Нейросетевая модель прогнозирования качества анодной массы для условий ОАО «БрАЗ»
МИНИСТЕРСТВО ОБРАЗОВАНИЯ КРАСНОЯРСКОГО КРАЯ
КРАЕВОЕ ГОСУДАРСТВЕННОЕ БЮДЖЕТНОЕ ПРОФЕССИОНАЛЬНОЕ
ОБРАЗОВАТЕЛНОЕ УЧРЕЖДЕНИЕ
«КРАСНОЯРСКИЙ ИНДУСТРИАЛЬНО - МЕТАЛЛУРГИЧЕСКИЙ ТЕХНИКУМ»
Код специальности 22.02.02
РЕФЕРАТ
Тема: Система автоматизации ТП прокалочного и котельного отделений цеха анодной массы ОАО "БрАЗ"
Дисциплина: Автоматизация производства
Выполнил:Краевое государственное бюджетное профессиональное образовательное учреждение «Красноярский индустриально-металлургический техникум» КОНТРОЛЬНАЯ РАБОТА №__________ Вариант №_______ Дисциплина________________________________________________________________________ Группа____________________________________курс______________________________________ Специальность_____________________________________________________________________ Фамилия ,имя ,отчество (полностью) __________________________________________ ________________________________________________________________________________________ Шифр___________________________________________ Домашний адрес студента _________________________________________________________________________________________ Входящий номер_________________дата проверки_________________________________ Оценка работы______________________________________________________________________ Подпись преподавателя___________________________________________________________ Фамилия преподавателя__________________________________________________________ |
Группа: МЗ-19
Выполнил:
Проверил:
Красноярск 2021 год
Содержание
1. Общие сведения об анодной массе 3
|
|
2. Нейросетевая модель прогнозирования качества анодной массы для условий ОАО «БрАЗ» 5
3. Система автоматизации ТП прокалочного и котельного отделений цеха анодной массы ОАО "БрАЗ" г.Братск Иркутской обл. 7
Общие сведения об анодной массе
Одним из наиболее крупных потребителем электродов является алюминиевая промышленность. Электроды в широком смысле этого слова называют проводники, служащие для подвода электрического тока к среде, на которую он воздействует. Эта среда может быть водным раствором, расплавленным или твёрдым раскалённым веществом.
Электроды в алюминиевой промышленности работают в весьма жёстких эксплутационных условиях (высокая температура, агрессивная среда в виде расплавленных солей и т.д.), поэтому они должны удовлетворять следующим основным требованиям:
- выдерживать высокую температуру
- иметь хорошую электропроводность, малую пористость и достаточную механическую прочность
- обладать хорошей стойкостью против окисления кислородом воздуха и разъедания различными химическими веществами
|
|
- содержать минимальное количество примесей
- иметь правильную геометрическую форму
- быть достаточно дешёвыми
Наиболее полно этим требованиям отвечают электроды из углеродистых материалов.
Сырьё, применяемое для производства углеродистых изделий.
Для производства углеродистых изделий применяют сырьё двух видов:
- твёрдые углеродистые материалы, составляющие основу (скелет) электрода
- связующие углеродистые материалы, которые заполняют промежутки между зёрнами углеродистых материалов и соединяют (цементируют) эти зёрна между собой при коксовании электрода в процессе обжига
Основным элементом, составляющим твердые и связующие углеродистые материалы, служит углерод. В настоящее время известны только две аллотропические формы твердого углерода: алмаз и графит. Так называемый аморфный углерод (уголь, антрацит, кокс, сажа и т.д.) представляет собой графит мелкокристаллической структуры. Под влиянием высоких температур кристаллы графита укрупняются. Наиболее резкое и наиболее интенсивное изменение размеров кристаллов графита в углях наблюдается при t выше 2000оС.
|
|
Из углеродистых материалов изготовляются также блоки и плиты для футеровки электролизеров, электропечей и другого металлургического оборудования. Ниже приведена характеристика основных видов электродных изделий, применяемых в алюминиевой промышленности, и краткие сведения о их получении.
