Одна тонна бумаги вырабатывается за.
3.2 Исходные данные для расчета материального баланса
Исходные данные для расчета материального баланса представлены в таблице 3.
Таблица 3 - Исходные данные для расчета материального баланса сушильной части БДМ
Исходные данные | Значение |
Производительность бумажной фабрики, т/год | |
Число рабочих дней, сут | |
Число часов работы БДМ в сутки, ч | |
Обрезная ширина бумаги на накате, м | |
Масса метра квадратного, г | |
Сухость бумаги после прессов, % | |
Сухость бумаги после сушильной части, % | |
Сухость бумаги после наката и продольно-резательного станка (ПРС), % | |
Влажность сухого брака, % | |
Влажность мокрого брака, % | |
Коэффициент эффективности использования рабочего хода машин, К2 | 0,96 |
Коэффициент выхода нетто товарной продукции из брутто всей машинной продукции (учет оборотного брака), К3 | 0,97 |
Расход раствора глинозема, г/л Расход флокулянта «Праестол», г/л Расход меловой суспензии, г/л | 0,4 |
Концентрация волокна в воде от промывки сетки, г/л | 0,30 |
Композиция по волокну, %: - целлюлоза сульфатная беленая лиственная - целлюлоза сульфатная беленая хвойная | |
Зольность, % | 8,7 |
Расчет баланса воды, волокна и наполнителя на 1 т нетто тетрадной бумаги ведем следующим образом.
Продольно-резательный станок:
Количество образующегося брака на машине:
- абсолютно сухой бумаги на накате 7561,4 · 0,94 = 7107,72 кг/час;
|
|
- воды в нем 7561,4 – 7107,72 = 453,68 кг/час;
- абсолютно сухой бумаги в сухом браке 7107,72 · 0,01 = 71,07 кг/час
- воды в нем кг/час.
- абсолютно сухой бумаги в мокром браке 7107,72 · 0,01 = 71,07 кг
Следовательно, на ПРС поступает: а.с.в.:
7561,4 + 71,07 = 7632,47 кг/час;
воды:
453,68 + 4,54 = 458,22 кг/час.
Принимаем, что 75 % брака образуется на гауч-вале, т.е. 25 % на прессах. Тогда на гауч-вале мокрого брака образуется
71,07 · 0,75 = 53,30 кг
воды в нем 53,30 · 75 / 25 = 159,90 кг.
На прессовой части образуется брака:
71,07 – 53,30 = 17,77 кг
воды в нем 17,77 · 58 / 42 = 24,54 кг
Расход волокнистого сырья, с учетом промоев, влажности и зольности бумаги:
Мч = Рч · К (4);
где Рч – часовой расход волокнистого сырья, кг;
К – коэффициент, учитывающий промои, зольность и влажность картона;
К = (1 + П / 100) · (1 - З / 100) · (1 - W / 100) (5);
где П – промои, 0,1 %;
W – влажность бумаги %,
З – зольность бумаги %,
К = (1 + 0,1/ 100) · (1 – 8,7 / 100) · (1 – 12 / 100) = 0,8042
Часовой расход абсолютно сухой целлюлозы:
Мч = 7561,4 · 0,8042 = 6080,88 кг,
Часовой расход воздушно-сухой целлюлозы: 6080,88 · 0,88 = 5351,17 кг.
Удельный расход волокнистого сырья Муд составляет:
Муд. = К / 0,88 · 1000 = 0,8042 / 0,88 ·1000 = 913,9 кг/т.
Часовой расход наполнителя при зольности бумаги 8,7 % и удерживаемость наполнителя 80 % составит:
|
|
87 · 100 · 7,5614 / 80 = 822,30 кг а.с.в.
Расход наполнителя при влажности 5 % составит:
822,30 / 0,95 = 865,58 кг.
Расход сернокислого глинозема 20 · 7,5614 = 151,23 кг
Расход флокулянта «Праестол» 0,4 · 7,5614 = 3,02 кг
Расход меловой суспензии 110 · 7,5614 = 831,75 кг
3.3 Расчет баланса воды и волокна
3.3.1 Накат
С наката сходит с основным потоком 7107,72 кг волокна, с ним воды 453,68 кг. Брака 71,07 кг и с ним воды 24,54 кг. Следовательно, на накат поступит:
абсолютно сухой бумаги 7107,72 + 71,07 = 7178,79 кг,
воды 453,68 + 24,54 = 478,22 кг.
7178,79
478,22
|
71,07
24,54
7107,72
453,68
3.3.2 Сушильная часть
На сушильную часть поступает бумага сухостью 42 %, следовательно, воды поступит на сушильную часть
7178,79 · 58 / 42 = 9913,57 кг
Испарится воды
9913,57 – 478,22= 9435,35 кг
Потерь волокна в сушильной части нет.
7178,79
9913,57
Сушильная 0
часть 9435,35
7178,79
478,22
Таким образом, суммируя все произведенные расчеты, можно рассчитать итоговый баланс воды и волокна. Результаты расчета материального баланса сведу в таблицу 4.
