КЛАССИФИКАЦИЯ СОЕДИНЕНИЙ ДЕТАЛЕЙ
Тема 1.2. Технологические процессы сборки автотракторной техники
Основные понятия технологических процессов. Технологическая организация процессов сборки.
В структуре технологических процессов производства изделий
машиностроения наибольший удельный вес занимают обработка
металлов резанием и сборка. Трудоемкость узловой и общей сборки
составляет в среднем около 30% всей трудоемкости изготовления
машин. В массовом и крупносерийном производствах эта доля
меньше, а в единичном и мелкосерийном, где выполняется боль
шой объем пригоночных работ, трудоемкость сборки нередко до
стигает 40% .
Необходимо отметить еще один вид сборочных работ, широко
применяемый в народном хозяйстве, — разборку и сборку машин
и механизмов при их ремонте в эксплуатационных условиях.
Ремонт машины не может быть произведен без частичной или пол
ной ее разборки. Так как после разборки и исправления де
фектов или замены износившихся деталей следует сборка машины,
и это повторяется в течение всего срока службы машины несколько
раз, то трудоемкость ремонтных работ в народном хозяйстве очень
большая. При капитальном ремонте трактора, например, трудо
емкость нередко превышает затраты труда на его изготовление.
При этом до 70% трудоемкости составляют разборочные и сбороч
ные работы. Нетрудно представить, какой это огромный расход
|
|
трудовых ресурсов, если учесть, что количество работников,
ежегодно занятых на ремонте парка тракторов, превышает чис
ленность рабочих тракторных заводов.
процесса. Технологический процесс сборки — это совокупность
операций по соединению деталей в определенной технически и эко
номически целесообразной последовательности для получения сбо
рочных единиц и изделий, полностью отвечающих установленным
■для них требованиям. Если при механической и большинстве
других видов обработки понятие «технологический процесс» от
носится к детали, то в сборочном производстве оно имеет отно
шение прежде всего к соединению двух или большего числа де
талей.
процесса. Технологический процесс сборки — это совокупность
операций по соединению деталей в определенной технически и эко
номически целесообразной последовательности для получения сбо
рочных единиц и изделий, полностью отвечающих установленным
■для них требованиям. Если при механической и большинстве
других видов обработки понятие «технологический процесс» от
носится к детали, то в сборочном производстве оно имеет отно
шение прежде всего к соединению двух или большего числа де
|
|
талей.
Объектами основного производства в машиностроении - из
делиями являются машины, механизмы и установки, их агрегаты
или детали. Структура изделии машиностроения (ГОСТ 2.101—68)
приведена в табл. 3.
Таблица 3
Вид
Определение
Изделие основного проиЗ'
водства
Сборочная единица
Деталь
Предмет производства, подлежащий изготовлению
на предприятии и предназначенный для поставки
(реализации)
Изделие, составные части которого подлежат соеди
нению между собой на предприятии — изготовителе
сборочными операциями (свинчиванием, сочлене
нием, клепкой, сваркой, пайкой, опрессовкой,
развальцовкой, склеиванием и т. п.)
Изделие, изготовленноэ из однородного по наиме
нованию и марке материала, без применения сбо
рочных операций
В качестве примера на рис. 1 показаны двигатель, являю
щийся изделием основного производства, и его составные части:
сборочные единицы и механизмы.
В дополнение к этим стандартным составным частям изделия
на многих машиностроительных заводах широко используют тер
мины: группа и подгруппа. Группа — сборочная единица, для ко
торой целесообразна самостоятельная организация производства.
В группу могут входить детали, другие группы и покупные из
|
|
делия. Группа, в свою очередь, может входить в другую группу или
непосредственно в изделие. Подгруппа — составная часть группы.
Если она входит непосредственно в группу, ее условно называют
подгруппой первого порядка. Если она входит в подгруппу пер
вого порядка, то ее именуют подгруппой второго порядка. Соот
ветственно могут быть подгруппы третьего и большего порядков.
Следовательно, порядок входящей подгруппы на единицу
больше базовой. Таким образом, группа или подгруппа состоит
из отдельных деталей, или из деталей и подгрупп соответствую
щих порядков.
Сборку любой машины нельзя осуществлять в произвольной
последовательности. В равной степени это относится также и к
сборке отдельных механизмов и даже к большинству простейших
соединений. Последовательность сборки определяется прежде
всего конструкцией собираемого изделия или его составных ча
стей, а также степенью требуемого разделения сборочных работ.
Установленная последовательность ввода деталей и групп в тех
нологический процесс сборки изделия характеризует систему его
комплектования.
Последовательность комплектования может быть одновариант
|
|
ной для простых сборочных единиц и многовариантной для ком
плексных групп и изделий. Примерами одновариантной последо
вательности комплектования могут быть сборочные единицы, при
веденные на рис. 2.£BJiepBOM случае (рис. 2, а) в гнездо устанав
ливается шарикоподшипник, а затем стопорное кольцо; во втором
(рис J2, б) шарикоподшипник устанавливается на валик и стопорит
ся кольцом; в третьем (рис. 2, в) — после напрессовки шарико- подшипника на шлицах валика устанавливают шестерню. Другие
последовательности комплектования здесь невозможны.
Однако в сложных сборочных единицах и изделиях, когда в
комплектовании участвуют десятки и сотни деталей, возможен
ряд вариантов последовательности сборки. При большом числе
деталей в изделии таких вариантов может быть очень много. Кон
струкции машин все более усложняются, и количество деталей
и их соединений неуклонно растет. Например, в тракторе ДТ-54А
насчитывается 1600 деталей, а в современном тракторе Т-150К их
уже 3600. Еще недавно турбины собирались из 15—18 тыс. дета
лей, а сейчас паровая турбина мощностью 300 МВт имеет их 60
тысяч. В этом случае возникает задача применения оптимального
варианта, обеспечивающего наилучшее выполнение установленных
технических требований и высокое качество, к объекту сборки при
минимальных затратах труда и средств.
При разработке технологического процесса сборки изделие,
исходя из условий его конструкции, расчленяют на части так,
чтобы осуществить сборку наибольшего количества сборочных
-единиц независимо друг от друга. В связи с этим в машине или
механизме различают конструктивные и сборочные элементы. Ус
ловное выделение первых может быть произведено на основе их
назначения в изделии; например, механизмы привода и регули
рования в станке, механизмы газораспределения в двигателях,
-механизмы управления и пр. При выделении же сборочных эле
ментов обязательным условием является возможность осуществле
ния сборки каждого из них независимо от другого. Конструктив
ные элементы не всегда могут быть сборочными, и наоборот, хотя
такое совпадение встречается часто. В этих случаях элементы на
зываются конструктивно-сборочными.
Процесс комплектования сборочных элементов — сборочных
единиц, изделия для наглядности изображают в виде схем. Эту
схему следует строить так, чтобы соответствующие сборочные еди
ницы — группы, подгруппы и детали были представлены в порядке
их введения в технологический процесс сборки. Так как процесс
сборки начинается с введения в него основной, или, как ее обычно
называют, базовой детали или подгруппы, то, очевидно, и схема
должна начинаться с условного изображения этих составных ча
стей изделия. Детали, подгруппы и группы изображают на схеме
в виде небольших прямоугольников, в которые вписывают индекс,
номера и количества соответствующих частей. Общая схема ком
плектования изделия представлена на рис. 3, a [42].
Для машины с большим количеством деталей и сборочных еди
ниц развернутая схема может быть громоздкой и потому неудоб
ной для пользования. В таких случаях в производстве применяют
укрупненные схемы (рис. 3, б), на которые наносят только услов
ные обозначения групп, а также деталей, не входящих в группы
и подгруппы. Укрупненные схемы могут быть разработаны и
для комплексных групп.
КЛАССИФИКАЦИЯ СОЕДИНЕНИЙ ДЕТАЛЕЙ
В изделиях машиностроения имеется большое количество раз
нообразных соединений деталей. В машинах примерно 35—40%
соединений типа цилиндрический вал — втулка, 15—20% пло
скостных, 15—25% резьбовых, 6—7% конических, 2—3% сфери
ческих и др. Все эти соединения характеризуются различными кон
структивными, технологическими и экономическими факторами:
степенью относительной подвижности, возможностью разборки,
технологичностью в сборке и демонтаже, видом контакта сопря
гающихся поверхностей деталей, прочностью, химической стой
костью, затратами труда и средств на сборку и т. д.
По конструкции и условиям эксплуатации соединения деталей
могут быть разделены на подвижные и неподвижные. Детали под
вижных соединений обладают возможностью относительного пе
ремещения в рабочем состоянии по некоторым траекториям, оп
ределяемым кинематической схемой механизма, звеньями которого
эти детали являются. Детали неподвижных соединений в рабочем
состоянии перемещаться не могут.
Подвижные и неподвижные соединения в зависимости от воз
можности их демонтажа подразделяются на разъемные (свободно
разбираемые) и неразъемные (неразбираемые). Количество разъ
емных соединений в современных машинах и механизмах состав
ляет от 65 до 85% всех соединений. При этом под разъемными
(демонтируемыми) соединениями подразумеваются лишь те, ко
торые могут быть полностью разобраны без повреждения соеди
няющих и скрепляющих их деталей. Остальные соединения отно
сятся к группе неразъемных, хотя в условиях эксплуатации и ре
монта машин нередко подвергается разборке некоторая часть и
этих соединений; однако процесс разборки в этом случае значитель
но усложняется, и часто одна или обе соединяемые детали после
разборки оказываются непригодными к последующей сборке или
же требуют специальных пригонок.
Таким образом, соединения могут быть неподвижные разъем
ные (например, резьбовые, пазовые и конические); неподвижные
неразъемные (например, соединения запрессовкой или разваль
цовкой, а также заклепочные); подвижные разъемные (например,
валы — подшипники скольжения, плунжеры—втулки, зубья ко
лес, каретки—станины); подвижные неразъемные (некоторые
подшипники качения, запорные клапаны).
Такая классификация соединений проста по своей схеме, но
имеет недостаток, так как в каждую группу указанной классифи
кации входит большое количество соединений, различных по своей
технологической характеристике и способу сборки.
В отдельных исследованиях по классификации соединений пред
лагается учитывать характер деформаций (упругие, пластические),
молекулярные силы (сцепление, адгезию), форму соединяемых деталей (геометрическое замыкание), силы, возникающие при сборке
соединения (способ силового замыкания).
Некоторые исследователи подразделяют все соединения дета
лей машин на пять классов: механические, сварные и паяные,
клеевые, магнитные и комбинированные, или на соединения:
резьбовые, паяные, сварные, армированные и получаемые давле
нием. Недостатком этих классификаций является то, что в них
не отражается степень подвижности деталей собранного сое
динения, а также возможность его демонтажа, что важно для
повторных сборок в условиях эксплуатации машин и меха
низмов.
Предлагается еще один принцип классификации соединений —
по виду контакта сопрягающихся поверхностей деталей, так как
качество, долговечность, износостойкость в конечном счете за
висят от правильности контактирования деталей, соединяемых
в процессе сборки. Этот контакт может быть непосредственным
(в подшипниковых сборочных единицах, зубчатых передачах, резь
бовых соединениях и пр.) или через промежуточный слой материала
(при сварке, пайке, склеивании). При этом в зависимости от формы
сопрягаемых поверхностей возможен общий, местный, литейный
или точечный контакт деталей. Ниже приведена схема классифи
кации соединений деталей по различным признакам (рис. 4).
Выбор наиболее экономичного вида соединения деталей — это
сфера конструирования машины. Если при этом технико-экономи
ческие показатели принимаемого соединения повышаются по
сравнению с ранее применявшимися соединениями, то задача
считается решенной.
Непременным условием улучшения технико-экономических по
казателей сборочного процесса, повышения его эффективности и
качества труда сборщиков является механизация операций, рост
уровня оснащенности труда сборщиков.
Научно-технический уровень сборочного производства оцени
вается тремя группами показателей, характеризующими техни
ческий уровень производства, уровень организации труда и уро
вень организации производства.
В отраслях машиностроения, где уровень механизации отно
сительно невысок, эффективен путь возможно более широкого
внедрения на всех этапах сборки таких механизированных средств,
как электропневмоинструмент, гидравлические ключи, перенос
ные установки с пневмогидроприводом и т. п. Внедрение их обычно
не требует большой перестройки процесса и поэтому осуществ
ляется в кратчайшие сроки. При этом опыт свидетельствует, что
механизация отдельных сборочных операций в конечном счете
малоэффективна. Частичное улучшение отдельных производствен
ных операций повышает производительность труда лишь на 5—6%
в год, тогда как внедрение комплексных технологических систем
дает возможность обеспечить рост производительности труда в
2—2,5 раза. Поэтому, чтобы заметно сократить трудоемкость, сни
зить общие затраты на сборку, нужно взять твердый курс на
разработку целостных систем. Наибольший эффект должна
дать интегральная, комплексная механизация по всему циклу
производства, учитывающая также транспортные и складские
работы.
Особого внимания заслуживают вспомогательные и транспорт
ные работы в сборочных цехах. Объем этих работ огромен, его
можно представить таким частным примером. Чтобы выполнить
сменную программу по сборке тракторных двигателей Д-240,
к сборочным постам надо подать 235 тыс. деталей и комплекту
ющих изделий. Трудоемкость вспомогательных работ при сборке
нередко превышает объем технологических. Поэтому для получе
ния необходимого эффекта в сборочных цехах обязательно следует
механизировать одновременно основные и вспомогательные ра
боты. Таким образом, остро встает необходимость внедрения кон
вейеров, в том числе с автоматическим адресованием, механизи
рованных стендов, подъемников, ультразвуковых промывочных
установок и другого оборудования .
Применение сборочных автоматов обеспечивает более высокий
уровень качества изделий.
В современном машиностроении неуклонно развивается про
цесс специализации, возрастает серийность выпускаемых изделий.
Концентрация производства однотипной конечной продукции соз
дает благоприятные условия для широкого применения новых,
более прогрессивных видов технологического оборудования.
В автоматической системе сборочных машин в настоящее
время есть отдельные операции, выполнять которые механизмами
пока оказывается сложно и дорого. Включение в этом случае в ав
томатизированную систему живого труда вполне допустимо. Но
нельзя забывать, что это остается вынужденным решением. Оно
ни в какой мере не снимает задачу последующего перехода к ком
плексной системе автоматических машин, где человек будет выпол
нять лишь функции наблюдения и управления.
Каждая деталь машины или механизма при работе занимает
в любой момент времени вполне определенные положения отно
сительно других деталей. Это условие обеспечивается соответ
ствующей кинематической схемой и конструкцией машины или
механизма, что в конечном счете выражается определенностью
базирования деталей, характеризуемой неизменным сохранением
соответствующего контакта сопряженных (соприкасающихся) по
верхностей.
Предусмотренное конструкцией положение любой детали в ма
шине или механизме обеспечивается при сборке благодаря соот
ветствующим ее поверхностям, осям или точкам. Поверхность или
выполняющее ту же функцию сочетание поверхностей, ось, точка,
принадлежащая заготовке или изделию и используемая для ба
зирования, согласно ГОСТ 21495—76 называется базой.
По своему назначению базы делятся на три вида: конструктор
ские, технологические и измерительные. На характер сборочных
соединений влияют конструкторские базы, которые бывают основ
ными и вспомогательными. Например, поверхности А корпуса
коробки скоростей и приводного вала
при соприкосновении с другими поверхностями (в данном случае
с поверхностями станины и подшипника) обеспечивают определен
ность положения корпуса и вала. Такие поверхности называются
основными базовыми. В отличие от них к вспомогательным базам относится сочетание поверхностей станины , на которые
опирается корпус коробки скоростей основными базами, и поверх
ность скольжения подшипника .
Поверхность Б отверстия шкива является базовой
для этой детали, а сопрягающаяся з ней поверхность вала в дан
ном случае выполняет роль вспомогательной базы. Следовательно,
при сборке соединений основные базы одной детали опираются
на вспомогательные базы другой. Основные и вспомогательные
базовые поверхности образуют в совокупности сопряжения, а при
достижении силового замыкания — соединения.
относится сочетание поверхностей станины , на которые
опирается корпус коробки скоростей основными базами, и поверх
ность скольжения подшипника .
Поверхность Б отверстия шкива является базовой
для этой детали, а сопрягающаяся з ней поверхность вала в дан
ном случае выполняет роль вспомогательной базы. Следовательно,
при сборке соединений основные базы одной детали опираются
на вспомогательные базы другой. Основные и вспомогательные
базовые поверхности образуют в совокупности сопряжения, а при
достижении силового замыкания — соединения.
Основные методы сборки. Сборочные размерные цепи. Техническая классификация методов сборки.
Осуществление основного назначения машины связано с пре
образованием движений, передачей сил и моментов. Силы и мо
менты, воздействуя на звенья механизма и их соединения, могут
изменять, искажать их форму, что вызывает отклонение от за
данного характера движения всего механизма и машины. Боль
шее или меньшее значение этих отклонений, характеризующее точ
ность машины, зависит от конструктивных, технологических и
эксплуатационных факторов. При этом одним из важнейших тех
нологических факторов являются погрешности, допущенные при
сборке механизмов, т. е. в процессе формирования их из отдель
ных деталей. Эти погрешности в различных сочетаниях в конеч
ном счете приводят к ошибкам результирующих характеристик
собираемого изделия.
Под точностью сборки подразумевается степень совпадения ма
териальных осей, контактирующихся поверхностей или иных
элементов сопрягающихся деталей с положением их условных
^прототипов, определяемым соответствующими размерами на чер
теже или техническими требованиями.
Одним из основных элементов обеспечения точности сборки является бази
рование. Для сохранения точности взаимного расположения элементов машин
необходимо достичь неизменности базирования или постоянства контакта сопря
гаемых поверхностей, что, конечно, должно обеспечиваться соответствующей
констоукцией деталей и их соединений.
