РАЗДЕЛЕНИЕ ГЕТЕРОГЕННЫХ ЖИДКИХ СИСТЕМ ФИЛЬТРОВАНИЕМ
Материалы: ткани хлопчато-бумажные (бельтинг, миткаль), синтетические (капрон, нейлон, капрон-лавсан), шерстяные. Плетеные и штампованные металлические сетки, песок гравий, пористые керамические материалы. Роль фильтровальной перегородки может выполнять и слой осадка, причем его фильтрующие свойства бывают очень высокие.
Гидравлическое сопротивление фильтра:
А=133-200 – постоянная;
- высота слоя осадка;
- скорость фильтрации в порах, м/с;
µ - вязкость, Па*с;
- диаметр пор, м.
Обозначив порозность ԑ
где w – скорость фильтрации
где F – площадь сечения пор;
П – смоченный периметр.
Но в единице объема V объем пор=, а их поверхность удельной поверхности f:
Через пористый слой используют формулу Кармана:
К=180;
Фильтрование под давлением
Скорость фильтрования:
где r – сопротивление осадка отнесенное к единице высоты.
Общее сопротивление фильтрования состоит из сопротивления фильтра, сопротивления осадка.
Т.к. – меняется, то V и τ являются переменными величинами
где – удельная производительность фильтра.
Объем осадка, отложившегося на фильтре:
где – удельный объем осадка, приходящийся на 1
фильтра.
Продолжительность фильтрации:
Интегрируем:
Удельная производительность:
Мембранные методы разделения систем
1. Микрофильтрация м
2. Ультрафильтрация м
3. Обратный осмос м
|
|
Применяются пористые мембраны из синтетических пленок на ацетатцеллюлозной основе или пористого стекла. Размер пор таких мембран от 0.5 мкм до м (Ангетрем).
Полупроницаемые мембраны характеризуются проницаемостью – удельной производительностью:
Селективность (φ) – способность пропускать те или иные вещества:
и – концентрации растворенного вещества в исходной жидкости и фильтрате.
При ультрафильтрации концентрируются высокомолекулярные вещества.
При обратном осмосе концентрируются все растворенные вещества.
Осмос Равновесие Обратный осмос
Осмос открыт в 1748 году французским химиком Нолле. Изучался ботаником Пфеффером, 1877 г. В 1887 году Ван-Гофф вывел формулу для измерения осмотического давления:
i – постоянная Ван-Гоффа; i=1+a;
a – степень диссоциации растворенного вещества;
R –газовая постоянная;
T –абсолютная температура;
x –концентрация растворенного вещества, г/л;
M – молекулярная масса растворенного вещества, г/моль.
Следует отметить, что осмотическое давление слабо диссоциирует: 3% М=30000 П=2356Па, а для 3% NaCl (а=2; М=58.5) П=2400* т.е. в1000 раз больше.
При разделении обратным осмосом требуется довольно высокое давление низкомолекулярных растворов.
|
|
При одинаковом П растворы называются изотоническими (заменитель крови), повышенном П – гипертоническими; при пониженном П – гипотоническими.
Для фруктовых соков П=1.5 МПа, для концентратов этих соков 10МПа, для 2.5МПа, для молока 0.7МПа.
Движущая сила процесса:
при
При ультрафильтрации и микрофильтрации осмотическое давление П мало пренебрегают для этих процессов: :
Необходимо исследовать работу процесса о.осм.:
- работа сжатия;
- работа продавливания, т.к. жидкости практически несжимаемы.
На опреснение морской воды расходуется 7кВт*час путем испарения 80кВт, т.е. в 10-12 раз меньше (но надо учесть качество энергии: там низкопотенциальное здесь чистая электроэнергия).
Устройство мембранных фильтров можно классифицировать на плоское и цилиндрическое.
Область применения:
1. Молочная промышленность (сгущение молока, сыворотки и т.п.).
2. Пищевая промышленность ( сгущение белков, соков, бульонов, кофе, чая). Сгущенные продукты отличаются более высоким качеством, чем традиционные.
3. Очистка сточных вод пищевых предприятий благоприятна для окружающей среды.
Разделение газовых систем (очистка газов)
Подразумевается выделение из аэрозолей частиц твердой и жидкой дисперсной фазы.
|
|
Цели:
1. Технологические: получение воздуха необходимых параметров для технологических процессов (бродильные, пневмотранспорт, расфасовка), выделение ценных частичек топлива из уноса.