Виды электродных изделий и требования к ним
Углеродистые электроды и изделия в зависимости от способа их изготовления подразделяют на прессованные обожженные и непрерывные самообжигающиеся.
Блоки анодные обожженные применяют в качестве анодов в алюминиевых электролизерах. Каждый такой анод представляет собой призматический блок, па верхней плоскости которого имеется одно или несколько ниппельных гнезд (углублений). Для подвода тока к аноду служат стальные ниппеля, которые вставляют в ниппельные гнезда и заливают расплавленным чугуном или заделывают углеродистой пастой. Размеры обожженных анодов зависят от размеров электролизеров. Для мощных электролизеров в нашей стране выпускают аноды сечением 1450х700 мм и высотой 600 мм.
Анодные блоки изготавливают из малозольных и малосернистых коксов.
Блоки угольные подовые, служащие для футеровки подины (катода) алюминиевых электролизеров, имеют форму призмы шириной 550 мм, высотой 400 мм ч длиной от 600 до 2400 мм. На одной из плоскостей катодного блока по его длине имеется паз для заливки чугуном или заделки стального стержня, который служит для отвода тока от катода.
|
|
Механическая прочность на сжатие подовых блоков должна быть не менее 22,6 МПа, пористость не более 22 % н удельное электросопротивление не более 90.10-6 Ом.м.
Для футеровки подии мощных электролизеров изготавливают углеграфитовые половые блоки. В результате добавки графита значительно уменьшается электросопротивление блоков. Углеграфитовые блоки должны иметь электросопротивление не более 60.10-6 Ом.м и механическую прочность на сжатие не менее 25,6 МПа.
Блоки угольные боковые применяются для внутренней футеровки боковых стенок алюминиевых электролизеров. Эти блоки изготовляют толщиной 200 мм, высотой 550 мм н длиной от 600 до 800 мм. Механическая прочность на сжатие угольных боковых плит должно быть не менее 22,5 МПа.
Анодная масса используется в алюминиевых электролизерах с непрерывными самообжигающимися анодами. Такой анод состоит из металлического кожуха с анодной массой, которую по мере сгорания загружают в кожух. Под действием выделяющегося в электролизере тепла анодная масса обжигается.
Выпускается анодная масса в брикетах или в расплавленном состоянии.
В алюминиевой промышленности применяются также графитированные электроды, которые отличаются от угольных повышенной химической и термической стойкостью, а также низким удельным электросопротивлением. Удельное электрическое сопротивление графитированных электродов в зависимости от их марки и диаметра должно быть не ниже (7,5÷12).10-6 Ом.м, а предел механической прочности при разрыве не ниже 2,9—3,4 МПа.
Технологическая схема производства анодной массы.
Нейросетевая модель прогнозирования качества анодной массы для условий ОАО «БрАЗ»
Стабильность работы электролизера в значительной мере зависит от работы анода. Хороший анод обеспечивается качественным производством анодной массы, которая создается подбором соответствующих сырьевых материалов и качественным смешиванием анодной массы.
В производство анодной массы на ОАО «БрАЗ» вовлекаются кокосы разных поставщиков, имеющих различную сырьевую базу и особенности технологии. Качественные показатели сырья имеют значительный разброс даже у одного и того же представителя. Усилиями представителей завода все поступающее сырье максимально усредняется с целью получения стабильной смеси с приемлемыми качественными показателями. Но при существующей вариативности и нестабильности поступления вагонов и термоцистерн – всех факторов учесть невозможно.
Таким образом, зачастую в производство запускается смесь сырья от разных поставщиков. В таких условиях технологическим службам цеха очень трудно спрогнозировать качество анодной массы и показатели работы анодов в электролизе.
Влияния различных промышленных процессов на расход анода исследовались во многих работах в России и за рубежом.