Таблица 4 – Сводная таблица материального баланса
Статья | Приход, кг/ч | Статья | Расход, кг/ч | ||
Волокно G | Вода W | Волокно G | Вода W | ||
Сушильная часть | |||||
Полотно с последнего пресса | 7178,79 | 9913,57 | Полотно на накат | 7178,79 | 478,22 |
Испаренная вода | 9435,35 | ||||
Итого | 7178,79 | 9913,57 | 7178,79 | 9913,57 | |
Накат | |||||
Полотно с сушильной части | 7178,79 | 478,22 | Полотно на ПРС | 7107,72 | 2251,29 |
Брак в разбиватель | 71,07 | 24,54 | |||
Итого | 7178,79 | 478,22 | 7178,79 | 478,22 | |
Продольно-резательный станок | |||||
Полотно с наката | 7107,72 | 453,68 | Бумага на склад | 7561,4 | 458,22 |
Брак в разбиватель | 458,22 | 4,54 | |||
Итого | 7107,72 | 453,68 | 7107,72 | 453,68 |
|
|
3.4 Тепловой баланс сушильной части БДМ
Исходные для расчета теплового баланса и расхода пара на сушку представлены в таблице 5
Таблица 5 – Исходные данные
Наименование показателя | Ед. изм. | Обозначение | Значение |
Производительность машины | т/сут | Р сут | 173,913 |
Масса 1 м2 | г | q | |
Обрезная ширина полотна на накате | м | B | 4,2 |
Сухость полотна на накате | % | x к | 94,0 |
Начальная температура полотна | оС | t н | 71,0 |
Конечная температура полотна | оС | t к | 114,0 |
Диаметр сушильных цилиндров | м | d | 1,5 |
Продолжение таблицы 5
Начальная сухость | % | x н | 42,0 | |
Коэффициент обхвата цилиндров: полотном сеткой | a b c | 0,67 0,6 | ||
Толщина: торцевой стенки цилиндра бумажного полотна сетки | м | d d б d c | 0,025 0,0050 0,003 | |
Коэффициент теплопроводности материала стенки цилиндра | Вт/(м2· oC) | l | 50,0 | |
Температура наружного воздуха: зимой летом | оС | t нз t нл | -15,0 20,0 | |
Влажность наружного воздуха зимой летом | % | j нз j нл | 0,8 0,7 | |
Температура уходящего воздуха | оС | t у | 45,0 |
|
|
Длину сушильного цилиндра lц , м, найдем по формуле (6) [10].
= ((l + 2 b) · 100)/(100 – y) · 0,13(6)
где l – необрезная ширина бумажного полотна, м;
b – ширина кромок, м;
y – величина поперечной усадки полотна, %, y = 2,5 % [5]
= ((4,2 + 2·0,03)·100)/(100 – 2,5) = 4,37 м.
Количество сушильных цилиндров n на БДМ определим по формуле
n = B/(qπdlα), (7)
где B - количество испаренной воды в час, кг;
q - удельный съем воды с 1 м2 полезной сушильной поверхности, кг/(м2·ч),
q = 20 кг/(м2·ч) [5]
d - диаметр сушильного цилиндра, м;
l - длина сушильного цилиндра, м;
α - коэффициент обхвата сушильных цилиндров бумагой.
n = 9435,35/(12·3,14·1,5·4,37·0,67) = 57,02 шт.
Принимаем n = 58 шт.
Рассчитаем часовой расход теплоты на сушку бумаги. Общий расход теплоты на сушку бумаги складывается из полезного расхода теплоты и тепловых потерь в окружающее пространство и находится по формуле
Qобщ = Qпол + Qпот (8)
Полезный расход теплоты на сушку Qпол, кДж/ч, бумаги можно определить по формуле
Qпол = Q1+Q2+Q3= в·сб(tк–tн)+Bнcв(tк–tн)+B(i–cвtс), (9)
где Q1 - расход теплоты для нагрева абсолютно сухого волокна в воздушносухой бумаге, кДж/ч;
Q2 - расход теплоты для нагрева воды в мокром полотне, поступающем на сушку, кДж/ч;
Q3 - расход теплоты для испарения воды, кДж/ч;
в - масса абсолютно-сухой бумаги, кг/ч;
сб - теплоемкость абсолютно сухой бумаги, кДж/(кг·ºC),
сб = 1,3 кДж/(кг·ºC) [6]
tн, tк - температура бумаги перед сушильной частью и после нее, ºC;
Bн - масса воды в мокром полотне, поступающем на сушку, кг/ч;
cв - теплоемкость воды, кДж/(кг·ºC), св = 4,19 кДж/(кг·ºC)
tс - средняя температура сушки (практически можно принять tк = tс), ºC;
B - количество воды, испаряющейся из бумаги, кг/ч;
i - энтальпия пара, удаляемого из бумаги, при средней температуре сушки, кДж/кг.
Тогда полезный часовой расход теплоты на сушку бумаги составит
Qпол = 7178,79·1,3(114 – 42) + 9913,57·4,19(114 – 42) + 9435,35·(2665,6 –
– 4,19·94) = 52013847,55 кДж/ч.
Тепловые потери можно определить по формуле
Qпот = q1+ q2 + q3 + q4 + q5 + q6 + q7, (10)
где q1, q2 - потери теплоты свободными участками полотна и сушильной сетки, кДж/ч;
q3 - потери теплоты днищами бумагосушильных цилиндров, кДж/ч;
q4 - потери теплоты открытой боковой поверхностью бумагосушильных цилиндров кДж/ч;
q5 - потери теплоты боковой поверхностью бумагосушильных цилиндров, покрытых бумагой и сеткой, кДж/ч;
q6 - потери теплоты боковой поверхностью бумагосушильных цилиндров, покрытых бумагой, но не покрытых сеткой, кДж/ч;
q7 - потери теплоты боковой поверхностью бумагосушильных цилиндров, покрытых сеткой, но не покрытых бумагой, кДж/ч.
1. Потери теплоты свободными участками картонного полотна определим по формуле
q1 = 3,6Fбα'(tб – tв), (11)
где Fб - площадь боковой поверхности свободных участков бумажного полотна с двух сторон, м2;
α' - коэффициент теплоотдачи бумаги воздуху Вт/(м2·oC);
tб - средняя температура полотна бумаги на свободных участках, равная средней температуре сушки, oC;
tв - температура окружающего воздуха, oC.
