Тема 2. Металлические материалы
15.02.2018
Задание на период карантина с 14.02 по 22.02.2018
Для групп С-21 и С-22
МДК01.01. Строительные материалы и изделия
Преподаватель: Артемьева А.И.
Тема | Задание | Форма отчета |
Тема 1. Стекло | 1. Используя лекцию (см. ниже), написать конспект в тетради. | Конспект в тетради |
3. Написать сообщение «Производство стекла» | Письменно в тетради, объем работы минимум 2 листа | |
5. Подготовиться к Проверочной работепо теме. | На уроке после карантина | |
Тема 2. Металлические материалы | 1. Используя лекцию (см. ниже), написать конспект в тетради | Конспект в тетради |
2. Составить тест по теме, 10-15 вопросов и 3 варианта ответа. Критерии оценок: «15 вопросов» - 5 «12 вопросов» - 3 «10 вопросов» -4 | Сдать на уроке после карантина | |
3. Подготовиться к проверочной работе по теме. | На уроке после карантина |
Тема 1. Стекло и изделия из стекла.
Классификация и свойства стекол.
Стекло –твердое аморфное вещество, способное после нагревания до вязкотекучего состояния снова превращаться при определенном режиме охлаждения в твердое вещество. Стекла получают путем переохлаждения расплава независимо от их состава и температурной области затвердевания. Они обладают в результате постепенного увеличения вязкости механическими свойствами твердых тел, причем процесс перехода из жидкого состояния в стеклообразное должен быть обратимым.
|
|
По происхождениюстекла подразделяют на природные и искусственные. К природнымотносят стекла, образованные в процессе деятельности вулканов при извержении магмы, например, обсидиановое стекло. К искусственнымотносят стекла, создаваемые в процессе производства из многокомпонентной смеси.
Искусственные стекла по составу бывают органические и неорганические. Органические стекла получают на основе продуктов органического происхождения, в основном смол. Они представляют собой органические полимеры – полиакрилаты, поликарбонаты, полистирол, сополимеры винилхлорида с метилметакрилатом – находящимися в стеклообразном состоянии. Наибольшее практическое применение нашли стекла на основе полиметилметакрилата. Подавляющее большинство искусственных промышленных стекол относятся к неорганическим.
По типу неорганических соединений различают следующие классы стекол: элементарные, галогенидные, халькогенидные, оксидные, металлические, сульфатные, нитратные, карбонатные и др.
Промышленные стекла по назначению подразделяются на строительное, техническое, электровакуумное, оптическое, тарное, химико-лабораторное, безопасное, сортовое и другие.
В группу строительное стекло входят: листовое оконное и витринное (полированное и неполированное); листовое армированное и узорчатое; конструктивно-строительные элементы (пустотелые стеклянные блоки, профилированное стекло); архитектурно-художественное стекло (листовое цветное стекло, стеклянная мозаика и облицовочная плитка).Электровакуумное стекло применяют для изготовления оболочек ламп накаливания, люминесцентных ламп, ламп высокоинтенсивных источников света – кварцевых и галогенных, телевизионных кинескопов, электронно-лучевых трубок, различных устройств рентгеновской техники, оболочек радиоэлектронных ламп, межслойной изоляции гибридных интегральных электронных схем, компонентов резисторов, конденсаторов.
|
|
Технические стекла – предназначены для изменения интенсивности, характера спектра и направления проходящих через них световых потоков. К светотехническим относятся стекла, работающие в диапазоне электромагнитных волн, охватывающем ультрафиолетовую, видимую и инфракрасную области. В соответствии с назначением выделяют следующие группы технических стекол:рассеивающие, призматические, стекла с избирательным поглощением.
Тарное стекло – предназначено для расфасовки, хранения, транспортирования продуктов различной консистенции.
|
|
Химико-лабораторное стекло, из него изготовляют колбы, пипетки, дистилляционные колонки. Применение стекла обеспечивает высокую степень чистоты продуктов, легкость очистки и прозрачность, которая позволяет наблюдать за ходом процесса.
Особую группу составляют цирконий-содержащие стекла, термометрическое стекло, медицинское стекло, водомерные стекла, стеклянные фильтры.
Безопасное стекло–это стекла, при разрушении не дающие острых разлетающихся осколков. К ним относят безосколочное трехслойное стекло - триплекс, армированное стекло и закаленное стекло.
Специальное стекло. К таким материалам следует отнести лазерные, фото- и полихромные стекла, стекла для стекловолоконной оптики, металлические стекла.
