Краткая характеристика угольных месторождений.
МИНИСТЕРСТВО ОБРАЗОВАНИЯ И НАУКИ РОССИЙСКОЙ ФЕДЕРАЦИИ
ФЕДЕРАЛЬНОЕ ГОСУДАРСТВЕННОЕ БЮДЖЕТНОЕ ОБРАЗОВАТЕЛЬНОЕ УЧРЕЖДЕНИЕ
ВЫСШЕГО ПРОФЕССИОНАЛЬНОГО ОБРАЗОВАНИЯ
«НАЦИОНАЛЬНЫЙ МИНЕРАЛЬНО-СЫРЬЕВОЙ УНИВЕРСИТЕТ «ГОРНЫЙ »
Кафедра разработки месторождений полезных ископаемых
КОНСПЕКТ ЛЕКЦИЙ
Технология горного производства
Для специальности МП, МТ)
Автор : доцент Сиренко Ю.Г.
Санкт-Петербург
2013
ОГЛАВЛЕНИЕ
1. Введение
2. .Горно-геологические условия залегания МПИ
3. Краткая характеристика угольных месторождений
4. Краткая характеристика рудных месторождений
5. Способы разработки МПИ
6. Основные принципы подземной разработки месторождений
7. Горные предприятия. Запасы и потери ПИ
8. Основные параметры горных предприятий
9. Производственная мощность и срок службы шахты 10. Стадии разработки шахтных полей
11. Способы подготовки шахтных полей
- Вскрытие шахтных полей
- Классификация. Требования к оптимальному способу вскрытия.
- .Взаимное расположение шахтных стволов в ш.п.
15. Вскрыие пологих пластов
- Вскрытие пологих пластов наклонными стволами
- . Достоинства вскрытия наклонными стволами
- Вскрытие пологих пластов вертикальными стволами и квершлагами
- . Вскрытие пологих пластов вертикальными стволами и гезенками
- Вскрытие крутых и крутонаклонных пластов
- . Вскрытие штольней
- Комбинированные способы вскрытия
- .Вскрытие шахтных полей на больших глубинах
- . Вскрытие вертикальными стволами и горизонтными квершлагами
- . Блоковое вскрытие
- . Технология очистных работ в длинном очистном забое
- Околоствольные дворы. Поверхностный комплекс шахты
- Типы ОД
- Системы разработки пластовых месторождений. Понятие «очистные работы» и «системы разработки месторождений». Классификация систем разработки. Факторы, влияющие на выбор системы разработки.
- .Сплошные системы разработки.
- Особенности разработки рудных месторождений.
- Разработка МПИ открытым способом.
|
|
Технология горного производства (для МП и МТ)
Введение
Содержание курса, его цели и задачи. Связь курса со смежными дисциплинами. Состояние угольной промышленности в России и в мире. Условия залегания и разработки пластовых месторождений. Осложняющие факторы. Экономические ориентиры технической политики при разработке пластовых месторождений
РЕКОМЕНДУЕМАЯ ЛИТЕРАТУРА
Основная
1. Пучков Л.А.. Жежелевский Ю.А. Подземная разработка месторождений полезных ископаемых. Учебник. М. 2007.
|
|
2. Егоров П.В., Бобер Е. А. и др. Основы горного дела. Учебник. 2-е изд. 2006.
3. Васильев А.В., Зубов В.П.Сиренко Ю.Г.. Моделирование на ЭВМ стоимостных показателей горных работ в шахтах. Методические указания к расчетно-графическим работам для студентов горно-геологических специальностей. РИЦ Национального минерально-сырьевого университета «Горный”,2012 г.
Дополнительная
1. Килячков А.П. Технология горного производства. М., Недра, 1992.
2. Черняк И.Л., Ярунин С.А., Бурчаков Ю.И. Технология и механизация подземной добычи угля. М., Недра, 1981.
4. Бурчаков А.С., Гринько Н.К., Черняк И.Л. Процессы подземных горных работ. М., Недра, 1982
3. Задачник по подземной разработке угольных месторождений. Авт. Сапицкий К.Ф., Дорохов Д.В., Зборщик М.П., Андрушко В.Ф. М., Недра, 1981.
4. Васильев А.В., Сиренко Ю.Г. Моделирование на ЭВМ основных параметров шахты. / Санкт-Петербургский горный институт, СПБ, 1995
5. Правила безопасности в угольных шахтах. (ПБ-05-618-03). Серия 05, выпуск 11 / колл. Авт. М..: ФГУП ''Научно-технический центр по безопасности в промышленности'', 2005, 296 с.
.
Введение
Для повышения эффективности производства работники угольной отрасли сосредотачивают свои усилия на трех главных направлениях:
|
|
- комплексная механизация и автоматизация производственных процессов, которые создают предпосылки для выемки угля без постоянного присутствия людей в очистном забое, облегчают и улучшают условия труда, способствуют повышению производительности труда;
- опережающее развитие добычи угля открытым способом, главным образом на Востоке страны;
- повышение производительности труда на основе широкого внедрения в производство достижений науки и техники, прогрессивной технологии, передового опыта, научной организации труда, развертывания социалистического соревнования, поиска и максимального использования резервов, а также систематического повышения общеобразовательного уровня и профессионального мастерства рабочих. В соответствии с программой курса рассматриваются вопросы разработки пластовых месторождений подземным способами во всем их многообразии - вскрытие, подготовка, системы разработки и технология очистных работ (Дается программа).
1.2 Горно-геологические условия залегания месторождений полезных ископаемых.
Полезными ископаемыми называют природные минеральные вещества, которые добываются из недр земли для использования в народном хозяйстве.
|
|
Существуют различные классификации полезных ископаемых: по назначению, по генезису и т.п. По промышленному назначению их можно разделить на руды металлов (и металлы), топливо и нерудные месторождения.
Месторождение - это естественное скопление полезного ископаемого в земной коре.
Большое значение для разработки имеет форма месторождения. В зависимости от формы различают пластовые месторождения, жилы, штоки, гнезда и т.д. Из числа пластовых месторождений наибольшее распространение имеют угольные. Нередко они имеют значительное распространение по площади.
Угленосным районом называется часть бассейна, объединенная тектоническими особенностями и качеством углей, а иногда административно-хозяйственными особенностями.
Бассейн - это площадь непрерывного залегания угленосных отложений.
Границы месторождения определяются условиями залегания ПИ. При негоризонтальном залегании границами угольных месторождений могут быть: по восстанию - выход пластов под наносы, по падению - границы разведанности, по простиранию - выклинивания пласта, крупные геологические нарушения и т.д.
Месторождение называется промышленным, если целесообразность его разработки обоснована экономически и имеет народнохозяйственное значение в настоящее время или в будущем. В противном случае оно не промышленное.
Крупные месторождения обычно разрабатываются несколькими шахтами.
Краткая характеристика угольных месторождений.
Энергетическая ценность углей, (рис.1.1). Разница между объёмами добытого угля, (кривые 2 и 3, рис. 1.1) и его энергетической ценностью (кривые 4 и 5) характеризует качество разрабатываемых пластов по установленным ГКЗ кондициям и степень соответствия применяемых средств механизации добычи горно-геологическим условиям разработки по засорению угля вмещающими породами Возрастающая разница в объёмах добычи угля и его энергетической ценностью в отечественной промышленности (кривые 2 и 5, рис 1.1), объяснялась Минуглепромом СССР постоянно ухудшающимися горно-геологическими условиями разработки месторождений, необходимостью вовлечения в разработку тонких и весьма тонких пластов и пластов сложного строения, социально-экономическими требованиями комплексной механизации добычи угля в длинных очистных забоя, а также целесообразностью обогащения всей массы добытого угля на земной поверхности.
В процессе восстановления мировых экономик в посткризисный период отмечается постепенное улучшение показателей работы угольной отрасли. Практически все показатели работы отечественной угольной промышленности в 2010 г. были значительно выше, чем годом ранее в условиях глобального финансово-экономического кризиса и постепенно приближаются к уровню докризисного периода.
Россия является одним из мировых лидеров по производству угля. В ее недрах сосредоточена треть мировых ресурсов угля и пятая часть разведанных запасов – 193,3 млрд т. Из них 101,2 млрд т бурого угля, 85,3 млрд т каменного угля (в том числе 39,8 млрд т коксующегося) и 6,8 млрд т антрацитов. Промышленные запасы действующих предприятий составляют почти 19 млрд т, в том числе коксующихся углей — около 4 млрд т. Прогнозные ресурсы составляют 3816,7 млрд т. Российская Федерация занимает второе место по запасам и пятое место по объему добычи угля (более 320 млн т в год). При существующем уровне добычи угля его запасов хватит более чем на 550 лет.
В угольной промышленности России действует 228 угледобывающих предприятий (91 шахта и 137 разрезов) общей годовой производственной мощностью более 370 млн т. Практически вся добыча угля обеспечивается частными предприятиями. Переработка угля осуществляется на 68 обогатительных фабриках и установках механизированной породовыборки.
В пределах Российской Федерации находятся 22 угольных бассейна и 129 отдельных месторождений. Добыча угля ведется в семи федеральных округах, 26 субъектах Российской Федерации и в 85 муниципальных образованиях России, из которых 58 являются углепромышленными территориями на базе градообразующих угольных предприятий. В отрасли задействовано около 200 тыс. человек. С угольной отраслью России связано (вместе с членами семей шахтеров и смежниками) около 3 млн человек.
В России уголь потребляется во всех 86 субъектах Российской Федерации. Основные потребители угля на внутреннем рынке – это электростанции и коксохимические заводы. Из угледобывающих регионов самым мощным поставщиком угля является Кузнецкий бассейн – здесь производится 57% всего добываемого угля в стране и около 80% углей коксующихся марок.
Но совершенно особая, просто трагическая ситуация складывается с угледобывающей промышленностью, скорость развала которой превосходит все мыслимые представления. Напомню, каменный уголь был и продолжает оставаться основой мировой энергетики. Его добычу стремительно наращивают все страны мира. За последние 10—15 лет производство угля в Австралии увеличилось в 3,7 раза, в ЮАР — в 3,2, Китае — в 3, Индии — в 2,6, в США — в 1,7 раза. Доля угля в мировом производстве электроэнергии составляет около 50%, в Польше — 96, ЮАР — 95, Австралии — 86, КНР — 71, Великобритании — 63, ФРГ — 63, США — 56%. США уже довели ежегодную добычу угля до 1100, а Китай — до 1500 миллионов тонн.
И лишь Россия — единственная страна в мире, где за последние 10 лет добыча угля упала вдвое,— с 450 млн. до 230 млн. тонн — на фоне экспорта угля, рубеж. Доля угля в российском топливно-энергетическом балансе составляет сейчас лишь... 12%, а в выработке электроэнергии — 26%. В переводе на простой русский язык это означает, что ельцины-гайдары-черномырдины ухитрились за две «пятилетки» полностью развалить и уничтожить мощнейшую угольную промышленности страны.
Если на душу населения Австралия добывает более 12 тонн, Польша — 5,5 тонны, США — 3,7 тонны, то на современного россиянина приходится всего лишь 1,5 тонны угля. А ведь СССР добывал около 700 миллионов тонн угля и уступал в этом отношении лишь США. Сейчас мы спешим занять то же место, которое занимала в мире крайне отсталая дореволюционная Россия. Напомню наивным патриотам «мощной царской России», что в 1913 году страна добывала всего лишь 29 миллионов тонн угля — в 18 раз меньше, чем США, и в 10 раз меньше, чем Германия или Великобритания.
ДОБЫЧА УГЛЯ 2010 г |
Добыча угля в России за 2010 г. составила 323 млн т. По сравнению с 2009 г. она увеличилась на 20,4 млн т (рост на 7%), однако это пока ниже уровня наиболее удачного для угольной отрасли 2008 г. на 5,9 млн т или на 2%. Поквартальная добыча составила: в первом – 83,3; во втором – 73; в третьем – 76,7; в четвертом – 90 млн т (на 13,3 млн т, или на 17% выше предыдущего квартала).
(2005 г. – 299,8 млн. т.; 2006 – 310; 2007 -;314,4; 2008 - 328,9; 2009 – 302,6; 2010 – 323)
Подземным способом добыто 102,1 млн т угля (на 5,3 млн т, или на 5% меньше чем годом ранее). Снижение добычи угля подземным способом обусловлено временным выбытием добывающих мощностей на шахте «Распадская» (добыча угля на шахте прекращена с момента аварии - 8 мая 2010 г.) и проведением массовых проверок технического состояния шахт, вследствие данной аварии. Поквартальная добыча угля подземным способом составила: в первом – 28,8; во втором – 23,9; в третьем – 24,2; в четвертом – 25,2 млн т (на 1 млн т, или на 4% выше предыдущего квартала). За 2010 г. проведено 496 км горных выработок (на 22 км, или на 4% ниже уровня 2009 г.), в том числе вскрывающих и подготавливающих выработок – 384 км (на 28 км, или на 7% ниже чем годом ранее).
Добыча угля открытым способом составила 220,9 млн т (на 25,7 млн т, или на 13% выше уровня 2009 г.). Поквартальная добыча угля открытым способом составила: в первом – 54,5; во втором - 49,1; в третьем – 52,5; в четвертом – 64,8 млн т (на 12,3 млн т, или на 23% выше предыдущего квартала). При этом объем вскрышных работ за 2010 г. составил 1135,4 млн куб. м (на 170,1 млн куб. м, или на 17,6% выше объема 2009 г.).
Удельный вес открытого способа в общей добыче составил 68,4% (годом ранее – 64,5%).
