Шабрение, притирка, шлифование и
Схема СУДОРЕМОНТНОЙ ПРАКТИКИ (I ЭТАП)
Таблица 4.1
Номера и наименование частей, разделов | Всего часов по учебному плану | Из них | |
Лекции | Практическая и самостоятельная работа | ||
1 | 2 | 3 | 4 |
4.1. Слесарный участок | |||
4.1.1. Характеристика участка, на котором выполняется практика | 1,0 | 1,0 | - |
4.1.2. Охрана труда при слесарных работах | 2,0 | 2,0 | - |
4.1.3. Организация и оснащение слесарного участка | 1,0 | 1,0 | - |
4.1.4. Приемы разметки | 6,0 | 2,0 | 4,0 |
4.1.5. Приемы слесарной обработки деталей | 6,0 | 1,0 | 5,0 |
4.1.6. Слесарная обработка поверхностей деталей | 10,0 | 1,0 | 9,0 |
4.1.7. Обработка отверстий и нарезание резьбы | 8,0 | 1,0 | 7,0 |
4.1.8. Выполнение зачетной работы | 2,0 | ||
Итого | 36,0 | 9,0 | 25,0 |
4.2. Станочный участок | |||
4.2.1. Правила по технике безопасности при работе на металлорежущих станках | 2,0 | 2,0 | - |
4.2.2. Противопожарные правила | 1,0 | 1,0 | - |
4.2.3. Станки, приспособления и инструменты. Номенклатура обрабатываемых деталей | 2,0 | 2,0 | - |
4.2.4. Технологический процесс изготовления детали | 1,0 | 1,0 | - |
4.2.5. Рабочее место станочника | 1,0 | 1,0 | - |
4.2.6. Управление металлорежущими станками | 3,0 | 1,0 | 2,0 | |||
4.2.7. Обработка наружных поверхностей | 9,0 | 1,0 | 8,0
| |||
4.2.8. Обработка внутренних поверхностей | 10,0 | 1,0 | 9,0 | |||
4.2.9. Обработка заготовок фрезерной группы | 5,0 | 1,0 | 4,0 | |||
4.2.10. Выполнение зачетной работы | 2,0 | |||||
Итого | 36,0 | 11,0 | 23,0 | |||
4.3. Сварочный участок | ||||||
4.3.1.Техника безопасности и охрана труда при сварочных работах, противопожарные правила | 3,0 | 3,0 | - | |||
4.3.2. Оснащение электро и газосварочного участка | 1,0 | 1,0 | - | |||
4.3.3. Технология ручной дуговой электросварки, газосварки | 1,0 | 1,0 | - | |||
4.3.4. Подготовка заготовок | 1,5 | 0,5 | 1,0 | |||
4.3.5. Типы сварных швов и соединений | 1,0 | 1,0 | - | |||
4.3.6. Характеристика сварочных материалов | 1,0 | 1,0 | - | |||
4.3.7. Технологические режимы сварки | 1,0 | 1,0 | - | |||
4.3.8. Направление валиков и сварка встык в нижнем вертикально-потолочном положении | 10,0 | 1,0 | 8,0 | |||
4.3.9. Сварка нахлесточных соединений | 5,5 | 0,5 | 5,0 | |||
4.3.10. Сварка тавровых соединений | 5,5 | 0,5 | 5,0 | |||
4.3.11. Многопроходные и многослойные швы | 4,5 | 0,5 | 4,0 | |||
4.3.12. Зачетная работа | 2,0 | 2,0 | ||||
Итого | 36,0 | 11,0 | 23,0 |
- ИНДИВИДУАЛЬНЫЕ ЗАДАНИЯ ДЛЯ ОТЧЕТА ПО ПЕРВОМУ ЭТАПУ
ТЕХНОЛОГИЧЕСКОЙ СУДОРЕМОНТНОЙ ПРАКТИКИ
|
|
- Отчет должен содержать по 3 ответа на вопросы по каждому участку: слесарному, станочному и сварочному.
Номера вопросов по каждому из участков выбирается по приведенной ниже таблице 5.1.
Задания для отчета по учебно-технологической практике
Таблица 5.1.
