Стержни классифицируют по ряду признаков.
Вопрос №16
Элетрошлаковый переплав.
Этот переплав происходиит в элетропечах дугового типа.
Электропечи имеют преимущества т.к в них можно получать высокую температуру металла,создавать окислительную,восстановительную, нейтральную, вакуум что позволяет выплавлять сталь любого состава. Используется для выплавки конструкционных,высоколегированных инструментальных специальных сплавов и сталей.
Ээлекстропечи бывают:
-дуговые
-индукционными
дуговые печи питаются трехфазным током. В них может быть плавка двух видов
-на шихте из легированных отходов легированных сталей и сплавов(это и есть метод переплава)
-на углеродистой шихте (этот метод окисления примесей.
Мощность тока в дуговой печи порядка 25-45кВ. Для выплавки легированных сталей в дуговыых печах в сталь вводят легирующие элементы в виде ферросплавов. Для равномерного горения дуги добавляют в шихту кальций!
Вопрос №7
сущность передела чугуна в сталь.
Сущность передела чугуна в сталь является снижение содержание углерода и примесей путем их избирательного окисления и перевода в шлак и газы в процессе плавки.
Основным материалом для производства стали является передельный чугун и стальной лом. Содержание углерода в стали меньше чем в чугуне а именно 2.14%
в процессе производства в первую очередь окисляется железо с выделением тепла. Почти одновременно с ним окисляются активные элементы как Si,P,C,Mn....с выделением или поглащением тепла.
|
|
Сам же процесс идет в несколько этапов:
1. расплавление шихты и нагрев ванны жидкого металла
2. «кипение» металлической ванны. На этом этапе выделяется в виде пузырьков газ СО и создается эффект как при кипении поэтому и кипение называется.
3. Раскисление стали. Происходит восстановление оксида железа растворенного в жидком металле.
Все реакции протекаемы при производсте подчиняются закону распределения и принципу Ле Шателье(реакции с выделением теплоты идут быстрее при пониженных температурах среды в которой проходит реакция.).
Вопрос №14
) Общая характеристика индукционных тигельных печей
Индукционный нагрев — нагрев тел в электромагнитном поле за счёт теплового действия вихревых электрических токов, протекающего по нагреваемому телу и возбуждаемого в нём благодаря явлению электромагнитной индукции. При этом ток в нагреваемом изделии называют индуцированным или наведённым током. Индуцированными установками называют электротермические устройства, предназначенные для индукционного нагрева тел или плавки тех или иных материалов. Индукционная печь — часть индукционной установки, включающая в себя индуктор, каркас, камеру для нагрева или плавки, вакуумную систему, механизмы наклона печи или перемещения нагреваемых изделий в пространстве и др. Индукционная тигельная печь (ИТП), которую иначе называют индукционной печью без сердечника, представляет собой плавильный тигель, обычно цилиндрической формы, выполненный из огнеупорного материала и помещённый в полость индуктора, подключенного к источнику переменного тока. Металлическая шихта загружается в тигель, и, поглощая электромагнитную энергию, плавится.
|
|
Достоинства тигельных плавильных печей:
Выделение энергии непосредственно в загрузке, без промежуточных нагревательных элементов;
Интенсивная электродинамическая циркуляция расплава в тигле, обеспечивающая быстрое плавление мелкой шихты, отходов, выравнивание температуры по объёму ванны и отсутствие местных перегревов, гарантирующая получение многокомпонентных сплавов, однородных по химическому составу;
Принципиальная возможность создания в печи любой атмосферы (окислительной, восстановительной или нейтральной) при любом давлении;
Высокая производительность, достигаемая благодаря высоким значениям удельной мощности, особенно на средних частотах;
|
|
Возможность полного слива металла из тигля и относительно малая масса футеровки печи, что создаёт условия для снижения тепловой инерции печи благодаря уменьшению тепла, аккумулируемого футеровкой. Печи этого типа удобны для периодической работы с перерывами между плавками и обеспечивают возможность быстрого перехода с одной марки сплава на другую;
Простота и удобство обслуживания печи, управления и регулировки процесса плавки, широкие возможности для механизации и автоматизации процесса;
Высокая гигиеничность процесса плавки и малое загрязнение воздуха.
