Назначение и содержание паспортов металлорежущих станков
Дата 1.10.2021
специальность 15.02.09 Технология машиностроения
гр.43тм – заочное
преподаватель Наливайко С.А.
Дисциплина МДК 03.01. Реализация технологических процессов изготовления деталей
КОНСПЕКТ ЛЕКЦИИ
по теме 1.2 «Наладка и эксплуатация оборудования»
1. Эксплуатация металлорежущих станков. Назначение и содержание паспортов металлорежущих станков
План лекции
1. | Основные сборочные единицы станков |
2. | Приводы в металлорежущих станках |
3. | Движения в металлорежущих станках 4. Назначение и содержание паспортов металлорежущих станков Контрольные вопросы |
1. | Основные сборочные единицы станков |
К основным сборочным единицам станка относятся:
• | станина, корпусные детали (поперечины, хоботы, ползуны, плиты, столы, суппорты и др.) и направляющие; |
• | привода станков; |
• | шпиндели и их опоры; |
• | коробки подач; |
• | бесступенчатые приводы; |
• | механизмы прямолинейного движения. |
Станина. Станина служит для монтажа деталей и узлов станка, относительно нее ориентируются и перемещаются подвижные детали и узлы. Станина, как и другие элементы несущей системы, должна обеспечивать в течение срока службы станка возможность обработки заготовок с заданными режимами и точностью. Это достигается правильным выбором конструкции, материала станины и технологии ее изготовления для обеспечения необходимой жесткости, виброустойчивости и износостойкости направляющих.
|
|
Станины делят на горизонтальные и вертикальные (стойки). Форма сечения горизонтальных станин (рис. 1.2.1.1, а) определяется многими факторами: расположением направляющих, условиями удаления стружки и СОЖ, условиями размещения резервуаров для СОЖ и защитных устройств, необходимостью установки на ней подвижных и неподвижных узлов, требованиями жесткости, удобством проведения ремонтных работ и т.п. Форма сечения вертикальных станин (рис. 1.2.1.1, б) определяется главным образом требованиями к жесткости. В целях повышения жесткости станины выполняют с двойными стенками или сплошного сечения с замкнутым контуром, увеличенным числом перегородок и ребер; с этой же целью исключают люки и окна или уменьшают их размеры.
Направляющие. Требуемое взаимное расположение узлов станка и возможность относительного перемещения инструмента и заготовки обеспечивают направляющие. Для перемещения узла направляющие должны допускать только одну степень свободы движения. Это достигается соответствующей конструкцией направляющих или силовым замыканием (действием сил тяжести, подпружиненных элементов и т.п.).
|
|
По назначению и конструктивному исполнению направляющие можно классифицировать по следующим признакам:
• | по виду движения: направляющие главного движения (например, стол-станина продольно-строгального станка); направляющие движения подачи; направляющие перестановки сопряженных и вспомогательных деталей и узлов, неподвижных в процессе обработки; |
• | по траектории движения: направляющие прямолинейного и кругового движения; |
• | по направлению траектории перемещения узла в пространстве: горизонтальные, вертикальные и наклонные; |
• | по геометрической форме: призматические, плоские, цилиндрические, конические (только для кругового движения) и их сочетания. |
Рис. 1.2.1. | 1. | Сечения горизонтальных (о) и вертикальных (б) станин |
Кроме указанных можно отметить такие дополнительные признаки классификации направляющих, как способность восприятия отрывающих сил и опрокидывающих моментов (замкнутые направляющие), способ выполнения направляющих (за одно целое с подвижным узлом или станиной либо накладные, прикрепленные к узлу или станине).
|
|
Наибольшее распространение в станках получили направляющие скольжения и качения.
2. | Приводы в металлорежущих станках |
Приводом называется совокупность механизмов, служащих для приведения в движение исполнительных звеньев станка. В привод входит также источник движения. Привод должен обеспечивать возможность регулирования скорости движения исполнительных звеньев станка.
Приводы станков подразделяются на ступенчатые и бесступенчатые. К первым относятся приводы со ступенчатыми шкивами, приводы с шестеренными коробками скоростей и приводы в виде многоскоростных асинхронных электродвигателей. Возможны также ступенчатые приводы, являющиеся комбинацией упомянутых выше механизмов. К бесступенчатым приводам можно отнести приводы с механическими вариаторами, электродвигатели постоянного тока с регулируемой частотой вращения, гидравлические приводы и комбинированные, представляющие собой сочетание регулируемого электродвигателя постоянного тока или привода с вариатором со ступенчатой коробкой скоростей, или, наоборот, механического вариатора с многоскоростным асинхронным электродвигателем переменного тока.