Предпослед-няя цифра зачетной книжки | Последняя цифра зачетной книжки | |||||||||||||
0 | 1 | 2 | 3 | 4 | 5 | 6 | 7 | 8 | 9 | |||||
Номера вопросов | ||||||||||||||
0 | 1,2,3 | 1,2,10 | 1,2,9 | 1,2,7 | 1,3,7 | 1,4,10 | 1,4,5 | 1,8,9 | 1.2,8 | 1,2,9 | ||||
1 | 1,4,5 | 1,2,6 | 1,3,10 | 1,5,6 | 1,2,5 | 1,3,9 | 1,2,6 | 1,2,8 | 1,3,5 | 1,3,6 | ||||
2 | 1,6,7 | 1,2,7 | 1,4,7 | 1,2.10 | 1,3,6 | 1,3,7 | 1,3,8 | 1,5,6 | 1,6,8 | 1,7,9 | ||||
3 | 1,8,9 | 1,2,8 | 1.5,10 | 1,4,10 | 1,7,10 | 1.2.9 | 1,5,6 | 1,4,6 | 1,5,8 | 1,6.10 | ||||
4 | 1,2,10 | 1,2,9 | 1,3,4 | 1,3,8 | 1,4,6 | 1,6,10 | 1,2,5 | 1,7,9 | 1,4,6 | 1,2,5 | ||||
5 | 1,3,5 | 1,3,6 | 1,6,8 | 1,7,9 | 1,5,8 | 1,6,9 | 1,3,10 | 1,2,9 | 1,4,7 | 1,5,8 | ||||
6 | 1,4,6 | 1,3.7 | 1,6,7 | 1,2,5 | 1,3,9 | 1,2,6 | 1,2,6 | 1,2,10 | 1,2,7 | 1,4,9 | ||||
7 | 1,5,7 | 1,3,8 | 1,4,7 | 1,5,8 | 1,2,7 | 1,3,7 | 1,4,6 | 1,5,8 | 1,6,8 | 1,7,10 | ||||
8 | 1,6,8 | 1,3,9 | 1,7,9 | 1,4,9 | 1,6,8 | 1,4,9 | 1,3,7 | 1,6,8 | 1,6,10 | 1,4.10 | ||||
9 | 1,7,10 | 1,4,2
| 1,2,10 | 1,3,10 | 1,3,5 | 1,3,8 | 1,6,7 | 1,4,2 | 1,2,8 | 1,4,7 | ||||
- Перечень вопросов для отчета
Слесарный участок
1. Охрана труда при выполнении слесарно-ремонтных работ:
общие сведения об охране труда в цехе и на предприятии; меры безопасности при выполнении слесарных работ; первая помощь при несчастных случаях и предотвращение их.
2. Организация и оснащение слесарного участка, планировка участка; оборудование и оснастка.
3. Подъемно-транспортные устройства; установочно-крепежные приспособления.
4. Контрольно-измерительный инструмент: штангенциркуль, нутрометр, кронциркуль, микрометр, угломер.
5. Контрольно-измерительный инструмент: резьбомер, щуп, лекальные линейки, контрольная плита, проверочный угольник.
6. Приемы разметки: инструмент и приспособления для разметочных работ; нанесение рисок на размечаемые поверхности деталей.
7. Инструмент и приспособления для вырубки и резания металлов; приемы резания металлов ручной ножовкой; форма напильников и приемы пропиливания поверхностей.
8. Слесарная обработка поверхностей: обработка поверхностей шабрением, притирочно-доводочные работы; правка валов и полирование их поверхностей.
|
|
9. Обработка отверстий и нарезание резьбы, приспособления и инструмент для операции сверления отверстия; управление сверлильным станком; техника безопасности при сверлильных работах.
10. Заточка сверл и техника сверления отверстий. Элементы метрической и трубной резьбы; инструменты для нарезания резьбы; практика нарезания резьбы метчиками и плашками. Развертывание и торцевание отверстий.
Станочный участок
1. Правила по технике безопасности при работе за токарным станком. Противопожарные мероприятия.
2. Типы металлорежущих станков и их технические характеристики.
3. Номенклатура обрабатываемых деталей. Приспособления и инструменты для обработки деталей. Мерительный инструмент.