Fб = 2lbn, (12)
где l - длина свободного участка бумаги между цилиндрами, (1,1…1,2 м для сушильного цилиндра диаметром 1,5 м), м;
b - ширина бумажного полотна (условно принимается равной необрезной ширине бумаги на накате), м;
n - количество свободных участков (принимается равным количеству сушильных цилиндров).
Fб = 2·1,5·4,26·58 = 741,24 м2.
α' = 5,58 + 3,95· V,· (13)
где V – рабочая скорость БДМ, м/мин
α' = 5,58 + 3,95· = 38,21 Вт/(м2·oC).
q 1 = 3,6·1712,52·38,21· (114 – 60) = 12720639,66 кДж/ч.
2. Потери теплоты свободными участками сушильных сукон
q2 = 3,6Fбα1'(tс – tв), (14)
где α1' - коэффициент теплоотдачи сукнами воздуху, Вт/(м2·oC)
α' = 6,16 + 4,187· V, (15)
где V – рабочая скорость БДМ, м/мин
α' = 6,16 + 4,187· = 40,75 Вт/(м2·oC).
q2 =3,6·1712,52·40,75 ·(114 – 60) = 13566240,94 кДж/ч.
3. Потери теплоты днищами бумагосушильных цилиндров
Условно принимаем, что сушильная группа разбита по подаче пара и отводу конденсата на три по n1, n2, n3 цилиндров в группе:
n1 = 12, n2 = 26, n3 = 20
t1 = 87 oC, t2 = 140 oC, t3 = 114 oC
Отсюда
q3 = 3,6·2 K [(t1 – tв) n1 + (t2 – tв) n2 + (t3 – tв) n3 ], (16)
где dб - диаметр бумагосушильного цилиндра, м;
K - коэффициент теплопередачи пара воздуху через торцевую стенку цилиндра, Вт/(м2·oC);
t1, t2, t3 - температура пара в сушильных группах, oC.
Коэффициент теплопередачи вычисляется по формуле
K = 1/ (1 / α1 + δ / λ + 1 / α2), (17)
где α1 - коэффициент теплоотдачи от пара стенке сушильного цилиндра, Вт/(м2·oC); α1 = 5851 Вт/(м2·oC);
δ - толщина торцевой стенки цилиндра, м;
λ - коэффициент теплопроводности материала стенки цилиндра, Вт/(м2·oC);
α2 - коэффициент теплоотдачи от торцевой стенки цилиндра воздуху, Вт/(м2·oC).
α2 = 5,58 + 3,95· V, (18)
где V – рабочая скорость БДМ, м/мин
α2 =5,85 + 3,95· = 38,48 Вт/(м2·oC).
K =1/(1/5815 + 0,025/50 + 1/38,48) = 37,51 Вт/(м2·oC);
q3 = 3,6 · 2 · 37,51 · [(87 - 60) · 12 + (140 - 60) · 26 + (114 - 60) · 20] = 1661919,11 кДж/ч.
4. Потери теплоты открытой боковой поверхностью сукносушильных цилиндров
q4 = 3,6Kπdц[(1- α)lб + (1 - βс)(lс - lб) + (l ц- lс)]·[(t1 - tв)n1 + (t2 - tв)n2 + (t3 – tв)n3], (19)
где α - коэффициент охвата сушильного цилиндра картоном;
βс - коэффициент охвата сушильного цилиндра сеткой;
lб - ширина бумаги, м (условно принимают ширину бумаги на накате);
lц - длина (ширина) сушильного цилиндра, м;
lс - ширина сетки, м;
t1, t2, t3 - температура цилиндров в первой, второй, третьей группах, oC;
K - коэффициент теплопередачи пара воздуху через боковую поверхность бумагосушильного цилиндра, Вт/(м2·oC).
q4 = 3,6·37,51 ·3,14·1,5·[(1– 0,67)·4,2 + (1 – 0,6)(4,26 – 4,2) + (4,37 – 4,26)]·[(·[(87 - 60)·12+(140 - 60)·26+(114 - 60)20] = 3368156,06 кДж/ч
5. Потери теплоты боковой поверхностью сукносушильных цилиндров, покрытых бумагой и сеткой
q5 = 3,6Kπdцlбα[(t1 - tв)n1+ (t2 - tв)n2+ (t3 - tв)n3], (20)
где K = 1/(1/α1 + δ/λ + δб/λб + δс/λс + 1/α2),
где δб - толщина бумаги, м;
λб - коэффициент теплопроводности бумаги, Вт/(м·ºC);
δс - толщина сукна, м;
λс - коэффициент теплопроводности сукна, Вт/(м*ºC)
K = 1/(1/5815 + 0,025/50 + 0,0010/0,0465 + 0,005/0,04 + 1/ 38,48)= 5,77 Вт/(м2·ºC);
q5 = 3,6·5,77 ·3,14·1,5·4,2·0,67·[(87 - 60)·12+(140 - 60)·26+(114 - 60)·20] = 959182,97 кДж/ч.
6. Потери теплоты боковой поверхностью бумагосушильных цилиндров, покрытых бумагой, но не покрытых сеткой
q6 = 3,6Kπd ц l (α - β с)[(t 1- t в) n1 + (t2 - tв) n2 + (t3 - tв) n3 ], (21)
где K=1/ (1 / α1 + δ / λ + δб / λб + 1 / α2) (22)
K =1/(1/5815 + 0,025/50 + 0,0010/0,0465 + 1/ 38,48) = 20,74 Вт/(м2·ºC);
q6 = 3,6·20,74·3,14·1,5·4,2·(0,67 – 0,6)·[(87 - 60)·12+(140 - 60)·26+(114 - 60)·20]= 360211,55 кДж/ч.
