ФОРСИРОВАННЫЕ ИСПЫТАНИЯ И ИХ РОЛЬ В ОЦЕНКЕ НАДЕЖНОСТИ И ДОЛГОВЕЧНОСТИ ГИДРАВЛИЧЕСКИХ АГРЕГАТОВ
ИСПЫТАНИЯ ГИДРАВЛИЧЕСКИХ СИСТЕМ И АГРЕГАТОВ
1. НАЗНАЧЕНИЕ, ВИДЫ И ЦЕЛЬ ИСПЫТАНИЙ
Испытания гидравлических систем и агрегатов являются важнейшим методом контроля их технического состояния как в процессе отработки новых изделий, так и в процессе их длительной эксплуатации. Испытаниям могут подвергаться отдельные агрегаты, узлы систем или целые системы в собранном виде.
В качестве примера приведена классификация испытаний принятая в авиационной промышленности, которая носит общий характер и применима как для испытания самолетов, двигателей, так и отдельных систем и агрегатов.
В зависимости от поставленных целей испытания подразделяются на научно-исследовательские, опытные и серийные.
Научно-исследовательские испытания обычно предшествуют всем другим видам испытаний. Цели этих испытаний могут быть различными, но их главная задача сводится к изучению и анализу происходящих в агрегатах или системе явлений и процессов, определению различных характеристик, а также изучению факторов, влияющих на надежность и долговечность.
Проведение научно-исследовательских испытаний является обязательным условием при разработке принципиально новых конструкций агрегатов и узлов гидравлических систем. Такие испытания, как правило, проводятся в научно-исследовательских институтах, лабораториях высших учебных заведений и конструкторских организациях.
|
|
Результаты научно-исследовательских испытаний дают возможность уточнить и дополнить выдвинутые теоретические положения и методы расчета, определить рабочие параметры и характеристики, определить нагрузки, действующие на потребители, и решить многие другие вопросы. На основе проведения таких испытаний могут быть также разработаны технические требования на проектируемые агрегаты и системы. В отдельных случаях материалы испытаний могут послужить основой для создания новых методов расчета и теоретических обобщений.
Опытные испытания представляют собой второй этап в создании новых конструкций. Целью опытных испытаний являются отработка и доводка новых агрегатов и систем. В процессе этих испытаний используются результаты, полученные при научно-исследовательских испытаниях.
В соответствии со своей основной целью опытные испытания могут подразделяться на доводочные, лабораторные, летные, государственные и эксплуатационные.
Доводочные испытания могут проводиться по двум направлениям: отработка агрегатов и отдельных узлов систем (в лабораторных условиях) и отработка собранной гидравлической системы на опытной машине. При проведении таких испытаний стараются воспроизвести реальные условия работы агрегатов, которые можно ожидать в процессе длительной эксплуатации машины.
|
|
После окончания опытных испытаний, как правило, удается выполнить отладку рабочих процессов, отработку конструкции агрегатов или узлов, проверить правильность выбора материалов и технологии изготовления, определить предварительный срок службы тех или иных агрегатов, довести параметры и характеристики агрегатов и системы до обусловленных в технических требованиях. Зачастую при этом возникает необходимость в проведении специальных испытаний по программам, учитывающим те или иные условия эксплуатации, например, низкие или высокие температуры окружающей среды.
После успешного проведения доводочных и лабораторных испытаний приступают к опытнымиспытаниям гидравлической системы на машине в реальных условиях.
Естественно, что в период проведения опытных испытаний могут обнаружиться отдельные недостатки конструкции, а также те или иные неисправности, которые устраняются до поступления изделий в серийное, производство.
В процессе государственных испытаний специальная комиссия проверяет соответствие характеристик и параметров испытываемого объекта установленным для него техническим требованиям; при этом возможны доработки испытываемого объекта, улучшающие его характеристики.
|
|
После окончания государственных испытаний и положительного заключения государственной комиссии по испытуемому объекту последний передается на эксплуатационные испытания, которые длительны и проводятся в реальных условиях эксплуатации, для которых предназначена данная машина.
Серийные испытания проводятся на заводах-изготовителях. Различают следующие виды серийных испытаний: сдаточные, контрольные, длительные стендовые и эксплуатационные.
Каждый выпускаемый заводом агрегат проходит сдаточные испытания; при этом проверяются основные его параметры, правильность сборки и соответствие техническим требованиям.