4. Основные виды токарных работ. Рабочее место токаря. Уход за станком. Техника безопасности при токарных работах.
5. Управление металлорежущим станком: кинематика станка; пуск и остановка; установка заготовки; установка резца; управление суппортом; установка заданного числа оборотов, продольной и поперечной подачи; установка резца на глубину резания.
6. Заточка режущего инструмента: выбор формы резца и углов его заточки; правила и приемы заточки резцов; приспособления, станки и инструменты для заточки, контроль качества заточки и правильности геометрии.
7. Обработка наружных поверхностей деталей судовых механизмов: выбор заготовок; черновое и чистовое обтачивание; подрезание торца и уступов; вытачивание наружных канавок; отрезание, нарезание резьбы.
8. Обработка цилиндрических отверстий: сверление и рассверливание сквозных и глухих отверстий.
9. Обработка внутренних цилиндрических отверстий; нарезание резьб.
10. Обработка заготовок на станках фрезерной группы. Типы станков и их назначение.
Сварочный участок
1. Техника безопасности и охрана труда при сварочных работах.
2. Организация и оснащение сварочного участка: планировка участка; оборудование и оснастка, приспособления и инструменты.
3. Конструктивные схемы сварочных трансформаторов и генераторов. Газосварочное оборудование.
4. Технология ручной дуговой сварки, газосварки.
5. Подготовка заготовок. Типы сварных швов и соединений.
6. Характеристика сварочных материалов. Технологические режимы сварки.
7. Дефекты сварочных швов; методы контроля сварочных швов.
8. Наплавка валиков и сварка встык в нижнем положении.
9. Сварка нахлесточных соединений.
10. Сварка тавровых соединений.
Шабрение, притирка, шлифование и
ПОЛИРОВАНИЕ
Шабрение выполняют для получения более точной и ровной поверхности после ее предварительной обработки опиливанием. За один проход шабер снимает слой металла толщиной 0,005 – 0,7 мм. Качество шабрения определяют по числу пятен на площади 25 х 25 мм (таблица 6) , которые должны быть равномерно распределены. Рабочим инструментом служит шабер, представляющий собой металлический стержень с режущей кромкой на конце. Шаберы изготавливают из инструментальной стали У10 или У12 (У10А или У12А), Р18, ШХ15.
Припуски на шабрение зависят от предварительной обработки деталей и их габаритов (таблица 7,8).
Притирку применяют с целью получения высокой степени прилегания соприкасающихся поверхностей. Качество поверхности после притирки соответствует 1 – 2-му классам точности по 10 – 14-му классам шероховатости. Припуск на притирку должен быть в пределах 0,01 – 0,02 мм.
Показатели качества шаброванной поверхности
Таблица 6
Класс точности шаброванной поверхности | Минимальное число пятен на площади 25х25 мм | Допускаемое отклонение от плоскостности мкм | Класс шероховатости поверхности |
0-й | 25 | 0,16 – 0,32 | 9 – й |
1 - й | 25 | 0,32 – 0,63 | 8 -й |
2 -й | 20 | 0,63 – 1,25 | 7 -й |
3 -й | 12 | 1,25 – 2,5 | 6 -й |
Припуски на шабрение плоскостей, мм
Таблица 7
Ширина плоскости, мм | Длина плоскости, мм | ||||
100 - 500 | 500 - 1000 | 1000 - 2000 | 2000 - 4000 | 4000 -6000 | |
До 100 | 0,1 | 0,15 | 0,2 | 0,25 | 0,3 |
100 –500 | 0,15 | 0,2 | 0,25 | 0,3 | 0,4 |
500 –1000 | 0,18 | 0,25 | 0,35 | 0,45 | 0,5 |
Припуски на шабрение отверстий, мм
Таблица 8
Диаметр отверстия, мм | Длина отверстия, мм | Диаметр отверстия, мм | Длина отверстия | ||||||
До 100 | 100 - 200 | 200 - 300 | Свы-ше 300 | До 100 | 100 - 200 | 200 - 300 | Свы-ше 300 | ||
До 80 | 0,05 | 0,08 | 0,12 | - | 180 - 360 | 0,15 | 0,2 | 0,25 | 0,3 |
80- 180 | 0.1 | 0,15 | 0,2 | 0,2 | Свыше 360 | 0,2 | 0,25 | 0,3 | 0,3 |
Слой обрабатываемого притиркой материала удаляют путем механического или химико-механического воздействия, с помощью притирочных порошков или паст, которые подбирают в зависимости от обрабатываемого материала (таблица 9). По полирующей способности пасту ГОИ различают трех видов: тонкую, среднюю и грубую.