7. Потери теплоты боковой поверхностью бумагосушильных цилиндров, покрытых сеткой, но не покрытых бумагой
q7 = 3,6Kπdц(lс - lб)βс[(t1 - tб)n1 + (t2 - tв)n2 + (t3 - tв)n3], (23)
где K = 1/(1/α1 + δ/λ + δс/λс + 1/α2)
K = 1/(1/5815 + 0,025/50 + 0,005/0,04 + 1/ 38,48) = 6,59 Вт/(м2·oC);
q7 = 3,6·6,59·3,14·1,5·(4,26 – 4,2)·0,67[(87 - 60)·12+(140 - 60)·26+(114 - 60)·20] = 32760,57 кДж/ч.
Отсюда общие потери теплоты
Qпот = 12720639,66 + 13566240,94 + 1661919,11 + 3368156,06 + 959182,97 +
+ 360211,55 + 32760,57 = 32669110,86 кДж/ч.
Общий расход теплоты
Qобщ = 52013847,55 + 32669110,86 = 84682958,41 кДж/ч.
Термический КПД сушильной части
η = Qпол/Qобщ; (24)
η = (52013847,55 /84682958,41)·100 = 93,42 %.
Удельный расход теплоты
Qуд = Qобщ/Рч, (25)
где Рч - часовая производительность БДМ, кг/ч.
Qуд = 84682958,41 /7561,4 = 11199,38 кДж/ч.
Удельный расход пара
Dуд = Qуд/ (Iп-Iк), (26)
где Iп - энтальпия пара, кДж/кг;
Iк - энтальпия конденсата, кДж/кг.
При давлении свежего пара 5,0 ·105 Па (теплосодержание i = 2747,8 кДж/кг) удельный расход пара на 1 кг бумаги составляет
Dуд = 11199,38 /(2747,8 - 4,19 ·151,1) = 5,30 кг/кг бумаги.
Приняв потери пара в трубопроводе равными 5 %, получим фактический расход пара на 1 кг бумаги
D = 5,30/0,95= 5,58 кг/кг.
3.5 Расчет вентиляции сушильной части и зала БДМ
Расход сухого воздуха L, кг/ч, для удаления испаряющейся влаги определяют по формуле (27) [10].
L = 1000· 1,1 B /(dуφу - dпφп), (27)
где B - количество влаги, испаряющейся в сушильной части машины, кг/ч;
dу, dп - содержание влаги в 1 кг уходящего и поступающего воздуха при полном насыщении, г;
φу, φп - относительная влажность поступающего и уходящего воздуха;
1,1 - коэффициент, учитывающий испарение влаги в мокрой части БДМ.
Определим количество воздуха для вентиляции:
– зимой
Lз = 1000·1,1·9435,35/(158,5·0,65 - 1,05·0,8) = 101569,56 кг/ч;
– летом
Lл = 1000·1,1·9435,35/(158,5·0,65 - 15,19·0,7) = 112335,32 кг/ч.
Объем воздуха, подаваемого в зал БДМ, составит
Li’ = L/yt, (28)
где y t – плотность воздуха при температуре t, кг/м3.
Плотность воздуха при температуре t можно определить из формулы:
(29)
где y0 – плотность воздуха при абсолютном нуле, 1,293 кг/м3;
T0 – температура абсолютного нуля, 273 К;
Tt = 273+ t°С.
Следовательно, получим
– зимой
L'з = = 74237,29 м3/ч;
– летом
L'л = = 93244,40 м3/ч,
Расход теплоты для подогрева поступающего воздуха определяется из теплового баланса как разница между расходом тепла в зале БДМ и приходом теплоты в зал для создания нормальных условий работы в зале и нормального процесса сушки бумаги.
Приход теплоты рассчитываем по формуле (30):
Qприх = Q1 + Q2 + Q3 + Q4 + Q5, (30)
где Q1 - теплота, отдаваемая паром, кДж/ч;
Q2 - теплота поступающего в зал (наружного) воздуха, кДж/ч;
Q3 - теплота бумажной массы, кДж/ч;
Q4 - теплота свежей воды, кДж/ч;
Q5 - теплота трения, кДж/ч.
1) Теплота Q1, отдаваемая паром, кДж/ч
Q1 = D(Iп - Iк), (31)
где D - расход пара в сушильных цилиндрах, при температуре 140 °С, кг/ч;
Iп - энтальпия пара, кДж/кг;
Iк - энтальпия конденсата, кДж/кг.
D = D’×Рчас; (32)
где D’ – фактический удельный расход пара, кг/кг;
Рчас – часовая производительность БДМ, кг/ч.
D = 2,3·9435,35= 21701,31 кг/ч;
Q1 = 21701,31 ·(2740,0 - 589,5) = 46668667,16 кДж/ч
2) Теплота Q2, поступающего наружного воздуха, кДж/ч
Q2 = LпIс, (33)
где Lп - расход приходящего воздуха, кг/ч;
Iс - энтальпия свежего (приточного) воздуха, кДж/кг.
Определим теплоту поступающего в зал воздуха:
– зимой
Q2 = LзIз,
где Iз - энтальпия наружного воздуха зимой, кДж/кг, I з = -12,49 кДж/кг;
Q2 = 101569,56 ·(-12,49) = –1268603,80 кДж/ч;
– летом
Q2 = LлIл,
где Iл - энтальпия наружного воздуха летом, кДж/кг, Iл = 58,66 кДж/кг;
Q2 = 112335,32 ·58,66 = 6589589,87 кДж/ч
3). Теплота Q3, приносимая бумажной массой, кДж/ч
Температура массы, поступающей в машинный бассейн, и оборотной воды, tм: зимой 10 °С, летом 20 °С. Расчет ведем без учета потерь волокна в мокрой и прессовой части. Концентрация массы в машинном бассейне – 3%.
