Тема: Донбасс во второй половине 1970-х – середине 1980-х
Лекция
Тема: Промышленный Донбасс на заключительном этапе Великой Отечественной войны и первое послевоенное десятилетие.
В Донбассе исторически сложился мощный топливный комплекс, основу которого составляет угольная промышленность. Анализ изменений, которые происходили в этом секторе региональной экономики, позволяет утверждать, что в первые послевоенные годы власть была заинтересована в быстром восстановлении и интенсивном развитии угольной промышленности региона. В этот период Донбасс играл роль ведущего поставщика топливно-энергетических ресурсов для всей страны.
Возрождение угольной промышленности началось сразу же после освобождения территории региона от оккупационных войск. В феврале 1943 года было принято постановление Государственного Комитета Обороны «О восстановлении угольных шахт Донбасса», которое обязывало Наркомат угольной промышленности «немедленно приступить» к восстановлению шахт и угольных предприятий в освобожденных районах Донбасса. В составе Наркомата было организовано Главное управление по восстановлению угольных шахт (Ворошиловград), на которое возлагалось оперативное, хозяйственное и техническое руководство восстановительными работами. Возобновлялась деятельность комбинатов «Ворошиловградуголь» и «Сталинуголь» [125].
Учитывая недостаток кадров, предусматривалось направить из Метростроя на работу в Донбасс 500 квалифицированных рабочих и 50 инженерно-технических работников, запрещалась мобилизация в армию рабочих и инженерно-технических работников, занятых на восстановлении шахт [126]. Необходимое для восстановления и организации добычи угля оборудование и механизмы передавались на шахты Донбасса промышленными предприятиями других городов страны. Была оказана и другая материальная, финансовая, техническая помощь региону [127].
|
|
В условиях продолжения военных действий угледобычу организовывали, прежде всего, на тех шахтах, которые легко можно было восстановить. Возобновляли добычу также на мелких шахтах, часто реконструировались лишь отдельные производственные узлы, многие угольные предприятия восстанавливали, обычно, в прежнем, довоенном виде.
Конечно, подобная политика восстановления в какой-то мере была оправдана жесткими требованиями военного времени, необходимостью скорейшего обеспечения экономики страны, которая продолжала воевать, энергетическими ресурсами. Однако восстановление наспех консервировало устаревшую технику, оборудование, методы организации работы, тем самым, закладывая основу для будущих экономических и социальных проблем в регионе.
|
|
Масштабное восстановление и дальнейшее развитие угольной промышленности региона значительно ускорились после окончания войны. Власть, рассматривая Донбасс как важную ресурсно-энергетическую составляющую общесоюзной экономики, оказывала его восстановлению особое внимания. Наиболее характерными чертами этого процесса были следующие.
Во-первых, интенсивное восстановление угольной отрасли на основе привлечения значительных финансовых, материально-технических, трудовых ресурсов. В четвертой пятилетке общие капиталовложения в развитие хозяйства Украины составили 9,2 млрд. руб., из них почти треть было инвестировано в экономику региона [128]. При этом темпы развития угольной отрасли Донбасса были значительно выше, чем общесоюзные. Если в течение 1946-1950 годов угледобычу по стране предполагалось увеличить на 51%, то в республике – более чем в 2,8 раза и довести добычу угля в 1950 г. до 86,1 млн.т, что составляло 34,4% общесоюзной добычи [129].
Стержневая идея восстановительных работ – быстрое количественное наращивание производственных мощностей – была в полной мере реализована в Донбассе. В течении первой послевоенной пятилетки в Сталинской и Ворошиловградской областях планировалось восстановить и построить новые шахты общей мощностью 77,5 млн. т, что составляло 42,3% от запланированного на 1950 г. объема добычи угля в стране [130]. То есть Донбасс все еще оставался главной топливно-энергетической базой СССР. Сосредоточение значительных финансовых, материально-технических, кадровых ресурсов на решении проблемы увеличения угледобычи дало в целом положительные результаты. В течение 1946 – 1950 годов в Донбассе из 263 основных шахт, подлежащих восстановлению, было восстановлено и введено в действия 259 шахт. Кроме того, было заложено 60 новых шахт [131].
|
|
Во-вторых, одновременно с восстановлением инфраструктуры угольной отрасли предпринимались попытки по совершенствованию ее материально-технической базы, интенсификации производства. Уже в первые послевоенные годы на шахтах появилась новая техника, оборудование. С 1946 г. было внедрено металлическое и железобетонное крепление. В 1949 г. паровые подъемные машины были полностью заменены на электрические. Произошли значительные изменения в укомплектовании шахт угледобывающей техникой.
