Порядок проведения испытания
Для исследования горную породу дробят или изготавливают из нее прозрачные шлифы. Гравийные материалы подвергают петрографической разборке с использованием бинокулярной лупы. Зерна потенциально реакционноспособных минералов, выделенные при минералого-петрографической разборке, взвешивают и определяют их содержание Х1, % по массе, по формуле
, (2.44)
где
т1 — масса ПРС зерен, г;
т — масса аналитической пробы, взя, г.
Горную породу, щебень (гравий) относят к потенциально реакционноспособным, если при петрографической разборке обнаружено наличие одной или нескольких разновидностей минералов, содержащих реакционноспособный кремнезем в количествах, равных или превышающих значения, указанные в таблице 2.18.
Таблица 2.18
Минерал и вид кремнезема | Виды потенциально реакционно-способных пород | Минимальное содержание минерала, % по массе, при котором возможна щелочная коррозия бетона |
Опал | Базальты и другие лавы. Известняки, роговики, сланцы опаловидные | 0,25 |
Стекло кислое аморфное | Обсидианы, перлиты, липариты, дациты, андезитодациты, андезиты, туфы и аналоги этих пород, имеющие стекловидную основу | 3,0 |
Халцедон кри-птомикрокрис-таллический | Кремни, известняки, доломиты, песчаники с опалохалцедоновым и халцедонокварцевым цементом, яшмы, роговики | 5,0 |
Кристобалит, тридимит кристаллические | Расплавы, состоящие из кремнезема (материалы, полученные плавлением) | 1,0 |
Кварц выветрелый деформированный | Кварцевые витрофиры, кварциты, песчаники, вулканические и метаморфические кислые породы | 3,0 |
|
|
Оптические и физические характеристики модификаций кремнезема в шлифах, которые необходимо учитывать при минералогопетрографическом анализе, приведены в таблице 2.19.
Таблица 2.19
Модификация кремнезема | Кристаллическая система | Внешние формы | Показатель светопреломления | Истинная плотность, (см3) | ||
Ng | Nm | |||||
b-кварц | Тригональная | Призмы | 1,553 | 1,544 | 2,65 | |
a-кварц | Гексагональная | Бипирамиды | 1,540 | 1,530 | 2,60 | |
у -тридимит | Ромбическая | Пластинки-двойники | 1,473 | 1,470 1,489 | 2,27 | |
b-тридимит | Тригональная Триклиническая | — Зерна-двойники | 1,470 1,487 | — 1,484 | — 2,32 | |
a-кристобалит | Кубическая | Октаэдры | 1,466 | — | 2,21 | |
Водный кремнезем | Отсутствует | — | — | — | 1,90 | |
Опал | Отсутствует | — | — | 1,406 1.460 | 2,30 | |
Халцедон | Не установлена | Кристаллы в виде волокон | 1,540 | 1,532 1,530 | 2,55 2,58 | |
Стекло кислое аморфное | Отсутствует | — | — | 1,458 | 2,20 | |
Химические методы
Методы основаны на определении содержания в горной породе, щебне (гравии) реакционноспособного кремнезема, растворимого в 1 М растворе гидроксида натрия.
|
|
Содержание растворимого в щелочах кремнезема определяют весовым или фотоколориметрическим методом.
Горную породу щебень (гравий) считают нереакционноспособными по отношению к щелочам и пригодными к использованию в качестве заполнителя для бетонов, если содержание в них растворимого кремнезема не более 50 ммоль/л
Рисунок 2.10 — Сосуд из коррозионно-стойкого материала
1 — корпус; 2 — крышка; З — захват;
Средства контроля и вспомогательное оборудование
Сита стандартные с отверстиями диаметром 5 мм и сеткой №0315 и 016
Ступка.
Весы настольные циферблатные по ГОСТ 29329 или лабораторные по ГОСТ 24104.
Весы аналитические по ГОСТ 24104 с погрешностью взвешивания ± 0,0002 г.
Сосуд из нержавеющей стали, фторопласта, винипласта по ГОСТ 9639 или другого коррозионно-стойкого материала (рисунок 2.10).
Электропечь с терморегулятором температуры (80±1)°С.
Насос водоструйный.
Склянка Бунзена.
Воронки с фильтром Шотта.
Пипетки по ГОСТ 29227 вместимостью 25 мл.
Натрия гидроокись (гидроксид натрия) по ГОСТ 4328, 1 М раствор.
Порядок подготовке к испытанию
Для определения потенциально реакционной способности горной породы, щебня и гравия, в которых обнаружено присутствие одной или нескольких разновидностей реакционноспособных минералов, отбирают пробу массой не менее 300 г, измельчают до крупности от 0,3 15 до 0,16 мм, после чего ее промывают дистиллированной водой на сите с отверстиями размером 0,16 мм и высушивают до постоянной массы.
|
|
Порядок проведения испытания
Отвешивают две навески массой по 25 г, каждую из которых высыпают в отдельный сосуд из коррозионно-стойкого материала и добавляют по 25 мл 1 М раствора гидроксида натрия. Сосуды с содержимым несколько раз встряхивают для удаления пузырьков воздуха, плотно закрывают крышками и помещают в электропечь, предварительно нагретую до 80°С. Одновременно ставят глухой опыт, для чего в третий сосуд наливают 25 мл 1 М раствора гидроксиланатрия. В течение испытания в электропечи поддерживают температуру (80±2)°С.
