Сопротивление вязкому разрушению
Оно выражается такими характеристиками, как предельная пластичность (εк, Ψ, δк) ударная вязкость при вязком разрушении КС max , анизотропия вязкости и пластичности, истинное сопротивление разрыву (Sk). Оно очень важно для обеспечения надежной эксплуатации ответственных сооружений типа оболочек, нагруженных пневмитическим давлением (газопроводы большого диаметра и высокого давления, газгольдеры и резервуары большого объема, крупногабаритные сосуды давления в виде кожухов доменных печей, оболочек аэродинамических труб, корпусов воздухонагревателей), особенно при изготовлении их из сталей повышенной и высокой прочности. Кроме того, сопротивление вязкому разрушению во многом определяет возможность выполнения технологических операций холодной гибки, штамповки, вальцовки, правки и сварки.
Установлено, что вязкое разрушение зарождается и распространяется путем образования, роста и объединения микроскопических пустот (пор). В чистых металлах и сплавах поры образуются в заключительной стадии деформирования на «критических» дефектах решетки, подготовленных деформированием. В технических сплавах значительную роль в образовании пор играют также неметаллические включения и выделения избыточных фаз.
Важно знать наличие анизотропии пластичности, появляющейся в прокате в виде вытянутых и строчечных включений. Анизотропия пластичности сильно ограничивает пригодность стали к операциям холодной гибки, штамповки, глубокой вытяжки, завальцовки, способствуя преждевременному образованию трещин. Но наиболее губительно она сказывается на образовании ламелярных (пластинчатых) или слоистых трещин при сварке. Они возникают в основном металле вблизи сварных швов под воздействием напряжений и термодеформационных циклов сварки и имеют характерное ступенчатое строение.
|
|
Для оценки сопротивления стали вязкому разрушению пригодны характеристики предельной пластичности (εк, Ψ, δк ) и истинное сопротивление разрыву (Sk), получаемые при испытании на растяжение, в том числе на образцах, вырезанных из проката в направлении толщины, полные диаграммы деформирования в координатах истинные напряжения - истинные деформации, а также уровень ударной вязкости при вязком разрушении («верхнее плато» на температурной зависимости ударной вязкости).
Технико-экономическая эффективность
Технико-экономическая эффективность применения того или иного варианта стали в металлоконструкциях определяется в основном показателями двух категорий, отражающими изменение массы конструкций и изменение их стоимости. Возможность снижения массы конструкции при повышении прочности стали уже рассматривалось ранее. Однако одно только снижение массы конструкции в большинстве случаев еще не является достаточным стимулом для применения более прочной стали. Другое непременное условие - получение экономического эффекта.
|
|
Стоимость стали повышенной и высокой прочности, как правило, выше стоимости традиционной углеродистой стали, поэтому замена будет рентабельной только в том случае, если возможное удорожание металла перекроется экономией в результате снижения массы конструкции. При этом вопреки распространенному мнению достигаемое здесь удешевление обусловлено не только тем, что с уменьшением массы конструкции снижается стоимость израсходованного металла, а в значительной мере также и тем, что с уменьшением массы почти пропорционально снижаются затраты на изготовление, транспортировку, окраску и монтаж конструкции.
Экономический эффект применения нового материала в конструкциях обычно подсчитывают методом приведенных затрат, включая три следующих этапа:
·определение удельного (и общего) изменения массы металла, обусловленного применением более эффективной стали вместо традиционной;
|
|
·расчет удельной стоимости металлоконструкций при изготовлении их из традиционной и новой стали;
·определение изменения стоимости металлоконструкций для эквивалентного количества традиционного и нового материала (собственно экономический эффект).
Классификация сталей
Стали, используемые в сварных металлоконстукциях, различаются по ряду признаков, отражающих их изготовление, служебные свойства и область применения. Важнейшими из этих признаков являются:
· способ выплавки и разливки стали;
· степень раскисленности;
· химический состав;
· состояние поставки;
· уровень (класс) прочности;
· категория (группа) качества по хладостойкости.
По способу выплавкиприменяемую в сварных металлоконструкциях сталь можно разделить на мартеновскую, кислородно-конверторную и электросталь.
