Виды охрупчивания сталей и их причины
ДЕГРАДАЦИОННЫЕ ПРОЦЕССЫ ОБОРУДОВАНИЯ И МАТЕРИАЛОВ
11.1. Деградационные процессы, виды предельных состояний
При эксплуатации технологического оборудования в той или иной мере, в зависимости от условий и режимов работы, происходит деградация конструкционных материалов. Деградация— явление, наблюдающееся в материалах с течением длительного времени и выражающееся в соответствующем снижении способности конструкции сопротивляться воздействию на нее различных нагрузок и, соответственно, снижающее остаточный ресурс оборудования.
Диагностирование технического состояния оборудования и прогноз его изменения при дальнейшей эксплуатации осуществляется на основе анализа деградационных процессов и выявления определяющих параметров технического состояния. Определяющие параметры технического состояния (ПТС) — это параметры, изменение которых в отдельности или в некоторой совокупности приводит оборудование в неработоспособное состояние.
В нефте- и газодобывающей и перерабатывающей промышленности выделяют следующие деградационные процессы, приводящие к потере работоспособности технологического оборудования:
• изменение геометрии конструкции или отдельных ее элементов;
• поверхностное изнашивание или коррозийное повреждение;
• образование и развитие макродефектности;
• деградация (старение) механических свойств материалов.
|
|
В зависимости от действующего механизма деградационного процесса различают следующие виды предельных состояний:
• вязкое, усталостное или кратковременное хрупкое разрушение элемента или всей конструкции;
• предельная пластическая деформация металлоконструкции, обусловленная прогибом или нарушением устойчивости несущих элементов, образованием «пластических шарниров» или явлениями ползучести, определяющая необходимость прекращения ее эксплуатации;
• разгерметизация или течь конструкции.
Определяющими параметрами, приводящими к перечисленным видам предельных состояний, являются напряженно-деформированное состояние элементов конструкции, механические свойства конструкционных материалов, степень поражения коррозией, количество и размеры повреждений и дефектов.
Характеристики деградационных процессов
Рассмотрим основные характеристики и особенности деградационных процессов в порядке, перечисленном выше.
Процессы изменения геометрии охватывают широкий круг явлений и могут иметь как локальный, так и общий характер, касающийся конструкции в целом. К их числу относят: отклонения от начальной (исходной) формы технологического оборудования (отклонения от прямолинейности, плоскостности, вертикальности, цилиндричности и др.), образование гофр, отдулины, расслоения и т. д. Их причинами наряду с природными явлениями (например, пучение грунта при промерзании, оползни и др.) и эксплуатационными нагрузками является и деградация материалов.
|
|
Роль материалов в указанном выше перечне явлений может быть различной [12]. Так, при формировании отдулин и расслоений существенно влияние химического состава и структуры сталей. Наибольшую склонность к образованию отдулин обнаруживают в сосудах и аппаратах давления, эксплуатируемых в контакте с водородсодержащей средой (особенно при наличии сероводорода) и выполненных из кремнемарганцовистых (16ГС, 09Г2С) и марганцовистых (09Г2, 14Г2) сталей.
Наличие в этих сталях, раскатанных при прокатке пластичных сульфидов и оксисульфидов способствует скоплению водорода на границах раздела ферритная матрица - включение. Дальнейшее накопление водорода в стали сопровождается его молизацией в пустотах (порах). Водород из атомарного состояния переходит в молекулярное, вызывая повышение давления на границе раздела феррит-включение. Отмечено повышение давления водорода в указанных выше ловушках до 70 и даже до 150 атм, что в ряде случаев существенно превышает рабочее давление в аппаратах.
|
|
Изнашивание — это процесс разрушения и отделения материала с поверхности твердого тела при трении, проявляющийся в постепенном изменении размеров и формы тела (ГОСТ 22674—88. «Обеспечение износостойкости изделий»). Интенсивность изнашивания определяют в единицах объема, массы, длины и др. Износостойкость оценивается величиной, обратной скорости или интенсивности изнашивания.