В процессе контрольных испытаний, которые, как правило, проводятся выборочно, проверяются более тщательно основные параметры и характеристики агрегатов и систем. Периодичность этих испытаний и их объем зависят от назначения изделий, а в ряде случаев согласовывают с заказчиком.
Агрегаты гидравлических систем на заводах-изготовителях подвергаются длительным стендовым испытаниям. Они могут разделяться на три вида:
|
|
1) ресурсные испытания до гарантированного срока службы;
2) испытания за месячную программу.
Длительность этих испытаний устанавливается до 50% гарантированного ресурса. Таким испытаниям обычно подвергаются авиационные двигатели;
3) испытания до разрушения агрегата.
Все эти испытания проводятся по согласованию с заказчиком и по специально утвержденным программам и методикам. В процессе длительных испытаний определяются надежность серийных изделий и их срок службы. По результатам испытаний разрабатываются предложения по улучшению испытанных конструкций.
Эксплуатационные испытания носят также длительный характер и проводятся эксплуатирующими организациями в реальных условиях работы машины. Все замечания по техническому состоянию изделий, а также пожелания по улучшению конструкции и повышению надежности систематизируются и отсылаются на завод и в конструкторское бюро для изучения и реализации их в производстве на последующих сериях.
В связи с повышенным вниманием к вопросам надежности и долговечности различных технических изделий серьезное внимание уделяется длительным испытаниям для определения фактического ресурса изделий.
Различные виды таких испытаний проводятся уже давно на серийных заводах и в конструкторских организациях, однако они не всегда достигают желаемой цели, так как в большинстве случаев не учитывают реальные условия эксплуатации. К тому же с увеличением сроков службы агрегатов свыше 2000 ч, возникают затруднения с выполнением длительных испытаний. Даже при круглосуточной работе для проведения таких испытаний нужно более двух месяцев.
Особенно серьезные затруднения в этой области испытывает авиационная промышленность. Последнее объясняется тем, что после выполнения тех или иных доработок гидравлические агрегаты необходимо испытать на надежность. Без этих испытаний невозможно запускать серию, а проведение испытаний затягивается на несколько месяцев. В таких случаях целесообразно проведение ускоренных или форсированных испытаний гидравлических агрегатов.
ФОРСИРОВАННЫЕ ИСПЫТАНИЯ И ИХ РОЛЬ В ОЦЕНКЕ НАДЕЖНОСТИ И ДОЛГОВЕЧНОСТИ ГИДРАВЛИЧЕСКИХ АГРЕГАТОВ
2015-03-27
2355
Поделись
1
2
3
4
При определении надежности и долговечности гидравлических агрегатов немаловажную роль играет анализ статистических данных по отказам, возникающим в процессе эксплуатации.
Имея эти данные, в достаточном количестве можно построить -характеристику, которая позволит определить среднее значение интенсивности отказов в период нормальной эксплуатации гидравлической системы. Однако -характеристика, построенная только по данным эксплуатации, как правило, не может дать исчерпывающих сведений, необходимых для установления технически обоснованного срока службы. Это может быть объяснено тем, что в большинстве случаев агрегаты снимаются с эксплуатации и отправляются на ремонт после отработки установленного срока службы, но до наступления явлений физического износа (до наступления периода III, рис.1).
Рис. 1. Графики зависимости частоты:
1 – частота отказов; 2 – интенсивность отказов от времени.
Последнее в первую очередь характерно для гидравлических систем летательных аппаратов и систем автоматических устройств, обслуживающих ответственные операции на производстве.
Построение полной -характеристикй с правой частью (см. рис. 1), обусловленной появлением износовых отказов, может быть получено лишь при условии обобщения статистических данных и по данным лабораторным ускоренным испытаниям, проводимым по специальной программе.
Испытания агрегатов на надежность позволяют установить: закон распределения времени безотказной работы с учетом возможности появления отказов различного характера и в зависимости от величины нагрузки и условия испытаний; период приработки и период наступления интенсивного износа; характеристики отклонения параметров от установленных допусков.
Зачастую целесообразно испытывать на надежность готовое изделие или машину. В этом случае экспериментальные характеристики будут содержать: закон распределения времени безотказной работы и его числовые характеристики в зависимости от условий работы; распределение отказов по видам деталей; характеристики ремонтопригодности. Последнее играет немаловажную роль при определении технического ресурса.