Сопряжения деталей, образуемые в процессе сборки изделий,
в зависимости от количества степеней свободы, как уже отмеча
лось, будут обладать различными свойствами и могут быть непод
вижными или подвижными. От относительных размеров деталей,
образующих сопряжение, зависит степень его неподвижности или
подвижности. Эти степени характеризуются величиной натягов
или зазоров, выдерживаемых при сборке сопряжений, или, иначе,
величиной и знаком конструктивных и производственных отклоне
ний размеров сопрягаемых деталей.
Точность замыкающего звена размерной цепи обеспечивается
методами полной, неполной или групповой взаимозаменяемости,
пригонкой или регулировкой. Аналитическому рассмотрению этих
методов посвящены работы Б. С. Балакшина, Н. А. Бородачева,
П. Ф. Дунаева и др. Необходимо отметить, что использование раз
личных путей для достижения точности должно обосновываться
в каждом конкретном случае экономическими расчетами. В част
ности, для сборки в автоматизированном производстве большие
преимущества имеет метод полной взаимозаменяемости, однако
сфера применения этого метода серьезно ограничивается, так как
он достаточно экономичен, когда высокая точность достигается
посредством размерных цепей с небольшим числом звеньев, а
также при значительной программе производства. В ряде слу
чаев целесообразно применять метод групповой взаимозаменяемо
сти. При известных условиях, когда можно ограничиться минимальным числом групп, экономический эффект от использования
этого метода будет повышаться.
В практике построения технологических процессов сборки для
достижения требуемой точности сравнительно редко применяется
метод неполной взаимозаменяемости, однако экономичность этого
метода во многих случаях дает основание для его более широкого
использования.
Сборка, особенно автоматическая, при полной взаимозаменяемости — про
цесс наименее трудоемкий, но при этом 100% -ный контроль деталей требует значи
тельной доли затрат труда и средств. В случае неполной взаимозаменяемости
требования к точности снижаются, и контроль осуществляется с меньшими затра
тами, хотя трудоемкость самого процесса сборки увеличивается. Тем не^менее
метод неполной взаимозаменяемости_во многих случаях имеет большие экономи
ческие преимущества, особенно при^многозвенных размерных цепях.
Напомним в связи с этим, что средний допуск на изготовление деталей при
полной взаимозаменяемости δср= , где
где бзам — допуск замыкающего звена; т — общее число звеньев,
а при неполной взаимозаменяемости средний допуск
δ''ср= , где здесь t - процент риска; λср — среднее относительное среднеквадратичное отклонение
Так как знаменатель во второй формуле меньше, чем в первой, то δ''сp>δcp,
Следовательно, средняя величина допуска при частичной взаимозаменяемости
может быть существенно увеличена даже при небольшом проценте риска.
В общем случае замыкающий размер сопряжения может быть
представлен в виде функции переменных величин — составляю
щих размеров: АΔ=f(А1,А2,А3+…..+Аm-1), откуда
dAΔ= . dA1+
. dA2+….
. dAm-1, где dAΔ, dA1,dA2 и т.д –величины полей рассеяния,
размеров;
, и т.д.
Очевидно, что величина зазора в сопряжении после определенного
срока работы сборочной единицы зависит от ее первоначаль ного значения. Поэтому зазор, который получен при сборке,
непосредственно влияет на длительность периода эксплуатации
сопряжения.
Оптимальную величину зазоров в сопряжениях обычно опре
деляют экспериментально. Получение этих величин путем гидро
динамического расчета дает только приближенные значения/так
как многообразие факторов (свойство материалов сопрягающихся деталей, характер действия нагрузок, условия теплопередачи,
эллипсность, конусность и пр.) не дает возможности учесть их
влияния в совокупности. При этом часто оптимальная величина
зазора, найденная экспериментально, для ряда сопряжений может
быть меньше расчетной, а для других — больше. Например, ис
следование основных сопряжений, проведенное на автомобиль
ных двигателях, дало основание для изменения зазоров (табл. 5).
Увеличение зазоров в шатунных подшипниках позволило ус
транить надиры и уменьшить выкрашивание баббитового слоя
из-за контактного трения шейки вала.
Правильный выбор посадок в сопряжениях, кроме увеличения
общего срока службы всей машины, имеет большое значение для
обеспечения равностойкости (в отношении износа) ее отдельных
сборочных единиц и деталей. Иными словами, крайне желательно,
чтобы сопрягающиеся детали изнашивались равномерно, равно
как и все детали одной сборочной единицы. В этом случае облег
чается ремонт машины, который может быть сведен к последова
тельной замене через определенные промежутки времени отдель
ных ее частей.
моделирования технологических размерных цепей [28].
В ряде соединений в условиях мелкосерийного производства
требуемая точность достигается путем так называемой сопряжен
ной обработки. В этом случае охватывающую деталь — втулку
изготовляют с соблюдением экономически выгодных допусков, а
парную охватываемую деталь — вал затем обрабатывают (доводят)
на станке при активном контроле до размера, обеспечивающего
требуемую посадку в сопряжении с данной втулкой. Принци
пиальная схема этого процесса с пневматическим контролем дана
на рис. 21. Здесь разность диаметров отверстия втулки 3 и вала 1
может быть определена по показаниям дифференциального от-
счетного устройства 5. При определенном значении этого показа
ния доводка вала прекращается.
При сборке по методу групповой взаимозаменяемости для каж
дой детали, входящей в размерную цепь, допуск на неточность
изготовления расширяют, но после изготовления детали сорти
руют по размерам на несколько групп в пределах более узких
допусков. Готовые детали сортируют (производят селекцию) в пределах
указанных допусков на несколько (в данном примере пять) раз
мерных групп, после чего производят сборку, используя группы
деталей с уже значительно меньшими допусками. Иными словами, в процессе подбора
детали выбирают с такими размерами, чтобы зазор или натяг в каждой данной паре лежал в более узких пределах, чем
тот который можно достичь при соединении произвольно взятых
деталей. Поэтому создается возможность обеспечить в процессе
сборки большую точность, а также стабильность посадки, что
часто бывает очень важно. В условиях производства, в зависимости от его масштабов применяют один
из двух видов подбора деталей — штучный и групповой. При штучном подборе
одну из деталей предварительно измеряют, после чего, руководствуясь величиной
зазора или натяга, необходимого для данного соединения, определяют требуемые
предельные размеры сочленяющейся детали и уже по этим размерам выбирают Групповой подбор осуществляется путем предварительной сор
тировки деталей, которая может быть механизирована и произ
ведена до поступления деталей на сборку. Для этого допуски на
изготовление сопрягающихся деталей делятся на одно и то же
количество интервалов.
Рассортировка охватывающих и охватываемых деталей на раз
мерные группы связана с существенным недостатком, заключаю
щимся в том, что значительное количество этих деталей, нередко
до 30—40%, остается без применения, так как сопряжение их
друг с другом не отвечает установленным требованиям точности.
Повышение точности обработки одной из деталей в случае
селективной сборки не способствует росту точности сопряжения;
при сортировке на две группы это вообще не дает эффекта, а при
сортировке на большее число групп оказывает отрицательное
влияние. Если необходимо повысить точность сопряжения, то
валы обрабатывают на один квалитет грубее, чем отверстия.
После рассортировки каждая группа охватывающих и охваты
ваемых деталей получает соответствующую одинаковую буквен
ную, цифровую или цветовую маркировку.
На заводах крупносерийного и массового производства детали
рассортировывают при помощи сортировочных автоматов, про
изводительность которых нередко достигает нескольких тысяч де
талей в час, а точность сортировки — до 0,5 мкм.
Детали, участвующие в возвратно-поступательном движении
(ползуны, шатуны), сортируют по массе, так как при наличии
большой разницы в массах возможно появление в машине допол
нительных неуравновешенных сил, вызывающих вибрацию. Глав
ным образом это относится к быстроходным механизмам и маши
нам. Например, для многоцилиндровых двигателей внутреннего сгорания допускаемая разница в массе поршней одного и того же
двигателя обычно колеблется от 20 до 40 г (при диаметре поршня
до 150 мм). Поэтому поршни перед сборкой взвешивают и рас
пределяют на четыре-пять групп так, чтобы разница их масс не
превышала указанных величин.
В мелкосерийном производстве для этих целей пользуются специальными
приспособлениями типа весов с широкой шкалой для сравнения массы проверяе
мых поршней с массой эталонного поршня. Для этого шкалу разделяют обычно на
несколько зон направо и налево от центрального положения стрелки, исходя из
установленных пределов допускаемых отклонений масс в каждой зоне. Помещая
поршень на весы, по отклонению стрелки определяют, к какой зоне он относится,
и сортируют поршни по группам, соответствующим зонам шкалы весов.
Поршни, массы которых лежат вне пределов, установленных на шкале,
подвергают соответствующей корректировке. При этом приспособления для
взвешивания снабжают фрезерными головками, дающими возможность, не сни
мая детали, подогнать ее массу фрезерованием до требуемой величины. Глубина
фрезерования, а следовательно, и количество снимаемого металла нередко
устанавливаются автоматически, так как приближение детали к фрезе опреде
ляется избытком ее массы.
В крупносерийном и массовом производствах детали по массе сортируются
на автоматах. Фирма La Salle Machine Tool, Inc (США) создала девятипозицион
ную гидрофицированную установку с электрическим управлением производитель
ностью 600 поршней в час. Поршни поступают из накопителя автоматически и
взвешиваются, при этом данные следуют в запоминающее устройство. На основа
нии информации из блока памяти на позициях подгонки с бобышек поршней
сфрезеровывается соответствующее количество металла с точностью ± 2 г. В конце
установки производится вторичное контрольное взвешивание и, в случае обнару
жения погрешности, отбраковка соответствующих деталей.
Автоматы для взвешивания шатунов позволяют определять разницу масс
на каждом конце контролируемого шатуна и шатуна-эталона. Для удобства
сравнения взвешиваемых шатунов с эталоном и рассортировки их на весовые
группы шкалы указателей разделяют на соответствующее (три, пять) число зон.
Когда шатун подается на автомат, сразу же определяется та зона, которой соот
ветствуют массы на каждом его конце.
Недостатками сборки по методу подбора деталей ягляются
ограниченная взаимозаменяемость, необходимость создания в це
хе излишних запасов деталей, а также некоторое повышение тру
доемкости и стоимости сборки за счет времени, затрачиваемого на
сортировку. Несмотря на это, подбор деталей следует считать
для многих конструктивных узлов основным методом, допуска
ющим получение необходимой точности сборки при экономической
точности обработки сопрягаемых деталей. Пользуясь этим мето
дом, можно избежать в собираемом механизме зазоров на верхнем
и нижнем пределах, повысив тем самым качество сборки и изно
состойкость сочленений в условиях эксплуатации.
Для достижения собираемости многих сборочных единиц ма
шин и механизмов широко применяют, особенно в тяжелом,
транспортном и некоторых других отраслях машиностроения,
пригонку деталей по месту. При сборке по методу пригонки необ
ходимая точность в сопряжении достигается изменением размера
одной из деталей узла путем слесарной или механической обра
ботки. Другие же сопряженные детали изготовляют по допускам,
выгодным для данного производства. Пригоночные работы
в процессе сборки отнимают много времени и заранее трудно поддаются учёту
Это усложняет сборку, нарушает её ритм и нередко является причиной плохого качества
сборочных работ. Кроме того, операции пригонки , связанные со снятием стружки, ,вызывают загрязнение ранее собранных и установленных сборочных единиц и поэтому
требуют дополнительной затраты времени на их промывку, а нередко, и разборку.
Метод пригонки применяется гл.обр. в индивидуальном и мелкосерийном производствах, однако и в условиях серийного
производства многих машин объем пригоночных работ иногда
еще значителен.
Вместо пригонки деталей в ряде случаев бывает намного удоб
ней и выгоднее достигать требуемой посадки введением в цепь
сменного звена — компенсатора, имеющего различные размеры. устранить влияние несоосности.
Использование компенсатора, конечно, предусматривается кон
струкцией. С учетом этого производится решение размерных це
пей сборочных единиц или механизма. При этом распространен
ными являются цельные неподвижные компенсаторы, комплекты
компенсирующих прокладок одинаковой толщины и комплекты разной толщины. В первом случае при решении размерной цепи
находят параметры комплекта компенсатора, количество ступеней
размеров, число компенсаторов на каждой ступени, обеспечиваю
щее требуемую точность сборки данной партии изделий, точность
самих компенсаторов. Во втором и третьем случаях определяют
толщину каждой прокладки и допуск на этот размер, а также ко
личество необходимых прокладок. Расчет ведут преимущественно
на основе теории вероятностей с допущением определенного риска
несобираемости (обычно 0,27%).
Комплекты прокладок обычно делают из листового металла
различной толщины. Эти компенсаторы применяют при регулиров
ке зазоров в зацеплении конических зубчатых колес, конических
роликоподшипниках, подшипниках скольжения и во многих дру
гих элементах машин.
Применение компенсаторов увеличивает число деталей в ма
шине и поэтому несколько усложняет конструкцию, но это обычно
не повышает стоимость машины, так как благодаря компенсиру
ющим устройствам ускоряется сборка и снижаются затраты на ме
ханическую обработку. При наличии компенсатора детали могут
быть изготовлены по значительно расширенным допускам, в то же
время может быть достигнута весьма высокая точность сопряже
ний, особенно при подвижном компенсаторе.
КОНТРОЛЬ ТОЧНОСТИ ПРИ СБОРКЕ
Осуществляемые в процессе сборки контрольные операции
дают возможность установить в соединениях, сборочных единицах
и в машине степень соответствия относительного положения и пе
ремещения исполнительных поверхностей техническим требова
ниям на сборку. В общем случае методы контроля могут быть раз
делены на визуальные и с применением технических средств,
измерений (универсальных, специальных, механизированных, ав
томатизированных) .
В практике сборки без специальных приборов проверяют, на
пример, форму и размеры пятен касания при контроле на краску,
плотность посадки простукиванием «на звук», состояние поверх
ностей, кромок, стыков и пр. Понятно, что этот метод субъекти
вен, и точность таких измерений весьма мала.
С помощью технических средств измерений контролируют за
зоры в сопряжениях и относительное положение деталей. Для этого
применяют концевые и штриховые меры длины, щупы, штанген-
инструменты, микрометрические инструменты, рычажно-меха-
нические, электрические и пневматические приборы, а такжэ
различные специальные контрольные приспособления и уста
новки. условиями. Если возможно, то в качестве контрольной базы все
гда следует принимать установочные базы.
К основным видам геометрических проверок, осуществляемых
при сборке сборочных единиц и механизмов с помощью техни
ческих средств, относятся контроль зазоров (рис. 27), проверка
на радиальное, осевое и торцовое биения (рис. 28), контроль
параллельности и перпендикулярности (рис. 29), соосности, прямо
линейности и плоскостности (рис. 30), положения деталей в неко
торых сборочных единицах (рис. 31).
Для обеспечения требуемой точности измерений необходимо,
чтобы контролируемая сборочная единица и прибор или кон
трольные приспособления находились в удобном для рабочего по
ложении и базировались на жестких опорах. Поэтому контроль
ные посты целесообразно оборудовать плитами, подставками для
измерительного инструмента и средствами для закрепления про
веряемых сборочных единиц.
Номенклатура приборов и приспособлений, применяемых при
механизированных измерениях, достаточно широка. Особенно
часто используют приспособления с индикаторами часового типа.
Выбор необходимого типа контрольного приспособления зависит
от требуемой точности и допустимой погрешности измерения; при
этом последняя характеризуется разностью между показанием
контрольного приспособления и фактическим значением контро
лируемого параметра. Относительная погрешность измерения со
ставляет 15—20% допуска контролируемого параметра.
Классификация соединений и их технологичность. Классификация соединений, применяемых при сборке. Подвижные и неподвижные соединения, их технологичность
Основными организационными формами сборки являются ста
ционарная и подвижная. При стационарной сборке изделие пол
ностью собирают на одном сборочном посту. Все детали и сбороч
ные единицы, требуемые для сборки изделия, поступают на этот
пост.
При подвижной сборке собираемое изделие последовательно
перемещается по сборочным постам, на каждом из которых вы
полняется определенная операция. Посты оснащаются приспособ
лениями и инструментами, необходимыми для выполнения дан
ной операции. Детали и узлы для сборки поступают на соответ
ствующие посты.
Стационарная сборка может быть осуществлена без расчлене
ния (принцип концентрации) и с расчленением (принцип диффе
ренциации) сборочных работ.
Стационарную сборку изделия без расчленения работ прак
тически должен осуществлять один рабочий высокой квалифи
каций. Цикл сборки изделия по этому методу при значительной
трудоемкости сборочного процесса удлиняется, и при большой
•программе выпуска требуется большее количество сборочных
площадей, инструмента, оборудования и пр. Этот метод часто
применяется в опытном производстве при сборке специальных,
уникальных приборов, а также в мелкосерийном производстве,
■когда весь процесс сборки изделия состоит из небольшого количе
ства операций. Однако в настоящее время такая организация
сборки, получившая название «метода расширенных заданий»,
начинает распространяться и в ряде производств средней серий
ности. Как показывает опыт, качество сборки при этом возрастает
и нередко повышается производительность труда. Сборщик не
только выполняет все операции от начала до конца (малогабарит
ные сборочные единицы изделия, число операций до 30), но и производит испытание. Это значительно повышает его ответствен
ность за сборку и надежность изделия.
Разновидностью метода сборки без расчленения процесса
является бригадный метод, когда сборку всего крупногабарит
ного изделия выполняет бригада рабочих; но бригадный метод
часто уже является первым шагом на пути дифференциации, ибо
внутри бригады, как показывают наблюдения, имеет место неко
торое разделение работ: одни рабочие специализируются на одной
группе сборочных операций, другие — на другой.
