Виды электрического контроля:
ФЕДЕРАЛЬНОЕ АГЕНТСТВО ЖЕЛЕЗНОДОРОЖНОГО ТРАНСПОРТА
Федеральное государственное бюджетное образовательное учреждение
высшего образования
«Иркутский государственный университет путей сообщения»
(ФГБОУ ВО ИРГУПС)
Факультет транспортные системы
Кафедра «Физика, механика и приборостроение»
ПОЛУЧЕНИЕ ПЕРВИЧНЫХ ПРОФЕССИОНАЛЬНЫХ УМЕНИЙ И НАВЫКОВ ПРОВЕДЕНИЯ ИЗМЕРЕНИЙ ПАРАМЕТРОВ РАЗЛИЧНЫХ ОБЪЕКТОВ ПО ЗАДАННОЙ МЕТОДИКЕ, В ТОМ ЧИСЛЕ ПЕРВИЧНЫХ УМЕНИЙ И НАВЫКОВ ПРОЕКТНО-КОНСТРУКТОРСКОЙ ДЕЯТЕЛЬНОСТИ
Отчет по учебной-ознакомительной практике
УП.420300.12.03.01.ПЗ
Выполнил студент гр. ПС.2-20-1 Ходаков И.Ю. «___» __________ 20__г. ____________________ (подпись) | Руководитель практики от университета ассистент кафедры ФМиП Мурзин С. В. «___» __________ 20__г. ____________________ (подпись) |
Иркутск, 2022
Содержание | |||
Введение | 3 | ||
1 | Дефекты и их обнаружения | 4 | |
1.1 | Дефекты | 4 | |
2 | Основы пайки | 7 | |
2.1 | Пайка | 7 | |
2.2 | Режимы и показатели пайки | 8 | |
2.3 | Виды пайки и лужения | 8 | |
3 | Методы неразрушающего контроля | 11 | |
3.1 | Основные понятия | 11 | |
3.2 | Виды неразрушающего контроля | 13 | |
3.3 | Электронный метод контроля | 17 | |
Заключение | 21 | ||
Список использованных источников | 22 |
|
|
Введение
Целями прохождения учебной практики являются:
–получение первичных профессиональных умений и навыков проведения измерений параметров различных объектов по заданной методике, в том числе первичных умений и навыков проектно-конструкторской деятельности;
–осуществление анализа поставленной задачи исследований в области приборостроения.
Задачами проведения практиками являются:
–углубленное ознакомление с видами неразрушающего контроля, со средствами диагностики, приборными системами и технологиями;
–развитие и накопление первичных навыков использования в эксплуатации методов и способов диагностирования при работе с измерительными приборами, освоение приемов, методов и способов обработки, представления и интерпретации результатов проведенных исследований. Для достижения поставленных целей при прохождении учебной практики ставились следующие задачи:
–ознакомление с историей конструирования приборов в России;
–углубленное ознакомление с видами неразрушающего контроля, со средствами диагностики, приборными системами и технологиями;
|
|
–развитие и накопление первичных навыков использования в эксплуатации методов и способов диагностирования при работе с измерительными приборами, освоение приемов, методов и способов обработки, представления результатов проведенных исследований.
В соответствии с целями и задачами учебной практики запланировано:
–изучение истории конструирования приборов в России и за рубежом и задач исследования в области приборостроения;
–измерение приборами параметров и исследование объекта;
–написание отчета по практике, выполнение индивидуального задания.
1 Дефекты и их обнаружения
Дефекты
В соответствие с ГОСТ 15467 дефектом называется каждое отдельное несоответствие продукции установленным требованиям.
Классификация дефектов:
- по возможности обнаружения:
1) явные, обнаружение, которых возможно предусмотренными правилами, методами и средствами контроля, хотя они могут и не выявляться визуально;
2) cкрытые, к ним относятся дефекты, выявление которых не предусмотрено нормативной документацией; они обычно выявляются при обнаружении явных дефектов или в процессе эксплуатации;
- по местоположению:
|
|
1) локальные (трещины, риски, неметаллические включения и т. д.);
2) расположенные в ограниченных зонах объема или поверхности детали (зоны ликвации, неполной закалки, коррозионного поражения, местный наклеп и т. д.); их можно подразделить на внутренние (глубинные) и наружные (поверхностные и подповерхностные);
3) распределенные во всем объеме детали или по всей ее поверхности (общее несоответствие химического состава, структуры, качества механической обработки и т. д.);
- по форме, размерам и ориентировке:
1) резкие концентраторы напряжений;
2) нерезкие концентраторы напряжений;
- по этапу возникновения:
1) конструктивные;
2) производственные (ремонтные), возникающие в процессах изготовления, сборки или ремонта изделия;
3) эксплуатационные, зарождающиеся и или развивающиеся в процессе эксплуатации изделия;
4) аварийные.