Через 24 ч сосуды вынимают из электропечи и охлаждают холодной водой так, чтобы температура их в течение 15 мин снизилась до комнатной.
После охлаждения содержимое каждого сосуда фильтруют в сухую пробирку через сухой фильтр. Сначала в воронку, не встряхивая, сливают по стеклянной палочке раствор, затем шпателем на фильтр переносят твердый остаток. Жидкость фильтруют до тех пор, пока скорость фильтрации не замедлится до 1 капли за 10 с (промывание не допускается). Для фильтрования используют водоструйный насос со склянкой Бунзена и воронкой с фильтром Шотта для каждой пробы (рисунок 2.11).
|
|
Фильтрат взбалтывают до получения однородного раствора и используют для определения содержания растворимого кремнезема.
2.3.1.23 Весовой метод определения содержания растворимого кремнезема
Метод основан на выделении растворимого кремнезема из раствора гидроксида натрия и определении его массы.
Рисунок 2.11— Устройство для сбора фильтрата
1 — водоструйный насос; 2 — резиновая пробка; З — воронка с фильтром Шотта;
4 — склянка Бунзена; 5 — пробирка для сбора фильтрата;
Средства контроля и вспомогательное оборудование
Весы аналитические по ГОСТ 24104 с погрешностью взвешивания ± 0,0002 г.
Электропечь с терморегулятором температуры (1000±50)°С.
Шкаф сушильный.
Баня водяная.
Чашки фарфоровые для выпаривания по ГОСТ 9147.
Тигли платиновые по ГОСТ 6563.
Пипетки по ГОСТ 29227 и ГОСТ 29228 на 5 мл.
Фильтры беззольные (белая лента).
Кислота соляная концентрированная плотностью 1,19 г/см3 по ГОСТ 3118.
Серебро азотнокислое (нитрат серебра) по ГОСТ 1277.
Кислота азотная концентрированная по ГОСТ 4461.
Раствор азотнокислого серебра, содержащий в 100 мл 1 г азотнокислого серебра и 1 мл концентрированной азотной кислоты.
Вода дистиллированная по ГОСТ 6709.
Порядок проведения испытания
Для определения содержания растворимого кремнезема пипеткой отбирают от 5 до 10 мл фильтрата, помещают его в фарфоровую чашку, добавляют от 5 до 10 мл концентрированной соляной кислоты и выпаривают на водяной бане до получения сухого остатка.
Остаток в чашке увлажняют 5 мл концентрированной соляной кислоты, выдерживают 5—10 мин, добавляют 100 мл горячей дистиллированной воды, перемешивают, выдерживают 10 мин на водяной бане и фильтруют (фильтр — белая лента), остаток на фильтре промывают горячей водой до исчезновения реакции на хлориды (при добавлении 1—2 капель раствора нитрата серебра вода должна оставаться прозрачной).
Фильтр с осадком помещают в тигель. Фильтрат переносят в фарфоровую чашку, выпаривают досуха и выдерживают в течение30 мин в сушильном шкафу при температуре около 105 0С. Сухой остаток увлажняют 5 мл концентрированной соляной кислоты, разбавляют водой и фильтруют. Остаток на фильтре промывают до исчезновения реакции на хлориды. Фильтр с осадком помешают в тигель вместе с первым фильтром, подсушивают, озоляют, прокаливают при температуре (1000±50)°С до постоянной массы и взвешивают. Масса осадка т в тигле, г, соответствует содержанию кремнезема в 5 мл раствора гидроксида натрия.
Обработка результатов испытания
Содержание растворимого кремнезема SiO2p ммоль/л исходного раствора гидроксида натрия, определяют по формуле
, (2.45)
где
т — масса осадка в тигле, г;
106 — переводной коэффициент;
V — объем фильтрата, взятого для определения растворимого кремнезема, мл;
60 — молекулярный вес кремниевой кислоты.
За результат принимают среднеарифметическое значение двухпараллельных определений.
2.3.1.24 Фотоколориметрический метод определения
содержания растворимого кремнезема
Метод основан на определении содержания кремнезема, растворившегося в растворе гидроксида натрия, путем фотометрического измерения оптической плотности окрашенной в синий цвет кремнемолибденовой гетероподикислоты.
Средства контроля и вспомогательное оборудование
Фотоколориметр или спектрофотометр.
Колбы мерные по ГОСТ 1770 вместимостью 100 мл.
Пипетки по ГОСТ 29227 и ГОСТ 29228 на 1, 2 и 5 мл.