2. Энергетические: выделение частичек топлива из уноса.
3. Защитные: очистка воздуха от вредных частиц, воздействующих на окружающую среду, предохранение от дискомфортных условий труда и т.д. ( и
пыль, горючая пыль сахара, муки, пищевых продуктов, которая еще и может взорваться).
Способы очистки:
1. Осаждение под действием силы тяжести
2. Осаждение под действием ц/б
3. Фильтрование
4. Мокрая очистка
5. Осаждение под действием электростатических сил.
1. Осаждение под действием силы тяжести. Применяется для тяжелых частиц размером более 100 мкм.
Время процесса по аналогии с гидравлическими отстойниками:
Степень очистки:
2. Для очистки в ц/б поле применяют циклоны. Э. Подается со скоростью не больше 20-25 м/с (завихрение, повышение сопротивления). Для частицы круглой формы по аналогии с гидравлическим процессов запишем равенство ц/с и сопротивления среды:
- минимальный размер частицы:
|
|
т.к. при постоянной скорости w величина ц/б силы обратно пропорциональна радиусу R, то целесообразно изготовлять циклоны диаметром 100-250 и компоновать их в батарею (мультициклоны).
Применяется для выделения частиц. Степень разделения составляет 70-95%. Иногда в циклон вводят пар или воду, которые коагулируют смачивание (агломерация) и смывают ее со стенок.
3. Фильтрация. Широкое распространение получили рукавные фильтры со встряхивающим устройством. Обувочный воздух должен иметь температуру выше точки росы, иначе жидкость забьет фильтры.
Степень очистки частиц 5-10 мкм С=98-99%.
4. Влажная очистка. Используется для удаления смачиваемых частиц. С=98-99%. Масляные или висценовые фильтры сеток, заполненных стекловолокном, металлическими кольцами.
Для очистки от частиц менее…используют фильтры ФП, в которых используется ультратонкое волокно, дополнительно действуют электростатические силы.
Широко используются бактерицидные фильтры со слоем стекла или базальтового волокна, металлокерамики, пенополеуретаном, тканных синтетических материалов с добавкой тексахлорофила. Мембраны стерилизуются окисью этилена вместо пара.
5. Электростатический способ. Постоянные электроды не применяются из соображений техники безопасности.
Флотация
Флотация – процесс разделения жидких неоднородных систем, основанный на избирательном примыкании пузырьков воздуха к частицам, образующим внутреннюю фазу системы. Находящиеся в воде пузырьки газа прилипают к гидрофобной ( плохосмачиваемой водой) частице и поднимают ее вверх, где она удаляется в виде пены. Гидрофильные частицы не прилипают к пузырькам и осаждаются на дно аппарата. Применяется для обезжиривания сточных вод, выделения кормовых дрожжей и т.п.
ЛЕКЦИЯ № 7
МЕХАНИЧЕСКИЕ ПРОЦЕССЫ
1. Измельчение материалов. Измельчением называется процесс деления материалов на части, осуществляемый путем механического воздействия. Различают два вида измельчения: дробление ( при котором частицы не имеют определенной формы) и резание (когда одновременно с уменьшением размера частицам придается определенная форма).
Измельчением широко пользуются во всех отраслях нашего хозяйства. Предполагают, что на этот процесс расходуется 10% всей энергии.
В общественном питании измельчение имеет огромное значение для:
1) Подготовка сырья для приготовления пищи ( чистка овощей, нарезка мяса, лука, хлеба и т.д.)
2) Придание продукту требуемой консистенции (пюре, фарш)
3) Порционирование продуктов (нарезка порций лангета и т.п.)
4) Утилизация отходов сырья и остатков пищи.
В зависимости от вида применяемых усилий измельчать можно путем:
В измельчительных машинах это достигается сочетанием нескольких способов: раздавливание и разрыв, удар и стирание и т.д.
Рассмотрим, какие силы возникают при раздавливании. Под нагрузкой материал деформируется по всему объему, внутреннее напряжение постоянно повышается и при достижении выше прочности сжатия происходит разрушение, причем образуются частицы различного размера и формы.
Раскалывание создает большую концентрацию нагрузок в месте контакта с рабочим элементом.
Разламывание происходит за счет изгибающих сил.
Процесс резания происходит за счет концентрации напряжений и одновременного продольного повреждения тканей тела.
Распиливание – более грубое резание.
