.
Белые чугуны, содержащие от 2,14 до 4,3% С перлит + вторичный цементит +ледебурит, — доэвтектические чугуны; 4,3% С ледебурит—эвтектический чугун; от 4,3 до 6,67% С цементит первичный + ледебурит - заэвтектпчеекие чугуны.
Линия PQ показывает, что с понижением температуры растворимость углерода в феррите уменьшается от 0,02% при 727°С до 0,006% при комнатной температуре. При охлаждении ниже 727° С из феррита выделяется избыточный углерод в виде цементита, называемого третичным. В низкоуглеродистых сталях в условиях медленного охлаждения третичного цементита выделяется, по границам зерен феррита, что уменьшает пластические свойства, особенно способность к холодной штамповке листовой стали.
Сплавы, содержащие <= 0,02%С, называют техническим железом.
В практике диаграммой состояния железо - углерод пользуются не только для получения заданных (первоначальных или конечных) структур в сплаве, но и для определения теплового режима при термической обработке, температуры нагревания металла при обработке давлением (прокатке, кокке, штамповке), а также для определения температурных пределов при этих операциях.
Влияние на сталь углерода, постоянных примесей и легирующих элементов
Углерод оказывает, основное влияние на свойства стали. С увеличением содержания углерода, в стали, повышаются твердость и прочность, уменьшаются пластичность и вязкость.
В углеродистой стали кроме железа и углерода содержатся еще постоянные примеси таких элементов, как сера, фосфор, кремний, марганец.
Сера и фосфор являются вредными примесями. Допускаемое их содержание в зависимости от качества стали должно быть не более 0,05% каждого. Сера не растворяется в железе, а образует с ним сульфид железа, который с железом образует эвтектику Fe—FeS с т. пл. 988° С. Эта эвтектика при затвердевании стали, располагается вокруг зерен и виде легкоплавкой оболочки, и при горячей обработке (ковке, прокатке и т. п.) такие оболочки расплавляются, теряется связь между зернами, образуются трещины. Это явление получило название красноломкости стали. Фосфор, растворяясь в феррите, резко снижает его пластичность, вызывает внутрикристаллическую ликвацию, способствует росту зерна, что приводит к хрупкости изделий при обычной температуре (хладноломкость). Кремний (до 0,5%) и марганец (до 0,8%) практически не оказывают влияния, на свойства стали.
Легированными сталями называют, стали, содержащие в своем составе специально введенные легирующие элементы, такие, как никель, хром, молибден, титан, ванадий, вольфрам и др., или в которых содержится повышенное (более 0,5—1,0%) количество кремния или марганца. Введение легирующих элементов в сталь повышает механические свойства или придает им специальные свойства, например жаростойкость, жаропрочность, кислотостойкость и др.
Легирующие элементы при введении в сталь могут образовывать с железом твердые растворы, растворяться в цементите [например, (Fe, Сг)3С] или образовывать самостоятельные химические соединения с углеродом (специальные карбиды), например VC, Сг7С3 и др.
Легированные стали по структуре в условиях равновесия делят на следующие кассы: перлитный, ледебуритный, ферритный, аустенитный, а по структуре, получаемой после охлаждения на воздухе, на перлитный, мартенситный, аустенитный, карбидный.
Дата добавления: 2018-04-05; просмотров: 4558; Мы поможем в написании вашей работы! |
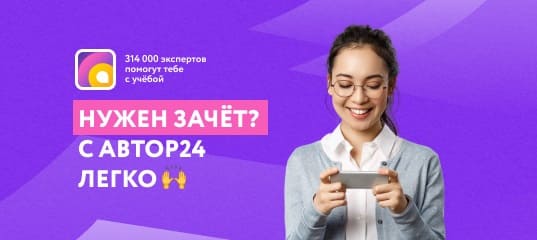
Мы поможем в написании ваших работ!