До 1960 г. для металлоконструкций использовали почти исключительно сталь, выплавленную в мартеновских печах. В последующие периоды во всем мире получил большое распространение наиболее производительный способ выплавки в кислородных конверторах с использованием для продувки через расплавленный металл кислорода высокой чистоты не менее 99,5% О2. Качество кислородно-конверторной стали не уступает качеству мартеновской, и с 1971 г. эти виды стали не разделяются.
|
|
С пуском крупных электродуговых печей, имеющих массу плавки 100-250 т и более, увеличилась выплавка стали в электропечах. Эта сталь отличается повышенной чистотой по содержанию вредных примесей - серы и фосфора.
В процессе электрошлакового переплава исходные заготовки (слябы) из стали мартеновской, кислородно-конвертерной или электростали переплавляются с нагревом электрическим током под слоем расплавленной шлаковой смеси специального химического состава. При этом содержание серы и кислорода уменьшается в 2-3 раза. Неметаллические включения, еще остающиеся в слитке, имеют малые размеры и равномерно распределены по объему.
По степени раскисленности сталь разделяется:
·кипящая (кп);
·полуспокойная (пс);
·спокойная (сп).
При выплавке стали в мартене или конвертере из передельного чугуна, содержащего 3-4 % углерода, окисление углерода (до содержания 0,06-0,25%С в стали) связано с образованием газообразных продуктов СО и СО2, вызывающих кипение металлической ванны. Если не проводить раскисления, то кипение продолжается после выпуска плавки в ковш и после разливки ее в изложницы до затвердевания слитка. Такая сталь называется кипящей.
Выделение газообразных продуктов при кристаллизации слитка кипящей стали приводит к резкому усилению его неоднородности по содержанию С, S и P, называемой ликвацией. Головная (верхняя) часть и сердцевина слитка обогащены примесями. Зона максимального содержания ликвирующих элементов в слитке кипящей стали расположена на расстоянии 5-15 % высоты слитка от его верха, ликвация по углероду достигает 400 % и по сере 900% среднего содержания этих элементов в плавке.
Идущая в отход при прокатке головная часть слитка (обрезь) кипящей стали составляет 4-10 % его массы. Но и в оставшейся части слитка после его прокатки имеются обширные зоны ликвации с содержанием С до 0,3-0,4% и серы до 0,15% при среднеплавочном содержании С = 0,12-0,22 % и S <= 0,05%. В результате разные листы и профили, входящие в одну партию (плавку) кипящей стали, но изготовленные из разных частей слитка (головной, средней или донной), неодинаковы по содержанию C, S и P.
Спокойная сталь раскисляется в сталеплавильном агрегате, а также в ковше при выпуске из печи. При этом в жидкий металл вводятся энергичные раскислители: марганец, кремний. алюминий, иногда кальций или титан. Эти элементы обладают значительно большим сродством к кислороду, чем углерод, поэтому окисление углерода прекращается, и сталь перестает кипеть. Благодаря этому слитки спокойной стали гораздо однороднее по химическому составу, чем кипящей. Ликвация по углероду лишь на 60%, а по сере на 110% превышает среднеплавочное содержание этих элементов.
Содержание кислорода в спокойной стали низкое. Наличие в химическом составе элементов-раскислителей и, главное, остаточного алюминия делает спокойную сталь менее склонной к росту зерна. Поэтому прочностные свойства и сопротивление хрупкому разрушению в более однородном и мелкозернистом прокате спокойной стали выше, чем в прокате кипящей стали.
Вместе с тем затвердевание слитка спокойной стали связано с образованием большой усадочной раковины. Для получения бездефектного тела слитка сталь разливают в изложницы с теплоизолирующими прибыльными надставками. Усадочная раковина образуется в верхней утепленной части слитка, которую перед прокаткой удаляют. Обрезь составляет 12-16% массы слитка. Поэтому выход годного проката из слитков спокойной стали меньше, чем из слитков кипящей. Вследствие этого, а также из-за большей продолжительности плавки за счет операции раскисления, дополнительного расхода ферросплавов и алюминия спокойная сталь дороже кипящей.
