Изделия из древесины с применением цемента
ОП.01 Основы материаловедения
25.03.2020 года
17 группа
1час
Раздел 2 Классификация материалов, применяемых в штукатурных работах, их основные свойства и область применения
Тема занятия : Органические заполнители. Назначение и основные свойства.
Задание: внимательно прочитайте текст занятия «Органические заполнители» и законспектируйте в тетради виды органических заполнителей, их назначение и свойства. Выполненные работы присылать Вконтакте до 31 марта не в группу по дистанционному обучению, а сообщением преподавателю.
Заполнители органические
Органические заполнители, как правило, применяют для производства теплоизоляционных и теплоизоляционно-конструкционных материалов и изделий:
1) цементного фибролита;
2) ксилолита;
3) арболита;
4) камышебетона;
5) торфоплит;
6) теплоизоляционных плит из костры льна;
7) некоторых пластмассовых изделий.
В качестве древесных и других органических заполнителей обычно используют:
1) отходы лесозаготовок (вершины, сучья, пни, корни);
2) отходы лесопиления и деревообработки (горбыли, рейки, щепа, стружки и опилки);
3) сельскохозяйственные отходы (рисовую солому, льняную и конопляную костру, стебли хлопчатника, подсолнечную лузгу);
4) одубину (отходы заводов дубильных экстрактов);
5) побочные продукты целлюлозно-бумажной промышленности;
6) сечку камыша.
Основными являются древесные и сельскохозяйственные отходы.
|
|
Сырьевая база для получении древесных заполнителей остаётся практически неограниченной, поскольку ежегодный объём древесных отходов составляет примерно 150 млн. м3. Большая часть их пока рационально не используется.
Древесные отходы
На территории России сосредоточено около 70% мировых запасов древесины, причём на 80% - в наиболее ценных лесах хвойных деревьев. Массовая заготовка и переработка древесины связаны с накоплением отходов до 200 млн. м3, в том числе около 50 млн. м3 опилок.
На качество искусственных строительных конгломератов, в которых применяют древесные заполнители, оказывает влияние порода дерева. Древесные заполнители получают главным образом из отходов хвойных пород (ели, пихты, сосны и других). Реже используются отходы лиственных пород – осины, берёзы, бука и других. Из древесных заполнителей перспективными являются отходы деревообработки. Их подвергают предварительной подготовке с целью освобождения от загрязняющих примесей и получения частиц нужной формы (дроблёнка, стружки, древесная шерсть) и размеров. Кусковые отходы древесины подвергают сначала первичной, а затем вторичной переработке. Первичную переработку производят с помощью рубильных машин, в результате чего получают технологическую щепу в виде ромбовидных кусков с размерами по длине волокон древесины 10-40 мм. Щепа непригодна для изготовления искусственных строительных конгломератов, так как является слишком крупной, и изделия с ней имеют большую пористость и низкую прочность. При вторичной переработке, которую производят с помощью молотковых мельниц (дробилок) и стружечных станков, технологическую щепу превращают в дроблёнку и стружку. Кроме специально приготовленной стружки, применяют также стружку и опилки от столярного и мебельного производства. Древесную шерсть приготовляют на древесношерстяных станках из чураков.
|
|
Свойства древесных заполнителей
На качество искусственных строительных конгломератов большое влияние оказывают свойства древесных заполнителей.
Большое значение имеет средняя плотность древесины и насыпная плотность древесного заполнителя, которые зависят от многих факторов. Средняя плотность древесины колеблется в широких пределах.
Важным свойством древесного заполнителя является его пористость. В заполнителе имеются поры внутри частиц и поры (пустоты) между ними. Пористость зависит от различных факторов: от крупности частиц, степени уплотнения и других. Для получения наиболее плотного заполнителя необходимо подобрать смесь частиц древесного заполнителя с минимальной пористостью
|
|
Большое влияние на качество древесных заполнителей оказывает и влажность древесных отходов. Влажность древесины у разных пород деревьев различна, а для одной и той же породы она зависит от местоположения в стволе, от времени года, суток, от температуры и других факторов. Значительно увлажнённые отходы плохо поддаются переработке их в заполнители.
Древесный заполнитель обладает гигроскопичностью. При поглощении влаги древесина набухает, что сопровождается давлением разбухания. Набухание происходит при поглощении влаги оболочками клеток, которые при этом увеличиваются в объёме, тогда как поглощение влаги капиллярами древесины набухания не вызывает. При расчёте составов искусственных строительных конгломератов (например, арболита) учитывают набухание древесного заполнителя.
При высыхании древесного заполнителя происходит уменьшение его объёма (усушка). Усушка древесины связана с испарением влаги из клеточных оболочек. При удалении влаги из капилляров усушки не происходит. Наибольшая усушка происходит поперёк волокон (до 12%), а вдоль волокон она незначительна (0,1%). В целом усушка древесного заполнителя в бетоне вызывает дополнительные напряжения и влияет на деформативные свойства. Волокнистое строение заполнителя вызывает некоторую анизотропию прочности изделий.
|
|
Содержание хвои в заполнителе должно быть не более 5%, а коры – не более 15% от массы абсолютно сухой древесины. Не допускаются заполнители, имеющие запах и гнили. Гниль необходимо удалять просевом заполнителя через сито с диаметром отверстий 1,5-2 мм.