Сортовое стекло – к нему относят обширный класс стеклоизделий, вырабатываемых из хрустальных, бесцветных и окрашенных стекол методами ручного и механизированного выдувания и прессования. Они служат для употребления в быту, хранения жидких пищевых продуктов, украшения жилица. Сортовые стеклоизделия должны отличаться высоким качеством стекла. По основным признакам изделия из сортового стекла классифицируют следующим образом: по назначению: столовая посуда, посуда для вина и напитков, художественно-декоративные изделия; по способу выработки (выдувные, прессовыдувные, прессованные, полученные методом свободного выдувания, скульптура); по виду стекла: бесцветные, хрустальные, цветные.
|
|
Изделия из стекла классифицируют;
— по способу формования (выработки);
— форме;
— размерам;
— видам и сложности декорирования;
— комплектности;
— назначению.
По способу формования стеклоизделия подразделяются:
— на прессованные;
— прессовыдувные;
— выдувные;
— тянутые;
— моллированные.
Изделия из стекла.
1.Стеклопакеты - между листами стекла находится прослойка из сухого воздуха или инертного газа. Листы соединяют в стеклопакет спайкой.
2.Стеклянные блоки – для получения светопрозрачной ограждающей конструкции с хорошими тепло- и звукоизоляционными характеристиками. Внутренняя поверхность блоков имеет рифление для рассеивания света. Размеры от 200х200 до 400х400 мм при толщине до 100 мм.
3.Стеклянные трубы изготавливают из обычного прозрачного стекла способом вертикального или горизонтального вытягивания. Длина труб 1000-3000 мм, внутренний диаметр 38-200 мм. Трубы выдерживают гидравлическое давление до 2 МПа.
4.Стекловолокно – для получения стеклоткани и стекловойлока, которые испльзуют как армирующий компонент при производстве стеклопластика или основы в рулонных кровельных и гидроизоляционных материалах.
5.Пеностекло – блоки из стекла, вспученного в момент нахождения в расплавленном состоянии. Применяется как теплоизоляционный материал.
6.Стемалит представляет листовое стекло различной фактуры, покрытое с одной стороны глухими керамическими кристаллами разного цвета. Изготавливают его из неполированного витринного или прокатного стекла толщиной 6-12 мм. Применяют его для наружной и внутренней облицовки зданий, изготовления стеновых панелей
Ситаллы и шлакоситаллы.
Ситаллы получают путём введения в расплавленную стеклянную массу специального состава катализаторов кристаллизации. Из такого расплава формируют изделия, затем их охлаждают, в результате чего расплавленная масса превращается в стекло. При последующей тепловой обработке стекла происходит его полная или частичная кристаллизация — образуется ситалл. Они имеют большую прочность, малую среднюю плотность, высокую износостойкость. Их применяют при облицовке наружных или внутренних стен, изготовления труб, плит для полов.
Шлакоситаллы получают на основе металлургических шлаков и модификаторов. У них высокая прочность, износостойкость и химическая стойкость. По долговечности может конкурировать с природными каменными материалами (гранит, габбро и т.п.).
Тема 2. Металлические материалы
Металлические материалы принято классифицировать по основному компоненту. По ряду признаков их разбивают на группы:
1.Чёрные металлы:
1)железистые (железо, никель);
2)тугоплавкие (с температурой плавления > 1539°);
3)урановые (уран, плутоний);
4)редкоземельные (церий, неодим);
5)щелочноземельные (калий, натрий).
2.Цветные металлы:
1)лёгкие (магний, алюминий);
2)благородные (золото, платина);
3)лёгкоплавкие (висмут, свинец).
Кматериалам чёрной металлургии принадлежат стали, чугуны, ферросплавы и сплавы на основе железа, легированные цветными металлами в количестве, превосходящем стали.
Кматериалам цветной металлургии принадлежат важнейшие цветные металлы – алюминий, медь, цинк, свинец, никель, олово и сплавы на их основе. К металлическим материалам относятся и материалы порошковой металлургии.
Стали
Сталью называется сплав железа с углеродом, в котором углерода содержится не более 2,14 %. Это теоретическое определение. На практике в сталях, как правило, не содержится углерода более 1,5 %.
Влияние углерода и примесей на свойства стали.Углерод существенно влияет на свойства стали даже при незначительном изменении его содержания. В стали имеются две фазы – феррит и цементит (частично в виде перлита). Количество цементита возрастает прямо пропорционально содержанию углерода. Как уже говорилось, феррит характеризуется высокой пластичностью и низкой твёрдостью, а цементит, напротив, очень низкой пластичностью и высокой твёрдостью. Поэтому с повышением содержания углерода до 1,2 % снижаются пластичность и вязкость стали и повышаются твёрдость и прочность.
