ОБОРУДОВАНИЕ, ПРИБОРЫ, МАТЕРИАЛЫ,
НАГЛЯДНЫЕ ПОСОБИЯ И ПРИНАДЛЕЖНОСТИ
3.1. Термические печи.
3.2. Сосуд с водой.
3.3. Твердомер Роквелла.
3.4. Секундомер.
3.5. Клещи и мраморные плитки.
3.6. Наждачная бумага.
3.7. Набор образцов из сталей марок 10, 50, У12 в отожженном состоянии (по 4 образца каждой марки);
3.8. Плакаты:
3.8.1. Диаграмма состояния «железо-углерод» (смотри приложение А)
3.8.2. Влияние содержания углерода на механические свойства стали в отожженном состоянии.
3.8.3. Влияние содержания углерода на твердость закаленных сталей.
3.8.4. Мартенситные кривые углеродистых сталей.
3.8.5. Соотношение чисел твердости.
ПОРЯДОК ВЫПОЛНЕНИЯ РАБОТЫ
4.1. Изучить настоящие методические указания.
4.2. По маркировке сталей установить среднее содержание углерода в исследуемых образцах сталей; с использованием диаграммы состояния «железо-углерод» определить численные значения критических точек, структурные составляющие при комнатной температуре в отожженном состоянии, а также вычислить оптимальные температуры закалки. Данные занести в таблицу 1.
Таблица 1 – Характеристики исследуемых марок сталей в отожженном состоянии
Марка стали | (С), % | Критические точки, 0С | Структура в отожженном состоянии при 25 0С | HRB | Оптимальная температура закалки, 0С | ||
10 50 У12 |
4.3. Зачистить торцевую часть отожженных образцов наждачной бумагой, измерить их твердость. Данные занести в таблицу 1.
|
|
4.4. С помощью клещей загрузить в термические печи, нагретые до температуры 600, 780, 840 и 900 0С по одному отожженному образцу из исследуемых сталей.
4.5. Выдержать загруженные образцы при заданных температурах в течение 10 минут (в среднем 1 мин на 1 мм сечения образца).
4.6. С помощью клещей перенести нагретые образцы в сосуд с водой.
4.7. После охлаждения образцы вынуть из сосуда и протереть ветошью, а затем зачистить наждачной бумагой и измерить твердость. Полученные результаты твердости занести в таблицу 2.
4.8. Используя таблицу «Соотношение чисел твердости» перевести значения твердости HRB отожженных образцов (таблица 1) в значение твердости HRC. Заполнить таблицу 2.
Таблица 2 – Значения твердости исследуемых марок сталей в отожженном и закаленном состояниях
Марка стали | HRC | ||||
После отжига от оптимальной температуры нагрева | После закалки от температур, 0С | ||||
600 | 780 | 840 | 900 | ||
10 50 У12 |
4.10. По результатам эксперимента построить график зависимости твердости HRC от температуры нагрева сталей под закалку с нанесением на ось абсцисс значений критических точек сталей.
4.11. По результатам эксперимента построить графики зависимости твердости HRC от содержания углерода в стали при закалке от оптимальной температуры.
|
|
4.12. Сделать выводы по работе, объяснив причины изменения твердости стали при закалке от различных температур нагрева.
СОДЕРЖАНИЕ ОТЧЕТА
5.1. Наименование работы.
5.2. Цель работы.
5.3. Таблица 1 – Характеристики исследуемых марок стали
5.4. Таблица 2 – Значения твердости исследуемых марок сталей в отожженном и закаленном состояниях.
5.5. Рисунок 1 – Графики зависимости твердости НRC от температуры нагрева сталей под закалку.
5.6. Выводы по работе.
КОНТРОЛЬНЫЕ ВОПРОСЫ
6.1. Что называется закалкой на мартенсит и ее цель?
6.2. Что понимается под критическими точками в сталях и как они обозначаются?