К недостаткам тигельных печей относятся относительно низкая температура шлаков, наводимых на зеркало расплава с целью его технологической обработки. Шлак в ИТП разогревается от металла, поэтому его температура всегда ниже, а также сравнительно низкая стойкость футеровки при высоких температурах расплава и наличие теплосмен (резких колебаний температуры футеровки при полном сливе металла). Однако преимущества ИТП перед другими плавильными агрегатами значительны, и они нашли широкое применение в самых разных отраслях промышленности.
В зависимости от того, идёт ли процесс плавки на воздухе или в защитной атмосфере, различают печи:
|
|
открытые (плавка на воздухе),
вакуумные (плавка в вакууме),
компрессорные (плавка под избыточным давлением).
По организации процесса во времени:
периодического действия
полунепрерывного действия
непрерывного действия
По конструкции плавильного тигля:
с керамическим (футерованным) тиглем,
с проводящим металлическим тиглем,
с проводящим графитовым тиглем,
с холодным (водоохлаждаемым) металлическим тиглем.
Контактное устройство индукционной тигельной печи
Электрооборудование включает в себя:
печь,
комплект измерительных приборов с трансформаторами,
генератор повышенной или высокой частоты,
коммутационную и защитную аппаратуру,
конденсаторную батарею, ёмкость которой можно менять.
Электрооборудование и измерительные приборы в случае повышенной и высокой частоты должно иметь специальное исполнение, допускающее использование специальной аппаратуры в зоне повышенных частот.
Переключатель S позволяет изменять в процессе плавки коэффициент связи индуктора и садки. Такое изменение необходимо в связи с тем, что активное сопротивление шихты различно в различные моменты процесса. Контакторы К1, К2, К3 позволяют изменять в процессе плавки ёмкость компенсирующей конденсаторной батареи и поддерживать cos.=1 в цепи индуктора. Это приходится делать, потому что во время плавки также изменяется и индуктивное сопротивление садки, так как изменяется магнитная проницаемость, величины вихревых токов и т. д.
Вопрос №23
) Литейная форма (рис. 2) представляет собой систему элементов, образующих рабочую полость с внешними контурами получаемой отливки. После заливки в такую полость жидкого металла он охлаждается в ней и затвердевает, образуя отливку.
Литейная форма состоит из нескольких, обычно из двух, частей (полуформ), собранных в одно целое. Полуформа, т. е. верхняя или нижняя половина литейной формы, представляет собой опоку, в которой находится в уплотненном состоянии смесь неорганических (кварцевый песок, глина и др.) и органических (опилки, уголь и др.) материалов.
Назначение литейной опоки — удерживать смесь при ее уплотнении, перемещении и сборке полуформ. Опоки снабжают цапфами или ручками для их транспортирования. Крупные опоки имеют крестовины, которые придают опоке жесткость и прочность.
Сборку полуформ производят по штырям, которые вставляют в отверстия приливов на опоке. Штыри — тщательно обработанные металлические стержни. При ручной формовке и сборке форм применяют обычно одни и те же штыри. Иногда штыри закрепляют в нижней опоке.
В литейной форме выполняют систему каналов, т. е. литниковую систему, предназначенную для подвода жидкого металла в полость формы и для обеспечения ее заполнения, а также питания отливки при затвердевании. Литниковая система включает подводящие (чашу, стояк, шлакоуловитель, питатели) и питающие (прибыль, выпор) элементы.
Все объявления
Рис. 2. Литейная форма:
1, 2 —полуформы, 3 — выпор, 4 — крестовины опок, 5 — литниковая чаша, 6 — стояк, 7 — шлакоуловитель, 8 — штырь, 9 — питатель, 10 — цапфа опоки, 11 — вентиляционные каналы, 12 — жеребенка, 13 — холодильник, 14 — стержень, 15 — полость формы
Для приема расплавленного металла и удерживания шлака служит литниковая чаша, расположенная в верхней полуформе. Вертикальный или наклонный канал — стояк предназначен для подачи металла из литниковой чаши в шлакоуловитель. Последний расположен горизонтально и предназначен для удерживания шлака и других неметаллических примесей расплавленного металла. Следующий за шлакоуловителем литниковый канал — питатель (их может быть несколько) служит для подвода жидкого металла непосредственно в рабочую полость формы.
Для вывода газов из рабочей полости формы, для контроля заполнения формы расплавленным металлом при заливке, а иногда для питания отливки при затвердевании служит вертикальный канал — выпор, расположенный в верхней полуформе. Кроме того, для улучшения газопроницаемости формы в ней выполняют вентиляционные каналы — тонкие полости, получаемые при накалывании полуформ острыми металлическими иглами-душниками.
