Показатели ремонтопригодности.
Понятия надёжности.
Надежность – это свойство объекта сохранять во времени в установленных пределах все параметры, обеспечивающие выполнение требуемых функций в заданных условиях эксплуатации.
Уровень надежности в значительной степени определяет развитие техники по основным направлениям: автоматизации производства, интенсификации рабочих процессов и транспорта, экономии материалов и энергии.
Современные технические средства очень разнообразны и состоят из большого количества взаимодействующих механизмов, аппаратов и приборов. Первые простейшие машины и радиоприемники состояли из десятков или сотен деталей, а к примеру, система радиоуправления ракетами состоит из десятков и сотен миллионов различных деталей. В таких сложных системах в случае отсутствия резервирования отказ всего одного ответственного элемента может привести к отказу или сбою в работе всей системы.
Низкий уровень надежности оборудования вполне может приводить к серьезным затратам на ремонт, длительному простою оборудования, к авариям и т.п.
Основные термины и определения.
Термины и определения надежности в технике регламентированы ГОСТ 27.002, а для автомобильного подвижного состава, его агрегатов, систем, механизмов, узлов и деталей — ОСТ 37.001.055.
Под надежностью автомобиля понимается его свойство сохранять во времени или в течение некоторой наработки в установленных пределах значения всех параметров, характеризующих способность выполнять требуемые функции в заданных режимах и условиях применения, технического обслуживания, ремонтов, хранения и транспортирования.
|
|
Параметры изделия, определяющие его эксплуатационные показатели и допускаемые пределы их изменений, указываются в технической документации (государственных и отраслевых стандартах, технических условиях, руководящих технических материалах, нормативных документах по технической эксплуатации, требованиях ГАИ и др.).
Надежность в зависимости от назначения автомобиля и условий его эксплуатации включает следующие свойства: безотказность, долговечность, ремонтопригодность и сохраняемость.
Безотказность — свойство автомобиля непрерывно сохранять работоспособное состояние в течение некоторого времени или некоторой наработки. Безотказностью автомобиль должен обладать как в период его эксплуатации, так и в периоды хранения и транспортирования.
Признаком нарушения работоспособности автомобиля является необходимость проведения работ по текущему ремонту, в то время как проведенш технического обслуживания не является признаком нарушения его работо способности.
|
|
Долговечность — это свойство автомобиля сохранять работоспособное состояние до наступления пре дельного состояния при установленно системе технического обслуживания ремонта. Долговечность изделий, являющихся составными частями боле» сложных, может характеризовать без отказность последних. Например, долговечность ремня привода вентилятор; может характеризовать безотказност двигателя.
Ремонтопригодность за ключается в приспособленности авто мобиля к предупреждению и обнаружению причин возникновения отказа, повреждений и поддержанию и восстановлению работоспособного состояни путем проведения технического обслуживания и ремонтов. Значения показа телей ремонтопригодности должны за даваться в технической документаци для регламентированных условий тех нического обслуживания и ремонта.
Сохраняемость — это свои ство автомобиля сохранять значени показателей безотказности, долговечности и ремонтопригодности в течени и после хранения и (или) транспортирования.
Для конкретных объектов автомобильного подвижного состава, его агрегатов, систем, механизмов, узлов и деталей эти свойства могут иметь paзличную относительную значимость. Например, безотказность магистральных автомобилей, удаляющихся на большое расстояние и длительное время от базы, должна быть больше, чем автомобилей-самосвалов, ежедневно возвращающихся из рейсов на свою базу. Для легковых автомобилей, особенно используемых личными владельцами, наиболее ценным качеством является ремонтопригодность.
|
|
Автомобиль, находящийся в эксплуатации, при исправном состоянии должен соответствовать всем требованиям нормативно-технической и конструкторской документации. Это понятие шире понятия «работоспособное состояние». Работоспособный автомобиль в отличие отисправного удовлетворяет лишь тем требованиям нормативной документации, которые обеспечивают его нормальное функционирование при выполнении заданных функций, т. е. осуществлении автоперевозок. При этом он может не удовлетворять, например, требованиям, относящимся к его внешнему виду (нарушение декоративного покрытия, вмятины на кузовных деталях и др.).
