РЕМОНТ УЗЛОВ СИСТЕМЫ ОХЛАЖДЕНИЯ
Прочитайте внимательно текст, выпишите в тетрадь способы ремонта деталей систем и решите тест, работу выполнить до 11.02.22г
Тема Ремонт системы смазки и системы охлаждения
Вопросы:
РЕМОНТ УЗЛОВ СМАЗОЧНОЙ СИСТЕМЫ
РЕМОНТ УЗЛОВ СИСТЕМЫ ОХЛАЖДЕНИЯ
Ремонт масляного насоса.
Надежность двигателя во многом зависит от исправности узлов системы смазки и качества применяемых масел.
Характерные неисправности системы смазки:
- износ деталей масляного насоса и фильтров,
- нарушение регулировок клапанов,
- потеря герметичности узлов,
- загрязнение системы.
Ремонт масляного насоса. Техническое состояние масляного насоса характеризуется его производительностью при номинальной частоте вращений ведущего валика и рабочем давлении, а также давлением открытия предохранительного клапана.
Определение износов. Перед проверкой и ремонтом масляного насоса его промывают и осматривают снаружи. При осмотре определяют износ валиков, втулок и обнаруживают другие повреждения. Затем насос испытывают на стенде на производительность и давление открытия предохранительного клапана.
Вязкость масла при этом должна быть такой же, как и при испытании насоса после ремонта, и соответствовать вязкости картерного масла у прогретого двигателя.
По результатам испытаний судят о необходимости ремонта насоса.
В случае необходимости разбирают насос, моют его детали и выявляют дефекты и износ.
|
|
У корпуса масляного насоса изнашиваются поверхности в местах сопряжения с торцами шестерен и стенки гнезд в местах сопряжения с вершинами зубьев шестерен, места посадки втулки ведущего валика и пальца ведомой шестерни. Кроме того, изнашивается гнездо предохранительного клапана, повреждается резьба, образуются трещины.
При износе корпуса резко снижается производительность насоса.
Износ деталей предохранительного клапана приводит к нарушению его герметичности и снижению давления открытия.
У ведущей и ведомой шестерен насоса изнашиваются торцы и зубья по высоте и толщине. При износе шестерен по торцам и зубьев по высоте уменьшается производительность масляного насоса. На производительность масляного насоса износ зубьев толщине не оказывает существенного влияния. Износ наружной поверхности втулок насоса приводит ослаблению их посадки в корпусе, крышке и ведомой шестерне, а износ внутренней поверхности — к увеличению зазора между втулками, ведущим валиком и пальцем ведомой стерни.
Несвоевременное устранение этой неисправности может быть причиной аварийного износа гнезд корпуса и выхода насоса из строя. Палец ведомой шестерни изнашивается в местах сопряжения корпусом и втулкой ведомой шестерни.
|
|
Ведущий валик масляного насоса изнашивается в местах сопряжения со втулками. При несвоевременном устранении этого износа резко увеличивается зазор и быстро изнашиваются корпус и шестерни. У валика изнашиваются также шлицы или шпоночные канавки.
На поверхностях предохранительных клапанов во время эксплуатации появляются риски, задиры, местные износы, вследствие чего нарушается герметичность клапана. Отложение на клапане смолистых веществ приводит к его залеганию.
На клапанах шарикового типа появляются кольцевые выбоины риски. Витки пружины клапанов при длительной работе стираются, что приводит к потере ими упругости, а иногда и к поломке.
Устранение износов. Износ поверхности корпуса, сопрягаемой с крышкой, устраняют шлифовкой или припиливанием с последующим шабрением.
Неплоскостность торцовой поверхности измеряют при помощи иглы и щупа.
Утопание нагнетательных шестерен относительно торцовой верхности корпуса измеряют при помощи линейки и щупа.
Наибольшую трудность представляет восстановление изношенных колодцев корпуса насоса. Колодцы восстанавливают меднением, мелированием, наплавкой меди или латуни, эпоксидными смолами, также расточкой гнезд с последующей запрессовкой вкладышей. Расточка гнезд с последующей постановкой вкладышей наиболее простой способ восстановления корпуса.
|
|
.Изношенные отверстия под втулку валика и палец шестерни развертывают и в них запрессовывают втулку увеличенного размера.
Посадочное место шариковых клапанов восстанавливают зенкованием до выведения следов износа с последующей осадкой шарика по гнезду.
Изношенные клапаны плунжерного типа восстанавливают притиркой.
Трещины, обнаруженные в корпусе, заваривают сваркой или запаивают твердыми припоями.
