Задача 2. Оценка опасности дефектов магистрального трубопровода, определяемых с помощью внутритрубной диагностики
Задача 1. Определение толщины стенки трубы
Постановка задачи:Определить толщину стенки трубы участка магистрального трубопровода с наружным диаметром Dн. Исходные данные для расчета: категория участка, внутреннее давление – р, марка стали, температура стенки трубы при эксплуатации – tэ, температура фиксации расчетной схемы трубопровода – tф, коэффициент надежности по материалу трубы – k1. Рассчитать нагрузки на трубопровод: от веса трубы, веса продукта (нефть и газ), напряжения от упругого изгиба (радиус упругого изгиба R=1000 Dн). Плотность нефти принять равной r. Исходные данные приведены в табл. 3.1.
Расчетную толщину стенки трубопровода δ, мм, следует определять по формуле (3.1)
При наличии продольных осевых сжимающих напряжений толщину стенки следует определять из условия
(3.2)
где n - коэффициент надежности по нагрузке - внутреннему рабочему давлению в трубопроводе, принимаемый: для газопроводов — 1.1, для нефтепроводов — 1.15; p – рабочее давление, МПа; Dн - наружный диаметр трубы, мм; R1 – расчетное сопротивление растяжению металла труб, МПа; ψ1 - коэффициент, учитывающий двухосное напряженное состояние труб
(3.3)
|
|
где нормативное сопротивление растяжению (сжатию) металла труб, принимается равным пределу прочности sвр по прил. 5, МПа; m – коэффициент условий работы трубопровода принимаемый по прил. 2; k1 , kн – коэффициенты надежности, соответственно, по материалу и по назначению трубопровода, принимаемые k1 — табл. 3.1, kн по прил. 3.
(3.4)
где σпр.N - продольное осевое сжимающее напряжение, МПа.
(3.5)
где α, Е, μ – физические характеристики стали, принимаемые по прил. 6; Δt – температурный перепад, 0С, Δt= tэ – tф ; Dвн – диаметр внутренний, мм, с толщиной стенки δн, принятой в первом приближении, Dвн = Dн –2 δн.
Увеличение толщины стенки при наличии продольных осевых сжимающих напряжений по сравнению с величиной, полученной по первой формуле, должно быть обосновано технико-экономическим расчетом, учитывающим конструктивные решения и температуру транспортируемого продукта.
Полученное расчетное значение толщины стенки трубы округляется до ближайшего бóльшего значения, предусмотренного государственными стандартами или техническими условиями на трубы.
Пример 1. Определить толщину стенки трубы участка магистрального газопровода диаметром Dн = 1220 мм. Иходные данные для расчета: категория участка - III, внутреннее давление – р = 5,5 МПа, марка стали – 17Г1С-У (Волжский трубный завод), температура стенки трубы при эксплуатации – tэ = 8 0С, температура фиксации расчетной схемы трубопровода – tф = -40 0С, коэффициент надежности по материалу трубы – k1 = 1,4. Рассчитать нагрузки на трубопровод: от веса трубы, веса продукта (нефть и газ), напряжения от упругого изгиба (радиус упругого изгиба R=1000 Dн). Плотность нефти принять равной r. Исходные данные приведены в табл. 3.1.
|
|
Решение
Расчет толщины стенки
Нормативное сопротивления растяжению (сжатию) металла труб (для стали 17Г1С-У) равно sвр =588 МПа (прил. 5); коэффициент условий работы трубопровода принимаемый m = 0,9 (прил. 2); коэффициент надежности по назначению трубопровода kн = 1,05 (прил. 3), тогда расчетное сопротивление растяжению (сжатию) металла труб
(МПа)
Коэффициент надежности по нагрузке - внутреннему рабочему давлению в трубопроводе n = 1,1.
Расчетная толщина стенки трубопровода
(мм)
Физические характеристики стали α = 1,2·10-5, Е = 2,1·105, μ = 0,3
Продольное осевое сжимающее напряжение, МПа
Коэффициент, учитывающий двухосное напряженное состояние труб
|
|
Толщина стенки с учетом продольных осевых сжимающих напряжений
(мм)
Принимаем толщину стенки равной 11 мм.