В массивных частях отливки могут возникнуть дефекты усадочного происхождения — поры, раковины, которые снижают ее прочность. Такие дефекты предупреждают использованием прибыли — элемента литниковой системы в виде полости, заполняемой жидким металлом для питания отливки в процессе ее затвердевания. С этой же целью применяют металлические холодильники, которые устанавливают в форму около массивных частей отливки.
Литейный стержень — элемент литейной формы, предназначенный для образования отверстий, полостей или других сложных контуров в отливке. Стержни в форме фиксируют на знаках — выступах, входящих в соответствующие впадины рабочей полости. Дополнительными опорами стержней являются металлические подставки (жеребейки) различной конструкции и конфигурации, которые сплавляются с заливаемым в форму жидким металлом.Литейная форма (рис. 2) представляет собой систему элементов, образующих рабочую полость с внешними контурами получаемой отливки. После заливки в такую полость жидкого металла он охлаждается в ней и затвердевает, образуя отливку.
Литейная форма состоит из нескольких, обычно из двух, частей (полуформ), собранных в одно целое. Полуформа, т. е. верхняя или нижняя половина литейной формы, представляет собой опоку, в которой находится в уплотненном состоянии смесь неорганических (кварцевый песок, глина и др.) и органических (опилки, уголь и др.) материалов.
Назначение литейной опоки — удерживать смесь при ее уплотнении, перемещении и сборке полуформ. Опоки снабжают цапфами или ручками для их транспортирования. Крупные опоки имеют крестовины, которые придают опоке жесткость и прочность.
Сборку полуформ производят по штырям, которые вставляют в отверстия приливов на опоке.
на модельную плиту 3 устанавливаютнижнюю половину модели -1, модели питателей 4 и опоку 5 (рис. 4.12, б), в которую засыпают формовочную смесь и уплотняют. Опоку поворачивают на 180° (рис. 4.12, в), устанавливают верхнюю половину модели 2, модели шлакоуловителя 9, стояка 8 и выпоров 7. По центрирующим штырям устанавливают верхнюю
опоку 6, засыпают формовочную смесь и уплотняют. После извлечения модели стояка и выпоров форму раскрывают. Из полуформ извлекают модели (рис. 4.12, г) и модели питателей и шлакоуловителей, в нижнюю полуформу устанавливают стержень 10 (рис. 4.12, д) и накрывают нижнюю полуформу верхней. На рис. 4.12, е показана литейная форма для корпуса вентиля. После заливки расплавленного металла и его затвердевания литейную форму разрушают и извлекают отливку (рис. 4.12, ж).
Вопрос 20
Модельный комплект – совокупность технологической оснастки и приспособлений необходимых для образования в форме полости, соответствующей контурам отливки. В модельный комплект включают модели, модельные плиты, стержневые ящики и другие приспособления.
Литейная модель-приспособление с помощью которого в литейной форме получают полость с формой и размерами, близкими к конфигурации получаемой отливки. Модели бывают неразъемные, с отъемными частями и др.
Модельная плита- металлическая плита с закрепленными на ней моделями и элементами литниковой системы.
Стержневой ящик-приспособление,служащее для изготовления стержней. Бывают:цельные, разъемные, вытряхные.
Вопрос 29
Литье по выплавляемым моделям- это способ получения отливок заливкой расплавленного металла в разовую тонкостенную неразъемную литейную форму, изготовленную из жидкоподвижной огнеупорной суспензии по моделям разового использования с последующим затвердиванием залитого металла, охлаждением отливки в форме и извлечением отливки из формы. Отличительные особенности литья: низкая теплопроводность, плотность материалов формы, хорошая заполняемость полости формы, низкая скорость затвердивания отливок, укрупление кристаллического строения и тд.
Технологический процесс: изготовление моделей и сборка модельных блоков,покрытие моделей огнеупорной оболочкой,выплавление модельного состава, подготовка литейных форм к заливке, заливка расплавленного металла в литейную форму, затвердивание и охлаждение отливок,выбивка отливок и их отделения от литниковой системы, очистка отливок.
Этим способом литья получают сложные по конфигурации отливки с толщиной стенки 1..3 мм и массой от нескольких граммов до нескольких десятков килограммов из жаропрочных труднообрабатываемых сплавов, коррозиционныно стойкие стали,углеродистые стали.