Неработоспособным считается такое состояние автомобиля, при котором значение хотя бы одного параметра, характеризующего его способность выполнять заданные функции, не соответствует требованиям нормативно-технической и конструкторской документации.
|
|
Следует различать два вида неработоспособности: устранимую и неустранимую. В первом случае работоспособность объекта может быть восстановлена при выполнении ремонтных работ, во втором — восстановление работоспособности технически невозможно (предельное состояние объекта) или экономически невыгодно, в связи с чем дальнейшее применение такого объекта по назначению недопустимо или нецелесообразно.
Таким образом, переход в предельное состояние определяется наступлением момента, когда дальнейшая эксплуатация автомобиля невозможна или нецелесообразна по одной или нескольким из следующих причин: становится невозможным поддержание безопасности, безотказности или эффективности объекта на допустимом уровне во время эксплуатации; в результате изнашивания и (или) старения объект пришел в такое состояние, при котором ремонт требует больших затрат или не обеспечивает необходимый уровень восстановления работоспособности.
Автомобиль относится к таким изделиям, которые не сохраняют работоспособное состояние до наступления предельного, т. е. его безотказность меньше наработки, соответствующей долговечности.
Отказ — событие, заключающееся в нарушении работоспособного состояния объекта. Следует различать отказ и повреждение. Последнее заключается в нарушении исправного состояния объекта при сохранении работоспособного.
Переход объекта из одного состояния в другое обычно происходит вследствие повреждения или отказа.
При нарушении его работоспособного состояния различают отказ автомобиля в целом и отказ агрегата, узла, детали и др.
Отказ автомобиля обусловливает вынужденный его простой на линии во время, запланированное для транспортной работы, или невыезд в очередной плановый рейс в связи с неисправностями.
Дефекты, устраняемые в процессе проведения очередного планового технического обслуживания или ремонта, которые выполняются в междусменное время, рекомендуется считать отказами не автомобиля, а соответствующих агрегатов, узлов, деталей. Отказы, происшедшие из-за неправильной эксплуатации, при оценке безотказности.
Различают также отказы автомобиля, устраняемые водителем с помощью имеющегося при автомобиле инструмента и запасных деталей, и требующие вызова технической помощи или буксировки автомобиля на базу. Отказы и неисправности, возникающие в процессе эксплуатации автомобиля, по виду, характеру, причинам возникновения, трудоемкости и стоимости устранения значительно разнятся между собой. Без анализа отказов, изучения их физической сущности, частоты повторяемости, трудоемкости устранения, влияния на продолжительность простоя в ремонте и изменения технического состояния автомобиля невозможно обеспечить эксплуатационную надежность автомобилей.
При проведении анализа отказов необходимо учитывать все факторы, приводящие к нарушению работоспособности автомобиля. Прежде всего следует определить место отказа или неисправности (агрегат, узел, деталь), для указания которого пользуются нумерацией и наименованиями, принятыми в системе обозначений автомобильного подвижного состава.
Отказы и неисправности разных видов имеют различные формы проявления. Для описания внешнего проявления или характера неисправности применяются такие понятия, как биение, вибрация (карданного вала); затруднено, невозможно включение или самопроизвольное выключение (передач); ослабление крепления соединения (деталей); перегрев, выкипание (радиатора); течь (сальниковых уплотнений); замыкание, обрыв цепи, перегорание, пробой, разрегулировка (для деталей электрооборудования) и т. п. Все причины отказов и неисправностей могут быть отнесены к одной из следующих трех основных групп: конструкционного характера, производственно-технологического, эксплуатационного.
Типичными ошибками конструирования являются: недостаточная защищенность узлов трения; наличие концентратов напряжений; неверное представление о характере распределения напряжений; неправильный расчет несущей способности; неадекватность расчетной модели; неправильный выбор материалов и др.
