Характеристика методов получения заготовок
2.1 Литьё
Характеристики методов литья представлены в таблицах 1-5.
Метод литья в песчаные формы применяется для всех литейных сплавов, типов производства, заготовок любых масс, формы и габаритов, отличается универсальностью и относительно низкой стоимостью. Точность и шероховатость поверхностей отливки зависит от способа формовки, материалов моделей и составов формовочных смесей.
Недостатками метода литья в песчаные формы являются большой расход формовочных и вспомогательных материалов, большие припуски на механическую обработку.
В машиностроительном производстве литьём в песчаные формы получают 80% отливок.
Литьём в оболочковые формы изготовляются заготовки сложной формы, например, ребристые. Поверхности отливки имеют относительно низкую шероховатость. Ко времени затвердевания металла форма легко разрушается, не препятствуя усадке металла, остаточные напряжения в отливке незначительные. Расход формовочных материалов на порядок ниже, чем при литье в песчаные формы.
Недостатками литья в оболочковые формы являются неудобство работы с горячими металлическими моделями и относительно высокая стоимость.
Литьём по выплавляемым моделям изготовляются точные и сложные отливки из труднодеформируемых и труднообрабатываемых сплавов с высокой температурой плавления.
Технологический процесс литья по выплавляемым моделям самый длительный и трудоёмкий среди всех методов литья. Экономичность метода достигается выбором деталей, точность и шероховатость поверхностей которых обеспечиваются литьём, а механической обработке подвергаются только сопрягаемые поверхности.
|
|
Кокильным литьём обеспечиваются мелкозернистая структура и лучшие механические свойства металла отливки, чем литьём в песчаные формы. Выход годных заготовок увеличивается до 75…95%. Исключаются трудоёмкие операции формовки, сборки и выбивки,.
Для кокильного литья характерны дефекты отливок: деформации, трещины, газовые пористости.
Литьём под давлением обеспечивается получение сложных тонкостенных (менее 1 мм) отливок из цветных сплавов, близких по форме к деталям, с высокой точностью и малой шероховатостью поверхностей. Механической обработке подвергаются только сопрягаемые поверхности. Прочность отливки выше, чем при литье в песчаные формы.
Недостатком метода является высокая стоимость пресс-форм, изготавливаемых по 6 – 8 квалитетам.
Штамповкой жидкого металла (разновидность литья под давлением) изготовляются тонкостенные заготовки корпусов, фланцев, тройников из чёрных и цветных сплавов. Отсутствуют газовые и усадочные раковины. Коэффициент использования металла достигает 0,9…0,93.
|
|
Центробежным литьём изготовляются заготовки типа тел вращения из чугуна, стали и цветных сплавов, например, втулки, диски. Это пока единственный метод получения качественных заготовок из титановых сплавов. Отливки имеют относительно высокую плотность.
Недостатком центробежного литья является сложность получения качественных отливок из сплавов подверженных ликвации.
2.2 Обработка давлением
Характеристики методов обработки давлением представлены в таблицах 6 и 7.
Ковка является универсальным методом производства поковок массой от 10 г до 350 т на молоте или прессе. Припуски составляют от 3 до 44 мм при ковке на молоте и от 7 до 110 мм при ковке на прессе. В процессе ковки улучшаются механические свойства материалов, особенно ударная вязкость.
Применение колец и подкладных штампов позволяет сократить расход металла на 15…20% по сравнению с ковкой на универсальном инструменте.
Горячей объёмной штамповкой в открытых и закрытых штампах, в штампах для выдавливания на молотах, прессах, специальных машинах получаются заготовки ответственных деталей массой от 0,5 до 30 кг и более.
Штамповкой в закрытых штампах обеспечивается высокое качество структуры заготовок. Отсутствует расслоение металла в местах образования заусенца, как это имеет место при штамповке в открытых штампах.
|
|
Недостатком штамповки в закрытых штампах является низкая стойкость штампов. Штампы чаще разрушаются, чем изнашиваются.