Гидравлическим способом добыто 1,3 млн т (на 58 тыс. т, или на 5% выше уровня 2009 г.). Гидродобыча ведется в ООО «Объединение «Прокопьевскуголь» (1,07 млн т) и в шахтоуправлении «Прокопьевское» (235 тыс. т).
ДОБЫЧА УГЛЯ ДЛЯ КОКСОВАНИЯ |
В 2010 г. было добыто 65,1 млн т коксующегося угля, что на 4,1 млн т, или на 7% выше уровня 2009 г. Поквартальная добыча составила: в первом – 16,9; во втором – 15,7; в третьем – 15,2; в четвертом – 17,3 млн т (на 2,1 млн т, или на 14% выше предыдущего квартала).
Доля углей для коксования в общей добыче составила только 20%. Основной объем добычи этих углей пришелся на предприятия Кузбасса – 78%. Здесь было добыто 50,5 млн т угля для коксования, что на 1,6 млн т меньше чем годом ранее (спад на 3%). Добыча коксующегося угля в Печорском бассейне составила 7,2 млн т (2009 г. – 5,9 млн т; рост на 21%). В Республике Саха (Якутия) было добыто 7,4 млн т угля для коксования (годом ранее было 3 млн т; рост в 2,5 раза).
Добыча угля в России по видам углей, млн т
По результатам работы в 2010 г. наиболее крупными производителями угля для коксования являются: ОАО «Мечел» (14481 тыс. т, в том числе ОАО ХК «Якутуголь» - 7409 тыс. т, ОАО «Южный Кузбасс» - 7072 тыс. т); ООО «Холдинг Сибуглемет» (8095 тыс. т, в том числе ОАО «Междуречье» - 3113 тыс. т, ОАО «Шахта «Полосухинская» - 2903 тыс. т, ОАО «Шахта «Большевик» - 1303 тыс. т, ЗАО «Шахтоуправление «Антоновское» - 776 тыс. т); ООО «Евраз Холдинг» (7913 тыс. т, в том числе ОАО «ОУК «Южкузбассуголь» - 7509 тыс. т, ООО «Шахта №12 - 404 тыс. т); ОАО «Воркутауголь» (7197 тыс. т); ОАО «Распадская» (7160 тыс. т); ОАО «УК «Кузбассразрезуголь» (4686 тыс. т); ОАО «Белон» (4133 тыс. т); ОАО «СУЭК-Кузбасс» (2743 тыс. т); ООО «Объединение «Прокопьевскуголь» (2246 тыс. т).
Российские производители коксующегося угля (добыча за 2010 г., тыс. т) Всего добыто 65111 тыс. т
НАГРУЗКА НА ЗАБОЙ И ПРОИЗВОДИТЕЛЬНОСТЬ |
В 2010 г. среднесуточная добыча угля из одного действующего очистного забоя по сравнению с 2009 г. увеличилась с 2566 т на 6% и составила в среднем по отрасли 2730 т.
Среднесуточная нагрузка на комплексно-механизированный очистной забой составила 3627 т и возросла по сравнению с 2009 г. с 3421 т на 6%, а на лучших предприятиях она значительно превышает среднеотраслевой показатель.
По итогам 2010 г. наиболее высокая среднесуточная добыча из действующего очистного забоя достигнута: ОАО «Шахта «Южная» - 9476; ЗАО «Салек» - 7618 т; ОАО «СУЭК-Кузбасс» - 6911 т; ОАО «Шахта «Заречная» - 6578 т; ОАО «Распадская» - 6294 т; ООО «Шахта «Колмогоровская-2» - 5826 т; ОАО «Шахтоуправление «Интинская угольная компания» - 5525 т; ЗАО «Шахта Воргашорская-2» - 5454 т; ОАО «УК «Кузбассразрезуголь» - 5113 т.
По основным бассейнам среднесуточная добыча угля из одного действующего очистного забоя составила: в Кузнецком – 2879 т (из комплексно-механизированного забоя - 4395 т); в Печорском – 3349 т (из КМЗ – 3349 т); в Донецком – 1351 т (из КМЗ – 1351 т); в Дальневосточном регионе – 2324 т (из КМЗ - 2324 т); в Уральском регионе – 440 т (из КМЗ – 440 т).
Удельный вес добычи угля из комплексно-механизированных забоев в общей подземной добыче в 2010 г. составил 85% (на 0,3% выше уровня 2009 г.). По основным бассейнам этот показатель составил (%): в Печорском – 89,7 (2009 г. – 84,7); в Донецком – 89,5 (2009 г. – 87); в Кузнецком – 83,6 (2009 г. – 84,1); в Уральском регионе – 96,6 (2009 г. – 88,6); в Дальневосточном регионе – 92 (2009 г. – 92,1).
Среднедействующее количество комплексно-механизированных забоев в 2010 г. составило 88,4 (годом ранее было 102,5). По основным бассейнам этот показатель составил: в Печорском – 10,1 (2009 г. – 10,2); в Донецком – 9,5 (2009 г. – 9,2); в Кузнецком – 44,3 (2009 г. – 54,1); в Уральском регионе – 1 (2009 г. – 1,2) в Дальневосточном регионе – 22,5 (2009 г. – 25,5).
По итогам работы в 2010 г. среднемесячная производительность труда рабочего по добыче угля (квартальная) достигла 192,2 т. Годом ранее производительность труда была 167,7 т/мес., т.е. она возросла на 15%. При этом производительность труда рабочего на шахтах составила 133,9 т/мес., на разрезах – 285,6 т/мес. За десятилетие производительность труда рабочего возросла почти в 2 раза (в 2000 г. она составляла в среднем 110,3 т/мес.).
СЕБЕСТОИМОСТЬ |
Себестоимость добычи 1 т угля за январь-ноябрь 2010 г. составила 970,02 руб. За год она возросла на 63,04 руб. При этом производственная себестоимость добычи 1 т угля возросла на 48,51 руб. и составила 781,94 руб., а внепроизводственные расходы на добычу 1 т выросли на 13,57 руб. и составили 183,16 руб. В свою очередь производственная себестоимость по элементам затрат распределена следующим образом: материальные затраты составили 385,73 руб./т (рост на 60,87 руб./т по сравнению с январем-ноябрем 2009 г.); расходы на оплату труда – 152,26 руб./т (сокращены на 8,01 руб./т); отчисления на социальные нужды – 39,43 руб./т (уменьшены на 2,63 руб./т); амортизация основных фондов – 79,01 руб./т (сокращена на 11,98 руб./т); прочие расходы – 125,50 руб./т (увеличены на 10,25 руб./т).
ЧИСЛЕННОСТЬ ПЕРСОНАЛА |
Средняя численность работников предприятий угледобычи и переработки на конец декабря 2010 г. составила 164,7 тыс. человек (за год уменьшилась на 9,1 тыс. чел.). При этом среднесписочная численность работников по основному виду деятельности на угледобывающих и углеперерабатывающих предприятиях на конец декабря составила 158,2 тыс. чел., т.е. за год уменьшилась на 7,8 тыс. человек. Среднесписочная численность рабочих по добыче угля (квартальная) составила 96,4 тыс. чел. (2009 г. – 103,4 тыс. чел.), из них на шахтах – 59,3 тыс. чел. (2009 г. – 65,1 тыс. чел.) и на разрезах – 37,1 тыс. чел. (2009 г. – 38,3 тыс. чел.).
Среднемесячная заработная плата одного работника на российских предприятиях угледобычи и переработки на конец декабря 2010 г. составила 27327 руб., за год она увеличилась на 17%.
Основные показатели работы угольной отрасли России за 2010 г.
Показатели | 2010 г . | 2009 г . | К уровню 2009 г., % |
Добыча угля, всего, тыс. т: | 323 000 | 302 573 | 106,8 |
- подземным способом | 102 050 | 107 430 | 95,0 |
- открытым способом | 220 950 | 195 143 | 113,2 |
Добыча угля для коксования, тыс. т | 65 111 | 60 973 | 106,8 |
Переработка угля, всего тыс. т: | 126 023 | 117 726 | 107,1 |
- на фабриках | 117 573 | 108 761 | 108,1 |
- на установках механизированной породовыборки | 8 450 | 8 965 | 94,3 |
Поставка российских углей, всего тыс. т | 295 028 | 283 893 | 103,9 |
- из них потребителям России | 179 725 | 176 508 | 101,8 |
- экспорт угля | 115 303 | 107 385 | 107,4 |
Импорт угля, тыс. т | 29 616 | 24 014 | 123,3 |
Поставка угля потребителям России с учетом импорта, тыс. т | 209 341 | 200 522 | 104,4 |
Среднесписочная численность работников по основному виду деятельности, чел. | 158 166 | 166 014 | 95,3 |
Среднесписочная численность рабочих по добыче угля (квартальная), чел. | 96 390 | 103 404 | 93,2 |
Среднемесячная производительность труда рабочего по добыче угля (квартальная), т | 192,2 | 167,7 | 114,6 |
Среднемесячная заработная плата одного работника, руб. | 27 327 | 23 402 | 116,7 |
Среднесуточная добыча угля из одного действующего очистного забоя, т | 2 730 | 2 566 | 106,4 |
Среднесуточная добыча угля из одного комплексно-механизированного забоя, т | 3 627 | 3 421 | 106,0 |
Количество категорированных аварий | 22 | 13 | 1,7 раза |
Количество случаев со смертельными травмами | 144 | 58 | 2,5 раза |
Проведение подготовительных выработок, тыс. м | 496 | 518 | 95,8 |
Вскрышные работы, тыс. куб. м | 1 135 383 | 965 271 | 117,6 |
ПОСТАВКА УГЛЯ
Угледобывающие предприятия России в 2010 г. поставили потребителям 295 млн т угля. Это на 11,1 млн т, или на 4% выше уровня 2009 г. Поквартальная поставка составила: в первом квартале – 78,2; во втором – 70,8; в третьем – 68,3; в четвертом – 77,7 млн т (на 9,4 млн т, или на 14% выше предыдущего квартала). Из всего поставленного объема на экспорт отправлено 115,3 млн т. Это на 7,9 млн т больше чем годом ранее (рост на 7%).Внутрироссийские поставки составили 179,7 млн т. По сравнению с 2009 г. эти поставки увеличились на 3,2 млн т, или на 2%.По основным направлениям внутрироссийские поставки распределились следующим образом:- обеспечение электростанций – 96,8 млн т (увеличились на 5,2 млн т, или на 6% к уровню 2009 г.);- нужды коксования – 38,5 млн т (увеличились на 1 млн т, или на 3%);- обеспечение населения, коммунально-бытовые нужды, агропромышленный комплекс – 23 млн т (снизились на 1,4 млн т, или на 6%);- остальные потребители (нужды металлургии – энергетика, РАО «РЖД», Минобороны, Минюст, МВД, Минтранс, ФПС, Атомная промышленность, Росрезерв, цементные заводы и др.) – 21,4 млн т (снизились на 1,6 млн т, или на 7%).
ИМПОРТ УГЛЯ
Импорт угля в Россию в 2010 г. по сравнению с 2009 г. увеличился на 5,6 млн т, или на 23% и составил 29,6 млн т. Из них в первом квартале импортировано 7,5; во втором – 7,3; в третьем – 6,8; в четвертом – 8 млн т (на 1,2 млн т, или на 18% выше предыдущего квартала). Импортируется в основном энергетический уголь, практически весь объем импортного угля поступает из Казахстана (поставлено 28,8 млн т энергетического угля), незначительная часть поступает из США (поставлено 649 тыс. т, из них 625 тыс. т коксующегося угля) и Украины (поставлено 167 тыс. т, из них 6 тыс. т коксующегося угля). В 2010 г. импортировано 29 млн т энергетического угля; с учетом импорта, на российские электростанции поставлено 125,8 млн т угля (на 10,2 млн т, или на 9% больше чем годом ранее). В 2010 г. импортировано 631 тыс. т коксующегося угля; с учетом импорта, на нужды коксования поставлено 39,1 млн т (на 1,6 млн т, или на 4% выше прошлогоднего уровня). Всего на российский рынок в 2010 г. поставлено с учетом импорта 209,3 млн т, что на 8,8 млн т, или на 4% выше уровня 2009 г. При этом доля импортного угля в поставках угля на российский рынок составила 14% (2009 г. – 12%).
ЗКСПОРТ УГЛЯ
Объем экспорта российского угля в 2010 г. по сравнению с 2009 г. увеличился на 7,9 млн т, или на 7% и составил 115,3 млн т. Из них в первом квартале экспортировано 24,8; во втором – 27,5; в третьем – 27; в четвертом – 26,3 млн т.Экспорт составляет более трети добытого угля (36%). Основная доля экспорта приходится на энергетические угли – 97,3 млн т (84% общего экспорта углей). Основным поставщиком угля на экспорт остается Сибирский ФО, доля этого региона в общих объемах экспорта составляет 92%. Россия по экспорту угля находится на пятом месте в мире, а по энергетическим углям – на третьем месте.
Из общего объема экспорта в 2010 г. основной объем угля отгружался в страны дальнего зарубежья – 101,7 млн т (88% общего экспорта). В страны ближнего зарубежья поставлено 13,6 млн т.Лидерами среди стран-импортеров российского угля в 2010 г. были: Украина (поставлено 12,9 млн т), Великобритания (11,8 млн т), Турция (10,9 млн т), Китай (10,8 млн т), Япония (10,4 млн т).