В частности, особенности технологии «полусухого» анода и статический анализ факторов, влияющих на расход анода Содерберга для условий ОАО «БрАЗ», освещены в работах. Однако исследование работы анода осуществлено не достаточно полно, т.е. без учета существующих взаимосвязей: качества поставляемого сырья, технологии производства анодной массы и эксплуатации анода. Это объясняется отсутствием соответствующего инструмента для комплексного анализа имеющихся статистических данных завода. В настоящее время в базах цеха анодной массы и АРМ электролиза имеется более 100 параметров прямо или косвенно связанных с получением анодной массы и эксплуатации анода.
С целью более глубокого и качественного анализа производства и прогнозирования качества анодной массы предложено использовать новые информационные технологии в виде интеллектуальных методов обработки информации, в частности, искусственных нейронных сетей. Нейросетевой подход наиболее эффективен в задачах классификации, поиска закономерностей, прогнозирования и оптимизации. Применение нейронных сетей оправдано для задач имеющих большое количество входной информации, когда данные неполны, зашумлены, частично противоречивы.
Реализация такого подхода потребовала осуществить корректировку структуры базы данных ЦАМ в плане более полного учета всех контролируемых параметров, начиная со сменных данных.
Постановка задачи прогнозирования качества анодной массы потребовала объединения знаний разных специалистов: технологов по анодной массе, электролиза и технической кибернетике.
Цех анодной массы включает в себя три отделения: участок подготовки сырья, прокалочно-утилизационное и размольно-смесильное отделения. Технологический процесс производства анодной массы в размольно-смесительном отделении (РСО) состоит из следующих пределов: средний размол, грохочение, тонкий помол, дозировка компонентов коксовой шихты и жидкого пека, нагрев компонентов, смешение и охлаждение. Структурная схема ЦАМ изображена на рис.1
Рис.1 – Структурная схема ЦАМ
Поступающие нефтяные электродные коксы подвергают дроблению до кусков размером не более 70 мм (молотковые дробилки) т направляют на прокалку во вращающуюся печь при температуре 1200±50С.
Затем кокс дробят на дробилках до частиц размером не более 6-8 мм (средний размол и грохочение), а часть измельчают в шаровых мельницах до размера не более 0.16 мм (тонкий помол). Раздробленный кокс классифицируют на несколько фракций и отправляют в сортовые бункеры. В отдельный бункер помещают пылевую фракцию. В соответствии с рецептурой и сортовых бункеров коксовая шихта дозируется, перемешивается, подогревается и поступает в смесители.
Поступающий каменноугольный пек (связующее вещество) шихтуют, термостатируют, нагревают и подают в смеситель в определенном соотношении. Кокосовая шихта смешивается с пеком (согласно рецепту) в смесителях непрерывного действия. Далее готовая анодная масса охлаждается и поступает на склад, где происходит ее естественная сушка.
3. Система автоматизации ТП прокалочного и котельного отделений цеха анодной массы ОАО "БрАЗ" г.Братск Иркутской обл.
АСУ ТП предназначена для обеспечения эффективного контроля, управления и противоаварийной автоматической защиты технологического процесса прокалки кокса и утилизации отходящих с прокалочных печей газов.
Описание объекта автоматизации
Целью процесса прокалки кокса для производства анодной массы является удаление из него влаги, летучих веществ и улучшение физико-химических свойств.
В прокалочном отделении расположены четыре технологические линии прокаливания кокса. Процесс прокалки осуществляется в трубчатых вращающихся печах диаметром 3 метра и длиной 45 метров. Производительность печи от 8 до 16 т/час в зависимости от вида прокаливаемых коксов. Термообработка коксов производится в противотоке материала и газового потока, который образуется в результате сгорания топлива (мазута), части летучих и углерода кокса. Для обеспечения процесса сгорания топлива осуществляется организованная подача воздуха в топку с помощью дутьевых вентиляторов. Питание прокалочных печей производится с помощью ленточных весовых дозаторов непрерывного действия, управляемых в дистанционном или автоматическом режиме.
