Порядок конструирования и оформления сборочного чертежа приспособления.
При выборе конструкции приспособления можно использовать источники [5], [6].
Конструирование сводится к последовательному вычерчиванию эле-ментов приспособления вокруг контура обрабатываемой детали. Рекомендуется придерживаться следующего порядка:
Контур обрабатываемой детали наносят в необходимом количестве проекций, располагаемых так, чтобы оставалось достаточно места для последующего вычерчивания элементов приспособления. Контур вычерчивают тонкими линиями. Вокруг контура вначале вычерчивают установочные элементы. Далее проектируют и вычерчивают направляющие детали (кондукторные втулки, габариты для установки фрез и т. п.) и механизмы, затем зажимные и вспомогательные элементы и механизмы. После этого определяют контуры корпуса приспособления, используя ту или иную форму стандартных заготовок корпусов. Выбранную конструкцию детали или узла приспособления сразу же вычерчивают во всех проекциях. Также вычерчивают необходимые размеры и сечения в масштабе 1:1; исключение могут составлять приспособления для особо крупных или мелких деталей. На общем виде даётся нумерация деталей и составляется спецификация.
Размеры, допуски и посадки на чертежах приспособлений.
На чертеже общего вида указываются:
1) габаритные и справочные размеры приспособления;
2) контрольные и координирующие размеры с допусками, точность которых влияет на погрешность размеров детали (расстояния между осями кондукторных втулок и т. п.);
|
|
3) размеры сопряжений с посадками, точность которых определяет расположение и условия работы отдельных механизмов приспособления.
Также на сборочном чертеже указываются технические требования.
Процесс проектирования станочного приспособления заканчивается получением комплекта конструкторской документации: сборочного чертежа, спецификации, рабочих чертежей нестандартных деталей приспособления.
5. Пример выполнения некоторых разделов курсового проекта по проектированию приспособления для обработки детали «кронштейн»
5.1. Пример выполнения общего раздела
5.1.1. Описание конструкции детали и операции механической обработки
Обрабатываемая деталь называется кронштейн и может использоваться в качестве опоры скольжения. Заготовкой является отливка из серого чугуна марки СЧ18. Исходя из годовой программы выпуска 5000 шт. принимается крупносерийное производство.
В крупносерийном производстве отливки получают литьем в многоразовые формы. Для крепления кронштейна на каком-либо основании служат два сквозных отверстия Ø 16 мм. Для установки вкладыша по посадке в системе отверстия опоры скольжения, в кронштейне предусмотрено отверстие Ø 40 Н7. Все конструктивные элементы и размеры детали указаны на чертеже кронштейна.
|
|
Чтобы получить отверстие диаметром 40 мм по 7-му квалитету точности, необходимо осуществить черновое, чистовое растачивание, обеспечив 14-й квалитет точности и шероховатость обработанной поверхности Ra 0,8 – 3,2 мкм.
Окончательная обработка отверстия (тонкое растачивание) обеспечит 7-й квалитет точности и шероховатость Ra 0,4 – 0,8 мкм.
Для осуществления всех трех операций растачивания отверстия в условиях крупносерийного производства необходимо применение трех станков. Так как кронштейн относится к классу корпусных деталей, при этом необходимо выдержать допуск 0,08 мм размера 60 мм, который определяет расположение оси отверстия Ø 40 Н7, то для чернового, чистового и тонкого растачивания отверстия лучше будет выбрать горизотально-расточной станок модели 2М614.
Техническая характеристика горизонтально-расточного
станка мод. 2М614
диаметр шпинделя в мм – | |
размеры рабочей поверхности стола в мм – | 800 × 1000 |
наибольший вес обрабатываемой детали в кг – | |
расстояние от оси шпинделя до поверхности стола в мм: наименьшее – наибольшее – | |
число скоростей вращения шпинделя – | |
предел чисел оборотов шпинделя в минуту – | 20–1000 |
предел величин продольных подач шпиндельной бабки на один оборот шпинделя в мм/об – | 0,025–8 |
Мощность главного электродвигателя в кВт – | 6,5–7 |
На этом станке можно осуществлять черновое, чистовое и тонкое растачивание закрепленным в расточной оправке твердосплавным резцом. Кинематика станка состоит из цепей главного движения, движения подачи, цепи ускоренных перемещений стола и цепи вертикального установочного перемещения шпиндельной бабки.