Основные страны – импортеры российского угля в 2010 г., тыс. т
Лидерами среди экспортеров российского угля являются: ОАО «СУЭК» (в 2010 г. отправлено на экспорт 25,3 млн т), ОАО «УК «Кузбассразрезуголь» (24,2 млн т), ОАО ХК «СДС-Уголь» (9,2 млн т), ОАО «Мечел» (7,9 млн т), ООО «УК «Заречная» (4,7 млн т).
АВАРИЙНОСТЬ И ПРОИЗВОДСТВЕННЫЙ ТРАВМАТИЗМ
В 2010 г. произошло 22 категорированные аварии, на 9 аварий больше чем годом ранее. Количество случаев со смертельными травмами резко возросло до 144 против 58 в 2009 г.Труд под землей всегда был и остается опасным и рискованным. К несчастью, подземная стихия в очередной раз напомнила об этом. В ночь на 9 мая 2010 г. в Кузбассе на шахте «Распадская» произошли два взрыва с интервалом примерно в четыре часа. В результате двух взрывов погибли 67 человек, судьба 24 горняков оставалась неизвестной, поскольку проведение поисково-спасательных работ было затруднено действующем в шахте пожаром. По состоянию на 31.12.2010 г. число погибших при аварии на шахте «Распадская» достигло 76 человек, судьба 17 шахтеров оставалась неизвестной. Бойцы отряда ВГСЧ и рабочие шахты ведут откачку воды и разбор завалов в аварийных выработках. В январе 2011 г. были обнаружены и подняты на поверхность тела еще двух погибших горняков. После этой тяжелейшей аварии началась полномасштабная проверка всех угольных шахт, которая еще раз подтвердила необходимость коренного улучшения промышленной безопасности и охраны труда в угольной отрасли.
Выпуск углей крупных и средних классов в 2010 г., тыс. т
Бассейны, регионы | 2010 г . | 2009 г . | К уровню 2009 г., % |
Всего по России | 15 753 | 14 000 | 112,5 |
Кузнецкий бассейн | 11 519 | 9 998 | 115,2 |
Республика Хакасия | 1 484 | 1 383 | 107,3 |
Печорский бассейн | 1 095 | 957 | 114,5 |
Иркутская область | 841 | 892 | 94,3 |
Новосибирская обл. | 362 | 255 | 1,4 раза |
Донецкий бассейн | 336 | 360 | 93,3 |
Амурская область | 93 | 126 | 73,9 |
Челябинская область | 24 | 30 | 80,0 |
Динамика обогащения угля на обогатительных фабриках России, млн т
Коксующийся уголь весь обогащается, энергетический – только 20%.
Добыча угля в мире в 1980—2005 гг.
Страна, регион | 1980 | 1990 | 2000 | 2005 | ||||
млн т | % | млн т | % | млн т | % | млн т | % | |
Северная Америка | 793,7 | 20,9 | 1010,7 | 20,8 | 1055,2 | 23,5 | 1103,3 | 18,7 |
в т.ч. США | 753,7 | 19,8 | 934,4 | 19,2 | 975,3 | 21,7 | 1027,5 | 17,4 |
Южная Америка | 10,9 | 0,3 | 30,0 | 0,6 | 53,6 | 1,2 | 73,2 | 1,2 |
в т.ч. Колумбия | 4,5 | 0,1 | 20,9 | 0,4 | 38,1 | 0,8 | 59,1 | 1,0 |
Европа вне СНГ | 1212,3 | 31,8 | 1209,6 | 24,9 | 755,0 | 16,8 | 731,5 | 12,4 |
в т.ч. Германия | 483,1 | 12,7 | 466,8 | 9,6 | 205,2 | 4,6 | 208,1 | 3,5 |
Польша | 230,6 | 6,1 | 215,2 | 4,4 | 162,5 | 3,6 | 158,9 | 2,7 |
Великобритания | 130,8 | 3,4 | 94,4 | 1,9 | 30,9 | 0,7 | 20,1 | 0,3 |
СНГ | 717,4 | 18,9 | 800,9 | 16,5 | 402,3 | 8,9 | 456,2 | 7,9 |
в т.ч. Казахстан | 93,2 | 2,5 | 131,0 | 2,7 | 74,5 | 1,6 | 86,6 | 1,5 |
Россия | 391,1 | 10,3 | 410,7 | 8,4 | 250,6 | 5,6 | 291,1 | 4,9 |
Украина | 197,1 | 5,2 | 165,0 | 3,4 | 62,7 | 1,4 | 60,4 | 1,0 |
Ближний Восток | 0,9 | 1,1 | 1,3 | * | 1,4 | * | ||
Африка | 125,3 | 3,3 | 182,5 | 3,7 | 232,5 | 5,2 | 250,8 | 4,2 |
в т.ч. ЮАР | 119,9 | 3,2 | 175,3 | 3,6 | 226,1 | 5,0 | 245,3 | 4,2 |
Азия и Океания | 942,6 | 24,8 | 1626,4 | 33,5 | 1994,2 | 44,4 | 3276,7 | 55,6 |
в т.ч. Австралия | 105,3 | 2,8 | 204,3 | 4,2 | 306,9 | 6,8 | 376,0 | 6,4 |
Китай | 621,1 | 16,3 | 1080,6 | 22,2 | 1193,2 | 26,5 | 2207,0 | 37,4 |
Индия | 114,4 | 3,0 | 225,2 | 4,6 | 336,0 | 7,5 | 429,7 | 7,3 |
Индонезия | 0,9 | * | 10,9 | 0,2 | 76,3 | 1,7 | 152,4 | 2,6 |
МИР, всего | 3803,1 | 100,0 | 4861,2 | 100,0 | 4494,6 | 100,0 | 5893,1 | 100,0 |
* Менее 0,1%.
Донбасс - наиболее развит и поставляет 1/3 добываемых в СНГ углей. Там имеются угли всех марок, необходимых для промышленности. В бассейне залегает около 150 пластов с мощностью от 0,5 до 2,0 м, разрабатываемых на глубине 300-1200 м. Газоносность пластов высокая, в отдельных районах Донбасса пласты подвержены внезапным выбросам угля и газа. Вмещающие породы средней и ниже средней крепости. Водоносность незначительная. Залегание пластов от пологого до крутого.
Кузбасс - самые большие запасы углей всех марок и высокого качества. По добыче на II месте после Донбасса. Мощность пластов 1-I6 м. углы падения разные. Боковые породы крепкие и средней крепости. Разработка ведется как подземным, так и открытым способами. Глубина шахт 300-500 м. Угли в основном идут на удовлетворение потребностей Урала и Сибири.
Карагандинский угольный бассейн - Ш место по добыче. По горно-геологическим условиям разработки сходен с Донбассом. Но здесь преобладают пологие пласты (a до 18°) m = 2-8 м. Глубина разработки до 500 м. Значительная часть углей пригодна для коксования и направляется на Урал и предприятия Казахстана.
Печорский бассейн расположен на севере европейской части России и характерен пластами средней мощности m =1,2-3,5 м высококачественного коксующегося угля. Уголь идет в основном на удовлетворение нужд промышленности северных районов.
Подмосковный бассейн - горизонтально залегающие пласты, сильно обводнены, вмещающие породы ниже средней устойчивости, m -I.5-3,5, H 5-100 м.
Львовско -Волынский бассейн - такие же пласты, что и в Подмосковье, m 0,7-1,5 м, Н = 300 м.
Оба бассейна имеют местное значение, их уголь идет на удовлетворение нужд прилегающих районов.
На Урале - Кизеловский угольный бассейн - различные a , m =0,7-4 м, кокcующийся уголь, сильно обводненные пласты. Запасы кончаются. Практически закрыт.
- Челябинский бассейн - бурые угли для энергетических целей, мощные пологие пласты. Вмещающие породы ниже средней устойчивости.
В Средней Азии ряд месторождений с мощными пластами разрабатываются для нужд энергетики. Экибастузское месторождение в Казахстане m до 140 м.
Дальний Восток (Буреинское, Сучанское, Артемовское и О.Сахалин), эти месторождения эксплуатируются для удовлетворения нужд промышленности Восточных районов.
В связи с возобновлением строительства БАМа большое развитие получает добыча угля в Южно-Якутском и Канско-Ачинском бассейнах.
Большие запасы угля, в т.ч. и для коксования сосредоточены в еще не освоенных Тунгусском, Таймырском и Ленском бассейнах.
Краткая характеристика рудных месторождений.
Рудные месторождения, в отличие от угольных, характеризуются большим многообразием форм залегания. Они делятся на пластовые и пластообразные, жильные, и массивные.
Из отечественных рудных месторождений к типичным пластовым можно отнести Джезказганское медное, Миргалимсайское свинцовое, Никополь-Марганцевое и Чиатурское месторождения. Типичными пластообразными рудными телами представлено большинство месторождений Криворожского бассейна.
Жильные месторождения имеют мощность от 10-20 см до 2-5 м. Угол падения и мощность жильных месторождений могут резко меняться даже в пределах одного рудного тела.
Наиболее крупными рудниками, разрабатывающими жильные месторождения, являются золотые рудники Магаданской области, Якутской АССР, оловянные рудники Приморья, полиметаллические рудники Северного Кавказа, золотые, оловянные и вольфрамо-молибденовые рудники Забайкалья.
Массивные месторождения имеют мощность более 5 м. Эти месторождения иногда имеют форму правильных линз и столбов, но часто их форма бывает очень сложной и неправильной и обычно такие месторождения не имеют четко выраженных границ с окружающими породами. К массивным относятся некоторые месторождения (железорудные) Кривого Рога, Урала и Горной Шории, меднорудные месторождения Урала, полиметаллические - Алтая, молибденовые - Северного Кавказа.
Рудные, как и угольные месторождения, могут быть простыми и сложными.
Простые представлены одним пластом или одним рудным телом.
Сложные - свита пластов, жил или параллельных залежей и т.д.
Способы разработки МПИ.
Способ разработки - это совокупность всех производственных процессов, осуществляемых на данном горном предприятии.
При каждом способе разработки, в зависимости от конкретных геологических условий и уровня развития механизации горных работ, наибольшая эффективность добычи достигается применением наиболее оптимальных способов вскрытия, подготовки и систем разработки.
Основные принципы подземной разработки месторождений.
При подземной разработке необходимо выполнять следующие специфические для нее принципы:
1. Минимальное распространение процессов деформаций и разрушений в породах, покрывающих и подстилающих толщ.
2. Ведение горных работ всегда под "свежей кровлей" - "золотое правило" подземной разработки.
3. Планомерное управление обрушением вмещающих пород (управление кровлей).
4. Предупреждение аварий:
а) прорывов воды, газов, нефти из подземных и поверхностных источников и старых выработок;
б) взрывов газа и пыли;
в) горных ударов и внезапных выбросов;
г) эндогенных пожаров и т.д.
5. Минимальное разубоживание ПИ.
6. Обеспечение безопасности труда и создание необходимых санитарно-гигиенических условий (профилактика проф.вредностей, обеспечение нормальной температуры, влажности, запыленности и т.д.).
Выполнение этих принципов подземной разработки, для конкретных геологических условий и конкретных комплексов природных процессов в данном горном массиве, требует в первую очередь применения соответствующих систем разработки и способов управления горным давлением, а точнее: выбора правильных способов управления физическими процессами в данных конкретных условиях.
2. Горные предприятия. Запасы и потери полезного ископаемого
2.1. Горные предприятия.
Горное предприятие - это промышленное предприятие, на котором ведется разработка месторождений полезных ископаемых.
Горное предприятие, предназначенное для добывания угля (или сланца) подземным способом, называют шахтой. В понятие шахты как самостоятельной производственно-хозяйственной единицы включаются наземные сооружения и совокупность подземных горных выработок.
Несколько шахт, имеющих единый технологический комплекс на поверхности для приема, переработки и отправки угля, образуют рудник.
По относительной метанообильности, т.е. по выделению метана на I т среднесуточной добычи шахты делятся на 5 категорий:
I категория - выделение метана до 5 м3 /т
II категория - -"- от 5 до 10 м3/т
III категория - выделение метана от 10 до 15 м3/т
Сверхкатегорные - -"- 15 м3/т и более
Имеются шахты, опасные по внезапным выбросам угля и газа;
шахты с выбросами породы.
Имеются и негазовые шахты, а также шахты» в которых выделяется углекислый газ (например. Подмосковный бассейн).
В зависимости от размеров месторождения для его разработки может быть построено несколько шахт. В этом случае месторождение делят на части.
Часть месторождения, отведенная для разработки одной шахты, называется шахтным полем.
Между соседними шахтными полями обычно оставляют барьерные целики. Они предохраняют горные работы от прорыва воды и газов из отработанной шахты.
Границами шахтного поля являются ограничивающие его вертикальные и горизонтальные поверхности. В случае негоризонтального залегания пластов обычно различают границы ш.п. по восстанию (верхняя граница) по падению (нижняя граница) и по простиранию (боковые границы).
1 - линия выклинивания (граница месторождения по простираний)
2 - сброс ( граница по простиранию)
3 - техническая граница месторождения по восстанию
4 - граница разведанности (граница по падению)
5 - барьерные целики
При разделении месторождения на шахтные поля им по возможности придают форму прямоугольникам, вытянутого по простиранию. В этом случае размеры шахтного поля определяются на основании технико-экономических расчетов»
При невыдержанных элементах залегания и наличии крупных нарушений, при необходимости оставлять целики под водоемами и сооружениями шахтные поля могут иметь самую различную конфигурацию.
Шахтное поле имеет 2 размера:
S - длину по простиранию - 6-10 до 12-20 км;
H - длину по падению - 4-5 км.