Изнашивание по характеру воздействия на поверхность трения принято подразделять на следующие виды:
• механическое изнашивание, к которому относятся абразивное (включая гидро- или газоабразивное), эрозионное (в том числе гидро- или газоэрозионное), кавитационное, усталостное, изнашивание при фреттинге, изнашивание при заедании;
• коррозийно-механическое: окислительное, изнашивание прифреттинг-коррозии, водородное, электроэрозионное.
Классическая диаграмма изменения скорости износа по времени включает три участка (см. рис. 1.2): участок приработки деталей, характеризуемый большой скоростью износа; участок установившегося износа (износ с относительно стабильной скоростью); участок катастрофического износа вплоть до предельного состояния.
|
|
Для оценки износа используют различные методы в зависимости от вида оборудования: прямое измерение с помощью различных мерительных инструментов; толщинометрию с помощью ультразвуковых или иных толщиномеров; контроль содержания металла в смазочном материале и др. Все большее применение находит метод поверхностной или тонкослойной активации, основанный на локальном облучении изнашиваемой поверхности изделия и измерении интенсивности излучения образованной радионуклидной метки. Изменение интенсивности излучения при эксплуатации изделия переводится в характеристики износа по градуировочному графику. Контроль осуществляется дистанционно и позволяет оценивать износ от десятых долей микрометра до нескольких миллиметров с точностью 5...15 %. Данный метод применяют как для контроля машинного оборудования, так и для емкостного (сосуды, резервуары, трубопроводы и др.).
Коррозийная стойкость конструкционного материала — одна из важнейших, а зачастую и самая важная характеристика, определяющая надежность и срок службы технологического оборудования.
Коррозия (от лат. corrodere — пожирать, изгладывать) — это процесс разрушения металлических материалов в результате их физико-химического взаимодействия с компонентами окружающей среды. Коррозия — это процесс, посредством которого сплавы железа возвращаются в более стабильную химическую форму, характерную для окиси; процесс, прямо противоположный металлургическим процессам, не нуждающийся в каких-либо энергетических затратах.
Коррозия является сложным процессом, зависящим от многих факторов и от их конкретного сочетания. Учитывая это многообразие, коррозию классифицируют по следующим признакам:
• по механизму протекания коррозийного процесса — химическая (в газовой или жидкостной среде, не проводящей электрический ток) и электрохимическая (в среде электролита). В большинстве случаев коррозийное поведение металлов является частным случаем их электрохимического поведения;
• по типу агрессивных сред, в которых протекает коррозия —
коррозия в газовой или жидкостной среде, особенно при высоких
температурах; биокоррозия под воздействием продуктов жизнедеятельности микроорганизмов; коррозия в почве под действием растворов солей, содержащихся в грунте; коррозия блуждающим током; коррозия, обусловленная воздействием атмосферных осадков с поверхностью металла. При контакте двух металлов различной активности с электролитом образуется гальваническая пара. Электроны
переходят от более активного металла к менее активному, при этом
более активный металл разрушается;
• по условиям протекания коррозийного процесса — контактно-
электрохимическая коррозия, вызванная контактом металлов, имеющих разные стационарные потенциалы в данном электролите; контактная (в зоне контакта разнородных металлов в среде электролита); щелевая, протекающая на участках поверхности возле конструкционных или технологических зазоров между двумя металлами, а также в местах неплотного контакта металла с неметаллическим коррозийно-инертным материалом; избирательная (компонентно-избирательная и структурно-избирательная), связанная с повышенной коррозийной активностью одного из компонентов сплава; коррозийно-эрозионная (фреттинг-коррозия), обусловленная одновременным воздействием коррозийной среды и микроскопических смещений сдвига в результате вибрации в местах контакта плотно сжатых или катящихся одна по другой деталей; коррозийная кавитация, являющаяся результатом коррозийного и одновременно ударного воздействия из-за образования кавитационных полостей в жидкости; коррозия под напряжением (стресс-коррозия), сопровождающаяся растрескиванием металла в результате одновременного воздействия растягивающих напряжений и агрессивной среды. Необходимым условием коррозийного растрескивания является наличие специфических компонентов в составе коррозийной среды. Для сплавов на основе меди таким компонентом является аммиак, для нержавеющих сталей — хлориды и щелочи, в то время как в растворах серной, азотной и уксусной кислоты, а также в чистой воде они не подвержены этому виду разрушения.