Крышку масляного насоса с изношенной торцовой поверхностью шлифуют или припиливают и затем шабрят. Отверстие под втулку развертывают и в него запрессовывают втулку увеличенного размера.
Втулки с изношенной наружной поверхностью восстанавливают осадкой в корпусе или крышке. При износе внутренней поверхности втулки обычно выбраковывают.
Изношенные пальцы и валики восстанавливают наплавкой с последующими проточкой и шлифованием шеек, а также фрезерованием шлицев.
У маслоприемника насоса может быть оборвана и повреждена сетка, а также нарушена плотность соединения его с корпусом масляного насоса.
|
|
Порванные места сетки запаивают. При этом общая площадь запайки не должна превышать 10%.
У привода масляного насоса изнашиваются втулки кронштейнов, валики и соединительные муфты. Изношенные детали восстанавливают обычными способами.
Обкатка и испытание. Отремонтированный масляный насос обкатывают, испытывают и регулируют на специальных стендах.
В процессе обкатки насоса не должно быть постороннего шума, перегрева деталей, просачивания масла в местах соединений и через предохранительный клапан. После обкатки регулируют предохранительный клапан.
По окончании ремонта масляного, насоса проверяют его на производительность при нормальной частоте вращения и определенном противодавлении в соответствии с техническими условиями.
Масляные насосы большинства автомобильных двигателей испытывают только на развиваемое давление.
Ремонт масляных фильтров.
Качество очистки масла от продуктов износа и других примесей зависит от состояния масляных фильтров.
Основные неисправности. Масляные фильтры после разборки промывают и дефектуют.
У фильтров двигателей с центробежной очисткой масла могут быть следующие неисправности: износы шеек ротора и втулок, а также износ и забивание отверстий форсунок (сопл) и защитных сеток на заборных трубках ротора центрифуги (в этом случае ухудшается герметичность ротора и снижается частота вращения его, вплоть до остановки); износ клапанов, резьб, появление трещин па корпусе фильтра, деформация колпаков, повреждение прокладок, что приводит к нарушению регулировок клапанов фильтра и подтеканию масла.
Восстановление деталей. При износе оси ротора центрифуги и втулок ось шлифуют до выведения следов износа. В в корпус ротора запрессовывают втулки ремонтных размеров.
При тугом вращении или заедании корпуса ротора допускается пришабривание втулок.
После запрессовки втулок их обрабатывают одновременно специальной комбинированной разверткой. В случае образования трещин и при обломах корпус и крышку ротора центрифуги выбраковывают.
Сопловые отверстия прочищают медной проволокой и проверяют на пропускную способность при помощи прибора для тарировки жиклеров карбюратора.
Трещины в корпусе фильтра заваривают биметаллическим электродом. Повреждения гнезд клапанов и пружин устраняют так же, как и повреждения предохранительного клапана масляного насоса.
Погнутые стальные колпаки фильтров выправляют, а трещины на горловине запаивают твердыми припоями.
Контроль. После сборки центрифуги на стенде регулируют перепускной клапан, определяют герметичность ротора и частоту его вращения.
После окончательной сборки центрифуги проверяют ее на стенде на герметичность и пропускную способность совместно с масляным насосом нормальной производительности при номинальной частоте вращения и противодавлении.
Ремонт масляных радиаторов. В масляном радиаторе чаще всего забиваются внутренние полости трубок и засоряются маслосборники отложениями, в связи с чем уменьшается пропускная способность радиатора, повышается температура масла. При высокой температуре масла уменьшаются его вязкость и маслянистость, что приводит к повышенному износу деталей, а также старению масла.
Перед ремонтом масляный радиатор вываривают в 5—10-процентном растворе каустической соды в течение 2—3 ч, а затем промывают горячей водой. Отложения в трубках масляного радиатора можно также удалить четыреххлористым углеродом или другим раствором моющего средства. Течь трубок или маслосборников радиатора устраняют пайкой поврежденных мест латунным припоем. Смятую и оборванную ленту трубки выпрямляют и припаивают по всей длине латунным припоем. После ремонта радиатор проверяют на герметичность.
РЕМОНТ УЗЛОВ СИСТЕМЫ ОХЛАЖДЕНИЯ
Характерные неисправности: загрязнение и образование накипи на стенках водяной рубашки, а также баков и трубок радиатора, течь баков и трубок радиатора, трещины на стенках водяной рубашки, повреждение термостата, износ отдельных деталей вентилятора и водяного насоса. Эти неисправности приводят к нарушению теплового режима двигателя и его перегреву.
Перед ремонтом узлов внутренние полости системы охлаждения промывают специальными растворами.