- по возможности устранения:
1) устранимые, устранение которых технически возможно и экономически целесообразно;
2) неустранимые.
- по возможности использования продукции:
1) критические (делают использование продукции практически невозможным или недопустимым);
2) значительные (оказывают существенное влияние на возможность использования изделия по назначению или снижают его долговечность);
|
|
3) малозначительные (не оказывают существенного влияния ни на использование изделия по назначению, ни на его долговечность).
Конструктивные дефекты – это несоответствие требованиям технического задания или установленным правилам разработки (модернизации) продукции. Они являются следствием несовершенства конструкции и ошибок при конструировании. Причины таких дефектов могут быть различными:
- неправильный выбор материалов;
- неправильное назначение режимов термической обработки;
- неправильное назначение допусков в сопряжениях;
- заниженный класс чистоты поверхности деталей;
- неверное определение размеров деталей (результатом этого могут быть слишком большие действующие напряжения);
- нерационально выбранная форма детали;
- малые радиусы галтелей (это может явиться причиной слишком больших коэффициентов концентрации напряжений в опасных сечениях);
- создание концентраторов напряжений в опасных сечениях;
- малая выносливость деталей изделия;
- низкая жесткость конструкции (повышение вибрации) и т.д.
Своевременное выявление конструктивных дефектов позволит непрерывно совершенствовать выпускаемую продукцию, повышать ее надежность и долговечность.
К производственным дефектам относится несоответствие требованиям нормативной документации на изготовление или поставку продукции. Они возникают обычно в результате нарушений техпроцесса при производстве или восстановлении деталей, узлов и машин в целом, а также при неправильно назначенных технологических процессах.
Производственные дефекты, если они не были выявлены в процессе изготовления или восстановления изделия, проявляются, как правило, в начальный период эксплуатации.
Дефекты этой группы могут возникнуть вследствие применения материала не соответствующей марки, отступления от размеров и допусков на изготовление и ремонт деталей, нарушения технологии механической или термической обработки деталей, нарушения технологических процессов сборки или регулировки изделия или его узлов и блоков и т.д.
Отклонение химического состава (и, как следствие, физических и химических свойств металла отливок) от заданного вызывается неправильным расчетом шихты или нарушением режима ведения плавки металла. Этот дефект является неустранимым. В результате изменяются механические свойства сплава, что может привести к преждевременному разрушению изготовленной из него детали, ее ускоренному изнашиванию.
Существует большое количество различных способов обработки металлов давлением: свободная ковка, прессование, штамповка, высадка, волочение, прокатка и др. Обработка давлением позволяет получить металл требуемой формы, уплотняет его, заваривает некоторые дефекты, измельчает структуру, улучшает механические свойства [2].
2 Основы пайки
2.1 Пайка
Пайка ‑ технологическая операция, применяемая для получения неразъёмного соединения деталей из различных материалов путём введения между этими деталями расплавленного металла (припоя), имеющего более низкую температуру плавления, чем материал соединяемых деталей.
По ГОСТ 17325-79 Пайка – образование неразъемного соединения с межатомными связями путем нагрева соединяемых материалов ниже температуры их плавления, их смачивания припоем, затекания припоя в зазор и последующей его кристаллизации.
Лужение – образование на поверхности материала металлического слоя путем плавления припоя, смачивания припоем поверхности и последующей его кристаллизации.
Паяное соединение – соединение, образованное пайкой.
Паяемый материал – основной материал заготовок или изделий, соединяемых пайкой или подвергаемых лужению. По ГОСТ 3.1109-82
Припой – материал для пайки и лужения с температурой плавления ниже температуры плавления паяемых материалов.
Вспомогательный материал (ГОСТ 3.1109-82) – к вспомогательным материалам относятся: паяльные флюсы, вещества, ограничивающие растекание припоя и т.п.
Паяльный флюс – вспомогательный материал, применяемый для удаления окислов с поверхности паяемого материала и припоя и предотвращения их образования.
