Зубодолбление многорезцовой головкой.
Тема 2.6 Обработка зубьев зубчатых колёс
Тема: «Виды зубчатых колёс. Методы нарезания зубчатых колёс»
Цели урока:
Дидактическая:
создание условий для формирования знаний о методах обработки зубчатых поверхностей на различных станках, об методах нарезания цилиндрических зубчатых колёс.
Воспитательная:
воспитание осознанного отношения к процесса обучения, интереса к будущей профессии.
Развивающая:
развитие познавательного интереса, гибкости мышления, сообразительности, смекалки
Оснащение урока:
1 ММК.
2 Презентация.
Вид урока: смешанный урок
Методы и приёмы: сообщение нового материала с элементами демонстрации и привлечением студентов.
План урока.
Виды зубчатых колёс.
2. Основные методы обработки зубьев цилиндрических колес.
3. Фрезерование зубьев цилиндрических колес дисковыми и пальцевыми модульными фрезами.
4. Фрезерование зубьев цилиндрически колёс червячными фрезами.
5. Нарезание зубьев цилиндрических колес долбяком.
6. Зубодолбление многорезцовой головкой.
7. Протягивание зубьев.
Задание на дом: 2. с.95-102
Почти во всех машинах и механизмах встречаются болты, подшипники, валы, зубчатые колеса. Сегодня мы изучим виду зубчатых колес, о методах обработки зубчатых поверхностей на различных станках.
Виды цилиндрических зубчатых колёс.
В передачах современных машин широко применяют зубчатые колёса, разнообразные по форме, размерам и профилям.
|
|
Форма венца зубчатого колеса | цилиндрические зубчатые колёса | конические зубчатые колёса | |
Форма зубьев относительно оси колеса | прямые, косые и шевронные | винтовые | прямые, круговые и тангенциальные |
Взаимное расположение осей валов | оси валов параллельны | оси валов скрещены | оси валов пересекаются (межосевой угол может быть как равен 90º; так и отличен от 90º) |
Профиль зуба | В основном с эвольвентым профилем |
Все зубчатые колеса делятся на одновенцовые и многовенцовые колеса.
Основные методы обработки зубьев цилиндрических и конических колес.
Зубчатые колеса обрабатывают на разнообразных зубообрабатывающих станках. Зубья на колесах нарезают двумя способами: копированием (рис. 3, а, б) и обкаткой (3, в). При копировании режущему инструменту придают форму впадины между зубьями, а затем производят обработку. При этом профиль инструмента копируется на обрабатываемой поверхности.
![]() |
Рисунок 3 – Способы нарезания колёс.
Зубонарезание способом копирования можно выполнять: последовательным нарезанием каждого зуба колеса модульной дисковой или пальцевой фрезой на универсальном фрезерном станке; одновременным долблением всех зубьев колеса; одновременным протягиванием всех зубьев колеса; круговым протягиванием. Способ копирования применяется главным образом при изготовлении зубчатых колес невысокой точности.
|
|
Современным, точным и производительным способом изготовления зубчатых колес является нарезание зубьев по способу обкатки червячной фрезой, круглым долбяком, реечным долбяком (гребенкой), резцовой головкой, накатыванием зубчатыми валками.
3. Фрезерование зубьев цилиндрических колес и реек дисковыми и пальцевыми модульными фрезами.
Фрезерование зубьев колес представляет собой разновидность фасонного фрезерования. В процессе работы фреза переносит (копирует) свой профиль во впадину зубьев, создавая, таким образом, две половины профилей двух соседних зубьев После нарезания одной впадины заготовка поворачивается на размер шага с помощью делительного механизма, фреза снова врезается и проходит по новой впадине между зубьями.
Такой способ применяют в единичном и мелкосерийном производстве, а также при ремонтных работах. Процесс ведут на горизонтально-фрезерных станках с делительными головками. Недостатками этого способа являются:
|
|
1. Низкая точность обработки зуба, так как дисковые модульные фрезы изготовляют с приближенными профилями зубьев, причем каждый типоразмер фрезы рассчитан на несколько смежных чисел зубьев нарезаемых колес в определенном интервале.
2. Низкая производительность и высокая себестоимость обработки (большое основное и вспомогательное время). Низкая производительность определяется прерывностью процесса обработки, вызывающей потери времени на врезание фрезы при изготовлении каждого очередного зуба, на индексирование (поворот) заготовки, на подвод заготовки к фрезе, а также относительно малым числом зубьев фрезы, работающих одновременно.