На чертежах и маркшейдерских планах шахтные поля со всеми расположенными в их пределах выработками изображают при пологом и наклонном падении пластов как проекции на горизонтальную плоскость, а при крутом падении - только на вертикальную плоскость.
Кроме этих проекций дается разрез шахтного поля вкрест простирания пластов. Пласты угля здесь наносят с соблюдением их истинного угла падения.
Часть шахтного поля, расположенная по одну сторону от главного ствола, называется крылом шахты. В зависимости от места заложения ствола шахтные поля могут быть двукрылыми и однокрылыми.
Запасы и потери угля.
Запасами называют полное количество полезного ископаемого в данном месторождении или его отдельных частях. В зависимости от мощности и условий залегания пласта, а также качества угля различают балансовые и забалансовые запасы полезного ископаемого
Балансовые - по качеству ПИ удовлетворяют требованиям (кондициям) их промышленного использования и при современном уровне техники и экономики пригодны для добывания.
Забалансовые - не удовлетворяют этим требованиям и поэтому их использование в настоящее время нецелесообразно. Но их можно рассматривать как объект промышленного освоения в дальнейшем с развитием и совершенствованием техники добычи, обогащения и использования.
При разработке месторождения, отработке шахтного поля не все балансовые запасы могут быть выданы на поверхность. Часть из них остается в недрах и составляет потери. Та часть балансовых запасов, которая может быть выдана на поверхность за вычетом потерь называется промышленными запасами.
Потери полезного ископаемого принято разделять на 3 группы;
I. Общешахтные.
2. Связанные с геологическими нарушениями.
3. Эксплуатационные.
Или на 2 группы - по площади и по мощности.
1. Общешахтные потери - в охранных целиках под зданиями и сооружениями, водоемами и другими поверхностными сооружениями, а также, в барьерных целиках, предназначенных для отделения шахтных полей и некоторых их участков друг от друга. Размеры этих потерь не связаны с применяемой системой разработки.
Потери угля в барьерных целиках. Эти целики работают на сжатие под влиянием веса пород покрывающей толщи и на сдвиг под влиянием напора воды, скопившейся в старых выработках. Их размеры можно посчитать по методу, предложенному В.Д.Слесаревым или с помощью эмпирических формул.
Эти потери нецелесообразно включать в потери одной из шахт.
Потери угля в охранных целиках. Эти целики оставляются под поверхностными сооружениями, водоемами и т.д. Их размеры определяются на основании правил охраны сооружений от вредного влияния горных работ. Ориентированно размеры этих потерь можно принимать 0,5-2% при пологих пластах и I,5—4% при крутых от балансовых запасов.
2. Потери, связанные с геологическими нарушениями определяются характером и числом нарушений, их ориентированием в шахтном поле, глубиной разработки и т.д.
3. Эксплуатационные потери. Они связаны с применением систем разработки и технологией очистных работ. К этим потерям относятся: невынимаемые части целиков у подготовительных выработок, в очистном пространстве и на границах выемочных участков (их называют потерями по площади). Определяются они расчетом после определения размеров целиков; пачки угля , оставляемые в почве или кровле, или между слоями угля (потери по мощности зависят от строения пласта и технологии работ).
К эксплуатационным относятся и потери от неправильного ведения горных работ (целики вследствие завалов и т.д.), от подземных пожаров, выбросов, а также потери при транспортировании, погрузке и перегрузке ПИ (принимаются около 0,5% от балансовых запасов).
Часть балансовых запасов, которые могут быть выданы на поверхность при разработке шахтного поля называются промышленными запасами. Они равны балансовым за вычетом потерь.
Количество ПИ, добываемого из месторождения, оценивается коэффициентом извлечения, который показывает какую часть балансовых запасов добывают, т.е. выдают на поверхность.
При ориентировочных расчетах с достаточной степенью точности этот коэффициент (С) можно принимать равным:
для тонких пластов - 0,92-0,90; для пластов средней мощности - 0,88-0,85; для мощных пологих пластов - 0,85-0,82; для мощных крутых пластов - 0,80-0,75. При известных размерах шахтного поля промышленные запасы можно ориентировочно подсчитать по формуле:
где
Q - промышленные запасы ш.п., т;
S - размер ш.п. по простиранию, м;
H - размер ш.п. по падению, м;
m - мощность пласта, м;
g - средняя плотность угля, т/м3 (1,2-1,6);
С - коэффициент извлечения.
Если в ш.п. несколько пластов, то запасы по ним суммируются.
3. Основные параметры горных предприятий.
Основными параметрами шахт являются производственная мощность, срок службы и размеры шахтных полей. Эти параметры неразрывно связаны между собой. Их нужно тщательно определять, так как они во многом определяют всю экономику угледобычи.
Производственная мощность и срок службы шахты.
Производственная мощность шахты (А) - это количество ПИ в тоннах, добываемого в единицу времени (сутки, год), при полном использовании производственного оборудования и фронта очистных работ.
Срок службы (Т) - время в годах, в течение которого будут выниматься промышленные запасы.
Между этими параметрами существует зависимость:
Стадии разработки шахтных полей.
Чтобы приступить к добыче ПИ необходимо произвести вскрытие и подготовку шахтного поля.
Вскрытие ш.п. - обеспечение доступа с поверхности земли к месторождению путем проведения горных выработок, с целью создания условий для подготовки и отработки запасов ПИ.
Главная цель вскрытия - создание транспортных связей между очистными забоями и пунктами приема ПИ на поверхности, обеспечение условий для безопасного перемещения людей и создание комфортных условий на рабочем месте.
Вскрывающие выработки делятся на главные, имеющие выход на земную поверхность (стволы, штольни) и вспомогательные, не имеющие выхода на земную поверхность (квершлаги, гезенки и т.д.).
Подготовка ш.п. - это определенный порядок проведения подготовительных выработок после вскрытия ш.п., обеспечивающий ведение очистной выемки.
Очистная выемка - комплекс работ по извлечению (добыче) ПИ из очистного забоя. Фронт очистных работ перемещается, сокращается. Для его воспроизводства необходима непрерывная подготовка -проведение подготовительных и нарезных работ.
Совокупность работ по вскрытию, подготовке и очистной выемке и есть разработка месторождений ПИ. В соответствии с "Основами законодательства РФ" при разработке месторождений полезных ископаемых должно быть обеспечено:
1) применение рациональных и эффективных методов добычи, недопущение сверхнормативных потерь;
2) доразведка месторождения;
3) учет состояния и движения запасов;
4) недопущение порчи соседних месторождений и сохранение консервируемых запасов;
5) сохранение и учет добываемых и не используемых ПИ, а также отходов, содержащих полезные компоненты;
6) безопасность рабочих шахты и населения, охрана недр и окружающей среды, зданий.
4. Способы подготовки шахтных полей.
Для удобства разработки ш.п., как правило, делится на более мелкие части. Так, например, при разработке пологих пластов ш.п. по падений делится на две, три и даже четыре примерно равные части (ступени или горизонты). Размеры этих частей не превышают 1000-1200 м. Границей между горизонтами является главный откаточный штрек и верхняя или нижняя граница ш.п.
Часть ш.п., расположенная выше главного откаточного штрека, обслуживается бремсбергом и называется бремсберговым полем, а расположенная ниже главного откаточного штрека - уклонным полем. Чаще всего каждый из горизонтов, в зависимости от геологических, технических и экономических факторов, делят на этажи, блоки или столбы по падению (восстанию) пласта. В зависимости от этого различают два основных способа подготовки ш.п.: этажный и панельный и, как их разновидности, блоковый и погоризонтный.
5. Вскрытие шахтных полей.
Классификация. Требования к оптимальному способу вскрытия.
Многообразные способы вскрытия пластовых месторождений классифицируются по различным признакам:
- по типу основных вскрывающих выработок;
- по ориентированию основных вскрывающих выработок в пространстве;
- по типу и расположению вспомогательных вскрывающих выработок;
- по числу подъемных горизонтов и т.д.
При вскрытии свиты пластов применяются раздельные (каждый пласт вскрывается отдельно), совместные и комбинированные способы вскрытия.
По условиям залегания различают способы вскрытия горизонтальных, пологих, крутых, наклонных пластов и пластов с изменяющимися углами падения.
По типу основных вскрывающих выработок различают:
- вскрытие штольнями,
- вскрытие стволами,
- комбинированные.
Способы вскрытия стволами делятся на три группы:
- вертикальными стволами,
- наклонными стволами,
- комбинированные.
Широко применяются на практике классификация способов вскрытия по сочетанию основных и вспомогательных вскрывающих выработок. К вспомогательным относятся квершлаги, гезенки, иногда слепые стволы.
Гезенки применяются при горизонтальном и весьма пологом залегании пласта, а с увеличением угла падения они заменяются квершлагами.
По числу горизонтов, с которых ведется подъем ПИ, различают одногоризонтные и многогоризонтные способы вскрытия.
На выбор оптимального способа вскрытия влияют горно-геологические и горнотехнические факторы.
Горно-геологические: число пластов в свите, углы падения пластов и их изменения, свойства и мощность вмещающих пород, мощность наносов, водоносные горизонты и плывуны, тектоника! месторождения, газоносность пластов, глубина залегания, рельеф местности и т.д.
Горнотехнические: уровень развития горной техники, размеры т.п., производственная мощность и срок службы шахты и т.д.
Требования к оптимальному способу вскрытия для конкретных условий:
- минимальные капитальные вложения на вскрытие месторождения,
- минимальные эксплуатационные расходы (подъем, транспорт, поддержание выработок, водоотлив, проветривание),
- минимальный срок ввода, шахты в эксплуатацию,
- оптимальные технические решения (однотипность транспорта, эффективное и надежное проветривание, максимальная концентрация горных работ),
- максимальное извлечение ПИ.
Взаимное расположение стволов в шахтном поле
Правильный выбор места заложения стволов в ш.п. является одним из основных факторов, т.к. от этого зависят суммарная длина главных выработок (стоимость их проведения и поддержания), расходы на транспорт груза и проветривание выработок, потери ПИ в охранных целиках около стволов.
Место заложения стволов определяется принятым способом. вскрытия и корректируется в соответствии с рельефом местности, свойствами пересекаемых пород, наличием старых горных выработок и геологических нарушений.
Главный ствол (воздухоподающий) может быть расположен у верхней границы ш.п., у нижней границы или в любом другом месте по падению пласта, например, в центре ш.п.
Шахтное поле делится на две равные части - бремсберговую и уклонную.
И по простиранию расположение главного ствола целесообразнее в центре ш.п., т.е. два равных крыла.
Взаимное расположение главного и вспомогательного ствола может быть:
а) центральное (центрально-сдвоенное),
б) центрально-отнесенное,
в) фланговое (диагональное),
г) комбинированное,
д) секционное (блоковое).
Комбинированное и секционное расположение главного и вспомогательного стволов сочетает в себе преимущества центрально-сдвоенного, центрально-отнесенного и флангового и применяются при строительстве современных крупных шахт.
Первые: три - основные - рассмотрим подробнее.
Вскрытие пологих пластов.
6.I. Вскрытие пологих пластов наклонными стволами.
При вскрытии пласта, наклонными стволами с поверхности до нижней границы первого этажа по падению пласта примерно в центре ш.п. проходят три ствола - главный и два вспомогательных с расстоянием между ними не менее 30 м. Главный служит для подъема ПИ, один вспомогательный - для спусков грузов, другой - для спуска и подъема людей. Он оборудован: механическим подъемом и лестницами или сходнями с перилами. Три ствола - необходимость обеспечения высокой производительности шахты. На уровне границы годного угля (верхняя техническая граница) проходит вентиляционный этажный штрек, а у нижней границы этажа - откаточный этажный штрек. Между ними проводят разрезную печь и начинают очистную выемку.
Для обеспечения бесперебойной добычи угля во время отработки I этажа углубляют наклонные стволы и проводят этажный откаточный штрек. Откаточный этажный штрек I этажа служит вентиляционным для II этажа.
Для подъема ПИ по главному стволу чаще используются ленточные конвейеры, обеспечивающие полную конвейеризацию общешахтного транспорта. При углах падения, больших 18°, применяется рельсовый транспорт с использованием в качестве подъемных сосудов вагонеток или скипов. При современном техническом уровне одноступенчатый канатный подъев можно осуществить по длине наклонных стволов до 1000 м. При большей длине - многоступенчатый, что сложнее и менее выгодно.
Угольные пласты залегают, как правило, свитами, состоящими из нескольких пластов. Поэтому встает вопрос об их совместном рациональном, вскрытии, т.е. не проходить стволы по каждому из пластов, а найти способы их совместной подготовки и разработки.
Возможные способы вскрытия пологих пластов наклонными стволами:
наклонными стволами и этажными квершлагами, наклонными стволами и этажными скатами, наклонными стволами и капитальными квершлагами, наклонными стволами, пройденными под углом к линии простирания и капитальным квершлагом.
6.1.5. Достоинства вскрытия наклонными стволами
Простота, малый объем горных работ и малая стоимость проходки стволов, малые сроки ввода шахты в эксплуатацию, небольшие капиталовложения; простота поверхностного комплекса: и околоствольных дворов и др.
Недостатки;
Большая длина стволов, большая стоимость их поддержания -особенно в неустойчивых породах (наносах), невысокая производительность канатного подъема, утечки воздуха через целики между главными выработками (стволами), трудность обслуживания транспорта по наклонным стволам и др.