Эффективность измельчения оценивается степенью измельчения, удельной нагрузкой на рабочий орган и удельным расходом энергии на проведение процесса:
- степень измельчения;
- поверхность частиц после измельчения;
i- поверхность частиц исходного продукта.
Для расчета условно принимают поверхность частицы равной площади куба по среднему размеру частицы . Тогда можно определить поверхность одной частицы по формуле:
Для определения поверхности берут пробу и делают рассев, выделяя различные фракции. Зная вес каждой фракции определяют количество частиц:
– плотность.
Тогда площадь частиц каждой фракции будет:
В зависимости от значения і различают:
1. крупное і=3-5;
2. среднее і=5-10;
3. мелкое і=10-50;
4. тонкое і ;
5. коллоидное і .
Процесс деформации и измельчения твердых тел сопровождается затратой энергии, которая расходуется на образование упругих и пластических деформаций, и преодоление сил молекулярного сцепления, после чего тело разрушается с большой суммарной поверхностью. Как при упругой, так и при пластической деформации происходит частичный переход механической энергии в тепловую, в результате чего повышается температура тела и аппарата. Поэтому в некоторых аппаратах предусматривается охлаждение рабочих органов. Кроме того, часть энергии расходуется на преодоление сопротивлений, связанных с износом.
Расход энергии на измельчение продукта и получение определенной дисперсности определяется в каждом конкретном случае опытным путем с учетом свойств материала и конструкции аппарата.
В общем случае расход энергии А (кДж) согласно гипотезе академика Ребиндера П.А. выражается
Где к – энергия, расходуемая на 1новой поверхности;
– величина вновь образованной поверхности в
;
m – число циклов деформаций;
Е – модуль упругости материала 1 рода,
V –объем материала;
- разрушающее напряжение, Па.
Первая составляющая определяет расход энергии на образование новой поверхности.
Вторая составляющая - расход энергии на пластические деформации.
Третья составляющая – расход энергии на образование продукта износа.
Для уменьшения энергозатрат необходимо:
1. измельчать материал до крупности необходимой технологии, дальнейшее к невозвратимым потерям;
2. уменьшать количество циклов деформации «Т»;
3. уменьшать упругие деформации материала рабочего органа и повышать его износоустойчивость;
4. снижать величину разрушаемого напряжения путем предварительного обработки (термическая обработка, замораживание и т.д.).
Измельчающие машины
Крупное, среднее и мелкое измельчение происходят на дробилках, а тонкое и коллоидное – на мельницах. Для измельчения необходимой степени часто оно ведется в несколько стадий последовательно.
Резательные машины применяются как спецообразование (овощерезки, хлеборезки, шпигорезки, мясорубки и т.д.).
1. В конусных дробилках материал измельчается за счет раздавливания и испарения. Исходный материал загружается в пространство, образованное внешним неподвижным и внутренним эсцентрично расположенным вращающимся корпусом.
2. В вальцевых дробилках исходный материал захватывается вальцами, и проходя между ними, дробится и истирается. Насечки на вальцах называются «рифлями». Иногда один из вальцов вращается с меньшей частотой, за счет чего увеличивается эффект истирания. Возникающий на вальцах расклад сил трения
Равнодействующая, которой старается втянуть частицу между волками, и выталкивающей силы Р реакции волков, равнодействующая которой
направлена вверх. Для нормальной работы необходимо соблюдать неравенство
Или но т.к. f = tgφ (угол трения)
то α<2φ, т.е. угол захвата меньше двойного угла трения.
Величина угла захвата зависит от коэффициента трения, размера частиц, диаметра валков и зазора между ними, т.е. угол захвата уменьшается с увеличением диаметра валков и зазора, и с уменьшением диаметра частиц.
Обычно α=30-36°, а окружная скорость валков находится в пределах 2.5-5 м/с. Соотношение между диаметром валков и частицей:
для гладких D=(20-25)d;
для рифленых D=(10-12)d;
для зубчатых D=(2-5)d/
Потребляемая мощность N в кВт:
где D, l, – даны в см, а n – об/мин
3. В молотковых дробилках исходный материал поступает в бункер и оттуда – в рабочую камеру, где подвергается воздействию вращающихся молотков, насаженных на стержни, шарнирно соединенные с валом. Измельчение происходит за счет стесненного удара. Измельченный продукт удаляется через перфорированное днище.
