Выбор режима ручной дуговой сварки
Министерство образования и науки Российской Федерации
Федеральное государственное автономное образовательное
учреждение высшего образования
«Южно-Уральский государственный университет (НИУ)»
Кафедра «Техника и технологии в металлургии»
Направление 18.03.01 «Химическая технология»
Лабораторная работа №2
по дисциплине «Материаловедение»
Проверила Т.В.Баяндина
| ||
| Автор работы студентка группы ДО-309 | |
| ||
Челябинск 2017
ОТЧЕТ
РУЧНАЯ ДУГОВАЯ СВАРКА
Цель работы: ознакомление с сущностью процесса, оборудованием, особенностями формирования сварного соединения при различных режимах сварки.
Краткая теоретическая часть
Сварка – это технологический процесс получения неразъемных соединений различных материалов: однородных и разнородных металлов и сплавов, керамических материалов,пластмасс.
Сварка является одним из наиболее широко распространенных технологических процессов в машиностроительном производстве.
Сущность процесса сварки заключается в создании условий для сближения свариваемых заготовок на расстояние действия межатомных сил. В обычных условиях такому сближению мешают неровности, окисные пленки, загрязнения на поверхности соединяемых деталей. Поэтому требуется определенная энергия для активизации атомов свариваемых материалов. Эта энергия сообщается извне в виде электромагнитного излучения или механического воздействия, которые повышают активность и диффузионную подвижность атомов.
|
|
В зависимости от способа передачи этой энергии все виды сварки делятся на двегруппы:
- сварка плавлением. Образование сварного соединения происходит за счет создания
общей ванны расплавленного металла кромок свариваемых деталей.
- сварка давлением. Формирование межатомных связей в результате совместнойпластической деформации заготовок, в результате которой происходит сближение атомов нарасстояние действия межатомных сил.
Классификация методов сварки по данному признаку представлена в таблице 1
Таблица 1
Классификация основных методов сварки
Процесс сварки | Метод сварки |
сварка плавлением(термический) | электродуговая (электрошлакова),газова, плазменная, электроннолучевая, лазерная, термитная |
сварка давление(механический, термомеханический) | контактная, диффузионная, холодная, взрывом, ультразвуковая, трением |
Выбор того или иного метода сварки зависит от многих факторов, одним из которыхявляется свариваемость.
Под свариваемостью понимают способность материалов образовывать в процессесварки соединение, не уступающее по своим механическим и физико-химическим свойствамсвариваемым материалам. Способность к сварке различных материалов определяется их химическим составом и свойствами с одной стороны, и применяемым методом сварки с другой.
|
|
Основными критериями свариваемости являются два: склонность к образованию дефектов(трещин, пор, шлаковых включений и т.д.) и показатели механических свойств в зоне сварного соединения. По показателю свариваемости материалы делятся на хорошо, удовлетворительно и плохо сваривающиеся.
В машиностроении и строительстве, благодаря своей доступности и дешевизне, широкое применение имеет метод ручной дуговой сварки.
Ручная дуговая сварка. Сущность процесса, оборудование, материалы
Метод относится к сварке плавлением, где в качестве источника энергии используетсятепло электрической дуги.
Электрическая дуга представляет собой мощный стабильный разряд электричества ватмосфере ионизированных газов и паров металла.
Дуга горит двумя электродами, причем, как правило, одним из электродов являетсясвариваемая заготовка. Схема сварочной дуги представлена на рис. 1
|
|
Рис. 1 Схема сварочной дуги постоянного тока прямой полярности
Сварочная дуга состоит из котодного пятна 2, которое образуется на электроде 1,столба дуги 3, анодного пятна 4, образующегося на аноде (изделии 5). Катодом является плавящийся электрод, анодом – свариваемая заготовка. При обратной полярности катодом является изделие, а анодом электрод. Применяется также дуга переменной полярности (при использовании переменного тока).
Полная тепловая мощность дуги определяется по формуле:
Q = K × ICB. ×U Д , Вт(1)
где ICB. – сила сварочного тока, А;
U Д – напряжение дуги, В;
K – коэффициент, учитывающий потери тепла при использовании различных способов сварки, типов электродов и т.д. На практике величина K может колебаться от 0,9 до 0,5.
На рис. 1 показано распределение температур и доли тепловой мощности, выделяющейся в различных участках электрической дуги. Как видно из рис. 1 тепловые возможностиэлектрической дуги позволяют расплавить большинство используемых конструкционныхматериалов и дуговая сварка эффективно используется в машиностроении и строительстве.