При сборке нескольких одноименных машин за каждым рабо
чим бригады нередко закрепляют одну или несколько сборочных
единиц изделия, вследствие чего члены бригады специализируются
на выполнении сборочных работ определенного вида. Однако по
конструктивным условиям в большинстве случаев вести сборку
всех сборочных единиц одновременно не представляется возмож
ным. В связи с этим при таком методе сборки большое значение
имеет правильное календарное планирование [42 ] начала и конца
сборочных работ по узлам с учетом их трудоемкости и последова
тельности установки на машину.
Бригадный метод сборки широко распространен в единичном
и мелкосерийном производствах, а также при выполнении повтор
ной сборки машины на месте ее постоянной работы (например,
сборка вновь устанавливаемых сложных полиграфических машин
в типографиях, сборка крупных гидравлических прессов, турбин
с их установкой и пр.).
• Стационарная сборка с расчленением работ предполагает деле
ние процесса на узловую сборку основных групп и общую сборку
изделия. При этом сборку каждой группы и общую сборку изде
лия выполняют в одно и то же время многие сборщики. В результате одновременного выполнения сборочных операций
большим количеством рабочих длительность процесса сборки
может быть значительно сокращена. Расчленение процесса сборки дает значительный экономиче
ский эффект. Сокращается потребность в рабочей силе и произ
водственных площадях, увеличивается выпуск машин, умень
шается трудоемкость, снижается себестоимость сборочных работ.
В ряде производств объект сборки при расчлененном про
цессе остается на одном месте. Собираемые машины размещают
на стапелях или стендах, а рабочий (или группа рабочих) выпол
няет у каждого объекта сборочную операцию, после окончания
которой переходит к следующему объекту, где проделывают ту же
операцию, и т. д. При этом методе сборки каждую группу рабочих
целесообразно снабжать небольшим передвижным столом, на
котором помещаются инструмент и приспособления. Полную сборку некоторых крупных и тяжелых машин осущест
вить на заводе-изготовителе трудно. Для этого требуются значи
тельные площади, соответствующие габаритам машины, специаль
ные подъемные средства. Поэтому на ряде заводов тяжелого маши
ностроения применяется так называемый цепной метод сборки. Машину собирают последовательно, начиная с базовой сборочной
единицы. Но весь процесс общей сборки разрабатывается и ор
ганизуется так, чтобы на определенных этапах собранные ранее
узлы можно было, без нарушения качества дальнейших работ,
разобрать и отправить заказчику.
Таким образом, потребные для сборки площади сокращаются,
и уменьшается цикл сборки..
Подвижная сборка и расчлененный процесс организуют так,
что рабочие, выполняющие отдельные операции, находятся на за
крепленных за ними местах (постах), к которым подаются соот
ветствующие детали и сборочные единицы, объект же производ
ства последовательно перемещается от одного поста к другому.
Это перемещение может быть свободным, когда собираемые
изделия располагаются, например, на тележках, перемещаемых
самими исполнителями, «принудительным, когда объек
ты сборки перемещаются при помощи механических транспортных
устройств непрерывного или прерывного действия. Свободное пере
мещение осуществляется обычно в мелкосерийном производстве,
принудительное — в крупносерийном и массовом.
ПОТОЧНАЯ СБОРКА
В условиях крупносерийного и массового производств процесс
сборки может быть расчленен таким образом, что каждую опера
цию будет выполнять только один рабочий. В этом случае объект
работы (сборочная единица или изделие) должен в процессе произ
водства последовательно перемещаться от одного рабочего к дру
гому. Под этим подразумевается движение собираемого изделия,
обычно осуществляемое при помощи транспортных средств.
Такую организацию сборки принято называть поточной.
Основные факторы, характеризующие поточный метод сборки,
следующие: закрепление за каждым рабочим местом вполне опре
деленных сборочных операций, чередующихся по ходу технологического процесса сборки; передача собираемого объекта на каж
дую следующую операцию немедленно после окончания предыду
щей; ритмичная (строго по графику) синхронная работа на всех
рабочих местах сборочной линии; слаженная, четкая работа всех
смежных и обслуживающих поток участков производства; возмож
ность широкого внедрения средств механизации. Под поточной линией сборки понимается ряд рабочих мест,
участвующих в сборке сборочных единиц или машины, расположен
ных соответственно последовательности операций технологического
процесса.
Непрерывность процесса при поточной сборке достигается бла
годаря тому, что длительность любой сборочной операции на ли
нии сборки равна или кратна темпу сборки изделия.
ПРИГОНОЧНЫЕ РАБОТЫ ПРИ СБОРКЕ
Точность сборки на основе принципов полной или неполной
взаимозаменяемости обеспечивается преимущественно в массовом
и крупносерийном производствах. В мелкосерийном и тем более
в единичном производстве принцип взаимозаменяемости экономи
чески не оправдан и применяется лишь в отдельных случаях.
Детали в этих производствах обрабатывают на универсальном
оборудовании обычно без применения специальных приспособле
ний, а контроль осуществляется универсальным измерительным
инструментом, не всегда обеспечивающим требуемую точность
измерений. Погрешности взаимного расположения поверхностей
деталей в процессе их обработки нередко значительно превышают
допускаемые отклонения. Это вызывает, как уже отмечалось,
необходимость в процессе сборки дополнительно обрабатывать
детали и сборочные единицы, пригоняя их по месту. Таким обра
зом, под пригонкой понимается ручная или механическая обра
ботка в процессе сборки сопрягающихся поверхностей деталей для
достижения необходимой точности сопряжений или обеспечения
других качественных показателей.
Пригонка может иметь место и в серийном производстве, так
как в отдельных случаях при малых допусках посадок экономи
чески выгоднее применить пригонку деталей в процессе сборки,
чем повышать точность обработки. Пригонка деталей иногда не
обходима также для компенсирования неблагоприятного суммиро
вания допусков в многозвенной размерной цепи, а также при на
личии конструктивных особенностей сопрягаемых деталей.
Если обеспечивается точность сборки пригонкой, детали —■
звенья размерной цепи изготовляют по увеличенным допускам,
экономически достижимым в производстве. Таким образом, пригоночные работы при сборке могут;быть
технически необходимыми, экономически целесообразными, а
также вызванными некачественным изготовлением деталей в обра
батывающих цехах.
Процесс пригонки состоит из двух этапов: определения вели
чины погрешности и устранения ее снятием излишнего слоя
металла. личные доделочные операции.
Наиболее распространенными видами пригоночных работ яв
ляются опиливание, зачистка, притирка, полирование, шабре
ние, сверление отверстий по месту, развертывание отверстий,
подторцовывание и гибка.
Как известно, при обработке металла режущими инструмен
тами на поверхности остаются царапины и неровности, размеры
которых зависят от способа обработки. Качество обработки поверхности влияет также на стабильность
соединений при сборке, так как при грубой обработке поверх»
ности сопряжений быстро изнашиваются и меняется характер по
садки. При неподвижных посадках в случае грубо обработанных
поверхностей в процессе сборки может изменяться величина на
тяга (например, при запрессовке).
СБОРКА РЕЗЬБОВЫХ СОЕДИНЕНИЙ
Резьбовые соединения в конструкциях машин составляют 15—
25% от общего количества соединений. Такая распрсстраненнссть
объясняется их простотой и надежностью, удобством регулиро
вания затяжки, а также возможностью разборки и повторной
сборки соединения без замены детали.
Широко применяются следующие разновидности резьбовых соединений:
для обеспечения неподвижности и прочности сопрягаемых деталей; для обеспече
ния прочности и герметичности; для правильности установки сопрягаемых дета
лей; для регулирования взаимного положения деталей.
Трудоемкость сборки резьбовых соединений машин составляет 25—35%
общей трудоемкости сборочных работ.
Процесс сборки резьбсвсго соединения в общем случае скла
дывается из следующих элементов; подачи деталей, установки
их и предварительного ввертывания (наживления), подвода и
установки инструмента, завинчивания, затяжки, отвода инстру
мента, дотяжхи, шплинтовки или выполнения иного процесса,
необходимого для предохранения от самоотвинчивания. Из техно
логических работ в процессе завинчивания 12—17% идет на пред
варительное ввертывание, 18—20% на затяжку и 5—8% на до-
тяжку (от всего времени сборки соединения). В случае автомати
ческой сборки все эти три элемента процесса выполняются последо
вательно одним инструментом. Однако при механизированном
выполнении работ предварительное ввертывание часто производят
вручную. Объясняется это тем, что от доброкачественности нажив
ления зависит правильная первоначальная установка одной де
тали по резьбовому отверстию другой, а также возможность исклю
чения срывов первых ниток резьбы, что нередко приводит к порче
дорогостоящих корпусных деталей.
ПОСТАНОВКА ШПИЛЕК
Неподвижность шпильки, ввинченной в корпус, достигается
натягом, создаваемым обычно одним из трех способов: коническим
сбегом резьбы (рис. 92, а), упорным буртом (рис. 92, б) или тугой
резьбой с натягом по среднему диаметру (рис. 92, в). При первом
способе шпилька завинчивается достаточно свободно в гнездо
вплоть до сбега, а при дальнейшем ее вращении в витках сбега
возникают расклинивающие силы, создающие необходимый натяг.
Стабильность такого соединения зависит преимущественно
от механических характеристик материалов корпуса и шпильки,
угла сбега резьбы (рис. 92, а) и момента завинчивания шпильки.
Для стальных шпилек и корпусов из алюминиевых и магниевых
сплавов угол сбега обычно составляет 20°. При стальных корпусах
для повышения усталостной прочности и большей неподвижности
соединения угол сбега уменьшают.
Этот способ постановки шпилек имеет существенные недо
статки, состоящие в том, что расклинивающее действие нередко
вызывает чрезмерное смятие начальных витков резьбы в отверстии
и микроскопические радиальные трещины, особенно если базо
вая деталь чугунная. Поэтому, как свидетельствует опыт, исполь
зование сбега резьбы рационально лишь в соединениях, не не
сущих особенно больших нагрузок и не подверженных вибра
циям. При постановке шпилек выполняют следующие основные тре
бования:
1) шпилька должна иметь достаточно плотную посадку в кор
пусе, чтобы при свинчивании даже туго посаженной гайки она
не вывинчивалась;
2) если неподвижность шпильки обеспечивается натягом по
среднему диаметру резьбы, то ее при постановке недовертывают
до начала сбега резьбы на угол несколько больший, чем требуется
для затяжки гайки, навинчиваемой на эту шпильку;
3) ось шпильки должна быть перпендикулярна (с определен
ными допустимыми отклонениями) поверхности детали, в которую
ввернута шпилька. Отклонение от перпендикулярности вызывает
значительные дополнительные напряжения в резьбе шпильки и
часто может быть причиной обрыва ее при работе в машине.
Для выполнения третьего требования необходимо при доделоч-
ных работах на сборке избегать сверления отверстий, а также
нарезания резьбы без кондуктора. Если такие работы необходимо
производить в процессе сборки, то их целесообразно выполнять
на сверлильном станке. Перекос шпильки, особенно в тяжело нагруженном соедине
нии, очень опасная погрешность, результатом которой может быть
обрыв шпильки из-за перенапряжения. Для предохранения резьбы от повреждения на выступающие
концьГустановленных шпилек в^процессе сборки необходимо на
девать или в крайнем случае сразу же навинчивать гайки.
Для ввертывания шпилек вручную применяют инструмент,
являющийся по существу гайкой, которую навинчивают на сво
бодный конец шпильки и тем или иным способом стопорят на ней. При завинчивании шпилек механизированным инструментом
для удерживания их используют головки, принцип действия ко
торых также основан на захвате шпильки либо за резьбу, либо за
цилиндрическую часть. При завинчивании шпилек механизированным инструментом
для удерживания их используют головки, принцип действия ко
торых также основан на захвате шпильки либо за резьбу, либо за
цилиндрическую часть.
СБОРКА БОЛТОВЫХ И ВИНТОВЫХ СОЕДИНЕНИЙ
В конструкциях машин применяются болтовые и винтовые
соединения, собираемые без затяжки и с предварительной затяж
кой. Область использования соединений первого типа крайне
ограничена, соединения же второго типа распространены чрез
вычайно широко.
Предварительная затяжка соединений при сборке играет
существенную роль в повышении долговечности работы сборочных
единиц или машины и должна быть такой, чтобы упругие деформа
ции деталей соединения при установившемся режиме работы
машины или механизма находились' в определенных пределах,
обусловленных конструктивными особенностями. Степень пред
варительной затяжки болта или винта зависит от сил, нагру
жающих соединение. На прочность резьбовых соединений, , испытывающих
переменные нагрузки, оказывают влияние точность параметров резьбы (особенно шага),
концентрация напряжений, характер распределения нагрузки по виткам и пр. Но при этом влияние
качества сборки и прежде всего правильно выбранной посадки
в резьбе, величина предварительной затяжки, отсутствие переко
сов во многих тяжело нагруженных соединениях особенно заметны.
На степень предварительной затяжки резьбового соединения
влияют конструкция сборочного инструмента; состояние и вид
покрытия торцовых поверхностей гайки, болта или винта, а также
опорной поверхности детали; состояние, точность и вид покрытия
резьбы; жесткость скрепляемых деталей; повторяемость сборки;
скорость завинчивания; условия сборки и индивидуальные на
выки сборщика.
Влияние конструкции сборочного инструмента прежде всего
проявляется в способе захвата головки болта или гайки и длине
рукоятки ключа. Плотный обхват гайки ключом и большая длина
его рукоятки дают возможность увеличить предварительную за
тяжку; свободный захват гайки ключом и меньшая длина рукоятки,
а также неудобная ее форма могут быть причинами уменьшения
предварительной затяжки. Состояние опорных поверхностей де
талей и торца гайки сказывается на коэффициенте трения, и в связи
с этим при одном и том же моменте на ключе затяжка может быть
больше или меньше. В достижении высокого качества сборки резьбовых соединений
наживление гайки играет большую роль; смятие, срыв резьбы,
заедание в значительной мере зависят от того, как произведено
цаживление. Особенно важно это при механическом наживлении.
В этом случае для безусловной ориентации гайка должна иметь
возможно больше степеней свободы. Поэтому применяют специаль
ные головки , где гайка удерживается подпружинен
ными шариками и самоориентируется относительно болта
(шпильки). Правильно выбранная последовательность навинчивания гаек
исключает перекосы и коробление деталей. Недовернутая гайка
вызывает перегрузку соседних с ней шпилек, и это может явиться
причиной их разрыва во время работы машины.
Общий принцип — затягивать сначала средние гайки, затем пару соседних
справа и пару соседних слева, после чего снова пару соседних справа и т. д.,
постепенно приближаясь к краям по так называемому методу спирали .
В процессе разборки резьбовых соединений целесообразно
придерживаться обратного порядка отвинчивания гаек; это позво
лит предотвратить перекосы скрепляемых деталей. Рекомендуется
вначале поочередно слегка отпустить все гайки и после этого
отвинтить их полностью.
Разрабатывая технологию сборки нового многоболтового со
единения, с целью изыскания более рациональной последователь
ности затяжки целесообразно воспользоваться следующим спо
собом: вначале заложить встык по контуру сопряжения белую
и копировальную бумагу, затем затягивать гайки (винты) с тре
буемым моментом в различной последовательности, каждый раз
проверяя характер отпечатка на белой бумаге. Очевидно, рацио
нальная последовательность будет та, при которой отпечаток
будет равномерный по всей площади сопряжения.
При затяжке гайки обычным ключом следует внимательно
следить за тем, чтобы момент на ключе не превышал допустимой
величины. Бесконтрольная затяжка может быть причиной разрыва
шпильки или болта.
ПОСТАНОВКА ВИНТОВ
Процесс сборки соединения, в котором скрепляющей деталью
является винт, состоит обычно из следующих элементов: установки
подсобранных деталей соединения на подставку (в случае сборки мелких и средних сборочных единиц); захвата винта механической
отверткой (рис. 117, а); завинчивания винта в деталь (рис. 117, б);
снятия собранного соединения. При сборке крупных сборочных
единиц или общей сборке изделия процесс состоит из наживления
и завинчивания винта, а при автоматической подаче винтов к на
конечнику механической отвертки — из одного перехода: завин
чивания.
Так как винтовые соединения обычно многократно собирают
и разбирают (при каждой разборке и сборке, а иногда дополни
тельно и при пригонке), посадка резьбы здесь не может быть с на
тягом, как в шпильках; резьба в этом случае имеет размеры, обус
ловливающие нормальный зазор по среднему диаметру, как в со
пряжении болт—гайка, но гайкой в данном случае могут быть
корпусные детали из стали, чугуна, алюминиевого сплава и пр.
Тугое винтовое соединение нежелательно; но не менее нежела
тельна и другая крайность — слишком свободное соединение,
поэтому, если винт, завернутый до половины нарезки, имеет
хотя бы небольшую качку, его нужно заменить.
ПОСТАНОВКА РЕЗЬБОВЫХ ВТУЛОК И ЗАГЛУШЕК
В часто разбираемых резьбовых соединениях для уменьшения
износа резьбы корпуса в него ввертывают втулки (латунные)
с наружной и внутренней резьбами . Чтобы втулки
не вывинчивались из гнезда, их ставят с натягом и расчеканивают
или раскернивают. Для облегчения постановки таких втулок
необходимо, чтобы отверстие в корпусе имело небольшую фаску.
К соединению втулки с корпусом нередко предъявляется еще
требование герметичности, так как жидкости (горячее масло, вода,
бензин) и газы протекают под давлением и легко просачиваются
через неплотности.
Герметичности достигают торцовым уплотнением. Поэтому
очень важно, чтобы поверхности торцов сопрягаемых корпуса и
втулки были перпендикулярны оси резьбы. Для уплотнения со
единений под торец детали ставят прокладку из
легкодеформируемого материала — отожженную медную, медно
асбестовую, из паронита и др. Если обе торцовые поверхности
сопрягаемых деталей перпендикулярны оси резьбы и достаточно
чисты (нет глубоких царапин, рисок), то прокладки выдержи
вают даже высокие давления. Однако при каждой переборке
в ответственных соединениях прокладки следует менять.