Следует иметь в виду, что при коррозии под напряжением растрескивание может произойти и в результате наводороживания. Этот вид разрушения называется водородным растрескиванием (из-за давления до 70...150 атм в зонах скопления водородомолизации, а также из-за облегчения роста трещин в результате снижения пластичности наводороженного металла перед ее вершиной).
Коррозийная усталость также относится к типу коррозийного растрескивания под напряжением. Однако в этом случае напряжения не статические, а переменные. Коррозийно-усталостное разрушение начинается при одновременном воздействии на металл циклических напряжений и коррозийных повреждений в виде язв, каверн и межкристаллитной коррозии. Эти повреждения являются очагами зарождения многочисленных трещин, разветвляющихся по мере роста и заканчивающихся пучками (напоминающими корневую систему растений), ориентированными в разные стороны. Коррозийно-усталостное повреждение металла проявляется понижением предела его выносливости, который при этом непрерывно понижается с увеличением числа циклов нагружений. Другими словами, четко выраженный горизонтальный участок, соответствующий пределу неограниченной выносливости, на кривой усталости металла с коррозийно-усталостными трещинами отсутствует.
По характеру коррозийного разрушения на поверхности или в объеме металла коррозию разделяют на сплошную, равномерную по всей поверхности или неравномерную на различных участках и местную.
Местную коррозию подразделяют на следующие виды:
• пятнами, диаметр которых больше глубины прокорродировавшего слоя металла;
• язвенная, в виде каверн, диаметр которых соизмерим с их глубиной;
• питтинговая или точечная в виде множества отдельных точек диаметром 0,1...2 мм значительной глубины;
• межкристаллитная, характеризуемая избирательным растворением металла по границам зерен;
• ножевая (является разновидностью межкристаллитной), разрезающая металл словно ножом вдоль шва в зоне термического влияния сварки и возникающая при использовании некоторых сплавов в
особо агрессивных условиях;
• подповерхностная, начинающаяся от точечных поражений и распространяющаяся в стороны под очень тонким, например наклепанным, слоем металла, который затем вздувается пузырями или шелушится;
• ручейковая в виде узкой полоски на внутренней поверхности нефтепровода, обусловленная потоком нефти;
• нитевидная, возникающая под защитными покрытиями при их местном повреждении под действием капиллярных сил.
Особо опасными видами местной коррозии вследствие трудности их обнаружения являются межкристаллитная, стресс-коррозия (коррозийное растрескивание под напряжением), а также ножевая коррозия.
Способность сопротивляться разрушающему воздействию коррозийной среды характеризует коррозийную стойкость металла. ГОСТ 9.908—90 устанавливает десятибалльную шкалу коррозийной стойкости металлов при условии их равномерной коррозии (табл. 11.1).
Таблица 11.1
Группа стойкости | Скорость коррозии, мм/год | Балл |
I. Совершенно стойкие | < 0,001 | 1 |
II. Весьма стойкие | 0,001. ..0,005 0,005.. .0,01 | 2 3 |
III. Стойкие | 0,01. ..0,05 0,05.. .0,1 | 4 5 |
IV. Пониженностойкие | 0,1... 0,5 0,5.. .1,0 | 6 7 |
V. Малостойкие | 1,0.. .5,0 5,0.. .10,0 | 8 9 |
VI. Нестойкие | >10,0 | 10 |
Наряду с металлами состояние оборудования определяется также состоянием материалов уплотнительных устройств. Эластичные герметизирующие материалы испытывают на стойкость к воздействию агрессивных сред при заданных температурах и продолжительности испытаний.
В сумме косвенные и прямые убытки от коррозии металлов и затраты на защиту от нее в развитых странах составляют около 4 % валового национального дохода. Часть этих затрат неизбежна, тем не менее потери от коррозии можно существенно сократить при использовании специальных методов и средств борьбы с ней. Требования к защите промышленного оборудования от коррозии установлены Единой системой стандартов защиты от коррозии и старения материалов (ЕСЗКС). Основные количественные показатели различных видов коррозии и коррозийной стойкости материалов и методы испытаний на коррозию стандартизованы целой группой ГОСТов (около 40).