Распайка – разъединение паяного соединения при нагреве его выше температуры начала плавления материала паяного шва.
Подпайка – повторный нагрев паяного соединения и введение новой порции припоя с целью устранения дефектов. Перепайка – распайка и повторная пайка.
Сборочный зазор под пайку – зазор между поверхностями паяемых заготовок или изделий, устанавливаемый при сборке.
Паяльный зазор – зазор между поверхностями паяемых заготовок или изделий, образующийся при температуре пайки.
Паяемость – свойство материала образовывать паяное соединение при заданном режиме пайки [3].
2.2 Режим и показатели пайки
Режим пайки - совокупность параметров и условий, при которых осуществляется пайка. Под параметрами понимают температуру пайки, время выдержки при этой температуре, скорость нагрева и охлаждения. Под условиями понимают способ нагрева, припой, флюс (газовую среду), давление на соединяемые заготовки и т.п.
Температура пайки – температура паяемых материалов и расплавленного припоя в месте их контакта, при которой происходит формирование паяного соединения.
Термический цикл пайки – совокупность значений температуры паяемых материалов и припоя в месте их контакта, при которых происходит нагрев, выдержка и охлаждение при пайке.
Время нагрева при пайке – интервал времени нагрева паяемых материалов и припоя в месте их контакта от температуры окружающей среды до температуры пайки [3].
2.3 Виды пайки и лужения
Низкотемпературная пайка – пайка при температуре, не превышающей 723 К.
Пайка готовым припоем – пайка, при которой используется заранее изготовленный припой.
Пайка расплавлением полуды – пайка предварительно луженых заготовок или изделий без дополнительного введения припоя.
Контактно-реактивная пайка – пайка, при которой припой образуется в результате контактно-реактивного плавления.
Реактивно-флюсовая пайка – пайка, при которой припой образуется в результате разложения компонентов флюса.
Сваркопайка – пайка разнородных материалов, при которой более легкоплавкий материал локально нагревается до температуры, превышающей температуру его плавления и выполняет роль припоя.
Капиллярная пайка – пайка, при которой расплавленный припой заполняет паяльный зазор и удерживается в нем преимущественно поверхностым натяжением.
Некапиллярная пайка – пайка, при которой расплавленный припой заполняет паяльный зазор преимущественно под действием своего веса или прилагаемой к нему извне силы.
Пайкосварка – некапиллярная пайка, при которой соединяемым кромкам заготовок придается форма, подобно разделке кромок при сварке плавлением.
Флюсовая пайка (лужение) – пайка (лужение) с применением флюса.
Бесфлюсовая пайка (лужение) – пайка (лужение), при которой для удаления окислов с поверхности паяемых материалов и припоя и предотвращения их образования применяются газовые среды или создается вакуум, или разрушение окисной пленки осуществляется ультразвуковыми колебаниями или частицами твердого материала.
Пайка в активной газовой среде – бесфлюсовая пайка с применением активных газов или нейтральных газов с добавкой активных газообразных веществ.
Пайка в вакууме – бесфлюсовая пайка с применением разреженного газа при давлении ниже 10^5 Па.
Ультразвуковая пайка (лужение) – бесфлюсовая пайка (лужение) с применением ультразвуковых колебаний.
Абразивное лужение - бесфлюсовое лужение с применением трения паяемого материала частицами твердого материала.
Газопламенная пайка – пайка, при которой нагрев паяемых материалов и припоя осуществляется газовой горелкой.
Индукционная пайка – пайка, при которой нагрев паяемых материалов и припоя осуществляется теплом, выделяющимся в них под воздействием электромагнитного поля.
Дуговая – пайка, при которой нагрев паяемых материалов и припоя осуществляется электрической дугой.
Пайка электросопротивлением – пайка, при которой нагрев паяемых материалов и припоя осуществляется пропусканием через них электрического тока.
Пайка инфракрасными лучами – пайка, при которой нагрев паяемых материалов и припоя осуществляется инфракрасными лучами.
Лазерная пайка – пайка, при которой нагрев паяемых материалов и припоя осуществляется лазером (излучением оптического квантового генератора) [3].
3. Методы неразрушающего контроля
3.1 Основные понятия
Техническая диагностика - область знаний, охватывающая теорию, методы и средства определения технического состояния объектов.