Кислота кремниевая по ГОСТ 4214.
Кислота серная концентрированная по ГОСТ 2184 плотностью1,84 г/см3.
Кислота винная по ГОСТ 5817, 28 %-ный раствор.
Натрий сернистокислый (сульфит натрия) по ГОСТ 195.
Аммоний молибденовокислый (молибдат аммония) но ГОСТ 3765.
Эйконоген.
Калий пиросернокислый по ГОСТ 7172.
Раствор молибдата аммония: 89 г молибдата аммония растворяют в 800 мл дистиллированной воды, затем медленно приливают 62 мдсерной кислоты. Раствор охлаждают до 20 0С и разбавляют дистиллированной водой до 1 л.
Раствор восстановителя: 2,4 г сульфита натрия и 0,2 г эйконогена растворяют в 70 мл дистиллирован ной воды, добавляют 14 г метабисульфита калия и разбавляют дистиллированной водой до 100 мл.
Стандартные растворы: в пять мерных колб вместимостью 100 мл наливают 0,1; 0,2; 0,4; 0,6 и 0,8 мл раствора кремниевой кислоты, содержащего 5,2 ммоль/л растворимого 8102. В каждую колбу добавляют от 70 до 80 мл дистиллированной воды и 2,5мл раствора молибдата аммония, тщательно перемешивают, через 10 мин добавляют 2,5 мл 28 %-ного раствора винной кислоты, тщательно перемешивают. Выдерживают раствор 5 мин, добавляют 2 мл раствора восстановителя и разбавляют дистиллированной водой до метки 100 мл. Определяют оптическую плотность полученных пяти растворов и строят калибровочную кривую зависимости оптической плотности от содержания SiO2 в растворе, при этом на оси абсцисс откладывают содержание SiO2 в ммоль/л, на оси ординат — оптическую плотность растворов.
Порядок проведения испытания
От фильтрата, отбирают 0,1—0,5 мл, переносят в мерную колбу вместимостью 100 мл. В колбу вливают от 70 до 80 мл дистиллированной воды и 2,5 мл раствора молибдата аммония. Содержимое колбы перемешивают. Через 10 мин в колбу добавляют 2,5 мл 28 %-ного раствора винной кислоты и снова тщательно перемешивают. Раствор выдерживают в течение 5 мин, добавляют 2 мл раствора восстановителя и разбавляют дистиллированной водой до метки 100 мл. Через 15 мин измеряют оптическую плотность раствора на фотоколориметре, применяя красный светофильтр, или на спектрофотометре при l= 815 нм в кювете толщиной 10 мм.
Содержание растворимого кремнезема в анализируемом растворе определяют по градуировочной кривой, предварительно построенной на основании результатов фотоколориметрирования стандартных растворов, или способом сравнения.
Обработка результатов испытаний
Содержание растворимого кремнезема SiO2p, ммоль/л, определяют по формуле
, (2.46)
где
С — концентрация испытываемого раствора, определенная поградуировочной кривой, ммоль/л;
V — объем анализируемого раствора, взятого для фотоколориметрирования, мл.
100 — вместимость колбы, мл.
За результат принимают среднеарифметическое значение двухпараллельных определений, если абсолютное допустимое расхождение результатов параллельных определений не превышает указанных значений.
Ускоренный метод с измерением деформаций
Метод основан на определении в установленные сроки (не более 1 мес.) относительных деформаций образцов мелкозернистого бетона, изготовленных на заполнителях, полученных из горной породы или щебня (гравия), содержащих более 50 ммоль/л растворимого кремнезема.
Средства контроля и вспомогательное оборудование
Чаша для затворения по ГОСТ 310.3.
Лопатка для перемешивания по ГОСТ 310.3.
Ванна с гидравлическим затвором по ГОСТ 310.3.
Столик встряхивающий и форма-конус по ГОСТ 310.4.
Набор стандартных сит по ГОСТ 8735.
Весы циферблатные по ГОСТ 29329 или лабораторные по ГОСТ 24104.
Электропечи сопротивления лабораторные с регулятором температуры (80±1)°С и (38±1)°С по ГОСТ 28923.
Штыковка размером 10х20х150 мм из дерева хвойных пород дляуплотнения мелкозернистой бетонной смеси.
Штангенциркуль по ГОСТ 166.
Формы для изготовления контрольных образцов бетона типа ФП по ГОСТ 22685 размерами, указанными на рисунке 2.12, и реперами, изготовленными в соответствии с рисунком 2.13 из коррозионно-стоикой нержавеющей стали по ГОСТ 5632.
Стержень контрольный для измерения деформаций длиной, равной длине образца, из коррозионно-стойкой нержавеющей стали по ГОСТ 5632.
Устройство для измерения деформаций образцов, состоящее из штатива по ГОСТ 10197 и индикатора, обеспечивающего измерение линейных размеров с точностью ±0,01 мм, по ГОСТ 577.