Вопрос № 2
Чугун - сплав железа с углеродом (обычно более 2%) содержащий также постоянные примеси (Si, Mn, Р и S). Ч. — важнейший первичный продукт чёрной металлургии, используемый для передела при производстве стали и как компонент шихты при вторичной плавке в чугунолитейном производстве. Ч. вторичной плавки — один из основных конструкционных материалов; применяется как литейный сплав. Широкому использованию Ч. в машиностроении способствуют его хорошие литейные и прочностные свойства (по прочности некоторые Ч. лишь немногим уступают углеродистой стали.
Классификация и свойства чугуна.
Чугун - основной продукт доменной плавки. В доменных печах получают чугун различного хим-ого состава в зависимости от его назначения. Получаемый чугун в доменных печах, подразделяется на передельный чугун, используемый для передела в сталь, и литейный чугун, служащий одним из основных компонентов шихты в чугунолитейном производстве (используют на машиностроительных заводах при производстве фасонных отливок).
Виды чугуна:
Серый Чугун (СЧ). ГОСТ 1412-70 — наиболее широко применяемый вид Ч. (машиностроение, сантехника, строительные конструкции) — имеет включения графита пластинчатой формы. Для деталей из серого Ч. характерны малая чувствительность и более высокий коэффициент поглощения колебаний при вибрациях деталей. Важная конструкционная особенность серого Ч. — более высокое, чем у стали, отношение предела текучести к пределу прочности на растяжение. Наличие графита улучшает условия смазки при трении. Свойства серого Ч. зависят от структуры металлической основы, формы, величины, количества и характера распределения включений графита. Перлитный серый Ч. имеет высокие прочностные свойства и применяется для цилиндров, втулок и др. нагруженных деталей двигателей, станин и т.д. Для менее ответственных деталей используют серый Ч. с ферритно-перлитной металлической основой. СЧ 12- двузначное число 12 обозначает предел прочности при растяжении (кге/) содержит от 2,8-3,5% углерода, входит Cr и Mn. Серый чугун в виде пластинок.
Белый Чугун - представляет собой сплав, в котором избыточный углерод, присутствует в связанном состоянии в виде карбидов железа Fe3C (цементит- хим. Соединение железа с углеродом 6,67%). Кристаллизация белых Ч. происходит по метастабильной системе с образованием цементита и перлита. Белый Ч. вследствие низких механических свойств и хрупкости имеет ограниченное применение для деталей простой конфигурации, работающих в условиях повышенного абразивного износа. Легирование белого Ч. карбидообразующими элементами (Cr, W, Mo и др.) повышает его износостойкость. Плохая свариваемость.
Половинчатый Чугун - содержит часть углерода в свободном состоянии в виде графита, а часть — в связанном в виде карбидов. Применяется в качестве фрикционного материала, работающего в условиях сухого трения (тормозные колодки), а также для изготовления деталей повышенной износостойкости (прокатные, бумагоделательные, мукомольные валки).
Ковким называется Чугун - в отливках, изготовленных из белого Ч. и подвергнутых последующему графитизирующему отжигу, в результате чего цементит распадается, а образующийся графит приобретает форму хлопьев. Ковкий Ч. обладает лучшей демпфирующей способностью (Способность материала поглотить вибрацию (циклические нагрузки) за счет внутреннего трения), чем сталь, и меньшей чувствительностью к надрезам, удовлетворительно работает при низких температурах. Механические свойства ковкого Ч. определяются структурой металлической основы, количеством и степенью компактности включений графита. Металлическая основа ковкого Ч. в зависимости от типа термообработки может быть ферритной, ферритно-перлитной и перлитной. Наиболее высокими свойствами обладает ковкий Ч., имеющий матрицу со структурой зернистого перлита; им можно заменять литую или кованую сталь. В тех случаях, когда требуется повышенная пластичность, применяют ферритный ковкий Чугун. КЧ 30-6 – первое число обознач. Предел прочности, второе относительное удлинение в %. Содержит 2,4-2,8 С, входит Si и Mn.
ГОСТ 1215-59
Высокопрочный Чугун - характеризующийся шаровидной или близкой к ней формой включений графита, получают модифицированием жидкого чугуна присадками Mg, Ce, Y, Ca и некоторых др. элементов. Высокопрочный Ч. обладает хорошими литейными и технологическими свойствами (жидкотекучесть, линейная усадка, обрабатываемость резанием). Такой Ч. применяется для замены стальных литых и кованых деталей (коленчатые валы двигателей, компрессоров и т.д.), а также деталей из ковкого или обычного серого Ч. ВЧ 50-2 двузначное число обозначает предел прочности при растяжении (кге/), второе ударную вязкость. Содержит 3,2% С, входит Cr и Mn.