Методом штамповки выдавливанием обеспечиваются снижение расхода металла, плотная микроструктура, высокое качество поверхностного слоя, низкая шероховатость. Точность размеров соответствует 12-му квалитету.
Недостатками штамповки выдавливанием являются высокая энергоёмкость и низкая стойкость штампов.
Холодной объёмной штамповкой получаются заготовки с высокими механическими свойствами благодаря холодному течению металла в штампе. Производительность холодной высадки на прессах автоматах составляет сотни заготовок в час.
Холодной объёмной штамповке принадлежит будущее, но этот метод очень энергоёмкий.
Прокаткой получаются заготовки, которые применяются для изготовления деталей обработкой резанием. Штучные заготовки из проката используются для ковки и штамповки.
2.3 Комбинированные методы и метод порошковой металургии
Сложные заготовки разделяются на отдельные простые части, которые отливаются, штампуются, вырезаются, обрабатываются по сопрягаемым поверхностям и соединяются сваркой.
|
|
Применение таких заготовок позволяет снижать трудоёмкость механической обработки и уменьшать расход металла.
Методом порошковой металлурги изготовляются заготовки из тугоплавких материалов, псевдосплавов (медь – вольфрам, железо – графит), пористых материалов для подшипников скольжения.
Заготовки, получаемые методом порошковой металургии, обычно подвергаются только отделочной механической обработке.
Экономичность метода проявляется при больших объёмах производства из-за высокой стоимости технологической оснастки и материалов.
Таблица 1 – Характеристики методов литья [3], с. 308
Метод получения заготовки | Минимальная толщина стенки заготовки, мм | Квали-тет | Шероховатость, Rz, мкм | Материал | Тип произ-водства | ||
из чугуна | из стали | из цветных сплавов | |||||
Литьё в песчаную форму: при ручной формовке по деревянным моделям в опоках при машинной формовке по ме-таллическим мо-делям со сборкой стержней в кон-дукторах Литьё по выплав-ляемым моделям Кокильное литьё Литьё под давле-нием | 3 – 5 3 – 5 0,5 – | 5 – 8 5 – 8 0,5 – | 3 – 8 3 – 8 0,5 | 15 – 17 12 – 15 12 – 15 12 – 14 | 20 – 80 5 – 20 2,5 – 20 2,5 – 40 0,63 – 30 | Чугун, сталь, сплавы цвет-ных металлов Высоколеги-рованные тру-днообрабаты-ваемые стали Сплавы цвет-ных металлов, сталь, чугун Сплавы цвет-ных металлов | Единичное и мелкосе-рийное Крупносе-рийное и массовое Серийное и массовое Серийное и массовое Крупносе-рийное и массовое |
Таблица 2 – Квалитеты размеров и шероховатость поверхности отливок [5], с. 126
Метод литья | Квалитеты | Параметры шероховатости, мкм | |
Rz | Ra | ||
Литьё в песчаную форму Кокильное литьё Литьё по выплавляемым моделям Литьё под давлением | 15 – 17 12 – 16 12 – 14 10 - 15 | 320 – 80 320 – 20 | 2,5 – 1,25 2,5 – 0,32 |
Таблица 3 – Рекомендуемая толщина стенок отливок [5], с. 127
Метод литья | Толщина стенки, мм | |
минимальная | оптимальная | |
Литьё в песчаную форму Кокильное литьё Литьё по выплавляемым моделям Литьё под давлением | 0,5 0,5 | 5 – 12 5 – 8 3 – 5 2 - 4 |
Таблица 4 – Сравнительные характеристики основных методов литья [5], с. 126
Характеристики | Под давлением | По выплавляемым моделям | Кокильное литьё | В песчаную форму |
Производительность Выход годных отливок Стоимость оснастки Продолжительность освоения Сложность конфигурации отливки Возможность использования различных сплавов | I I IV IV III IV - III | IV II II III I II | II IV III II IV IV - III | III III I I II I |
Обозначения: I – самые высокие; IV – самые низкие.