Емкость с крышкой размером 300х200х70 мм и два стержня размером 10х10х200 мм, изготовленные из коррозионно-стойкой нержавеющей стали по ГОСТ 5632 или винипласта по ГОСТ 9639.
Вода дистиллированная по ГОСТ 6709.
Натрия гидроокись (гидроксид натрия) по ГОСТ 4328.
Рисунок 2.12 — Форма для изготовления образцов-балочек
1 форма; 2 — боковые стенки формы; З — торцевая стенка формы; 4 — репер;
5 — стопорный винт для крепления репера; б — держатель репера
Рисунок 2.13 — Репер для испытаний
Порядок подготовки к испытанию
Пробу портландцемента марки не ниже 400 с содержанием минеральных добавок не более 5 % по массе (ПЦДО, ПЦД5) отбирают по ГОСТ 30515 и подготавливают к испытанию по ГОСТ 310.1. Портландцемент должен выдерживать испытание на равномерность изменения объема по ГОСТ 310.3.
Пробу горной породы, щебня (гравия) массой не менее 5 кг отбирают в соответствии с требованиями действующих нормативных документов. Отобранную пробу породы промывают и высушивают. Из щебня (гравия) высевают фракцию 5—10 мм, крупные фракции измельчают до фракции 5—10 мм. Методом квартования полученную пробу сокращают до З кг и вторично измельчают, просеивают через набор стандартных сит по ГОСТ 8735 и отбирают пробу массой 1000 г, при этом соотношение фракций, % по массе, должно быть:
10 — от 5 до 2,5 мм;
25—от 2,5 до 1,25 мм;
25 — от 1,25 до 0,63 мм;
25 — от 0,63 до 0,315 мм;
15 — от 0,315 до 0,16 мм.
Испытания проводят на образцах-балочках размером 25х25х254 мм изготовленных из мелкозернистых бетонных смесей состава — цемент: измельченный заполнитель в соотношении 1:2,25 по массе. Расплыв конуса при испытании на встряхивающем столике по ГОСТ 310.4 должен составить 106—115 мм. Количество воды затворения определяют предварительным подбором.
Взвешивают 440 г цемента и 900 г измельченного заполнителя. В сферическую чашу заливают всю воду затворения, высыпают взвешенный цемент, перемешивают лопаткой цемент с водой в течение30 с, добавляют взвешенный измельченный заполнитель и перемешивают смесь в течение 60 с.
Смесь оставляют на 90 с в чаще, накрыв чашу стеклом, затем еще раз перемешивают в течение 15 с. Определяют расплыв конуса. Если он меньше указанного, допускается однократное добавление воды.
Внутреннюю поверхность форм для образцов смазывают тонким слоем минерального масла, устанавливают реперы и закрепляют их стопорными винтами.
По окончании перемешивания заполняют форму с реперами бетонной смесью в два приема и отформовывают три образца. Смесь тщательно штыкуют вокруг реперов деревянной штыковкой, а затем уплотняют на встряхивающем столике 30 ударами и снимают излишки смеси металлической линейкой или ножом.
Форму с образцами закрывают стеклом на резиновых прокладках и помещают над водой в ванну с гидравлическим затвором.
Температура хранения образцов в ванне (20±5)°С. Через (24±1) ч форму извлекают из ванны и расформовывают образцы.
Порядок проведения испытания
В емкость для испытаний на расстоянии 200 мм по ширине устанавливают стержни, на которые на расстоянии не менее 15 мм друг от друга укладывают расформованные образцы. В емкость с образцами наливают дистиллированную воду так, чтобы уровень воды в емкости был не менее чем на 20 мм выше верха образцов.
Емкость с образцами и водой закрывают крышкой и на (24±1) ч помещают в электропечь с регулятором поддержания температуры(80±1)°С. Через указанное время емкость с образцами извлекают из электропечи. Образцы вынимают из емкости, помещают каждый образец в полиэтиленовый пакет для охлаждения до температуры (20±5)°С, но не менее чем на 4 ч.
Перед проведением испытания устройство для измерения деформаций необходимо отрегулировать по длине контрольного стержня. Неизменность первоначального отсчета, но индикатору проверяют установкой и измерением длины контрольного стержня перед началом, в процессе испытания и после его окончания. Отклонение в отсчете по индикатору не должно превышать ±0,01 мм. При большем отклонении следует отрегулировать устройство.
Образец, установленный в устройство для измерения деформации, поворачивают вокруг оси на один оборот и снимают начальный отсчет по индикатору. Измерение повторяют три раза. Записывают среднеарифметическое трех измерении.
Из емкости для испытаний после извлечения из нее образцов сливают дистиллированную воду и емкость заливают 1М раствором гидроксида натрия. Для приготовления раствора берут 40 г гидроксида натрия, растворяют в 900 мл дистиллированной воды и доводят объем раствора до 1 л.
Образцы укладывают в емкость для испытаний, уровень раствора гидроксида натрия над образцами должен быть на 20 мм выше верха образцов.