4. Фрезерование зубьев цилиндрически колёс червячными фрезами наиболее широко применяется в промышленности. Червячная фреза представляет собой червяк, имеющий профиль осевого сечения винтовых ниток в виде зубчатой рейки, и продольные канавки, образующие режущие зубья рейки (рис. 1 в).
Зубчатая рейка обеспечивает зацепление с эвольвентными колесами любого числа зубьев и червячная фреза может нарезать колеса с любым числом зубьев (того же модуля и угла зацепления) одинаково точно. В этом заключается одно из больших преимуществ нарезания зубьев колес червячной фрезой.
|
|
В процессе нарезания червячная фреза и нарезаемое колесо находятся в состоянии относительного движения зацепления, соответствующего червячной передаче с передаточным числом ,
где nф и nз — частоты оборотов фрезы и зубчатого колеса; Zф и Z3 — число заходов червячной фрезы и число зубьев нарезаемого зубчатого колеса.
При резании червячная фреза вращается и движется поступательно в соответствии с вращением нарезаемого зубчатого колеса (рис. 4).
Червячная фреза кроме вращения имеет еще и поступательное движение подачи вдоль образующей боковой цилиндрической поверхности нарезаемого колеса. Процесс резания при этом происходит непрерывно и в нем участвует одновременно несколько режущих зубьев, благодаря чему этот способ нарезания зубьев является одним из наиболее производительных.
![]() |
Рисунок 4 - Схема зубофрезерования.
Червячную фрезу устанавливают или на полную высоту зуба (т. е. глубину резания) при нарезании зубьев за один рабочий ход, или при нарезании зубьев с модулем более 8 мм за два рабочих хода — на 0,6 высоты зуба при первом и на 0,4 при втором рабочем ходе. Для чистового рабочего хода оставляется припуск от 0,5 до 1 мм на толщину зуба по начальной окружности (для размеров модуля 8... 15 мм). Обычными червячными фрезами нарезают зубья как с нормальным, так и с корригированным профилем. В последнем случае фрезу соответственно условиям корригирования смещают при установке, приближая ее к заготовке или удаляя от нее.
Зубофрезерование можно производить при продольной (рис. 5, а), осевой (рис. 5, б) и диагональной (рис. 5, в) подачах.
![]() |
Рисунок 5 – Схема зубофрезерования различными подачами.
При продольной подаче червячная фреза перемещается вдоль оси обрабатываемой детали, при осевой — вдоль собственной оси. Диагональная подача — это сочетание вертикальной подачи вдоль обрабатываемой детали и осевой подачи фрезы вдоль своей оси. При диагональной подаче выше стойкость инструмента и качество поверхности рабочего профиля зубьев колес.
![]() |
На зубофрезерных станках можно производить нарезание зубьев попутным (рис. 6, а) или встречным (рис. 6, б) фрезерованием; при этом попутное фрезерование эффективнее, так как оно обеспечивает более благоприятные условия стружкообразования, меньшие колебания сил резания, меньшие вибрации при резании, что повышает стойкость инструмента и качество обработанной поверхности.
Рисунок 6 – Попутное и встречное зубофрезерование.
Значительная часть времени зубофрезерования расходуется на врезание, особенно при применении червячных фрез большого диаметра, так как с увеличением диаметра фрезы возрастает длина врезания. Для прямозубых колес средних модулей время врезания составляет 30...40% машинного времени. При осевом врезании подачу обычно несколько понижают по сравнению с последующей подачей при резании. Трудоемкость врезания можно уменьшить примерно на 30% заменой осевого врезания (рис. 7, б) радиальным (рис. 7, а), сохраняя последующую продольную подачу; в этих условиях станок и инструмент в течение всего процесса обработки загружаются более равномерно.
Рисунок 7 – Осевое и радиальное врезание.
Червячными фрезами нарезают как прямые, так и косые зубья цилиндрических колес. В последнем случае ось фрезы устанавливают под углом к торцу нарезаемого колеса, равным сумме углов подъема винтовой нитки фрезы и винтовой нитки (угла наклона зуба) нарезаемого колеса (при разных направлениях винтовых линий фрезы и колеса) и разности этих углов, если направления винтовых линий фрезы и нарезаемого колеса одинаковы.
Наиболее распространенным зубообрабатывающим станком является зубофрезерный станок для нарезания зубчатых колес с прямыми и косыми зубьями, а также червячных колес и червяков методом обкатки.
![]() |
Рисунок 8 – Общий вид зубофрезерного станка.