Повышение содержания углерода влияет и на технологические свойства стали. Ковкость, свариваемость и обрабатываемость резанием ухудшаются, но литейные свойства улучшаются.
Кроме железа и углерода в стали всегда присутствуют постоянные примеси. Наличие примесей объясняется технологическими особенностями производства стали (марганец, кремний) и невозможностью полного удаления примесей, попавших в сталь из железной руды (сера, фосфор, кислород, водород, азот). Возможны также случайные примеси (хром, никель, медь и др.).
Марганец и кремнийвводят в любую сталь для раскисления, т.е. для удаления вредных примесей оксида железа FеО. Марганец также устраняет вредные сернистые соединения железа. При этом содержание марганца обычно не превышает 0,8 %, а кремния – 0,4 %. Марганец повышает прочность, а кремний – упругость стали.
Фосфоррастворяется в феррите, сильно искажает кристаллическую решётку, снижая при этом пластичность и вязкость, но повышая прочность. Вредное влияние фосфора заключается в том, что он сильно повышает температуру перехода стали в хрупкое состояние, т.е. вызывает её хладноломкость. Вредность фосфора усугубляется тем, что он может распределяться в стали неравномерно. Поэтому содержание фосфора в стали ограничивается величиной 0,045 %.
Сератакже является вредной примесью. Она нерастворима в железе и образует с ним сульфид железа FeS, который образует с железом легкоплавкую эвтектику. Эвтектика располагается по границам зёрен и делает сталь хрупкой при высоких температурах. Это явление называется красноломкостью. Количество серы в стали ограничива-
ется 0,05 %.
Водород, азот и кислородсодержатся в стали в небольших количествах. Они являются вредными примесями, ухудшающими свойства стали.
Классификация сталей.По химическому составу стали могут быть углеродистыми, содержащими железо, углерод и примеси, и легированными, содержащими дополнительно легирующие элементы, введённые в сталь с целью изменения её свойств.
По содержанию углерода стали делятся на низкоуглеродистые (до 0,25 % С), среднеуглеродистые (0,25…0,7 % С) и высокоуглеродистые (более 0,7 % С).
По назначению различают стали конструкционные, идущие на изготовление деталей машин, конструкций и сооружений, инструментальные, идущие на изготовление различного инструмента, а также стали специального назначения с особыми свойствами: нержавеющие, жаростойкие, жаропрочные, износостойкие, с особыми электрическими и магнитными свойствами и др.
По показателям качества стали классифицируются на обыкновенного качества, качественные, высококачественные и особо высококачественные. Качество стали характеризуется совокупностью свойств, определяемых процессом производства, химическим составом, содержанием газов и вредных примесей (серы и фосфора). В соответствии с ГОСТом стали обыкновенного качества должны
47
содержать не более 0,045 % Р и 0,05 % S, качественные – не более 0,035 % Р и 0,04 % S, высококачественные – не более 0,025 % Р и 0,025 % S и особо высококачественные – не более 0,025 % Р и 0,015 % S. Углеродистые конструкционные стали могут быть только обыкновенного качества и качественными.
Качественные конструкционные углеродистые стати маркируются цифрами 08, 10, 15, 20, 25, ..., 85, которые обозначают среднее содержание углерода в сотых долях процента. Эти стали отличаются от сталей обыкновенного качества большей прочностью, пластичностью и ударной вязкостью. Если для сталей обыкновенного качества максимальная прочность составляет 700 МПа, то для качественной она достигает 1100 МПа.
Легированные стали
Легированной называют сталь, содержащую специально введённые в неё с целью изменения строения и свойств легирующие элементы. Легированные стали имеют целый ряд преимуществ перед углеродистыми. Они имеют более высокие механические свойства, прежде всего прочность. Легированные стали обеспечивают большую прокаливаемость, а также возможность получения структуры мартенсита при закалке в масле, что уменьшает опасность появления трещин и коробления деталей. С помощью легирования можно придать стали различные специальные свойства (коррозионную стойкость, жаростойкость, жаропрочность, износостойкость, магнитные и электрические свойства).
Стали обыкновенного качества могут быть только углеродистыми, т.е. легированные стали, как минимум, являются качественными.