ГОСТ 7239-77
Легированные Чугун - Для улучшения прочностных, эксплуатационных характеристик или придания Ч. особых свойств (износостойкости, жаропрочности, жаростойкости, коррозионностойкости, немагнитности и т.д.) в его состав вводят легирующие элементы (Ni, Cr, Cu, Al, Ti, W, V, Mo и др.). Легирующими элементами могут служить также Mn при содержании > 2% и Si при содержании > 4%. Легированные Ч. классифицируют в соответствии с содержанием основных легирующих элементов — хромистые, никелевые, алюминиевые и т.д. По степени легирования различают низколегированные (суммарное количество легирующих элементов < 2,5%), среднелегированные (2,5—10%) и высоколегированные (> 10%).
Вопрос №15
В индукционных печах металл нагревается токами, возбуждаемыми в непеременным полем индуктора. По существу индукционные печи также являются печами сопротивления, но отличаются от них способом передачи энергии нагреваемому металлу. В отличие от печей сопротивления электрическая энергия в индукционных печах превращается сначала в электромагнитную, затем снова в электрическую и, наконец, в тепловую.
При индукционном нагреве тепло выделяется непосредственно в нагреваемом металле, поэтому использование тепла оказывается наиболее полным. С этой точки зрения эти печи — наиболее совершенный тип электрических печей.
Индукционные печи бывают двух типов: с сердечником и без сердечника тигельные. В печах с сердечником металл находится в кольцевом желобе вокруг индуктора, внутри которого проходит сердечник. В тигельных печах внутри индуктора располагается тигель с металлом. Применить замкнутый сердечник в этом случае невозможно.
В силу ряда электродинамических эффектов, возникающих в кольце металла вокруг индуктора, удельная мощность канальных печей ограничивается определенными пределами. Поэтому эти печи используют преимущественно для плавления легкоплавких цветных металлов и лишь в отдельных случаях применяют для расплавления и перегрева чугуна в литейных цехах.
Удельная мощность индукционных тигельных печей может быть достаточно высока, а силы, возникающие в результате взаимодействия магнитных печей металла и индуктора, оказывают в этих печах положительное воздействие на процесс, способствуя перемешиванию металла. Бессердечниковые индукционные печи применяют для выплавки специальных, особенно низкоуглеродистых сталей и сплавов на основе никеля, хрома, железа, кобальта.
![]() |
Рисунок 2. Конструкция индукционной печи а - конструктивное оформление; 1 - индуктор, 2 - крепление витков индуктора, 3 - каркас, 4 - изоляция, 5 - подовая плита, 6 - тигель, 7 - цапфы, 8 - крышка б - футеровка тигля; 1 - подовая плита, 2 - тигель, 3 - воротник, 4 - сливной желоб, 5 - огнеупорная обмазка |
Важным достоинством тигельных печей являются простота конструкции и малые габариты. Благодаря этому они могут быть полностью помещены в вакуумную камеру и в ней возможно по ходу плавки обрабатывать металл вакуумом. Как вакуумные сталеплавильные агрегаты индукционные тигельные печи получают все более широкое распространение в металлургии качественных сталей.
![]() |
Рисунок 3. Схематическое изображение индукционной канальной печи (а) и трансформатора (б)
Вопрос №28
Литьё металлов в кокиль — более качественный способ. Изготавливается кокиль — разборная форма (чаще всего металлическая), в которую производится литьё. После застывания и охлаждения, кокиль раскрывается и из него извлекается изделие. Затем кокиль можно повторно использовать для отливки такой же детали. В отличие от других способов литья в металлические формы (литьё под давлением, центробежное литьё и др.), при литье в кокиль заполнение формы жидким сплавом и его затвердевание происходят без какого-либо внешнего воздействия на жидкий металл, а лишь под действием силы тяжести.
Основные операции и процессы: очистка кокиля от старой облицовки, прогрев его до 200—300°С, покрытие рабочей полости новым слоем облицовки, простановка стержней, закрывание частей кокиля, заливка металла, охлаждение и удаление полученной отливки. Процесс кристаллизации сплава при литье в кокиль ускоряется, что способствует получению отливок с плотным и мелкозернистым строением, а следовательно, с хорошей герметичностью и высокими физико-механическими свойствами. Однако отливки из чугуна из-за образующихся на поверхности карбидов требуют последующего отжига. При многократном использовании кокиль коробится и размеры отливок в направлениях, перпендикулярных плоскости разъёма, увеличиваютс я.