Объект технического контроля (ОК) – это подвергаемая контролю продукция, процессы ее создания, применения, транспортирования, хранения, технического обслуживания и ремонта, а также соответствующая техническая документация. Объектами контроля являются предметы труда (изделия, материалы, техническая документация), средства труда (оборудование предприятий) и технические процессы.
Методы контроля: разрушающий и неразрушающий контроль.
Разрушающий контроль – это совокупность методов исследования, которые требуют отбора проб или вырезки образцов непосредственно из материала объекта, при этом, объект остается неработоспособен до восстановления мест отбора проб (образцов).
Неразрушающий контроль (НК) – совокупность методов измерения и контроля показателей качества изделия без изменения присущих ему свойств, размеров и характеристик.
Также под неразрушающим контролем понимают определение показателей качества изделий и материалов без изменения присущих им свойств, параметров, характеристик с целью исключить на стадии изготовления потенциально ненадежные изделия со «скрытыми» дефектами.
Дефектоскопический контроль и дефектоскопия – это одно из направлений неразрушающего контроля, при котором осуществляется контроль качества материалов, деталей, узлов и покрытий, а также контроль состояния скрытых элементов, механизмов, агрегатов и конструкций с помощью проникающих физических полей и химических веществ.
Результатом НК является установленная оценка соответствия объект контроля (ОК) предъявляемым техническим требованиям, применяемая как результат сопоставления окончательной информации об ОК с требованиями НТД (нормативно-техническая документация).
В задачу НК входит выявление возможных отклонений от установленных технических характеристик ОК. Такими отклонениями могут быть дефекты типа нарушений сплошности, изменение структуры и физикомеханических свойств материала, размеров, покрытий, соединений и т.п. Конечным результатом НК является регистрация всех обнаруженных отклонений и, по возможности, количественная оценка их параметров (координат, размеров и формы дефектов, величин, зависящих от физико-механических характеристик материала и т.п.). Отбраковка негодных изделий проводится на основе заранее установленных норм.
Метод НК – это метод контроля, при котором не должна быть нарушена пригодность объекта в применении, основанная на том или ином физическом явлении.
Вид НК – условная группировка методов НК, объединенная общностью физических характеристик.
Виды НК классифицируются по следующим классификационным признакам: по характеру полей или излучений, взаимодействующим с ОК; по характеру взаимодействия физических полей или веществ с ОК; по первичным информативным признакам; по способам индикации первичной информации;. по способам представления окончательной информации.
Контролепригодность – это свойство объекта, обеспечивающее возможность, удобства и надежность его контроля (диагностирования) на всех стадиях жизненного цикла.
Технологическая инструкция по НК – это документ, ориентированный на решение задач НК объекта с указанием операций контроля и их параметров.
Технологическая карта НК – это документ в виде карты, таблицы содержащий основные данные технической документации.
Заключение по результатам НК – это документ, составленный по результатам НК, содержащий информацию о выполненном контроле и его результате.
Достоверность НК – это показатель НК (количественный и качественный) связанный с вероятностями принятия безошибочных решений при наличии или отсутствии дефекта.
Основные параметры НК – это совокупность параметров НК, обеспечивающая выполнение установленных НТД требований по обнаружению дефекта, измерению параметров дефекта и оценки влияния дефектов на объект [4].
3.2 Виды неразрушающего контроля
Методы НК разделяют на группы, называемые видами, объединенные общностью физических признаков. Существует 8 различных видов НК:
Радиоволновый метод неразрушающего контроля основан на регистрации изменений параметров электромагнитных волн радиодиапазона, взаимодействующих с объектом контроля. Обычно используются волны сверхвысокочастотного (СВЧ) диапазона с длиной от 1мм до100 мм. Контролируют изделия из материалов, где радиоволны не очень сильно затухают: диэлектрики (пластмассы, керамика, стекловолокно), магнитодиэлектрики (ферриты), полупроводники, тонкостенные металлические объекты. По характеру взаимодействия с ОК различают методы прошедшего, отраженного, рассеянного излучения и резонансный. При использовании этого вида контроля наличие дефектов в исследуемых изделиях приводит к появлению дополнительных отражений электромагнитного поля, которые изменяют интерференционную картину и вызывают дополнительные потери энергии. Этот метод применяется в дефектоскопии диэлектриков, а также при исследовании состояния поверхности проводящих тел. Недостатком СВЧ метода является сравнительно низкая разрешающая способность устройств, реализующих этот метод, обусловленная малой глубиной проникновения радиоволн в металлы.
