Химический анализ и коррозионные испытания сварного соединения
Химический анализ служит для отбраковки материалов по составу и установления причин появления дефектов в сварном соединении. При исследовании соединения обычно производят химический анализ основного, присадочного (электродов и проволоки) и наплавленного металлов шва.
При анализе металла шва необходимо выяснить соответствие содержания в нем углерода, кремния, марганца и легирующих элементов значениям, рекомендуемым для различных способов сварки, марок электродов, составов основного металла и т. д. Кроме того, важно знать, что содержание вредных элементов (серы, фосфора и др.) в стали не превышает допустимых пределов. В некоторых случаях, особенно при разработке нового состава покрытия или технологии сварки, выполняют также анализ металла шва на содержание азота, кислорода и водорода.
Пробы для химического анализа в виде стружки отбирают в соответствии с ГОСТ 7122 — 81 с таким расчетом, чтобы в них содержалось небольшое количество основного металла. Иногда стружку получают из образцов, предназначенных для механических испытаний.
Необходимая для анализа масса стружки зависит от числа проверяемых химических элементов: для определения углерода достаточно 3 … 5 г стружки, для определения азота и кислорода — 50 … 60 г, а для полного анализа состава — 50 г.
Стружка должна быть обезжирена спиртом или эфиром. Содержание кислорода и азота определяют методом горячей экстракции или расплавлением стружки в вакууме в специальных муфельных печах. Если полученные результаты сомнительны, то производят повторный отбор не менее двух проб.
|
|
В тех случаях, когда отбор проб затруднен, химический состав сварных швов определяют с помощью спектрального анализа, выполняемого на специальных приборах — спектрометрах, позволяющих с высокой точностью установить количественный состав элементов, входящих в металл шва. При спектральном анализе на поверхности образца зажигают микродугу. Пары́ металла, попадающие в эту дугу, создают присущий им спектр, который разлагается на аналитические линии. Сравнением этих линий с эталонными определяют количественный и качественный состав элементов в сплаве.
Один из способов изучения структуры металлов основывается на применении радиоактивных изотопов. Чаще всего для изучения состава металла используются радиоактивные изотопы серы и фосфора, которые вводят в шов через проволоку или основной металл. Из шва, содержащего радиоактивные изотопы, изготовляют шлифы, отпечаток которых на фотопленке или фотобумаге отображает характер распределения этих изотопов: наибольшее потемнение отвечает их максимальной концентрации. По характеру распределения изотопов определяют распределение соответствующих химических элементов в металле шва и скорости их выгорания в процессе сварки.
|
|
Испытания на коррозионную стойкость проводят с использованием нескольких методов. Сначала даны несколько определений используемых здесь понятий. Затем описаны сами методы испытаний.
Сварные соединения из углеродистых, легированных и высоколегированных сталей, работающие в условиях химически активной среды, подвержены коррозии (разъеданию). По своему действию на металл коррозию разделяют на химическую и электрохимическую.
Химическая коррозия представляет собой процесс непосредственного химического взаимодействия между металлом и средой, как, например, окисление железа на воздухе при высоких темпера турах с образованием окалины.
Электрохимическая коррозия — это разрушение металла с участием электрического тока, который возникает при работе металла в воде, растворах кислот, солей и щелочей.
Различают два вида коррозии: общая и межкристаллитная.
При общей коррозии вся поверхность металла или часть его химически взаимодействует с агрессивной средой. С течением времени поверхность разъедается и толщина металла соответственно уменьшается.
|
|
При межкристаллитной коррозии происходит разрушение металла по границам зерен. Внешне металл не меняется, но связь между зернами значительно ослабевает, и при испытании на изгиб в растянутой зоне образца образуются трещины по границам зерен.
Для испытания на коррозионную стойкость сварных соединений , сварные образцы (для ускорения процесса испытания) подвергают действию более сильных коррозионных сред, чем те, в которых конструкцию будут эксплуатировать.
Испытания на коррозионную стойкость сварных соединений против общей коррозии проводят несколькими методами.
Весовой метод заключается во взвешивании сварных образцов размером 80 X 120 мм и толщиной 6—10 мм со швом посредине до и после испытания и определении потерь в весе (в г/м2) за определенное время. Усиление шва снимают. Перед испытанием образцы взвешивают с точностью до 0,01 г и замеряют их общую поверхность по всем шести граням. Затем образцы кипятят несколькими циклами по 24—48 ч в азотной или серной кислоте соответствующей концентрации в зависимости от условий работы сварного соединения.
