Классификация способов химического и электрохимического осаждения материалов. Виды и назначение покрытий
Применение пайки при ремонте машин. Сущность пайки и области ее применения
Пайка – процесс получения неразъемного соединения металла, находящегося в твердом состоянии, при помощи расплавленного металла или сплава, имеющего температуру плавления ниже, чем соединяемые металлы.
При ремонте автомобиля пайку используют для устранения трещин и пробоин в радиаторе, топливных и масляных баках, трубопроводах, приборов электрооборудования и т.д.
Пайка имеет следующие преимущества:
+ простота технологического процесса, применяемого оборудования.
+ сохранение точной формы, размеров, химического состава деталей.
+ возможность соединения деталей, изготовленных из разнородных металлов.
+ достаточно высокая прочность соединения деталей.
+ низкая себестоимость восстановления деталей.
Основной недостаток – некоторое снижение прочности соединения деталей по сравнению со сваркой.
Легкоплавкие припои представляют собой сплавы цветных металлов. Наибольшее применение получили оловянно-свинцовые припои (ПОС): ПОС-18, ПОС-30, ПОС-40, ПОС-50 (цифры – содержание олова). Эти припои применяются для восстановления деталей, работающих при высоких температурах и небольших нагрузках (радиатор, топливный бак, электрические провода).
Тугоплавкие припои представляют собой чистые цветные металлы и их сплавы. Медно-цинковые припои марок ПМЦ-54, ПМЦ-48 (цифры указывают процентное содержание меди в припое) применяют для пайки меди, бронзы, латуни и других металлов. Лучшие тугоплавкие припои – серебряно-медно-цинковые ПСр10, ПСр25, ПСр12М (цифра указывает %-ное содержание серебра в припое). Эти припои позволяют получать высокопрочные и пластичные соединения, но очень дорогие.
|
|
Применение полимерных материалов при ремонте машин.
При ремонте машин широко применяют полимерные материалы как для изготовления, так и для восстановления деталей. Это объясняется тем, что они обладают рядом ценных свойств (небольшая объемная масса, значительная прочность, хорошая химическая стойкость, высокие антифрикционные и диэлектрические свойства, вибростойкость, достаточно высокая теплостойкость некоторых из них и т. д.).
Использование полимеров позволяет во многих случаях избежать сложных технологических процессов при восстановлении деталей, таких, как сварка, наплавка, гальванические покрытия и др. Технология применения полимеров проста и доступна для внедрения на ремонтных предприятиях.
Классификация способов восстановления деталей полимерными материалами и их сущность.Восстановление деталей является одним из основных источников повышения экономической эффективности автомобильного производства.
|
|
Основная задача, которую преследуют ремонтные предприятия, – это снижение себестоимости ремонта автомобилей и агрегатов при обеспечении гарантий потребителей, т. е. гарантии послеремонтного ресурса.
Значение восстановления деталей состоит так же в том, что оно позволяет уменьшить потребности в производстве запасных частей.
Исследования ремонтного фонда (автомобилей и агрегатов, поступающих в ремонт) показали, что в среднем около 20 % деталей – утильных, 25...40 % – годных, а остальные 40...55 % – можно восстановить.
Даже процент утильных деталей можно значительно снизить на АРП, если оно будет располагать эффективными способами дефектации и восстановления.
При восстановлении деталей сокращаются расходы, связанные с обработкой деталей, т.к. при этом обрабатываются не все поверхности деталей, а лишь те, которые имеют дефекты.
Технологии восстановления деталей относятся к разряду наиболее ресурсосберегающих, так как по сравнению с изготовлением новых деталей сокращаются затраты (на 70 %). Основным источником экономии ресурсов являются затраты на материалы. Средние затраты на материалы при изготовлении деталей составляют 38 %, а при восстановлении – 6,6 % от общей себестоимости. Для восстановления работоспособности изношенных деталей требуется в 5...8 раз меньше технологических операций по сравнению с изготовлением новых деталей.
|
|
Несмотря на рентабельность, трудоёмкость восстановления деталей ещё неоправданно высока и даже на крупных ремонтных предприятиях в среднем до 1,7 раз больше трудоёмкости изготовления одноименных деталей на автомобильных заводах.
Мелкосерийный характер производства, использование универсального оборудования, частые его переналадки, малые партии восстанавливаемых деталей затрудняют возможность значительного снижения трудоёмкости отдельных операций.
Основное количество отказов деталей автомобилей вызвано износом рабочих поверхностей – до 50 %, 17,1 % связано с повреждениями и 7,8 % вызвано трещинами.
Основное место среди технологических отказов автомобилей занимает двигатель – это до 43 % отказов. Примерно 85 % деталей восстанавливают при износе не более 3 мм, т. е. их работоспособность восстанавливается при нанесении покрытия незначительной толщины. Нанесение металла на несущие поверхности с последующей механической обработкой позволит многократно использовать деталь.
|
|
Эффективность и качество восстановления деталей в значительной степени зависит от технических возможностей способа, обеспечивающего необходимый уровень эксплуатационных свойств. В зависимости от характера устраняемых дефектов, все способы восстановления деталей подразделяются на три основные группы:
· восстановление деталей с изношенными поверхностями,
· механическими повреждениями,
· повреждениями противокоррозионных покрытий.