После разборки машины радиатор и головку цилиндров дополнительно вываривают, чтобы удалить оставшуюся накипь.
2.1 Ремонт радиатора. Основные дефекты радиатора — изгиб и разрывы трубок, отпаивание трубок от опорных пластин, повреждение охлаждающих пластин, трещины на верхнем и нижнем баках. Большинство повреждений обнаруживают наружным осмотром и испытанием радиатора под давлением воздуха в ванне с водой.
В неразборных сердцевинах радиатора поврежденные трубки отпаивают от опорных пластин специальным паяльником или паяльной лампой. От охлаждающих пластин трубки отпаивают при помощи нагретого шомпола или нихромовой проволоки. В первом случае шомпол нагревают до температуры 800—900° С и вставляют в трубку. Затем отпаянную трубку вместе с шомполом вынимают из радиатора.
Для отпайки трубок при помощи нихромовой проволоки ее подключают ко вторичной обмотке сварочного трансформатора. Участок проволоки, расположенный в трубке, нагревается меньше, чем находящийся на воздухе. Поэтому для лучшего использования выделяющегося тепла проволоку необходимо перемещать относительно сердцевины.
Восстановленную трубку проверяют на герметичность. Если трубок повреждено больше, сердцевину радиатора выбраковывают или перебирают.
Трещины в верхних и нижних чугунных бачках радиаторов заваривают биметаллическим электродом или заделывают клеями на нове эпоксидных смол. После ремонта радиатор испытывают на герметичность.
Ремонт вентилятора и водяного насоса сводится к восстановлению посадочных мест, замене уплотнений, заварке или заделке трещин, правке крестовин и лопастей, подтяжке их креплений и статической балансировке. В процессе ремонта вентилятора необходимо охранять форму и заданный угол наклона лопастей.
2.2 Ремонт термостата. Основные дефекты термостата: коробление клапана, отрыв штока, появление трещин гофрированного элемента, изгиб пластины подвески. Указанные неисправности обнаруживают при погружении термостата в нагретую воду. Поврежденные места пружинной коробки запаивают припоем ПОС-40. Пружинные коробки заполняют 15% -ным раствором этилового спирта.
При испытании термостата в ванне с водой начала открытия клапана должно быть 70°С, а полное открытие - при 85°С. Высота полного подъёма клапана 9-9,5 мм. Её регулируют, вращая клапан на резьбовом конце хвостовика пружинной коробки.
2.3 Ремонт водяного насоса Основные возможные дефекты деталей водяного насоса: сколы и трещины корпуса, срыв резьбы в отверстиях, износ посадочных мест под подшипники и упорную втулку; изгиб и износ посадочного места под крыльчатку на валике, под втулками, сальниками и шкивами вентиляторов; износ, трещины и коррозия поверхности лопаток крыльчатки; износы внутренней поверхности втулок и шпоночной канавки. Корпус насоса охлаждения изготавливают у ЗИЛ-130 из алюминиевого сплава АЛ4, корпус подшипников - из серого чугуна; у ЗМЗ-53 - из СЧ 18-36, у ЯМЗ КамАЗ - из СЧ 15-32. Основные дефекты корпуса подшипников водяного насоса двигателя ЗИЛ-130: износ торцевой поверхности под упорную шайбу; обломы торца гнезда и износ отверстия под задний подшипник; и износ отверстия под передний подшипник.
Трещины и обломы корпуса заваривают или заделывают синтетическими материалами. Сколы на фланце и трещины на корпусе устраняют сваркой. Деталь предварительно нагревают. Рекомендуется заварку производить ацетилено-кислородным нейтральным пламенем. Трещины можно заделывать эпоксидной смолой. Изношенные поверхности под подшипники при зазорах не более 0,25 мм следует восстанавливать герметиками "Унигерм-7" и "Унигерм-11". При зазоре более 0,25 мм для устранения дефекта требуется ставить тонкие (толщиной до 0,07 мм) стальные ленты.
Погнутый валик правят под прессом, а изношенный менее допустимого восстанавливают хромированием и последующим шлифованием до номинального размера. Изношенную шпоночную канавку на валу заваривают, а затем фрезеруют новую канавку под углом 90-180° к старой.
Крыльчатки можно изготавливать литьём из алюминиевого сплава или капрона. При этом ступица (втулка) должна быть стальной.