Q3 = (вбcб + Bнcв)tм, (34)
где вб - количество волокна, поступающего на БДМ, кг/ч;
cб - удельная теплоемкость волокна, кДж/(кг·ºC), cб = 1,22 - 1,30 кДж/(кг·oC)
Bн - количество воды, поступающей с массой, кг/ч;
cв - удельная теплоемкость воды, кДж/(кг·ºC);
tм -температура бумажной массы, ºC.
Найдем теплоту бумажной массы:
- зимой
Q3 = (7107,72·1,25 + 9913,57·4,19)·10 = 504225,08 Дж/ч;
- летом
Q3 = (7107,72·1,25 + 9913,57·4,19)·20 = 1008450,17 кДж/ч
4) Теплота приносимая свежей водой Q4, кДж/ч
Расход воды на одну БДМ составляет 33 м3/т, часовой расход 623,79 м3/ч. Принимаем, что 50 % этой воды в виде сточной уходит из зала БДМ, а остальная сточная вода уходит с ловушки.
Q4 =Wt в с в,(35)
где W – часовой расход воды, кг/ч;
tв - температура воды, ºC:
сб – удельная теплоемкость волокна, кДж/(кг×°С);
– зимой – 3 ºC;
– летом – 18 ºC.
- зимой:
Q4 = 4,19·9435,35·3 = 118602,35 кДж/ч;
- летом:
Q4 =4,19·9435,35·18 = 711614,10 кДж/ч.
5) Теплота, выделяющаяся в результате трения частей механизмов, работающих в помещении сушильной машины, кДж/ч
Q5 = 3600 kN, (36)
где k - коэффициент, указывающий, какое количество механической энергии переходит в тепловую, и зависящий от типа подшипников (примерно 15 %);
N - суммарная мощность электродвигателей, обслуживающих БДМ, кВт,
(1 кВт = 1 кДж/с);
Общий расход электроэнергии на 1 тонну картона 460 кВт×ч. Часовая производительность БДМ Рчас» 27,73 т/час.
Тогда найдем суммарную мощность электродвигателей, обслуживающих БДМ:
N = 460 × 27,73 = 12755,8 кВт.
Q5 = 3600·0,15·12755,8 = 6888132 кДж/ч.
Общий приход тепла в час в зал БДМ составит:
- зимой:
Qприх = 46668667,16 – 1268603,80 + 504225,08 + 118602,35 + 6888132 =
= 52911022,79 кДж/ч;
- летом:
Qприх = 46668667,16 + 6589589,87 + 1008450,17 + 711614,10 + 6888132 =
= 61866453,30 кДж/ч.
Расход теплоты определяют по формуле
Qух = Q6 + Q7 + Q8 + Q9, (37)
где Q6 - теплота, уносимая бумагой, кДж/ч;
Q7 - теплота, уносимая влажным воздухом, кДж/ч;
Q8 - тепловые потери здания, кДж/ч;
Q9 - теплота, уносимая сточными и оборотными водами, кДж/ч.
1 Теплота, уносимая высушенной бумагой
Q6 = (Gбcб + Bбcв)tб,, (38)
где Gб - часовая выработка абсолютно сухой бумаги, кг/ч;
Bб - количество воды в бумаге, кг/ч;
cб - теплоемкость бумаги, кДж/(кг·oC);
tб – температура бумаги, оС, t = 70 оС.
Q6 = (7107,72·1,4 + 453,68·4,19)·70 = 829620,96 кДж/ч
2 Теплота, уносимая влажным воздухом, кДж/ч
Q7 = LуIу, (39)
где Ly -расход уходящего воздуха, кг/ч;
Iу – энтальпия уходящего воздуха, кДж/ч:
Iу = 473,47 кДж/ч;
- зимой:
Q7 = 229433,41·473,47 = 108629836,6 кДж/ч
- летом:
Q7 =260558,10·473,47 = 123366443,6 кДж/ч
3 Тепловые потери здания
Размеры здания для двух БДМ 132х24х17,2 м, кубатура его составляет 54489,6 м3, на одну машину 27244,8 м3. Примем удельные потери тепла зданием 1,163 Вт/(м2×°С). Тогда потери тепла зданием составят
Q8 = 3,6КF·0,5(tб – tк), (40)
где К – коэффициент теплоотдачи для каждого типа излучающей теплоту поверхности, Вт/(м2×°С);
tб - температура внутри помещения;
tк - температура снаружи помещения;
F – площадь излучающей поверхности.
- зимой:
Q8 = 3,6 × 2,095·27244,8 (25 + 15) = 8219211,26 кДж/ч;
- летом:
Q8 = 3,6·2,095 ×27244,8 (25 – 20) = 1027401,41 кДж/ч.
4. Теплота, уносимая сточными и оборотными водами, кДж/ч
Q9 = Wстtс св, (41)
где Wст - количество сточных вод, уходящих из зала БДМ (условно Wст равно количеству свежей воды, расходуемой на производство бумаги), кг/ч;
tс - температура сточных вод, ºC.
- зимой:
Q9 = (623799·8 + 623799·10)0,5 = 5614191 кДж/ч;
- летом:
Q9 = (623799·20 + 623799·20)0,5 = 12475980 кДж/ч.
