Назначение твердых окислителей, характеристика
Главными компонентами твердых окислителей являются оксиды железа, содержание которых должно быть как можно более высоким; количества SiO2, серы и фосфора также ограничивают. Добавочные материалы используют для изменения свойств шлаков или для наведения новых шлаков.
Ремонты мартеновских печей
Работа по так называемому холодному ремонту мартеновских печей, проводимая периодически через каждые 2,5—3 месяца, в современных мартеновских цехах, оборудованных значительным числом (до 15) большегрузных печей (300—400 т), требует разборки большого объема огнеупорной кладки, замены ее новой и наряду с отмеченными выше крайне неблагоприятными метеорологическими условиями сопровождается значительным запылением воздуха кварцеодержащей пылью. Кроме того, операции, связанные с ремонтом, еще слабо механизированы и требуют участия большого числа рабочих. Основными оздоровительными мероприятиями в этих условиях должны в первую очередь являться мероприятия технического и технологического порядка, а именно: а) удлинение кампании или длительности работы печи без холодного ремонта путем применения магнезитовых и хроммагнезитовых огнеупоров для верхнего, а также для нижнего строения печи и высокоглинистого шамотного кирпича для насадок; б) механизация ремонтных работ и более четкая их последовательность и организация;в) внедрение новых методов очистки шлаковиков (выемка шлака в виде монолита без предварительного перфораторного бурения и взрывов), удаление шлака в жидком виде, устройство выдвижных шлаковиков и т. п.; г) проветривание рабочего пространства ванны печи и отсос горячего воздуха из верхней зоны (регенераторов и шлаковиков посредством усиления естественной тяги на трубу или путем использования установок механической вытяжной вентиляции.
|
|
Ремонт конвертера
Для условий технологии ремонта футеровки конвертеров путем совместной раз-дувки конечного шлака с факельным торкре- тированием недефицитными торкрет-массами разработана модель диссоциации карбонатной пыли в торкрет-факеле. Результаты расчетов свидетельствуют о возможности существенной замены части обожженной огнеупорной со-ставляющей торкрет-массы пылью доломити- зированного известняка, сырого доломита и магнезита. Частицы огнеупора, карбонатного материала или продукта его диссоциации остаются твердыми вплоть до контакта с по-верхностью футеровки. Капли золы выполня- ют роль связующего материала, удерживаю- щего огнеупорные частицы на стенке конвер- тера. Примеси в самом огнеупорном материале снижают температуру их плавления и способ-ствуют эффекту прилипания к футеровке
|
|
Характеристика печного пролета мартеновского цеха
Практически для всех крупных мартеновских цехов отечественных металлургических заводов характерна единая схема планировки, транспортных потоков и организации выполнения основных работ. Характерными особенностями планировочных решений мартеновских цехов являются: организация выплавки и разливки стали в главном здании цеха, разливка стали в изложницы, вынесение всех работ по хранению и подаче шихтовых материалов и подготовке изложниц в специализированные отделения, располагаемые в отдельных зданиях, использование для связи между отделениями железнодорожного транспорта.
Основные грузопотоки в мартеновском цехе — подача и загрузка в печи стального лома и сыпучих материалов, подача и заливка чугуна, подача изложниц, уборка слитков й шлака; главные вспомогательные грузопотоки — подача огнеупоров и материалов для ремонта и уборка ремонтных отходов.
Способы подачи кислорода для интенсификации мартеновской плавки
1. Метод интенсификации сжигания горючего в рабочем пространстве мартеновской печи. Кислород подается в рабочее пространство печи в зону горения топлива. При отоплении печей жидким топливом или холодным высококалорийным газом кислород вводится обычно через форсунку или горелку под струю топлива. При отоплении печей подогретым газом (генераторным, смесью коксового и доменного) кислород подается в струю газа через две водоохлаждаемые фурмы, установленные с наружной стороны газового кессона под углом 8—10° к горизонту (рис. 27). Кислород подается со скоростью не ниже критической под давлением 6—10 ати. При обогащении воздуха кислородом повышается температура горения топлива и несколько увеличивается лучеиспускательная способность пламени Наряду с этим струи кислорода, вводимые в зону горения с большой скоростью, ускоряют смешение топлива с воздухом и придают факелу большую жесткость и настильность.
|
|
Из выражения для определения теоретической температуры горения (tтeop)
следует, что возрастание температуры факела с повышением содержания кислорода в воздухе (при обогащении воздуха кислородом) происходит за счет уменьшения объема горения вследствие снижения содержания в них балластного азота.
Наиболее значительно поднимается температура (рис. 28) при обогащении воздуха кислородом до 30%; при обогащении же до 40% возрастание температуры становится менее значительным вследствие увеличивающейся диссоциации продуктов горения (CO2 и H2O). При скрап-процессе можно считать экономически целесообразным обогащение воздуха кислородом до 25—27%, а прискрап рудном процессе — в ряде случаев до 30—35%.
|
|
Обогащение воздуха кислородом приводит к уменьшению потерь тепла с отходящими продуктами горения и улучшению использования тепла в рабочем пространстве мартеновской печи. Уменьшение объема продуктов горения создает возможность увеличения подачи топлива в печь при тех же тяговых устройствах.