Заглушки — стальные, бронзовые латунные, алюминиевые
обычно должны препятствовать просачиванию жидко
стей при наличии разности давления. Если заглушки не вывин
чиваются при разборке, сопряжения часто уплотняют в резьбе белилами или суриком. Однако засохшие белила и сурик сильно
затрудняют отвертывание заглушек, так что иногда во избежание
порчи резьбы основной детали их приходится даже высверливать.
Такие уплотнения испытывают на герметичность под давлением
жидкости, несколько превосходящим рабочее давление, причем
если потребуется заменить заглушку, это необходимо сделать до
того, как засохнут белила.
Пробки и ниппеля часто выполняют с конической резьбой,
имеющей в этих случаях общеизвестные преимущества перед ци
линдрической. Цилиндрические резьбы в соединениях, находя
щихся под гидравлическим давлением, требуют при сборке раз
личных уплотняющих веществ; конические резьбы обеспечивают
непроницаемость за счет деформации витков.
При нормальной затяжке деталей с конической резьбой пос
ледняя одновременно стопорится, поэтому дополнительных средств
для предотвращения самопроизвольного отвинчивания не тре
буется.
СБОРКА СОЕДИНЕНИЙ СО ШПОНКАМИ
Точность сборки соединения с одной или несколькими шпон
ками обеспечивается изготовлением его элементов по размерам
с допусками.
Размеры шпонок выполняют по системе вала, так как посадки
в пазах вала и ступицы, как правило, различны. При неподвиж
ных соединениях шпонку устанавливают в паз вала плотно или
даже с натягом, а в пазу ступицы посадка создается более сво
бодная.
Посадку Р/h
шпонки в пазу втулки применяют обычно тогда,
когда втулка, передавая крутящий момент, должна свободно
перемещаться вдоль оси вала. При монтаже на вал охватывающей
детали необходимо следить, чтобы она не «сидела» на шпонке,
т. е. центрировалась бы исключительно на цилиндрической или
конической поверхности вала. При этом между верхней плоскостью
шпонки и впадиной паза втулки должен быть достаточный зазор.
Если в собранной сборочной единице зазор проверить нельзя, то
перед постановкой охватывающей детали рекомендуется промером
определить размер D+t1. Он должен быть больше соответствующего размера вала со шпонкой на величину требуемого зазора.
D+t1 –это диаметр вала вместе с выступающей шпонкой.
Устанавливая в паз шпонки больших размеров с посадками N/h и P\h,
не следует пользоваться молотком или другими ударными приспособлениями. Вследствие неравномерных и нецентральных ударов возможен поперечный перекос
шпонки и врезание ее кромки в тело вала или наоборот.
Этого недостатка избегают, запрессовывая шпонки под прессом или струбцинами.
Еcли шпонку устанавливают с посадкой N/h в паз охватывающей детали,
то эту операцию удобно производить на прессе в приспособлении. Правильная сборка соединений со шпонками в значительной
мере обеспечивает работоспособность и надежность работы сбороч
ной единицы. Большое значение при этом прежде всего имеет
строгое соблюдение посадок в сопряжениях шпонки с валом
и охватывающей деталью. Увеличенные зазоры — одна из основных причин
нарушения распределения нагрузок, смятия и разрушения шпонки.
При вынимании шпонок из пазов пользуются одним из способов. В качестве инструмента обычно употребляют мягкие выколотки.
Разборку соединения со шпонками производят сдвиганием
охватывающей детали с посадочного места, а при креплении детали
на конце вала — удалением шпонки из паза. Для облегчения работы в торце шпонки
целесообразно предусматривать отверстие с резьбой, которое можно использовать
для установки Г-образного штыря, сцепляющегося со съемником .
' При извлечении клиновой шпонки с головкой использование молотка и зу
била, загоняемого между головкой шпонки и ступицей детали, во всех случаях не
может быть оправдано. Такой способ демонтажа ведет к искривлению шпонки,
порче торцовых поверхностей деталей, а нередко и к деформациям вала. Извле
кать шпонку с головкой необходимо при помощи приспособлений.
Призматическую шпонку после демонтажа охватывающей детали удобно
извлекать при помощи винтов-съемников , ввинчиваемых в предусма
триваемые для этой цели отверстия. -
В условиях крупносерийного и массового производства приз
матические и сегментные шпонки обычно не пригоняют (в процессе
самой сборки). В единичном и мелкосерийном производствах
такие работы допускаются, особенно когда к шпоночным соеди
нениям предъявляют особые требования в отношении точности.
Шпоночные соединения имеют недостатки, заключающиеся
в том, что при передаче больших и особенно знакопеременных
крутящих моментов шпоночный паз на валу приходится делать
глубоким, при этом снижается прочность вала. При боковых
зазорах между шпонкой и пазом охватывающей детали паз посте
пенно разрабатывается, что может вызвать срез шпонки или ее
деформацию. Учитывая это, особые требования предъявляют
к точности центрирования шпоночного соединения и плотности
посадки на валу охватывающей детали.
СБОРКА ШЛИЦЕВЫХ СОЕДИНЕНИЙ
Соединение деталей по шлицам позволяет обеспечить более
точное центрирование, чем при соединении деталей со шпонкой,
а также повышенную прочность. Распространены прямобочные,
эвольвентные и треугольные шлицевые цилиндрические соедине
ния. В прямобочном шлицевом соединении охватывающая деталь
может быть центрирована по наружной поверхности шлицев, по
поверхности впадин или по боковым сторонам шлицев. В соеди
нениях с эвольвентными шлицами центрирование осуществляется
профилями зубьев или по наружной поверхности шлицев. При
треугольных шлицах детали центрируются по боковым профилям
шлицев. В зависимости от применяемой посадки центрирующих поверх
ностей шлицевые соединения можно отнести к одной из следу
ющих групп: тугоразъемные, легкоразъемные и подвижные.
При сборке шлицевых соединений полная взаимозаменяемость
даже в условиях массового производства обычно не достигается
из-за весьма малых зазоров, выдерживаемых в центрирующих
сопряжениях.
Сборку шлицевых соединений начинают с осмотра состояния шлицев обеих
деталей. Даже незначительные забоины, задиры или заусенцы в шлицевом соеди
нении не допускаются. Особое внимание уделяют осмотру внешних фасок и за
круглений внутренних углов шлицев, так как при неправильном выполнении
этих элементов возможно заедание на шлицах при сборке соединения. В туго
разъемных соединениях охватывающую деталь обычно напрессовы
вают на вал при помощи специального приспособления или на прессе.
Собирать такие соединения, применяя молоток, не рекомендуется. Нерав
номерные удары могут вызвать перекос охватывающей детали на шлицах и даже
задир их. При очень тугих шлицевых соединениях целесообразно охватывающую
деталь перед запрессовкой нагреть до 80—120° С. Зазоры в легкоразъемном шлицевом соединении
являются причиной перекоса сопрягающихся деталей, особенно
при несимметрично действующей нагрузке относительно средней
плоскости охватывающей детали. В результате этого возникают
дополнительные осевые силы, вызывающие колебательное движе
ние деталей соединения вдоль шлицев и усиленный износ пос
ледних. После установки и закрепления охватывающей детали на шлицах соедине
ние следует проверить на биение . Допускаемые величины радиального и торцового
биений зависят от назначения соединения и указываются в сборочном чертеже или технических требованиях на сборку. В легкоразъемных и подвижных шлицевых соединениях охва
тывающие детали устанавливают на место под действием неболь
ших усилий и даже от руки; при этом охватывающие детали кон
тролируют, кроме проверки на биение, еще и на перемещение по
шлицам на качку . В правильно собранной сбо
рочной единице перемещение охватывающей детали должно быть
легким, без заеданий. Качка охватывающей детали под действием
создаваемого вручную крутящего момента допустима лишь в очень
ограниченных пределах, определяемых техническими требова
ниями на сборку.
Особое значение в подвижных шлицевых соединениях имеет
соосность отверстия охватывающей детали и шлицевого вала.
При полной соосности все шлицы вала имеют контакт со шли
цами отверстия . В том же случае, если соосность
нарушена, в постоянном контакте теоретически будет находиться
только один шлиц , что ухудшает условия работы
соединения. Это обстоятельство необходимо учитывать при сборке.
В целях снижения напряжений смятия на боковых поверхно
стях шлицев сопряжения их в тяжело нагруженных ответственных
соединениях проверяют также с помощью краски на прилегание.
СБОРКА НЕПОДВИЖНЫХ КОНИЧЕСКИХ СОЕДИНЕНИЙ
Конические соединения с неподвижной посадкой часто при
меняют взамен цилиндрических; в сборке они имеют ряд преиму
ществ. Вследствие того, что в начале сборки вал легко входит в отверстие и самоцентрируется, сборка конических соединений
значительно облегчается, что особенно важно при установке
крупных деталей (маховиков, больших зубчатых колес). Напря
женность посадки и необходимый натяг в коническом соединении
создаются напрессовкой охватывающего конуса на охватываемый
и поэтому могут регулироваться. Такие соединения часто при
меняют без шпонок, так как при определенных натягах возможна
передача крутящего момента только силами трения, возника
ющими на поверхности контакта. Конические соединения удобны
в разборке.
Сборку конического соединения начинают с подбора охватыва
ющей детали по конусу вала. Проверку ведут по краске, на качку,
а также по глубине посадки охватывающего конуса на валу.
Коническая поверхность охватывающей детали должна плотно
соприкасаться с поверхностью конуса вала. Конические поверхности вала и охватывающей детали обычно
обработаны с шероховатостью Ra < 1,25 мм. В крупногабарит
ных соединениях отверстия при этом шабрят или развертывают
специальными сборными развертками, вследствие чего умень
шается трудоемкость пригонки.
Сборки с неподвижными соединениями.
К ним относятся соединения с гарантированным натягом,
сварные, паяные, склеиваемые и заклепочные.
По способу получения нормальных напряжений на сопряга
емых поверхностях соединения с гарантированным натягом
условно делят на поперечно-прессовые и продольно-прес
совые.
В поперечно-прессовых соединениях сближение сопрягаемых
поверхностей происходит радиально или нормально к поверхности.
Такие соединения осуществляют одним из следующих способов
нагреванием охватывающей детали перед сборкой, охлаждение
охватываемой детали, путем пластической деформации (напри
мер, развальцовки), приданием упругости охватываемой де
тали.
При продольно-прессовом соединении охватываемая деталь
под действием прикладываемых вдоль оси сил запрессовывается
в охватываемую с натягом, в результате чего возникают силы
трения, обеспечивающие относительную неподвижность де
талей.
Пластическую деформацию используют при сборке соединений,
натяг в которых создается радиальным расширением охватываемой
или сжатием охватывающей детали.
Основное назначение соединений, получаемых таким спосо
бом, — обеспечить неподвижность и герметичность от проникнове
ния газов или жидкостей. Они относятся к числу редко демонти
руемых, так как их разборка во многих случаях сопровождается
порчей одной или обеих деталей. В/конструкциях машин соедине
ния этого типа имеют большое распространение (рис. 191).
Распространенными видами пластической деформации, исполь
зуемыми в конструкциях машин для создания неподвижности
и плотности, являются вальцевание, раздача,^бортование, осадка,
формирование, обжатие.
Сварные соединения в конструкциях машин получают все
большее распространение. Прочность этих соединений обычно не
ниже прочности клепаных, они значительно менее трудоемки,
более технологичны.
Процесс соединения деталей при помощи сварки в большинстве
случаев является сборочным; он при необходимости может быть
введен непосредственно в поток узловой или общей сборки.
Сварку можно осуществлять дугой, плазмой, электросопротивлением, тре
нием, токами радиочастоты, взрывом, применением больших пластических де
формаций, ультразвуком, лазером.
Распространенными в машиностроении способами сварки яв
ляются: контактная — точечная и шовная; дуговая — полуавто
матическая и автоматическая под слоем флюса, в среде защитных
газов; электрошлаковая; ультразвуковая. В ряде производств
осваиваются новые виды сварки: электронным лучом, плазмен
ная — квантовая, диффузионная.
В связи с широким применением в конструкциях машин пла
стических масс (полиэтилена, винипласта, полихлорвинила, по
листирола, органического стекла и др.) возникла необходимость
сварки деталей из этих материалов. Используют преимущест
венно тепловые виды сварки и сварку нагревом ТВЧ. Основными элементами сборочно-сварочного процесса яв
ляются подготовка поверхностей под сварку, сборка и установка
сборочной единицы, закрепление, пуск, подвод сварочной го
ловки, подача электрода, сварка, отвод головки, выключение,
снятие сваренной сборочной единицы, контроль. При выполнении
сборочно-сварочных работ в мелкосерийном производстве широко
применяют механизированные приспособления, а в крупносерий
ном и массовом производствах — полуавтоматические и автомати
ческие сварочные установки . Большой объем сборочных работ с применением сварки выполняется при
изготовлении кузовов_и кабин различных транспортных машин. При сборке ку
зовов легковых автомобилей широко используют такие виды сварки, как точеч
ная и роликовая. Широко применяют сварочные прессы. Детали кузова соеди
няют одновременно до 600 сварочных точек. На ряде операций предусматривают
многопостовые сварочные машины, многопозиционные автоматы и так называемые
подвижные сварочные пистолеты.
Пайкой называется процесс получения неразъемного соеди
нения двух или нескольких деталей с применением присадочного металла — припоя путем их нагрева в собранном виде до темпе
ратуры плавления припоя. Расплавляемый припой затекает в спе
циально создаваемые зазоры между соединяемыми деталями и диф
фундирует в металл этих деталей. При этом протекает элементар
ный процесс взаимного растворения и металла деталей, и припоя
в результате чего образуется сплав, более прочный, чем припой.
В зависимости от температуры плавления припоя различают
пайку мягкими и твердыми припоями. Мягкие (обычно оловяни-
сто-свинцовые) припои имеют температуру плавления ниже
400° С, твердые (медные, медно-цинковые припои) 400—1200° С.
Мягкие припои обладают небольшим пределом прочности — до
10 кгс/мм2, а твердые — до 50 кгс/мм2 и выше. При необходимости
иметь большую прочность соединения применяют твердые припои;
если же пайка производится только для получения плотности,
используют мягкие припои.
Состав и назначение припоев определяются действующими
стандартами. Вид припоя назначают при разработке конструкции
сборочной единицы, с учетом условий работы последней в машине
и материала деталей, и оговаривают техническими требованиями. Кроме припоя, при пайке применяют флюсы, назначение кото
рых сводится к защите места спая от окисления при нагреве сбо
рочной единицы, обеспечению лучшей смачиваемости места спая
расплавленным металлом и растворению металлических окислов.
В качестве флюсов для твердых припоев применяют буру и пла
виковый шпат, а также смеси их с различными окислителями или
солями щелочных металлов. При пайке мягкими припоями поль
зуются канифолью, хлористым цинком, нашатырем и фосфорной
кислотой. Применяют также газообразные флюсы на основе метил-
бората и фтористого бора. Пайку точных соединений производят
без флюсов в защитной атмосфере или в вакууме. Процесс пайки включает подготовку сопрягаемых поверхно
стей деталей под'пайку, сборку, нанесение флюса и припоя, нагрев
места спая, промывку и зачистку шва.
В зависимости от способа нагрева пайку подразделяют на
следующие основные виды: газовую, погружением (в металличе
скую или соляную ванны), электрическую (дуговая, индукцион
ная, контактная), в печах, ультразвуковую.
В индивидуальном и мелкосерийном производствах распро
странены способы пайки с местным нагревом посредством паяль
ника или газовой горелки; в крупносерийном и массовом произ
водствах сборочные единицы при пайке нагревают в ваннах и газо
вых печах, а также широко применяют электронагрев. Особенно широко используется индукционный нагрев ТВЧ.
Форму индуктора приспособляют к форме соединяемых деталей,
вследствие чего нагрев сосредоточивается непосредственно вблизи
места спая. Это предохраняет детали от коробления и окисления.
При пайке нагревом ТВЧ можно одновременно с одного нагрэва
закаливать детали, осуществлять групповой нагрев одноименных
узлов. Мощность применяемых при пайке высокочастотных гене
раторов 5—40 кВт. Процесс пайки нагревом ТВЧ можно в значи
тельной степени механизировать.
Перспективным направлением развития технологии пайки
металлов и неметаллических материалов является использование
ультразвука. Оборудование в этом случае состоит из генератора
ультразвуковой частоты и электропаяльника с ультразвуковым
магнитострикционным вибратором или из ванны с расплавленным
припоем, в котором возбуждаются преобразователем колебания
ультразвуковой частоты (около 20 ООО Гц). Особенно удобен этот
способ пайки деталей из алюминия и алюминиевых сплавов, так
как высокочастотные колебания в расплавленном припое разру
шают оксидную пленку и отпадает необходимость во флюсе. Детали для пайки должны быть тщательно подготовлены.
Места под спай необходимо осмотреть и при наличии коррозии
зачистить, а затем промыть и обезжирить. Особое внимание следует обратить на зазор между сопрягае
мыми поверхностями в соединении, предназначенном для пайки.
От величины этого зазора в связи с различными условиями капил
лярности зависит диффузионный обмен припоя с металлом деталей
и прочность соединений .
Припой должен быть зафиксирован относительно
места спая . Припои закладывают в месте спая в виде
фольговых прокладок, проволочных контуров, лент, дроби, паст
вместе с флюсом, а также наносят в расплавленном виде. В про
цессе автоматизированной пайки припой в виде пасты вносят с по
мощью шприц-установок в требуемых дозах.
Соединения необходимо пригнать таким образом, чтобы зазор
был одинаков по всему сечению .
Для лучшей капиллярности фаски закругления в месте спая
следует устранить . Собранное под пайку соедине
ние во избежание смещения деталей при нагреве должно быть на
дежно закреплено.