Таблица 3.1
Исходные данные для расчета (задача 1)
№ вар. | Dн мм | Категория участка | r, кг/м3 | tф , 0С | tэ , 0С | р, МПа | Марка стали | k1 |
1 | 530 | В | 850 | -33 | 4 | 5,0 | 13Г1С-У | 1.4 |
2 | 620 | I | 840 | -35 | 10 | 6,8 | 17Г1С | 1.34 |
3 | 720 | II | 750 | -40 | 16 | 6,9 | 13Г2АФ | 1.47 |
4 | 820 | III | 770 | -39 | 14 | 7,3 | 13Г1С-У | 1.4 |
5 | 1020 | IV | 780 | -38 | 8 | 4,3 | 09ГБЮ | 1.34 |
6 | 1220 | В | 870 | -37 | 12 | 10 | 12Г2СБ | 1.47 |
7 | 530 | I | 840 | -36 | 6 | 5,8 | 09Г2ФБ | 1.4 |
8 | 820 | II | 830 | -34 | 18 | 6,5 | 13Г1СБ-У | 1.34 |
9 | 1020 | III | 890 | -32 | 20 | 4,3 | 10Г2ФБ | 1.47 |
10 | 1220 | IV | 810 | -31 | 22 | 5,3 | 10Г2ФБЮ | 1.4 |
11 | 530 | IV | 850 | -37 | 4 | 4,5 | 13Г1С-У | 1.4 |
12 | 620 | В | 840 | -36 | 10 | 5,8 | 17Г1С | 1.34 |
13 | 720 | I | 750 | -34 | 16 | 6,5 | 13Г2АФ | 1.47 |
14 | 820 | II | 770 | -32 | 14 | 4,3 | 13Г1С-У | 1.4 |
15 | 1020 | III | 780 | -31 | 8 | 5,3 | 09ГБЮ | 1.34 |
16 | 1220 | IV | 870 | -33 | 12 | 10 | 12Г2СБ | 1.47 |
17 | 530 | III | 840 | -35 | 6 | 6,8 | 09Г2ФБ | 1.4 |
18 | 820 | IV | 830 | -40 | 18 | 6,9 | 13Г1СБ-У | 1.34 |
19 | 1020 | В | 890 | -39 | 20 | 7,3 | 10Г2ФБ | 1.47 |
20 | 1220 | I | 810 | -38 | 22 | 4,3 | 10Г2ФБЮ | 1.4 |
21 | 720 | IV | 780 | -39 | 4 | 5,3 | 12Г2СБ | 1.47 |
22 | 820 | В | 870 | -38 | 10 | 4,5 | 09Г2ФБ | 1.4 |
23 | 1020 | I | 840 | -37 | 16 | 5,8 | 13Г1СБ-У | 1.34 |
24 | 1220 | II | 830 | -36 | 14 | 9 | 10Г2ФБ | 1.47 |
25 | 530 | III | 890 | -34 | 8 | 4,3 | 10Г2ФБЮ | 1.4 |
Задача 2. Оценка опасности дефектов магистрального трубопровода, определяемых с помощью внутритрубной диагностики
|
|
Постановка задачи: Классифицировать дефекты магистрального трубопровода диаметром Dн и толщиной стенки d по степени опасности, если задана марка стали трубопровода, длины дефектов – L1, L2, L3, глубина дефекта (табл. 3.3). Построить зависимость коэффициента снижения прочности от длины и глубины дефекта.
В трубопроводе с наружным диаметром Dн и толщиной стенки d по результатам внутритрубной диагностики обнаружены поверхностные дефекты (рис. 1).
![]() ![]() ![]() ![]() ![]() |
Рис. 1. Расчетная схема трубы с дефектом
Разрушение трубы с дефектом произойдет в том случае, если кольцевое напряжение достигнет значения s, подсчитываемого по формуле [16]:
, (3.47)
где предел текучести, МПа;
проекция площади дефекта на продольное сечение трубы, м2;
глубина дефекта, м;
проекция площади бездефектной трубы на продольное сечение трубы, м2;
длина дефекта, м;
толщина стенки, м;
параметр Фолиаса, определяется по формуле:
- (3.48)
В расчетах трубопроводов используется понятие коэффициента снижения прочности j, равного отношению предельных давлений для трубы с дефектом и бездефектной трубы.
Преобразовывая выражение в квадратных скобках в эмпирическом уравнении (1), получаем для осевого дефекта постоянной глубины следующую формулу для коэффициента снижения прочности:
, (3.49)
где с= t / , t– остаточная толщина стенки трубы, м; t=
d; .
Пример 4. Классифицировать дефекты магистрального трубопровода диаметром 1220 мм и толщиной стенки 12 мм по степени опасности, марка стали 13Г1С-У (Волжский трубный завод), длины дефектов – 0.1, 0.2, 0.3 м, глубина дефекта d=0.2d и d=0.4d. Построить зависимость коэффициента снижения прочности от длины и глубины дефекта.
Решение
Длина дефекта L=0.1 м, глубина дефекта d=0.2d.
Тогда оставшаяся толщина стенки t= d - d = 0.8d . Значение с = 0.8d/ d=0.8.
По формуле (3.48) определяем параметр Фолиаса М (L=0.1 м):
= 1.24
Для определения кольцевого напряжения по формуле (3.47), при котором произойдет разрушение трубы с дефектом, рассчитаем значения А и А0 .
А=0.1×0.2d= 0.1×0.2×0.012=0.00024
А0 = 0.1×d = 0.1×0.012 = 0.0012 м2
Значение предела текучести для заданной марки стали найдем по техническому каталогу на трубы: =461 МПа [11]
Тогда =461×0.564=260 МПа
По формуле (3.49) определяем коэффициент снижения прочности jе:
= 0.95
Точно также проведем расчет для других длин и глубин дефекта. Результаты расчета сведены в табл. 3.2 и рис. 3.5.