Шпиндель – одна из наиболее ответственных деталей станка. Он передает вращение закрепленному в нем инструменту или обрабатываемой заготовке.
|
|
В качестве основного материала для шпинделей применяют среднеуглеродистую конструкционную сталь 45 с последующим улучшением (закалкой с высоким отпуском до твердости HRC 22-28). При повышенных требованиях к шпинделю и необходимости обеспечения высокой твердости его поверхности применяют сталь 40X с закалкой и отпуском до HRC 40-50. При особо высоких требованиях к поверхностной твердости шеек шпинделя применяют малоуглеродистые стали типа 20X с последующей цементацией, закалкой и отпуском до HRC 56-62. Для слабонагруженных шпинделей особо точных станков применяют сталь 35ХМЮА, которую подвергают азотированию с последующей закалкой и отпуском до HV 850-1000. Для шпинделей тяжелых станков применяют марганцовистые стали типа 50Г2 с последующей нормализацией или закалкой и высоким отпуском до HRC 28-35. Для изготовления полых шпинделей большого диаметра иногда целесообразно применять серый или высокопрочный чугун с шаровидным графитом в литой структуре.
Конструктивная форма шпинделей определяется способом крепления на нем зажимных приспособлений или инструмента, посадками элементов привода и типом применяемых опор. Шпиндели, как правило, изготовляют пустотелыми для возможности прохода прутка, а также для уменьшения веса. Передние концы шпинделей станков общего назначения стандартизованы.
В качестве опор шпинделей станков применяют подшипники качения и скольжения. Так как от шпинделей требуется высокая точность вращения, то подшипники качения, используемые в опорах шпинделей, должны быть высоких классов точности. Выбор класса точности подшипника определяется допуском на биение переднего конца шпинделя, который зависит от требуемой точности обработки. Обычно в передней опоре применяются более точные подшипники, чем в задней.
Коробки подач предназначены для получения требуемых величин подач и сил подачи при обработке на станке различных деталей.
Коробка подач в большинстве случаев приводится от шпинделя станка или от отдельного электродвигателя. Значения подач должны обеспечивать требуемый класс чистоты поверхности, а также высокую стойкость инструмента и производительность станка. Подачи в общем случае должны располагаться по геометрической прогрессии.
Изменение величины подачи может производиться различными способами: при помощи механизмов с зубчатыми передачами и без применения зубчатых передач (например, электрическим или гидравлическим путем, храповым или кулачково-рычажными механизмами и т.д.).
Бесступенчатые приводы применяют для плавного и непрерывного изменения частоты вращения шпинделя или подачи. Они позволяют получать наивыгоднейшие скорости резания и подачи при обработке различных деталей. Кроме того, они дают возможность изменять скорость главного движения или подачу во время работы станка без его остановки.
В станках применяют следующие способы бесступенчатого регулирования скоростей главного движения и движения подачи:
1. Электрическое регулирование производится изменением частоты вращения электродвигателя, который приводит в движение соответствующую цепь станка.
2. Гидравлическое регулирование применяется главным образом для регулирования скоростей прямолинейных движений (в строгальных, долбежных, протяжных станках), значительно реже – вращательных движений.
3. Регулирование при помощи механических вариаторов. Большинство механических вариаторов, применяемых в станках, является фрикционными вариаторами.
3. | Движения в металлорежущих станках |
В современных металлорежущих станках для осуществления прямолинейных движений используют преимущественно следующие механизмы:
• | зубчатое колесо-рейка; |
• | червяк-рейка; |
• | ходовой винт-гайка; |
• | кулачковые механизмы; |
• | гидравлические устройства; |
• | электромагнитные устройства типа соленоидов. |
Механизм зубчатое колесо-рейка применяют в приводе главного движения и движения подачи, а также в приводе различных вспомогательных перемещений.
Механизм червяк-рейка применяется в виде двух типов передач: с расположением червяка под углом к рейке, что позволяет (в целях большей плавности хода передачи) увеличить диаметр колеса, ведущего червяк, и с параллельным расположением в одной плоскости осей червяка и рейки, когда рейка служит как бы длинной гайкой с неполным углом охвата винта-червяка. Условия работы этой передачи значительно благоприятнее условий работы передачи зубчатое колесо-рейка.
Ходовой винт-гайка является, широко применяемым механизмом для осуществления прямолинейного движения. С помощью этого механизма можно производить медленные движения в приводе подач.
Винтовые пары качения. Винтовые пары скольжения из-за больших потерь при скольжении в резьбе и связанного с ним износа заменяются винтовыми парами качения. Они имеют малые потери на трение, высокий к.п.д., кроме того, в них могут быть полностью устранены зазоры в резьбе в результате создания предварительного натяга.
Кулачковые механизмы, преобразующие вращательное движение в прямолинейное поступательное, применяются главным образом на автоматах. Различают кулачковые механизмы с плоскими и цилиндрическими кулачками.
Для получения на металлорежущем станке детали требуемой формы и размеров рабочим органам станка необходимо сообщить определенный, иногда довольно сложный комплекс согласованных друг с другом движений. Эти движения можно подразделить на основные (рабочие) и вспомогательные. К основным движениям относятся главное движение, называемое также движением резания, и движение подачи. При помощи этих движений осуществляемся процесс снятия стружки с обрабатываемой заготовки. Скорость главного движения определяется оптимальной скоростью резания, а величина подачи зависит от требуемого класса чистоты обработанной поверхности.