После кипячения с образцов мягкими скребками из дерева, алюминия или меди полностью удаляют продукты коррозии и образцы снова взвешивают. Вычитая вес образца после испытания из первоначального веса и отнеся разность к общей площади поверхности образца (в м2) и одному часу испытания, получают показатель коррозии по потере веса в г/м2*ч и пересчитывают его на потерю веса в г/м2*год.
|
|
Скорость проникания коррозии П в мм/год определяют по формуле
П = (К/δ)*10-3
где К — потеря веса, г/м2*год;
δ — плотность металла, г/см3.
Полученные расчетные данные сравнивают с данными ГОСТа.
По ГОСТ 13819—68 оценку коррозионной стойкости черных и цветных металлов, а также их сплавов при условии их равномерной коррозии проводят по десятибалльной шкале коррозионной стойкости (табл. 15).
Таблица 1. Десятибалльная шкала коррозионной стойкости.
Группа коррозионной стойкости | Скорость коррозии металла, мм/год | Балл |
Совершенно стойкие | менее 0,001 | 1 |
Весьма стойкие | 0,001-0,005 | 2 |
0,005-0,01 | 3 | |
Стойкие | 0,01-0,05 | 4 |
0,05-0,1 | 5 | |
Пониженно стойкие | 0,1-0,5 | 6 |
0,5-1 | 7 | |
Малостойкие | 1-5 | 8 |
5-10 | 9 | |
Нестойкие | больше 10 | 10 |
Этой шкалой нельзя пользоваться при наличии в металле межкристаллитной коррозии и коррозионного растрескивания.
Профилографический метод состоит в определении степени коррозирования (глубины разъедания) различных участков сварного соединения (основного металла, зоны термического влияния и металла шва). Образцы испытают в среде, аналогичной по действию той, в которой будет работать сварное соединение, но более быстродействующей с определенным коэффициентом ускорения. Глубину разъедания измеряют с помощью специальных профилографов и профилометров (рис. 1), после чего на бумаге вычерчивают профиль сварного соединения после коррозии.
При электрохимическом (потенциометрическом) методе определяют разность потенциалов в той или иной коррозионной среде между сварным швом, зоной термического влияния и основным металлом. Это дает довольно правильные представления о направлении процесса коррозии.
Рис. 1. Испытания на коррозионную стойкость шва профилометром: а — общий вид профилометра; б — образцы для испытаний: 1 — после сварки; 2 — перед испытанием; 3 — после испытания; в — профиль сварного соединения: I — до испытания; II — после испытания; г — глубина проникания коррозии.
Объемный метод применяют для коррозионных испытаний только основного металла. Он заключается в определении количества газов, образующихся в результате коррозии.
При методе определения коррозионной стойкости по изменению механических свойств для испытания подбирают сильно действующую среду, как, например, раствор серной или соляной кислоты. Образцы выдерживают в коррозионной среде определенное время, а затем подвергают механическим испытаниям, по результатам которых судят о стойкости сварных швов против коррозии.
Качественную оценку коррозионных поражений проводят внешним осмотром, а также исследованием с помощью лупы или микроскопа сварных соединений после коррозионных испытаний. Эта оценка служит дополнением к методам количественной оценки коррозионных поражений.
Межкристаллитной коррозии подвержены главным образом аустенитные и аустенитно-ферритные нержавеющие стали с большим содержанием хрома.
При сварке этих сталей отдельные участки основного металла, расположенные по обе стороны от шва, подвергаются действию температур, которые могут вызвать распад твердого раствора и выпадение карбидов железа и хрома на границах зерен. Снижение содержания хрома приводит к потере коррозионной стойкости металла и развитию межкристаллитной коррозии (рис. 2), которая может поразить также участки шва, подверженные повторному воздействию сварочного нагрева.
Рис. 2. Межкристаллитная коррозия в результате выпадения карбидов а — при сварке пересекающихся швов; б — при возобновлении сварки шва после смены электрода; в — при двустороннем сварном шве.
Испытания на межкристаллитную коррозию аустенитных, аустенитно-ферритных и аустенито-мартенситных коррозиестойких сталей проводят по ГОСТ 6032—58*.
Образцы (рис. 3) вырезают механическим способом. Контрольную поверхность толщиной до 10 мм состругивают на глубину до 1 мм. Образцы толщиной более 10 мм вырезают поперек шва с таким расчетом, чтобы толщина его была 5 мм, а ширина равнялась толщине основного металла. Чистота поверхности образцов перед испытанием должна быть не ниже Δ7.
Рис. 3. Образцы для испытания на межкристаллитную коррозию
а — при толщине металла до 10 мм; б — при толщине металла более 10 мм; S — толщина металла: I — место вырезки образца; II — контрольная поверхность; III — отход.
Склонность металла к межкристаллитной коррозии определяют по методам A, AM, В:
А — в водном растворе медного купороса и серной кислоты;
AM — в водном растворе медного купороса и серной кислоты в присутствии медной стружки;
В — в водном растворе медного купороса и серной кислоты с добавкой цинковой пыли.