Способы вскрытия наклонными стволами применяются:
- при углах падения пласта до 18°- 20 при конвейерном транспорте;
- при углах падения до 30 при ребристых лентах;
- при мощности наносов 30~40м;
- при отсутствии крупных геологических нарушений, резких изменений углов падения, при отсутствии плывунов в зоне проходки стволов.
6.2. Вскрытие пологих пластов вертикальными стволами и квершлагами
Рассмотрим два основных способа вскрытия:
- вертикальными стволами и капитальными квершлагами;
- вертикальными стволами и этажными квершлагами.
Главные вертикальные стволы проходятся до горизонта капитального квершлага 2. Квершлагом вскрывают остальные пласты, свиты. По каждому из пластов проходят бремсберги 3,4,5 (капитальные - при этажном способе подготовки, панельные - при панельном). Проветривание через общий шурф 6 и вентиляционный квершлаг 10, или с помощью шурфов на каждом пласте - 6.
К моменту окончания отработки бремсберговых полей готовят уклонные поля капитальными (панельными) уклонами ~ 7,8,9.
этот способ вскрытия широко распространен, но в современных условиях его рекомендуют для шахт с годовой мощностью около 1,8 млн.т в год, при суммарной мощности междупластий вскрываемой свиты до 250-300 м; при числе пластов 4-7 и сроке службы 50 -60 лет.
При большей угленосности и мощности междупластий рациональными могут оказаться другие способы (блоковый и т.д.).
От главных вертикальных стволов - I проходят капитальный 2, или панельный бремсберги. Остальные пласты свиты вскрываются этажными (ярусными) квершлагами 4 (вентиляционный), 3, 6, 8, 9, 10 Квершлаги 8, 9 и 10 проходят от уклона 7, который проходится на высоту одного этажа после отработки бремсбергового поля. Откаточный этажный квершлаг служит для нижележащего этажа - вентиляционным.
Этот способ экономически выгоден, когда затраты на проведение квершлагов 4,3,6,8 меньше затрат на проведение вместо них бремсбергов и уклонов, т.е. при меньшем междупластьи.
Достоинства способов вскрытия вертикальными стволами и квершлагами:
Одногоризонтные способы вскрытия, в отличие от многогоризонтных, не требуют углубки стволов, установки новых подъемных машин и переоборудования поверхности при подготовке нового горизонта.
В связи с этим объем капиталовложений на действующей шахте значительно меньше, чем при многогоризонтных способах вскрытия..
Недостатки:
Необходимость углубки уклонов, что уменьшает их пропускную способность. Для обеспечения запланированной добычи приходится проходить фланговые уклоны.
По условиям подъема длина уклона ограничена, приходится проходить уклоны второй ступени, что ухудшает показатели работы транспорта, вентиляцию, увеличивается время передвижения людей к рабочим местам.
Для исключения этих недостатков длину ш.п. по падению уменьшают до 2000-2200 м. С развитием техники этот размер может быть увеличен.
6.3. Вскрытие пологих пластов вертикальными стволами .и гезенками.
Вскрытие с применением квершлагов становится невыгодным
при весьма пологих пластах (a = 3° - 8-9°), т.к. имеют место
квершлаги большой длины. В таких случаях применяют вместо квершлагов - гезенки.
Гезенки, как и квершлаги, могут быть капитальными, этажным и участковыми.
Вскрытие крутых и круто - наклонных пластов
В отличие от вскрытия пологих пластов, свиты крутых пластов вскрываются только многогоризонтными способами, центрально-сдвоенными стволами с поэтажной углубкой.
Главный ствол служит для подъема ПИ и проветривания и оборудуется одним или двумя скиповыми подъемами.
Второй (вспомогательный) ствол оборудуется двумя клетевыми подъемами - один для обеспечения рабочего горизонта, другой для подготовки следующего горизонта.
На крупных, особенно газоносных, шахтах может быть целесообразным осуществлять вскрытие тремя стволами. В этом случае третий ствол служит для проветривания и подготовки нового горизонта»
Основные способы вскрытия крутых пластов:
- вертикальными стволами и этажными квершлагами;
- вертикальными стволами и промежуточными: квершлагами.
8. Вскрытие штольней .
Самый экономичный и простой способ вскрытия. Применяется в гористой или сильнопересеченной местности. В зависимости от взаимного расположения склона и пласта штольни проходят вкрест простирания, по простиранию или под углом к простиранию пласта. Штольни целесообразно располагать так, чтобы большая часть ш.п. отрабатывалась без механического подъема ПИ и механического водоотлива. С другой стороны - устье штольни должно быть выше уровня паводковых вод за последние 40-50 лет. Склоны выше штольни не должны быть опасны по горным обвалам и снежным лавинам. По склонам оставляют охранные целики.
Место заложения устья штольни увязывают с условиями и подземного и поверхностного транспорта. Иногда с учетом всех этих факторов приходится идти на увеличение длины штольни. Штольни проходят с подъемом 0,001. У нас мало распространен этот способ, в США - широко.
9. Комбинированные способы вскрытия:
Комбинированные способы вскрытия применяются на месторождениях с многочисленными пластами, имеющими сложные условия залегания: складчатость, сбросы, надвиги, перегибы, изменяющиеся углы падения и т.д.
Нередко комбинированные способы вскрытия оказываются более эффективными и при вскрытии в обычных условиях.
Эти способы представляют наиболее многочисленный класс, который разделяется на группы. Основными группами комбинированных способов вскрытия являются:
- вертикальными и наклонными стволами;
- штольнями и стволами;
- стволами (штольнями), капитальными и этажными квершлагами;
- стволами (штольнями), горизонтными квершлагами и гезенками или скатами;
- стволами (штольнями), горизонтными квершлагами и слепыми стволами;
- стволами, квершлагами, гезенками, слепыми стволами и т.д.
10. Вскрытие шахтных полей на, больших глубинах.
10.I.Вскрытие вертикальными стволами и горизонтными квершлагами;
С увеличением глубины горных работ возрастают напряжения в горных породах, увеличивается газоносность угольных пластов, повышается температура пород, изменяются физико-механические свойства углей и пород. Все это усложняет условия проветривания, условия поддержания выработок, повышается опасность горных ударов и внезапных выбросов и т.д., т.е. усложняется эксплуатация глубоких шахт и способы вскрытия пластов на больших глубинах.
Строительство глубоких шахт требует больших капиталовложений и длительных сроков строительства. Это может окупаться только при закладке крупных шахт, т.е. при больших запасах и значительных размерах шахтных полей.
Ш.П., расположенные на больших глубинах, целесообразнее вскрывать вертикальными стволами и квершлагами. При этом одногоризонтные способы вскрытия становятся малоэффективными, т.к. капитальные бремсберги и уклоны приходится проходить значительной длины: (ступенчатый подъем), а их устойчивость хуже, чем квершлагов.
Этажные квершлаги при вскрытии пологих пластов также имеют чрезмерно большую длину, поддержание их становится невыгодным и, в связи с этим, возникает необходимость в частых углубках стволов.
Поэтому при глубоких шахтах во многих случаях более целесообразно принимать промежуточный вариант - вскрытие с горизонтными квершлагами, т.е. с разделением ш.п. на горизонты. Наклонная высота горизонта принимается 800-1200 м. Одним горизонтным квершлагом целесообразно вскрывать 2-4 этажа. Каждый горизонт можно отрабатывать капитальными бремсбергами или капитальными бремсбергами и уклонами.
В некоторых случаях вскрытие этажей между горизонтами можно осуществлять гезенками или скатами.
Подготовка может быть полевой.
Блоковое вскрытие.
Шахты большой производительной мощности (А=10-20 тыс. т/сутки) требуют максимальной производительности каждого очистного забоя, пласта и транспортной выработки, т.е. требуется высокая концентрация работ. Размеры ш.п. таких шахт составляют 12-16 км по простиранию и 3-4 км по падению и более.
Проветривание крупных шахт, из-за большой длины выработок и высокой концентрации работ, усложняется, т.к. требуется проходить основные выработки больших сечений или проходить 2-3 выработки, что экономически невыгодно. Рациональнее в таких условиях делить шахтное поле по простиранию на отдельные участки по 2,0-2,5 км, т.е. на блоки . Способ вскрытия в этом случае называется блоковым.
Околоствольные дворы. Поверхностный комплекс шахты
Околоствольный двор - это совокупность горных выработок, расположенных у ствола шахты. Эти выработки предназначены для соединения стволов шахты с главными откаточными и вентиляционными. выработками и для размещения технических и служебных пунктов общешахтных служб. К выработкам околоствольного двора; относятся откаточные выработки, служебные камеры и ходки.
Откаточные выработки предназначены для приема и отправления поездов. Служебные камеры - для размещения в них механических и электрических установок, хранения материалов, сбора шахтной воды и т.д.
Ходки соединяют откаточные выработки и камеры:.
Типы околоствольных дворов
В зависимости от порядкам движения грузов и порожняка, т.е. от схемы путей различают несколько, типов околоствольных дворов (вагонетки с глухим кузовом):
Круговой (а), петлевой (б), тупиковый (в), челноковый (г).
Камеры околоствольного двора: насосная, водосборника, центральная подстанция, угольная и породная разгрузочные ямы, депо аккумуляторных электровозов (зарядная и преобразовательная подстанции, ремонтная мастерская), камера ожидания, камера медицинского пункта, депо противопожарного поезда, камера диспетчера, подземная кладовая, склад ВВ и т.д.
Основными факторами, влияющими на выбор схемы околоствольного двора, являются:
1. Вид транспорта горной массы на шахте.
2. Схема вскрытия ш.п., взаимное расположение стволов.
3. Устойчивость горных пород.
4. Экономичность привязки околоствольного двора к вскрывающим выработкам (минимальные объемы на единицу мощности шахты).
Объемы околоствольного двора составляют 7-15% общего объема подземных выработок, а продолжительность их сооружения превышает 60% общего срока строительства шахты.
Технологический комплекс поверхности - это комплекс зданий, сооружений и оборудования, предназначенных для подъема, приема, переработки и отправки потребителям ПИ, приема и складирования породы, додачи воздуха в шахту, обеспечения горных работ электро- и пневмоэнергией, бытового обслуживания трудящихся и для очистки шахтных вод.
Капитальные затраты на сооружение поверхности - 20-25% общих затрат.
Основное требование - компактность, т.е. максимальная плотность застройки.
Технологический комплекс поверхности шахты состоит из 3-х основных блоков и отдельно стоящих зданий и сооружений, которые по своим технологическим особенностям не могут быть сблокированы.
1 - блок главного ствола
2 - блок: вспомогательного ствола
3 - блок административно-бытового комбината (АБК)
Вентиляционная установка, открытая подстанция, резервуары для воды, эстакады, градирня и т.д.
Блок главного ствола : копер, помещения технологического комплекса по приему угля и породы, пункт погрузки угля в ж.д. вагоны, станция погрузки породы, котельная, помещения подъемной установки.
Блок вспомогательного ствола: копер, комплекс по обмену вагонеток, помещения ремонтных мастерских, калориферная и компрессорная.
Блок АБК: административно-конторская часть, зал собраний и банная часть.
Мероприятия по охране окружающей среды.
На выбор схемы расположения технологического комплекса влияют: способ вскрытия, вид шахтного подъема, взаимное расположение стволов, количество отдельно выдаваемых марок угля, производственная мощность шахты и срок службы.
Околоствольные дворы и комплекс поверхности взаимно увязаны между собой: откаточные выработки ОД, ориентируют по направлению продольных осей клетевого ствола, а они зависят от компановки поверхностного комплекса и расположения железнодорожных путей.
Околоствольные дворы и технологические комплексы ориентируются по частям света. Стрелка С-Ю проходит через ось главного ствола.
ПОДЗЕМНАЯ РАЗРАБОТКА УГОЛЬНЫХ МЕСТОРОЖДЕНИЙ
15. Системы разработки пластовых месторождений. Классификация систем разработки. Факторы. влияющие на выбор системы разработки.
15.1. Понятия "очистные работы" и "система разработки месторождения".
Очистные выработки - это выработки, предназначенные для добычи полезного ископаемого. Работы в очистных выработках - очистные работы.
Система разработки - это установленный для данных геологических условий залегания пласта и принятых средств механизации выемки угля определенный порядок ведения подготовительных, нарезных и очистных работ в пределах этажа или панели, увязанный в пространстве и времени. Или:
Системой разработки называется определенный порядок проведения подготовительных и очистных выработок в их взаимной увязке во времени и пространстве.
Систем разработки множество. Каждая из них должна удовлетворять трем основным требованиям:
1. Безопасность ведения работ,
2. Экономичности.
3. Наименьшие потери полезного ископаемого.
- Требования безопасности в России - безусловны!
- Экономичность достигается минимальными затратами живого и овеществленного труда, энергии и материалов на I т ПИ. Минимальные затраты трудам возможны при высокой производительности, которая обеспечивается комплексной механизацией производственных процессов, НОТ и рациональными конструктивными элементами систем разработки. Высокая производительность труда - важнейшее условие экономичности системы, т.к. зарплата составляет более 50% издержек производства.
- Потери ПИ экономически обосновываются в совокупности с другими технико-экономическими показателями. У нас большие запасы, но мы должны думать и о сохранении запасов для будущих поколений, т.к. потребление растет. Забота государства: об охране природы.
Система разработки должна обеспечивать условия для комплексной механизации производственных процессов и концентрации производства путем:
- исключения взаимного влияния очистных и подготовительных работ;
- обеспечения автономности работы очистного забоя по условиям транспорта и проветривания;
- создания условий для высокой надежности работы комплексов и агрегатов;
- исключения влияния на работу лав газовыделения из забоев» выработок;
- прогнозирования геологических нарушений с целью исключения непредвиденных остановок лав.