В кокилях получают отливки из чугуна, стали, алюминиевых, магниевых и др. сплавов. Особенно эффективно применение кокильного литья при изготовлении отливок из алюминиевых и магниевых сплавов. Эти сплавы имеют относительно невысокую температуру плавления, поэтому один кокиль можно использовать до 10000 раз (с простановкой металлических стержней). До 45 % всех отливок из этих сплавов получают в кокилях. При литье в кокиль расширяется диапазон скоростей охлаждения сплавов и образования различных структур. Сталь имеет относительно высокую температуру плавления, стойкость кокилей при получении стальных отливок резко снижается, большинство поверхностей образуют стержни, поэтому метод кокильного литья для стали находит меньшее применение, чем для цветных сплавов. Данный метод широко применяется при серийном и крупносерийном производстве.
Вопрос № 24
Литейный стержень— это элемент литейной формы для образования отверстия, полости или иного сложного контура в отливке. Для получения сложных или очень крупных отливок применяют формы, собранные из стержней, их также используют для выполнения элементов литниковой системы.
Стержни классифицируют по ряду признаков.
1. По кратности использования стержни подразделяют на разовые и многократные. Разовые стержни применяют для получения одной отливки, различают два вида разовых стержней:
песчаные, удаляемые из отливки на выбивной решетке или на специальном оборудовании (вибрационных машинах, пескогидравлических камерах, галтовочных барабанах и др.), такие стержни используют наиболее часто;
металлические, изготовленные из легкоплавких сплавов, образуют в отливках сложные, обычно криво-линейные и узкие каналы, удаляют такие стержни из отливок выплавлением.
Многократные металлические стержни изготовляют из стали и реже из чугуна, стержни применяют для образования в отливках отверстий и полостей. Наиболее часто такие стержни используют на современных кокильных машинах.
Разовые стержни бывают песчаные, песчано-глинистые, песчано-смоляные, песчаные с встроенными наружными и внутренними холодильниками, керамические.
2. Разовые стержни из песка подразделяют по массе и иногда по объему на мелкие, средние и крупные.
3. С учетом метода упрочнения разовые стержни могут быть сырые, сухие, химически и самотвердеющие, спекаемые в нагреваемых ящиках.
4. По конструктивным признакам различают стержни сплошные, тонкостенные и оболочковые (рис. 15, а, б, в).
5. По назначению стержни подразделяют на:
центровые, образующие в отливках отверстия или перекрывающие сверху полость вытряхного кокиля;
наружные, образующие на наружных стенках отливки сложные поверхности, приливы, бобышки, а также защищающие отдельные части кокиля от быстрого изнашивания под действием струи расплава;
литниковые, применяемые для оформления всей или части литниковой системы (чаши или воронки, фильтровальной сетки, выпора, прибыли и др.);
вспомогательные, которые применяют для крепления основных стержней или служат прокладками между отливкой и толкателями в кокиле.
Вопрос №21
.Литниковая система, Литниковая питающая система — система каналов и полостей в форме, которые организуют плавное, бездефектное и направленное затвердевание отливки.
Литниковая система состоит из воронки или литниковой чаши, стояка, коллектора или шлаковика, питателей и выпора.
После затвердевания расплава металла литниковая система обрубается и идёт на переплав.
Литниковая система состоит из следующих элементов (рис. 55): литниковой чаши 1, стояка 2, коллектора или шлакоуловителя 3, питателей 4, выпора 5 и прибыли 6.
Рис. 55. Литниковая система
Литниковую чашу устраивают для приема металла из ковша и направления его в стояк. Литниковая чаша уменьшает силу удара струи жидкого металла о форму, обеспечив более равномерное питание формы, и задерживает шлак, всплывающий на поверхность металла в этой чаше.
Для лучшего удержания шлака при отливке ответственных Деталей в литниковой чаше делают перегородку, не доходящую до дна чаши, или ставят фильтровальные сетки.
Стояк — это вертикальный канал, по которому металл поступает в коллектор (шлакоуловитель). По последнему металл растекается к питателям, непосредственно соединяющим коллектор с полостями формы.
Шлаки, содержащиеся в жидком металле, частично отделяются от него в литниковой чаше, а частично всплывают и остаются в коллекторе (шлакоуловителе), не попадая в питатель.
