Дефекты изготовления изделий из пластмасс.
Ингредиенты пластмасс и их назначение
Ингредиенты | Их назначение |
Полимер, олигомер | Основа пластической массы |
Наполнители | Для регулирования физико-механических свойств, повышения твердости, уменьшения деформируемости, снижения усадки, уменьшения прозрачности, удешевления материала. Для получения композиционных: слоистых. Волокнистых. Стружечных материалов. |
Стабилизаторы | Для защиты полимеров от внешних воздействий («старения»): термической и окислительной деструкции (антиоксиданты), озонного старения (антиозонанты), фотоокислительной деструкции (светостабилихторы). |
Пластификаторы | Для повышения пластичности и расширения температурного интервала, высокоэластичного состояния готового материала. Для снижения вязкости и температуры формования. |
Красители | Для получения окрашенных материалов. Высокодисперсные растворимые красители используют для получения прозрачных окрашенных пластмасс. |
Пигменты | Для получения окрашенных , малопрозрачных и непрозрачных пластмасс. |
Сшивающие агенты (отвердители) | Вводят для завершения процесса отверждения (реактопласты – ненасыщенные полимерные смолы). |
Антиадгезионные добавки | Вещества, регулирующие адгезионные свойства, применяются для снижения прилипания (адгезии). |
Порообразователи | Для получения легких пористых, вспененных материалов. |
Порошкообразные металлы | Для улучшения электрически х, магнитных, теплофизических свойств, внешнего вида. |
Антистатики | Для снижения уровня статического электричества, так как полимеры диэлектрики. |
Антипирены | Для снижения горючести пластмасс. Затрудняют воспламенение и распространение пламени. |
Антимикробные добавки (антисептики) | Для препятствия заражению и развитию икроорганизмов |
|
|
Все ингредиенты позволяют повысить уровень потребительских свойств полимерных материалов: надежность, а именно, долговечность, устойчивость к действию внешних факторов при эксплуатации и хранении; эстетические свойства; универсальность в применении.
Методы переработки пластмасс в изделия
Переработка пластмасс – это комплекс технологических процессов и операций, обеспечивающий получение материалов, полуфабрикатов или изделий из пластмасс с использованием специального оборудования.
Проектирование изделий. Это начальный этап проектирования рациональной конструкции изделия и формирующих инструментов, выбор метода переработки пластмассы и технологического режима. Важным этапом здесь является разработка рецептуры пластмассы, оптимальной для данного метода переработки и качества получаемых изделий.
|
|
Подготовительные операции. Включают стадии: сушка полимеров, приготовление композиций (гранулирование, таблетирование, смешение), введение пластификаторов и наполнителей, окончательное смешение всех компонентов рецептуры.
Основная стадия – изготовление изделий определенной формы и размера (формообразование).
Заключительная стадия – обработка изделия для повышения уровня качества, удаление незначительных дефектов, декорирование, сборка, упаковка.
Технология переработки полимера зависит от типа пластмассы. Термопласты и реактопласты перерабатывают по-разному. Так как:
Термопласты - материалы, которые при повышенной температуре способны переходить в высокоэластичное или вязкотекучее состояние, а при охлаждении вновь превращаться в твердое. Формообразование изделия происходит в результате физического процесса – охлаждения.
Реактопласты – материалы, которые переходят в высокоэластичное или вязкотекучее состояние под действием температуры лишь в короткий период времени, необходимый для формования. Формообразование происходит за счет химической реакции сшивания макромолекул. При повторном нагревании они не расплавляются. Их повторная переработка невозможна без дополнительного разрушения.
|
|
Выбор метода переработки зависит и от физического состояния в момент формования.
Основные методы формообразования изделий из пластмассы:
1. Безнапорное формование используется в трех основных технологиях
- полимеризация в форме – происходит химическая реакция из жидких мономеров непосредственно в форме, соответствующей формам изделия. Например: получение в блоке листового органического стекла, галантерейных изделий, имитация барельефов;
- формирование из пластизолей (дисперсия частиц определенных полимеров в жидком пластификаторе) или растворов – получение пленок методом полива с последующим испарением жидкости(растворителей); из дисперсий (латексов) окунанием готовой формы и астабилизации диссперсии (латексные перчатки, шары); ротационное формование пластизолей – во вращающейся вокруг двух или более осей закрытой металлической форме происходит перераспределение пластика по внутренней поверхности формы (тонкостенные полые изделия: головы кукол, мячи);
- спекание порошков – применяют для получения изделий из полимеров с высокой температурой плавления (фторопласты) или из порошкообразных полимеров (полиолефины, поликарбонаты), таким способом наносят антикоррозионное или антипригарное покрытие на поверхность изделий.
|
|
2. Литье под давлением основано на принципе передавливания расплава пластмассы под давлением в пресс-форму, с последующим охлаждением массы в пресс-форме до твердого состояния. Масса литьевых изделий может колебаться от нескольких граммов (игрушка, деталь) до нескольких килограммов (ящик, контейнер). Это термопласты.
Особенности таких изделий являются точность размеров, зеркальный блеск поверхности, наличие следов от литника – места выхода расплава из сопла литьевой машины.
3. Метод экструзии получение изделий из полимерных материалов (резиновых смесей, пластмасс, крахмалсодержащих и белоксодержащих смесей) путём продавливания расплава материала через формующее отверстие в экструдере. Этим методом можно получить готовые профильные изделия различного сечения непрерывной длины в виде стержней, труб, лент, листов.