По данным ООО НТЦ «Диатэкс» [12], на долю общей коррозии (утонение стенки) приходится не более 28 % отказов нефтехимического оборудования из-за коррозийных повреждений. Более важное значение имеют другие виды коррозии, при которых повреждения носят локальный характер, т. е. сосредоточены на ограниченном участке поверхности металла. Основная масса отказов обусловлена коррозийным растрескиванием (~ 24 %), межкристаллитной коррозией (~ 15 %), питтинговой коррозией (- 14 %), коррозийно-механическим износом (~ 7 %) и другими видами коррозии (- 13 %). Особо следует отметить повреждение металла под действием водорода (водородное растрескивание), которое не относится к коррозии, но вызывается ею.
Определяющими параметрами, приводящими оборудование, подвергшееся коррозии, в предельное состояние, являются: потеря прочности при уменьшении толщины стенки; наличие растрескивания металла, коррозийных язв, питтинга в зоне сварных швов; распространение дефектов (трещин, коррозийных язв и др.) на регламентированную нормативной документацией площадь и глубину.
Процессы зарождения и развития макродефектности в элементах конструкций определяются следующими факторами:
• величиной эксплуатационных нагрузок;
• величиной остаточных напряжений после сварки;
• химическим составом и структурой материала.
Вклад химсостава и структуры в образование макродефектности особенно весом для таких опасных явлений, как коррозийное растрескивание под напряжением, стресс-коррозия, сульфидное растрескивание и т.д.
Наличие крупнозернистой и неоднородной структуры также способствует возникновению и развитию межзеренного разрушения и образованию трещин. Данный эффект в большей степени встречается в околошовной зоне сварных соединений — зоне термического влияния (ЗТВ). Практика технического диагностирования показывает, что в элементах конструкций, имеющих крупнозернистую структуру (с размером ферритных зерен 100...300 мкм и более), доля межзеренного разрушения достигает 35...40%, что облегчает зарождение и развитие трещин под воздействием остаточных сварочных, а также эксплуатационных напряжений.
Деградация (старение) материалов, включая и конструкционные стали, с течением времени проявляется в ухудшении механических свойств, определяющихся в первую очередь их химическим составом и микроструктурой, и обусловлена термодинамической неравновесностью исходного состояния материала и постепенным приближением его структуры к равновесному состоянию в условиях диффузной подвижности атомов.
Анализ эксплуатационных факторов, действующих на металл, позволяет выделить следующие процессы, приводящие его к старению:
• разупрочнение — проявляется в том, что прочностные характеристики металла (временное сопротивление или условный предел текучести) отличаются от исходных (нормативных) более чем на 5 % в меньшую сторону. Может быть следствием длительного пребывания металла при высокой температуре, например во время пожара;
• циклическое воздействие нагрузок — вызывает микропластические деформации в зонах концентрации напряжений в результате накопления дислокаций, ускоряющих развитие повреждаемости металла;
• охрупчивание — является наиболее опасным следствием изменения физико-механических свойств материала (применительно к сталям, имеющим объемно-центрированную кубическую решетку: углеродистым и малолегированным). Охрупчивание сдвигает область хрупкого разрушения в область положительных температур, резко снижает трещиностойкость и приводит к внезапному разрушению
конструкции.
Изменение механических свойств, обусловленных развитием процессов охрупчивания, выражается, с одной стороны, в увеличении твердости материала и предела его текучести, с другой — в снижении вязкопластических показателей, показателей ударной вязкости и трещиностойкости. В различных нормативных документах используются различные предельные показатели, характеризующие процессы охрупчивания. Так, в ПБ 03-605-03 «Правила устройства вертикальных стальных резервуаров для нефти и нефтепродуктов» приведена минимальная ударная вязкость материала. Для шаровых резервуаров и газгольдеров для хранения сжиженных газов под давлением в соответствии с РД 03-380—00 предельными являются увеличение отношения предела текучести к временному сопротивлению свыше 0,75 для легированных сталей и свыше 0,65 для углеродистых, при этом относительное удлинение для легированных сталей не должно быть менее 17 %, а для углеродистых — менее 19 %. Для стальных подземных газопроводов по РД 12-411—01 для труб из малоуглеродистой стали допустимое отношение фактического предела текучести к временному сопротивлению, приведенных к температуре 20 °С, должно быть не более 0,9, ударная вязкость КСU — не менее 30 Дж/см2.