Применение кислорода для интенсификации тепловой работы печи приводит к значительному ускорению прогрева и плавления шихты, формирования активного шлака, создает благоприятные условия для дефосфорации и десульфурации металла. Подача кислорода в факел в период кипения ускоряет процесс обезуглероживания металла и нагрев ванны, что приводит к сокращению продолжительности и этого периода плавки. Таким образом, с применением кислорода сокращается продолжительность всей плавки, что сопровождается также и снижением расхода топлива.
Наибольший эффект от использования кислорода достигается на печах с основными сводами при условии надлежащей организации производства, в частности при ускорении завалки шихты.
На заводах России подача кислорода в факел производится от начала завалки шихты до конца плавления, и в ряде случаев прискрап рудном процессе вплоть до чистого кипения. При скрап-рудном процессе увеличение производительности мартеновских печей при обогащении воздуха кислородом до 25% составляет 18—20%, при обогащении воздуха до 30—35% производительность возрастает до 40—60%. Экономия топлива составляет соответственно около 15 и до 30—40%, а расход кислорода 35—40 и 50—60 м3/т. При обогащении воздуха до 25% было достигнуто увеличение производительности на печах при скрап процессе на 13—15%, снижение расхода условного топлива на 5—7% при удельном расходе кислорода 18—22 м3/т.
2. Метод «прямого окисления» жидкой ванны кислородом нимеет целью ускорение процесса окисления примесей в результате непосредственного действия кислорода на расплавленный металл. Кислород вводят в ванну чаще всего в период доводки вплоть до раскисления, а при скрап-рудном процессе кислород также можно вводить и в период плавления после заливки чугуна. Самым простым способом является ввод кислорода в ванну через железные трубки диаметром 1''—1 1/4'', вставленные в завалочные окна или в специальные отверстия в задней стенке печи.
Наиболее рациональна подача кислорода через отверстия в своде печи с помощью водоохлаждаемых фурм (см. рис. 27). Кислород подают под давлением 8—10 ати; продувка ванны кислородом приводит к существенному ускорению процесса окисления углерода, особенно значительному при низкой концентрации углерода в металле (ниже 0,1%). Например, для снижения содержания углерода с 0,1 до 0,04% при обычном процессе необходимо 2—2,5 часа, а при «прямом окислении» всего 50 мин. Эффективность применения кислорода в сильной степени зависит от содержания углерода в металле. При содержании углерода выше 0,4% при продувке используется почти весь кислород, а при содержании менее 0,1%—небольшая часть кислорода (до 10%). Прямое окисление в начале доводки благоприятствует дефосфорации металла. Интенсивныйбарботаж ванны при продувке кислородом улучшает десульфурацию металла и способствует снижению газонасыщенности стали. Обычно продувку начинают при 0,3—0,5% углерода и заканчивают за 10—30 мин. до выпуска плавки. При этом достигается увеличение производительности на 8—10% и сокращение удельного расхода топлива на 6—8% при расходе кислорода 5—6 м3/т.
Прямое окисление ванны получило широкое распространение при выплавке малоуглеродистой стали.
Существенным недостатком метода прямого окисления является интенсивное пылеобразование, так как в зоне взаимодействия струи кислорода с металлом развиваются высокие температуры. По расчетным данным Л.М. Ефимова, при окислении чистого железа чистым кислородом температура поверхности жидкого металла в реакционной зоне может достигать 3010° К, по другим данным, 3900—4000° К. Непосредственные измерения температуры реакционной зоны пирометром цветного излучения показали, что при продувке ванны кислородом перегрев ее относительно температуры металла оказался равным 700° и более, при продувке воздухом 300—400°.
В результате развития высоких температур в реакционной зоне количество плавильной пыли в продуктах горения по сравнению с обычной плавкой возрастает с 2—3 до 16—32 г/м3, причем вынос пыли увеличивается с повышением концентрации углерода в металле.
В связи с этим снижается выход металла и возможно сокращение кампании печи. Для уменьшения интенсивности пылеобразования в струю кислорода добавляют воду или пар. Применение кислородо-водяной смеси с 40—50% воды приводит к снижению количества пыли в 5 раз.
Комбинированный метод применения кислорода путем подачи его в факел и ванну является наиболее эффективным. По этому методу кислород подают в факел в период завалки, прогрева и плавления, а иногда — в период рудного кипения. Продувку ванны начинают в конце рудного кипения при содержании углерода 0,3—0,6%. В последнее время все шире применяют также прямое окисление в периоды плавления и доводки.
Комбинированный способ использования кислорода при надлежащей организации производства в цехе позволяет повысить производительность мартеновских печей на 25—50%.
Применение сжатого воздуха для интенсификации сжигания топлива и продувки ванны в последнее время находит все более широкое применение, особенно на заводах, не имеющих кислородных станций. Подача компрессорного воздуха в головку (по бокам кессона или в торец) способствует лучшей организации пламени, снижает недожог топлива в рабочем пространстве, повышает теплоусвоение ванной печи, способствует повышению производительности печи на 8—10% и снижению расхода топлива на 6—8%.