Оборудование для ручной дуговой сварки состоит из источника электропитания иэлектрододержателя с гибким кабелем.
|
|
Материалом для ручной дуговой сварки являются электроды.
Обязательно использование средств защиты от светового и ультрафиолетового излучения дуги и капель расплавленного металла. Обычно это защитный щиток или шлем с затемненным стеклом.
Источники питания для ручной дуговой сварки могут быть как постоянного тока(выпрямители, сварочные генераторы), так и переменного тока (понижающие трансформаторы).
Использование постоянного тока дает более устойчивую дугу, сварочные трансформаторы (переменный ток) намного проще в эксплуатации.
Электроды для ручной дуговой сварки представляют собой металлические проволочные стержни с нанесенным на их поверхность слоем специального покрытия. Стандартпредусматривает 77 марок проволоки диаметром от 0,2 до 12 мм. По составу стальную электродную проволоку разделяют на три группы: углеродистую, легированную и высоколегированную. Обозначение марки проволоки состоит из букв и цифр, например Св-08 или Св-ЗОХГСА. Первые две буквы "Св" означают назначение проволоки - "сварочная", а следующие за ними цифры и буквы аналогичны обозначениям, принятым для сталей.
Электродное покрытие состоит из многих компонентов и должно обеспечивать хорошую ионизацию дуги, защиту металла сварочной ванны от воздействия кислорода воздуха,раскисление, легирование и т.д.
По назначению электроды подразделяются ГОСТ 9466-75:
- для сварки углеродистых и низколегированных сталей с временным сопротивлением
разрыву до 60 кгс/мм (600 М11а), с условным обозначением У;
- для сварки легированных сталей с временным сопротивлением разрыву свыше 60
кгс/мм (600 МПа) - Л;
- для сварки легированных теплоустойчивых сталей - Т;
- для сварки высоколегированных сталей с особыми свойствами - В;
- для наплавки поверхностных слоев - Н.
По виду покрытия электроды подразделяются:
- с кислым покрытием, А;
- с основным покрытием, Б;
- с целлюлозным покрытием, Ц;
- с рутиловым покрытием, Р;
- с покрытием сметанного вида, двойное буквенное обозначение;
- с прочими видами покрытий, П.
В зависимости от того, в каком пространственном положении выполняется сварка
(рис. 2) электроды подразделяются:
- для сварки во всех положениях с условным обозначением 1;
- для сварки во всех положениях, кроме вертикального, сверху вниз - 2;
- для положений нижнего горизонтального на вертикальной плоскости и вертикально-
го снизу вверх – 3
Рис. 2 Пространственные положения шва при ручной сварке:
а - нижнее, б - вертикальное, в - потолочное, г - горизонтальное
Кроме вышерассмотренной классификации, электроды подразделяют на типы.
Так, согласно ГОСТ 9467-75 для сварки конструкционных углеродистых и легированных сталей предусмотрено 14 типов электродов (Э 38, Э-150). Здесь буква Э означает электрод для дуговой сварки, а следующие за ней цифры – временное сопротивление разрывунаплавленного металла в кгс/мм2. Для сварки легированных теплоустойчивых сталей предусмотрено 9 типов электродов (Э-09М, Э09МХ и др.), отличающиеся химическим составомнаплавленного металла.
Для сварки высоколегированных сталей электроды согласно ГОСТ 10052-75 классифицируются по химическому составу и механическим свойствам наплавленного металла.
Помимо типа электрода, важной характеристикой является его марка, которая определяет состав покрытия, род и полярность тока, возможность сварки в различных пространственных положениях, каждому типу электрода соответствует одна или несколько марок.
Схема процесса ручной дуговой сварки представлена на рис. 3
Рис. 3 Схема процесса ручной дуговой сварки металлическим покрытым электродом
Зажигание электрической дуги 8 между электродом и свариваемыми заготовкамипроизводится прикосновением конца стержня электрода 7 к свариваемому изделию 1 и последующим быстрым отводом электрода на расстояние 3-6 мм. Под действием тепла дугипроисходит расплавление кромок свариваемых заготовок, а также электродного или присадочного металла, который в виде капель переходит в ванну основного расплавленного металла и смешивается с ним, образуя, так называемую, металлическую ванну 9 Вместе состержнем электрода плавится и его покрытие 6, при этом вокруг дуги образуется газоваясреда 5, а на поверхности расплавленного металла – жидкая шлаковая ванна 4, защищающаяего от вредного влияния атмосферы. Металлическая и шлаковая ванны вместе образуют сварочную ванну. В процессе сварки по мере оплавления электрода последний постепенноопускают для поддержания постоянной длины дуги, а также перемещают его вдоль оси швасо скоростью Vсв. При этом ранее образовавшаяся металлическая ванна, остывая, затвердевает, образуя сварной шов 3, а шлаковая ванна, остывая, превращается в шлаковую корку 2
В зависимости от расположения свариваемых деталей сварные соединения разделяются на несколько типов (рис. 4).