Наиболее типичные дефекты, возникающие по причинам производственного и технологического характера: отклонение размеров деталей от чертежа; неоднородность состава материала (наличия включений, охрупчивающих примесей и др.); дефекты, возникающие при плавке и изготовлении заготовок (пористость, усадочные раковины, расслоения); дефекты вследствие недостаточной точности механической обработки деталей (ожоги, задиры, заусенцы, прорезы); дефекты сварки (трещины, остаточные напряжения, углубления, непровар); дефекты структуры материала вследствие нарушения режимов термообработки (перегрев, закалочные трещины, обезуглероживание и т. п.); дефекты, возникающие при обработке поверхностей (водородное охрупчивание); недостаточная точность сборки (повреждения поверхностей, задиры, неправильная установка деталей, неправильная регулировка).
Дефекты производственно-технологического характера являются наиболее распространенными, их число в значительной степени зависит от точности выполнения технологического процесса, организации производства, состояния производственной дисциплины и эффективности контроля.
Основными причинами отказов и повреждений эксплуатационного характера являются: нарушение правил эксплуатации автомобилей (например, в дорожных условиях, для которых они не приспособлены; работа с прицепом, хотя конструкцией это не предусмотрено; переоборудование без разрешения завода- изготовителя);
перегрузки и непредвиденные нагрузки (нарушение инструкции по эксплуатации в части загрузки автомобиля, неправильные действия водителя — броски сцепления, переезд препятствий на большой скорости и др.); неправильное техническое обслуживание (нарушение периодичности и технологии ТО, повреждение изделия или неправильная его установка при ТО и ТР, и др.).
Отказы автомобилей подразделяются на частичные и полные, характеризующие частичную или полную утрату автомобилем работоспособности.
Кчастичным отказам, снижающим эксплуатационные качества автомобиля, относятся отказы, ухудшающие такие показатели, как время подготовки к движению из-за необходимости проведения незапланированных крепежных или регулировочных работ, устранения течи топлива, смазочного материала; снижающие среднюю скорость движения и грузоподъемность автомобиля, но допускающие его использование в течение некоторого времени.
К полным отказам, лишающим автомобиль подвижности, относятся отказы, без устранения которых движение автомобиля невозможно (например, поломка карданного вала)
или недопустимо (например, разрушение питающей магистрали пневмопривода тормозов).
При этом следует различать полные отказы, для устранения которых автомобиль должен быть доставлен на станцию технического обслуживания или в автотранспортное предприятие (так называемые отказы дорожные), и отказы (так называемые отказы линейные), устранение которых может быть осуществлено на линии, т. е. непосредственно на месте, где произошел отказ.
Показатели надежности
Общие положения.
Надежность автомобиля зависит от множества факторов, характеризующих качество его проектирования, изготовления, организацию технической эксплуатации, а также условия эксплуатации. Поэтому надежность автомобилей даже одной и той же модели различна.
Характеристики надежности автомобилей, их деталей, узлов и агрегатов имеют вероятностный характер. Поэтому ее можно характеризовать только путем обработки большого числа данных, полученных при его эксплуатации или испытаниях, с помощью методов теории вероятностей и математической статистики.
Как известно из теории вероятностей, явления, которые при неоднократном воспроизведении одного и того же опыта протекают каждый раз несколько по-иному, называются случайными.
Отказы деталей автомобилей, происходящие во время испытаний или при их эксплуатации, относят к случайным, поскольку возникновение их в каждом отдельном случае предсказать невозможно.
Вероятность события принято выражать положительным числом (от нуля до единицы).
Показатели надежности оцениваются теоретическими уравнениями или статистическими методами, приемлемыми для практических целей.
Поскольку все нормативы для автомобилей устанавливаются на километр пробега, характеристику его надежности принято рассматривать как функцию пробега.
Показатели безотказности. Одним из важнейших показателей безотказности является вероятность безотказной работы, т. е. вероятность того, что в пределах заданной наработки отказ объекта (автомобиля, узла, агрегата, детали) не возникнет.
Степень рассеивания оценивается при помощи безразмерной характеристики, называемой коэффициентом вариации и определяемой как отношение среднего квадратического отклонения случайной величины к средней наработке.
В качестве показателя безотказности используется также гаммапроцентная наработка до отказа, т. е. наработка, в течение которой отказ объекта не возникнет с вероятностью у» выраженной в процентах.
К показателям безотказности относятся также интенсивность отказов и параметр потока отказов.