Таблица 5 – Применение методов литья в приборостроении [5], с. 125
Метод литья | Изготовляемые изделия | Тип производства |
Литьё в песчаную форму Кокильное литьё Литьё по выплавляемым моделям Литьё под давлением | Крупногабаритные корпусные детали из бронзы, алюминиевых и магниевых сплавов, реже из чёрных сплавов Детали несложной конфигурации из алюминиевых и магниевых сплавов, реже из чугуна и бронзы Небольшие детали сложной конфигурации из конструкционных и жаропрочных сталей, медных, реже из алюминиевых сплавов Тонкостенные корпусные детали сложной конфигурации из латуней, цинковых, алюминиевых и магниевых сплавов | Среднесерийное, мелкосерийное, единичное Массовое, крупносерийное, среднесерийное Массовое, серийное Массовое, крупносерийное, среднесерийное |
Таблица 6 – Характеристика заготовок, получаемых обработкой давлением [3], с. 316
Метод получения заготовки | Толщина стенки, мм | Квалитет | Шерохо-ватость, Rz, мкм | Материал | Тип производства |
Ковка: на прессах и молотах на молотах в подкладных штампах на прессах на машинах с радиаль-ным обжатием, горячая то же, холодная Штамповка: на горизонтально-ковоч-ных машинах на горячештамповочных машинах Холодная высадка на автоматах | 20 – 25 – Диаметр заготовки 30 мм Диаметр заготовки 5 мм 2,5 1,5 | 15 – 16 8 – 9 8 – 9 15 – 16 14 - 15 | До 80 До 40 До 40 20 – 40 1,6 – 6,3 20 – 80 До 40 1,25 - 5 | Углеродистые и легированные стали То же ² Углеродистые и легированные стали, сплавы из цветных метал-лов То же ² ² Углеродистые и легированные стали | Единичное и мелкосерийное Мелкосерий-ное Мелкосерий-ное Серийное, крупносерий-ное, массовое То же ² ² ² |
Таблица 7 – Квалитеты размеров и шероховатость поверхностей заготовок, получаемых объёмной и листовой штамповкой [7], с. 516
Метод обработки | Квалитет (экономический) | Значение параметра Rа, мкм | |
Горячая ковка в штампах | 14 - 17 | 12, 5 - 100 | |
Горячая вырубка и пробивка | 14 - 16 | 12,5 - 100 | |
Горячая объёмная штамповка без калибровки | 9 - 11 | 12,5 - 50 | |
Холодная штамповка в вытяжных штампах | Вытяжка полых заготовок про-стой формы (корпус, стакан) | По диаметру 10 – 11 По высоте 8 - 12 | 0,8 – 3,2 |
То же, но глубокая вытяжка | |||
Холодная штамповка в вырубных, пробивных и зачистных штампах | Контурные размеры при вырубке плоских деталей | 12 - 13 | Зона среза 3,2 – 6,3 Зона скалывания 25 - 100 |
То же при пробивке | |||
То же при зачистке | 8 - 9 | 0,8 – 3,2 | |
То же при зачистке и калибровке | 6 - 7 | 0,8 – 3,2 |
Профессор В.П. Фандеев
Дата добавления: 2015-12-20; просмотров: 36; Мы поможем в написании вашей работы! |
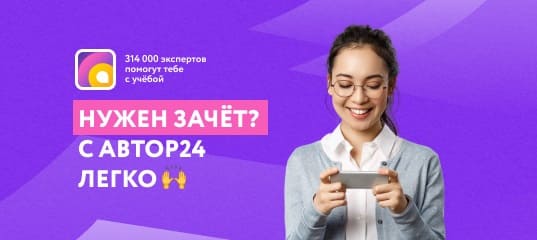
Мы поможем в написании ваших работ!