Материалы из каменных, шлаковых расплавов, ситаллы, шлакоситаллы.
Каменным литьем принято называть сравнительно новый вид промышленного производства каменных изделий обладающих определенной формой и изготовленных путей кристаллизации расплавленных горных пород, искусственных смесей и шлаков.
Материалы из каменного расплава обладают высокой прочностью, износостойкостью и стойкостью в химически агрессивных средах. Это позволяет применять изделия для облицовки технологических аппаратов и узлов, работающих в наиболее тяжелых условиях, заменяя другие дорогостоящие материалы, в частности металлы.
Сырьем для получения каменного литья служат горные порода магматического происхождения, преимущественно базальты и диабазы, обладающее пониженной вязкостью в расплавах. По химическому составу базальты более постоянны, и каменное литье из вех обладает высокой химической стойкостью и прочностью на истирание. Температура плавления их 1100-1450°С. Расплав базальта обладает хорошими литейными качествами и кристаллизуется в течение 5-15 мин.
Температура, при которой расплавленный базальт превращается в твердое вещество, называется температурой замерзания или температурой кристаллизации. Обратное превращение вещества из твердого (кристаллического) состояния в жидкое, т.е. расплав, совершается тоже при строго определенной температуре, называемой температурой плавления. При постоянном давлении температура плавления и температура замерзания веществ определенного химического состава тождественны.
В качестве сырья для получения светлого каменного литья используют кварцевый песок (45%), доломит (34%), мел иди мрамор (21%). Кроме основных материалов, в шихту для снижения температуры плавления добавляют плавиковый шпат (3%), а для отбеливания расплава – окись цинка (0,8%). Перед загрузкой в печь сырьевые материалы измельчают, просеивают и дозируют в заданном соотношении.
Для плавки шихты используют шахтные, ванные, вращающиеся и электрические печи. Наиболее распространены ванные печи. Базальтовую шихту в ванных печах плавят при температуре 1450°С, Готовый расплав из ванны стекает в разливочный копильник, где охлаждается до 1250°С.
Характерная особенность жидкого состояния расплава заключается в том, что составляющие его частицы – ионы, атомы и молекулы находятся непрерывно в сложно-хаотическом – броуновском движении. С понижением температуры кинетическая энергия частиц уменьшается и движение их постепенно замедляется до тех пор, пока они утратят способность перемещаться в пространстве друг относительно друга. В таком состоянии конечное взаимное расположение этих частиц может быть упорядоченным, т.е. кристаллическим или беспорядочным – стекловидным.
Регулируя температурные условия охлаждения расплава во времени, получают изделия каменного литья сой или иной степени кристаллизации. Если же медленно кристаллизующийся расплав подвергнуть быстрому охлаждению, он не закристаллизуется и превратится в стекло. Таким образом, основная сущность получения изделий каменного литья заключается в том, чтобы залитый в форму расплав закристаллизовать, подвергая его правильной температурной обработке. Охлаждение расплава перед разливкой благоприятно оказывается на структуре отливаемых изделий и уменьшает число усадочных дефектов (трещин, раковин).
Для литья изделий применяют формы (кокили) из чугуна или жароупорной стали (постоянные формы), из силикатных материалов (временные формы) и земляные (одноразовые формы). Для уменьшения внутренних напряжений, возникающих при охлаждении, отливки подвергаются кристаллизации и отжигу. Степень кристаллизации расплава изменяется в зависимости от свойств расплава и размеров изделий. Кристаллизация и отжиг проводят в специальных печах (муфельных, туннельных, камерных) при температуре 800-900°С, затем изделия перемещают в зону отжига, а откуда на склад готовой продукции. Технические свойства различных видов каменного литья по некоторым показателям во много раз превышают свойства естественных камней магматического происхождения.
Изделия из каменного литья обладают следующими физико-техническими свойствами:
– плотность 2900-3000 кг/м3;
– предел прочности при сжатии 300-400 МПа, в отдельных случаях 1000 и даже 2000 МПа
при изгибе – 60-65 МПа;
– потери при истирании – 0,05-0,06 г/см2;
– химическая стойкость – 99,0-99,8%;
– твердость 7-8 и выше;
– коэффициент теплопроводности – 0,85.
