ТЭП ККП с продувкой конвертера сверху техническим кислородом
Сортамент и качество КК стали, область её применения. Качество кислородно-конвертерной стали Качество стали определяется в значительной степени ее химическим составом и содержанием вредных добавок и неметаллических включений. Особое внимание при производстве конвертерной стали уделяют получению металла с низким содержанием газов, прежде всего, азота. Пути повышения качества конвертерной стали в значительной степени зависят от требований, предъявляемых к готовым изделиям из нее. В современной металлургии широко используются разные методы повышения качества стали: • получение сверхчистой стали без вредных примесей; • снижение содержания неметаллических включений; • дегазация металла; • изменение состава и формы включений (модифицирование); • отработка технологического режима плавки, позволяющая получить точно заданный химический состав и температуру; • обеспечение стандартных условий разлива металла с соблюдением оптимальных температурных условий; • обработка металла шлаковыми и экзотермическими смесями; • предупреждение вторичного окисления струи металла во время разливки и др. Многолетний опыт использования конвертерной стали показывает, что она не уступает по качеству мартеновской стали, а по некоторым показателям даже превосходит ее. Эти преимущества обусловлены более низким содержанием кислорода, азота, серы, фосфора и неметаллических включений. Содержание азота в стали Содержание азота в конвертерной стали зависит от цепочки технологических факторов: • содержания углерода в стали и азота в шихте; • температуры металла и продолжительности продувки; • чистоты кислорода, используемого для продувки; • подсасывания воздуха в рабочее пространство конвертера. Увеличение чистоты кислорода приводит к снижению содержания азота в стали. Необходимо использовать кислород чистотой 99,5 %, который обеспечивает получение в стали 0,002—0,004 % азота. Другим источником попадания азота в металл может быть атмосферный воздух, который попадает в полость конвертера главным образом при высоком расположении кислородной фурмы в момент наведения шлака. После снижения высоты расположения фурмы подсасывание воздуха прекращается. Размер горловины конвертера и подсасывание воздуха находятся в прямой зависимости. Также имеет значение метод утилизации конвертерных газов. При отводе дымовых продуктов плавки по открытой схеме с полным догоранием СО до СО2в зазор между верхом горловины конвертера и низом охладителя направляется атмосферный воздух, который образуется тягой дымососа. Часть воздуха всасывается в горловину конвертера и повышает количество азота в ванне. При работе по схеме отведения конвертерных газов без сжигания СО в нижней части котла создается небольшое избыточное давление, предупреждающее попадание воздуха в конвертер. В интервале температур выпуска металла из конвертера (1500—1620 °С) влияние температуры на растворимость азота практически не наблюдается. Среднее содержание азота в стали для указанного интервала не превышает 0,007 %. Содержание кислорода Содержание кислорода в конвертерной стали определяется содержанием углерода в металле и степенью окисленности конечного шлака. Кроме того, растворение кислорода в металле зависит от содержания марганца и кремния, а также от температуры. Влияние окисленности шлака определяется величиной коэффициента распределения FeO между металлом и шлаком. В результате влияния этих факторов концентрация кислорода в металле растет с уменьшением содержания углерода и увеличением окисленности шлака. В случае выплавки высокоуглеродистых марок стали основное влияние на содержание кислорода в металле оказывает содержание углерода. Конечное содержание кислорода регулируется раскислением металла алюминием. Для улучшения качества стали и борьбы с вредными газами используют внепечную обработку. В некоторых случаях такая обработка более эффективна и экономически оправдана, чем обработка непосредственно в сталеплавильных агрегатах. Содержание водорода Содержание водорода в конвертерной стали обычно незначительное из-за ограниченности источников его попадания в металл. Кроме водорода, оказавшегося в ванне вместе с шихтовыми материалами, главным источником его является влага, содержащаяся в кислороде, а также влажность воздуха, который подсасывается в полость конвертера. Как правило, содержание водорода в металле в конце продувки редко превышает 3—4 см3/100 г металла. Но в процессе выпуска металла и разливки вследствие контакта с атмосферным воздухом содержание водорода в стали может несколько возрасти. В случае прогара кислородной фурмы охлаждающая ее вода начинает попадать непосредственно в реакционную зону и содержание водорода в ванне заметно возрастает. Содержание неметаллических включений Содержание неметаллических включений в конвертерной стали определяется главным образом технологией раскисления. Поскольку в конце операции при правильно организованном процессе металл не содержит повышенного количества серы, кислорода и азота, создаются условия для получения стали, содержащей незначительное количество сульфидных, оксидных и нитридных неметаллических включений. Их количество, остающееся в металле, определяется технологией обработки металла в ковше и разливкой. Вредные примеси в шихте Примеси цветных металлов (меди, цинка, свинца), обычно находящиеся в бытовом металлоломе и ломе автомобильной промышленности, попадают в конвертер во время завалки и негативно влияют на качество стали. Поэтому на предприятиях по переработке лома, а также в скрапоразделочных цехах металлургических заводов необходимо уделять большое внимание сортировке лома и очищению его от цветных металлов. Но не всегда эти мероприятия бывают эффективными. Для выплавки качественного металла необходимо использовать отходы собственного производства (возврат) или металлизированное сырье. Наличие в ломе небольшого количества мышьяка, олова, свинца (0,02—0,04 %), которые во время плавки переходят в