Емкость с образцами закрывают крышкой и на (24±1) ч помещают в электропечь с регулятором поддержания температуры (80±1)°С. По истечении указанного времени образцы извлекают из электропечи и помещают каждый образец в полиэтиленовый пакет для охлаждения до температуры (20±5)°С, но не менее чем на 4 ч. При работе с горячей щелочью используют индивидуальные средства защиты.
Величину деформации образца определяют путем измерения длины контрольного стержня и образца до и после выдержки его в растворе гидроксида натрия.
Измерения проводят ежедневно в одно и то же время суток, при этом необходимо получить одиннадцать измерений деформаций.
Обработка результатов испытания
Относительную деформацию каждого образца e, %, определяют по формуле
, (2.47)
где
— отсчет по индикатору после испытания в 1 М растворе гидроксида натрия на момент испытания t, мм;
— начальный отсчет по индикатору после испытания в дистиллированной воде, мм;
— база измерения, равная 254 мм.
Среднее относительное удлинение образцов eср определяют по формуле
, (2.48)
где
— относительная деформация первого, второго и третьего образцов.
Горная порода, щебень (гравий) считаются нереакционноспособными по отношению к щелочам, если в процессе испытаний величина деформации расширения образцов в растворе гидроксида натрия менее 0,1 %, при условии, что последний (одиннадцатый) результат испытания отличается от трех предшествующих результатов измерений не более чем на 15 %. Если деформации превышают указанные значения, то горная порода, щебень (гравий) считаются потенциально реакционноспособными со щелочами и возможность использования их в качестве заполнителей для бетона определяются испытанием образцов бетона.
Метод испытаний образцов бетона
Метод основан на определении в установленные сроки (в течение одного года) относительных деформаций образцов бетона, изготовленных на заполнителях, полученных из горной породы или щебня (гравия), содержащих растворимый кремнезем более 50 ммоль/л, портландцементе с заданным составом и природном нереакционноспособном песке с модулем крупности Мк свыше 2,0 до 2,5.
Средства контроля и вспомогательное оборудование
Средства контроля и вспомогательное оборудование со следующими дополнениями:
формы ФП размером 70х70х280 мм по ГОСТ 22685;
виброплощадка лабораторная с частотой колебаний (2900±100) колебаний/мин и амплитудой (0,5±0,05) мм;
контейнер герметичный с крышкой для испытания образцов бетона;
сита;
стержень контрольный длиной (280±1) мм из коррозионно-стойкой стали по ГОСТ 5632.
Порядок подготовки к испытанию
Пробу портландцемента марки не ниже 400 с содержанием минеральных добавок не более 5 % по массе (ПЦДО, ПЦД5) отбирают по ГОСТ 30515. Содержание прочих добавок допускается в количестве не более 1 % по массе. Портландцемент должен выдерживать испытание на равномерность изменения объема по ГОСТ 310.3. Если содержание щелочей в цементе в пересчете на Na2O менее 1,5 %, то при изготовлении бетонной смеси в воду затворения следует добавлять Na2O в количестве, обеспечивающем общее содержание щелочей 1,5 % массы цемента.
Пробы песка и исследуемого крупного заполнителя промывают и высушивают до постоянной массы. Крупный заполнитель измельчают до крупности 20 мм и просеивают. В исследуемом крупном заполнителе содержание фракций, % по массе, должно быть:
40 — для фракции св. 5 до 10 мм;
60 —»» св.10 до 20 мм.
Испытания проводят на образцах-балочках размером 70х70х280 мм.
Состав бетонной смеси для изготовления образцов-балочек назначается по массе и должен составлять 1:1,4:2,6. Подвижность бетонной смеси, определяемая осадкой конуса, не должна превышать2—4 см. Не допускается введение в воду затворения воздухововлекающих или газообразующих добавок.
Для каждого испытания готовят З образца-балочки. Перед укладкой бетонной смеси формы покрывают тонким слоем минерального масла. После смазки устанавливают реперы из нержавеющеи стали так, чтобы предупредить попадание масла на поверхность репера, и закрепляют их стопорными винтами.
Для предупреждения вытекания раствора места сопряжения поддона и боковых стенок формы должны быть покрыты смесью парафина и канифоли, взятых в соотношении 3:5 по массе, предварительно подогретой до температуры 110—120°С.
Бетонную смесь приготавливают путем перемешивания составляющих в порядке, принятом при изготовлении образцов для определения прочности бетона.
Сразу после окончания перемешивания формы заполняют бетонной смесью в два приема, тщательно укладывая ее в углах формы и вокруг реперов. Затем бетонную смесь уплотняют на виброплощадке, поверхность образца выравнивают со стенками формы, после чего формы немедленно помешают в ванну с гидравлическим затвором.
Через (48±2) ч образцы извлекают из форм и помещают над водой герметически закрывающийся контейнер. В контейнере образцы устанавливают в вертикальном положении на 2—3 см над водой таким образом, чтобы давление образца не передавалось на репер.