Общий расход тепла на одну БДМ составит:
- зимой:
Qух = 829620,96 + 108629836,6 + 8219211,26 + 5614191 = 123292859,82 Дж/ч;
- летом:
Qух = 829620,96 + 123366443,6 + 1027401,41 + 12475980 = 137699445,97 кДж/ч.
Баланс тепла в зале БДМ приведен в таблице 6
Таблица 6 - Баланс тепла в зале БДМ в кДж/ч
Статьи прихода и расхода | Зимой | Летом |
Приход тепла | ||
Тепло, отдаваемое паром | 46668667,16 | 46668667,16 |
Тепло, приносимое свежим воздухом | - 1268603,80 | 6589589,87 |
Тепло, приносимое массой | 504225,08 | 1008450,17 |
Тепло, приносимое свежей водой | 118602,35 | 711614,10 |
Тепло от трения частей механизмов | ||
Итого | 52911022,79 | 61866453,30 |
Расход тепла | ||
Тепло, уносимое картоном | 829620,96 | 829620,96 |
Тепло, уносимое влажным воздухом | 108629836,6 | 123366443,6 |
Теплопотери зданием | 8219211,26 | 1027401,41 |
Тепло, уносимое сточными и оборотными водами | ||
Итого | 123292859,82 | 137699445,97 |
Недостаток тепла | 70381837,03 | - |
Избыток тепла | – | 75832992,67 |
4 РАСЧЕТ КОЛИЧЕСТВА УСТАНАВЛИВАЕМОГО ОСНОВНОГО И ВСПОМОГАТЕЛЬНОГО ОБОРУДОВАНИЯ
Подберу и рассчитаю следующее оборудование, находящееся в сушильной части БДМ и далее по потоку полотна бумаги:
- колпак закрытый;
- укрытие сушильных частей БДМ на первом этаже;
- цилиндры сушильные;
- ПРС.
4.1 Колпак закрытый
Предназначен для организованного удаления паровоздушной смеси из сушильной части, интенсификации процесса сушки бумажного полотна, сокращения расхода тепловой энергии, исключения растекания по залу горячего, насыщенного влагой воздуха, что улучшает условия работы персонала и снижает вредное воздействие атмосферы зала на строительные конструкции и оборудование. Кроме того, колпак снижает шум в зале от сушильной части.
Технические характеристики закрытого принимаемого колпака представлены в таблице 7 [7, с. 45].
Таблица 7 – Техническая характеристика закрытого колпака
Обрезная ширина полотна, м | Размеры, мм | Масса 1 м длины колпака, т | |
Высота (от уровня пола второго этажа) | Ширина | ||
Свыше 2520 до 4200 | 7000-7500 | 7000-9500 | 1,0-1,2 |
4.2 Укрытие сушильных частей БДМ на первом этаже
Предназначены для интенсификации процесса сушки, снижения расхода тепловой энергии, исключения растекания горячего, насыщенного влагой воздуха по залу бумагоделательных машин, для улучшения условий работы персонала и снижения вредного воздействия на строительные конструкции и оборудование.
Укрытия имеют щиты раздвижные для лицевой стороны и стационарные с дверями – для приводной стороны.
Укрытия состоят из стального каркаса с антикоррозийным лакокрасочным покрытием, панелей из алюминиевых листов и системы освещения сушильной части в подвале.
Технические характеристики укрытия сушильных частей БДМ на первом этаже представлены в таблице 8 [7, с. 45].
Таблица 8 – Укрытие сушильных частей КДМ на первом этаже
Обрезная ширина полотна, м | Размеры колпака, мм | Масса 1 м2 укрытия, т | ||
Ширина укрытия | От оси шин с лицевой стороны | От оси шин с приводной стороны | ||
4.3 Цилиндры сушильные
Предназначены для контактной сушки бумажного полотна.
Основные части цилиндра – корпус и соединенные с ним болтами торцевые крышки, которые изготовляются цельнолитыми или запрессованными цапфами.
В крышке лицевой стороны имеется герметично закрытый люк овальной формы для проведения монтажа и ремонта конденсатоотводного устройства и термопланок или внутреннего осмотра цилиндра. Термопланки устанавливаются для увеличения теплопередачи в сушильных цилиндрах.
В качестве уплотнительного материала поверхностей разъемов корпуса цилиндра и крышек применяется специальные пасты. Корпуса цилиндров отливаются из обычного чугуна, либо лигерованным никелем, хромом и др.
По каталогу ЗАО «Петрозаводскмаш» [7, с. 83] принимаю сушильные цилиндры с диаметром 1500 мм., его техническая характеристика представлена в таблице 9.
Таблица 9 - Техническая характеристика периферического наката
Обрезная ширина полотна, м | Габаритные размеры, мм | Масса, т | ||
длина | ширина | высота | ||
7500/5000 | 4000/2400 | 27/23 |
Приближенно мощность электродвигателя наката может быть рассчитана по формуле (42):
Nнакат = 1,67 × 10-5 × f × B0 × V; (42)
где f – давление прижима рабочих вилок, 1500 Р/м;
B0 – обрезная ширина картонного полотна;
V – скорость БДМ м/мин.
Nнакат = 1,67 × 10-5 × 1500 × 4,2 × 495,70 = 52,15» 53 кВт.
4.4 Продольно-резательный станок
Предназначен для перемотки и продольного разрезания бумажного полотна на форматы. Принимаю к установке современный продольно-резательный станок WinBelt фирмы METSO.
Примерная мощность, потребляемая продольно-резательным станком, рассчитывается по формуле (43).
NПРС = ; (43);
где g – масса 1м2 бумаги, г\м2;
B0 – обрезная ширина картонного полотна, м;
V – средняя рабочая скорость станка (в 2 раза больше скорости БДМ) м/мин;
KH – коэффициент натяжения бумажного полотна, 0,2.