сталь, вызывают ее хладноломкость. В холодном состоянии медь ухудшает пластичные свойства металла. Содержание 0,001 % Sb придает стали хрупкость, мышьяк ухудшает свариваемость. Учитывая растущие требования, предъявляемые к качеству металла со стороны потребителей, в наше время регламентируют содержание нежелательных добавок на уровне 0,001 %. Качество стали определяется также количеством серы и фосфора. Сера снижает пластичность стали, способствует красноломкости стали, т. е. способности к образованию трещин при высоких температурах, понижению сопротивления усталости, уменьшению сопротивления коррозии; резко ухудшает качество поверхности готового проката, снижает ударную вязкость. В некоторых случаях она может быть использована как легирующий элемент для получения особых свойств, необходимых для механической обработки — хрупкости стружки автоматной стали. Но обычно с серой в сталеплавильном производстве борются всеми доступными способами. Наиболее резко сера проявляет свои негативные качества при низких отрицательных температурах. Содержание серы в стали, которая используется для деталей, работающих при низких температурах, находится на минимальном уровне (0,005—0,008 %). Большое значение имеет наличие серы при разливке стали на машинах непрерывного литья заготовок. Технологическими нормами и заводскими инструкциями для этого способа регламентируется содержание серы: для обычных марок стали — менее 0,025 %, при разливке в изложницы — менее 0,035 %. При содержании серы более 0,02 % количество поверхностных дефектов на слябах увеличивается приблизительно вдвое. Для готовой стали, которую подвергают холодной прокатке и протяжке, необходимо минимально допустимое содержание серы. Сера влияет на формирование структуры отливок, особо важное значение это приобретает при отливке крупных и особо крупных слитков и отливок. Нежелательным элементом в стали является фосфор, который вызывает склонность рельсовой стали к насыщению водородом и образованию флокенов, а канатной стали — к ухудшению механических свойств и др. Область использования и сортамент стали, выплавляемой в кислородных конвертерах, расширяется с каждым годом. Кислородно-конвертерная сталь используется в наиболее ответственных областях: судостроении, строительстве мостов, трубопроводов высокого давления, автомобилестроении, для изготовления рельсов различного назначения и т. д.
|
|
|
|
|
|
|
|
ТЭП ККП с продувкой конвертера сверху техническим кислородом.
Для сравнения технологических процессов и определения наиболее выгодных необходимо использовать параметры, которые имеют место во всех сравниваемых процессах. Таким показателем экономической эффективности технологических процессов является себестоимость продукции, выраженная в денежной форме.
Экономическая эффективность работы конвертера определяется по формуле:
где П - годовая производительность конвертера, т. стали в год; Т -масса металла, шихты; 1440 - число минут в сутках; а -выход годных слитков; п -число рабочих суток в году; t - длительность плавки, мин.
Основной показатель, характеризующий производительность мартеновских печей, является съем стали с 1 м2 площади пода печи в сутки с (т/м2):
где C - съем стали, Р--суточная производительность, S - площадь пода печи, м2.
Так, более высокие технико-экономические показатели у кислородно-конвертерного способа выплавки стали. Это обусловленно рядом его преимуществ: большая производительность агрегата на единицу емкости и одного рабочего, ниже (на 54-10%) удельные капитальные затраты на строительство цеха той же производительности, меньше в 2-3 раза расход огнеупоров на единицу мощности агрегата. Экономическая эффективность обеспечивается за счет снижения ее себестоимости путем снижения расходов по переделу, доля которого в себестоимости составляет до10% (13-14% при мартеновской плавке; 25% -- при электроплавке).
Для управления конвертерной плавкой разработаны математические модели процесса, основанные на вещественном и термическом балансе плавки. На основании математического описания процесса создается программка для компьютера, в которую вводят начальные данные о составе чугуна, флюсов, охладителей, количестве сыпучих, температуре чугуна, чистоте кислорода, основности конечного шлака, составе и температуре готовой стали и т.п. Компьютер на базе приобретенной инфы и уравнений математической модели процесса предсказывает ход плавки, рассчитывает количество и время присадок, расход кислорода на плавку и момент окончания продувки, рассчитывает нужное количество раскислителей, вводимых в ковш.
Главные технико-экономические характеристики работы конвертерных цехов последующие: Вместимость конвертеров, т……………………………………..100-350 длительность, мин: продувки………………………………………………………….15-24 цикла плавки……………………………………………………..30-50 годичная производительность цеха, млн т слитков: три 100-т конвертера…………………………………………...2,5-3,0 три 250-т конвертера…………………………………………...4,7-5,0 выход пригодного, %………………………………………………..…..89-92 расход, на 100 кг стали: извести, кг………………………………………………………….6-10 лома, кг…………………………………………………………....18-27 расход кислорода, м3/т стали……………………………………..….50-56 расход огнеупоров на футеровку конвертеров, кг/т стали…………....2-4 стойкость футеровки, число плавок………………………………400-800. Вместимость конвертеров, т……………………………………..….20-180 длительность, мин: продувки………………………………………………………....18-28 цикла плавки…………………………………………………….…50-65 выход пригодного, %……………………………………………………..87-89 расход кг/100 кг стали: извести……………………………………………………………..10-16 лома………………………………………………………………...20-35 расход кислорода, м3/т стали………………………………………...60-63 стойкость футеровки, число плавок………………………...…….120-450. Недочетами конвертерного процесса являются сложность и высочайшая цена чистки отходящих газов, также необходимость использования в шихте водянистого чугуна.
Дата добавления: 2018-04-04; просмотров: 592; Мы поможем в написании вашей работы! |
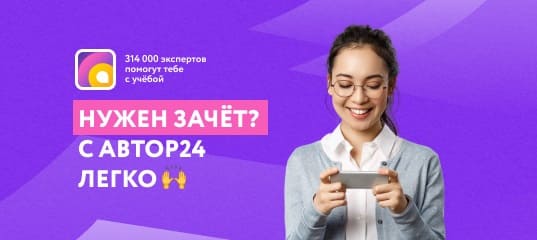
Мы поможем в написании ваших работ!