Деградация наиболее характерна для полимерных материалов. Она приводит к необратимому изменению свойств под воздействием механических или термических напряжений, солнечного света, газовых и жидкостных химических сред, ионизирующих излучений и других факторов. Причины старения полимерных материалов — химические и структурные превращения макромолекул. Следствие старения — ухудшение механических характеристик и последующее разрушение полимерного изделия.
Виды охрупчивания сталей и их причины
Различают два вида охрупчивания стали: внутризеренное охрупчивание, вызванное наклепом внутренних объемов зерен ферритной матрицы, и межзеренное, обусловленное ослаблением границ зерен и снижением их когезивной (зернограничной) прочности. В общем случае суммарную степень охрупчивания можно представить в виде
где -- степень охрупчивания вследствие наклепа зерен и ослабления их когезивной прочности соответственно.
Различают технологические и эксплуатационные факторы охрупчивания сталей. Первые возникают в процессе изготовления, транспортировки и монтажа конструкции, вторые — в процессе ее эксплуатации.
К технологическим факторам охрупчивания относятся все виды воздействий на стадиях изготовления, транспортировки и монтажа оборудования, связанных с пластическим деформированием стали (например, вальцовка оболочек, холодная штамповка днищ, подгиб кромок обечаек, усадка металла в околошовной зоне при сварке и т.д.), а также ускоренное охлаждение сварных швов, приводящее к образованию крупнозернистых структур, наводороживание сварных швов при попадании влаги в сварочную ванну или использование непросушенных материалов и т.д.
Многочисленными исследованиями (ЦНИИПСК им.Мельникова) установлено, что при пластической деформации стали, например СтЗсп, на 3...5 % плотность дислокаций в феррите возрастает на полтора-два порядка, т. е. увеличивается плотность дефектов кристаллической решетки. Наличие в металле многочисленных дислокаций, имеющих зоны растяжения, вызывает приток в эти зоны атомов внедрения типа углерода и азота. Закрепление дислокаций атомами внедрения приводит к снижению их подвижности и, соответственно, к повышению предела текучести. Этот эффект проявляется также в элементах конструкции, испытывающих перегрузки и работающих в условиях малоцикловой усталости.
Явление повышения предела текучести и сопутствующее ему охрупчивание стали получило название деформационного старения.
В ряде случаев неучет этого явления приводит к большим экономическим потерям. Так, по данным В.М. Горицкого (ЦНИИПСК им. Мельникова), вследствие недостаточной хладостойкости стали и хрупкого трещинообразования в зоне кольцевых швов в 2002 г. на Ангарском нефтехимическом комбинате были списаны четыре сварных вертикальных резервуара для хранения нефти объемом 30 000 м3 каждый. Для стенок резервуаров использовали листовую сталь 09Г2С 12-й категории толщиной 12...18 мм. Многие партии горячекатаного проката имели минимальный запас хладостойкости. Пластическая деформация стали, возникающая при рулонной технологии сборки, вызвала охрупчивание металла. В результате только 50 % обследованных листов после технологической операции рулонирования удовлетворяли требованиям ГОСТ 19281-89 к стали 09Г2С 12-й категории.
В связи с этим в нормативных документах, разработанных в последние годы, эффект деформационного старения учитывается. Так, в «Правилах устройства вертикальных цилиндрических стальных резервуаров для нефти и нефтепродуктов» (§2.4.3 ПБ 03-605-03) для резервуаров с рулонной технологией сборки, по сравнению с полистовой, расчетная температура металла при толщинах свыше 10 мм понижается на 5 °С.