Все испытания проводят в колбе или специальном бачке из хромоникелевой стали с обратным холодильником. В реакционный сосуд загружают образцы и заполняют его соответствующим раствором на 20 мм выше образцов. Затем образцы кипятят в растворе: для метода А - 24 ч, AM - 15 или 24 ч; В - 144 ч.
Рис. 4. Сосуд для испытания анодным травлением
а — горизонтальных поверхностей; б — вертикальных поверхностей; I — свинцовая воронка; 2 — резиновая манжетка; 3 — поверхность контролируемой детали.
После кипячения образцы промывают, просушивают и загибают на угол 90°. При этом радиус закругления губок или оправки должен быть равен: при толщине образцов до 1 мм — 3 мм, от 1 до 3 мм - не более трехкратной толщины образца и свыше 3 мм — 10 мм.
Поверхность в зоне изгиба образца тщательно осматривают с помощью лупы при увеличении в 8—10 раз. Если на поверхности будут обнаружены поперечные трещины, то это значит, что металл склонен к межкристаллитной коррозии и непригоден для эксплуатации.
Кроме методов A, AM и В существуют еще методы Б и Д.
При методе Б производят анодное травление участков поверхности деталей или зоны термического влияния. Металл сварного шва этим методом не контролируют. Метод Б основан на анодной поляризации и состоит в воздействии коррозионной среды и электрического тока на поверхность испытуемой детали.
Сосуд для коррозионной среды (рис. 4) состоит из свинцовой воронки с резиновой манжетой, плотно прилегающей к поверхности контролируемой детали. Для испытаний собирают установку по схеме, приведенной на рис. 5.
Рис. 5. Электрическая схема для испытания методом анодного травления
1 — источник постоянного тока; 2 — амперметр с ценой деления не более 0.1 а; 3 — реостат или магазин сопротивления; 4 — выключатель; 5 — свинцовый сосуд; 6 — резиновая манжета; 7 — контролируемый образец.
Испытания проводят по обеим сторонам сварного шва в шахматном порядке, а в случае перекрытых швов — во всех местах перекрещивания (рис. 6). Поверхность контролируемых участков шлифуют наждачной бумагой и промывают чистым авиационным бензином и спиртом. На отшлифованную поверхность плотно устанавливают сосуд и наливают в него 3—5 мл электролита (60% серной кислоты и 0,5% уротропина), включают электрический ток и в течение 5 мин подвергают металл коррозированию. Полярность устанавливают таким образом, чтобы испытуемое изделие служило анодом, а свинцовый сосуд — катодом. С помощью реостата устанавливают ток плотностью 0,65 а/см2 при напряжении 5—9 в.
По прошествии 5 мин ток выключают, детали промывают водой и протирают спиртом. Образовавшиеся пятна на поверхности образца рассматривают под микроскопом при увеличении не менее чем в 30 раз. При контроле готовых сварных конструкций, когда применение микроскопа невозможно, допускается применение бинокулярной лупы или оптических трубок с 20-кратным увеличением. Если пятно анодного травления имеет однородный светлый или темный цвет, то это значит, что металл не склонен к межкристаллитной коррозии. Браковочным признаком является образование в нем непрерывной сетки.
Рис. 6. Схема проведения контроля перекрывающихся сварных швов методом анодного травления
1 — сварной шов; 2 — место анодного травления.
По методу Д образцы испытывают в кипящей 65% ной азотной кислоте. Перед испытанием образцы взвешивают на аналитических весах с точностью до 0,1 мг. Затем их помещают в стеклянную колбу с обратным холодильником, заливают кислотой из расчета не менее 9 мл кислоты на 1 см2 поверхности образца и кипятят в течение 48 ч.
Всего проводят три цикла кипячения (каждый раз в новом растворе), промывая, просушивая, обезжиривая и взвешивая образцы после каждого цикла. Коррозионную стойкость определяют по скорости коррозии образцов, выраженной в мм/год за каждые 48 ч. Если скорость коррозии превысит 2 мм/год или будет иметь место ножевая коррозия, металл бракуют.
Дата добавления: 2022-06-11; просмотров: 100; Мы поможем в написании вашей работы! |
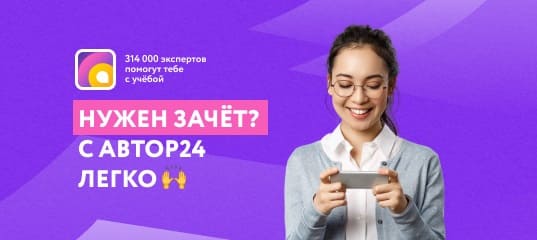
Мы поможем в написании ваших работ!