Станок выполняет три движения: вращения червячной фрезы, вертикальную подачу фрезы, вращение заготовки.
5. Нарезание зубьев цилиндрических колес долбяком.
В отличие от нарезания зубьев червячными фрезами зубодолбление позволяет обрабатывать зубчатые венцы там, где нет достаточного пространства для выхода фрезы, например, блок шестерен, вал шестерня с фланцем, внутренние венцы и т. д. (рис. 9). В таких случаях зубодолбление становится единственным экономически целесообразным методом обработки. При обработке открытых венцов зубчатых колес малых модулей (до 2,5 мм) зубодолбление не только не уступает, но часто превосходит по производительности зубофрезерование.
Рисунок 9 – Схема зубодолбления.
При обработке колес модулем от 2,5 до 5 мм с целью повышения производительности могут применяться комбинированные схемы обработки, совмещающие черновую и чистовую обработку зубьев. В общем случае зубодолблению можно обеспечить более высокую точность обработки, но из-за потерь на холостые ходы по производительности все лее уступает зубофрезерованию.
В машиностроении зубодолбление занимает второе место (после зубофрезерования червячными фрезами) и применяется там, где метод фрезерования применять дорого или невозможно.
Применение операции зубодолбления часто экономически целесообразно при обработке колес с узким венцом (ободом), модулем до 2 мм и большим числом зубьев (даже в тех случаях, когда возможна обработка и червячной фрезой).
Различают дисковые, чашечные и хвостовые зуборезные долбяки. Дисковыми и чашечными долбяками обрабатывают только наружные (внешние) зубья колес. Хвостовые долбяки применяют для обработки колес внутреннего зацепления (рис. 10).
Для нарезания прямозубых колес применяются дисковые долбяки, косозубых — косозубые долбяки, прямозубых колес в упор - чашечные, долбяки, для колес с внутреннего зацепления — хвостовые долбяки, шевронных колес — косозубые парные долбяки.
![]() |
Рисунок 10 - Схемы долбяков:
а — насадной дисковый долбяк; б — насадной чашечный долбяк; в — хвостовой долбяк.
При нарезании косозубых колес косозубый долбяк совершает дополнительный поворот в направлении наклона зуба нарезанного колеса.
В процессе обработки долбяк совершает возвратно-поступательное движение параллельно оси обрабатываемого колеса (рис. 11) – главное двимжение. Долбяк и колесо вращаются вокруг своих осей, при непрерывном движении обката производится сближение осей (долбяка и колеса). Следует учитывать, что процесс резания прерывистый, поэтому профиль зубьев обычно имеет огранку в поперечном направлении.
Долбяк подводится к заготовке до соприкосновения с ней. С этого момента начинается процесс резания, с автоматическим перемещением долбяка. При холостом ходе заготовка отводится от инструмента. Число двойных ходов составляет обычно от 2500 до 700 в минуту. Заготовка в процессе обработки совершает вращательное движение вокруг своей оси, создавая непрерывное движение обката.
![]() |
Рисунок 11 – Схема долбления зубьев.
Зубодолбление многорезцовой головкой.
В массовом производстве для нарезания наружных цилиндрических и блочных колёс, а также шлицевых валов небольшой длины применяют зубодолбёжные головки, производительность которых в 6 раз превышает обычное зубодолбление. Высокая производительность достигается тем, что в работе одновременно участвует столько резцов (долбяков), сколько нужно нарезать зубьев на заготовке, причем резцы имеют форму впадин зубчатого колеса. Многорезцовую обработку ведут по схеме, приведенной на рис. 12
Рисунок 12 – Схема долбления многорезцовой головкой.
Резцы 1 расположены радиально по отношению к заготовке 2. Процесс резания совершается при возвратно-поступательном вертикальном движении заготовки 2 при неподвижной резцовой головке. Радиальная одновременная подача резцов 1 происходит в нижнем положении заготовки 2, когда заготовка выходит из зацепления с резцами.
Протягивание зубьев.
Протяжки применяют для обработки зубчатых колес как с внутренними, так и наружными зубьями. При обработке внутреннего зубчатого профиля колес протяжки выполняются аналогично эвольвентным шлицам отверстий. Наружные протяжки для обработки зубьев могут быть однопрофильные секторные и охватывающие.
Однопрофильные протяжки последовательно обрабатывают впадину между зубьями колес с поворотом заготовки на угловой шаг. Протяжки могут выполняться либо в виде шпоночных, либо круговых. Круговое протягивание не имеет холостых ходов и является производительным и перспективным методом обработки.