Контейнер с образцами помещают на (32±2) ч в электропечь с регулятором поддержания температуры (38±1)°С.
Первые измерения производят через (96±2) ч после изготовления образцов.
За (16±2) ч до первого замера контейнер переносят из электропечи в помещение для остывания до комнатной температуры.
Последующие замеры проводят ежемесячно в один и тот же день в течение 12 мес. с момента изготовления образцов. Между замерами образцы хранят в контейнере в электропечи с температурой (38±1)°С.
За (16±2) ч до очередного замера контейнер переносят из электропечи в помещение для остывания до комнатной температуры.
Обработка результатов испытания
После каждого измерения определяют относительное удлинение ei,%, каждого образца по формуле
, (2.49)
где
— длина образца, мм;
— длина контрольного стержня (280±1), мм.
Среднее относительное удлинение образцов каждого испытания определяют по формуле
, (50)
Если относительное удлинение образцов каждого испытания не превышает 0,04 %, испытание проводят в течение года, каждый раз сравнивая полученный результат с предыдущим.
Горная порода, щебень (гравий) относят к нереакционноспособным, если последнее (двенадцатое) значение относительного удлинения не превышает 0,04 %.
Если относительное удлинение превышает указанное значение, применение таких заполнителей в бетоне допускается после проведения специальных исследований с учетом условий эксплуатации сооружений и при условии проведения мероприятий, предупреждающих развитие коррозии бетона.
2.3.1.25 Определение устойчивости структуры щебня (гравия)
против распадов
Устойчивость структуры щебня (гравия) против силикатного, сульфидного и известкового видов распада определяют путем выдерживания щебня (гравия) в дистиллированной воде в течение30 сут (сульфидный и известковый распад) и последующего испытания в автоклаве в среде насыщенного водяного пара (силикатный распад).
Средства контроля и вспомогательное оборудование
Весы по ГОСТ 24104 с погрешностью взвешивания ±0,0002 г;
Шкаф сушильный;
Автоклав на 200 кПа (2 ати);
Набор сит с отверстиями диаметром 5, 10, 20 и 40 мм;
Емкость для погружения проб щебня в дистиллированную воду;
Щетка металлическая;
Мешочки из плотной ткани или формы из оцинкованной жести с круглыми отверстиями диаметром не более З мм.
Порядок подготовки к испытанию
Из лабораторных проб щебня (гравия) фракций от 5 до 10 мм, св. 10 до 20 мм и св. 20 до 40 мм отбирают аналитические пробы массой по 5 кг — для первых двух фракций, 7 кг — для третьей фракции. Пробы очищают щеткой от рыхлых частиц и пыли, промывают и высушивают до постоянной массы.
Для проведения испытания отбирают по 2 лабораторные пробы массой по 2 кг каждая для щебня (гравия) фракций от 5 до 10 мм и св. 10 до 20 мм и массой по З кг — для фракции св. 20 до 40 мм.
Порядок проведения испытания
Подготовленные пробы щебня (гравия) помешают в мешочки или формы и погружают в емкость с дистиллированной водой на 30 сут.
По истечении указанного срока пробы высушивают до постоянной массы.
Высушенные пробы помещают в формы (без мешочков) и ставят в автоклав. В течение 30 мин давление в автоклаве постепенно поднимают до 200 кПа (2 ати). При этом давлении щебень (гравий) выдерживают б ч, после чего давление в течение 20 мин постепенно снижают до атмосферного.
Пробы щебня (гравия) вынимают из автоклава, каждую в отдельности промывают, высушивают до постоянной массы, просеивают через сито с отверстиями диаметром, соответствующим нижнему размеру испытываемой фракции. Остаток на сите взвешивают.
Испытание в автоклаве может быть заменено пропариванием в сосуде с закрывающейся крышкой. Высушенную пробу помещают в сосуд над слоем воды высотой 20—30 мм. Сосуд закрывают крышкой и ставят на электроплитку. С момента закипания воды в сосуде щебень (гравий) пропаривают в течение З ч. Затем щебень (гравий) извлекают из сосуда, помещают на З ч в ванну с водой комнатной температуры. Попеременное пропаривание и охлаждение до комнатной температуры повторяют три раза. После окончания испытания пробы щебня (гравия) высушивают до постоянной массы и просеивают через сито с отверстиями диаметром, соответствующим нижнему размеру испытываемой фракции. Остаток на сите взвешивают.
Обработка результатов испытания
Потерю массы данной фракции D т, %, определяют по формуле
, (2.51)
где
т1 — масса пробы до испытания, г;
т2 — масса пробы после испытания, г.
За результат принимают среднеарифметическое двух параллельных определении.
Потерю массы D тсм,%,щебня (гравия), состоящего из смеси нескольких фракций, определяют по формуле
, (2.52)
где
п — число фракций;
D т — потеря массы данной фракции, определенная по формуле(51), % по массе;
х — содержание данной фракции, % по массе.