Для получения особо прочных соединений при толстых швах
находит распространение новый способ пайки с помощью волок
нисто-металлических сталемедных прослоек, помещаемых в месте
спая. Прослойки получают путем суспензирования коротких ме
таллических волокон в глицерине с последующей прессовкой и
прокаткой. В такой прослойке стальное волокно как бы армирует
слой меди (соотношение стали к меди от 1 : 1 до 1 : 2). Место спая
с помещенной прослойкой нагревают выше точки плавления при
поя; при этом образующиеся капилляры из металловолокна дают
возможность лучше заполнить пространство стыка. Волокна также
действуют как диффузионные каналы с большим отношением по
верхности к объему. На этом принципе основано получение и дру
гих видов припоев.
Пайка — трудоемкий процесс. Поэтому там, где это возможно,
на операциях пайки следует предусматривать различные средства
механизации. В настоящее время создан ряд полуавтоматов и авто
матов для газовой, электрической и других видов пайки.
Склеивание — один из способов получения неподвижных не
разъемных соединений деталей. В процессе склеивания между сопря
гаемыми поверхностями деталей вводится слой специального веще
ства, способного при определенном физическом состоянии, благо
даря проявлению сил адгезии, неподвижно скреплять эти детали.
Одним из важных преимуществ склеивания является возможность получения соединений из разнородных металлов и неметаллических материалов. Кроме того, в процессе склеи
вания можно в значительной мере избежать внутренних напряжений и деформаций детали, так как технология не требует повышенных температур. В конструкциях машин
клеевые соединения применяют либо как самостоятельные, либо в комбинации с другими видами соединений. Существенными недостатками клеевых соединений являются их сравнительно низкая термостойкость, склонность к старению, необходимость в ряде случаев нагревания соединения при склеивании. Существует большое разнообразие марок клеев. Они делятся на две группы: конструкционные, или жесткие, и неконструкционные, или эластичные. Конструкционные клеи применяют, когда
требуется высокая прочность (на сдвиг до 500—550 кгс/см2, на
отдир—до 25—27 кгс/см2). Неконструкционные клеи, основан
ные на эластомерах, менее прочны (на сдвиг до 50 кгс/см2,
на отдир — до 7 кгс/см2), но более дешевы. Кроме того, клеи под
разделяют на жидкие, пастообразные, пленочные и порошкообразные.
Заклепочные соединения в конструкциях машин и механизмов
вытесняются сварными, клеевыми и резьбовыми соединениями.
Особенно заметно вытесняется клепка в связи с успехами в разви
тии сварки. В некоторых машинах многие сборочные единицы,
подверженные большим динамическим нагрузкам, имеют закле
почные соединения. Заклепки используют также и в тех массовых
сборочных единицах, где сопрягаются плохо свариваемые друг
с другом материалы и стоимость крепления заклепками меньше
стоимости резьбовых деталей. Более распространены заклепки со сплошным
стержнем , трубчатые и полутрубчатые
; материал заклепок — сталь, медь, латунь и алюми
ниевые сплавы. При соединении деталей заклепками отверстия для них обычно
подготовляют заранее. Сверление отверстий под заклепки одно
временно в обеих деталях в процессе сборки применяют лишь
в тех случаях, когда требуется особо повышенная точность в'сов
падении отверстий.
Диаметральные зазоры в сопряжении стержня заклепки с ба
зовой деталью должны выдерживаться строго по чертежу, так как
от этого в значительной мере зависит возможность появления из
гиба стержня, смещения деталей, а при переменных нагрузках —■
быстрый износ и разрушение соединения. Величина этих зазоров
составляет примерно 0,2 мм для заклепок с диаметром стержня
до 6 мм, 0,25 мм — при 6—10 мм и 0,3 мм — при 10—18 мм. Для получения качественного заклепочного соединения боль
шое значение имеет выбор длины заклепки (выступающая часть
стержня при установке заклепки от 1,3 до 1,6 диаметра стержня,
в зависимости от формы головок). Прочность заклепочного соединения в значительной мере зави
сит от размеров и формы замыкающей головки. Если она сфери
ческая, то ее размер и форма определяются размером и формой
лунки соответствующей обжимки. Плоские замыкающие головки
заклепок контролируют по высоте и диаметру , а потайные — линейкой и щупом .
Технологическое оборудование сборочных цехов. Оборудование сборочных цехов, автоматизация и механизация сборочных процессов.
Оборудование сборочных цехов условно может быть разделено
на две группы: технологическое, предназначенное не
посредственно д тя выполнения работ по осуществлению подвижных
или неподвижных сопряжений деталей, их регулировке и кон
тролю в процессе узловой и общей сборки, «вспомогатель
ное, назначение которого — механизировать все виды вспомога
тельных работ, объем которых при сборке изделий весьма большой. Техническая характеристика необходимого для сборочных
работ подъемно-транспортного оборудования зависит от типа и
масштаба производства, вида организации процесса сборки, кон
структивных и технологических данных собираемых изделий.
Средства для сборочных тцехов:
1. Подъёмные: гидравлические и пневматические, гидро-пневматические домкраты;
электрические лебёдки; полиспасты; тали; электро-и пневмоподъёмники; подъёмники- кантователи и др. спец.устр-ва.
2.Подъёмно-транспортные: тельферы; кран-балки; мостовые краны; поворотные краны; передвижные напольные краны.
3.Транспортные:рольганги; тележки рельсовые и безрельсовые; конвейеры.
35%, зерновых комбайнов 25%.
При ручном перемещении собираемых изделий применяют роль
ганги, рельсовые и безрельсовые пути с тележками, а при меха
ническом перемещении — конвейеры.
Рольганги. Наиболее распространенные при сборке разно
видности рольгангов показаны на рис. 500. Собираемые сборочныеединицы или изделия либо опираются на роликовую поверхность
рольгангов непосредственно, либо устанавливаются на деревян
ные или металлические поддоны соответствующей формы. Горизонтальный рольганг устанавливают в сборочном цехе на высоте Н =
= 0,6- 0,8 м от пола, наклонные рольганги — с уклоном 2—4° в сторону движе
ния груза. Радиус закругления подковообразного или замкнутого рольганга
делают не менее 2,5—3,5 В, где В — ширина рольганга (от 200 до 1200 мм в за-
висимости от габаритов перемещаемого изделия или поддона). В месте прохода
рольганг имеет откидную секцию, а для подачи и снятия собранных изделий преду
сматривают поворотные или подъемные секции. Пригоночные операции при сборке изделий часто выносят из
потока на специальное рабочее место. В этом случае рольганг
оборудуют отводными участками. Изделия передают на эти участки
при помощи поворотных или подъемных секций, приводимых в дей
ствие пневмоцилиндрами .
Сборочные тележки. При поточной сборке часто используют
тележки, на которых закрепляют собираемые изделия; тележки
последовательно передвигают от одного рабочего места к другому
со скоростью 10—15 м/мин. На колеса тележки надевают литые
резиновые шины, вследствие чего ее можно перемещать по обыч
ному полу или же по накладкам, выполненным в виде полос из
котельного железа, уложенных по полу цеха.
При значительном весе изделий тележки снабжают колесами
с ребордами для движения по рельсам. Для удерживания таких
тележек в требуемом месте предусмотрен стопорный механизм.
Рельсы укладывают на бетонных подушках таким образом, чтобы
головка их была заподлицо с полом или несколько утоплена. Для
возврата тележек в исходное положение применяют вспомогатель
ный рельсовый путь .
Конвейеры сборочные ленточные применяют при сборке мел
ких сборочных единиц и изделий. Широкое распространение они получили в приборостроении. Эти конвейеры представляют собой
плоскую тканепрорезиненную ленту шириной 200—800 мм; рабо
чая часть ленты скользит по гладкому деревянному или металли
ческому столу, а холостая ветвь опирается на ролики. Скорость
Движения ленты 0,02—0,5 м/с. При сборке изделий на ленточном конвейере пользуются длинными узкими
верстаками (ширина 0,4—0,6 мм), расположенными вдоль линии сборки. Обычно
рабочие места располагаются в этом случае с двух сторон конвейера ,
Сборка легких, точных изделий на узких верстаках неудобна; в таких случаях,
применяют индивидуальные рабочие столы размером 0,6x1 м ,
установленные перпендикулярно линии сборки.
Для сборки малогабаритных сборочных единиц и изделий получают также
распространение горизонтально замкнутые толкающие конвейеры с программным
устройством для обеспечения заданного темпа работы и автоматического адресо
вания объектов сборки по рабочим местам, где создаются постоянные заделы
собираемых изделий. В ряде конструкций таких конвейеров предусмотрено
дублирование выполнения операций с количеством дублеров от 2 до 10.
I Конвейеры обычно располагают на участке сборки в одну ли
нию. При большом количестве сборочных операций и крупногаба
ритном изделии длина конвейера может быть слишком большой
для размеров цеха. В таких случаях линию конвейера делают Г-
или П-образной. На углах предусматривают поворотные круги
(рис. 510) с передаточным конвейером. Цикл работы таких кругов
автоматизируют.
Для сборки сборочных единиц при небольшом количестве
операций применяют карусельные конвейеры , представ
ляющие собой круглый вращающийся стол, по периметру которого
размещается от четырех до восьми рабочих мест. На специальной
неподвижной стойке при необходимости устанавливают требуемое
по технологии сборки сборочной единицы оборудование (пресс,
клепальную скобу и пр.) или подвешивают механизированный ин
струмент. Внутри корпуса стола помещается привод, состоящий
из электродвигателя, вариаторов и червячного редуктора. На
сборочном участке карусельные конвейеры размещают вблизи
главного конвейера с таким расчетом, чтобы сборочные единицы
непосредственно поступали на общую сборку изделий.
Для машин, имеющих ходовую часть (тракторы, автомобили
и др.), конвейер имеет специальные тележки лишь на том участке,
где монтируют ходовую часть. В дальнейшем собираемый объект
присоединяют непосредственно к цепи или тросу. После оконча
ния сборки изделия сходят с конвейера на своем ходу. Такие
конвейеры могут иметь одну или две параллельные тяговые цепи.
В приводных механизмах конвейеров обычно предусматривают ва
риаторы для изменения скорости передвижения от 0,1 до 5 м/мин.
Движение конвейера может совершаться непрерывно или периоди
чески со скоростью 4—5 м/мин с последующими остановками про
должительностью, равной темпу сборки.
Транспортные конвейеры. Для транспортирования деталей
и сборочных единиц, предназначенных для сборки изделий, а
также готовых изделий на испытательные станции или в окраску
применяют подвесные конвейеры . Трасса подвесного
конвейера пространственная, поэтому одним конвейером можно
•обслужить большое количество рабочих постов на сборке. Скорость
подвесных конвейеров до 25 м/мин.
Путь подвесного конвейера обычно выполняется в виде моно
рельса, прикрепленного к строительным конструкциям, по кото
рому движутся каретки, соединенные разборной блочной или
пластинчатой цепью , а в конвейерах небольшой
грузоподъемности (масса единичного груза — до 30 кг) — сталь
ным канатом, который в 4—6 раз легче цепи.
Каретки на конвейере чередуются — рабочие и холостые. Рабочая каретка
предназначена для крепления на ней груза, а холостая —для поддержки цепи.
К рабочей каретке прикрепляют крючки, захваты, лотки, этажерки или другие
виды подвесок, на которых размещают транспортируемые детали и сборочные
«диницы. Траверсное исполнение кареток предусматривает возможность под
вески тяжелых грузов одновременно на две каретки.
Сборочные стенды. Машины и крупные сборочные единицы
часто собирают на станках-стендах конструкция которых зависит
от формы, веса и размеров изделия, а также организации произ
водства. Если сборку производят без перемещения изделия, то
стенды делают с неподвижными основаниями. В случае же, когда
собираемые изделия должны в процессе сборки перемещаться,
стенды снабжают ходовой частью в виде гладких или ребордчатых
роликов. Стенды делают ориентируемые, что позволяет устанавли
вать собираемый объект в удобное для данной операции положе
ние.
Для стационарной сборки крупных сборочных единиц целесообразно при
менять стенды-постаменты, позволяющие менять положение собираемого объекта
. Если конструкция изделия дает возможность производить основные
сборочные работы только с одной стороны, то применяют сборочные стенды с бо
ковым креплением объекта сборки.
Подъемные устройства, применяемые при сборке. Важным
вспомогательным элементом операции является необходимое во
многих случаях перемещение объекта сборки в вертикальном на
правлении или поворот и закрепление собираемой сборочной еди
ницы либо изделия в удобном для сборщика положении. Механи
зация этих процессов дает значительную экономию затрат времени
на сборку, повышает производительность и облегчает труд сбор
щика. Электроталь ТЭ-0,25 представляет собой подъемный механизм
общего назначения грузоподъемностью 250 кг; высота подъема 6 м, скорость
подъема 8 м/мин. Электродвигатель тали мощностью 0,4 кВт. Для передвижения
по монорельсу к тали присоединяется электротягач. Поршневые подъемники различных типов имеют грузоподъ
емности 100—1000 кг при высоте подъема 1—2 м и скорости подъема 2,7—
5,4 м/мин. Эти подъемники часто подвешивают к каретке, перемещаемой по
монорельсу.
Применяют также разнообразные конструкции специальных
пневматических подъемников, предназначенных для выполнения
определенных работ на одном рабочем месте. Грузоподъемность их
до 500 кг . Для съема с конвейера собранных изделий среднего габаритного
размера удобно использовать двухплечевые консольные краны с
электролебедкой .
При выполнении стапельных работ широко применяют органи
зационно-техническую оснастку в виде подъемно-раз
движных стремянок, козелков с подъемно-винтовым устройством» передвижных помостов, подставок, лестниц и пр. Все виды этой
оснастки целесообразно иметь сбор но-разбор ной конструкции, из
нормализованных элементов.
Сборочные приспособления и инструмент. Оснастка и инструмент сборочных цехов.
В зависимости от возможных масштабов использования сбороч
ные приспособления могут быть разделены на универсальные
и специальные. Первые в отличие от вторых могут быть применены
на любой операции, которая соответствует функциям, выполняе
мым данным приспособлением или инструментом.
Универсальные приспособления применяют в сборочных про
цессах в мелкосерийном и единичном производствах. В крупно
серийном и особенно в массовом производстве они имеют сравни
тельно небольшое распространение.
Специальные приспособления, как правило, проектируют для
выполнения определенной операции с конкретным объектом сбор
ки, поэтому они могут быть использованы лишь на той сборочной
единице и той операции, для которых они предназначены.
По типу привода сборочные приспособления подразделяют на
механические, гидравлические, пневматические и пневмогидрав-
лические. Тип привода выбирают на основе технико-экономиче
ского расчета. В зависимости от назначения приспособления можно разделить на следу
ющие основные группы:
а) приспособления-зажимы, которые служат для закрепления
собираемых изделий, сборочных единиц или деталей в требуемом для сборки
положении, а также для придания устойчивости сборочной единице и облегчения
ее сборки;
б) установочные приспособления, предназначенные для
правильной и точной установки соединяемых деталей или сборочных единиц
относительно друг друга, что гарантирует получение требуемых монтажных
размеров;
в) рабочие приспособления, используемые при выполнении
отдельных операций технологического процесса сборки, например вальцевания,
запрессовки, постановки и снятия пружин и т. д.;
г) контрольные приспособления, изготовленные примени
тельно к конфигурации, формам, размерам и другим особенностям проверяемых
сопряжений сборочных единиц и изделий для контроля конструктивных пара
метров, получающихся в процессе сборки. Сборка крупных сборочных единиц — конструкций, а в ряде
случаев и общая сборка изделий осуществляется в приспособле
ниях, называемых стапелями. При сборке детали закрепляют
в массивных каркасах-стапелях, на которых и производят все
необходимые пригоночные и сборочные операции. Благодаря со
хранению постоянства конструкторских баз в самих стапелях
обеспечивается совпадение и единство баз сборочных единиц и в ре
зультате точная стыковка их между собой при общей сборке.
Различают разделочные и собственно сборочные стапели. Пер
вые предназначены для выполнения механической доработки
стыковых поверхностей и других элементов агрегатов, вторые —
для выполнения всех подготовительных операций и сборки сбо
рочных единиц (с применением клепки, крепления на болтах и пр.). Основные требования, предъявляемые к любому сборочному
приспособлению, состоят в том, чтобы его конструкция обеспечи
вала точность установки деталей или сборочной единицы, удоб
ство расположения собираемого объекта и простоту его закрепле
ния, возможность легкого снятия сборочкой единицы (изделия)
после сборки, безопасность в работе.
Большое значение для точности сборки имеет известный прин
цип определенности базирования деталей в приспособлении. Оп
ределенность характеризуется таким относительным положением
деталей в сборке, при котором процесс соединения осуществляется
в полном соответствии с технологией и достигается высокое каче
ство сборки, обусловленное техническими требованиями. При
соединении, например, валика и втулки сопряжение возможно
лишь в случае определенности базирования обеих деталей, при
котором смещение е осей не превышает наименьшей
величины зазора плюс удвоенная величина фаски валика. Наиболее удачный способ базирования деталей в приспособ
лении такой, когда конструкторскими базами являются поверх
ности сопряжения. В этом случае можно обеспечить минимальную
погрешность установки.
ПРИСПОСОБЛЕНИЯ-ЗАЖИМЫ ДЛЯ ЗАКРЕПЛЕНИЯ
ДЕТАЛЕЙ И СБОРОЧНЫХ ЕДИНИЦ ПРИ СБОРКЕ
К приспособлениям-зажимам предъявляют следующие основ
ные требования: крепление детали сборочной единицы в приспо
соблении должно быть достаточно надежным и прочным; зажатие
должно осуществляться немногими и простейшими приемами и
возможно быстрее; закрепление не должно деформировать детали
или вызывать повреждение их поверхностей; при необходимости
точной установки деталей зажимы не должны смещать их во время
закрепления. Очевидно, что сборка не может быть точной, если при зажа
тии или при выполнении операций деталь будет деформироваться.
