Обоснование выбора технологического процесса
Необходимо дать краткую характеристику действующего технологического процесса, обратив особое внимание на содержание технологической проблемы. Рассмотреть наиболее вероятные пути и способы устранения причин возникновения этих проблем. На основании краткого анализа их достоинств и недостатков осуществить выбор наиболее предпочтительного варианта.
При проектировании технологического процесса изготовления деталей (узлов, агрегатов) должен быть выбран такой вариант процесса, который наряду с требуемым качеством деталей обеспечивает их наименьшую себестоимость. При сравнении различных технологических вариантов нет необходимости вести расчет по всей номенклатуре затрат, из которых складывается себестоимость детале-операции. В расчет принимаются только те затраты, которые различаются в сравниваемых вариантах. Совокупность этих затрат называется технологической себестоимостью. Технологическая себестоимость складывается из условно-переменных (зависящих от объема производства) и условно-постоянных (независящих в основном от изменения объема производства) затрат. Расчет ведется только на заменяемые операции сравниваемых технологических вариантов.
При расчете технологической себестоимости производится определение расходов:
- условно-переменных,
- условно-постоянных,
а также технологической себестоимости и критической программы выпуска деталей.
|
|
К условно-переменным относятся затраты на:
- прямую и дополнительную заработную плату основным рабочим, страховые взносы и поясной коэффициент, ЗП;
- основные материалы (учитываются, если они различаются по стоимости на единицу продукции в сравниваемых вариантах), М;
- электроэнергию, Эл;
- сжатый воздух, СВ;
- амортизацию оборудования, А.
Величина условно-переменных расходов V, р/шт, складывается из следующих затрат
V = ЗП + М + Эл + СВ + А (1.1)
Затраты на оплату труда рабочего определяются по формуле
ЗП = Сч * Тшт * (1+Кдоп) * (1+Котч) * (1+Кп), (1.2)
где Сч - часовая тарифная ставка рабочего, р.;
Тшт - норма штучного времени на операции, выполняемые рабочим ч.;
Кдоп - коэффициент, учитывающий дополнительную заработную плату;
Котч - коэффициент, учитывающий страховые взносы;
Кп - поясной коэффициент.
Кдоп = 0,2-0,4; Котч = 0,386; Кп = 0,2.
Затраты на оплату труда рабочего в базовом варианте
ЗП1 =
Затраты на оплату труда рабочего в проектируемом варианте
ЗП2 =
Стоимость материала М, р/шт, учитывается в том случае, если в одном из вариантов технологии изменяется либо марка материала, либо норма расхода.
М = Н * Ц * Кт - Нотх * Цотх, (1.3)
|
|
где Н - норма расхода материала на деталь, кг.;
Ц - цена одного килограмма материала, р.;
Кт - коэффициент, учитывающий транспортно-заготовительные
расходы по отношению к стоимости материала, равный 1.05-1,1;
Нотх - норма отходов материала, кг.;
Цотх - цена 1килограмма отходов, р.
Стоимость материала в базовом варианте, М1 =
Стоимость материала в проектируемом варианте, М2 =
Затраты на электроэнергию Эл, р/шт, определяются по формуле
Эл = Р *Sэ * Км * Квр * Тшт, (1.4)
где Р - суммарная установленная мощность электродвигателей оборудования, КВт;
Sэ - стоимость 1КВт-ч электроэнергии, р.;
Км - коэффициент использования оборудования по мощности;
Квр - коэффициент использования электродвигателей по времени.
Км * Квр = 0,5 – 0,9;
Затраты на электроэнергию в базовом варианте Эл1 =
Затраты на электроэнергию в проектируемом варианте Эл2 =
Затраты на сжатый воздух, приходящихся на одну операцию, р, определяются по формуле
СВ = Рв* Sсв * Тшт, (1.5)
где Рв – среднечасовой расход воздуха, м3;
Sсв – стоимость 1 м3, р.;
Тшт – штучное время по всем операциям сборки,ч.
Затраты на сжатый воздух в базовом варианте СВ1=
Затраты на сжатый воздух в проектируемом варианте СВ2=
|
|
Для того, чтобы правильно рассчитать расходы на амортизацию оборудования, нужно знать, сколько единиц оборудования требуется для выпуска заданной годовой программы изделий. Расчетное количество станков Срасч, шт., определяется по формуле
Nпр * Тшт-к. (1.6)
Cрасч = ---------------- -,
Fэф.ст * Квн
где Fэф. ст - эффективный годовой фонд времени работы станка, ч;
Тшт-к. – штучно – калькуляционное время, ч.
Nпр – годовая программа выпуска, шт.;
Квн – коэффициент выполнения норм.
Тшт-к. – данные использовать из комплексной практической работы по профилирующей дисциплине;
Nпр – данные использовать из задания на комплексную практическую работу 13;
Квн – 1 - 1,2.
В
Fэф. ст. = Fном * q * Kсм * (1 - -----), (1.7)
где Fном – номинальный фонд рабочих дней в году;
q – средняя продолжительность работы станка за смену ч.;
Ксм – коэффициент сменности работы станка;
В – коэффициент потерь времени на ремонт оборудования, %.
Fном = 250 – 260; q = 8; Ксм = 1 – 2; В = 2 – 12.