Под техническим ресурсом понимается суммарная наработка системы (элемента) от начала эксплуатации до ее прекращения, обусловленного изнашиванием или старением.
Практика показала, что проведение испытаний на надежность обходится дорого, так как эти испытания должны проводиться на большом числе образцов (агрегатов) и в течение длительного времени. Кроме того, обработка результатов испытаний при условии получения полной информации занимает длительное время. Поэтому приходится проводить форсированные испытания на надежность. Испытания эти проводятся при форсированных режимах и выполняются в сравнительно короткое время.
При разработке программы и методики форсированных испытаний необходимо уделять серьезное внимание выбору наиболее рациональных характеристик режима испытаний.
Кроме этого необходимо установить соотношение результатов форсированных и обычных натурных испытаний, а также соответствие их условиям эксплуатации.
В сущности метод форсированных испытаний представляет собой одну из разновидностей физического моделирования.
Действительно, при физическом моделировании характеристики реальной системы оцениваются по результатам, полученным при экспериментальных исследованиях модели. При форсированных испытаниях создается модель реальных условий работы и действующих нагрузок. Ввиду этого общность подхода остается в силе, хотя задачи, решаемые с помощью форсированных испытаний, являются более сложными, чем соответствующие задачи, решаемые при обычном физическом моделировании. Физическое моделирование и соответствующая ему математическая модель основаны на ряде соотношений, представляющих собой безразмерные коэффициенты, характеризующие основные параметры элемента.
При форсированных испытаниях, проводимых для оценки надежности, этому условию удовлетворяют временные характеристики безотказности элементов или систем, так как безотказность и вероятность отказа являются безразмерными величинами. Вместе с тем вид функции надежности остается неизменным при выражении временных параметров в минутах, часах или других единицах времени.
В ряде случаев при нормальных условиях эксплуатации элементов для оценки их надежности может быть успешно использован экспоненциальный закон.
Вероятность отказа рассматриваемого элемента гидросистемы в этом случае в интервале времени от t до t + dt может быть записана следующим образом;
Учитывая то, что величины и являются безразмерными, условия работы данного элемента могут быть смоделированы в том случае, если имеет место следующее равенство:
где — соотношение для форсированных испытаний;
— соотношение для реальных условий работы.
Из этого соотношения вытекает, что меньшему среднему времени безотказной работы Т ф соответствует и меньшее время форсированных испытаний t ф ; при этом время форсированных испытаний
По аналогии с физическим моделированием отношение представляет собой коэффициент подобия, устанавливающий соотношение между временем работы при реальных условиях и форсированных испытаниях.
Для элементов гидравлических систем надежность является функцией комплекса факторов, обусловливающих действующие нагрузки и продолжительность работы.
Вводя понятие условной обобщенной нагрузки, можно в общем виде записать
q = f1(x1, ),
где q— условная обобщенная нагрузка; x1 — частная нагрузка; — время.
В свою очередь, обобщенная нагрузка является функцией частных нагрузок, обусловленных рабочим давлением, температурными условиями, загрязнением рабочей жидкости и т. д.
Таким образом, при проведении форсированных испытаний можно моделировать любую из этих функций. Следовательно, форсированные испытания можно проводить, например, повышая рабочее давление в системе, что приведет к повышению нагрузок по сравнению с нормальными эксплуатационными; испытания можно также проводить, форсируя температурные режимы работы или повышая загрязненность жидкости. Например, можно записать, что обобщенная нагрузка является функцией давления и температуры:
х =f(p1,to)
где р 1 — давление рабочей жидкости;
to— температура.
По аналогии с теорией физического моделирования в нашем случае вероятности отказа элемента при обычных условиях работы и в условиях форсированных испытаний могут быть выражены с помощью безразмерного коэффициента £, характеризующего обобщенную нагрузку, и коэффициента t, характеризующего время безотказной работы
q = f3(£1, t); q = f4 (£1ф, t ф).
Соответствие коэффициентов определяется следующими равенствами:
£1 = £1ф; t = t ф; f3 = f4.
При обработке результатов, полученных в процессе форсированных испытаний характеристики безотказности, с помощью коэффициентов подобия, могут быть переведены в реальные характеристики, имеющие место при нормальной эксплуатации элементов. Естественно, что выбор величины коэффициентов способствует существенному сокращению длительности испытаний.
Следует иметь в виду, что при повышенных коэффициентах может нарушиться соответствие между функциями f3 и f4.