Интенсивность отказов — условная плотность вероятности возникновения отказа невосстанавливаемого объекта, определяемая для рассматриваемого момента времени как отношение плотности распределения наработки до отказа к вероятности безотказной работы при условии, что до этого момента отказ не возник:
При оценке безотказности восстанавливаемых изделий используют среднюю наработку на отказ, которая определяется отношением суммарной наработки восстанавливаемых объектов к математическому ожиданию числа их отказов в течение этой наработки:
Параметр потока отказов — отношение среднего числа отказов восстанавливаемого объекта за произвольно малую его наработку к значению этой наработки. Его используют в качестве показателя безотказности восстанавливаемых объектов, эксплуатация которых может быть описана следующим образом: с момента начала эксплуатации объект работает до отказа, после чего восстанавливается его работоспособность и объект вновь работает до отказа и т. д. (в расчете время восстановления не учитывается).
Большинство узлов, агрегатов и автомобилей в целом относятся к восстанавливаемым объектам. Их отказы устраняют текущим ремонтом. Временная потеря работоспособности при отказе не означает израсходование ресурса, пока изделие не достигло предельного состояния. Для восстанавливаемых изделий распределения отказов и ресурсов не совпадают. Уровень безотказности таких изделий характеризуется кривой изменения параметра потока отказов от начала эксплуатации до капитального ремонта и списания. Кривая изменения параметра потока отказов характеризует непредсказуемые отказы, вызванные перегрузками, дефектами изготовления, а также старением материала элементов конструкции. Начальное возрастание параметра потока отказов (на участке а) отражает отказы, обусловленные преимущественно нарушениями технологических процессов, браком при изготовлении деталей и сборке узлов и автомобиля в целом, которые приводят к преждевременным отказам, потере работоспособности автомобиля. Хотя обычно этот период непродолжительный, не выходящий за пределы гарантийной наработки, он должен быть по возможности сведен к минимальному.
Участок кривой b соответствует периоду нормальной эксплуатации. В этот период, наиболее длительный, возникает сравнительно небольшое число отказов, которые не связаны с разрушением деталей вследствие их недостаточной прочности или низкой износостойкости, а также производственными недостатками.
За пределами участка кривой b с увеличением наработки автомобиля (участок k) постепенно возрастает число отказов, возникающих в результате изнашивания, усталостных разрушений и старения материала деталей. В идеальном случае участок k желательно получать пологим, т. е. таким, чтобы на последнем участке наработки К до капитального ремонта не было резкого увеличения частоты отказов, т. е. чтобы повышение интенсивности отказов в последнем периоде было медленным. Наработка соответствует пробегу автомобиля после капитального ремонта, т. е. до его списания.
Показатели долговечности. К основным показателям долговечности автомобиля относятся средний ресурс, представляющий собой математическое ожидание ресурса, и г а ммпроцентный ресурс, определяемый как наработка, в течение которой объект не достигнет предельного состояния с заданной вероятностью V, выраженной в процентах. В нормативных конструкторских документах, как правило, указывается 90%-ный ресурс, а для систем, узлов и деталей, влияющих на безопасность движения,— 95%-ный.
Показатели долговечности автомобиля связываются с видом действий после наступления предельного состояния объекта. Если после наступления предельного состояния необходимо проведение капитального ремонта, указывают средний или ^-процентный ресурс до капитального ремонта. Гамма-процентный ресурс может быть определен графически по кривой убыли (вероятности безотказной работы).
Наиболее часто оценка долговечности автомобиля производится по средним показателям надежности (для определения объема производства запасных деталей; планирования ремонтов; пополнения парка автомобилей; расчетов, связанных с оценкой технико-экономической эффективности работ по повышению долговечности, и др.). Однако оценка долговечности автомобиля по средним показателям может быть достаточно полной только при условии, что при этом учитывается рассеивание его среднего ресурса, определяемое причинами как производственного, так и эксплуатационного характера. К первым относятся, например, неоднородность свойств материалов в состоянии поставки и после термической обработки. Свойства деталей зависят и от степени отлаженное технологического процесса. Даже при соблюдении технологической дисциплины неизбежны различия в размерах, форме деталей одного наименования. Рассеивание свойств изделий тем меньше, чем выше стабильность процессов производства, обеспечивающая однородность качества деталей.