Главное движение фрез-протяжек — вращательное, одновременно происходит перемещение инструмента в направлении обрабатываемой впадины, режущие кромки, последовательно вступают в работу — образуют различные участки профиля впадины.
Протяжки секторного типа обрабатывают одновременно группу зубьев, затем обрабатываемое колесо поворачивается для обработки следующего сектора зубьев. При применении протяжек охватывающего типа — рабочее движение подачи обычно сообщается заготовке. Режущие зубья охватывающей протяжки располагаются по всему обрабатываемому контуру зубчатого колеса. Они имеют форму нарезаемых впадин. Протяжки выполняются сборными в виде набора колец или отдельных шпоночных (протяжек).
Например, на операции зубонарезания обода на маховике автомобильных двигателей охватывающее зубопротягивание позволяет заменить 15 зубофрезерных станков (рис. 13). Охватывающее протягивание обеспечивает обработку одного венца маховика в пределах 3 с, стойкость инструмента между переточками составляет 10-12 тыс. изделий.
![]() |
Рисунок 13 - Схема охватывающей протяжки.
Однако конструкции охватывающих протяжек, предназначенных для одновременной обработки всех впадин зубьев колес очень сложны в изготовлении и дорогостоящи. Поэтому автомобилестроительные фирмы успешно используют высокопроизводительный и относительно простой метод однопрофильного кругового протягивания для изготовления зубчатых колес. Протяжка, выполненная в виде диска непрерывно вращаясь с постоянной скоростью против часовой стрелки, обрабатывает за один оборот только одну впадину колеса.
![]() |
Рисунок 14 - Схема блочного резца на головке для кругового протягивания.
Производительность данного метода и стойкость инструмента сравнима с охватывающим протягиванием, но за счет технологичности, процесс значительно дешевле.
Круговое протягивание прямых зубьев цилиндрических колес также относится к методу копирования, и, следовательно, точность зубонарезания в большой степени зависит от точности изготовления инструмента, в частности, зубьев круговой протяжки.
Резцовые блоки протяжки обычно имеют четыре-шесть зубьев и два-три отверстия для крепления блока на корпус протяжки (рис. 14). Перетачиваются резцы только по передней грани.
Отсутствие движения подачи, совмещение черновой и чистовой обработки, одновременная обработка двух боковых сторон впадин обеспечивает значительное преимущество данному методу обработки зубьев колес.
Для обеспечения эвольвентной боковой поверхности зубьев цилиндрических колес процесс протягивания может дополняться процессом фрезерования.
Фрезопротяжка создана путем объединения двух секторов (круговой протяжки, дисковой модульной фрезы). Свободный сектор разъединяет первый и последний режущие зубья протяжки. За один оборот фрезопротяжка производит черновое и чистовое нарезание зубьев. Чистовые зубья соответствуют профилю впадин зубьев.
Черновые зубья имеют передний угол заточки больше 0°, что обеспечивает высокую стойкость, профиль боковых сторон зубьев фрезопротяжки может выполняться по одной дуге окружности.
Рисунок 15 - Схема нарезания впадин зубьев колес фрезопротяжкой .
При фрезопротягивании зубьев колес на обработку затрачивается более 80 % времени резания, что снижает производительность. Кроме того, продольное перемещение больших масс (головки с колесом), необходимых в процессе резания, не только усложняет конструкцию станка, но и снижает его жесткость.
Контрольные вопросы.
1. Выберите зубчатые колеса цилиндрические, конические, прямыми, косыми, шевронными зубьями, одновенцовые и многовенцовые.
2. Перечислите методы нарезания цилиндрических колёс методом копирования.
3. Перечислите методы нарезания цилиндрических колёс методом обката.
4. В каких случаях применяется долбление зубьев долбяком?
5. Какие методы наиболее эффективны в массовом производстве? Какие в серийном ?
Дата добавления: 2022-06-11; просмотров: 32; Мы поможем в написании вашей работы! |
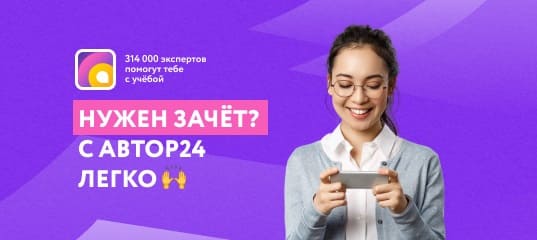
Мы поможем в написании ваших работ!