Тепловой метод НК основан на регистрации изменений тепловых или температурных полей контролируемых объектов. Он применим к объектам из любых материалов. Распределение температур в изделии зависит от его свойств: геометрических параметров, химического состава, наличия дефектов и других. По характеру взаимодействия теплового поля с ОК различают методы: пассивный (на объект не воздействуют внешним источником энергии) и активный (объект нагревают или охлаждают от внешнего источника). Недостатком этого метода контроля является необходимость использования контактных устройств, что затрудняет процессы автоматизации при непрерывных измерениях и контроле движущихся объектов. При бесконтактных измерениях возникают достаточно жесткие требования к чистоте окружающей среды.
Оптический НК основан на наблюдении или регистрации параметров оптического излучения, взаимодействующего с ОК. Это взаимодействие связано с поглощением, отражением, рассеиванием, дисперсией, поляризацией и др. оптическими эффектами. Данный метод применяют для измерения геометрических параметров изделий, контроля состояния поверхности и обнаружения поверхностных дефектов. Оптические методы имеют очень широкое применение благодаря большому разнообразию способов получения первичной информации. Возможность их применения для наружного контроля не зависит от материала объекта. Оптические методы широко применяют для контроля прозрачных объектов. В них обнаруживают макро- и микродефекты, структурные неоднородности, внутренние напряжения. Недостатками оптических методов являются узкий диапазон контролируемых параметров, жесткие требования к состоянию окружающей среды и чистоте поверхности изделия.
Радиационный НК основан на регистрации и анализе проникающего ионизирующего излучения после взаимодействия его с ОК. В зависимости от природы ионизирующего излучения вид контроля подразделяют на подвиды: рентгеновский, гамма-, бета- (поток электронов), нейтронный. Наиболее широко используют для контроля рентгеновское и гамма излучения. Их можно использовать для контроля объектов из самых различных материалов, подбирая благоприятный частотный диапазон. Эти методы в основном применяются в дефектоскопии, измерении геометрических и структурных особенностей материалов. К недостаткам данных методов относятся повышенные требования к технике безопасности, сложность, дороговизна и громоздкость аппаратуры, а также ограничения, связанные со сравнительно небольшими толщинами ОК.
Акутический НК основан на регистрации параметров упругих волн, возникающих или возбуждаемых в объекте. Чаще всего используют упругие волны ультразвукового диапазона (с частотой колебаний выше 20 кГц). Этот метод также называют ультразвуковым. Главная отличительная особенность данного метода состоит в том, что в нем применяют и регистрируют не электромагнитные, а упругие волны, параметры которых тесно связаны с такими свойствами материалов, как упругость, плотность, анизотропия (неравномерность свойств по различным направлениям) и др.
Магнитный НК основан на анализе взаимодействия магнитного поля с контролируемым объектом. Как правило, его применяют для контроля объектов из ферромагнитных материалов. По характеру взаимодействия физического поля с объектом этот вид контроля не дифференцируют: во всех случаях используют намагничивание объекта и измеряют параметры, используемые при контроле магнитными методами. Процесс намагничивания и перемагничивания ферромагнитного материала сопровождается возникновением гистерезиса. Химический состав, структура, наличие несплошностей и другие свойства, которые требуется контролировать, обычно связаны с параметрами процесса намагничивания и петлей гистерезиса.
Магнитные методы применяют для измерения толщины неферромагнитного покрытия на ферромагнитном основании; для дефектоскопии поверхностных и подповерхностных участков ферромагнитных материалов (магнитопорошковый метод); для получения информации о магнитной проницаемости и ее изменении в зависимости от напряженности магнитного поля (индуктивный метод).
В общем случае при намагничивании объекта контроля, вблизи поверхности которого имеется несплошность (дефект), в области дефекта возникают пространственные аномалии напряженности магнитного поля. Появляются поля рассеяния. Изменение напряженности магнитного поля, точнее градиента напряженности, используют как первичный информационный параметр для выявления дефектов.
Электрический НК основан на регистрации параметров электрического поля, взаимодействующего с контролируемым объектом (собственно электрический метод), или поля, возникающего в контролируемом объекте в результате внешнего воздействия (термоэлектрический метод). Его применяется для контроля диэлектрических и проводящих материалов. Методы электрического контроля (электростатический порошковый, термоэлектрический, электроискровой, электрического потенциала, емкостной) позволяют определять дефекты различных материалов, измерять толщины стенок, покрытий и слоев, сортировать металлы по маркам, контролировать диэлектрические или полупроводниковые материалы. Недостатками перечисленных методов электрического НК являются необходимость контакта с объектом контроля, жесткие требования к чистоте поверхности изделия, трудности автоматизации процесса измерения и зависимость результатов измерения от состояния окружающей среды.