Вызывают рассеивание показателей надежности также различная интенсивность и условия эксплуатации, качество технического обслуживания и ремонтов, внешние воздействия, определяющие процессы накопления повреждений в элементах деталей автомобилей.
Технико-экономические критерии предельного состояния автомобильного подвижного состава для оценки его ресурса по результатам испытаний разработаны Центральным научно- исследовательским автомобильным полигоном НАМИ и Центральным научно-исследовательским автомобильным и автомоторным институтом (НАМИ). Предельное состояние автомобиля, автобуса или прицепа наступает: при достижении предельного состояния рамы грузовых автомобилей, прицепов и полуприцепов или кузова легковых автомобилей и автобусов, определяемого техническими критериями, приведенными в табл. 2.1; расходе запасных частей на текущий ремонт более 10 % (при испытании на автополигоне) и 25 % (в условиях эксплуатации) от оптовой стоимости нового автомобиля без учета стоимости израсходованных шин, аккумуляторных батарей, радиоприемника и дополнительного снаряжения, автоламп, электропроводки.
Предельное состояние основных агрегатов определяется необходимостью полной разборки и ремонта базовых и основных деталей при устранении неисправностей, или по нормативным диагностическим параметрам агрегатов автомобилей.
Показатели ремонтопригодности.
Предельный износ посадочных поверхностей и отверстий под: вкладыши коренных подшипников, втулки распределительного вала, борты гильз цилиндров, "толкатели клапанов; трещины перемычек гильз, рубашек системы охлаждения, фланцев крепления агрегатов; коробление привалочных поверхностей Предельный износ или задиры коренных и (или) шатунных шеек; трещины, излом, изгиб, коробление Предельный износ посадочных поверхностей под подшипники, посадочных буртов; трещины усталости, изломы фланцев крепления, коробление привалочных плоскостей; повышенный шум, превышающий допустимые нормы Предельный износ шлицевых соединений, отверстий под стаканы подшипников; трещины усталости; коробление, изгиб, вызывающие неустранимый дисбаланс
Предельный износ посадочных мест под втулки шкворней, подшипники поворотных кулаков; коробление, прогиб балки или поперечины; изломы, трещины усталости Трещины и прогибы балки; предельный износ и разрушение шестерен, подшипников, валов; повышенный шум Предельный износ посадочных поверхностей под втулки (подшипники), рабочей поверхности; трещины усталости, излом фланцев крепления; предельный люфт механизма, неустранимый регулировкой
Разрушения, исключающие эксплуатацию автомобиля и требующие для ремонта демонтажа основных агрегатов с заменой лонжеронов или поперечин Усталостный излом одного и более силовых элементов, стоек дверных проемов по всему периметру; сквозная коррозия основания коробов
Примечание. Приведены лишь типичные неисправности, поэтому в отдельных случаях предельное состояние детали определяется невозможностью выполнять функции в пределах заданных характеристик.
Поскольку ремонтопригодность зависит прежде всего от периодичноститехнического обслуживания и трудоемкости проведения его и текущего ремонта, эти показатели нормируются ГОСТ 21624, устанавливающим требования к эксплуатационной технологичности и ремонтопригодности автомобилей.
К показателям ремонтопригодности относят периодичность технических обслуживании, удельную оперативную трудоемкость технического обслуживания, текущих ремонтов. Эти показатели определяют степень приспособленности конструкции автомобиля, агрегата или узла к выполнению с наименьшей трудоемкостью необходимых операций по предупреждению (техническое обслуживание) и устранению (ремонт) неисправностей и отказов.
Периодичность технического обслуживания является одним из важнейших показателей, определяющих совершенство конструкции автомобиля и соответствие ее требованиям эксплуатационной технологичности. За последние годы периодичность технических обслуживаний отечественных большегрузных автомобилей возросла в среднем в 1,5 раза. Так, у автомобилей МАЗ-500А периодичность ТО-1 составляла 2500 км, ТО-2 — 12 500 км, а для MA3-5335 увеличена соответственно до 5000 км и 20 000 км. Чтобы создавать автомобили с еще более высокой периодичностью технического обслуживания, необходимо расширить производство новых износостойких материалов, применение усовершенствованных конструктивных решений уплотнений узлов, самоконтрящихся резьбовых соединений, самосмазывающихся деталей, а также высококачественных смазочных материалов.