Это может происходить, например, вследствие неправильного по
ложения детали или сборочной единицы или неудачного выбора
места зажатия, при недостаточном количестве опор, под действием слишком большой силы зажатия и т. п. Следует учитывать, что
нередко деформируются даже довольно массивные детали, в осо
бенности если зажатие производится вручную, бесконтрольно.
Поэтому пневматические или гидравлические зажимы, удержи
вающие детали с постоянным и необходимым давлением, имеют
значительное преимущество перед ручными.
Целесообразно широкое использование нормализованных одно- или двух
поршневых пневматических зажимов , создающих силу до 1000 кгс при диа
метре поршней 80 мм.
При необходимости включения в зажимные элементы силовых винтов для
их вращения следует применять механический привод с муфтами, ограничива
ющими крутящий момент. Универсальные приспособления для закрепления. На сбороч
ных участках многих производств распространенным видом зажим
ных приспособлений являются слесарные тиски. Преимущество
их заключается в том, что они в ряде случае делают излишним из
готовление специальных зажимных приспособлений, особенно
если используются сменные губки, которым придается любая
форма в зависимости от формы зажимаемой детали. Губки изготов
ляют из мягкой стали, латуни, меди, алюминия. Иногда их отли
вают из свинца.
Если конструктивные формы детали или сборочной единицы
не позволяют осуществить зажатие в тисках, последние нередко
используют для закрепления разнообразных оправок или спе
циальных зажимов, удерживающих собираемые узлы при выпол
нении сборочной операции.
Однако обычные слесарные тиски относятся к группе медленно
действующих приспособлений, и при большой расчлененности
процесса сборки вспомогательное время на зажатие и отжатие
может составлять значительную долю основного времени, затра
чиваемого на операцию. Поэтому следует применять быстродей
ствующие тиски. Существует много разнообразных конструкций таких тисков —
рычажные, эксцентриковые и др. Однако наиболее целесообраз
ными являются конструкции с пневматическим приводом. Время,
требуемое для зажатия, благодаря применению пневматического
зажима значительно сокращается. При использовании, например,
винтового зажима с гаечным ключом для закрепления требуется
4,9 с, эксцентрикового зажима — 1,6 с, а пневматического —
только 0,35 с. Преимущества пневматического зажима: обеспече
ние стабильности закрепления, легкость регулирования, силы за
жатия, освобождение рабочего от утомительных движений, что
способствует повышению производительности труда на сборке. В зависимости от конфигурации закрепляемых деталей и сборочных единиц
тиски оснащают специальными наладками. Удобны также нормализованные
пневматические зажимы с диафрагменными камерами и рычагом-прихватом
, создающие силу зажатия 250—300 кгс. К группе универсальных зажимных приспособлений следует
отнести также струбцины. Наиболее часто при сборке применяют
винтовые, эксцентриковые и пневматические струбцины. В ряде случаев в пневматических зажимных приспособлениях
целесообразно использование вакуума. Монтируемая сборочная
единица устанавливается в этом случае на плиту , в вы
точке которой посредством вакуумного насоса создается разреже
ние. Для уплотнения применяется резиновая прокладка-кольцо,
укладываемая в канавку соответствующей формы. При расчете
следует учитывать, что наибольшая удельная сила прижима не
превышает 0,8—0,85 кгс/см2.
Специальные приспособления для закрепления. Такие при
способления предназначены для закрепления одной детали, сбо
рочной единицы или же группы деталей, сборочных единиц опре
деленной формы. Хотя область применения каждого приспособле
ния ограничена, тем не менее простота конструкции делает ис
пользование их экономически оправданным. Специальные приспо
собления особенно широко применяются в крупносерийном и мас
совом производствах.
Эти приспособления бывают стационарные и передвижные.
В зависимости от размеров сборочных единиц их устанавливают
на верстаке или на полу и закрепляют винтовыми, эксцентрико
выми или пневматическими зажимами. Для базирования сбороч
ных единиц применяют призмы, конусные центры, плоские вы
ступы или кольцевые опоры, часто облицованные вкладышами
из мягких сплавов, фибры или кожи. Для удобства сборки многие приспособления допускают по
ворот собираемого изделия в горизонтальной или вертикальной
плоскости. Одно из таких приспособлений-кантователей, позво
ляющих поворачивать собираемое изделие (автомобильный дви
гатель) на 180° в обе стороны, показано на рис.
Если при сборке требуется точная фиксация сборочной еди
ницы, а также прочное закрепление во избежание смещения ее
под действием прилагаемых сил, в приспособлениях приме
няют пневматические зажимы с клиновыми или рычажными
усилителями. При конвейерной сборке приспособления для закрепления со
бираемых сборочных единиц устанавливают на тележках или пла
стинах конвейера. Однако при сборке мелких узлов на ленточном
или пластинчатом конвейере нередко используют приспособления-
спутники, которые вместе с узлом снимает сборщик для выполне
ния операции на верстаке, а затем опять возвращает на конвейер.
Зажимные элементы в таких приспособлениях механические бы
стродействующие (рычаги, эксцентрики, клинья).
Сборка передач основных агрегатов. Методы соединений, сварные и паяные соединения. Сборка зубчатых и червячных передач. Сборка подшипниковых узлов. Сборка цепных передач. Сборка ременных передач. Сборка передач с использованием шпоночных и шлицевых соединений. Балансировка деталей перед сборкой.
УСТАНОВКА ПОДШИПНИКОВ СКОЛЬЖЕНИЯ
В КОРПУСЕ
Последовательность установки подшипников скольжения
в корпусе зависит от конструкции подшипников, а также всей со
бираемой сборочной единицы. Подшипники скольжения могут
быть цельными и разъемными. В первом случае подшипник пред
ставляет собой втулку, изготовленную из антифрикционного
материала, запрессовываемую в корпус. Во втором случае под
шипник состоит из двух частей — вкладышей с диаметральным
разъемом.
Процесс установки втулки в корпусе включает ее запрессовку,
закрепление от провертывания и подгонку отверстия.
Запрессовку в зависимости от размеров втулки и натяга в сопря
жении производят при обычной температуре, с нагревом или же
с охлаждением самой втулки.
Простейший способ запрессовки втулки в корпус ■— при по
мощи обычной универсальной выколотки и молотка. Этот способ,
широко распространенный в индивидуальном и мелкосерийном
производстве, дает удовлетворительные результаты лишь при ма
лых натягах в сопряжении, относительно большой толщине сте
нок втулки и при тщательном выполнении операции. Направле
ние движения при запрессовке создается здесь только отверстием
в корпусе, поэтому большое значение имеет правильная первона
чальная установка втулки, предотвращающая ее перекос, дефор
мацию и задир поверхности корпуса.
Операция запрессовки значительно упрощается применением
несложных приспособлений (рис. 258), которые обеспечивают
втулке направление и предотвращают ее перекашивание. Однако
диаметр втулки при этом способе запрессовки уменьшается, воз
можно также искажение ее формы. Поэтому при относительно
больших натягах, во избежание перекосов и сдавливания втулок
(особенно при монтаже тонкостенных втулок), их при запрессовке
необходимо более точно центрировать относительно отверстия
в корпусе.
Направление для запрессовки создается утолщен
ной цилиндрической частью самой оправки, на которой центри
руется и втулка. Усилие запрессовки передается через накладку, навинченную на хвостовик оправки. Такие оправки применяют
при сборке в крупносерийном и массовом производствах. Каждая
из них может быть применена только для запрессовки определен
ной втулки.
Существенным недостатком такой оправки является неудобство
ее применения при запрессовке коротких втулок, так как в этом
случае длина направляющей части оправки должна быть ограни
чена размерами посадочного отверстия, а при короткой направля
ющей части возможны перекосы самой оправки. Чтобы избежать
этого, целесообразно пользоваться приспособлением с направляю
щим стержнем (рис. 259, а и б).
Втулку надевают на шлифованную цилиндрическую часть
оправки 1. Оправка хорошо центрируется в стойке или на стержне
2. При давлении штока ^пресса 4 или при вращении гайки 3
оправка 1, перемещаясь вместе со втулкой 5, запрессовывает ее
в отверстие корпуса 6.
Основными условиями, от которых зависит нормальная работа
подшипников многоопорного вала, являются точность геометри
ческих размеров втулки и цапфы вала, соосность подшипников и
состояние поверхностей скольжения.
Из теории смазки известно, что допускаемая удельная нагрузка
на цапфе вала может быть тем больше, чем тоньше масляный слой
в подшипнике. Толщина же масляного слоя зависит от состояния
подшипников и может быть тем меньше, чем тщательнее обрабо
таны и собраны цапфа и втулка.
Если хорошо обработанная втулка при сборке деформируется
и получит овальную (рис. 264, а) или коническую (рис. 264, б)
форму, а также если она будет установлена с перекосом (рис. 264, в)
или будет повреждена ее рабочая поверхность (рис. 264, г), то
вследствие этих неточностей в подшипниках возможно местное
сухое трение. Если же требуемая минимальная толщина масляного
слоя будет выдержана в наиболее неблагоприятных точках, то
в других зонах контакта толщина слоя масла будет больше и не
сущая способность подшипника сократится, он будет работать
ненормально и быстрее износится. Поэтому после сборки следует
тщательно проверить состояние рабочей поверхности и форму за
прессованной втулки, не допуская указанных дефектов, а также
царапин, трещин, отслаивания антифрикционного слоя и других
погрешностей.
Овальность отверстия запрессованной втулки обнаруживают
путем промера диаметров отверстия индикаторным нутромером
(рис. 265) в двух взаимно перпендикулярных направлениях
в двух-трех поясах. Таким же способом может быть обнаружена
конусность.
В крупносерийном и массовом производствах такой контроль
осуществляется с помощью пневматических калибров (рис. 266),
выполненных в виде пробок 1 с соплами 2, имеющими отверстия
диаметром 1,4—1,5 мм.
Перпендикулярность оси отверстия запрессованной втулки
торцу корпуса можно обнаружить проверкой по схемам, приве
денным на рис. 267. Если ось отверстия неперпендикулярна торцу
корпуса, то между торцовой плоскостью сборочной единицы и
угольником измерительного устройства (рис. 267, а) или краем буртика калибра (рис. 267, б) будет зазор, измеряемый щупом.
Отклонение от перпендикулярности можно также обнаружить
на краску (рис. 267, в), причем буртик калибра 2 и кольцо 1 дают
возможность проверить на краску одновременно два торца.
Более точную проверку перпендикулярности оси торцу можно
выполнить контрольным приспособлением с индикатором
(рис. 268, а). Повреждение рабочей поверхности втулки (выпучивание, вмя
тины, риски и пр.) может быть обнаружено ее осмотром и проме
ром. При установлении поверхностных дефектов запрессованную
втулку, как уже отмечалось, дополнительно обрабатывают.
Процесс сборки сборочных единиц с разъемными подшипниками
скольжения в значительной мере определяется их конструкцией.
Разъемные подшипники (рис. 270) могут быть толстостенные и
тонкостенные. Однако, пользуясь таким условным делением, сле-
дует^иметь_в виду, что главным критерием отнесения подшипника
к тому или иному типу является не абсолютное значение толщины
его стенки, а отношение k толщины стенки (без заливки) к наруж
ному диаметру. Для толстостенных подшипников k = 0,065 -0,095, а для
тонкостенных k = 0,025-045.
Комплект разъемных подшипников состоит из двух деталей-
вкладышей. Во многих конструкциях нарушение этой комплек
тации не допускается.
Вкладыши толстостенных подшипников изготовляют из мало
углеродистой стали, чугуна или бронзы и заливают баббитом илидругим антифрикционным сплавом. Толщина слоя баобита 0,Old +
+ (0,5 -г-2) мм, где d — диаметр отверстия подшипника.
Вкладыши устанавливают в корпус и в крышку с небольшим
натягом или со скользящей посадкой. При монтаже вкладышей
в постели деревянную или алюминиевую планку накладывают на
обе плоскости вкладыша и по ней наносят легкие удары.
Для предотвращения перемещения вкладышей применяют уста
новочные штифты (рис. 271, 272). Их запрессовывают в .корпус при
помощи пресса или выколотки и молотка. Посадку штифтов в кор
пусе (б) осуществляют с натягом 0,04—0,07 мм. Вкладыш должен
устанавливаться на штифт с зазором а = 0,1 0,3 мм. Кроме того,
в одной из половин вкладышей отверстие под штифт в плоскости
возможного вращения подшипника должно иметь несколько вытя
нутую форму, чтобы при перекосе плоскостей разъема вкладыш
мог самоустанавливаться.
Перед установкой вкладышей в корпус и крышку все сопря
гаемые поверхности должны быть просмотрены, а при наличии
на них заусенцев зачищены шабером. Необходимо также прове
рить совпадение масляных каналов в корпусе и в крышке с отвер
стиями во вкладышах. Несовпадение этих отверстий на величину,
превышающую 0,2 их диаметра, не допускается. Масляные каналы
в корпусе перед установкой вкладышей должны быть тщательно
промыты керосином при помощи шприца. В единичном производстве после подгонки вкладышей по месту на них должны быть нанесены метки.
Крышки подшипников, как правило, фиксируют штифтами (рис. 273, а), па зами (см. рис. 272, 273, б), шипами(рис. 273, е) или на точно пригнанных болтах (рис. 273, г). Штифты запрессо вывают в корпусе с натягом 0,03—0,07 мм. Посадка крышки в пазах может
быть с небольшим зазором или натягом. гом. При фиксации на шипе натяг может быть двусторонний, т.е по обеим плоскостям шипа, или односторонний, т. е. когда с одной стороны
шипа допускается зазор, а с другой — натяг. Для получения од
нородности посадки (в крупносерийном и массовом производст
вах) крышки сортируют по посадочному размеру на две-три
группы.
Крышки подшипников при установке надевают на две или четыре шпильки.
Установка крышек производится легкими ударами деревянного или пластмассо
вого молотка. Возможны перекосы крышек на шпильках и искривления их.
Этого нужно избежать. Целесообразно применять специальное приспособление
в виде груза 1, перемещающегося по стержню 2 (рис. 274). В процессе сборки, подшипниковых сборочных единиц крышки
приходится демонтировать. Для съема крышек следует применять
пневматические или пневмогидравлические съемники одиночного
или группового действия . Как уже отмечалось, тол стостенные вкладыши можно
пригонять в процессе сборки по месту или они могут быть вза имозаменяемыми.
единиц после сборки. ;
Тонкостенные вкладыши (рис. 278) изготовляют из малоугле
родистой стали и заливают изнутри слоем антифрикционного
сплава. Распространены сталебаббитовые и сталебронзовые вкла-;
дыши, получаемые заливкой свинцовистой бронзы в стальную
трубу, а также сталеалюминиевые биметаллические, изготовлен
ные из полосы. В быстроходных автомобильных двигателях ис
пользуют триметаллические вкладыши со стальным основанием,
металлокерамическим или медно-никелевым подслоем и баббито
вой заливкой. В зарубежной практике распространены биметал
лические вкладыши, имеющие стальное основание и антифрикцион
ный слой из спеченной свинцовистой бронзы. Эти вкладыши про
сты в изготовлении и значительно дешевле, чем со свинцовистой
бронзой. Для рационального использования материалов в некото
рых тяжело нагруженных сборочных единицах верхний и нижний
вкладыши имеют различную заливку: более нагруженный вкла
дыш — из стали со свинцовистой бронзой, а парный с ним — из
стали с оловянистым баббитом.
Тонкостенные подшипники взаимозаменяемы, но верхний и
нижний вкладыши образуют комплект. Замена в комплекте одного
из вкладышей обычно не допускается. В крупносерийном и массовом производствах после механи
ческой обработки вкладышей и гнезд для них особой подгонки сопрягаемых поверхностей друг к другу не требуется. Иногда
лишь подбирают вкладыши на прилегание их в постелях по краске.
При хорошем подборе отпечатки краски на стыках корпуса и вкла
дышей, а также в постелях располагаются равномерно и примерно
везде одинаковы.
Плотное и равномерное прилегание вкладыша к корпусу имеет
большое значение для обеспечения нормальной работы подшип
ника. При недостаточно плотном прилегании в процессе эксплуа
тации возможно ослабление посадки и провертывание вкладышей
в постели. Причинами неравномерного прилегания являются мест
ные вмятины на сопрягаемых поверхностях, конусность и оваль
ность постелей, непараллельность торцовых поверхностей стыка
образующим наружной поверхности вкладышей, чрезмерная ше
роховатость поверхностей сопряжения постелей.
Следует предохранять вкладыши от коррозии, возникающей
в результате соприкосновения с их рабочими поверхностями пот
ных рук. С этой целью при сборке целесообразно применять хлоп
чатобумажные перчатки или смазывать руки специальной эмуль
гирующей смазкой. Большое значение для обеспечения нормальной работы под
шипников при многоопорном вале имеет их соосность. Соосность подшипников можно проверить макетным валом
(рис. 281, а), который вставляется внутрь смонтированных втулок.
При совпадении осей всех отверстий втулок этот вал, очевидно,
может быть введен в эти отверстия свободно. Невозможность такой
установки вала указывает на перекос или на смещение осей под
шипников. Диаметр макетного вала должен быть меньше мини мального диаметра отверстия подшипников на двойную величину
допускаемой несоосности. Вначале под макетный вал в каждом
подшипнике подкладывают полоски тонкой бумаги. Они должны
хорошо зажиматься. Слабее зажатие полоски свидетельствует о на
рушении соосности. После такой предварительной проверки ма
кетный вал равномерно покрывают тонким слоем краски и контро
лируют соосность по ее отпечаткам на вкладышах. Проверку соосности производят также оптическими методами
с помощью телескопа и коллиматора (рис. 285, б) или посредством
автоколлиматора и зеркала, которые обеспечивают большую точ
ность, чем контроль струной.