2.3.1.26 Определение содержания свободного волокна
асбеста в щебне из отходов асбестосодержащих пород
Содержание свободного волокна асбеста в щебне из отходов асбестосодержащих пород определяют путем отбора из пробы щебня свободных волокон асбеста.
Средства контроля и вспомогательное оборудование
Весы настольные циферблатные по ГОСТ 29329.
Сита с размером отверстий 5, 3 и 0,5 мм.
Щетка волосяная.
Пинцет.
Порядок проведения испытания
Пробу щебня массой не менее 25 кг, высушенную до постоянной массы, просеивают через сито с размером отверстий 5 мм. Материал, прошедший через сито, тщательно перемешивают, усредняют и отбирают 2 навески массой по 1000 г каждая.
Каждую навеску просеивают через сита с отверстиями З и 0,5 мм. Из остатков на ситах отбирают вручную или с помощью пинцета свободные волокна асбеста и волосяной щеткой очищают их от гали(асбестосодержащей породы). Выделенные свободные волокна асбеста объединяют и взвешивают для каждой навески отдельно.
Обработка результатов испытания
Содержание в щебне из отходов асбестосодержащих пород свободного волокна асбеста А, %, определяют по формуле
, (2.53)
где
т1 — масса отобранного волокна, г;
т — масса навески, г.
За результат принимают среднеарифметическое результатов испытании двух навесок.
2.3.1.27 Определение содержания слабых зерен и примесей металла в щебне из шлаков черной и цветной металлургии
Сущность метода заключается в выделении из щебня примесей металла и слабых зерен шлака.
Средства контроля и вспомогательное оборудование
Весы лабораторные общего назначения по ГОСТ 24104.
Шкаф сушильный.
Сита с отверстиями диаметром 5, 10, 20, 40 и 70 мм.
Магнит.
Молоток столярный типа МСТ-1 по ГОСТ 11042.
Порядок подготовки и проведения испытания
Щебень рассеивают на ситах на фракции. От каждой фракции отбирают навеску массой, указанной в таблице 2.20.
Таблица 2.20
Размер фракции, мм | 5-10 | 10-20 | 20-40 | 40-70 | св. 70 |
Масса навески, кг, не менее | 0,5 | 1,0 | 5,0 | 15,0 | 35,0 |
Проводят разборку навески каждой фракции, выделяя сначала с помощью магнита включения металла, затем слабые зерна шлакового щебня и примесей (бой огнеупорного кирпича, флюса и др.). К слабым относят зерна, легко разламывающиеся руками и разрушающиеся легким ударом молотка (предел прочности при сжатии в водонасыщенном состоянии менее 20 МПа).
Обработка результатов испытания
Выделенные из пробы слабые зерна и примеси (включения металла) взвешивают и определяют их содержание Хi, %, по формуле
, (2.54)
где
т, — масса слабых зерен и примесей (включений металла), кг;
т — общая масса навески, кг.
Содержание слабых зерен, примесей и включений металла вычисляют как среднеарифметическое результатов трех определении.
При испытании щебня, состоящего из смеси фракций, содержание слабых зерен и включений металла определяют отдельно по каждой фракции.
2.3.1.28 Определение активности шлаков
Сущность метода заключается в определении активности шлаков по значению предела прочности при сжатии образцов в водонасыщенном состоянии в возрасте 28 сут.
Средства контроля и вспомогательное оборудование
Мельница шаровая лабораторная, вибромельница или барабан с металлическими шарами.
Прибор для определения удельной поверхности типа ПСХ. Прибор малый Союздорнии для стандартного уплотнения (рисунок 14).
Пресс гидравлический с усилием от 50 до 500 кН.
Шкаф сушильный.
Мешалка лабораторная для приготовления шлакового теста. Весы лабораторные общего назначения по ГОСТ 24104 или настольные циферблатные по ГОСТ 29329.
Сито с отверстиями размером 0,071 мм по ГОСТ 6613. Чаша сферическая фарфоровая или металлическая для затворения.
Ванна с гидравлическим затвором для хранения образцов по ГОСТ 310.3.
Мастерок или лопатка для перемешивания по ГОСТ 310.3.
Рисунок 2.14 —Малый прибор Союздорнии для стандартного уплотнения
1 — рукоятка; 2— направляющий стержень; З — гиря; 4— плуижер; 5— направляющий насадный цилиндр; б — разъемный цилиндр; 7— подстаканник; 8— закрепляющие винты; 9 — металлическая пластинка
Порядок подготовки и проведения испытания
Аналитическую пробу шлакового щебня массой 5 кг высушивают до постоянной массы и размалывают в шаровой мельнице, вибромельнице или барабане с металлическими шарами так, чтобы остаток на сите с размером отверстий 0,071 мм был не более 6-10 %или удельная поверхность была равна (3000±100) см2/г. Удельная поверхность определяется в приборе ПСХ в соответствии с ГОСТ 310.3. Размолотый шлак выдерживают в воздушно-сухих условиях в течение 1 сут.
