Figure 7.5 Loading with vapour return
Cargo tank loading limits
Apart from the sloshing requirement outlined above, the question of cargo tank loading limits — as discussed in 7.5.5 should also be addressed. (Reference 2.37).
7.5.2 Control of vapours during loading
The control of cargo vapours during loading can be carried out by using:—
• A vapour return line to the shore coupled to a gas compressor
• The ship's reliquefaction plant for liquid return to the ship's tanks, or
• Both of the above.
For LNG ships, as depicted in Figure 7.5, gas-return to the shore, using a vapour return system, is normal. This is because there are no reliquefaction plants fitted on board. For such ships, the liquid cargo is loaded via the liquid header and piped to the appropriate tanks. Gas generated in the vapour space is returned to the shore using a cargo vapour compressor. This equipment is usually mounted on board ship but may be mounted ashore; the choice is dependant on project specifications.
When loading with a vapour return line in use, the loading rate is independent of the capacity of the ship's reliquefaction plant and is governed by:
• The flow rate acceptable to the ship and terminal, and
• The capacity of the cargo vapour compressor
Figure 7.6 Loading without vapour return
For fully refrigerated or semi-pressurised LPG ships, a vapour return line is normally connected to the ship's vapour manifold but this is most often put in place for safety relief purposes. Normal loading practice on such ships is to load through the liquid header, to draw off excess vapour via the vapour header, to operate the reliquefaction plant and to return the liquid to the ship's tank via the condensate return line. This operation controls cargo boil-off and ensures that tank pressure limits are not exceeded. The pipeline arrangement is shown in Figure 7.6. The introduction of a reliquefaction plant in the system can mean that loading rates are restricted by the capacity of the machinery. It is in this sense that the vapour return line acts as a safety device; should tank pressures become excessive, the ship's vapour manifold valve can be opened to relieve the situation. (For pressurised LPG carriers, the system should be similar to that described in this paragraph, and a vapour return should be fitted for safety relief purposes. However, a reliquefaction system is not fitted to such ships and loading is normally achieved by shore pumps creating sufficient pressure to allow cargo tank vapour to continuously condense into the bulk liquid.)
|
|
Where refrigerated storage is found in a terminal, the terminal's reliquefaction capacity is usually greater than that provided on board ship. As a result, where an LPG vapour return is used, in a similar way to that described for LNG ships, loading rates can be higher than those described in the previous paragraph. However, while advantageous, such systems for LPG are relatively rare.
A problem experienced when using vapour returns in the LPG trades is that terminals can be concerned about the vapour quality to be returned to the shore. This is especially so at the early stages of loading. Terminal personnel can be concerned about residual nitrogen which acts as an incondensible during reliquefaction. They may also be concerned about contamination with vapours from previous ship-cargoes. It is also difficult to account for the vapour returned to shore, especially if it is flared. This can lead to an overstatement of the Bill of Lading quantity, unless credit is given for the returned vapour. For these reasons it is unusual to find LPG terminals accepting return gas other than for safety reasons and then only to a flare (see also 8.1.6).
7.5.3 Loading — early stages
Loading refrigerated ships
When liquefied gas is being loaded, it is necessary to consider the location, pressure, temperature and volume of the shore tanks as well as the terminal's pumping procedures. Fully refrigerated ships usually load from fully refrigerated storage where tanks typically operate at a pressure of approximately 60 millibars.
This pressure will allow the cargo at the bottom of a full shore tank to sustain a temperature perhaps one degree Centrigrade warmer than its atmospheric boiling point.
When this cargo is pumped to the jetty, the pumping energy required for transfer is dissipated in the liquid as heat, to which must be added the heat flow into the liquid through the pipelines. The cargo may, therefore, arrive on the ship at an even warmer temperature. When loading without a vapour return line being used, the vapour which is displaced by the incoming liquid must be reliquefied on board. The power required for this, and to compensate for the pumping energy and the heat flux through the insulation, may leave little capacity for cooling the cargo during loading.
|
|
Therefore, as can be seen from the foregoing paragraphs, the early stages of loading can be critical, particularly where significant distances exist between the storage tank
and jetty. The ship's tank pressures must be regularly checked and on no account should relief valves be allowed to lift. Loading rates should be reduced, and if necessary stopped, when difficulties are experienced in maintaining acceptable tank pressures. In some ports in hot countries, where the terminal has long pipelines, this feature can be difficult to overcome. Under these circumstances, cargo stoppage would allow the pipeline contents once again to rise in temperature. Accordingly, in such ports, cargo flow should be maintained as long as it is safe to do so until cold product can be received on board at which time tank pressures will fall.
A rise in ship's tank pressure in the early stages of loading can also be controlled to some extent by loading limited quantities of liquid into the cargo tank via the top sprays, if fitted. This will help to condense some of the cargo vapours.
Loading pressurised ships
Pressurised ships normally arrive at a loading terminal having cargo tanks at atmospheric pressure. Firstly, the ship requests vapours from the shore to purge any remaining nitrogen or contaminants from the tanks. This also allows the equalisation of ship and shore pressures. Thereafter, the method used is to start loading at a very slow flow, giving time for the incoming liquid to expand safely at the first valves in the ship's system.
In this case, as the liquid is allowed through, local flash-cooling can occur and it is important to ensure that at no time, tank or pipeline temperatures are allowed to fall below design limitations.
Дата добавления: 2018-02-28; просмотров: 469; Мы поможем в написании вашей работы! |
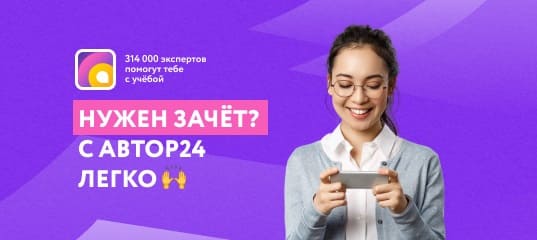
Мы поможем в написании ваших работ!