В первую очередь это замечание относится к величине коэффициента форсирования К ф, т. е. превышения нагрузки при форсированных испытаниях над нагрузкой, которая может иметь место при нормальной работе элемента
К ф = А ф / а н ,
где А ф и а н — соответственно нагрузка при форсированных испытаниях и обычных условиях работы.
Между коэффициентом подобия по нагрузке и среднему времени безотказной работы элемента существует определенная функциональная зависимость, которая в общем виде может быть представлена так:
К ф = = f4(х1,хф).
Вид функции f4(х1,хф)зависит от типа элемента, его конструкции и комплекса действующих нагрузок.
При разработке программы форсированных испытаний необходимо предусматривать проведение испытаний при нескольких различных значениях К ф > 1.
Отказы или разрушения испытуемых элементов при этом, естественно, будут возникать значительно быстрее, чем при значении коэффициента К ф = 1.
По результатам испытаний строится график N = f ( К ф ) в полулогарифмической системе координат.
Рис. 2. График зависимости N = f ( К ф ) |
Здесь N — число циклов повторной нагрузки; при этом по оси ординат (рис. 2) откладывается значение коэффициента К ф , а по оси абсцисс — наработка в часах или суммарное число циклов нагружения.
При форсированных испытаниях так же, как и при обычных, точность экспериментальных результатов зависит от числа испытанных образцов. Поэтому необходимо не только иметь методы оценки соответствия результатов форсированных испытаний характеристикам безотказности в обычных условиях работы элемента, но и оценивать точность получаемых результатов
Весьма часто при оценке качества элемента необходимо по результатам испытаний оценить, удовлетворяют ли характеристики испытанного элемента требованиям минимально допустимого среднего времени безотказной работы.
Один из возможных вариантов решения этой задачи представлен в работе Херда Г.Р. «Некоторые статистические методы и средства анализа и предсказания надежности». На практике часто достаточно воспользоваться односторонней оценкой, использовав для этой цели плотность вероятности наименьшего времени отказа, полученного при форсированных испытаниях
f1( t ф) = N . f( t). [Р( t ф)]N-1,
где Р( t ф) — надежность элемента.
Используя плотность вероятности f1( t ф), для некоторого фиксированного времени t ф, можно определить интегральную функцию распределения времени отказа.
Эта функция является одной из характеристик точности результатов, полученной при испытаниях
q1( t ф) = 1 - [Р( t ф)]N или q1( t ф) = 1 – [1 - q( t ф)]N.
Ввиду этого вероятность отказов при форсированных испытаниях определится следующим образом:
q1( t ф) = 1 - [1 – q1( t ф)] 1/ N.
Полученное значение вероятности q1(t ф) характеризует точность результатов. Следовательно, с вероятностью q1(t ф) можно утверждать, что доля систем Р(t ф)будет иметь время безотказной работы больше, чем минимальное время отказа, полученное при форсированных испытаниях.
Следовательно, Р(t ф)характеризует безотказность элементов в реальных условиях работы.
Если для форсированных испытаний использовалось N элементов, и при этом первый отказ был получен по истечении времени t 1ф, то можно утверждать, что при работе такого же количества элементов в реальных условиях первый отказ возникнет через время
t 1 = К ф . t 1ф.
Это же соотношение может быть использовано для определения потребного времени форсированных испытаний при условии, чтобы в реальных условиях в течение заданного времени отказы не возникали
t оф = t треб / К ф. .
Потребное количество элементов при этом для получения заданной точности может быть определено по следующей формуле:
.
Таким образом, чтобы элемент с вероятностью доверия q1( t ф) имел для заданного периода времени работы в реальных условиях t mpеб безотказность, равную Р(t ф), следует проводить форсированные испытания N элементов; при этом элементы в течение времени испытаний не должны иметь отказов.
Дата добавления: 2022-06-11; просмотров: 36; Мы поможем в написании вашей работы! |
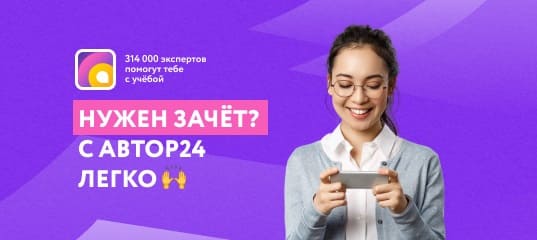
Мы поможем в написании ваших работ!