Утилизация отходящих с прокалочных печей газов осуществляется в котельном отделении, где расположены 4 котельных агрегата БГМ-35М (по одному на каждую прокалочную печь). Котлы могут работать как в чисто утилизационном режиме, т.е. только на отходящих газах, так и в режиме утилизации с подсветкой мазутом. Утилизационная котельная относится к категории производств по ОНТП-24 86 - "Г", класс помещения по ПУЭ - "П-2", степень огнестойкости - "II".
В состав автоматизируемого объекта входит следующее технологическое оборудование: прокалочные печи, холодильники, вентиляторы, дымососы, питатели, ленточные весовые дозаторы, задвижки, насосы, питательные электронасосы, редукционно-охладительные установки и т.д.
Для реализации АСУ ТП использован программно-аппаратный комплекс PCS7 v5.1.
Структура АСУ ТП и выполняемые функции:
Структура АСУ ТП
В качестве аппаратной базы для системы автоматизации прокалочного отделения выбран контроллер SIMATIC S7-400 на основе CPU 417-4H с децентрализованной периферией ET200M. Автоматизация котельного отделения выполнена на базе резервированного контроллера SIMATIC S7-400H на основе CPU 417-4H с переключаемой децентрализованной периферией на базе ET200M.
С инжиниринговой станции (ES) выполняется программирование контроллеров всех стадий, а также сопровождение проектов станций операторов.
Все контроллеры системы управления и операторские станции объединены локальной одноранговой электрической сетью Industrial Ethernet.
Общее количество обрабатываемых сигналов АСУ ТП:
Сигналы | Котельное отделение | Прокалочное отделение | Всего |
Аналоговые входы | 312 | 119 | 431 |
Аналоговые выходы | 4 | 4 | |
Дискретные входы | 184 | 134 | 318 |
Дискретные выходы | 375 | 128 | 503 |
Частотные входы | 8 | 8 | |
Система взвешивания SIWAREX | 4 | 4 | |
Количество ET200M | 16 | 5 | 19 |
АСУ ТП ВХ обеспечивает циклический опрос контроллерами всех датчиков с периодом опроса: 300 мс для дискретных датчиков, 600 мс для аналоговых датчиков расхода, давления, уровня и 1200 мс для аналоговых датчиков температур. Максимальное время обновления информации на рабочих местах операторов - 2 с.
В системе предусмотрены устройства бесперебойного питания для аппаратных средств нижнего уровня, а также для операторских станций верхнего уровня. Время работы контроллеров при полном отключении сетевого электропитания - не менее 2 часов.
Система отображения информации
Система отображения информации обеспечивает выполнение следующих функций:
1. Представление технологической информации на экранах мониторов в следующих форматах по выбору оператора:
в виде мнемосхем с различной детализацией, на которых воспроизводится информация о текущем состоянии технологического процесса и значения технологических параметров;
в виде обобщенных и детализированных кадров аварийных состояний, как технологического процесса, так и технических средств АСУ ТП;
в виде операторских рапортов (за час, смену, сутки, месяц).
2. Автоматическую сигнализацию и регистрацию достижения параметром аварийной и предупредительной границ;
3. Управление оператором механизмами в соответствии с технологическим регламентом. Система управления обеспечивает защиту от неправильных действий операторов;
4. Формирование и вывод на экран монитора протокола сообщений (событий), например, срабатывание предупредительной и аварийной сигнализаций, неисправность датчиков, сообщения о действиях оператора по квитированию, снятию с опроса и изменению состояния исполнительных механизмов и др;
5. Формирование и отображение на дисплее различных групп графиков изменения технологических параметров.
Мнемосхема "Котел №3
Дата добавления: 2022-01-22; просмотров: 30; Мы поможем в написании вашей работы! |
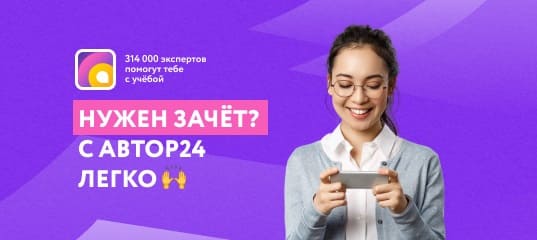
Мы поможем в написании ваших работ!