Активность шлака определяют на образцах-цилиндрах, изготовленных из шлакового теста максимальной плотности при оптимальном количестве добавляемой воды. Максимальную плотность шлакового теста устанавливают путем подбора.
Навеску размолотого шлака массой 720—750 г помешают в чашу, предварительно протертую влажной тканью, добавляют воду в количестве 6-8 %массы шлака и тщательно перемешивают мастерком в течение 5 мин. Из приготовленной смеси отбирают контрольную навеску, взвешивают, высушивают до постоянной массы при температуре (110±5)°С, охлаждают и вновь взвешивают, затем по формуле (41) определяют фактическую влажность.
Из приготовленной смеси в малом приборе Союздорнии для стандартного уплотнения формуют З образца диаметром и высотой 50 мм. Образцы уплотняют 40 ударами гири массой 2,5 кг, падающей с высоты 30 см. После уплотнения плунжер и насадку осторожно снимают, тщательно срезают ножом излишки шлакового теста. Сразу после изготовления образцы освобождают от формы и взвешивают с погрешностью до 0,1 г. Подготовку шлакового теста, изготовление серии образцов и взвешивание повторяют несколько раз, каждый раз увеличивая количество воды на 2 %. Воду прекращают добавлять после получения средней плотности образцов, значение которой закономерно снижается с каждым последующим определением.
Для определения оптимальной влажности и максимальной плотности для каждой серии образцов (различной влажности) определяют среднюю плотность образца gоб, г/см3, по формуле
, (2.55)
где
W — фактическая влажность смеси, %массы сухого молотогошлака;
— средняя плотность образцов, г/см3, определяемая по формуле
, (2.56)
где
п — число образцов;
— масса образца данной серии при данной влажности, г;
V — объем образцов, см3.
По результатам определений строят график, откладывая по оси ординат значения средней плотности образцов gоб, а по оси абсцисс — фактическую влажность. Наивысшая точка полученной кривой соответствует оптимальной влажности и максимальной плотности образцов.
Для определения прочности образцы изготавливают из шлакового теста с оптимальной влажностью и максимальной плотностью. Для этого в молотый шлак вводят воду в количестве, соответствующем оптимальной влажности и максимальной плотности, перемешивают в течение 2,5 мин в лабораторной мешалке. При отсутствии мешалки шлак с водой перемешивают мастерком или лопаткой в сферической чаше в течение 10 мин.
Из шлаковой смеси (3 кг) изготавливают по указанной выше методике при помощи малого прибора Союpдорнии для стандартного уплотнения 10 образцов-цилиндров высотой и диаметром 50 мм. Допускается уплотнять образцы на прессе при давлении 20 Мпа (200 кгс/см2), обеспечивающем плотность образца, равную плотности, получаемой на приборе стандартного уплотнения с выдержкой в течение З мин. Отклонение фактической влажности смеси от оптимальной допускается до ±0,5 %.
Образцы хранят 7 сут на воздухе при температуре (18—20)°С, после чего измеряют размеры образцов штангенциркулем, помешают их на 18 сут в камеру с влажностью не менее 95 %, затем в течение 2 сут насыщают водой комнатной температуры, при этом уровень воды над образцами должен быть не менее 2 см.
Насыщенные водой образцы испытывают в возрасте 28 сут на гидравлическом прессе, повышая давление на 0,3—0,5 МПа (3—5 кгс/см2) в секунду до разрушения образцов.
Обработка результатов испытания
Предел прочности образца sсж МПа, определяют с точностью до 0,1 МПа (1 кгс/см2) по формуле
или
, (2.57)
где
Р — разрушающее усилие пресса, Н (кгс);
F — площадь поперечного сечения образца, см2.
За показатель активности шлаков принимают предел прочности при сжатии, вычисленный как среднеарифметическое результатов испытания десяти образцов.
Примечание — Допускается определение активности производить на образцах, изготовленных из смеси с водошлаковыми отношениями 0,12; 0,14 и 0,16. из каждой смеси готовят 10 образцов.
За показатель активности в этом случае принимают наибольшее значение из трех средних пределов прочности при сжатии 10 образцов.
2.3.1.29 Определение электроизоляционных свойств
щебня для балластного слоя железнодорожного пути
Электроизоляционные свойства щебня определяют по удельной электрической проводимости насыщенного раствора, получаемого при перемешивании размельченного щебня с дистиллированной водой.
Дата добавления: 2016-01-05; просмотров: 20; Мы поможем в написании вашей работы! |
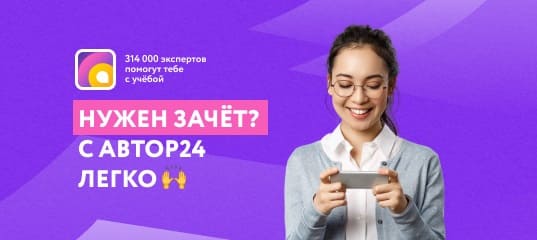
Мы поможем в написании ваших работ!