Подшипники качения монтируют в сборочной единице по
двум неподвижным посадкам — внутреннего кольца с валом и
наружного кольца с корпусом — обычно без специальных креп
лений, препятствующих проворачиванию.
Напрессовка подшипника качения на вал или установка его
с натягом в отверстие корпуса вызывают деформацию колец:
диаметр внутреннего кольца увеличивается, а наружного уменьшается.
В связи с этим диаметральный зазор (рис. 309) между поверхностями качения и
уменьшается . Уменьшение радиального зазора в подшипнике может про
изойти также при неодинаковом нагреве его колец, что следует
тоже учитывать при сборке. В частности, если внутреннее кольцо
подшипника по условиям работы сборочной единицы в машине
может нагреваться на t⁰ больше, чем наружное, то это вызовет
уменьшение зазора на величину 0,11- lO-4D1t
Таким образом, если оба кольца подшипника смонтировать
с натягом, то вследствие расширения внутреннего и сжатия на
ружного колец шарики или ролики могут быть защемлены, так
как радиальный зазор между ними и кольцами до установки под
шипника чрезвычайно мал (для подшипника среднего размера
и точности зазор в пределах 5—25 мкм).
Поэтому характер обеих посадок, как правило, различный. Кроме того, внутреннее и наружное кольца подшипника, находя
щиеся под действием постоянной радиальной нагрузки, работают
в разных условиях. Так как одно из колец подвижно, то износ
его желобка происходит равномерно. Неподвижное же кольцо
воспринимает действие нагрузки все время одним и тем же неболь
шим участком желобка, который интенсивно изнашивается. Для
уменьшения этого износа желательно, чтобы при сборке в сочле
нении неподвижного кольца с корпусом или валом была достигнута
посадка, позволяющая этому кольцу незначительно поворачива
ться. Иными словами, при постоянно действующей нагрузке вра
щающееся кольцо подшипника должно быть сочленено с деталью
сборочной единицы, безусловно, неподвижно, кольцо же невра-
щающееся должно получить более слабую посадку, дающую
возможность проворачивать его от руки в ненагруженном со
стоянии.
Если нагрузка при вращении меняет направление, выбор
посадок представляет несколько большие затруднения. Здесь
при назначении переходных посадок возможны небольшие зазоры.
Величину зазоров при сборке сборочных единиц необходимо со
блюдать особенно строго. Даже при незначительном увеличении
зазора между вращающимся валом и установленным на нем коль
цом подшипника при переменных нагрузках происходит качение
вала по кольцу — своеобразный процесс вальцевания, нередко
являющийся причиной быстрого износа вала. снижает его надежность.
Во многих машинах используют подшипники качения, имеющие
встроенное армированное резиновое уплотнение. Смазка в такие
подшипники закладывается один раз при их установке, и этого
достаточно на весь срок их работы. Так как кольца подшипников име ют малую жесткость, очень важно при сборке не допустить их перекоса. По этому, устанавливая подшипники на валу или в кор пусе , следует ис пользовать торцы колец как базы, до биваться плотного контакта колец с буртиками вала, корпуса или про межуточной детали. Для осуществления надежного сопряжения подшипника с ва
лом и корпусом посадочные места должны быть обработаны
(быть чистыми, гладкими, без рисок, задиров и коррозионных
пятен). Шероховатость посадочных поверхностей для высоко
точных подшипников должна соответствовать Ra = 1,25-4-0,32 мкм,
для менее точных Rz = 20 мкм, Ra = 1,25 мкм, а торцов заплечи
ков валов и корпусов Rz = 20 мкм, Ra = 1,25 мкм.
Допустимые отклонения от правильной геометрической формы
мест посадки шарико- и роликоподшипников на валах и в корпу сах следующие: овальность и конусность — не более 0,5 допуска
на диаметр, а для точных подшипников классов А и С — не более
0,25 допуска; биение заплечика для подшипников нормальной и
повышенной точности 0,02—0,03 мм на валу и 0,04—0,07 мм
в отверстии корпуса.
Контроль производится индикатором или миниметром.
Сборку сборочной единицы вал — подшипник качения осуще
ствляют следующим образом. Подшипник тщательно промывают
в 6%-ном растворе масла, в бензине или в горячих (75—85°С)
антикоррозионных водных растворах. В хорошо промытом подшипнике наружное кольцо легко и
равномерно вращается. Проверку ведут, удерживая подшипник
за внутреннее кольцо в горизонтальном положении.
Далее, промытый подшипник нагревают в масляной ванне в те
чение 15—20 мин и после этого напрессовывают на вал. Если
в холодном состоянии разность между внутренним диаметром
кольца подшипника и диаметром вала, соответствующая натягу
посадки, была Δ, то после нагрева подшипника этот натяг умень
шиться на величину dКαt, где d — внутренний диаметр кольца
подшипника, К α— коэффициент линейного расширения, равный
для стали 11·10-6, и t — температура подогрева подшипника.
Необходимо, чтобы Δ≤ dКαt ,откуда t≥Δ/dКα
Обычно температура нагрева подшипников при сборке назна
чается в пределах 60—100° С. Подшипники целесообразно нагре
вать в электрованне с точным контролем температуры масла.
Нагретый подшипник устанавливают на вал и доводят до места
небольшим осевым усилием. При этом сторона подшипника, на
которой нанесено заводское клеймо, должна быть снаружи.
Операцию напрессовки необходимо обязательно осуществлять
с применением оправок. Наносить удары непосредственно по
подшипнику нельзя, так как при этом могут быть повреждены
кольца, поломаны шарики и т. д.
Осевые силы, требуемые для установки подшипников каче
ния, должны прикладываться только к тому кольцу, которое
при данной операции сопрягается с базовой деталью . Если подшипник одновременно монтируется на вал и в кор пус, то усилия передаются на торцы обоих колец .
Во избежание перекоса подшипника при его запрессовке
целесообразно применять подставки, обеспечивающие хорошее
базирование деталей сборочной единицы . Если вал имеет небольшую длину и малую массу, напрессовы вать подшипник можно, прикладывая осевые усилия к валу
. Чтобы не повредить торец, его закрывают спе циальной накладкой 1\ подшипник упирается в кольцо 2. Этот способ неприменим, если напрессовка ведется ударами и вал
имеет большую массу или малую жесткость: при большой массе энергия удара будет поглощаться валом, в случае же недостаточной жесткости может получиться продольный изгиб его. После напрессовки подшипника на вал следует убедиться в том,
что шарики его не защемлены. Наружное кольцо должно вращаться
равномерно, без заедания, с незначительным шумом. Проверяют
также плотность соприкосновения торца кольца с буртиком или
заплечиком (рис. 318, а). Плотность прилегания к заплечику,
как уже отмечалось, имеет большое значение для нормальной ра
боты кольца. Однако очень важно, чтобы торец заплечика был перпендикулярен к оси посадочной шейки вала. При значительном перекосе заплечика в процессе напрессовки возникают реактивные силы , вызывающие дополнительные напряжения в кольце.
Получаемые при контроле зазоры являются условными, так
как их численное значение определяется не только размерами
элементов, но и величиной контактных деформаций, зависящей
от измерительного усилия, а также способом измерения и харак
тером закрепления сборочной единицы при проверке. Поэтому
в технологии сборки конкретной сборочной единицы следует спе
циально указывать, какой должен применяться метод контроля
зазоров.
Установку подшипника в корпусе, если его наружное кольцо
запрессовывают в отверстие, производят так же, как и монтаж
подшипника на валу, только нагревают при этом корпус или охлаждают подшипник. Для охлаждения обычно используют
сухой лед. Сборку производят с помощью специальных оправок
и приспособлений для запрессовки, обеспечивающих удобную
установку и закрепление собираемой сборочной единицы
(рис. 320). Поэтому в значительной мере устраняется возможность
появления брака из-за перекосов при запрессовке и ускоряется
процесс сборки.
Для запрессовки подшипника качения в корпус требуются
сравнительно небольшие силы. Подшипники с внешним диаметром
наружного кольца 80—130 мм запрессовывают силой 400—450 кгс.
Однако при плохом центрировании и даже незначительных пере
косах подшипника сила, необходимая для запрессовки, возрастает
в несколько раз. В связи с этим к конструкции приспособления
предъявляются жесткие требования в части обеспечения базиро
вания подшипника при его установке (см. рис. 33).
Крупногабаритные подшипники качения, устанавливаемые
в разъемные корпуса, часто проверяют на прилегание наружного
кольца к посадочной поверхности по краске. Прилегание счита
ется хорошим, если отпечатки краски составляют не менее 75% площади поверхности. При плохом прилегании возможно пришабри вание посадочных мест. В местах разъема отверстие в корпусе рас шабривают для предот вращения сжатия кольца подшип ника. Для подшипников диамет ром 120—260 мм а = 0,15 мм(толщина); b — 15 мм(высота). Если габаритные размеры и масса сборочной единицы позво ляют выполнять операции по установке подшипников качения на прессе, то эту возможность целесообразно использовать в тех нологии, предусмотрев соответствующую оснастку, обеспечива
ющую необходимое качество сборки. Перекосы нарушают нормальную работу подшипника, при этом
дорожки качения смещаются, шарики при их движении получают
переменную скорость, создаются дополнительные давления на
гнезда сепаратора, они сминаются, и перекашивается весь сепа
ратор. Нередко это является причиной разрушения сепаратора
и заклинивания шариков его обломками. Перекос может также
вызвать защемление тел качения, резкое повышение удельных
давлений и, как следствие, быстрый износ подшипника. Контроль
соосности отверстий под подшипники производят методами, из
ложенными выше. Для определения биения внутреннего и наружного колец
подшипника пользуются индикаторными приспособлениями, по
казанными на рис. 331. Положение наибольшего эксцентриситета
колец отмечается тонкой риской, наносимой электрографом или
краской.
В конструкциях машин и механизмов наиболее широко распространены зубчатые передачи со следующими видами колес:
цилиндрическими — прямозубыми, косозубыми, шевронными, вин товыми и коническими — с прямыми, криволинейными и косыми
зубьями. Червячные передачи применяют с цилиндрическим (ар
химедовым) и глобоидными червяками.
Для зубчатых цилиндрических и конических передач, а также
червячных передач государственными стандартами устанавливает
ся двенадцать ^степеней точности, обозначаемых в порядке убыва
ния точности степенями 1—12. Для каждой степени точности зубчатых передач государствен
ным стандартом установлены нормы: кинематической точности ко
леса, плавности^работы_колеса_и контакта зубьев. Нормы кинема
тической точности определяют полную погрешность угла поворота
зубчатых колес за оборот.
Нормы плавности работы колеса определяют величину состав
ляющих полной погрешности угла_поворота зубчатого колеса.
Нормы контакта зубьев определяют точность соблюдения отно
сительных размеров пятна контакта сопряженных зубьев колес
в передаче. Независимо от степени точности колес и передач
устанавливают нормы бокового зазора.
Основными являются величины минимального гарантирован
ного бокового зазора (при сопряжении В), обеспечивающего ком
пенсацию уменьшения бокового зазора от нагрева передачи при
разности температур зубчатой передачи и корпуса 25° и равенстве
коэффициентов линейного расширения. Нормы гарантированного
бокового зазора можно изменять. ГГри_изменении этих норм пред
почтительно применять одно из следующих сопряжений: Я — с ну
левым гарантированным зазором, Е, Д — с уменьшенным гаран
тированным зазором, А — с увеличенным гарантированным за
зором.
Важным фактором, определяющим эксплуатационное качество
зубчатой передачи, является боковой зазор между зубьями колес.
Боковой зазор измеряется для цилиндрических колес в сечении,
перпендикулярном к направлению зубьев, в плоскости, касатель
ной к основным цилиндрам, для конических — по нормали к по
верхностям зубьев у большего основания делительного конуса.
Зазор в зацеплении является необходимым для компенсации
возможных ошибок в размерах зубьев, неточности расстояния ме
жду осями зубчатых колес, изменения размеров и формы зубьев
при нагреве в процессе работы передачи. Но вместе с этим зазор
является причиной возникновения ударов и дополнительного из
носа зубьев при работе зубчатых колес, а также причиной появле
ния в передаче так называемого мертвого хода, когда отклонение
на некоторый угол ведущего зубчатого колеса не вызывает пово
рота ведомого. Таким образом, зазор в зацеплении должен быть
таким, чтобы при работе передачи не произошло заклинивания
зубьев, не нарушилась плавность вращения и в то же время мерт
вый ход был возможно меньше.
При сборке зубчатых передач выполняют следующие работы:
а) установку зубчатого или червячного колеса на валу; б) уста
новку валов с колесами в корпусе; в) сборку сборочной единицы
червяка и установку его в корпус; г) регулирование зацепления. Поступающие на сборку зубчатые и червячные колеса, а также
червяки и другие детали передач должны быть полностью обрабо
таны, промыты и высушены. На рабочих поверхностях зубьев ко
леса или червяка, предназначенного для точных и тяжело нагру
женных передач, не должно. быть заусенцев, забоин, задиров,
царапин и других погрешностей. Установку колес производят посредством пресса или же вруч
ную при помощи специальной мягкой оправки и молотка. Послед
ний способ применяют в мелкосерийном производстве лишь для
зубчатых колес малого размера, термически не обработанных,
монтируемых с небольшими натягами. Зубчатые колеса большого
размера, термически обработанные, а также устанавливаемые со
значительными натягами, следует непрессовывать только посред
ством пресса, с применением специальных приспособлений.
При больших диаметрах зубчатых колес целесообразно при
, напрессовке применять приспособления с направляющими план
ками или стержнями. В таком приспособлении (рис. 391) зубчатое
колесо устанавливают или укрепляют на упорной доске 1, кото
рая движется по направляющим стержням 2. В результате этого
осуществляют точное центрирование колеса при запрессовке,
особенно в начале ее.
В ряде случаев воспользоваться универсальными прессами
не представляется возможным, например при установке зубчатых
колес на длинных валах. Тогда целесообразно для напрессовки
применить специальные несложные установки, имеющие привод
от пневматической сети, насосных станций или пневмогидравли-
ческих устройств. Необходимо предотвращать перекосы зубчатых колес не только в
процессе монтажа, ной при их снятии с валов. Эти операции часто
приходится осуществлять в процессе сборки, когда возникает не
обходимость повернуть колесо относительно вала или устранить
какую-либо другую погрешность. Снимают зубчатые колеса с вала
также с помощью пресса или съемниками. При использовании
пресса колесо обычно опирают на его торцовую плоскость, а цен
трирование обеспечивается по наружной цилиндрической поверх
ности зубьев или тремя бобышками, входящими во впадины между
ними.
Следует иметь в виду, что при посадке с большими натягами
недостаточно жестких колес нередко получается искажение зуб
чатого профиля, что отражается на работе зацепления. В таких
случаях зубчатые колеса устанавливают на вал с весьма неболь
шим натягом или даже зазором (от —0,03 до +0,04 мм для валов
диаметром до 100 мм).
При установке на шлицевой вал несимметричных прямозубых
колес возможен их перекос вследствие зазоров в шлицевом соеди
нении. Тогда под действием крутящего момента при работе пере
дачи возникают дополнительные осевые силы, сдвигающие колесо.
Вследствие этого в сопряжении ступицы колеса со шлицами вала
следует выдерживать минимальные зазоры.
Перед напрессовкой зубчатого колеса на вал необходимо обра
тить внимание на состояние поверхностей отверстия и посадочной
шейки вала. Если зубчатое колесо напрессовывается до упора, то
фаска на зубчатом колесе должна быть достаточной величины во
избежание упора торца его в переднюю поверхность вала.
При напрессовке зубчатых колес возможны следующие погреш
ности: искажение профиля зубчатого венца, качание зубчатых
колес на шейке вала (рис. 393, а), радиальное смещение колеса за счет зазора посадки на вал или биения шейки вала (рис. 393, б),
перекос колеса на валу (рис. 393, в), неплотное прилегание к упор
ному буртику вала (рис. 393, в и г), перекосы в шпоночных соеди
нениях (рис. 393, д).
Иногда зубчатые колеса имеют зубья разной толщины, причем
в некоторых случаях самый тонкий и самый толстый зубья (в пре
делах допуска на толщину) располагаются один против другого,
т. е. через 180°, а все остальные зубья имеют постепенно изменя
ющуюся толщину. Этот дефект (неравномерная толщина зубьев)
по внешним признакам похож на дефект при смещении оси отвер
стия зубчатого колеса, но не аналогичен ему. Ось отверстия может
быть смещена и при совершенно одинаковой толщине всех зубьев.
Проверка колеса на качание производится обстукиванием
«мягким» металлическим молотком. Другие виды погрешностей
смонтированного на валу зубчатого колеса обнаруживают при
контроле сборочной единицы с помощью индикатора. После проверки сборочную единицу колеса необходимо еще
раз осмотреть, обращая внимание на состояние поверхностей и
кромок зубьев торцов (возможны забоины и крупные риски) и
креплений (затяжка гаек и винтов, а также их стопорение).
Следует иметь в виду, что перекос колеса, установленного на
шпонке (см. рис. 393, 5), при контроле сборочной единицы иногда
может быть не обнаружен. Но этот вид погрешности оказывает
существенное влияние на работоспособность сборочной единицы,
так как перекос шпонки или паза в ступице вызывает значитель
ные монтажные напряжения. Параллельность и отсутствие перекосов осей колес являются
важными факторами для обеспечения требуемой работоспособ
ности зубчатых передач. Перекос в зацеплении часто бывает ос
новной причиной обломов, сколов и выкрашивания зубьев и сни
жения долговечности 1 колес (рис. 401). Допустимые величины
отклонения параллельности fx (рис. 402) и перекоса fy осей отвер
стий при сборке зубчатых передач установлены государственным
стандартом. В стандарте (ГОСТ 1643—72) указаны предельные
величины отклонения от параллельности и перекосов осей в за
висимости от модуля на длине, равной ширине колеса (табл. 47).