Рис. 4 Типы сварных соединений:
а – стыковое; б – тавровое; в – угловое; г – нахлесточное.
Для обеспечения равномерного сквозного проплавления и получения требуемого качества шва при толщинах заготовок свыше 6 мм, во избежание непровара, предусматриваютпредварительную обработку кромок заготовок – У-образная и Х-образная разделка (рис. 4 а,б, в). В случае X-образной разделки сварку проводят с обеих сторон. Качественное сварноесоединение можно получить при толщине заготовок не более 30 мм.
Выбор режима ручной дуговой сварки
Основными параметрами режима ручной дуговой сварки является величина сварочного тока и диаметр электрода. При ручной дуговой сварке ток, который подводится к противоположному от дуги концу электрода, проходя по электроду нагревает его, что может привести к отслаиванию покрытия. Чем толще свариваемые детали, тем больше должен бытьдиаметр электрода, чтобы не допустить перегрева.
Диаметр электрода выбирается в зависимости от толщины свариваемых заготовок всоответствии с табл. 2
Таблица 2
Выбор диаметра электрода
Толщина свариваемыхизделий, мм | 1…2 | 3…5 | 4…10 | 12…24 |
Диаметр электрода, мм | 2…3 | 3…4 | 4…5 | 5…6 |
Выбрав диаметр электрода, определяем величину сварочного тока, пользуясь формулой:
IСВ. = k × DЭЛ(2)
где IСВ. – сила тока. А;
DЭЛ – диаметр электрода, мм;
k – опытный коэффициент, зависящий от марки электрода, А/мм.
Для электродов из низкоуглеродистой стали k =40…60 А/мм, для высоколегированной стали k =35…40 А/мм. Напряжение дуги при ручной дуговой сварке составляет 18…28В.
Следует иметь в виду, что на форму и размеры сварного шва оказывают влияние род иполярность тока. Так, при сварке постоянным током при прямой полярности (плюс источника тока присоединен к изделию, а минус – к электроду) на нагрев изделия расходуется 50%тепловой мощности дуги, на нагрев электрода – 30% и потери в окружающую среду составляют 20%. Это различие в тепловыделении на катоде и аноде используют при решении технологических задач. Сварку толстолистовых конструкций, требующих большего подвода теплоты для нагрева кромок свариваемых заготовок, выполняют на прямой полярности, а сварку тонколистовых заготовок (или при потолочном положении сварного шва) – при обратнойполярности (плюс источника тока присоединен к электроду, а минус – к изделию).
При сварке переменным током глубина провара на 15…20% меньше, чем при сварке постоянным током.
Неправильный выбор режима сварки может привести к возникновению дефектов (см. рис. 5), которые бывают двух типов: внешние и внутренние.
Рис. 5 Виды дефектов сварных соединений
К внешним дефектам относятся: наплывы (а), подрезы (б), наружныйнепровар (в),поверхностные трещины и поры (г); к внутренним – скрытые трещины и поры (д) и внутренние непровары (е).
Для выявления внешних и внутренних дефектов обязательным заключительным этапом сварки является контроль качества сварных соединений.
ПОРЯДОК ВЫПОЛНЕНИЯ РАБОТЫ
1 Ознакомиться с оборудованием поста для ручной дуговой сварки и процессом получения сварного соединения.
2 Для выданных образцов сварных соединений рассчитать параметры режима сварки,выбрать электрод, пользуясь данными табл. 3 Результаты представить в табл. 4
3 Зарисовать макроструктуру образца сварного соединения и указать видимые дефекты сварки.
СОДЕРЖАНИЕ ОТЧЕТА
1 Название и цель работы.
2 Конспект теоретической части с краткими сведениями ручной дуговой сварки.
3 Результаты работы (табл. 4).
Дата добавления: 2018-04-05; просмотров: 402; Мы поможем в написании вашей работы! |
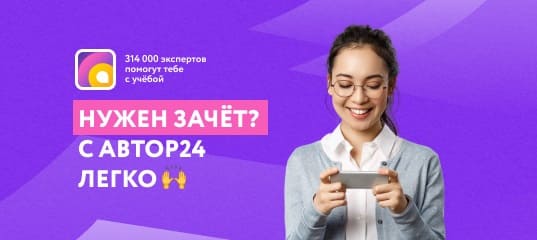
Мы поможем в написании ваших работ!