Факторы влияющие на выбор систем разработки.
Форма месторождения и наличие геологических нарушений - частые изменения элементов залегания пластов и геологические нарушения усложняют разработку месторождения.
Мощность пластов - подрывка пород при проведении выработок по тонким пластам и средней мощности.
- пласты m < 3,5 отрабатываются на полную мощность, а m >3,5 м с разделением на слои.
Угол падения - различное транспортирование угля вдоль очистного забоя:
- на крутых пластах в движение приходит не только кровля, но и почва;
- движение вентиляционной струи только вверх на газовых шахтах с a > 10° (§ 186 ПБ).
Строение пластов - крепкие прослойки, включения колчедана исключают применение комбайнов;
- На мощных пластах прослойки иногда используют в качестве границ между сдоями.
Крепость и особенно вязкость угля - существенно влияют на выбор средств механизации очистной выемки.
- влияют на размеры предохранительных целиков возле подготовительных выработок, т.е. на элементы системы разработки.
Кливаж - (более легкое отделение угля от массива) - влияние на производительность труда и устойчивость кровли.
Свойства боковых пород - влияют на:
- выбор способа управления кровлей;
- расположение выработок по пласту или породе. Взаимное расположение пластов в свите - подработка, надработка, т.е. соблюдение очередности выемки пластов.
Газоносность месторождения - проветривание, чем больше газа, тем больше нужно воздуха...» а это лимитирует сечение; выработок, длину лавы (V = 4 м/с - § 147 ПБ) содержание метана в исходящей струе лавы не выше 1% (§ 183).
- в газовых шахтах системы разработки с минимумом глухих забоев и восстающих.
- На пластах с высокой газообильностью - обособленное проветривание забоев, а это дополнительные выработки. Самовозгорание угля
- Минимум потерь (полная закладка и полевые выработки)
- Большая скорость подвигания забоя
- Выемка запасов угля отдельными участками и их изоляция. Обводненность месторождения - вода в очистных забоях снижает производительность» поэтому предварительное осушение.
Механизация производственных процессов - с появлением средств механизации выемки и транспорта угля на пологих пластах стало возможным увеличить длину лавы.
- На крутых пластах забои не уступные, а прямолинейные, т.е. более простые варианты системы разработки.
Факторов много. Каждый изучается отдельно, а учитываются они совместно.
15.3. Классификация систем разработки.
Большое разнообразие геологических условий и видов технологии выемки ПИ в очистных забоях обусловило многообразие систем разработки, что вызывает необходимость в их классификации.
В качестве классификационного выбрано одно характерное отличие, которое выделяет любую систему из группы других - очередность ведения подготовительных, нарезных и очистных работ. На основании этого отличия системы подразделяются на группы:
- сплошная, столбовая и комбинированная системы при длинных очистных забоях;
- камерная и камерно-столбовая системы при коротких забоях.
При столбовых системах разработки подготовительные и нарезные выработки проводятся до начала очистных работ и полностью оконтуривают запасы ПИ в пределах выемочного столба или яруса, т.е. при столбовой системе проведение подготовительных и очистных работ разделены в пространстве,
При сплошных системах проведение подготовительных выработок и очистная выемка угля в пределах выемочного поля, яруса, слоя производятся одновременно. Предварительное оконтури-вание запасов отсутствует.
При комбинированных системах для отработки столбов в выемочном поде или ярусов в панели применяют одновременно или последовательно сплошную и столбовую системы разработки» При этом одну часть поля отрабатывают независимо от другой.
Это основное классификационное отличие дополняется рядом признаков, которые характеризуют не столько систему, сколько ее варианты.
1-й признак - технология выемки. По этому признаку системы делят на 2 группы:
1-е длинными забоями (лавами и полосами)
2-е короткими забоями (камерами). Системы I группы (с длинными забоями) делятся (по m ) :
а) Системы разработки пластов на полную мощность.
б) Системы разработки с разделением на слои. П-й признак - общее направление выемки угля по отношению к элементам залегания пласта. Здесь различают системы разработки с выемкой угля по простиранию; по восстанию; по падению;
вкрест простирания.
III признак - технологическая схема подготовки этажа или яруса. Схемы эти могут быть различными. Например:
- с разделением и без разделения этажа на подэтажи;
- с пластовой или полевой (как индивидуальной, так и групповой) подготовкой этажа иди яруса;
- с доставкой ПИ на задний или передний бремсберг или квершлаг.
Основного отличия и трех признаков, рассматриваемых совместно, достаточно для полной характеристики системы разработки.
В целом классификация систем разработки пластовых месторождений выглядит так:
А. Системы разработки длинными забоями без разделения
пласта на слои.
I. Сплошные системы разработки.
1. Сплошные системы разработки с выемкой по простиранию.
а) без разделения этажа на подэтажи (лава-этаж);
б) с разделением этажа на подэтажи.
2. Сплошные системы разработки с выемкой по падению.
3. Сплошные системы разработки с выемкой по восстанию.
II. Столбовые системы разработки (длинными столбами)
1. Столбовые системы разработки длинными столбами по простиранию.
а) без разделения этажа на подэтажи (лава-этаж);
б) с разделением этажа на подэтажи.
2. Столбовые системы разработки длинными столбами по падению.
3. Столбовые системы разработки длинными столбами по восстанию.
4. Столбовые системы разработки длинными столбами весьма
пологих пластов,
Ш. Комбинированные системы разработки.
1. Система разработки парными штреками.
2. Прочие.
IV. Системы разработки с применением щитовой крепи.
V. Прочие системы разработки.
Б. Системы разработки короткими очистными забоями.
1. Камерные системы разработки.
2. Камерно-столбовые системы разработки.
3. Системы разработки короткими столбами.
4. Прочие системы разработки короткими столбами.
В. Системы разработки с делением пласта на слои»
1. Системы разработки наклонными слоями.
2. Системы разработки горизонтальными слоями.
3. Системы разработки с принудительным обрушением и выпуском угля.
Для конкретных условий выбирается одна наиболее прогрессивная и эффективная система.
Распределение добычи по системам разработки (в %%) сведено в таблицу:
Бассейны | Система разработки с длинными очистными забоями | Системы разработки с короткими забоями | ||||
Без разделения на слои | С делением пласта на наклонные в т.ч. с гибкими перекрытиями | Прочие (комбинированные, горизонтальными слоями) | ||||
Сплошная | Столбовая | В т.ч. столбовая с применением щитов | ||||
1 | 2 | 3 | 4 | 5 | 6 | 7 |
Донецкий | 27,2 | 50,3 | - | - | 22,5 | - |
Подмосковный | - | 100,0 | - | - | - | - |
Кузнецкий | 0,5 | 79,6 | 12,4 | 5,5 | 11,7 | 2,7 |
Печорский | 3,5 | 89,0 | - | 6,5 | 1,0 | - |
Карагандинский | 1,5 | 61,3 | - | 37,2 | - | - |
По СНГ | 14,5 | 63,5 | 2,2 | 7,4 | 13,8 | 0,8 |
Выбор системы может производиться методом отбора по принципу соответствия горно-геологическим условиям, а выбор варианта системы - методом экономических расчетов,
16. Сплошные системы разработки.
Эта система разработки до недавнего времени считалась основной при разработке тонких слоев, пластов. Но в силу присущих ей крупных недостатков (отсутствие предварительной доразведки месторождения, большие затраты на ремонт выработок, трудности в организации транспорта, вызванные одновременным ведением очистных и подготовительных работ) удельный вес этих систем в общей добыче угля снижается. Они вытесняются прогрессивными столбовыми системами.
В перспективе применение сплошных систем разработки будет оправдано при отработке пластов большой метаноносности; опасных по внезапным выбросам угля и газа и по горным ударам; тонких пластов, залегающих среди устойчивых боковых пород;
ПОДЗЕМНАЯ РАЗРАБОТКА РУДНЫХ МЕСТОРОЖДЕНИЙ
1. Основные особенности разработки рудных месторождений.
1.1 Характеристика рудных месторождений.
Руда - природное минеральное вещество, из которого в данных условиях и при данном уровне развития техники и экономики целесообразно извлекать полезные компоненты. В отличие от многих ПИ руду после извлечения надо переработать, чтобы получить ценные компоненты.
Пустая порода - тоже природное минеральное вещество, но не содержит ПИ или содержит так; мало. что извлекать не экономично. Разделение минерального вещества на руду и пустую породу относительно.
Минимальное промышленное содержащий полезных компонентов -ниже которого разработка месторождения экономически не выгодна' (в данный момент).
Металлы (полезные компоненты) находятся в руде в виде химических соединений - рудных минералов. Кроме рудных минералов, в руде всегда имеются сопутствующие минералы, не представляющие в данный момент промышленной ценности. Эти минералы называются рудной породой.
В зависимости от содержания полезных компонентов руды делятся:
- металлические (содержащие металлы);
- неметаллические (апатит, фосфорит и т.д.);
- комплексные.
По числу содержащихся полезных компонентов руды делятся на:
- простые (один полезный компонент)
- сложные (несколько полезных компонентов;
- полиметаллические (содержащие несколько металлов),
свинцово-цинковые. По ценности руды делятся на:
1 - богатые
2 - средней ценности
3 - бедные
Рудная масса - смесь руды и пустой породы. Горная масса " вся выдаваемая на поверхность масса руды и пустой породы из очистных и подготовительных забоев.
По характеру распределения полезного компонента руды делятся на сплошные и вкрапленные.
По степени устойчивости руды и вмещающие породы подразделяются (по Л.Д.Шевякову и М.И.Агошкову):
- очень неустойчивые - не допускающие обнажения и требующие опережающей крепи;
- неустойчивые - допускающие небольшое обнажение, но требующие поддержания. вслед за выемкой;
- средней устойчивости- - допускающие обнажение кровли и позволяющие работать с незакрепленной кровлей на площади 4 - 10 м2 при длительном обнажении требуют поддержания;
- устойчивые - допускающие значительное обнажение площадью порядка 100 - 200 м2 и требующие поддержания только в отдельных местах;
- очень устойчивые - допускающие большие обнажения: на длительное время (иногда десятки лет), не требующие крепи. По строению руды делятся:
- массивные; (плотные без трещин, включений и слоистости);
- трещиноватые;
- слоистые;
- рыхлые.
По объемному весу руды; делятся:
- тяжелые, g = 3,5 тс/м3 ;
- средние, g = 2,5 - 3,5 тс/м3 ;
- легкие, g < 2,5 тс/м3.
На разработку рудных месторождений существенное влияние оказывают и такие свойства руды: слеживаемость, окисляемость, самовозгораемость, влагоемкость.
Влажность руды способствует слеживаемости, смерзанию.
В отличие от угольных, рудные месторождения характеризуются многообразием форм залегания:
- пластовые и пластообразные;
- жильные и массивные.
Пластовые - джезказганское медное, Никополь-Марганцевое, Чиатурское
Пластообразные - Криворожский железо-рудный бассейн. Жильные - мощность от 10-20 см до 2-5 м меняется даже в пределах одного рудного тела, так же как - золотые рудники Магадана, Якутии; оловянные рудники Приморья; полиметаллические рудники Северного Кавказа, Забайкалья.
Массивные - m>5 м, форма правильных линз или столбов, но сложной и неправильной формы. К ним относятся некоторые железорудные месторождения Криворожья» Урала и горной Шории, меднорудные Урала, полиметаллические Алтая.
Вскрытие и подготовка рудных месторождений.
Как и угольные месторождения, рудные имеют 3 стадии разработки - вскрытие, подготовку и очистную выемку.
Вскрытые запасы руды - находятся выше горизонта подсечки их вскрывающими выработками.
Подготовленные запасы - на участке месторождения пройдены все подготовительные выработки, предусмотренные проектом принятой системы разработки.
Готовые запасы - запасы участка, в которых пройдены; все нарезные выработки, необходимые для очистных работ.
Шахтные поля разбиваются на этажи или панели. Этажи на -блоки.. Длина шахтного поля - I - 2 км.
1.2.3. Вскрытие рудных месторождений.
Основные положения вскрытия пластовых месторождений относятся и к рудным. Рудные месторождения вскрываются главными и вспомогательными выработками.
Гласные вскрываемые выработки - вертикальные и наклонные стволы и штольни.
Bспомогательные выработки - шахтные стволы и штольни (проветривание и второй запасной выход), квершлаги, слепые стволы, уклоны, капитальные восстающие. При больших глубинах слепые стволы, выполняющие основные функции, относятся к главным.
По типу главных вскрывающих выработок cnособы вскрытия делятся на простые и комбинированные - сочетание простых методов вскрытия.
На выбор вскрытия влияют горно-геологические и горнотехнические факторы (мощность рудника, размеры ш.п., срок службы, уровень развития техники).
I .2.4. Подготовка рудных месторождений.
Требования к подготовке. Обеспечить:
1. Безопасность ведения подготовительных и очистных работ.
2. Своевременную подготовку запасов п.и.
3. Минимум потерь при сохранности выработок на период выемки.
4. Минимум затрат на проведении и поддержание.
5. Попутную доразведку и дренаж (при больш. СО ).
6. Безопасность передвижения людей, руды, материалов. При этажной и панельной подготовке рудных месторождений
подготовительные выработки - это главные, этажные, откаточные и
вентиляционные штреки, восстающие, орты и т.д.