После восстановления корпус насоса охлаждения должен отвечать следующим техническим требованиям: торцевое биение поверхности корпуса подшипников под упорную шайбу крыльчатки относительно оси отверстий под подшипники не более 0,050 мм; биение торцевой поверхности бурта корпуса подшипников под корпус насоса относительно отверстий под подшипники не более 0,15 мм; шероховатость поверхности корпуса подшипников под упорную шайбу крыльчатки не более Rа=0,80 мкм, поверхностей отверстий под подшипники не более Rа=1,25 мкм.
Валики насосов охлаждения изготавливают у ЗИЛ и ЗМЗ из стали 45, HRC 50-60; у ЯМЗ - из стали 35, HB 241-286; у КамАЗ - из стали 45Х, HRC 24-30. Основные дефекты валика: износы поверхности под подшипники; износ шейки под крыльчатку; износ паза; повреждение резьбы.
Изношенные поверхности восстанавливают наплавкой в среде углекислого газа с последующим хромированием или железнением с последующим шлифованием на бесцентрово-шлифовальном станке. На уплотнительной шайбе допускаются риски и износ на глубину не более 0,5 мм. При большем износе шайбу заменяют. При установке валика следует заложить 100 г смазки "Литол-24" в межподшипниковую полость. Уплотняющую шайбу и торец опорной втулки перед установкой следует покрыть тонким слоем герметика или смазкой, состоящей по массе из 60% дизельного масла и 40% графита.
Изношенную или повреждённую резьбу в отверстиях восстанавливают нарезанием резьбы ремонтного размера или заваркой с последующим нарезанием резьбы номинального размера.
После сборки зазор между корпусом водяного насоса и лопастями крыльчатки должен быть 0,1…1,5 мм и валик легко вращаться. Водяные насосы обкатывают и испытывают на специальных стендах, например насосы двигателей ЯМЗ-240Б - на стенде ОР-8899, двигателей Д-50 и Д-240 - на КИ-1803, двигателя ЗМЗ-53 - на ОР-9822. Обкатку выполняют за 3 мин при температуре воды 85…90°С и испытывают по режиму.
Каждый отремонтированный насос проверяют на герметичность при давлении 0,12…0,15 МПа. Утечка воды через уплотнения и резьбу шпилек не допускается.
2.4 Ремонт вентилятора Возможные дефекты деталей вентиляторов следующие: износ посадочных мест в шкивах под наружные кольца подшипников качения, износ ручьев в шкивах под ремень, ослабление заклёпок на крестовине, изгиб крестовине и лопастей.
Изношенные посадочные места под подшипники восстанавливают железнением, хромированием. Изношенные ручьи шкивов (до 1мм) протачивают. Ослабленные заклёпки на крестовине лопастей подтягивают. Если отверстия под заклёпки изношены, их рассверливают и ставят заклёпки увеличенного диаметра. Передние кромки лопастей после переклёпки должны лежать в одной плоскости с отклонением не более 2 мм. Шаблоном проверяют форму лопастей вентиляторов и угол их наклона относительно плоскости вращения, который должен быть в пределах 30…35° (при необходимости правят).
Собранный со шкивом вентилятор статически балансируют. Для устранения дисбаланса сверлят углубления дисбаланса сверлят углубления в торце шкивов или утяжеляют лопасть с её выпуклой стороны приваркой или приклёпыванием пластинки.
Если в гидромуфте привода вентилятора подтекает масло через уплотнения, есть осевой зазор и заедание ведомого и ведущего валов при вращении лопастей крыльчатки и шкива от руки, необходим ремонт.
В деталях гидромуфты дефекты аналогичны дефектам деталей вентиляторов. Это обусловливает и подобные способы их устранения. Шариковые подшипники гидромуфты необходимо заменять при осевом и радиальном зазоре более 0,1 мм.
При сборке зазор между ведомым и ведущим колёсами гидромуфты должен быть 1,5…2 мм. Шкив привода гидромуфты при неподвижной ступице вентилятора и, наоборот, ступица при неподвижном шкиве должны вращаться свободно. Термосиловой датчик включателя гидромуфты регулируют постановкой регулировочных шайб на включение при температуре охлаждающей жидкости 90…95°С и на выключение при её температуре 75…80°С.
Дата добавления: 2022-12-03; просмотров: 17; Мы поможем в написании вашей работы! |
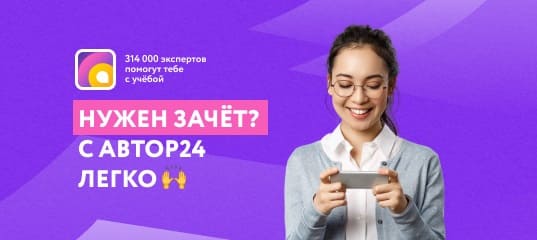
Мы поможем в написании ваших работ!