Размеры лепестков стружек, полученные на стружечных станках: длина 2-20 мм, минимальная толщина 0,1-1 мм.
Изделия из древесины с применением цемента
При изготовлении изделий с применением цемента (например, арболита) стружки минерализуют. Древесная шерсть, применяемая для приготовления цементного фибролита, состоит из длинных тонких стружек (ленточек) длиной 500 мм, шириной 2-5 мм и толщиной 0,2-0,7 мм. Её получают строганием специально приготовленных окорённых чураков длиной 0,5 м и диаметром 10-35 см; допускается применение более тонких чураков диаметром 8-9 см, а также диаметром свыше 35 см. С этой целью неделовую древесину – тонкомерный кругляк, дровяное долготьё и отходы лесопиления (горбыли, срезки) – освобождают от коры и выдерживают в тёплое время года (весенне-летний период) в штабелях. Затем материал распиливают пилой на чурки длиной 0,5 м и затем строганием на древесношерстных станках готовят из чураков древесную шерсть. Её сушат в конвейерных сушилах до влажности 20-25% и минерализуют.
Опилки, в зависимости от характера распиловки, разделяют на два основных вида: опилки от поперечной и продольной распиловки. При поперечной распиловке древесины на круглопильных станках получаются более мелкие частицы, чем при продольной распиловке, и они имеют волокнистое строение. Эти опилки почти полностью проходят через сито с диаметром отверстий 2 мм и основной фракцией в них является фракция 1-2 мм.
При продольной распиловке брёвен на лесопильной раме получают опилки близкой к кубической форме размерами от крупных частиц 7 мм до пылевидных. Наибольшая часть опилок имеет размеры от 2 до 5 мм. Кубовидная форма частиц обусловливает высокое отношение торцевых поверхностей к боковым, вследствие чего материалы и изделия из опилок обладают повышенными водопоглощением и впитываемостью связующих веществ, так как показатели этих свойств вдоль волокон больше, чем поперёк.
Биостойкость и трудносгораемость материалов на основе древесных заполнителей обеспечивается пропиткой заполнителей минерализаторами и последующим смешиванием их с минеральными вяжущими. Недостатками бетонов на древесных заполнителях является высокое водопоглощение и сравнительно низкая водостойкость.
Арболит
Арболит – это лёгкий бетон на заполнителях растительного происхождения, предварительно обработанных раствором минерализатора. Он применяется в промышленном, гражданском и сельскохозяйственном строительстве в виде панелей и блоков для возведения стен и перегородок, плит перекрытий и покрытий зданий, теплоизоляционных и звукоизоляционных плит. Арболитовые конструкции эксплуатируют при относительной влажности воздуха помещений не более 69%, при большей влажности необходимо устройство пароизоляционного слоя.
Наружная поверхность конструкций из арболита, соприкасающаяся с атмосферной влагой, независимо от влажностного режима эксплуатации, должна иметь отделочный (фактурный) слой.
Плотность и теплопроводность арболита при постоянной прочности могут изменяться в зависимости от вида заполнителей. Для арболита на измельчённой древесине со средней плотностью 400-850 кг/м3 теплопроводность составляет 0,08-0,17 Вт/(м·К).
На прочность арболита влияет порода древесины и влажность, особенно в диапазоне от 0 до 25%. Максимальную прочность этот материал приобретает при влажности 16-17%. Деформация при кратковременной нагрузке (показатель сжимаемости) у арболита в 8-10 раз больше, чем у лёгких бетонов на минеральных пористых заполнителях.
Арболит имеет достаточно большое значение водопоглощения. Однако преимуществом этого материала является лёгкая отдача поглощённой воды, то есть быстрое высыхание.
Морозостойкость арболитовых изделий назначается в зависимости от режима их эксплуатации и климатических условий района строительства. Во всех случаях она принимается не менее 25.
Для изготовления заполнителей из древесины исходный продукт для снижения количества вредных экстрактивных веществ определённое время выдерживают на складах (хвойные породы – не менее 2 месяцев, лиственные 6 месяцев).
При положительной температуре выдержка сокращается до 1 месяца при условии дальнейшего измельчения древесины в щепу. Дроблёнку хвойных и особенно лиственных пород обязательно замачивают в воде или растворах минеральных солей. Последние, нейтрализуя действие вредных веществ в древесине, одновременно ускоряют твердение цемента.
Дата добавления: 2022-06-11; просмотров: 23; Мы поможем в написании вашей работы! |
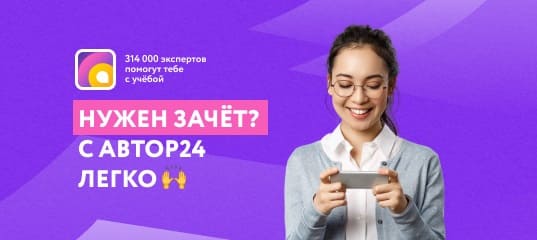
Мы поможем в написании ваших работ!