Восстающие - это вертикальные или наклонные выработки, пройденные с иткаточного на вентиляционный горизонт для разделения этажа на блоки. Они служат для спуска, руды, вентиляции, передвижения людей, доставки закладочного материала и т.д. 2 типа восстающих:
- пройденные в массиве руды или пустой породы до начала очистных работ;
- наращиваемые по мере подвигания вверх очистного забоя.
По назначению восстающие делятся на рудоспуски и ходки. Восстающие примыкают, как правило, не к почве и кровле штреков, а к стенкам.
Выработки (штреки или орты) служат для доставки руды до выработок откаточного горизонта или рудоспусков, выходящих на основной горизонт, а также для вторичного дробления руды.
Выработки горизонта грохочения (камеры, штреки, орты) служат для вторичного дробления крупных кусков руды и перепуска всей руды на основной горизонт . Горизонт грохочения располагают на 5-15 м выше: откаточного горизонта и соединяют с ним и с очистным пространством рудоспусками (дучками).
I.3. Основные производственные показатели при отработке рудных месторождений.
Основные производственные процессы: отбойка руды, вторичное дробление, доставка руды к откаточным выработкам, управление горным давлением.
1.3.2. Вторичное дробление руды.
При отбойке руды скважинами - выход негабаритов. Приходится дробить руду либо в забое, либо в специальных выработках - горизонта скреперования или грохочения. Сравнительно небольшие куски дробят вручную, крупные - накладными зарядами, очень крупные - с помощью "забурок" l = 20-30см. Это существенно снижает производительность труда. Стремятся свести к минимуму эту операцию в забое - увеличивают люки, руду транспортируют в вагонетках емкостью 4м и выше и куски 700х700 мм транспортируют к стволу, где устанавливают дробилки с приемным отверстием 1000х1200 мм.
1.3.3. Доставка
Различают два случая доставки:
1 - руда не требует вторичного дробления.
2 - руда требует вторичного дробления. м I - руда по выработанному пространству скатывается к днищу блока и через рудоспуски, оборудованные люками и затворами, грузится в вагонетки. Рудоспуски с люками проходятся через 4-6 м один от другого. Иногда рудоспуски устраиваются через 20-30 м, а руду к ним доставляют вдоль блока скреперными лебедками.
2 – при необходимости дробления руды создается сложная сеть выработок для доставки руды: скреперные штреки или орты, камеры грохочения или выработки для выпуска руды на почву откаточного штрека и последующей погрузки ее в вагонетки машинами.
5, б - квершлаги и штреки откаточного горизонта
7 - восстающие.
В крепких рудах скреперные штреки не крепят. Места сопряжений скреперного штрека с дучками наиболее опасны. Их крепят двутавровыми или швеллерными балками № 25-27.
При выпуске руды из дучек иногда: зависание: руды:. Приходится взрывать ВВ, привязанные на шесты.
Дробление руды в скреперном штреке доставка скрепером к рудоспуску, где устанавливается грохот из рельс, чтобы не попали большие куски в вагонетку и предохранить скрепериста от падения в люк.
I .3.4 Управление горным давлением.
Осуществляется способами обрушения пород или поддержанием выработанного пространства. Обрушение вмещающих пород:
- обрушение кровли вслед за очистной выемкой с сохранением открытого призабойного пространства;
- обрушение руды и вмещающих пород и заполнение выработанного пространства породой одновременно с' выпуском руды.
Поддержание выработанного пространства осуществляется оставлением рудных или породных целиков, магазинированием руды, креплением, закладкой пустой породой.
2. Системы разработки рудных месторождений.
2.1. Классификация систем разработки.
При РРМ применяется более 200 вариантов систем разработки из-за, разнообразия горно--геологических условий. Предложено около 20 классификаций. Наибольшее распространение подучила классификация проф.М.И.Агошкова, в основе которой - способ управления кровлей. По этой классификации все система разделены на. 8 классов:
I класс - системы разработки с открытым очистным пространством
II класс - системы разработки с магзинированием руды в очистном пространстве;
III класс - системы разработки с закладкой очистного пространства;
IV класс - системы, разработки с креплением очистного пространства;
V класс - системы разработки с креплением и закладкой очистного пространства;
VI класс - системы разработки с обрушением вмещающих пород;
VII класс - системы разработки с обрушением руды и вмещаю щих пород;
VIII класс - комбинированные системы разработки.
В классах системы разделяются на группы:
I, III, V, VI кл. - по направлению очистной выемки и форме забоя.
II кл. - по способам отбойки руды в очистном забое. IV кл. - по конструкции крепи. VII кл. - по способу обрушения руды. VIII кл. - по способу выемки камер.
Системы разработки с открытым очистным пространством.( I класс )
Открытым очистным пространством считается пространство, которое в процессе выемки руды не заполнено закладкой, часто устанавливаемой крепью или временно оставляемой рудой и в котором люди свободно могут передвигаться при отбойке и уборке руды.
Поддержание вмещающих пород целиками. Системы этого класса применяются для разработки залежей с крепкими (устойчивыми) рудами и породами.
РАЗРАБОТКА МЕСТОРОЖДЕНИЙ О TKP ЫТЫ M СПОСОБОМ.
I. Общие сведения о PMOС. Достоинства и недостатки.
При РМОС полезные ископаемые добывают непосредственно с земной поверхности. Удаляют покрывающую толщу пород и приступают к разработке месторождения.
Карьер (разрез) - совокупность горных выработок, служащих для разработки месторождения открытым способом, или - это горное предприятие, на котором осуществляют разработку месторождения открытым способом.
Карьерное поле - часть месторождения, разрабатываемая одним карьером. Границы карьерного поля (карьера) - это поверхности, проходящие через верхний и нижний контуры карьера.
При открытой разработке вынимают горизонтальные слои сверху вниз. Карьер приобретает уступную форму. Уступ - горизонтальный слой толщи пород или ПИ, разрабатываемый самостоятельными средствами отбойки, погрузки и транспорт А.
1-нижняя площадка уступа,
2-верхняя площадка уступа.
Рабочая площадка - где размещают оборудование.
Не рабочая площадка - свободна, У - откос-наклонная поверхность, ограничивающая уступ со стороны выработанного пространства. Угол наклона уступа к горизонтальной плоскости называется углом - откоса (w).
5 - нижняя бровка Линия пересечения откоса уступа с его
3 - верхняя бровка площадкой.
6 - забой - это торец или откос уступа, является объектом горных работ.
7 - борт карьера - это комплекс площадок и откосов уступов от поверхности земли до подошвы, карьера.
8 - откос борта - линия (поверхность), соединяющая верхний и нижний контуры карьера.
Уступ разрабатывается последовательными параллельными полосами - заходками. Часть заходки по длине, разрабатываемую самостоятельными средствами отбойки и погрузки, называют блоком»
Траншея - открытая горная выработка, имеющая значительную длину по сравнению с шириной и глубиной. Сечение трапециевидное, имеет борта и почву.
Капитальная траншея - наклонная траншея, с помощью которой земная поверхность связывается с уступами карьера.
Разрезная траншея - это горизонтальная траншея, предназначенная для создания первоначального фронта работ на уступе.
Основные преимущества открытого способа разработки.
1. Выше производительность труда, чем на шахтах. На шахтах 55т/мес, на карьерах 450 т/мес. на рабочего по добыче.
2. Себестоимость I т угля ниже, чем при подземном способе. Объясняется высокой производительностью труда на базе совершенной комплексной механизации.
3. Капитальные затраты на. строительство карьера в 1,5-2,5 раза меньше, чем шахты той же производительности. Меньше и сроки строительства, быстрее освоение проектной мощности, потери в 3 раза меньше, чем в шахте.
4. Расход леса 0,5 м /1000т, против 20-25м /1000т в шахтах,
5. Условия труда более гигиеничны и безопасны.
Недостатки:
1. Зависимость от климатических условий.
2. Под карьерами и отвалами пустых пород пропадают большие площади земли (с/х), которые пропадают навечно. Но ... ведется работа по рекультивации с/х земель. Область применения и удельный объем добычи угля открытым способом возрастет к 199 г до 46% от общей добычи.
Основные бассейны с открытой добычей угля: Экибастуз -180млн.т/год, Канско-Ачинский-200млн.т/год, Южно-Якутский -
130 млн.т/год, Кузбасс и т.д.
Этапы открытой разработки.
- подготовка поверхности;
- осушение месторождения и ограждение его от стока поверхностных вод;
- вскрытие месторождения;
- вскрышные и добычные работы;
- восстановление поверхности (рекультивация).
2.I. Подготовка поверхности - удаление искусственных и естественных препятствий, мешающих разработке; вырубить лес, отвести поверхностные воды и осушить водоемы, снести здания и сооружения на площади карьера, подготовить место для отвалов пустой породы, подвести дороги, построить производственные, служебные и жилые помещения, обеспечить карьер электроэнергией и т.д.
2.2. Осушение месторождения - необходимо для придания большей устойчивости откосам уступа и предотвращения оползней; для создания благоприятных условий для работы машин' и транспорта;
для создания безопасных условий труда.
2 вида осушения - предварительное и текущее.
Предварительное - до начала разработки. Осуществляется поверхностным и подземным способами. Поверхностный - каналы по контуру карьера - водосборник - сток или откачка. Применяется когда водоносный горизонт близко к поверхности.
Подземный способ осушения - сеть дренажных штреков по пласту или породе, или сеть скважин-фильтров.
Кроме канав к дренажных штреков применяют забивные и сквозные фильтры, водопонижающие скважины, оборудованные насосами.
2.3. Вскрытие месторождений - при помощи капитальных траншей (открывающих доступ от поверхности земли к ПИ) и разрезных траншей (подготавливающих карьерное поле к разработке). Капитальные траншеи могут быть: внутренние, внешние. На выбор способа вскрытия влияют следующие факторы:
- условия залегания ПИ (Н, т, a);
- рельеф местности;
- размеры и формы карьера;
- степень обводнения;
- условия привязки карьера к внешней сети железных дорог и магистралей и т.д.
Вскрытие может быть проведено отдельными, групповыми и общими капитальными траншеями. В особых случаях производят вскрытие подземными выработками: штольнями, наклонными и вертикальными стволами.
Вскрытие каждого уступа отдельной траншеей (внутренней или внешней) применяют при разработке неглубоких месторождений с горизонтальным или пологим залеганием пластов. При числе уступов не более 3-х - внешние траншеи; при большем числе уступов - внутренние.
Вскрытие групповыми траншеями - на группу из 2-3 уступов (при общем числе уступов 4-6) проводят одну внешнюю или внутреннюю траншею. Одна групповая траншея вскрывает породные уступы, другая - добычные. Этот способ применяют при разработке горизонтальных и пологих пластов большой мощности, залегающих на. большой глубине.
Вскрытие общими траншеями - применяют при разработке глубоких карьеров или месторождений, расположенных на косогорах. Все уступы карьера: вскрывают одной общей траншеей.
2.4. Вскрышные и добычные работы.
Существует 2. основных способа открытой разработки: экскаваторный и гидравлический. Экскаваторный - универсален. Гидравлический - при породах, поддающихся размыву и транспортированию водой. Оба эти способа предусматривают вскрышные и добычные работы.
2.4.1. Вскрышные работы - удаление пустых пород, доступ к полезному ископаемому от разрезной траншеи. Объем вскрышных работ зависит от глубины залегания.
Для оценки целесообразности открытой и подземной разработки существует понятие промышленного коэффициента вскрыши. Затраты на добычу I т угля открытым и подземным способами становятся одинаковыми.
Сп - пл.себе стоимость 1т ПИ, добываемого подземным способом
Со - пл.себестоимость 1т ПИ, добываемого открытым способом без вскрыши, руб.
3 - затраты на удаление 1м вскрышных работ, руб.
Коэффициент этот условный, т.к. показатели затрат меняются с развитием техники.
В этом случае переходят на подземный способ добычи, т.е. граница открытых работ.
Добычные работы. - работы по извлечению ПИ после проведения по ПИ разрезной траншеи.
Вскрышные и добычные работы включают следующие процессы:
- подготовка горных пород к выемке;
- выемочно-погрузочные работы;
- перемещение горной массы из забоев на поверхность;
- отвальные работы для вскрышных пород;
- складские работы для полезного ископаемого. Подготовка пород к выемке, т.е. отделение части вскрышных пород или ПИ от массива производится БВР или непосредственно экскаваторами (водой). Бурение станками, _ скв.=150-200 или 100-120мм, ВВ - аммонит.
Погрузка пород и ПИ - экскаваторами (мехлопата, драглайн). Рыхлые и мягкие породы вынимаются и грузятся экскаваторами. Экскаваторы - одноковшовые, роторные и многочерпаковые.
Транспорт на карьерах - важнейший технологический процесс, т.к. перемещается много горной массы.
В России применяется железнодорожный, автомобильный, конвейерный и гидравлический транспорт.
Порода в отвалы - бестранспортное перемещение или любым транспортом.
Уголь транспортируется на ОФ или потребителям.
Пустая порода, в отвалы - внутренние (пологое падение) и внешние (крутое падение).
Во внешние отвалы порода перемещается ж.д. и автотранспортом. Во внутренние отвалы - непосредственно экскаватором ЭШ 25/100, IOO/IOO с длиной стрелы до 100м и емкостью ковша 25м и более.
Для передвижки путей - путевые краны, путепередвигатели.
Автотранспорт - грузоподъемность 5-40т до 100 т.
2.4.3. Системы PMОC и их элементы.
Под системой открытой разработки угольных месторождений понимают установленный технологический порядок и взаимосвязь подготовительных, проходческих, вскрышных и добычных работ на уступах.