Метод экструзии с раздуванием позволяет раздуть горячим воздухом выходящий из экструдера полимерный материал в виде рукава: бутылки. Канистры, флаконы, игрушки. Характерный признак следы от полуформ в виде полосок на боковой поверхности изделия.
4. Инжекционно-выдувное формование – метод получения полых изделий выдуванием сжатым воздухом из готовых разогретых преформ. Преформы – заготовки, которые получают литьем под давлением. Те же полые изделия но с более точными линиями горла и дна пет-тара.
5. Горячим прессованием – можно получить изделия сложной формы, размеров и толщины. При этом на пресс-порошковую композицию повышенной температурой и давлением. В машину попадает материал, который под действием высоких температур превращается в расплав (жидкое состояние), далее через отверстия попадает в пресс форму. Здесь расплавленный материал при помощи поршня вдавливается в полость формы и удерживается в таком состоянии до полного затвердения. Получают листовые материалы.
6. Методы вакуумного и пневматического формования позволяет получать объемные изделия – как крупногабаритные, так и мелкого размера (от ванн до тарелок и стаканчиков). Принцип состоит в разогреве листовой заготовки выше температуры размягчения с последующим прижиманием размягченного листа к копируемой форме либо вакуумом, либо избыточным давление воздуха от 1,5 до 5 атм.
7. Каландрирование – непрерывное формование термопластов путем пропускания их расплава через зазор между вращающимися валками каландра. В этом случае полимерная композиция проходит один раз через несколько валков 3-5. При этом происходит увеличение ширины материала и его утоньшение, в результате чего получается пленка, заданной ширины и толщины. Последний вал каландра может быть полированным 9гладкая пленка) или рельефным, гравированным (пленка с тиснением).
После формообразования происходит декорирование и сборка изделий. При необходимости изделия подвергают механической обработке (вырубка, сверление, нанесение резьбы), сварке, склеиванию, поверхностной отделке (полировке). Декорирование производят методами гравировки, горячего тиснения, раскрашивания, металлизации, печати.
Дефекты изготовления изделий из пластмасс.
Дефекты изготовления изделий из пластмасс могут быть связаны: с неудачно подобранным составом пластмассы (дефекты состава); с нарушениями технологического режима формования или его неправильным выбором (дефекты формования); с операциями механической обработки или декорирования отформованного изделия (дефекты отделки).
По степени значимости все дефекты можно разделить на:
- критические (переводят изделие в брак) – низкие деформационно-прочностные свойства; грубые дефекты выработки и отделки; несоответствие изделия требованиям безопасности при использовании и эксплуатации;
- значительные (допускаются с ограничениями по количеству или допускают перевод в низшую градацию качества ОСНОВНЫМ ДОКУМЕНТОМ РЕГЛАМЕНИРУЮЩИМ КАЧЕСТВО БЫТОВЫХ ИЗДЕЛИЙ ИЗ ПЛАСТМАСС является ГОСТ Р 50962-96 « Посуда и изделия хозяйственного назначения из пластмасс. Общие технические условия». Согласно ГОСТ – стандартные изделия из пластмасс на сорта не подразделяются.) – нормируемые и устранимые дефекты выработки;
- малозначительные (допускаются) – показатели внешнего вида, цвет, небольшие отклонения от вместимости, массы, стойкость рисунка к истиранию.
Дефекты состава: инородные включения (видимые посторонние включения, являющиеся результатом загрязнения композиции пластмасс или оборудования); пониженная механическая прочность, возникшая при слишком малом или избыточном содержании наполнителя; повышенное водопоглощение за счет повышенной пористости материала или избыточного количества гигроскопичного наполнителя.
Дефекты формования: коробление – искривление формы изделия; раковины – пустоты в изделии в виде перевернутой ракушки; вздутия – мелкие или крупные выпуклости на поверхности; трещины – нарушения сплошности изделия; сколы – неровные острые углубления на поверхности изделия, возникшие при механических повреждениях; риски и царапины – тонкие углубленные линии на поверхности; заусенцы – острые выступы по краю или дну изделия; облой (грат) – утолщение на поверхности прессованных изделий, по месту разъема формы; выступление литника – неудаленный или незачищенный остаток литника на поверхности изделия; разводы – заметные следы растекания пластмассы в виде полос или пятен-наплывов; матовость – пятна пониженного блеска; стыки технологические – видимые выступающие линии соединения спая; следы от выталкивателя – выступы и углубления на корпусе, возникшие при выталкивании из формы еще не затвердевшего изделия.
Дефекты отделки могут являться следствием некачественного проведения операций по исправлению дефектов формования: неполное удаление литника; не заполированные риски и царапины; не заполированные следы от разъема формы.
Дефекты декорирования связаны с применением красочных составов с малой адгезией к поверхности (отслоение краски), нечеткий рисунок, растекание красителя, смещение основных частей декора, несимметричность, небрежность в выполнение декора (подтеки, непрокрасы, нечеткость контуров рисунка).
Дата добавления: 2022-06-11; просмотров: 187; Мы поможем в написании вашей работы! |
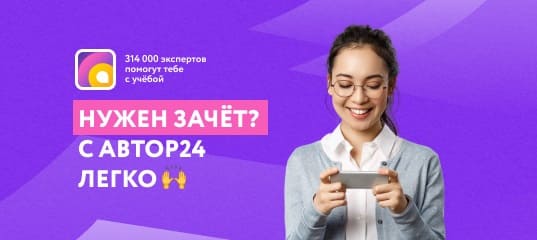
Мы поможем в написании ваших работ!