Материалы для притирки клапанов и уплотнений
арматуры
Таблица 9
Притираемый металл | Притирочные материалы | |
Грубая притирка | Окончательная притирка | |
Сталь 2Х13 | Корунд М14, наждак М14 или М20,паста ГОИ грубая | Наждак М10 |
Чугун серый, сталь 3Х13 | Корунд М14, наждак М20, паста ГОИ грубая | Корунд М10, наждак М10, паста ГОИ средняя |
Бронза и медно-никелевый сплав | Толченое стекло, паста ГОИ грубая, наждак М14 | Паста ГОИ средняя, наждак М10 |
Азотированная сталь 38Х2МЮА | Электрокарборунд М20 или М14 и паста ГОИ грубая | Электрокорунд М10, паста ГОИ средняя |
Обработку деталей шлифовальной шкуркой называют шлифованием. Шлифовальную шкурку изготавливают двух типов: для машинной и ручной обработки металлов и для обработки неметаллических материалов (дерево, кожа и др.). По износостойкости ее делят на два класса: А и Б. Износостойкость шлифовальной шкурки определяется отношением зернистости абразивного слоя к показателю осыпаемости. Различают три степени жесткости шлифовальной шкурки:
Показатель жесткости, мм 50 – 100 30 – 50 15 – 30
Степень жесткости 1 2 3
Шлифовальную шкурку изготавливают из дробленных абразивных материалов (электрокорунда, карбида кремния, монокорунда и др.). Основу шкурки составляют ткани: саржа легкая (СЛ), саржа средняя (ОСЛ) и др. Абразивный материал связан с основой мездровым клеем.
Доводку производят с помощью алмазных паст нормальной (Н), повышенной (П) и высокой (В) концентраций, которые применяют также для полирования деталей из закаленных легированных сталей, твердых сплавов и других материалов. Более качественную поверхность можно получить путем применения паст из синтетических алмазов.
Полирование применяют для окончательной (чаще декоративной) обработки металлов, к которым предъявляются высокие требования в отношении качества поверхности. Полирование осуществляют с помощью вращающихся кругов из войлока, фетра, полотна или бязи, а также абразивными ремнями и полировальной пастой ЛИК ( смесь окиси алюминия с парафином или стеарином, олеиновой кислотой, минеральным маслом и керосином) или пастой ГОИ (таблица 10).
Технические характеристики пасты ГОИ
Таблица 10
Показатели | Паста | ||
тонкая | средняя | грубая | |
Цвет | Светло-зеленый | Темно-зеленый | Почти черный |
Полирующая и шлифующая способность (съем металла), мкм | 6 - 8 | 10 - 15 | 20 – 50 |
Качество поверхности изделия после обработки | Зеркальное | Полузеркальное | Матовое |
Класс шероховатости | 11 | 9 | 7 |
Компоненты пасты ГОИ: окись хрома, % органическая основа, % содержание в пасте зерен размером 45 мкм, % сульфаты посторонние механические примеси | 69 – 74 26 – 31 3 Следы Не допускаются | 74 – 78 22 – 26 3 Следы Не допускаются | 64 – 88 12 – 16 3 Следы Не допускаются |
Дата добавления: 2022-12-03; просмотров: 49; Мы поможем в написании вашей работы! |
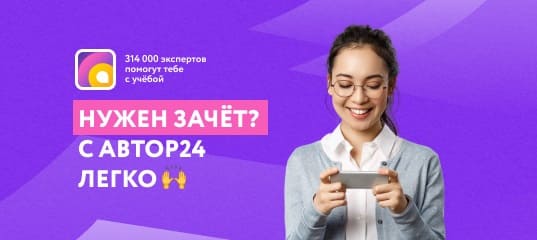
Мы поможем в написании ваших работ!