Маркируются легированные стали с помощью цифр и букв, указывающих примерный химический состав стали. Первые цифры в марке показывают среднее содержание углерода в сотых долях процента. Далее показывается содержание легирующих элементов. Каждый элемент обозначается своей буквой: Н – никель, Г – марганец, Ц – цирконий, Т – титан, X – хром, Д – медь, С – кремний, А – азот, К – кобальт, Р – бор, П – фосфор, Ф – ванадий, М – молибден, Б – ниобий, В – вольфрам, Ю – алюминий. Цифры, идущие после буквы, указывают примерное содержание данного легирующего элемента в процентах. При содержании элемента менее 1 % цифра отсутствует. Например, сталь 12Х18Н10Т содержит приблизительно 0,12 % углерода, 18 % хрома, 10 % никеля, менее 1 % титана. Для некоторых групп сталей применяют другую маркировку, которая будет указана при рассмотрении этих сталей.
Конструкционные стали
Конструкционные стали идут на изготовление деталей машин, конструкций и сооружений. Они должны обеспечивать длительную и надёжную работу деталей и конструкций в условиях эксплуатации. Поэтому основное требование к конструкционным сталям – комплекс высоких механических свойств.
Строительные сталисодержат малые количества углерода (0,1…0,3 %). Это объясняется тем, что детали строительных конструкций обычно соединяются сваркой. Низкое содержание углерода обеспечивает хорошую свариваемость.
Вкачестве строительных используются углеродистые стали Ст2
иСт3, имеющие предел текучести σ0,2=240 МПа. В низколегированных строительных сталях при содержании около 1,5 % Мn и 0,7 % Si предел текучести увеличивается до 360 МПа. К этим сталям относятся 14Г2, 17ГС, 14ХГС. Дополнительное легирование небольшими количествами ванадия и ниобия (до 0,1 %) повышает предел текучести до 450 МПа за счёт уменьшения величины зерна. К сталям такого типа относятся 14Г2АФ, 17Г2АФБ.
Приведённые стали применяют для строительных конструкций, армирования железобетона, магистральных нефтепроводов и газопроводов.
Цементуемые сталисодержат 0,1…0,3 % углерода. Они подвергаются цементации, закалке и низкому отпуску. После этой обработки твёрдость поверхности составляет HRC 60, а сердцевины HRC – 15…40. Упрочнение сердцевины в этих сталях тем сильнее, чем больше содержание легирующих элементов. В зависимости от степени упрочнения сердцевины цементуемые стали можно разделить на три группы.
К сталям с неупрочняемой сердцевиной относятся углеродистые цементуемые стали 10, 15, 20. Их сердцевина имеет ферритоперлитную структуру. Эти стали имеют высокую износостойкость, но
малую прочность (σв= 400…500 МПа). Поэтому они применяются для малоответственных деталей небольших размеров.
К сталям со слабо упрочняемой сердцевиной относятся низколегированные стали 15Х, 15ХР, 20ХН и др. Сердцевина имеет структуру
бейнит. Эти стали имеют повышенную прочность (σв = 750…850 МПа). К сталям с сильно упрочняемой сердцевиной относятся стали 20ХГР, 18ХГТ, ЗОХГТ, 12ХНЗ, 18Х2Н4В и др. Серцевина имеет мартенсит-
ную структуру. Стали этой группы имеют высокую прочность (σв = 1200…1600 МПа) и применяются для крупных деталей, испытывающих значительные нагрузки.
Улучшаемые сталисодержат 0,3…0,5 % углерода и небольшое количество легирующих элементов (до 3…5 %). Эти стали подвергаются улучшению, состоящему из закалки в масле и высокого отпуска. После термообработки имеют структуру сорбита. Механические свойства разных марок улучшаемой стали в случае сквозной прокаливаемости близки (σв = 900…1200 МПа). Поэтому прокаливаемость определяет выбор стали. Чем больше легирующих элементов, тем выше прокаливаемость. Следовательно, чем больше сечение детали, тем более легированную сталь следует использовать. По прокаливаемости улучшаемые стали могут быть условно разбиты на пять групп.
Впервую труппу входят углеродистые стали 35, 40, 45. Эти стали подвергаются нормализации вместо улучшения.
Ко второй группе относятся стали, легированные хромом 30Х,40Х.
Третью группу составляют хромистые стали, дополнительно легированные ещё одним – двумя элементами (кроме никеля) 30ХМ, 40ХГ, 30ХГС и др. Четвёртая группа представлена хромоникелевыми сталями, содержащими около 1 % никеля: 40ХН, 40ХНМ и др.