4. Дисковые дробилки (дезинтеграторы). Из загрузочного бункера исходный материал попадает в рабочую камеру между пальцами неподвижного и вращающегося диска. Измельчение происходит за счет стесненного удара. Измельченный продукт выходит через выгрузной патрубок.
Известны дезинтеграторы, в которых оба диска с пальцами вращаются в разные стороны.
Шаровые мельницы
Для более тонкого измельчения широко используются шаровые мельницы, принцип работы которых основан на использовании стесненного удара и истирания. Шары вместе с материалом при вращении барабана захватываются вверх и оттуда под действием силы тяжести падают вниз и ударяют по материалу, находящемуся между шарами.
Теоретическая частота вращения выводится из равенства:
Жернова
На принципе истирания работают жернова. Исходный продукт загружается в коническое отверстие и истирается в зазоре между жерновами. Такие машины используются для измельчения кофе, какао, зерна, сахара и т.д.
В общественном питании иногда возникает необходимость измельчения не только твердых продуктов, но и продуктов, состоящих из твердых и мягких компонентов (типа мясо-кость).
Такие продукты необходимо замораживать до t=-(20-30)°С, за счет чего его удается измельчить до размера 100-150 мкм, что позволяет использовать добавки в фаршах для изготовления котлет, люля-кебаб, колбасок и т.п.
Хороший эффект дает измельчение замороженных отходов и остатков пищи для приготовления из них кормовой муки.
В общественном питании достаточно тонкому измельчению подвергаются вареные овощи, свежие ягоды, фрукты, творог. Для этой цели используются различные протирочные машины, работающие по принципу раздавливания и истирания.
Протирочные машины
Внутри перфорированного цилиндра вращаются шарнирно-закрепленные лопасти (бичи), которые раздавливают продукт и протирают его через перфорацию. Выходит пастообразная масса.
Резание. Очень широко используется в общественном питании, т.к. этому процессу подвергается большинство видов сырья, полуфабрикатов, продуктов. Основная цель - разделение продукта на части, причем эти части должны иметь определенную форму и качество среза.
Резание можно разделит на три вида: резание пуансоном, резание резцом, резание ножом.
Пуансон вызывает срез материала. Резец, воздействуя на материал, образует стружку, как клин. Резание ножом – воздействие на материал кромки ножа.
Область применения имеет свои ограничения: пуансон – твердые материалы ( металл, кость, овощи), резец – твердые и пластичные материалы, ножи – мягкие пищевые продукты ( мясо, рыба, хлеб, овощи).
Ножи имеют форму двугранного одностороннего или двухстороннего клина. Рабочая грань А (лицевая), опорная Б. Линия пересечения граней называется рабочей кромкой или лезвием. Угол α или 2α называется углом заточки.
В общественном питании применяются ножи всевозможной формы и заточки, которые подробно будут изучены в курсе механического оборудования.
Академик Горячкин В.П. делит резание на две разновидности:
1. Клин перемещается перпендикулярно (рубка)
2. Резание со скольжением.
Рубка основана на том, что клин, перемещаясь в слой продукта, создает контактные напряжение, приводящие к срезу (перерубание) или скалыванию продукта.
При резке сначала идет уплотнение, а потом перерезание продукта, более качественная поверхность. Работа сжатия:
Если h – высота слоя, – высота сжатого продукта, Э – условный модуль сжатия материала, то полезная работа:
Где – усиление резания, Н.
Усиление резания, отнесенное к единице длины ножа, называется удельным. Оно резко отличается для разных продуктов – 1600-600 Н/м. Полезная работа:
Вводится понятие к.п. работы лезвия:
Скорость резания – скорость перемещения лезвия в данной точке. При увеличении скорости резания уменьшается усиление резания.
Способность лезвия разделять материалы на части называется режущей способностью, она меняется в процессе использования за счет износа. Отсюда понятие износоустойчивость – способность противостоять разрушаемому действию материала, сопротивляющегося перерезанию.
Дата добавления: 2022-11-11; просмотров: 24; Мы поможем в написании вашей работы! |
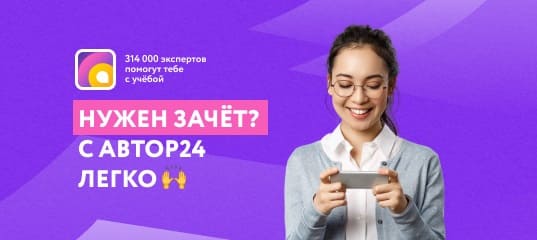
Мы поможем в написании ваших работ!