|
|
5.1.2. Разработка схемы базирования
Для операции растачивания отверстия в рассматриваемой детали в условиях крупносерийного производства лучше всего применить схему полного базирования. В данном случае схема полного базирования будет заключаться в установке кронштейна на опорную плоскость и на два пальца через цилиндрические сквозные отверстия, выполненные на этой плоскости. Здесь деталь лишается всех шести степеней свободы, а получение точности размера 60±0,04 мм, определяющего расположение обрабатываемого отверстия, будет автоматически получаться на заранее настроенном станке. Опорная плоскость кронштейна будет являться главной базирующей поверхностью, лишая при этом деталь трех степеней свободы. Эта же поверхность является конструктивной (или измерительной). По одному отверстию кронштейн будет устанавливаться на короткий цилиндрический палец, что позволяет лишить деталь дополнительно двух степеней свободы.
|
|
Вторым отверстием кронштейн будет устанавливаться на срезанный ромбический палец и деталь лишится в этом случае последней степени свободы.
Далее приводится рис 7. схемы базирования детали с указанием баз.
Рис. 7. Схема базирования кронштейна
5.1.3. Выбор типа приспособления и описание принципа его работы.
Для операции растачивания кронштейна в условиях крупносерийного производства лучше применять неразборное специальное приспособление. Этот тип приспособления проектируется и собирается из стандартных деталей и узлов. Конструкция неразборного специального приспособления будет содержать лишь небольшую часть специальных сменных наладок, которые будут заменяться при изменении конструкции обрабатываемой детали.
Заготовка устанавливается на цилиндрический палец и срезанный ромбический палец. Включается пневмоцилиндр, шток которого подвижно соединен с планкой, которая прижимает обрабатываемую деталь. Эта планка другим концом закреплена в опоре. После обработки воздух подается в другую полость пневмоцилиндра, и планка отходит от кронштейна, после чего обработанная заготовка снимается и устанавливается другая.
Приводится схема приспособления для заданной операции (рис. 8).
Рис. 8. Схема приспособления
Специальный раздел
5.2.1. Расчет погрешности базирования
Так как конструкторская база совпадает с технологической, то погрешность базирования будет равна нулю.
При установке детали по плоскости и двум отверстиям необходимо выполнить расчеты, связанные с установкой на пальцы.
Определяем наибольший зазор в соединении отверстия кронштейна Ø 16 Н9 (+0,043) с пальцем Ø 16 f 9 по формуле:
,
где = 16,043 – наибольший предельный диаметр отверстия заготовки;
= 15,941 – наименьший предельный диаметр пальца.
мм.
Наибольшее угловое смещение определим по формуле:
,
где L = 100 мм – межцентровое расстояние; – максимальный зазор в соединениях цилиндрического и срезанного пальцев с отверстиями кронштейна;
Возможный перекос кронштейна при установке на цилиндрический и срезанный пальцы составит 0,102 мм на длине 100 мм. Наибольшая угловая погрешность составит α = 0,058о.
5.2.2. Разработка схемы силового замыкания заготовки
в приспособлении
В качестве привода приспособления в условиях крупносерийного производства лучше взять пневмоцилиндр, работающий от общей пневмосети. При этом возможно значительное снижение вспомогательного времени, снижение утомляемости рабочего, а значит увеличение производительности и снижение себестоимости продукции.
В процессе обработки отверстия на кронштейн действует момент М силы резания, из-за чего заготовка стремится опрокинуться за счет плеч l1 и l2, тянущее усилие Qтян . на штоке пневмоцилиндра преобразуется в силу W зажатия заготовки, которая определяется по формуле:
где = 0,95 – коэффициент полезного действия. При этом сила W зажатия по значению должна быть такой, чтобы возможно было удержание заготовки от опрокидывания (рис. 9).
Рис. 9. Схема силового замыкания заготовки в приспособлении
Далее рассчитывается усилие резания на данной операции.
5.2.3. Расчет усилия зажима заготовки в приспособлении
Усилие, развиваемое прихватом, превышает составляющую Pz силы резания, поэтому тянущее усилие на штоке пневмоцилиндра можно определить по формуле:
,
где – плечи прихвата принимаем равными по 100 мм.
