Классификация методов контроля
К дефектам сварных соединений относятся различные отклонения от установленных норм и технических требований, которые уменьшают прочность и эксплуатационную надежность сварных соединений и могут привести к разрушению всей конструкции.
В соответствии с ГОСТ 30242 дефекты сварных соединений подразделяются на 6 групп.
1)Трещины
2)Поры
3)Несплавления
4)Нарушение формы шва
5)Твердое включение
6)Прочие дефекты не включенные в группу с 1-5.
Использование методов неразрушающего контроля позволяет существенно сократить объем необходимых проверок. Рассмотрим наиболее распространенные из этих методов.
Методы неразрушающего контроля предназначены для обнаружения дефектов материала и признаков разрушения деталей, в частности – нарушений сплошности материала, его структуры, его структуры, отклонений физико-химический свойств.
В зависимости от используемых физических процессов методы подразделяются на:
акустические;
капиллярные;
магнитные;
оптические;
радиационные;
радиоволновые;
тепловые;
электрические;
электромагнитные.
2) Типы сварочные дефектов. Влияние дефектов на эксплуатационные характеристики сварных соединений и конструкций в целом.
В соответствии с ГОСТ 30242 дефекты сварных соединений подразделяются на 6 групп.
1)Трещины
2)Поры
3)Несплавления
4)Нарушение формы шва
5)Твердое включение
6)Прочие дефекты не включенные в группу с 1-5.
|
|
Дефекты сварных соединений подразделяют на наружные и внутренние.
Наружные дефекты:
Нарушение размеров и формы шва; подрезы; наплывы; кратер — углубление в конце шва; прожоги.
Внутренние дефекты:
Поры; шлаковые включения; непровары; несплавления; трещины; дефекты структуры.
Пористость металла шва иногда частично выступает наружу, в виде углублений различного продольного расположения.
Причины образования наружных и внутренних дефектов, способы их исправления
Подрезы, наплывы — от завышенного или заниженного тока, а также недостаточных навыков сварщика.
Кратер — из-за небрежности сварщика.
Долговечность и надежность отдельных элементов и узлов сварных конструкций, а также всего сооружения в целом во многом зависят от качества сварных соединений, их прочности.
Влияние различных дефектов на механические свойства сварного соединения определяется многими факторами: формой и величиной дефектов, частотой их появления, материалом конструкции, характером действия внешних нагрузок (например, сильно снижают прочность пульсирующие, знакопеременные или ударные нагрузки). Поверхностные дефекты швов сварных соединений не представляют большой опасности для работоспособности конструкции, так как их легко обнаружить и устранить.
|
|
Наиболее опасными являются дефекты, которые имеют вытянутую форму и острые очертания, например трещины, способствующие концентрации внутренних напряжений и легко распространяющиеся в глубь металла.
Глубокие подрезы также являются зонами концентрации напряжений, но они менее опасны, чем трещины и непровары.
Большое влияние на прочность и несущую способность конструкций оказывают сварочные деформации. Искривление продольной оси элементов конструкций, работающих на сжатие, местное выпучивание, грибовидность полок балок и колонн могут привести к потере устойчивости и разрушению всей конструкции.
3) Визуально-измерительный контроль: краткая характеристика метода, применяемое оборудование и основные контролируемые параметры.
Это один из методов неразрушающего контроля оптического вида. Он основан на получении первичной информации о контролируемом объекте при визуальном наблюдении или с помощью оптических приборов и средств измерений. Внешним осмотром (ВИК-ом) проверяют качество подготовки и сборки заготовок под сварку, качество выполнения швов в процессе сварки и качество готовых сварных соединений.
|
|
Визуальный метод контроля позволяет обнаруживать несплошности, отклонения размера и формы от заданных более 0,1 мм при использовании приборов с увеличением до 10 х.
Визуальный контроль, как правило, производится невооруженным глазом или с использованием увеличительных луп до 7 х. В сомнительных случаях и при техническом диагностировании допускается применение луп с увеличением до 20 х.
Перед проведением визуального контроля поверхность в зоне контроля должна быть очищена от ржавчины, окалины, грязи, краски, масла, брызг металла, и других загрязнений, препятствующих осмотру.
Визуальный контроль и измерения производятся:
· на стадии входного контроля материала для выявления поверхностных дефектов (трещин, расслоений, забоин, закатов, раковин, шлаковых включений и др.), а также отклонений геометрических размеров заготовок от проектных;
· на стадии подготовки деталей под сборку и сварку для подтверждения соответствия установленным требованиям конструктивных элементов разделки и чистоты кромок, и прилегающих поверхностей, отсутствия углового и поверхностного смещения, величины зазоров, количества, расположения и качества прихваток;
|
|
· по окончании сварки, либо на отдельных её этапах - для выявления в сварном соединении поверхностных дефектов и несплошностей (трещин, раковин, пор, свищей, подрезов, прожогов, наплывов, грубой чешуйчатости и западаний между валиками, непроваров и др.); а также отклонений геометрических размеров сварного шва от требований, установленных стандартами.
· на стадии технического диагностирования - для выявления отклонений размеров и формы конструкции от проектных; эксплуатационных дефектов основного металла и сварного шва (усталостных трещин, коррозионных язв, питтингов и др.).
Измерения производятся с использованием приборов и инструментов:
· лупы измерительные;
· штангенциркули;
· линейки измерительные металлические;
· угломеры;
· угольники;
· щупы;
· шаблоны и др.
Дата добавления: 2015-12-17; просмотров: 10; Мы поможем в написании вашей работы! |
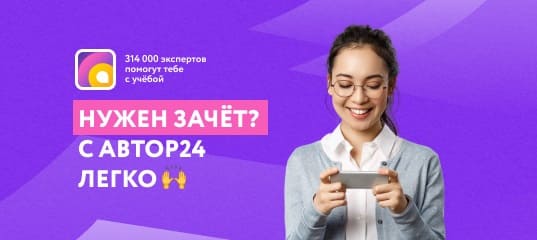
Мы поможем в написании ваших работ!