Вихретоковый вид неразрушающего контроля основан на анализе взаимодействия электромагнитного поля вихретокового преобразователя с электромагнитным полем вихревых токов, наводимых в контролируемом объекте. В этом методе используется эффект воздействия вихревых токов, возбуждаемых в проводящем образце, на электрические параметры преобразователя. Его применяют только для контроля изделий из электропроводящих материалов. Вихревые токи возбуждают в объекте с помощью преобразователя в виде катушки индуктивности, питаемой переменным или импульсным током. Приемным преобразователем (измерителем) служит та же или другая катушка. Интенсивность и распределение вихревых токов в объекте зависят от его геометрических размеров, электрических и магнитных свойств материала, от наличия в материале нарушений сплошности, взаимного расположения преобразователя и объекта, т.е. от многих параметров [4].
3.3 Электрический метод контроля
1 Область применения. Методы электрического контроля, востребованные в машиностроении, нефтегазовой и других отраслях промышленности, позволяют оценивать целостность поверхностных слоев и решать многочисленные практические задачи: Определять глубину несплошностей на металлических поверхностях, обнаруженных ранее с помощью других методов НК (применение электропотенциальной дефектоскопии). Контролировать и оценивать целостность изоляционных покрытий посредством применения электроемкостной и электроискровой разновидностей. Выявлять сквозные пробои изоляции. Сортировка металлов по маркам с помощью электрохимического, электроиндуктивного или термоэлектрического метода. Измерение толщины гальванического покрытия до 30 мм, количественно-качественная оценка сцепления биметаллов, выявление повреждений металлических слитков и экспресс-анализ стали (электротермический метод). Выявление несплошностей в поверхностных слоях неметаллических изоляционных покрытий (электростатический метод).
2 Нормативные ссылки. В настоящем стандарте использованы нормативные ссылки на следующие стандарт: ГОСТ 25315-82 («Контроль неразрушающий электрический. Термины и определения») рассматривает и закрепляет несколько совокупностей методов и средств электрического неразрушающего контроля. В их числе (виды методов и цели): Дефектоскопия (цель – выявление дефектов); дефектометрия (цель – измерение параметров дефектов); структуроскопия (цель – выявление неоднородности структуры); структурометрия (цель – оценка структуры)
Виды электрического контроля:
Термоэлектрический. Основан на оценке термо-ЭДС, проявляющейся при контакте заранее нагретого образца с объектом. Трибоэлектрический. Основан на оценке электрических зарядов в процессе трения материалов. Электропотенциальный. Разновидность контроля, основанная на оценке распределения потенциалов. Электроемкостный. Предполагает оценку электрической емкости объекта или его участка. Используется преимущественно при диагностике полупроводников, диэлектриков. Электроискровой. Способствует выявлению пробоев изоляции и их параметров. Электростатический порошковый. Разновидность контроля, основанная регистрации полей рассеяния посредством индикаторов (порошки, аэрозоли и т. п.). Аналог магнитопорошкового контроля. Электропараметрический. Предполагает оценку электрических характеристик объекта. Чаще применяется для диагностики состояния изоляции. Метод рекомбинационного излучения. Основан на регистрации последнего в полупроводниках. Метод экзоэлектронной эмиссии. Предполагает регистрацию экзоэлектронов, испускаемых объектом после стимулирующего воздействия. Метод контактной разности. Основан на оценке разности потенциалов на участках объекта. Предполагает пропускание через эти участки электрического тока.
Дата добавления: 2022-11-11; просмотров: 53; Мы поможем в написании вашей работы! |
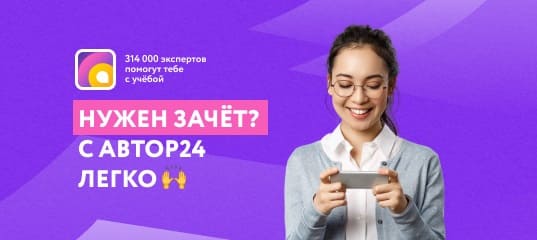
Мы поможем в написании ваших работ!