NПРС = = 99,50 кВт.
5 ЭНЕРГЕТИЧЕСКАЯ ЧАСТЬ
Энергетическая часть курсового проекта включает в себя расчет потребности в сушильного цеха в электроэнергии. Расчет выполняется по потребляемой средней активной мощности [9]. Результаты расчета сведу в таблицу 10.
Таблица 10 – Потребности сушильного цеха в электроэнергии
№ п/п | Наименование агрегата | Количество агрегатов, шт. | Коэффициент использования | Мощность, кВт | ||
номинальная | установленная | Потребляемая средняя активная | ||||
Гидроразбиватель | 0,98 | |||||
Накат | 0,98 | |||||
ПРС | 0,98 | |||||
Сумма потребляемой средней активной мощности ∑Рс = 504 кВт |
Расчет удельного расхода электроэнергии производится по следующим формулам (44), (45) и (46).
(44)
где Ру – установленная активная мощность, кВт;
n – число работающих двигателей, шт.;
РН – номинальная мощность двигателя, кВт.
(45)
где Рс – средняя активная мощность, кВт;
К - коэффициент использования.
(46)
где Зу – удельный расход энергии, кВт×ч/т;
Q – суточная производительность цеха или завода, т.
Значит, величина удельного расхода электроэнергии сушильного цеха бумажной фабрики производства тетрадной бумаги:
= 18,97» 19 кВт
6 ОХРАНА ПРИРОДЫ: ОЧИСТКА СТОЧНЫХ ВОД И ГАЗОВЫХ ВЫБРОСОВ В ПРОЕКТИРУЕМОМ ЦЕХЕ
Повышение содержания зольных элементов в бумажном сырье приводит к повышению загрязненности оборотной и сточной воды. Выход волокнистых полуфабрикатов косвенно характеризует загрязненность сточной воды. Загрязнения, состоят из волокон, частиц печатной краски и остатков химических реагентов. Эти загрязнения попадают в сточную воду предприятия или поступают вместе с массой на БДМ [3].
Система водоснабжения предприятия и степень замкнутости его водооборота являются одними из важнейших факторов, влияющих на загрязненность сточной воды производства. Объем сбрасываемых стоков производства невелик, однако представляет определенную экологическую опасность.
Присутствие в контуре водопользования растворенных веществ и мелких частиц примесей является нежелательным. При максимально замкнутом водопользовании расход воды составляет 4 м³/т оборотной воды, что соответствует 5,5 м³/т свежей воды. Производственный опыт показывает, что при данных условиях растворенные вещества поступают с промывными водами; ХПК достигает 7,5 кг/т.
При уменьшении объема сточной воды происходит накопление вредных веществ в производственной воде, что приводит к ухудшению показателей механической прочности бумаги, снижению производительности БДМ, коррозии оборудования и появлению неприятного запаха в производственных помещениях. В полностью замкнутой системе водопользования концентрация ХПК достигает более 30 кг/т.
Концентрация ХПК оборотной воды в контуре водопользования увеличивается с понижением объема сточной воды. Повышение величины ХПК необходимо ограничить за счет удаления небольшого объема сточной воды из системы и добавления свежей воды. Определенный объем воды удаляется из системы с отходами, а часть воды испаряется при сушке бумажного полотна на БДМ.
7 ТЕХНИКО-ЭКОНОМИЧЕСКИЕ ПОКАЗАТЕЛИ
В проектируемом сушильном цехе по производству тетрадной бумаги рассчитываются технико-экономические показатели на основе всех материалов курсового проекта, которые сведены в таблицу 11 [9].
Таблица 11 - Технико-экономические показатели
Показатели | Значение |
Производительность машины, т/сут | 173,913 |
Часовая выработка, кг/ч | 7561,4 |
Время выработки 1 т. продукции/мин. | 126,02 |
Количество часов работы машины в сутки, ч | |
Скорость машины, м/мин | 495,70 |
Масса 1 м2, г |
8.Автоматический контроль и регулирование процесса сушки бумаги
Непрерывный и автоматическийконтроль за основными показателями процесса сушки бумаги: давлением пара и его температурой, температурой сушильных цилиндров и влажностью бумажного полотна, а также автоматизация процесса сушки бумаги приобретают на современных бумагоделательных машинах большое значение, так как позволяют повысить качество вырабатываемой бумаги и снизить брак при производстве.
В настоящее время применяются следующие аппараты показывающего, регистрирующего и регулирующего действия для контроля и управления процессами сушки:
1) автоматические регуляторы, поддерживающие постоянное давление в паровой магистрали перед главным регулирующим вентилем;
2) показывающие и регистрирующие аппараты, контролирующие влажность бумажного полотна в конце сушки, а также аппараты, контролирующие температуру поверхности сушильных цилиндров;
3) автоматические регуляторы процесса сушки бумаги различныхсистем.
Автоматическое регулирование сушки бумаги полностью оправдывает себя на специализированных машинах, вырабатывающих один или небольшое количество видов бумаги. На бумагоделательных машинах широкого профиля, изготовляющих разнообразный ассортимент бумаги, автоматическое регулирование сушки осложняется необходимостью специальной настройки регулятора при каждой перемене вырабатываемого на машине вида бумаги. Поэтому в подобных случаях предпочитают оснащать машину приборами показывающего или, лучше, регистрирующего типа (с записью процесса на диаграммной бумаге), непрерывно контролирующими температуру цилиндров и влажность вырабатываемой бумаги - основных переменных величин, характеризующих сушку бумаги.