Таблица 3.2
Значения коэффициентов снижения прочности jе и параметра
Фолиаса М в зависимости от длины L и глубины дефекта d
d | Длина дефекта L, м (d =12 мм) | |||||
0,1 | 0,2 | 0,3 | ||||
М | jе | М | jе | М | jе | |
0.2d | 1,24 | 0,95 | 1,785 | 0,9 | 2,43 | 0,87 |
0.4d | 1,24 | 0,88 | 1,785 | 0,77 | 2,43 | 0,72 |
При дефекты относят к опасным, требующим первоочередного ремонта, а при
к неопасным дефектам.
Рис. 3.5. Зависимость коэффициента снижения прочности от глубины и длины дефекта
Как видно из рис. 3.5, дефекты трубопровода с глубиной d=0.4d, т.е. 4,8 мм и длинами дефекта 0,2 м и 0,3 м относятся к опасным дефектам, а остальные - к неопасным.
Данный график показывает: чем больше глубина и длина дефекта, тем выше вероятность его попадания в зону опасных дефектов.
Таблица 3.3
Исходные данные для расчета (задача 2)
№ вар. | Dн, мм | Марка стали |
Глубина дефекта, d | Длина дефекта, м | |||
L1 | L2 | L3 | |||||
1 | 530 | 13Г1С-У | 0,8× d | 0,2× d | 0,1 | 0,3 | 0,5 |
2 | 620 | 17Г1С | 0,75× d | 0,3× d | 0,2 | 0,4 | 0,6 |
3 | 720 | 13Г2АФ | 0,95× d | 0,4× d | 0,15 | 0,35 | 0,55 |
4 | 820 | 13Г1С-У | 0,25× d | 0,6× d | 0,25 | 0,35 | 0,55 |
5 | 1020 | 09ГБЮ | 0,15× d | 0,8× d | 0,1 | 0,35 | 0,6 |
6 | 1220 | 12Г2СБ | 0,75× d | 0,2× d | 0,3 | 0,45 | 0,65 |
7 | 530 | 09Г2ФБ | 0,1× d | 0,5× d | 0,1 | 0,35 | 0,45 |
8 | 820 | 13Г1СБ-У | 0,15× d | 0,7× d | 0,1 | 0,3 | 0,45 |
9 | 1020 | 10Г2ФБ | 0,95× d | 0,4× d | 0,2 | 0,35 | 0,5 |
10 | 1220 | 10Г2ФБЮ | 0,1× d | 0,6× d | 0,1 | 0,3 | 0,5 |
11 | 530 | 13Г1С-У | 0,65× d | 0,2× d | 0,15 | 0,35 | 0,55 |
12 | 620 | 17Г1С | 0,95× d | 0,3× d | 0,25 | 0,35 | 0,55 |
13 | 720 | 13Г2АФ | 0,85× d | 0,4× d | 0,1 | 0,35 | 0,6 |
14 | 820 | 13Г1С-У | 0,15× d | 0,6× d | 0,3 | 0,45 | 0,65 |
15 | 1020 | 09ГБЮ | 0,18× d | 0,8× d | 0,1 | 0,35 | 0,45 |
16 | 1220 | 12Г2СБ | 0,27× d | 0,2× d | 0,1 | 0,3 | 0,45 |
17 | 530 | 09Г2ФБ | 0,14× d | 0,5× d | 0,2 | 0,35 | 0,5 |
18 | 820 | 13Г1СБ-У | 0,23× d | 0,7× d | 0,1 | 0,3 | 0,5 |
19 | 1020 | 10Г2ФБ | 0,74× d | 0,4× d | 0,2 | 0,35 | 0,5 |
20 | 1220 | 10Г2ФБЮ | 0,27× d | 0,6× d | 0,1 | 0,3 | 0,5 |
21 | 720 | 12Г2СБ | 0,98 d | 0,2× d | 0,3 | 0,45 | 0,65 |
22 | 820 | 09Г2ФБ | 0,88× d | 0,3× d | 0,1 | 0,35 | 0,45 |
23 | 1020 | 13Г1СБ-У | 0,78× d | 0,4× d | 0,1 | 0,3 | 0,45 |
24 | 1220 | 10Г2ФБ | 0,18× d | 0,6× d | 0,2 | 0,35 | 0,5 |
25 | 530 | 10Г2ФБЮ | 0,08× d | 0,8× d | 0,1 | 0,3 | 0,5 |
Приложение 2
Дата добавления: 2018-02-28; просмотров: 906; Мы поможем в написании вашей работы! |
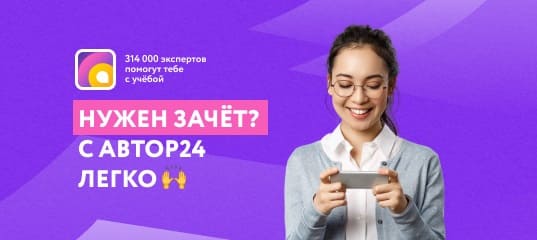
Мы поможем в написании ваших работ!