В верхних частях отливки устраивают выпора, через которые выходит воздух при заполнении формы жидким металлом. В больших формах делают несколько выпоров.
По мере остывания объем металла, залитого в форму, уменьшается. Функции выпоров при больших размерах их поперечного сечения — дополнять формы жидким металлом в процессе остывания отливки.
Литниковая система, совокупность каналов (элементов), через которые расплав из ковша или другого разливочного устройства подводится к рабочей полости литейной формы. Назначение Литниковая система — обеспечение оптимальных условий и продолжительности заливки формы с целью получения отливки с чёткими гранями и контурами, предотвращение попадания неметаллических включений (при заливке из поворотного ковша), а при затвердевании сплава — питание отливки для предотвращения усадочных раковин. Элементы Литниковая система в соответствии с их назначением разделяют на подводящие и питающие (в некоторых частных случаях такого разделения не существует).
К подводящим элементам Литниковая система относятся: чаша, стояк, дроссель, шлакоуловитель (коллектор, литниковый ход) и питатель (рис., а). Чаша — приёмник расплава, для удобства заливки, задержания шлака и предотвращения засоса воздуха должна вмещать достаточный объём металла. Стояк — вертикальный (редко наклонный) канал, присоединённый к чаше. Дроссель — узкий канал (или несколько каналов), расположенный обычно в основании стояка, являющийся местным гидравлическим сопротивлением, регулирует скорость заливки и устраняет вакуум (разрежение) в стояке. Шлакоуловитель — канал, обычно вытянутого трапециевидного сечения, расположенный за дросселем, служит для подачи сплава к питателям и задержания неметаллических включений. Для более полного задержания шлака в Литниковая система устраивают местные расширения в шлакоуловителе, применяют центробежные шлакоуловители, фильтровальные сетки (для отливок из чугуна — из огнеупорной стержневой или шамотной смеси, для отливок из цветных сплавов — из тонкой листовой стали, для всех сплавов с температурой заливки до 1350°С — из кремнезёмной ткани). Шлакоуловители не нужны при заливке форм из стопорного ковша (шлак остаётся в ковше) и при плотности неметаллических включений, близкой к плотности сплава (у некоторых цветных сплавов). В этих случаях канал, называемый коллектором, или литниковым ходом, только распределяет сплав. Питатель — присоединённый к шлакоуловителю канал, обычно прямоугольного сечения, через который сплав поступает в рабочую полость формы непосредственно или через прибыль.
Размеры подводящих элементов определяются в основном гидродинамическими факторами (конструкцией Литниковая система, напором, расходом и скоростью расплава).
К питающим элементам Литниковая система относятся боковая прибыль и шейка (рис., а). Боковая прибыль — компактный прилив на боковой поверхности отливки, предназначенный для её питания во время остывания и затвердевания сплава. Шейка — суженная часть прибыли, соединяющая сё с отливкой. Питающие элементы должны затвердевать медленнее отливки. Их размеры определяются в основном тепловыми факторами (теплофизическими свойствами сплава и формы), литейными свойствами сплава, массой, толщиной стенок, конфигурацией отливки и требованиями к ней (механические свойства, герметичность и т. д.).
При получении тонкостенных отливок из эвтектических сплавов (например, серого чугуна) короткого времени остывания питателей обычно оказывается достаточно для питания отливок. В этих случаях спец. питающие элементы не нужны и Литниковая система состоит только из подводящих каналов (рис., б, в, г, д). Если для питания требуется небольшой объём сплава, то система наряду с подводящими элементами имеет подводяще-питающие, например шлакоуловитель может одновременно служить прибылью, а питатель — шейкой (рис., е).
В зависимости от способа и места подвода Литниковая система разделяют на боковые, верхние и дождевые, сифонные, ярусные (этажные) и щелевые. По способу формовки различают горизонтальные Литниковая система с расположением питателя в горизонтальной плоскости разъёма и вертикальные, у которых питатель расположен в вертикальной плоскости разъёма или вне основной плоскости разъёма формы.
Вопрос № 31
Центробежное литье
Центробежный метод литья (центробежное литьё) используется при получении отливок, имеющих форму тел вращения. Подобные отливки отливаются из чугуна, стали, бронзы и алюминия. При этом расплав заливают в металлическую форму, вращающуюся со скоростью 3000 об/мин.
Под действием центробежной силы расплав распределяется по внутренней поверхности формы и, кристаллизуясь, образует отливку. Центробежным способом можно получить двухслойные заготовки, что достигается поочерёдной заливкой в форму различных сплавов. Кристаллизация расплава в металлической форме под действием центробежной силы обеспечивает получение плотных отливок.