Однако в практике нередки случаи, когда удовлетворительного
сцепления не получается вследствие допущенной где-либо ошибки
или в результате неблагоприятного суммирования отдельных от
клонений, каждое из которых находится в пределах допусков.
Сборщик в этом случае должен быстро найти причину неудовле
творительного сцепления и устранить ее. Укажем на наиболее
типичные случаи, встречающиеся в практике сборки.
1. Недостаточный зазор в зубьях по всему венцу. Наиболее
вероятные причины: а) все зубья на одном или обоих зубчатых
колесах выполнены большей толщины; в этом случае рекомендуется
испробовать другую пару зубчатых колес или передать зубчатые
колеса на проверку толщины зуба; б) расстояние между осями
зубчатых колес меньше (рис. 404, е) допустимого (рис. 404, а);
эту погрешность можно установить только соответствующими из
мерениями, а устранить — перепрессовкой втулок корпуса и пра
вильным их растачиванием.
2. Зазор по всему венцу велик. Причины: а) зубья на одном
или обоих зубчатых колесах тоньше, чем предусмотрено чертежом;
б) расстояние между осями зубчатых колес увеличено (рис. 404, б)\
устранение причин аналогично предыдущему.
3. Неравномерный зазор в зубьях. В этом случае рекомендуется
найти на глаз|наихудшее'положение (допустим, наименьший за
зор), после чего расцепить зубчатые колеса, одно из них повер
нуть на 180° и снова сцепить. Если после этого характер сцепле ния остается прежним, то причиной дефекта являются погреш
ности изготовления второго зубчатого колеса. Если же зазор,
имевший до перестановки минимальную величину, стал макси
мальным, то причина неточности сборки — первое колесо, кото
рое и нужно заменить. Погрешностями зацепления могут быть
неравномерная толщина зубьев, а также эксцентричное располо
жение зубчатого венца или втулки колеса относительно его оси
вращения; точно установить причину можно лишь после соответ
ствующих измерений колеса.
4. Зубчатое колесо перекошено и при зацеплении заметно бие
ние торцов зубьев. Такое колесо легко найти и проверить индика
тором; это —■ признак перекоса оси отверстия (или шейки) колеса.
Если же зуб колеса зацепляется неправильно (утоплен в направле
нии с торца) и при провертывании колеса на 180° положение не
меняется, то, очевидно, имеет место перекос оси гнезда зубчатого
колеса (в корпусе). Такую погрешность исправляют запрессовкой
новой втулки и ее растачиванием или перепрессовкой оси зубча
того колеса, если оно посажено на оси. При сборке крупных зуб чатых передач большого мо дуля зазор проверяют путем прокатывания между зубья ми свинцовых проволочек(трех-четырех), устанавливае мых по длине зуба. Диаметр проволочек берут равным (1,4-1,5)Сп. Каждую проволочку Волочку смазывают техническим вазелином и в виде П-образной скобки надевают на зуб. Толщину сплющенных частей проволо чек с обеих сторон зуба измеряют микрометром или индикато ром. В сумме это и дает боковой зазор Сп. Одновременно могут быть проконтролированы также отклонение от параллельности и перекос соей. Чтобы убедиться, что в зацеплении имеется зазор, иногда
между зубьями колес «прокатывают» полоску чистой писчей бу маги. Отсутствие разрывов на ней свидетельствует о наличии за зора. Плавность хода обычно определяют, провертывая собранный
механизм от руки, но лучше для этой цели употреблять динамо
метры, динамометрические ключи или специальные «упругие» ключи.
Если зазор в зацеплении не соответствует требованиям техни
ческих условий или же зубчатые колеса вращаются не плавно,
заклиниваясь при различных положениях, то сборочную единицу
разбирают, колеса притирают (в крупных передачах зубья нередко
шабрят) или подбирают новую пару и опять производят сборку.
Зацепления зубчатых колес проверяют также на краску (см.
рис. 404), причем действующим стандартом (ГОСТ 1643—72) уста
новлены нормы контакта парных колес в передаче. При вращении
меньшего колеса, зубья которого покрыты тонким слоем лазури,
на боковой поверхности зубьев парного колеса располагаются
следы прилегания, характеризуемые относительными размерами
контактного пятна по высоте и длине в процентах к соответствую
щим размерам зуба (за вычетом разрывов пятна).
Основной причиной неприлегания (неправильного пятна крас ки) зубьев по длине являются обычно отклонение от параллель ности и перекос осей отверстий в корпусе или те же погрешности
в сборочной единице зубчатое колесо — вал. Однако перекос ока
зывает намного большее влияние, чем отклонение от параллель
ности осей. Нарушение контакта зубьев по высоте — обычно ре
зультат неправильного их профиля.
После контроля на краску на зубья колес целесообразно нане
сти посредством пистолета-дозатора смазку. Вследствие этого
не будет сухого контакта зубьев в начале работы передачи.
Собранные быстроходные зубчатые передачи часто подвергают
обкатке на специальных установках с измерением передаваемых
крутящих моментов, в результате чего обеспечивается лучшая при
работка трущихся поверхностей, увеличение КПД передачи и
более правильное распределение нагрузки. Одновременно про
веряют правильность сборки агрегата^по нагреву его деталей
и шуму. ^
Уровень шума характеризует не только качество изготовления
зубчатых колес, но и в значительной мере взаимодействие многих
погрешностей, допущенных при сборке сборочной единицы. Рез
кий шум всегда является следствием серьезных неточностей изго
товления или сборки. Контроль на шум осуществляют в специальных камерах шумо-
мерами, улавливающими через микрофон звуки, которые потом
с помощью усилителя и гальванометра могут быть оценены по
шкале в децибелах. В настоящее время имеются конструкции
эффективных шумомеров, посредством которых на многих заводах
осуществляется окончательный контроль высокоскоростных зуб чатых передач.
Передача вращательного движения с одного вала на другой, параллельный ему вал, при больших межосевых расстояниях часто осуществляется в машинах и механизмах при помощи цеп ных передач.
В зависимости от назна чения в машиностроении при меняются^ цепи: пластинчато
зубчатые,% втулочные, вту лочно-роликовые, пластинча тые блочные со сплошными
звеньями и фасоннозвен ные. Пластинчато-зубчатые це пи, называемые иногда бес
шумными, применяют для передачи сравнительно боль ших мощностей при скоро
стях от 3 до 25 м/с. При ра боте цепь сопрягается со звездочкой, имеющей трапецеидальные зубья с углами впадин
от 32 до 57⁰ (при числах зубьев от 13 до 120).
Пластинчатые втулочно-роликовые цепи (однорядные и много
рядные) применяют для передачи движения при скоростях от 1
до 15 м/с. Фасоннозвенные цепи широко распространены в тихо
ходных передачах при скоростях до 3—4 м/с.
Втулочно-роликовые и фасоннозвенные цепи работают в сопря
жении со звездочками, профили зубьев которых очерчиваются
дугами окружностей.
Сборка цепной передачи состоит в установке и закреплении
звездочек на вал ах, надевании цепи и регулировании. Установку
звездочек на валах при обычном креплении с помощью шпонок
осуществляют так ж?, как и установку зубчатых колес. После
закрепления звездочки на валу ее следует проверить на радиаль
ное и торцовое биение.
Для правильной работьы цепной передачи оси звездочек должны
быть параллельны. Положение звездочек проверяют по уровню,
измерением межосевых расстояний и другими методами контроля
на параллельность осей валов . Отклонение от парал лельности осей'валов (звездочек) вызывает появление в передаче
дополнительной силы, сдвигающей звездочки. При этом наиболее
неблагоприятным является случай, когда оси обоих валов пере
кошены «внутрь» передачи.
Контролируется также относительное смещение i звездочек
при параллельных валах . Для устранения смещения конструкцией часто предусматри
вается возможность регулирования положения одной из звездочек
с последующим закреплением ее винтом. Для втулочно-роликовой цепи соединительное звено предста
вляет собой два валика, скрепленных пластинками (рис. 432, а).
Таким звеном можно соединить только цепь, имеющую четное
число звеньев. Для соединения концов цепи одну пластинку сни
мают, валики вставляют в отверстия втулок конечных звеньев,
затем устанавливают снятую ранее пластинку и валики зашплин-
товывают.
Если нужно собрать цепь с нечетным числом щагов, то вво
дится переходное звено (рис. 432, б). По такой же схеме при
помощи соединительных и переходных звеньев собирают пластин
чатые зубчатые цепи.
Концы втулочно-роликовой цепи соединяют либо на верстаке,
либо непосредственно на сборочной единице. На верстаке соби
рают цепи в том случае, когда звездочки расположены на концах
валов и цепь может быть на них надета после соединения ее кон
цов. Если же звездочки закрыты, то соединение концов цепи
производят на собираемом узле. При этом нередко по конструктив
ным условиям цепь предварительно должна быть установлена на
звездочки. В таких случаях концы цепи необходимо стягивать
при помощи специальных стяжек .
Пластинчатые зубчатые цепи также вначале надевают на звез
дочки, а затем стягивают стяжкой .
В ряде машин, например сельскохозяйственных, строительных,
дорожных, широкое применение находят фасоннозвенные цепи
. Их изготовляют из ковкого чугуна и собирают путем последовательного сочленения звеньев, без применения каких-либо крепящих устройств.
Надевать цепи на звездочки необходимо таким образом, чтобы
крючки звеньев были направлены в сторону движения цепи,
а не наоборот . Тогда звенья цепи при сбегании ее со
звездочки вращаются в шарнире крючка, а последний не трется
о поверхность зуба звездочки. Это уменьшает износ звена и звез
дочки.
Натяжение ветвей в правильно собранной цепной передаче
должно быть строго определенным. Недостаточное натяжение
ветви ухудшает ее набегание на ведомую звездочку, а излишнее
натяжение, кроме этого дефекта, вызывает еще усиленный износ
зубьев звездочек, подшипников опор и самой цепи. Операция
регулирования натяжения ветвей цепи обычно называется на
стройкой передачи. Надевать цепи на звездочки необходимо таким образом, чтобы
крючки звеньев были направлены в сторону движения цепи,
а не наоборот (рис. 434). Тогда звенья цепи при сбегании ее со
звездочки вращаются в шарнире крючка, а последний не трется
о поверхность зуба звездочки. Это уменьшает износ звена и звез
дочки.
Натяжение ветвей в правильно собранной цепной передаче
должно быть строго определенным. Недостаточное натяжение
ветви ухудшает ее набегание на ведомую звездочку, а излишнее
натяжение, кроме этого дефекта, вызывает еще усиленный износ
зубьев звездочек, подшипников опор и самой цепи. Операция
регулирования натяжения ветвей цепи обычно называется на стройкой передачи.
БАЛАНСИРОВКА СБОРОЧНЫХ ЕДИНИЦ
И МАШИН В СБОРЕ
Балансировка окончательно собранных сборочных единиц
на специальных установках или балансировочных станках пред
ставляет собой контрольно-пригоночную операцию, которая не
редко не включается в поток сборки, а выполняется на отдельном
участке. Тем не менее балансировочные работы составляют важ
нейшую часть процесса сборки.
Точность уравновешивания, допустимые дисбалансы устанавли
ваются техническими требованиями, исходя из особенностей
конструкции и назначения сборочных единиц и деталей, скорости
их вращения, допустимых вибраций машины, необходимой на
дежности и долговечности, возможных физиологических ощуще
ний оператора, работающего на машине в условиях эксплуатации,
и пр. Статическая балансировка сборочных единиц и деталей состоит
в определении величины дисбаланса и его устранении путем пере
становки отдельных элементов конструкции, удаления в нужных
местах сверлением, шлифованием, растачиванием части металла
или, наоборот, добавлением соответствующей его массы сваркой,
приклепыванием и пр., а также комбинированием этих способов.
Методы статической балансировки применяют в мелкосерийном
и единичном производствах. В условиях крупносерийного и мас
сового производств используют более точный и производитель
ный метод статической балансировки в динамическом режиме.
В этом случае балансируемая сборочная единица — ротор вра
щается с повышенной скоростью. Используемые балансировочные
станки имеют высокую производительность, обеспечивают оста
точный дисбаланс не более 0,5—1 гс- см на 1 кг массы баланси
руемой сборочной единицы, при этом устранение дисбаланса
производится без съема детали со станка, часто автоматически.
Эти станки просты в эксплуатации, не требуют специальных
фундаментов.
Для уравновешивания вращающихся сборочных единиц, име
ющих большую сравнительно с диаметром длину (например,
шпиндели, роторы турбин, коленчатые валы), одной статической
балансировки недостаточно. Такие сборочные единицы подвер гают динамической балансировке.
При динамической балансировке в сборе искусственно создается система
сил, в которой равнодействующие, а также моменты равны нулю или постоянны
по величине и направлению. лучших мировых образцов. Отечественная промышленность вы пускает универсальные и специальные балансировочные станки
для сборочных единиц и изделий массой до 100 т. Созданы гамма балансировочных машин для уравновешивания легких, средних и тяжелых роторов (ЭНИМС), станки для уравновешивания дета лей и узлов одновременно в двух плоскостях (МВТУ им. Н. Э. Баумана), балансировочные машины резонансного типа (МИИТ), а также полуавтоматическое и автоматическое балансировочное оборудование. В массовом производстве получают распространение автомати
зированные балансировочные машины, в которых процессы соеди
нения балансируемой детали (сборочной единицы) с приводом,
определения неуравновешенности, передача этих результатов
запоминающим устройствам, ориентация детали и режущего
инструмента и операция устранения дисбаланса производятся
автоматически. В некоторых таких автоматах процессы определе
ния неуравновешенности и ее устранения совмещены (однопсзи-
ционные автоматы); в двухпозиционных же автоматах эти про
цессы разделены.
Для уравновешивания коленчатых валов по проекту ЭНИМСа
создана автоматическая балансировочная линия, оснащенная кон
трольно-измерительной аппаратурой, включающей блоки па
мяти, решающее и коррекционные устройства и т. д. Производи
тельность этой линии — одно изделие в минуту. Она дает воз
можность снизить неуравновешенность в 50 раз.
В целях проведения динамической балансировки на повышен
ных скоростях и сокращения времени на операцию в настоящее
время ведутся опыты по применению кратковременных (менее
1 м-с) импульсов лазера для устранения излишнего металла без
остановки уравновешиваемой детали (сборочной единицы).
СБОРКА МАХОВИКОВ И ШКИВОВ С ВАЛАМИ
Наиболее распространены следующие способы крепления ма
ховика или шкива на валу: на конусе и шпонке (рис. 439, а), на
цилиндрической шейке при помощи призматической (рис. 439, б)
или клиновой (рис. 439, в) шпонки, на фланце вала (рис. 439, г).
При сборке маховиков (шкивов), посаженных на валу на конусе (см.
рис. 439, а), после контроля конуса на биение проверяют прилегание отверстия
ступицы на краску, для чего конус вала покрывают тонким слоем краски, наса
живают маховик (шкив) и затягивают гайку. Если сопряжение удовлетвори
тельное — отпечаток от краски располагается равномерно по всей поверхности
отверстия ступицы. При неравномерном распределении отпечатков отверстие
пригоняют по конусу вала шлифованием или притиркой эталонным притиром.
После пригонки отверстия ступицы на валу устанавливают шпонку и лег
кими ударами медного молотка загоняют ее в паз. При дальнейшей посадке ма
ховика (шкива) паз ступицы, попадая на шпонку, направляет движение ступицы.
Гайку, монтируемую на конце вала для создания требуемого натяга, целесооб разно навинчивать ключом с рукояткой длиной не более 20d (где d — диаметр
резьбы). При более длинных рукоятках ключей в конусном соединении возможно
возникновение сил, способных разорвать ступицу или вызвать трещины.
Маховик или шкив, базируемый на цилиндрической поверх
ности (рис. 439, б), напрессовывают на хвостовик вала с неболь
шим натягом при помощи специального приспособления. Винт 1 этого при
способления ввертывают или каким-либо другим способом за
крепляют в вале. Осевое давление для напрессовки создают вра
щением гайки 2. Намного упрощается и облегчается процесс установки махо
вика при использовании гидравлических приспособлений. Маховики и шкивы часто устанавливают на валах с помощью
переносных пневмогидравлических скоб или специальных ста
ционарных прессов.
При напрессовке ступицы особое внимание должно быть обра
щено на правильность расположения шпоночных канавок и плот
ность посадки шпонки. Чтобы шпоночные канавки вала и ступицы
совпали, при напрессовке применяют ложную направляющую
шпонку, которую затем вынимают и заменяют настоящей шпонкой,
забиваемой ударами медного молотка со стороны торца вала.
Конец шпонки должен быть заподлицо со ступицей или же закрыт
предохранительным колпаком. мерно затягивают и стопорят.
После закрепления маховика (шкива) на валу проверяют сбо
рочную единицу на радиальное и торцовое биения. Вал при этом
устанавливают на призмах или в центрах. Допустимое биение
маховиков и шкивов определяется конструктивными требова
ниями, но ориентировочно можно принять для радиального бие
ния (0,00025-0005) D, для торцового (0,0005-0,001) D, где
D — диаметр маховика или шкива.
Перед установкой на валы маховики (шкивы) должны быть
отбалансированы. В быстроходных же передачах производится
повторная балансировка валов в сборе с маховиками или шки вами.
Дата добавления: 2022-01-22; просмотров: 49; Мы поможем в написании вашей работы! |
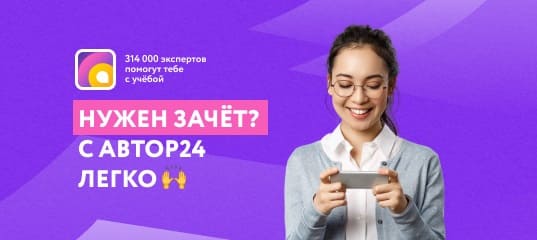
Мы поможем в написании ваших работ!