Расчетное количество станков в базовом варианте Срасч1 =
Расчетное количество станков в проектируемом варианте Срасч2 =
Принятое количество станков, Спр., определяется путем округления величины Срасч до целого числа
|
|
Принятое количество станков в базовом варианте Спр1=
Принятое количество станков в проектируемом варианте Спр2=
Расходы по амортизации оборудования А, р/шт определяются по формуле
Na *ОФоб (1.8)
А = -----------,
100* Nпр
где Na – норма амортизационных отчислений, 10%;
ОФоб–балансовая стоимость оборудования (полная первона-чальная с учетом переоценки), р.;
Расходы по амортизации оборудования в базовом варианте А1 =
Расходы по амортизации оборудования в проектируемом варианте А2=
Величина условно – переменных расходов в базовом варианте V1=
Величина условно – переменных расходов в проектируемом варианте V2=
Условно - постоянные расходы не изменяются при изменении объема производства. К ним относятся:
· оплата работ по наладке оборудования;
· затраты на эксплуатацию специальных приспособлений и технологического оснащения;
· затраты на текущий ремонт оборудования.
Величина условно – постоянных расходов С, р/год, определяется по формуле
С = ЗПнал + Зэкспл.присп. + Зрем.об. (1.9)
где ЗПнал - затраты на оплату труда рабочего, занятого наладкой
оборудования, р/год;
Зэкспл. присп. - затраты на эксплуатацию и ремонт специальных приспособлений, р/год;
Зрем.об. – затраты на текущий ремонт оборудования, р/год.
ЗПнал = Сч1 * Тпз * (1+Кдоп) * (1+Котч) * (1+Кп) * Кз, (1.10)
где Сч1 – часовая тарифная ставка рабочего, занятого наладкой, р.;
Тпз – подготовительно-заключительное время, час;
Кз – коэффициент занятости рабочих по наладке.
Сч1 = 20 – 35; Кз = 0,2 – 0,5
Затраты на оплату труда рабочего, занятого наладкой оборудования, в базовом варианте ЗПнал1 =
Затраты на оплату труда рабочего, занятого наладкой оборудования, в проектируемом варианте ЗПнал2 =
Зэкспл.присп. = 0.6 * ОФосн (1.11)
где ОФ осн – полная первоначальная (балансовая) стоимость оснастки, р.
принять равной 8 – 12% от стоимости оборудования
Затраты на эксплуатацию и ремонт специальных приспособлений в базовом варианте
Зэкспл.присп.1 =
Затраты на эксплуатацию и ремонт специальных приспособлений в проектируемом варианте
Зэкспл.присп.2 =
Зрем.об.= 0,1*ОФоб (1.12)
Затраты на текущий ремонт оборудования в базовом варианте Зрем1=
Затраты на текущий ремонт оборудования в проектируемом варианте Зрем2=
Величина условно – постоянных расходов в базовом варианте С1=
Величина условно – постоянных расходов в проектируемом варианте С2=
Таким образом, технологическая себестоимость единицы продукции Sтехн, р складывается из условно-переменных расходов на одну деталь и условно-постоянных расходов, приходящихся на одну деталь программы выпуска, и определяется по формуле
С
Sтехн1 = V + ------, (1.13)
Nпр
Технологическая себестоимость единицы продукции в базовом варианте
Sтехн1 =
Технологическая себестоимость единицы продукции в проектируемом варианте Sтехн2 =
Технологическая себестоимость годового задания, Sвып в обоих вариантах составляет:
Sвып1 = V1 * Nпр + C1;
Sвып2 = V2 * Nпр + C2 (1.14)
Математическая модель определения технологической себестоимости сравниваемых вариантов представлена на рисунке 2.1.
SВЫП, р. V1*Nпр+C1
![]() |
С2
V2*Nпр+C2
С1
NКР
![]() |
0 NШТ
Рисунок 2.1 Определение критического объема производства
Точка пересечения данных прямых соответствует критическому коли-честву деталей Nкр. шт, при котором себестоимости в обоих вариантах равны друг другу.
С2 - С1
Nкр = ------- (1.15)
V1 - V2
Эта величина показывает, при каких размерах задания сравниваемые варианты технологии равноценны. Если размеры установленного задания по выпуску данных деталей больше величины Nкр, то технолог может выбрать более дорогой по затратам на наладку и технологическую оснастку вариант, поскольку дополнительные расходы окупятся экономией на условно -переменных расходах. Если же заданный объем производства будет меньше величины Nкр, то предпочтение должно быть отдано варианту, в котором условно-постоянные расходы будут меньше.
Дата добавления: 2015-12-16; просмотров: 17; Мы поможем в написании вашей работы! |
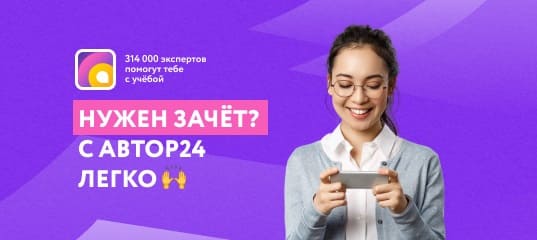
Мы поможем в написании ваших работ!