При этом, как правило, в отливках не бывает газовых раковин и шлаковых включений. Особыми преимуществами центробежного литья является получение внутренних полостей без применения стержней и большая экономия сплава в виду отсутствия литниковой системы. Выход годных отливок повышается до 95 %.
В нашем производстве используют машины с горизонтальными осями вращения. Широким спросом пользуются отливки втулок, гильз и других заготовок, имеющих форму тела вращения, произведенные с помощью метода центробежного литья. Что такое центробежное литьё?
Центробежное литье — это способ получения отливок в металлических формах. При центробежном литье расплавленный металл, подвергаясь действию центробежных сил, отбрасывается к стенкам формы и затвердевает. Таким образом получается отливка. Этот способ литья широко используется в промышленности, особенно для получения пустотелых отливок (со свободной поверхностью).
Технология центробежного литья обеспечивает целый ряд преимуществ, зачастую недостижимых при других способах, к примеру:
§ Высокая износостойкость.
§ Высокая плотность металла.
§ Отсутствие раковин.
§ В продукции центробежного литья отсутствуют неметаллические включения и шлак.
Центробежным литьём получают литые заготовки, имеющие форму тел вращения:
§ втулки;
§ венцы червячных колёс;
§ барабаны для бумагоделательных машин;
§ роторы электродвигателей.
Наибольшее применение центробежное литьё находит при изготовлении втулок из медных сплавов, преимущественно оловянных бронз.
По сравнению с литьём в неподвижные формы центробежное литьё имеет ряд преимуществ: повышаются заполняемость форм, плотность и механические свойства отливок, выход годного. Однако для его организации необходимо специальное оборудование; недостатки, присущие этому способу литья: неточность размеров свободных поверхностей отливок, повышенная склонность к ликвации компонентов сплава, повышенные требования к прочности литейных форм.
Вопрос № 18
18.Вакуумно-индукционных переплав осуществляют:
Выплавку металла в вакууме любого состава,раскисление металла с образованием минимального количества неметалических включений- продуктов раскисления.Используется для выплавки конструкционных, высоколигированных, инструментальных, специальных сплавов и сталей.
Вопрос № 27
Литье в оболочковые формы-это способ получения:отливок путем заливки расплавленного металла в разовую тонкостенную разъёмнуюлитейную форму,изготовленную из песчанно-смоляной смеси с термоактивным связующим по металлической нагреваемой модельной оснастке,с последующим затвердеванием залитого расплава, охаждением отливки в форме и выбивкой её из формы.
Вопрос 8.
Задача первого этапа выплавки стали заключается:
Задача первого этапа выплавки стали заключается в расплавлении шихты и нагреве ванны жидкого металла. На этом этапе температура металла невысока, происходит интенсивное окисление железа и окисление примесей(Si, P, Mn). Наболее важная задача данного процесса-удаление фосфора. Для этого используют основной шлак. содержащий CaO. Данный шлак должен поглощать из металла P и S и удерживать их.
Вопрос № 11
Мартеновская печь — печь для переработки передельного чугуна и лома в сталь нужного химического состава и качества. Название произошло от фамилии французского инженера и металлурга Пьера Мартена, создавшего первую печь такого образца в 1864 году.
В зависимости от состава огнеупорных материалов подины печи мартеновский способ выплавки стали может быть основным (в составе огнеупора преобладают СаО и MgO) и кислым (подина состоит из SiO2). Выбор футеровки зависит от предполагаемого состава шлака в процессе плавки.
1. скрап-процесс, при котором шихта состоит из стального лома (скрапа) и 25—45 % чушкового передельного чугуна; процесс применяют на заводах, где нет доменныхпечей, но расположенных в промышленных центрах, где много металлолома
Дата добавления: 2015-12-21; просмотров: 20; Мы поможем в написании вашей работы! |
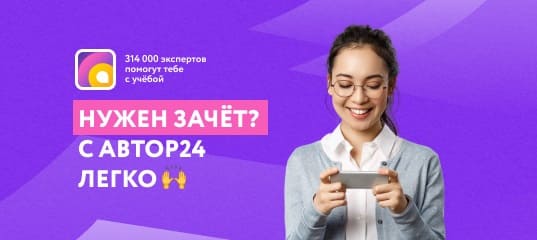
Мы поможем в написании ваших работ!