Доля восстанавливаемых наружных и внутренних цилиндрических поверхностей составляет 53,3 %, резьбовых – 12,7 %, шлицевых – 10,4 %, зубчатых – 10,2 %, плоских – 6,5 %, все остальные – 6,9 %.
Классификация способов химического и электрохимического осаждения материалов. Виды и назначение покрытий
В основе электрохимического осаждения металлических пленок лежит явление электролиза, при котором происходит катодное восстановление катионов. Впервые явление восстановления катионов металла исследовал русский физик и электротехник Б.С.Якоби, работы которого легли в основу гальваностегии (осаждение тонких пленок металлов) и гальванопластики (изготовление рельефных металлических копий с предметов)Электрохимическое осаждение применяют для создания контактных систем на диэлектрических подложках с предварительно нанесенной тонкой проводящей пленкой, получения объемных омических контактов-выводов к активным областям полупроводниковых структур, изготовления свободных масок, получения покрытий на деталях корпусов, обеспечивающих качественную герметизацию и в некоторых случаях защиту от коррозии.Для осаждения пленок подготовленные подложки помещают в электролитическую ванну на катоде (рис.10.2). Анод обычно изготавливают из того же металла, что и осаждаемая пленка. В состав электролита входит соль осаждаемого металла. Процесс осаждения пленок сопровождается растворением анода, что предотвращает обеднение электролита ионами металла. Площадь поверхности анода приблизительно в 1,5 раза превышает площадь поверхности, на которую осаждается пленка.Электрохимическое осаждение металлов согласно современным представлениям происходит в четыре стадии:1) электролитическая диссоциация соли в растворе;2) перенос ионов из объема электролита к электроду;3) переход ионов на границе фаз из объема электролита к металлу;4) диффузия адсорбированных атомов по поверхности электрода к местам роста пленки и встраивание атомов в кристаллическую решетку.Цинкование является основным методом защиты от коррозии деталей из черных металлов. Покрытие хорошо выдерживает развальцовку и изгибы, но плохо паяется и приваривается. Для деталей, работающих на трение, цинковое покрытие непригодно. Оно не может быть декоративным, так как на воздухе цинк тускнеет покрываясь тонкой пленкой окислов.Кадмирование применяется как антикоррозийное и декоративное покрытие для деталей из стали, цветных металлов и сплавов. Кадмий по своим химическим свойствам весьма близок к цинку, но более стоек. В отличие от цинка кадмий нерастворим в щелочах. Хорошие результаты дает кадмиевое покрытие при защите деталей, работающих в морских условиях. Кадмий хорошо
покрывает углубленные места и применяется для деталей, имеющих резьбу, подвергающихся развальцовке, вытяжке, гибке.Хромированиеприменяют для придания поверхностному слою высокой коррозийной стойкости, высокой твердости, износостойкости и жаростойкости. Недостатки этих покрытий: значительная пористость; плохая смачиваемость маслом; хрупкость. Xpoм обладает коррозийной стойкостью по отношению ко многим кислотам, щелочам и солям. Покрытие сохраняет свой блеск и окраску при высоких температурах (до 500°С).Меднение является самым распространенным защитно-декоративным покрытием. Гальванически осажденная медь имеет красивый розовый цвет; в условиях атмосферной коррозии легко покрывается окислами и темнеет. Как самостоятельное покрытие меднение применяют для местной защиты стальных деталей от цементации и увеличения электропроводности. Толщина слоя в этом случае составляет 20…40 мкм.Никелирование широко применяется благодаря ценным физико-химическим свойствам никеля. Покрытия хорошо полируются, устойчивы в растворах многих солей и щелочей. Как защитно-декоративное покрытие его применяют обычно с подслоем меди. Толщина слоя никеля берется от 5 до 15 мкм. Никелирование без подслоя применяется лишь для мелких и крепежных деталей. Толщина покрытия принимается от 12 до 35 мкм .Лужением называется процесс образования на поверхности материала металлического слоя путем плавления припоя, смачивания припоем поверхности и последующей его кристаллизации. Лужение осуществляется паяльником или погружением деталей в расплавленный припой.Лужение применяют для предохранения от окисления и облегчения пайки, для герметизации свинчиваемых резьбовых соединений и др.
Дата добавления: 2018-02-28; просмотров: 411; Мы поможем в написании вашей работы! |
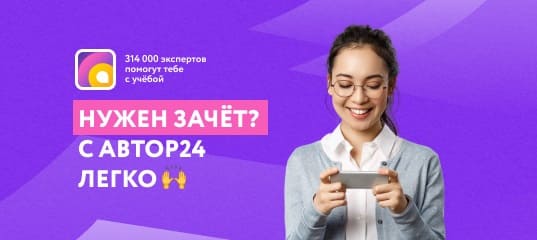
Мы поможем в написании ваших работ!