Низкое качество кипящей стали и небольшая технико-экономическая эффективность спокойной стали послужили стимулом к разработке варианта с промежуточной степенью раскисления – полуспокойной стали. Она выплавляется, как кипящая, но в ковше или при разливке в изложницы обрабатывается небольшим количеством раскислителей, гораздо меньшим, чем при выплавке спокойных сталей. Обычно применяют комплексное раскисление ферросилицием и алюминием. Быстрое прекращение кипения и затвердевание головной части слитка предотвращает развитие большой химической неоднородности. При этом для ликвации в слитках полуспокойной стали характерно превышение среднеплавочного содержания углерода на 80% и серы на 150%. Расстояние осевой ликвационной зоны от верха слитка составляет 15-30% его высоты; головная обрезь - 3-5% массы слитка.
Производство полуспокойных сталей характеризуется высокой технико-экономической эффективностью. В сравнении с производством спокойной стали выход годного проката из слитков выше на 8-10%, расход ферросилиция на раскисление снижен в 2-5 раз, алюминия в 5 раз, существенно уменьшается количество изложниц. Себестоимость и цена проката из полуспокойной стали на 2-9% ниже, чем из спокойной. Вместе с тем по качеству в части однородности химического состава, микроструктуры и механических свойств, сопротивления хрупкому разрушению и показателям прочности прокат полуспокойной стали уступает прокату спокойной стали, занимая промежуточное положение.
Химический состав стали- главная ее характеристика. Он определяет ее марку. При этом содержание химических элементов для данной марки стали задается не дискретно, а некоторым интервалом, в пределах которого изменение хим. состава не должно сопровождаться выведением свойств за границы гарантируемых уровней. Ширина интервала связана с возможностью сталеплавильного производства соблюдать заданную композицию.
Стали, в которых отсутствуют специальные добавки легирующих элементов или имеется лишь небольшое их количество, обусловленное технологией выплавки, называются углеродистыми.
По содержанию углерода различают стали:
- низкоуглеродистые (до 0,25 % С);
- среднеуглеродистые ( 0,3-0,6 % С);
- высокоуглеродистые (свыше 0,6 % С).
Для сварных металлоконструкций используются преимущественно стали с низким содержанием углерода. Они поставляются по ГОСТ 380-88, ГОСТ 14637-89 и ГОСТ 27772-88, а также сталь по ГОСТ 1050-88 главным образом в виде труб.
Стали, в которые специально вводятся добавки легирующих элементов для обеспечения требуемых свойств, называются легированными. Они могут содержать один, два, три и более легирующих элемента. Так, различают марганцовистую, хромистую, кремнемарганцовистую, хромоникелевую, хромоникельмолибденовую и другие легированные стали.
Легированные стали с небольшим содержанием легирующих элементов, обычно в сумме не превышающем 2-3 % по массе, и с низким содержанием углерода, используемые в строительстве, машиностроении, судостроении для изготовления сварных металлоконструкций, выделены в особую группу, их называют низколегированными. Прокат низколегированных сталей для металлоконструкций поставляется по ГОСТ 19281-89 (сортовой и фасонный), ГОСТ 19282-73 (листы и широкие полосы), ГОСТ 6713-91, ГОСТ 27772-88 и другим ТУ.
Стали с общим содержанием легирующих элементов от 3 до 10% - среднелегированные.
Стали с содержанием легирующих элементов более 10%, а одного легирующего элемента более 8%, называются высоколегированными. Они являются носителями особых свойств: коррозионной стойкости, жаростойкости, жаропрочности, хладостойкости при низких отрицательных (криогенных) температурах и др.
Марки стали
Маркировка всех легированных сталей однотипная: первые две цифры обозначают содержание углерода в сотых долях процента; буквы - условное обозначение легирующих элементов; цифра после буквы - примерное содержание легирующего элемента (единица и меньшее значение не ставятся); буква «А» в конце марки показывает, что сталь высококачественная и имеет пониженное содержание серы и фосфора.
Таблица 1.1
Легирующие элементы
Элемент | Углерод | Марганец | Кремний | Хром | Никель | Молибден | Ванадий | Вольфрам |
Символ | С | Mn | Si | Cr | Ni | Mo | V | W |
Обозна- чение | - | Г | C | Х | Н | М | Ф | В |
Азот | Медь | Алюминий | Бор | Кобальт | Титан | Ниобий | Селен | Фосфор | Цирконий |
N | Cu | Al | B | Co | Ti | Nb | Se | P | Zr |
А | Д | Ю | Р | К | Т | Б | Е | П | Ц |
Строительные стали
Строительные стальные конструкции используются в строительных сооружениях, магистральных трубопроводах, подъемных кранах и т. д.