70- дутьевой режим и конструкции кислородных фурм в конвертерном производстве
Кислород подают в конвертер через вертикально расположенную водоохлаждаемую фурму, которую вводят в полость конвертера через горловину строго по его оси. Давление кислорода перед фурмой составляет 1,0-1,6 МПа. Высоту фурмы над ванной можно изменять по ходу плавки; обычно она увеличивается при росте емкости конвертера и находится в пределах 1, 0-4, 8 м от уровня ванны в спокойном состоянии. Поднимают и опускают фурму с помощью механизма, сблокированного с механизмом вращения конвертера. Конвертер нельзя повернуть, пока из него не удалена фурма. Скорость подъема и опускания фурмы изменяется в пределах 0,1-1 м/с. Фурма выполнена из трех концентрично расположенных стальных труб и снабжена снизу медной головкой с соплами . Полости, образованные трубами, служат для подачи кислорода, подвода и отвода охлаждающей воды. Наиболее часто применяют фурмы с центральной подачей кислорода . По средней трубе при этом подводят охлаждающую воду, а по наружной - отводят. Применяются также кислородные фурмы с центральной подачей охладителя . В таких фурмах подаваемую через центральную трубу воду отводят по наружной трубе, а кислород подают по средней трубе. К верхней части труб прикреплены патрубки 5 для подвода кислорода, подвода и отвода воды. Чтобы избежать разрушения фурмы из-за напряжений, вызываемых различным тепловым расширением труб (наружная труба удлиняется сильнее, чем более холодные внутренние), в фурме предусматривают компенсирующие устройства: сильфонные компенсаторы, т.е. гофрированные металлические шланги ; подвижные сальниковые уплотнения при соединении двух труб; телескопическое соединение двух труб. Длина фурмы 300-т конвертера достигает 27 м. Головка фурмы является сменной, ее соединяют с трубами сваркой или резьбой в сочетании со сваркой. В головке расположены сопла Лаваля , через которые кислород поступает в полость конвертера и распределитель воды, направляющий ее вдоль поверхности головки. Головки выполняют сварными и иногда литыми. Всю головку или ее нижнюю часть с соплами, обращенную к зоне наибольших (до 2600 °С) температур в конвертере, выполняют из меди. Это делают потому, что, обладая высокой теплопроводностью, медь быстро передает тепло охлаждающей воде, и поэтому даже в зоне высоких температур головка не перегревается и сохраняет прочность. Число сопел Лаваля в головке изменяется от трех-четырех до шести-семи, возрастая по мере роста вместимости конвертера и количества вдуваемого кислорода. Сопла располагают веерообразно расходящимися, чтобы повысить степень рассредоточения дутья по объему ванны. Угол расхождения сопел (угол а наклона их осей к вертикали) уменьшают по мере снижения вместимости конвертера (от 19° у семисопловой фурмы для большегрузного конвертера до 9° у трехсопловой для небольшого конвертера); это необходимо, поскольку при большом угле расхождения кислородных струй они у малых конвертеров будут слишком приближаться к стенкам, вызывая усиленный износ футеровки. Сопла Лаваля применяют потому, что они, преобразуя энергию давления в кинетическую, обеспечивают скорость кислорода на выходе в 500 м/с и более; это необходимо для заглубления струй в ванну и Полного усвоения ею кислорода. Давление кислорода перед соплом должно быть более 0,9-1,2 МПа, а его диаметр определяют расчетом; приближенно диаметр минимального (критического) сечения сопла можно определить по формуле, мм: d = 3,5V/Р , где р- давление перед соплом, МПа; V- расход кислорода через сопло (обычно не более 250 м3/мин). Воду для охлаждения фурмы подают насосом в таком количестве, чтобы перепад температур на входе и выходе не превышал 30° во избежание выпадения из воды солей жесткости; на больших конвертерах расход воды достигает 500 м3/ч. Стойкость головок фурм составляет 50-150 плавок. В первые годы освоения кислородно-конвертерного процесса применялись односопловые фурмы, позволявшие работать с небольшими расходами (до 200-250 м3/мин) кислорода; увеличение расхода кислорода при подаче одной струей вызывало выбросы металла при продувке. Позднее были разработаны повсеместно применяемые в настоящее время многосопловые фурмы, которые благодаря рассредоточению кислородного потока на несколько струй, обеспечили более "мягкую" продувку и резкое уменьшение количества выбросов.
Дата добавления: 2018-04-04; просмотров: 701; Мы поможем в написании вашей работы! |
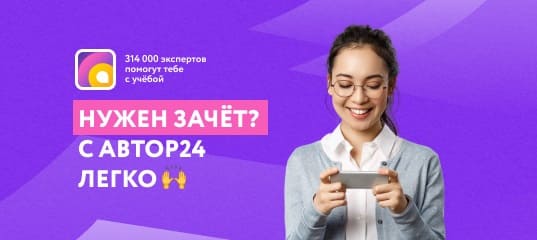
Мы поможем в написании ваших работ!