Песок, гравий, песчаники и строит. камень. Применение в промыш.
Песок – рыхлая осадочная порода, представленная мелкими обломками и зернами различных минералов и горных пород разной формы, размеров и степени окатанности. По гранулометрическому составу среди них различают мелкозернистые (величина зерен 0,25–0,1 мм), среднезернистые (0,5–0,25 мм), крупнозернистые (1–0,5 мм) и грубозернистые (2–1 мм) разности. Минеральный состав песков весьма разнообразный: кварцевые, кварц-полевошпатовые, кварц-глауконитовые, смешанные и др.
Гравий – рыхлая осадочная порода, состоящая из более или менее окатанных обломков различных горных пород (гранита, кремнистых пород, кварцита и др.) и минералов (большей частью кварца), причем размер зерен в основном варьирует от 1 до 10 мм (по данным некоторых авторов, – от 2 до 10 мм). Гравий в природе почти всегда встречается в смеси с песком, образуя песчано-гравийные и гравийно-песчаные породы, содержащие песок в количестве от 10 до 90 %.
Песчаники – осадочные сцементированные обломочные породы с зернами от 0,1 до 1 мм (по данным некоторых авторов, от 0,1 до 2 мм). По составу обломочных зерен выделяют песчаники трех основных типов: 1) мономинеральные (кварцевые), 2) олигомиктовые, 3) полимиктовые (граувакки, туффиты и др.). Цемент песчаников разнообразен (известковый, глинистый, кремнистый, железистый и др.).
Кварциты – это метаморфизованные и перекристаллизованные песчаники существенно кварцевого состава, в которых кварцевые зерна плотно прилегают друг к другу, образуя сплошную тонкозернистую массу, обладающую высокой механической прочностью.
|
|
Свойства. В основе применения в промышленности перечисленных выше горных пород лежат разнообразные физические и химические их свойства: рыхлость одних и механическая прочность других, абразивная способность зерен кварца, высокое содержание кремнезема и обусловленные этим огнеупорность и кислотоупорность. Залежи песка или гравия, разрабатываемые для заполнителей бетонов, должны быть чистыми, т. е. не содержать глинистого вещества, слюды и органических примесей. Для заполнителей бетонов очень важно такое свойство, как устойчивость к износу, особенно в тех случаях, когда бетон предназначен для дорожного строительства. Прочность заполнителя также имеет большое значение. Хороший заполнитель должен обладать большой устойчивостью к замораживанию и оттаиванию, увлажнению и усыханию. Трещиноватые и пористые обломки вредны, поскольку они могут расщепиться, расслоиться или растрескаться в бетоне. Имеет значение также форма частиц. Наиболее предпочтительны изометричные, округлые частицы, так как угловатые обломки делают бетон «шероховатым».
|
|
Свойства песка и гравия определяются тремя способами: визуальным осмотром, лабораторными испытаниями и петрографическим изучением.
Применение в промышленности. Песок и гравий применяются в качестве заполнителей, инертных и отощающих материалов в производстве строительного и силикатного кирпича, бетона, вяжущих растворов, стеновых блоков и т. п. Песок, гравий и щебень используются также для балластировки железнодорожных путей, устройства основания и подстилающего слоя автомобильных дорог. Фильтровальные пески применяются при создании мощных фильтровальных систем для очистки питьевой и технической воды, формовочные пески – для получения литейных форм и стержней, кварцевые пески – в стекольном производстве. Из кварцитов, обладающих большой механической прочностью, мелкозернистостью, малой пористостью и высокой кислотоупорностью получают материалы, используемые для сооружения кислотных башен, хранилищ для кислот и т. п.
Общетехнические условия. Качество и пригодность песков, гравия и кварцитов для различных видов производства определяются соответствующими ГОСТами и техническими условиями, в которых предусматриваются необходимые требования к гранулометрическому и минеральному составу обломков, степени их выветрелости, механической прочности, содержанию вредных примесей и др. Так, применяемые при плавке медных и никелевых концентратов флюсы из песчаников и кварцитов должны содержать не менее 80 % SiO2 и минимальное количество вредных примесей – оксидов железа, алюминия, магния и кальция.
|
|
Требования, предъявляемые к кварцевым пескам для стекольного производства, следующие: 1) однородность гранулометрического состава – не менее 90 % зерен с размерами от 0,1 до 0,3–0,5 мм; 2) содержание кварца не менее 96 %, а для оптического, зеркального и других стекол высших сортов – 99,3–99,8 %; 3) минимальное содержание оксидов железа и хрома, окрашивающих стекло в желтый и зеленый цвет.
Песчаники и кварциты, применяемые для производства динаса (огнеупор, содержащий не менее 90–93 % кремнезема и изготовленный на известковой, известково-железистой или иной связке), должны содержать не менее 95–97 % SiO2. Вредные примеси, которые лимитируются, – Fe, Al и Ca.
Технология производства стекла. Современная технология получения стекла включает ряд последовательных операций: подготовку необходимых сырьевых компонентов, их смешивание в определенных соотношениях в однородную шихту, варку шихты в стекловаренных печах для получения однородной жидкой стекломассы, доведения этой стекломассы до оптимальной для формирования изделий температуры и вязкости, формирование изделий, постепенное охлаждение полученных изделий, обработку (термическую, химическую, механическую) отформованных изделий.
|
|
Сырьевые материалы, используемые в производстве стекла, подразделяют на главные и вспомогательные. Главные материалы – кремнезем (обычно кварцевый песок или молотый кварц), борный ангидрид (бура или борная кислота), фосфорный ангидрид, оксид алюминия (глина, каолин, полевой шпат, глинозем), оксиды щелочных металлов (сода или безводный сульфат натрия, поташ, литийсодержащие минералы) и др. К вспомогательным сырьевым материалам относят всевозможные осветлители (сульфаты натрия и алюминия, хлористый натрий и другие, способствующие удалению пузырей), обесцвечиватели (для окисления соединений железа), красители (оксиды различных металлов), глушители (различные фтористые соединения) и восстановители (углеродистые вещества).
Стекловарение ведется при температурах 1400–1600 оС. Выделяются три стадии: провар, или собственно варка, когда происходит химическое взаимодействие между компонентами шихты и образование вязкой массы; очистка, или осветление, – удаление пузырьков и растворение остаточных кварцевых зерен; студка – охлаждение стекломассы до отпимальной температуры для получения из нее изделий.
Дата добавления: 2015-12-16; просмотров: 21; Мы поможем в написании вашей работы! |
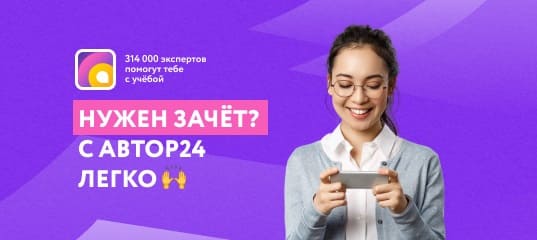
Мы поможем в написании ваших работ!