При изготовлении и монтаже этих конструкций на специализированных заводах они подвергаются обработке: сварке, резке, обработке резанием, правке, гибке, вальцовке. Как правило, термическая обработка не проводится. При этом сталь должна сопротивляться образованию трещин и должна сохранять структуру и механические свойства. Стальные конструкции длительное время при эксплуатации должны выдерживать статические, динамические и переменные нагрузки, часто при низких температурах. Стоимость стальных конструкций не должна быть высокой.
Строительная сталь должна иметь высокие прочность, свариваемость, сопротивление хрупкому разрушению, сопротивление вязкому разрушению. Применение конструкций из нее должно характеризоваться высокой технико-экономической эффективностью. Для отдельных специальных областей применения сталь должна иметь также особые свойства.
Недостаточная прочность ранее применявшегося проката из углеродистой стали обыкновенного качества с пределом текучести σт = 230...260 МПа и σB = 370...400 МПа и проката из низколегированной стали с σт ≤ 350 МПа и σB ≤ 500 МПа проводила к излишнему расходу стали и удорожала конструкции. Повышение прочности стали - наиболее действенное средство снижения металлоемкости и стоимости таких конструкций. Размеры поперечных сечений многих элементов металлоконструкций, а следовательно и их масса, определяют расчетом, при котором исходят из предела текучести и временного сопротивления материалов.
Возможности упрочнения строительной стали (при удовлетворении прочих требований) весьма значительны. В России установлены семь основных классов прочности, которым соответствует предел текучести не менее 225, 285, 325, 390, 440, 590 и 735 МПа. Сталь первого класса (σт ≥ 225 МПа) С225 условно называют сталью нормальной прочности, трех следующих классов (σт ≥ 285 МПа) С285, С325 и С390 - сталью повышенной прочности и остальных трех классов (σт ≥ 440 МПа) -С440, С590 и С735 сталью высокой прочности.
Под влиянием изменения содержания элементов, неоднородности слитка и условий прокатки прочностные показатели (σт, σB) сталей варьируются в некоторых пределах.
При увеличении толщины проката уменьшается скорость его охлаждения, в результате чего образуется грубая ферритно-перлитная структура меньшей прочности. По ГОСТ 535-88 и 27772-88 с увеличением толщины проката уменьшается гарантированный предел текучести.
Высокая надежность соблюдения норм прочности с вероятностью не ниже 95% обеспечивается по ГОСТ 27772-88 специальными приемкой и контролем.
Стандартные марки имеют следующие обозначения: впереди буква С (строительная сталь), затем три цифры - предел текучести материала, МПа или Н/мм2, далее могут быть буквы и цифры, означающие вариант химического состава, указание на специальную термообработку или повышенную коррозионную стойкость.
Рекомендуемый химический состав марок приведён в табл. 1.2.
Таблица 1.2
Химический состав сталей
Сталь | Углерода, не более | Марганца | Кремния | Серы, не более | Фосфора, не более | Хрома, не более | Ванадия | Других элементов |
С235 | 0,22 | ≤0,6 | ≤0,05 | 0,05 | 0,04 | 0,3 | - | - |
С245, С275 | 0,22 | ≤0,65 | 0,15 | 0,05 | 0,04 | 0,3 | - | - |
С255, С285 | 0,22 0,22 | ≤0,65-0,8 0,8-0,9 | 0,15-0,3 0,15-0,3 | 0,05 0,05 | 0,04 0,04 | 0,3 0,3 | - - | - - |
С345, С375 | 0,15 0,15 | 1,3-1,7 1,3-1,7 | 0,8 0,8 | 0,04 0,04 | 0,035 0,035 | 0,3 0,3 | - - | - - |
С390 | 0,18 | 1,2-1,6 | ≤0,6 | 0,04 | 0,035 | 0,4 | 0,07-0,12 | Азот 0,025 |
С440 | 0,2 | 1,3-1,7 | ≤0,6 | 0,04 | 0,035 | 0,4 | 0,08-0,14 | Азот 0,025 |
С590 | 0,15 | 1,3-1,7 | 0,4-0,7 | 0,035 | 0,035 | 0,3 | 0,07-0,15 | Молибден 0,25 |
Как следует из табл. 1.2, для строительных сталей в качестве легирующих используются такие вещества, упрочняющие материал, как кремний, марганец, хром, медь, и в меньшей степени элементы, образующие специальные карбиды и нитриды. При этом пределы текучести и временное сопротивление большинства строительных сталей находятся на среднем уровне, более высокое легирование сдерживается ухудшением свариваемости, снижением сопротивления хрупкому разрушению и, главное, удорожанием материалов.