К эксплуатационным факторам относят все виды механических, тепловых, коррозийных и химических воздействий на металл в период эксплуатации конструкции. К их числу относят:
• длительное воздействие повышенных температур (250...500 °С), приводящих к укрупнению зерна феррита и развитию обратной отпускной хрупкости;
• появление закалочных крупнозернистых структур в зоне сварных швов при нарушении технологии сварки в процессе ремонта (попадание влаги в сварочную ванну) или при ускоренном охлаждении сварного соединения (например, при сварке в зимний период без предварительного подогрева свариваемого металла);
• наводороживание металла сварных швов (при попадании влаги в сварочную ванну или при использовании непросушенных электродов и сварочных материалов);
• коррозийное растрескивание под напряжением, обусловленное воздействием механических нагрузок и электрохимических процессов коррозии;
• сезонную подвижку фундаментов опор машины и примыкающих трубопроводов, кратковременные перегрузки в период пуска или испытаний под нагрузкой и др.
Рис. 11.1. Схема изменения температурной зависимости трещиностойкости Кс стали вследствие зернограничного охрупчивания
Наиболее сложно обеспечить требуемое качество сварных швов при ремонте наводороженных в период эксплуатации металлоконструкций. При сварке такого металла сварочная ванна «кипит», а наплавленный металл при затвердевании обладает большой пористостью, приводящей к растрескиванию. Для получения удовлетворительного качества сварного соединения необходимо предварительно удалять водород путем нагрева наводороженной конструкции до температуры 500...550 °С и выдержки в течение 3...4 ч.
Второй вид охрупчивания, обусловленный снижением прочности границ зерен, является наиболее опасным. При зернограничном охрупчивании смещение температуры вязко-хрупкого перехода может достигать сотен градусов (рис. 11.1) [12].
Зернограничное охрупчивание может происходить под воздействием азотирования и науглероживания поверхностных слоев стали, обусловленных наличием (при повышенных температурах эксплуатации) в среде соответственно азота или углерода, или из-за сегрегации вредных примесей типа фосфора, сурьмы, мышьяка и т.д. и выделения карбидов по границам зерен при длительном (более 100 ч) воздействии повышенных (250...500 °С) температур. Наиболее частой причиной зернограничного охрупчивания материалов оборудования газонефтедобывающей и перерабатывающей промышленности является наводороживание металла из-за наличия в технологическом продукте сопутствующего сероводорода или других водородсодержащих газовых или жидкостных сред.
Сероводород сопутствует добыче нефти и природного газа, и для разных месторождений его содержание составляет 9...25 %. В присутствии воды происходит каталитическая реакция с выделением водорода и сернистого железа
H2S+Fe
Атомарный водород, имеющий малый диаметр, проникая в металл по границам раздела фаз и несплошностям, скапливается в порах ферритной матрицы. Дальнейшее накопление водорода приводит к его молизации, сопровождающейся возникновением повышенного давления в порах. На процесс диффузии водорода влияют поле напряжений, градиент температуры и дефектность строения металла. При неблагоприятном сочетании этих факторов в металле происходит сероводородное растрескивание и расслоение, которое может возникать внутри конструкции вдалеке от ее поверхности. Склонность к сероводородному растрескиванию под напряжением (СРН) определяется особенностями структуры металла: наличием структурных неоднородностей, количеством и распределением неметаллических включений, химическим составом. СРН более характерно для высокопрочных сталей аустенитного и аустенитно-мартенситного классов и возникает чаще всего в зонах термического влияния сварных швов. Сероводородному расслоению подвергаются, как правило, сосуды, аппараты и трубопроводы из углеродистых и низколегированных сталей; в отдельных случаях может происходить СРН сварных соединений.
Дата добавления: 2018-04-04; просмотров: 2407; Мы поможем в написании вашей работы! |
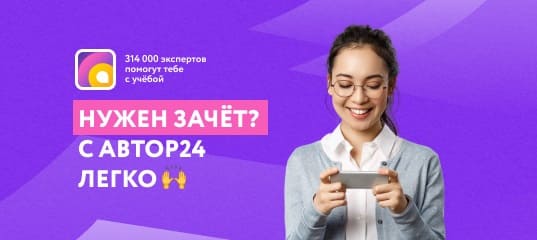
Мы поможем в написании ваших работ!