Для надежного управления процессом сушки при ручном и автоматическом регулировании давление пара в паровой магистрали перед регулировочнымвентилем, а следовательно, и его температура должны быть неизменными. Для этого на главном паропроводе (а иногда и на вспомогательных паропроводах) перед регулирующим вентилем устанавливают регулятор давления, который автоматически поддерживает постоянным давление пара в паровой магистрали.
Для контроля и автоматического регулирования влажности бумажного полотна в процессе сушки сконструировано и применяется в промышленности большое число различных аппаратов. Действие их основывается на восприятии импульса от одного из переменных факторов, связанных с изменением свойств бумаги при сушке. Такими факторами, например, могут быть изменение усадки бумаги при сушке, температуры бумажного листа, расхода пара на сушку, а также влажности бумаги, которая может быть измерена по се электропроводности, диэлектрической постоянной и влажности воздуха, пропускаемого над бумагой.
Большое значение при выработке бумаги на бумагоделательной машине имеют контроль и регулирование влажности бумажного полотна по ширине машины. Эту задачу в настоящее время еще нельзя считать окончательно решенной, однако пути к ее решению уже намечаются. Для непрерывного измерения влажности бумаги по ширине полотна и записи ее па диаграмме начинают применять подвижные датчики, непрерывно перемещающиеся по ширине бумажного полотна, а работающие по принципу бетаметров.
Неравномерная влажность бумаги зависит от ряда переменных факторов: неравномерного отлива бумаги на сетке из-за несовершенства напорных устройств, неравномерного отжима бумаги на прессах, загрязнений прессовых сукон и условий вентиляции бумаги в межцилиндровыхпространствах. Поэтому легче бывает исправить неоднородность полотна подсушкой влажных или увлажнением сухих полос вбумаге, нежели устранитьпричины, вызывающиенеоднородность бумажного полотна по влажности.
В соответствии с этим предложено два способа выравнивания влажности бумажного полотна по его ширине: подсушивание более влажных полос с помощью вентиляционныхколпаков скоростной сушки, допускающих регулирование подачи воздуха в отдельных секциях по ширине полотна, или увлажнение более сухих полос в бумаге с помощью соплового водяного спрыска. Оба эти способа допускают не только ручное, по и автоматическое управление работой секционного вентиляционного колпака или увлажнительного спрыска.
9. ОСНОВНЫЕ ПРАВИЛА БЕЗОПАСНОСТИ ЭКСПЛУАТАЦИИ
ПРОИЗВОДСТВА
Классификация буммашины №3 по взрывопожаробезопасности, степени огнестойкости, электрооборудования и санитарной характеристики.
Таблица 12 – Классификация производственного процесса
Наименование цеха, отделения, установки | Категория производства по СНИП П-90-81 | Класс помещения по правилам устр. эл. устан. ПЭУ-76 | Категория и группа взрывных смесей по ПХВРО | Группа произв. процессов по СНИП 92-76 и отраслевым нормам |
Сеточная часть буммашины | “Д” | - | - | II |
Прессовая часть буммашины | “Д” | - | - | II |
Сушильная часть буммашины | “В” | - | - | II |
Отделение резки, упаковки бумаги | “В” | П-Ш | - | II |
СПИСОК ИСПОЛЬЗОВАННЫХ ИСТОЧНИКОВ
1 Иванов Г.А. Общая технология изделий из бумаги и картона. – М.: Экология, 1993. – 160 с.
2 Фляте Д.М. Технология бумаги. - М.: Лесн. пром-сть, 1988. – 439 с.
3 Целлюлоза. Бумага. Под ред. Дипл. Инж. А. Опхердена. //М.: Лесная пром-ть, 1980. – 472 с.
4 Оборудование целлюлозно-бумажного производства. В 2-х т. Т. 2 Бумагоделательные машины / В.А Чичаев, А.А. Васильева, И.А. Васильев и др. - М.: Лесн. пром-сть, 1981. – 264 с.
5 Иванов С.Н. Технология бумаги. – М.: Лесн. пром-сть, 1970. – 695 с.
6 Комаров В.И. Технология бумаги. Методические указания к курсовому проекту. - Архангельск: АГТУ, 1977. – 33 с.
7 Оборудование для целлюлозно-бумажного производства. Каталог в 2 кн.: Кн.2 Оборудование для производства целлюлозы. [Текст]: - ЗАО Петрозаводскмаш. – Петрозаводск: Скандинавия, 2002. – 112 с.
8 Примаков С.Ф. Производство бумаги. - М.: Лесн. пром-сть, 1987. - 224 с.
9 Гурьев А.В. Технология целлюлозно-бумажного производства: методические указания к курсовому проектированию Учебное пособие. [Текст] / А.В. Гурьев, Л.А. Миловидова, Г.В. Комарова. – Архангельск: Изд-во АГТУ, 2005.-18 с.
10 Соколова Л.М., Овдейчук В.П., Самсон М.В. Учебное пособие по курсовому и дипломному проектированию технологических процессов ЦБП. Учебное пособие для техникумов. - М.: Лесн. пром-сть, 1982. - 160 с.
Дата добавления: 2015-12-18; просмотров: 33; Мы поможем в написании вашей работы! |
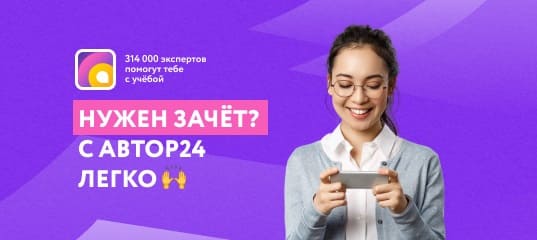
Мы поможем в написании ваших работ!