Система разработки считается эффективной, если она обеспечивает плановую производственную мощность карьера, минимальные потери ПИ, низкую себестоимость, высокую производительность оборудования и безопасные условия труда.
По классификации проф.Е.Ф.Шешко различают следующий системы разработки:
1- с поперечным перемещением вскрышных пород во внутренние отвалы
2- с продольным (вдоль фронта уступа) перемещением вскрышных пород во внутренние или внешние отвалы 3 - комбинированные, объединяющие в пределах одного карьера
особенности систем I и 2 класса
I. Системы разработки с поперечным перемещением, вскрышных
Пород во внутренние отвалы.
Наиболее просты и экономичны. Но могут применяться при соответствующем оборудовании (драглайны до 100м, мех.лопаты -65м, транспортно-отвальные мосты в сочетании с многочерпаковыми экскаваторами).
Применяются эти системы при разработке горизонтальных и пологих залежей. Разновидности: 1-е непосредственной перевалкой вскрыши, 2-е кратной экскаваторной перевалкой, 3-е забойным отвалообразователем, 4-с незначительным объемом вскрышных работ.
2. Системы с продольным перемещением вскрышных пород во внутренние и внешние отвалы.
Системы с перевозкой породы во внешние отвалы более сложны и менее экономичны. Но здесь транспорт осуществляется вдоль уступа: и не ограничивает размеры карьера. Эти системы широко применяются, а для разработки наклонных и крутых залежей является единственно возможным.
3. Комбинированные системы.
Основные параметры системы:
- высота уступа: по породе; 10-15 м и более, по углю - 3 м
- ширина заходки (уступа) - равна радиусу черпания экскаватора или зависит от угла поворота стрелы драглайна -15-20 м, А = 1,5Rr.
- длина блока - это часть заходки 300-600м. В каждом блоке свои механизмы - буровые, экскаваторы.
- ширина рабочей площадки - 40-45 м - в скальных породах при автотранспортном и конвейерном, а в слабых породах и при железнодорожном транспорте - 60-80-100м.
Углы откосов: 30-70° - уступов, 7-55° - бортов карьера.
ОБОГАЩЕНИЕ УГЛЯ
Общие сведения
Большая часть добываемых каменных и бурых углей, а также антрацитов не может быть эффективно использована в народном хозяйстве без предварительного их обогащения. Обогащение углей имеет большое народнохозяйственное значение.
Под обогащением понимают совокупность процессов первичной обработки углей или других полезных ископаемых, имеющих целью отделение всех полезных минералов от породы, т.е. от всех входящих в состав полезного ископаемого минералов, которые в настоящее время не представляют непосредственной практической ценности. При обогащении углей не происходит изменения состава минералов, а только механическое их разделение.
Обогащение угля осуществляется, как правило, на обогатительных фабриках, которые делятся на индивидуальные (ОФ), групповые (ГОФ) и центральные (ЦОФ).
Индивидуальные фабрики размещают на промплощадке шахты, на них обогащают уголь только этой шахты. Групповые обогатительные фабрики обогащают уголь нескольких шахт. По производительности они обычно больше индивидуальных и имеют специальные устройства для приемки привозных углей.
Продукты и показатели обогащения
В результате обогащения чаще всего получают два конечных продукта: концентрат, который состоит в основном из полезных компонентов, и хвосты — отходы обогащения, в которые переходит большая часть породы и вредных примесей. В хвостах иногда содержится значительное количество полезных компонентов. В таких случаях хвосты подвергают дополнительному обогащению.
Количество полученного концентрата характеризуется его выходом, т. е. отношением массы концентрата к массе исходной продукции, выраженным в процентах. В связи с тем, что влажность продуктов, в особенности при мокром обогащении, может быть различной и существенно отличаться от влажности исходного материала, выход относят обычно к абсолютно сухому углю.
Вся товарная продукция угольной промышленности, отгружаемая различным потребителям, должна удовлетворять определенным требованиям, которые устанавливают для каждой шахты или углеобогатительной фабрики.
Основные операции обработки углей при обогащении
Операции механической обработки угля на обогатительной фабрике могут быть разделены на три группы: подготовительные, собственно обогатительные и вспомогательные.
К первой группе операций относят дробление и грохочение. Дробление углей производят для различных целей, в том числе и для разъединения сростков углей и породы, т. е. для лучшей подготовки углей к непосредственному обогащению. Грохочение имеет целью разделение углей на различные сорта по крупности, Эту операцию широко применяют как на углеобогатительных фабриках, так и на сортировках.
Ко второй группе операций (собственно обогатительных) относят: а) простейшие методы обогащения (ручную сортировку, обогащение по трению, обогащение по крупности); б) гравитационные методы обогащения; в) флотацию; г) пневматическое обогащение.
Ручная сортировка является наиболее простым - способом обогащения углей. При этом способе куски породы или колчедана отделяют от угля вручную, основываясь на различии внешних признаков угля и вредных примесей.
Обогащение по трению основано на разнице в форме кусков угля и породы и величине их коэффициентов трения. Так, куски каменного угля или антрацита имеют более округлую форму, чем плоские куски сланца. Двигаясь по наклонной плоскости желоба, округлые куски угля перекатываются, опережая плоские куски сланца. На этом принципе основана работа различных сепараторов трения: неподвижных, барабанных, ленточных и спиральных.
Гравитационные методы обогащения
Данные методы обогащения являются преобладающими на всех действующих в СНГ угольных обогатительных фабриках. Они основаны на разнице плотностей и скоростей движения кусков угля и породы в разных средах. Различают мокрые и сухие процессы обогащения. Первые проводят преимущественно в водной среде, они включают такие процессы, как отсадка, концентрация на столах, обогащение на шлюзах, моечных желобах, в тяжелых жидкостях (суспензиях), а также в гидроциклонах.
Сухие процессы гравитационных методов обогащения проводят в воздушной среде в пневматических отсадочных машинах, в сухих лотках, на пневматических концентрационных столах.
При гравитационном обогащении в тяжелых средах разделение происходит не только по плотности, но и по крупности.
В водной среде обогащаемый материал может подвергаться воздействию: непрерывно восходящей струи; прерывно восходящей струи; струи, текущей по неподвижному наклонному желобу;
струн, текущей по качающейся поверхности; вращающейся струи.
В воздушной среде обогащаемый материал может подвергаться воздействию: непрерывно восходящей струи; прерывно восходящей струи,
В тяжелых средах обогащение может производиться: в неподвижной среде; в восходящем потоке; в комбинированном горизонтальном и вертикальном потоках; в горизонтальном потоке;
во вращающемся потоке.
При обогащении угля в тяжелых средах пользуются двумя тяжелыми жидкостями (минеральными суспензиями) плотностью 1,4—1,5 и 1,8—2. В первой жидкости всплывшая часть представляет собой наиболее чистый уголь — концентрат. Во второй жидкости порода тонет, а уголь с включениями примесей всплывает. Всплывающую часть называют промпродуктом.
Минеральные суспензии представляют собой механические смеси воды с тонкоизмельченными минералами, имеющими большую плотность (магнетит, барит и др.). В настоящее время гравитационное обогащение применяют как отдельно, так и в комбинации с другими методами,
Флотация углей
Флотационное обогащение основано на избирательном прилипании минеральных частиц, взвешенных в воде, к поверхности пузырьков воздуха. Этот способ применяют для обогащения угольной мелочи и пыли крупностью от 1 мм и ниже.
Через пульпу, состоящую из угля н воды, пропускают пузырьки воздуха. Вследствие плохой смачиваемости частицы угля прилипают к пузырькам воздуха и поднимаются вместе с ними на поверхность пульпы, образуя на ней слой минерализованной пены. Частицы вредных минералов, хорошо смачиваемых водой, не прилипают к пузырькам воздуха, а остаются в пульпе.
Для повышения эффективности флотации к пульпе добавляют ^различные вещества, называемые флотационными реагентами. Таких веществ в настоящее время известно довольно много. Часто в качестве реагента используют сульфидированный керосин, обладающий собирательными и вспенивающими свойствами.
Иногда отходы производственных предприятий являются хорошими реагентами. Например, продукты Лисичанского химкомбината, содержащие высшие жирные спирты, используют при флотации в качестве хороших пенообразователей.
Флотацию осуществляют в специальных аппаратах — флотационных машинах, которые в зависимости от способа перемешивания пульпы разделяют на механические, пневматические и механопневматнческие.
Пневматическое обогащение
В районах с холодным климатом обогащение в водной среде затруднено из-за замерзания воды, а в засушливых районах — из-за отсутствия ее. В этих случаях применяют пневматическое обогащение. В связи с тем, что воздух оказывает значительно меньшее по сравнению с водой сопротивление падающим частицам угля. при этом способе обогащения используют восходящую струю воздуха. Процесс обогащения в пневматических машинах сходен с процессом обогащения в гидравлических машинах.
Машины для пневматического обогащения разделяют на две основные группы: отсадочные машины с неподвижным или подвижным решетом и пульсирующей воздушной струёй и сепараторы с подвижной декой и пульсирующей или движущейся с постоянной скоростью струёй воздуха.
Вспомогательные процессы
К третьей группе операций (вспомогательных) относят обеспыливание, обезвоживание, сушку и осветление воды.
Обеспыливание применяют при гравитационных методах обогащения. Его осуществляют при помощи струи воздуха, циркулирующей в аппаратах для обеспыливания. При этом пыль не только не поддается обогащению, но и накапливается в моечных водах, загрязняет их и мешает обогащению основных классов.
В результате мокрых процессов обогащения получают концентраты со значительным содержанием воды, которые оказываются непригодными для дальнейшей переработки или непосредственного использования. В этом случае продукты обогащения подвергают обезвоживанию.
Обезвоживание крупнозернистого угля производится на неподвижных ситах, неподвижных грохотах, в обезвоживающих бункерах и центрифугах. Для обезвоживания тонкозернистых концентратов применяют сгущение, фильтрацию и сушку. Сгущение основано на естественном осаждении из пульпы твердых частиц под влиянием их силы тяжести.
кокс предназначен для литейного производства. Литейный кокс не должен содержать серы более 1,2—1,3%.
В настоящее время для выплавки 1 т чугуна требуется 400— 600 кг кокса. Из 1 т угля получают 750—770 кг кокса. При коксовании кроме кокса получают газ, бензол, каменноугольный пек и др.
В результате комплексного использования продуктов переработки угля в кокс и газ возникло сложное коксохимическое производство.
Для получения кокса в первую очередь используют угли марки К (коксующиеся). Однако таких углей при разработке угольных месторождений получают в количестве, недостаточном для удовлетворения потребностей в коксе. В связи с этим для получения кокса приходится применять смесь из таких марок Г, ГЖ, Ж, КЖ, К, К2, ОС, в пропорции, которая дает возможность получить кокс нужного качества. В смесь углей, называемую шихтой, вводят не все перечисленные марки, а только те из них, которые можно экономически выгодно применять в данном районе.
Процесс коксования состоит из сложных физических, химических и физико-химических превращений, он осуществляется в коксовых печах и батареях с температурой нагрева до 1000 Со. Существует много конструкций коксовых печей и коксовых батарей. Печи соединяют в батареи. Стандартное число печей в батарее 65.
РЕКОМЕНДУЕМЫЙ СПИСОК ЛИТЕРАТУРЫ
Основная
Основная
1. Пучков Л.А.. Жежелевский Ю.А. Подземная разработка месторождений полезных ископаемых. Учебник. М. 2007.
2. Михеев М.Л.Подземная разработка пластовых месторождений. Теоретические и методические основы проведения практических занятий /Михеев О.В., Виткалов В.Г., Козовой Г.И. и др./ Учебное пособие. М., МГГУ, 2001.
3. Егоров П.В.Основы горного дела. / Егоров П.В., Бобер Е.А., Кузнецов Ю.Н. и др.// М., МГГУ, 2000 .
4. Васильев А.В., Зубов В.П.Сиренко Ю.Г.. Моделирование на ЭВМ стоимостных показателей горных работ в шахтах. Методические указания к расчетно-графическим работам для студентов горно-геологических специальностей. РИЦ Национального минерально-сырьевого университета «Горный”,2012 г.
Дополнительная
1. Килячков А.П. Технология горного производства. М., Недра, 1992.
2. Черняк И.Л., Ярунин С.А., Бурчаков Ю.И. Технология и механизация подземной добычи угля. М., Недра, 1981.
3. Бурчаков А.С., Гринько Н.К., Черняк И.Л. Процессы подземных горных работ. М., Недра, 1982
4. Задачник по подземной разработке угольных месторождений. Авт. Сапицкий К.Ф., Дорохов Д.В., Зборщик М.П., Андрушко В.Ф. М., Недра, 1981.
5. Васильев А.В., Сиренко Ю.Г. Моделирование на ЭВМ основных параметров шахты. / Санкт-Петербургский горный институт, СПБ, 1995.
6. Правила безопасности в угольных шахтах. М.: Недра, 1995.
Дата добавления: 2022-01-22; просмотров: 159; Мы поможем в написании вашей работы! |
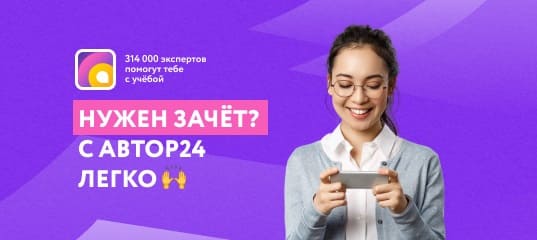
Мы поможем в написании ваших работ!