Основные механические характеристики проката из строительных сталей приведены в Марочнике сталей и табл.1.3.
Таблица 1.3
Механические свойства листового проката из сталей по ГОСТ 27772-88
Сталь | σт, МПа | σв, МПа | δ5, % | ан, дж/см2 (t=-20°C) | ан, дж/см2 (t=-40°C) | ан, дж/см2 (t=-70°C) | ан, дж/см2 после механического старения | Марка-аналог по другим стандартам |
С235 | 225-235 | 360 | 25-26 | - | - | - | - | ВСт3кп2 |
С245 | 235-245 | 370 | 24-25 | - | - | - | 28 | ВСт3пс6 |
С255 | 235-255 | 370-380 | 24-26 | 29 | - | - | 29 | ВСт3сп5, ВСт3Гпс5 |
С275 | 265-275 | 370-390 | 23-24 | - | - | - | 29 | ВСт3пс6-2 |
С285 | 265-285 | 380-390 | 23-24 | 29 | - | - | 29 | ВСт3сп5-2, ВСт3Гпс5-2 |
С345(Т) | 305-345 | 460-490 | 21 | - | 34 | 29 | 29 | 09Г2С, 14Г2, 12Г2С |
С345 | 265-345 | 430-490 | 20-21 | - | 34 | 29 | 29 | 09Г2, 15ХСНД, 14Г2 |
С390 | 390 | 540 | 20 | - | - | - | 29 | 14Г2Ф, 10ХСНД, 10Г2С1 т.о. |
С440 | 410-440 | 570-590 | 20 | - | - | 29 | - | 16Г2АФ |
С590 | 590 | 685 | 14 | - | 34 | - | - | 14Г2СМФ |
Строительные стали являются весьма распространенными материалами, производимыми в различных промышленных странах. При этом марки имеют зарубежные аналоги как по химическому составу, так и по свойствам, а основным критерием, характеризующим марку, является величина либо предела текучести (как в СНГ, США, Бельгии), либо предела прочности (как в Евронормах и большинстве европейских стран). Эти значения признаны определяющими расчетными и эксплуатационными показателями сталей при производстве строительных конструкций.
Для сталей с гарантированными механическими свойствами по толщине (с повышенной сопротивляемостью слоистому разрушению) в качестве критерия выбирается величина относительного сужения ψ. Чтобы обеспечить требуемые значения ψ (не менее 15-30%), материалы подвергаются внепечному рафинированию и модифицированию (направленному воздействию на состав, форму и распределение неметаллических включений). В таких сталях содержание серы снижается до 0,005-0,010%.
Хладостойкие стали для конструкций, эксплуатирующихся при низких температурах (в основном, для изотермических резервуаров, позволяющих хранить и транспортировать сжиженные газы), имеют повышенное содержание никеля 6 и 9 % при углероде не более 0,1 %. Оптимальные свойства материалов достигаются после термической обработки, включающей закалку или двойную нормализацию и отпуск. В этом случае обеспечиваются необходимые механические свойства: σв> 630 МПа, σ0,2>470 МПа, δ > 15-20%.
Дата добавления: 2018-02-28; просмотров: 842; Мы поможем в написании вашей работы! |
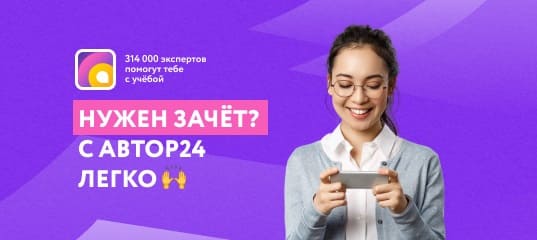
Мы поможем в написании ваших работ!