Электроплавка медных и медно-никелевых концентратов Особенности тепловой работы электропечи
Химизм в электропечи точно такой же как и при отражательной плавке.
Электроплавка отличается от других пирометаллургических процессов источником энергии для осуществления физико-химических превращений. Необходимая для проведения процесса температура поддерживается за счет тепла, получаемого путем преобразования электрической энергии в тепловую.
Наибольшее распространение в металлургии меди и никеля получили рудно-термические печи, в которых выделение тепла происходит при протекании тока через слой шлака, обладающего высоким удельным сопротивлением. Такие печи применяются при переработке сульфидных медноникелевых руд, плавке медных концентратов с повышенным содержанием кремнезема, в процессе электротермического обеднения шлаков.
Электроплавка медно-никелевых концентратов
Медно-никелевые концентраты проходят ряд подготовительных операций, включающих сушку, обжиг и спекание. Иногда концентраты сушат, окатывают на чашевых грануляторах и полученные окатыши обжигают на агломерационных машинах. При обжиге в газы удаляется до 40–50 % серы.
Агломерация, или спекание сульфидных медно-никелевых богатых руд и концентратов, осуществляется за счет тепла, выделяющегося при окислении сульфидов. На практике с целью получения более прочного агломерата и увеличения металлизации штейна при последующей плавке в шихту спекания добавляют небольшое количество коксовой мелочи.
|
|
Основными процессами агломерирующего обжига являются: сушка шихты, термическое разложение высших сульфидов (пирротина, халькопирита, пентландита), окисление части сульфидов железа, расплавление легкоплавких компонентов шихты и ее спекание при охлаждении расплавленной фазы.
За счет тепла окисления сульфидов и горения коксовой мелочи и слое шихты развиваются температуры 1 100–1 200 °С.
Для агломерации используют ленточные машины с площадью всасывания 50 и 75 м2. Производительность их составляет 12–15 т/м2·сут. Извлечение цветных металлов в агломерат составляет 98,5%. Состав агломерата, %: 5–6 Ni; 3,5–4,0 Сu; 8,8–11,5 S; 30–35 Fe; 14–17 SiO2.
Прогрессивным способом укрупнения медно-никелевых концентратов является их скатывание в гранулы диаметром 8–15 мм на чашевых грануляторах. Полученные гранулы подвергают термическому упрочнению на ленточной агломерационной машине.
Плавку медно-никелевых руд и концентратов можно осуществлять в отражательных печах; теория и практика этого процесса аналогичны плавке медных концентратов. Однако при содержании в сырье более 10 % MgO отражательная плавка малопроизводительна и требует большого расхода топлива.
|
|
На отечественных заводах для плавки медно-никелевой шихты используют электроплавку в рудно-термических печах. Химизм протекающих процессов образования штейна и шлака не отличается от таких процессов при отражательной плавке и электроплавке медных концентратов.
Ванна расплава в рудно-термической печи состоит из двух слоев. Высота верхнего шлакового слоя составляет 1 700–1 900 мм, а нижнего штейнового – 600–800 мм. Плавление шихты происходит за счет тепла, выделяемого непосредственно в шлаковом расплаве при пропускании через него электрического тока. Ток подводится с помощью трех или шести угольных электродов, концы которых погружены в шлак на 300–500 мм.
Электрическая энергия преобразуется в тепловую двумя путями. Большая часть тепла выделяется на границе электрод–шлак, где вследствие образования газового слоя возникают микродуги, остальная часть – в шлаковом расплаве, который служит проводником тока с высоким электрическим сопротивлением. Максимальный перегрев шлака происходит вблизи электродов. Шлак разогревается до 1 450 °С и выше, что дает возможность перерабатывать тугоплавкие шихты и получать шлаки с повышенным содержанием оксида магния (до 24 %). Отпадает необходимость добавок большого количества флюса (известняка).
|
|
Жидкими продуктами электроплавки являются штейн и шлак. Штейн выделяют из печи с температурой 1 100–1 150 °С; его состав, %: 7–16 Ni; 7–12 Сu; 0,3–0,5 Со; 47–55 Fe; 23–27 S.
Шлак представляет собой сплав оксидов кремния SiO2, железа FeO, магния MgO и алюминия Аl2О3. Температура шлака колеблется в интервале 1 250–1 400 °С; это отвальный продукт, содержащий, %: 0,07–0,11 Ni;
0,06–0,10 Сu; 0,03–0,04 Со; 41–45 SiO2; 24–30 FeO; 10–22 MgO; 5–12 Аl2О3; 3–5 CaO.
Электропечные газы образуются за счет термической диссоциации сульфидов (десульфуризация 10–20 %), карбонатов и горения углеродистых составляющих шихты и электродов.
Небольшой объем отходящих газов определяет невысокий пылевынос – всего 0,4–0,5% от массы твердой шихты. Пыль улавливают в пылевых камерах и электрофильтрах и возвращают в плавку.
Для плавки используют прямоугольные печи, чаще с шестью самоспекающимися электродами диаметром 1200 мм. Площадь пода печей – 120–180 м2, удельная мощность – 100–325 кВ·А/м2.
Некоторые технико-экономические показатели электроплавки приведен ниже:
удельный проплав – 8–10 т/м2·сут; расход электроэнергии – 570–820 кВт·ч/т шихты; извлечение в штейн никеля – 94–97 % извлечение в штейн меди – 94–96 %; извлечение в штейн кобальта – 75–80 %.
Дата добавления: 2022-06-11; просмотров: 70; Мы поможем в написании вашей работы! |
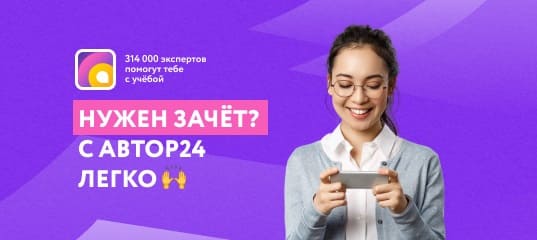
Мы поможем в написании ваших работ!