Каменное литье обладает высокими электроизоляционными свойствами, отдельные виды его огнеупорны, стекло- и щлакоустойчивы. Стойкость изделий каменного литья по отношению к корродирующему воздействию растворов солей, кислот и оснований ставит его на первое место среди известных в настоящее время химически стойких материалов.
Благодаря высоким техническим свойствам область применения изделий каменного литья с каждым годом расширяется. Каменное литье широко используется в угольной, горно-обогатительной и металлургической промышленности для футеровки бункеров, течек, корпусов флотационных машин и т.д. Каменное литье широко используется в химической промышленности для кладки и футеровки кислотовместилищ, реактивных ванн, химически стойких аппаратов и сосудов, трубопроводов, желобов и т.д. Плитки из каменного литья с успехом заменяют металл; их используют для полов в цехах с агрессивными средами и для футеровки аппаратов, подверженных сильному истирающему воздействию.
Стойкость каменного литья по отношению к атмосферным реагентам делает его незаменимым материалом для художественно-декоративной отделки зданий и сооружений. Из него изготовляют дорожные знаки, скульптуры, архитектурные украшения и т.д.
Цвет и окраска изделий каменного литья зависит от химического состава отливки. Такие красящие окислы, как Fe2O3, TiO2, MnO2, Cr2O3 и другие, окрашивают изделия в темные и даже черные цвета. Отсутствие этих окислов дает возможность получать светлоокрашенные даже относительно белые изделия.
Стоимость каменного литья, особенно светлого, сравнительно высока. Однако, если отнести стоимость изделий к сроку их службы, то применение каменного литья оказывается экономически выгодный.
|
|
|
|
|
|
|
|
Материалы из каменного расплава обладают высокой прочностью, износостойкостью и стойкостью в химических агрессивных средах. Используются для облицовки технологических аппаратов, работающих в наиболее тяжелых условиях, за менее дорогостоящие материалы (металлы).
Сырьем для каменного литья служат горные породы магматического происхождения, преимущественно является базальты и диабазы tплавл. = 1100-1450 оC.
Расплав базальта обладает хорошими литейными качествами и кристаллизуется в течение 5-15 мин.
В качестве сырья для светлого каменного литья используется кварцевый песок (45%), доломит (34%), мел или мрамор (21%).
Для литья изделий используется формы из чугуна или жароупорной стали (постоянные), из силикатных материалов (временные), земляные (одноразовые формы). Кристаллизация плюс отжиг в специальных печах.
Используются для футеровки бункеров, течек, корпусов машин, плитки из каменного литья – полы в цехах с агрессивными средами и т.д.
Материалы и изделия из шлаковых расплавов разновидность изделий, получаемых из расплавов горных пород. Используются для покрытия полов промышленных предприятий в виде облицовочных плиток, в виде шлаковой пемзу, ваты и т.д.
Шлаковая пемза - ячеистый материал, получаемый в результате вспучивания расплавленного шлака при быстром его охлаждении.
Центробежный способ – расплавленный шлак под действием вращающейся крыльчатки распыляется, вспучивается парами воды и под действием центробежной силы отбрасывается на охлаждающий экран – приемный бункер – конвейер для удаления готового продукта.
= 300 – 1100 кг/м3
заполнитель для легких бетонов
В каскадных лотках - струя шлакового расплава с полки на полку оказывается между двумя струями воды, которая испаряется и вспучивает расплав.
Шлаковая вата – материал состоящий из тончайших волокон, получаемых из расплавленных огненно-жидких доменных шлаков.
Технологический процесс заключается в следующем:
- в печь загружается доменный шлак соответственного состава и определенной крупности ( 50 – 70мм) и топливо (кокс, антрацит, древесный уголь);
- при t = 1200 – 1400 оС образуется шлаковый расплав;
- при вытекании из печи раздувается струе пара и осаждается в виде тонких нитей на конвейер;
- перемещение в камеру охлаждения;
- изготовление матов. (слои ваты выравнивают оклеивают бумагой или картоном, режут на куски заданной величины).
= 250 – 300 кг/м3
Ситаллы, шлакоситаллы (стекло и кристаллы) – материал из стекла тонкокристаллической структуры, плотный, вязкий, прочный, твердый, разной окраски от черной, желтой до белой. Это новый перспективный строительный материал, получаемый на основе регулируемого процесса микрокристаллизации расплава малощелочного стекла (строительные ситаллы) или расплава металлургического, доменного шлака (шлакоситаллы).