Н.
Исходя из формулы:
.
Определяем разность квадратов диаметров пневмоцилиндра и его штока
,
где р = 0,4 МПа – давление подачи сжатого воздуха в полость цилиндра.
мм2.
Принимаем диаметр цилиндра D = 50 мм, тогда диаметр штока будет равен:
мм.
По [1] принимаем пневмоцилиндр D = 50 мм, d = 16 мм.
Проверяем тянущее усилие на штоке пневмоцилиндра по формуле:
;
Сравниваем рассчитанное усилие зажима с силой резания на данной операции.
Уточненное усилие на штоке выше требуемого 669,4 > 636,75.
Следовательно, данный пневмоцилиндр подходит для зажатия заготовки.
5.2.4. Расчет экономической эффективности приспособлений
Эффективность применения того или иного приспособления определяется исходя из неравенства:
,
где Э – годовая экономия; Р – годовые затраты на приспособление
,
где q = 5000 шт. – годовая программа выпуска кронштейна; Тшт = 1,5 мин. – штучное время обработки кронштейна без приспособления; = 0,8 мин. – штучное время обработки с использованием приспособления;
= 0,17 руб/мин. – стоимость одной станко-минуты (приложение).
руб.
Годовые затраты на приспособление определяем из формулы:
,
где С – стоимость специального приспособления в зависимости от группы по сложности.
,
где q = 26 – количество деталей; k = 30 – стоимость одной детали (приложение)
;
руб.
Годовая экономия Э больше годовых затрат Р на приспособление 595 > 468, а потому можно сделать вывод, что внедрение данного приспособления экономически оправдано.
Приложения
Приложение 1
Себестоимость станко-минуты в руб./мин.
Виды работы | Составляющие себестоимости станкоминуты | Разряд работы | ||||
I | II | III | IV | V | ||
Токарные | апер | 0,0077 | 0,0087 | 0,0100 | 0,0115 | 0,0133 |
ап.п. | 0,0030 | 0,0030 | 0,0030 | 0,0030 | 0,0030 | |
апост | 0,0020 | 0,0023 | 0,0026 | 0,0030 | 0,0035 | |
ам | 0,0130 | 0,0140 | 0,0160 | 0,0170 | 0,0200 | |
Фрезерные | апер | 0,0077 | 0,0087 | 0,0100 | 0,0115 | 0,0133 |
ап.п. | 0,0034 | 0,0034 | 0,0034 | 0,0034 | 0,0034 | |
апост | 0,0020 | 0,0023 | 0,0026 | 0,0030 | 0,0035 | |
ам | 0,0130 | 0,0140 | 0,0160 | 0,0180 | 0,0200 | |
Сверлильные | апер | 0,0077 | 0,0087 | 0,0100 | 0,0115 | 0,0133 |
ап.п. | 0,0013 | 0,0013 | 0,0013 | 0,0013 | 0,0013 | |
апост | 0,0020 | 0,0023 | 0,0026 | 0,0030 | 0,0035 | |
ам | 0,0110 | 0,0120 | 0,0130 | 0,0150 | 0,0180 | |
Шлифовальные | апер | 0,0077 | 0,0087 | 0,0100 | 0,0115 | 0,0133 |
ап.п. | 0,0032 | 0,0032 | 0,0032 | 0,0032 | 0,0032 | |
апост | 0,0020 | 0,0023 | 0,0026 | 0,0030 | 0,0035 | |
ам | 0,0130 | 0,0140 | 0,0160 | 0,0180 | 0,0200 |
Приложение 2
Дата добавления: 2016-01-05; просмотров: 15; Мы поможем в написании вашей работы! |
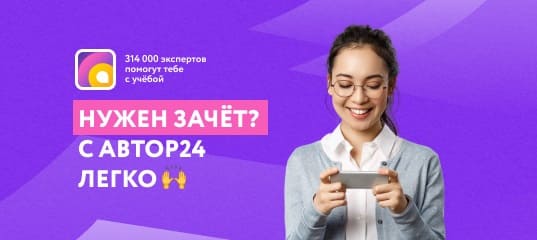
Мы поможем в написании ваших работ!