6.3. Что называется мартенситом закалки? Каковы особенности строения его кристаллической решетки и микроструктуры?
6.4. В чем причина того, что для доэвтектоидных сталей применяют полную, а для заэвтектоидных сталей неполную закалку?
6.5. Что такое закаливаемость стали и от чего она зависит?
6.6. Почему низкоуглеродистые стали не закаливаются?
6.7. Почему в сталях, содержащих более 0,6% углерода, в закаленных микроструктурах появляется остаточный аустенит?
|
|
6.8. Какова причина высокой твердости мартенсита закалки?
6.9. Какова связь размеров зерна аустенита с микроструктурой мартенсита и свойствами стали?
6.10. Какова формула для расчета оптимальных закалочных температур для до- и заэвтектоидных сталей?
Лабораторная работа № 12
МИКРОСТРУКТУРА И СВОЙСТВА СТАЛЕЙ ПОСЛЕ
ПОВЕРХНОСТНОЙ ЗАКАЛКИ И ХИМИКО-ТЕРМИЧЕСКОЙ ОБРАБОТКИ
ЦЕЛЬ РАБОТЫ
Изучить влияние основных способов поверхностного упрочнения на структуру и свойства металлов и сплавов.
ТЕОРЕТИЧЕСКИЙ РАЗДЕЛ
Разрушение металла под действием статических и динамических нагрузок, трения, усталостных напряжений и коррозии начинается обычно с поверхностных слоев. Поэтому, одним из основных направлений повышения надежности и долговечности машин и механизмов является поверхностное упрочнение нагруженных деталей. Добиться этой цели можно тремя методами: наклепом, термической обработкой и изменением химического состава поверхностных слоев металла. Последний метод упрочнения стальных деталей используют в комбинации с термообработкой и называют химико-термической обработкой (ХТО).
Все виды упрочнения уменьшают абразивный износ деталей (из-за повышения твердости) и склонность к усталостному разрушению (из-за появления остаточных напряжений сжатия в поверхностном слое).
|
|
2.1. Поверхностная закалка(закалка с нагревом ТВЧ) – производится для деталей из углеродистых и низколегированных сталей с содержанием углерода 0,4 – 0,6% после механической обработки заготовок, подвергнутых отжигу или нормализации. Нагрев поверхностных слоев до 840 – 1020 0С проводится в течение нескольких секунд с помощью токов высокой частоты (500 – 50000 Гц) в индукторе, имеющем форму детали. Последующее охлаждение струями воды приводит к закалке слоя толщиной 0,5 – 5 мм (зона нагрева выше АС3). После низкого отпуска, выполняемого для снятия остаточных напряжений, структура упрочненного слоя представляет из себя отпущенный мелкоигольчатый мартенсит с твердостью (HRC=50 – 60). Сердцевина детали, не прошедшая закалку, остается вязкой и имеет структуру троостита, сорбита или перлита с ферритом (HRC=20 – 30). Этот способ используется, главным образом, для упрочнения деталей простой формы в массовом производстве (валики, оси, пальцы и т.д.), отличается высокой производительностью, поддается автоматизации. Упрочнение после закалки ТВЧ сохраняется при нагреве до 200 – 220 0С.
2.2. Цементация – разновидность ХТО, используемая для поверхностного упрочнения деталей из низкоуглеродистых сталей (С≤0,25%), имеющих исходную структуру феррита с небольшим количеством перлита (после нормализации и отжига).
