Пример выполнения пояснительной записки
ВВЕДЕНИЕ
Станочные приспособления являются одними из основных элементов оснащения металлообрабатывающего производства, позволяющих эффективно использовать в производственном процессе станки общего назначения. Применение приспособлений даёт возможность специализировать и настраивать станки на заданные процессы обработки, обеспечивающие выполнение технологических требований и экономически рентабельную производительность.
Приспособления с механизированным управлением во многих случаях позволяют автоматизировать процессы закрепления и освобождения деталей, что во многом приближает станки с такими приспособлениями к условиям работы специализированного оборудования.
Применение приспособлений позволяет:
- устранить разметку заготовок перед обработкой, повысить ее точность;
- увеличить производительность труда на операции;
- снизить себестоимость продукции;
- облегчить условия работы и обеспечить ее безопасность;
- расширить технологические возможности оборудования;
- организовать многостаночное обслуживание;
- применить технически обоснованные нормы времени и сократить число рабочих, необходимых для выпуска продукции.
Повышение производительности обработки в значительной степени обусловлено внедрением механизации и автоматизации технологических процессов, оснащением производства специальными и переналаживаемыми приспособлениями.
|
|
1. ОПИСАНИЕ РАБОТЫ ПРИСПОСОБЛЕНИЯ
Специализированное наладочное приспособление для фрезерования деталей типа валов.
При использовании этого приспособления, обрабатываемая деталь – валик устанавливается на призмы, которые прикреплены к основанию с помощью штифтов и винтов. Ступенью валик упирается в торец призмы, для компенсации горизонтальных нагрузок, возникающих в процессе обработки. Также к основанию прикреплёна диафрагменная камера. Шток жёстко прикреплён к диафрагменной пластине, которая в свою очередь с помощью диафрагмы при подаче воздуха движется вверх, вниз.
При запуске воздуха в полость А диафрагма поднимает шток верх, который упирается в прихват, осуществляя зажим заготовки.
При запуске воздуха в полость Б диафрагма опускает шток вниз и тем самым происходит освобождение заготовки.
В целом приспособление центрируется на столе станка с помощью шпонок и крепится к столу болтами.
Данное приспособление средне простое, надёжное и обеспечивает зажим заготовки с необходимым усилием.
2. Выбор схемы базирования ЗАГОТОВКИ
При выборе схемы базирования детали следует учитывать направления и величины сил возникающих в процессе обработки, в зависимости от её вида. К таковым относятся: осевые силы и крутящие моменты.
|
|
Т.к. в данном случае производится фрезерование шпоночной фрезой за один проход, то возникают следующие силы:
· Ру – усилие возникающее при врезании фрезы;
· Рz – усилие продольной подачи или сила резания;
· Мz – крутящий момент фрезы.
Для компенсации возникающих усилий, с учётом правила «Шести точек» выбираем схему базирования – установка в призмах с упором в торец шейки большего диаметра.
Рисунок 1 - Схема базирования
3. Расчёт погрешности базирования ЗАГОТОВКИ
Т.к. положение базы – вдоль оси детали и применяется упор в торец, то погрешность базирования будет равна:
Погрешность базирования меньше величины допуска размера, значит базирование выбрано верно.
4. Расчёт усилия закрепления заготовки
где Pz – сила резания;
Kзап – коэффициент запаса;
К0=1,5 К1=1,3
К2=1,0 К4=1,0
![]() | Сp=82,5 х=0,95 y=0,8 q=1,1 w=0 u=1,1 | t=4 z=2 Sz=0,022 B=8 D=8 n=1,1 |
![]() |
5. РАСЧЁТ ОСНОВНЫХ ПАРАМЕТРОВ ЗАЖИМНОГО МЕХАНИЗМА
Расчёт диаметра пневмоцилиндра.
где WП – усилие зажима,
р – давление сжатого воздуха,
η – коэффициент полезного
|
|
действия, учитывающий потери в
пневмоцилиндре.
Принимаем стандартный диаметр пневмоцилиндра Dц=45 мм.
Расчёт действительной силы зажима.
Длина хода штока у камер с тарельчатыми диафрагмами составляет 20-22 % от внутреннего диаметра диафрагмы.
Время срабатывания диафрагменного пневмоцилиндра.
где VB=1500…2500 см/с, VB=15000 мм/с – скорость воздуха в магистрали,
do=6 мм – диаметр воздухопровода,
dд=0,7∙ 45 =0,7∙45=31,5 мм – диаметр диска.
6. ПРОЧНОСТНОЙ РАСЧЁТ ДЕТАЛЕЙ
6.1 Расчёт детали ось на срез:
, где Q = 599 Н - сила, действующая на ось;
Sср - площадь сечения круга;
Z – количество плоскостей среза.
Площадь среза:
, где d =14 мм - диаметр оси;
118 МПа - допустимое напряжение при
срезе для материала - Сталь 40Х
Исходя из полученной величины, делаем вывод, что деталь достаточно прочна, для работы в данных условиях.
6.2 Расчёт болтов, крепящих опору к основанию, на разрыв.
где: F - действующая сила, Н;
Sр - площадь min сечения болта, мм;
z = 2 - количество болтов
для материала - Ст.3
F = D * где D - усилие пневмоцилиндра, Н;
L - расстояние между точками прижима
детали и упора штока, мм;
l - расстояние между точкой прижима
детали и центром оси, мм.
|
|
П = где d - минимальный диаметр болта, мм
t = = = 15,26 МПа
Исходя из полученной величины, делаем вывод, что крепёжные элементы достаточно прочны, для работы при данных нагрузках.
7. ТРЕБОВАНИЯ БЕЗОПАСНОСТИ ПРИ РАБОТЕ С ПРИСПОСОБЛЕНИЕМ
1. Перед началом работы проверить надёжность закрепления приспособления на столе станка и затяжку резьбовых соединений.
2. Строго воспрещается производить ремонт и техническое обслуживание приспособления на работающих станках.
3.. Запрещается производить ремонт и обслуживание приспособления без отключения сжатого воздуха.
4. Запрещается, в процессе работы и по её окончанию, производить обдув приспособления сжатым воздухом.
5. По окончанию работы, приспособление необходимо очистить от стружки и обтереть сухой ветошью.
Дата добавления: 2016-01-05; просмотров: 10; Мы поможем в написании вашей работы! |
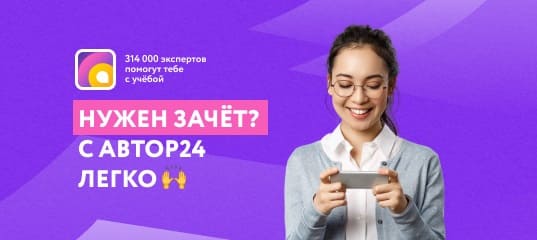
Мы поможем в написании ваших работ!