Удельной оперативной трудоемкостью технического обслуживания и удельной трудоемкостью текущего ремонта устанавливаются дозатраты на выполнение всех операций технического обслуживания автомобиля (без ежедневного обслуживания) , определяемые его конструкцией и состоянием. Эти показатели указываются в человеко-часах на 1000 км пробега (чел.ч/тыс. км). Разовая оперативная трудоемкость для ежедневного технического обслуживания указывается в человеко-часах. Значения нормируемых показателей трудоемкости технического обслуживания и текущего ремонта в зависимости от класса и вида автомобиля приводятся в ГОСТ 21624. Так, например, для легковых автомобилей с рабочим объемом двигателя 1,2...1,8 л удельная оперативная трудоемкость технического обслуживания должна быть не более 8 чел.-ч/тыс. км, а текущего ремонта — не более 2,3 чел.-ч/тыс. км.
Внимание конструкторов должно быть сосредоточено прежде всего на тех работах по техническому обслуживанию и ремонту, которые являются наиболее трудоемкими. Так, в общем объеме работ по техническому обслуживанию грузовых автомобилей удельный вес смазочных работ составляет 20.. .30 %, крепежных — около 20, контрольных — 25, электротехнических — 15 %• Поэтому снижение трудоемкости этих работ является наиболее актуальной задачей.
Точное обоснование периодичности и объема работ по проведению технического обслуживания автомобилей для различных условий эксплуатации весьма сложно, поэтому в нормативной документации такие рекомендации указываются по статистическим результатам исследований. В связи С этим значения, приведенные в нормативной документации по периодичности и объему воздействий, могут обусловить выявление значительных резервов для снижения их трудоемкости, если имеется возможность своевременно проверять действительную необходимость таких работ.
Указанным целям служит диагностирование: общее и поэлементное. При общем диагностировании выявляется техническое состояние систем, обеспечивающих безопасность движения и пригодность автомобиля к эксплуатации. При поэлементном, или
углубленном, диагностировании определяется техническое состояние всех агрегатов и систем автомобиля и уточняется перечень и объем работ по его техническому обслуживанию и ремонту. Поэтому к конструкции автомобиля предъявляется еще одно важное требование — приспособленность к проведению диагностических работ. Должны быть предусмотрены определенные места для подключения датчиков (в топливной магистрали, системе охлаждения, в пневматической системе тормозного привода и т. п.). Общее число диагностических параметров и объектов, требующих подключения приборов и проведения измерений, на автомобилях МАЗ, например, составляет 55...65.
Приспособленность автомобиля к проведению диагностирования способствует уменьшению потребности в квалифицированных механиках-контролерах примерно на 30 % при одновременном повышении эффективности и точности проверок. Стоимость работ по проверке основных систем автомобиля в сравнении с обычными методами снижается на 70...75 %, почти в 2 раза уменьшается число выполняемых операций.
Наконец, важное значение имеет и компоновка автомобиля. Так, например, при одинаковой конструкции двигателя компоновка автомобиля по схеме «кабина над двигателем» способствует снижению трудоемкости технического обслуживания двигателя примерно на 25 %.
Значения трудоемкости технических обслуживаний и текущих ремонтов не должны превышать требуемых государственными стандартами.
В конечном итоге критерием для комплексной оценки надежности автомобилей является не наработка на отказ и не вероятность безотказной работы, а трудоемкость их технического обслуживания и ремонта.
Дата добавления: 2022-01-22; просмотров: 57; Мы поможем в написании вашей работы! |
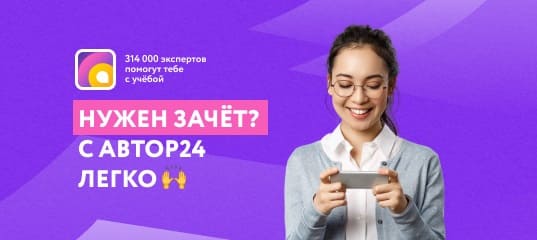
Мы поможем в написании ваших работ!