От стекла ситаллы отличаются тонкокристаллической структурой при содержании кристаллической фазы до 95%, что придает им исключительно высокие показатели механических свойств и стойкость к термическим воздействиям.
Технология производства ситаллов заключается в том, что в расплав стекла определенного химического состава вводят катализаторы кристаллизации (зародышеобразователи), например, фторида, фосфаты и формуют изделия необходимой формы, которые подвергаются термической обработке вначале при 700°С, а затем при 900-1100°С без размягчения или деформаций изделий.
По исходному сырью ситаллы делят на стеклоситаллы (из расплава стекла); петроситаллы (из расплава горных пород); шлакоситаллы (из расплава металлургических шлаков).
Ситаллы имеют объемную массу 2500-2600 кг/м3, предел прочности при сжатии до 600 МПа, при изгибе до 140 МПа, температуру размягчения 1000-1350°С, твердость больше стекла; кислото- и щелочеустойчивы, водонепроницаемы; ситаллы выпускаются листами с размером по длине 500-3000, по ширине - 500-1500, по толщине 5-25 мм, и плитами 250?250?(10-20) мм.
Как износостойкий материал, ситаллы применяют в приборо- и машиностроении, в строительстве, для футеровки мельниц, стальных бункеров, желобов, лотков сыпучих материалов м др., для кровельных покрытий отапливаемых и неотапливаемых промышленных зданий для любых полов и облицовки строительных конструкций, подверженных химической агрессии или абразивному износу.
Стеклянное волокно получают из расплавленного стекла в виде тонких нитей разного диаметра и длины. Прочность волокна, зависящая от диаметра нити, в 2-2,5 раза больше прочности штапельного волокна и характеризуется большой химической устойчивостью. Стеклянное волокно вырабатывается из обычного или специального по составу щелочноалюмосиликатного или малощелочного алюмоборосиликатного расплава стекла. Из стеклянного волокна d=5-7 мм изготавливают стекловату, стекломаты и другие звуко- и теплоизоляционные материалы. Из стеклянного волокна производят плиты, рулонный материалы, стеклоткани, которые обрабатывают синтетическими смолами без или с введением необходимых пигментов. Стеклопластики применяют как кровельный, гидроизоляционный и конструктивный материал.
Ситаллы – стеклокристаллические материалы, получаемые из стекла в результате его полной или частичной кристаллизации.
Ситаллы могут быть темного, коричневого, серого, кремового цвета, глухие и прозрачные.
Материалы обладают большой прочностью R = 500 МПа и высокой стойкостью к химическим и тепловым воздействиям.
- получают прокаткой, прессованием, вытягиванием стеклянных расплавов с соединениями фторидов, фосфатов щелочных и щелочноземельных металлов.
- применяют в виде конструкционного и отделочного материала.
Шлакоситаллы - плотные мелкозернистые металлы, представляющие собой затвердевший раствор металлургических шлаков со специальными добавками.
- для наружной и внутренней облицовки зданий, покрытий полов, в дорожном строительстве в виде листов и плит квадратной и прямоугольной формы.
l – 3000 мм b – 1500 мм, t – 6 - 15 мм
Rсж = 60-90 МПа кислотостойкость - 99,2 – 99,9 %
Rизг = 9-13 МПа щелочестойкость -73 – 82 %
= 2600 – 2750 кг/м
И = 0,015 – 0,03 г/см
Лицевая поверхность белого, черного, темно-серого цвета с полированной фактурой, цвет может регулироваться путем нанесения силикатных красок, которые закрепляются при термообработке.
Дата добавления: 2016-01-04; просмотров: 42; Мы поможем в написании вашей работы! |
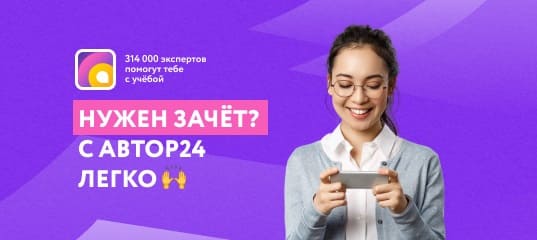
Мы поможем в написании ваших работ!