Впятую группу входят стали, легированные рядом элементов, причём содержание никеля доходит до 3…4 %: 38ХН3, 38ХН3МФ. Это лучшие марки улучшаемых сталей, хотя они сравнительно дороги.
Высокопрочные стали.Новейшая техника предъявляет высо-
кие требования к прочности стали (σв = 1500…2500 МПа). Этим требованиям соответствуют мартенитностареющие стали, сочетающие высокую прочность с достаточной вязкостью и пластичностью. Они представляют собой практически безуглеродистые (до 0,03 % С) сплавы железа с никелем (17…26 % Ni), дополнительно легированные титаном, алюминием, молибденом, ниобием и кобальтом.
Широкое распространение получила сталь Н18К9М5Т. Она подвергается закалке на воздухе с 800…850 °С. Высокую прочность маргенситностареюшие стали получают в результате старения, представляющего собой отпуск, производимый при температуре 450…500 °С. В результате такой термообработки сталь Н18К9М5Т
имеет предел прочности σв = 2000 МПа. Кроме упомянутой выше стали, нашли применение стали Н12К8М3Г2, МЮХ11М2Т, Н12К8М4Г2 и др. Мартенситностареющие стали применяют в авиационной промышленности, в ракетной технике, судостроении и т.д. Они обладают хорошей свариваемостью и обрабатываемостью. Эти стали являются достаточно дорогостоящими.
Износостойкие сталиспособны сопротивляться процессу изнашивания. Изнашивание – это процесс постепенного разрушения поверхностных слоёв трущихся деталей, который приводит к уменьшению их размеров (износу). Износостойкие стали можно разделить на три группы.
В первую группу входят стали, износостойкость которых достигается высокой твёрдостью поверхности. Они подвергаются закалке и низкому отпуску или химико-термическойобработке.
Имеют структуру мартенсита или мартенсита с карбидными включениями. К этой группе относятся подшипниковые стали, из которых изготавливаются шарики и ролики подшипников качения. Содержание углерода в них около 1 %.
Ко второй группе относятся стали, износостойкость которых достигается смазывающим действием графита. Эти стали имеют в структуре графитные включения, которые в процессе изнашивания выходят на поверхность и выполняют роль сухой смазки. Эти стали имеют высокое содержание углерода (~1 %) и кремния (~1 %), что повышает способность к графитизации.
Третью группу составляют стали, износостойкость которых достигается повышенной склонностью к наклёпу, плохо обрабатывается резанием, поэтому применяется в литом состоянии.
Стали со специальными свойствами Коррозионностойкие (нержавеющие) стали.
Коррозией называется разрушение металла под действием внешней агрессивной среды в результате её химического или электрохимического воздействия. Различают химическую коррозию, обусловленную воздействием на металл сухих газов и неэлектролитов (например, нефтепродуктов) и электрохимическую, возникающую под действием жидких электролитов или влажного воздуха. По характеру коррозионного разрушения различают сплошную и местную коррозию. Сплошная коррозия захватывает всю поверхность металла. Её делят на равномерную и неравномерную в зависимости от того, одинаковая ли глубина коррозионного разрушения на разных участках. При местной коррозии поражения локальны. В зависимости от степени локализации различают пятнистую, язвенную, точечную, межкристаллитную и другие виды местной коррозии.
Самый надёжный способ защиты от коррозии – применение коррозионностойких сталей. Коррозионная стойкость достигается при введении в сталь элементов, образующих на её поверхности тонкие и прочные оксидные плёнки. Наилучший из этих элементов –хром.
При введении в сталь 12…14 % хрома она становится устойчивой против коррозии в атмосфере, воде, ряде кислот, щелочей и солей. Стали, содержащие меньшее количество хрома, подвержены коррозии точно так же, как и углеродистые стали. В технике применяют хромистые и хромоникелевые коррозионностойкие стали.
Дата добавления: 2018-04-04; просмотров: 270; Мы поможем в написании вашей работы! |
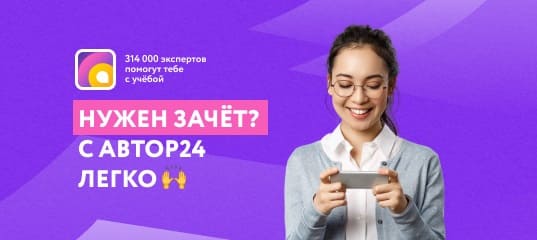
Мы поможем в написании ваших работ!