При нагреве деталей до 910 – 930 0С и выдержке при этой температуре в течение 6 – 12 часов в атмосфере СО или СН4 происходит насыщение стали углеродом (до 1 – 1,2%). Эффективная толщина цементованного слоя (от поверхности до участков с концентрацией углерода более 0,45%) составляет 0,5 – 2 мм. Простейшая термообработка после цементации – закалка и низкий отпуск. В этом случае, структура поверхностного слоя – высокоуглеродистый мартенсит, цементит и остаточный аустенит (HRC=58-62). По мере удаления от поверхности и снижения концентрации углерода твердость мартенсита снижается, на глубине более прокаливаемости стали структура переходит в троостит, сорбит и ферритно-перлитную смесь с пониженной твердостью (HRC=15-20), но высокой вязкостью. Процесс цементации сравнительно длителен, при нагреве и закалке возможно коробление деталей. В случае нагрева в процессе эксплуатации выше 200 – 220 0С цементованный слой разупрочняется.
2.3. Азотирование –способ ХТО, используемый для упрочнения тяжелонагруженных деталей, особенно из сталей, легированных хромом, алюминием, молибденом и другими нитридообразующими элементами (наиболее типичная сталь – 38Х2МЮА). Насыщение поверхностного слоя детали азотом после термического улучшения (закалка, высокий отпуск) и механической обработки проводят в атмосфере NH3 при температуре 500 – 600 0С. Время обработки для получения упрочненного слоя толщиной 0,3 – 0,6 мм составляет 20 – 60 часов.
В структуре стали 38Х2МЮА после азотирования различается светлый нетравящийся слой толщиной 0,01 – 0,03 мм из α- и γ- фаз (твердые растворы на основе нитридов с содержанием азота 6 – 12%), ниже – серый слой из смеси α- и γ- фаз с азотистым сорбитом, переходящий в структуру сорбита отпуска с содержанием азота менее 0,015%.
Твердость азотированного слоя для стали 38Х2МЮА составляет HV 1000 – 1200, для 40Х2НМА и 18Х2Н4ВА - HV 600 – 950 .
Помимо более существенного повышения твердости и усталостной прочности, чем при цементации или поверхностной закалке с нагревом ТВЧ, азотирование значительно увеличивает коррозионную стойкость поверхностного слоя. Положительное влияние этого вида обработки сохраняется при нагреве детали до 550 – 600 0С. Однако длительность и стоимость азотирования выше, чем для других способов упрочнения.
Для поверхностного упрочнения различных деталей из конструкционных и инструментальных материалов широко используется цианирование и нитроцементация, представляющая из себя комбинацию цементации и азотирования.
2.4. Борирование – способ ХТО (диффузионная металлизация), используемый для значительного упрочнения поверхности штампов, пресс-форм, втулок грязевых нефтяных насосов и других деталей, работающих в условиях, способствующих ускоренному абразивному износу или смятию. Насыщение поверхности металла бором (до 1% и более) производится чаще всего путем электролиза буры (Na2B4O7) при 600 – 1050 0С. Длительность получения слоя толщиной 0,1 – 0,2 мм составляет 2 – 6 часов. После борирования детали обычно подвергают закалке и низкому отпуску (предварительная обработка чаще всего заключается в отжиге для облегчения механической обработки).
В структуре упрочненного слоя наблюдаются светлые нетравящиеся бориды FeB, ниже - Fe2B. Центральная зона деталей имеет структуру мартенсита отпущенного, иногда бейнита, троостита или сорбита с содержанием бора менее 0,005%. Борированный слой обладает очень высокой твердостью (HV1800 – 2000), стойкостью по отношению к коррозии, окалинообразованию, нагреву. Однако он довольно хрупкий, часто имеет пористое строение.
Дата добавления: 2018-04-04; просмотров: 237; Мы поможем в написании вашей работы! |
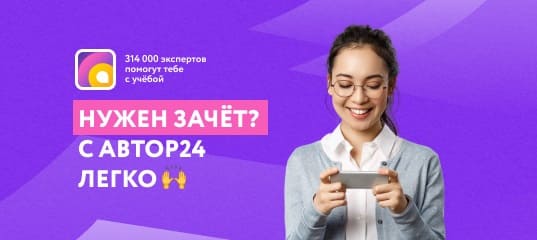
Мы поможем в написании ваших работ!