Главное движение в металлорежущих станках бывает чаще всего двух видов – вращательное и прямолинейное (возвратно-поступательное). В отдельных станках главное движение может иметь и более сложный характер, но определяется оно также через вращательное и поступательное движения. Главное движение может сообщаться либо обрабатываемой заготовке, либо инструменту. Например:
• | у станков токарной группы главным движением является вращение обрабатываемой заготовки; |
• | у фрезерных, шлифовальных и сверлильных – вращение инструмента; |
• | у долбежных, протяжных, части зубообрабатывающих и некоторых других – возвратно-поступательное движение инструмента; |
• | у продольно-строгальных станков – возвратно-поступательное движение заготовки. |
В некоторых станках главное движение получается в результате одновременного вращения заготовки и инструмента (например, при сверлении отверстий малого диаметра на токарных многошпиндельных автоматах).
Движение подачи у металлорежущих станков может быть непрерывным или прерывистым (периодическим), простым или сложным, состоять из нескольких самостоятельных движений или вовсе отсутствовать. Например, у токарных, фрезерных, сверлильных и других станков движение подачи является непрерывным. Прерывистым оно бывает, например, у продольно-строгальных станков. Примером сложного движения подачи может служить движение подачи в зубофрезерном станке при нарезании косозубого цилиндрического колеса. У круглошлифовальных станков несколько движений подачи — вращательное движение детали (круговая подача), продольное осевое перемещение детали или шлифовального круга (продольная подача) и, наконец, поперечная подача, сообщаемая шлифовальному кругу. В протяжных станках движение подачи отсутствует.
Вспомогательные движения необходимы для подготовки процесса резания, обеспечения последовательной обработки нескольких поверхностей на одной заготовке или одинаковых поверхностей на различных заготовках, К числу вспомогательных движений относятся:
• | движения для настройки станка на заданные режимы резания; |
• | движения для наладки станка в соответствии с размерами и конфигурацией заготовки; |
• | движения управления станком в процессе работы; |
• | движения соответствующих рабочих органов для подачи и зажима прутка или штучных заготовок; |
• | движения для закрепления и освобождения рабочих органов станка. |
Вспомогательные движения могут выполняться как автоматически, так и вручную. В станках-автоматах все вспомогательные движения автоматизированы и выполняются механизмами станка в определенные моменты времени в соответствии с технологическим процессом обработки детали.
Назначение и содержание паспортов металлорежущих станков
Документ, содержащий необходимые кинематические, динамические и конструктивные сведения, а также ряд общих данных о станке, называют паспортом станка. Наличие паспортов у станков позволяет технологам разрабатывать наиболее рациональные технологические процессы при правильном и эффективном использовании станочного парка; механикам — заранее готовиться к ремонту станков и быстро производить исправления при случайных поломках; нормировщикам — правильно назначать технически обоснованные нормы и т. д. Кроме паспорта, завод-изготовитель прилагает к станку руководство или инструкцию по уходу и обслуживанию, содержащую необходимые сведения о правильной эксплуатации станка.
Паспорта станков составляют по специальным разработанным формам, а при отсутствии утвержденной формы для данного типа станка — по форме, наиболее похожей на утвержденную форму на сходные по типу станки. В паспорт вписывают: общие сведения о станке, общий вид станка с обозначением органов управления, спецификацию органов управления, основные данные о станке, габаритные размеры рабочего пространства, посадочные и присоединительные базы станка, габаритные размеры станка в плане, сведения о ремонте станка, данные о комплектации и т. д.
КОНТРОЛЬНЫЕ ВОПРОСЫ
1. | Назовите основные сборочные единицы станков. |
2. | По каким признакам классифицируются направляющие станков? |
3. | Какие направляющие получили наибольшее распространение в станках? |
4. | Какой механизм называется приводом в металлорежущих станках? |
5. | Какие механизмы для осуществления прямолинейных движений используются в металлорежущих станках? |
6. | Назовите главные движения для станков токарной, фрезерной, сверлильной, протяжной и шлифовальной групп. |
7.Для чего нужен паспорт станка
8.Основные данные, которые указывают в паспорте станка
ЛИТЕРАТУРА
1. | Черпаков Б.И., Вереина Л.И. Технологическое оборудование машиностроительного производства: учебное пособие. – М.: Академия., 2015. – 416 с. с.8-34 |
2. | И.Н. Чернов. Металлорежущие станки. – М.: Машиностроение, 1988. – 482 с. с.7-77 |
3. | Металлорежущие станки: Учебник для нач. проф. обрабования / Б.И. Черпаков, Т.А. Альперович. – М.: Издательский центр «Академия», 2003. – 368 с. с.106-130 |
Дата добавления: 2022-01-22; просмотров: 46; Мы поможем в написании вашей работы! |
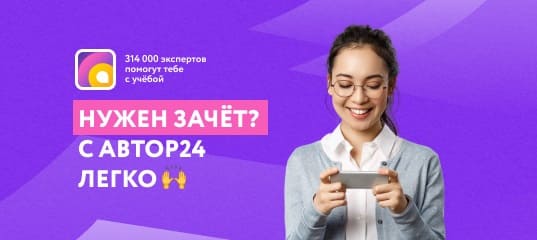
Мы поможем в написании ваших работ!