Одним из выдающихся технических достижений этого периода стало создание (1948 г.) и широкое внедрение в производство угольного комбайна «Донбасс». Эти универсальные машины обеспечили механизацию выемки угля из забоя. В больших объемах поставлялась в шахты и другая техника. В шахтах Ворошиловградской области в 1950 г. в сравнении с 1946 г. использовалось врубовых машин в 1,8 раза больше, ленточных конвейеров – более чем в 24 раза, электровозов – почти в 29 раз больше [132]. Техническое переоборудование шахт позволило значительно повысить общий уровень механизации основных процессов угледобычи. В 1950 г. зарубка и отбойка угля были механизированы почти на 99%, поставки из очистных забоев – на 100 %, откатка – на 95 % [133]. Все это создавало условия для комплексной механизации добычи угля.
|
|
В-третьих, новая техника и механизация угледобычи обусловили изменения и в организации производства. Производственный процесс перестраивался таким образом, чтобы работа в лавах осуществлялась в один цикл в сутки (первая и вторая смены – отгрузка угля из лавы, третья – ремонтно-подготовительные работы). В лавах, переведенных на график цикличности, организовывались комплексные бригады по добыче угля, по перемещению транспортеров, проходчиков и другие.
К концу 1950 г. почти четверть действовавших очистных забоев, были переведены на новую систему организации производства. Это позволило несколько улучшить технико-экономические показатели работы шахт. Так, на шахтах Ворошиловградской области с 1946 по 1950 год значительно увеличилась среднемесячная скорость продвижения действующей очистной линии забоя (с 19,7 до 24,1м), возросла среднегодовая протяженность действующих очистных забоев (с 30,1 до 76, 1 м) [134].
Высокие темпы восстановления разрушенных шахт, расширение шахтного строительства, совершенствование организации производства способствовали достаточно быстрому приросту добычи угля.
Как видно, за годы войны угледобыча в регионе уменьшилась почти в три раза. В первые три послевоенных года темпы прироста добычи угля были очень высокими: ежегодно объем добычи увеличивался на 20-30 %. Начиная с 1949 г. они значительно снизились, оставаясь при этом достаточно высокими (в Донецкой области прирост добычи составлял примерно 10 %, в Ворошиловградской области – 8 %). В 1950 г. в Донбассе было добыто 76,4 млн. т угля, или в 2,5 раза больше, чем в 1945 г. Довоенный уровень добычи угля был превзойден в 1951 г. Именно на этих успехах акцентировали внимание средства массовой информации, замалчивая при этом крайне негативные тенденции в развитии угольной промышленности, которые проявились уже в первые послевоенные годы.
Анализ опубликованных и архивных источников свидетельствует, что быстрое наращивание угледобычи происходило, прежде всего, за счет экстенсивных факторов. В условиях «битвы за большой уголь» на экономические показатели, эффективность работы, рентабельность отрасли мало обращали внимание. Главным было любой ценой добыть как можно больше угля.
Одной из острейших проблем оставалась низкая производительность труда шахтеров. Если в 1940 г. в Донбассе среднемесячная добыча угля на одного шахтера составляла 25,6 т, то в 1950 г. – только 21,7 т, а на некоторых шахтах – еще меньше [136]. Довоенная производительность труда (в 1940 году ежемесячно в среднем на одного шахтера в Донецкой области – составляла 26,6 т, в Ворошиловградской области – 24,6 т) была достигнута в регионе лишь к концу 1950-х годов.
Медленный рост производительности труда, на наш взгляд, был обусловлен несколькими факторами. Во-первых, эксплуатацией большого количества мелких, малоэффективных шахт, наскоро отстроенных в первые послевоенные годы, на которых в основном преобладал примитивный ручной труд. Естественно, ни о какой механизации на этих шахтах и речи не могло быть. На небольших шахтах (суточная добыча угля которых не превышала 300 тонн) в 1950 г. добывали почти половину (42,6%) всего донецкого угля (в 1940 г. – 13,8%) [137].
Во-вторых, на уровне производительности труда негативно сказывалось также неудовлетворительное использование машин и механизмов. Несмотря на более широкое использование на шахтах машин и технического оборудования, ручной труд в угольной промышленности преобладал.
В советской историографии доминировал тезис о нехватке рабочих кадров на шахтах Донбасса в послевоенные годы. Однако архивные материалы доказывают, что массовое перемещение рабочих из других регионов страны, на многих шахтах создавало даже избыток рабочих рук [138]. Конечно, это не стимулировало расширение использования машин и механизмов, а та техника, что была на шахтах, осваивалась крайне медленно. Так, месячная производительность тяжелых врубовых машин, хоть и выросла с 2112 т в 1945 г. до 3042 т в 1950 г., однако довоенного уровня (3424 т в 1940 г.) не достигла, а на многих шахтах была значительно ниже [139]. Сравнительно низкой была также и общая производительность комбайнов «Донбасс»: в 1950 г. она составляла в донецком регионе 4862 т, а, например, в Печорском бассейне – 5238 т [140]. Конечно, надо учитывать горно-геологические условия, квалификацию и опыт работников и другие факторы. Однако в условиях, когда главными в оценке работы шахты были валовые, количественные показатели (выполнение плана) менеджмент предприятия был мало заинтересован в освоении новой техники.
В-третьих, неэффективное использование техники было обусловлено также низким уровнем квалификации горняков, отсутствием у них опыта работы, ведь подавляющее большинство шахтеров послевоенного времени составляла сельская молодежь, которая попадала на шахты по «комсомольским призывам» или вследствие мобилизации. По этой же причине на шахтах оставался высоким уровень травматизма, случались многочисленные простои, аварии.
Одной из важнейших составных частей промышленного комплекса Донбасса является металлургическая промышленность. Она включает в себя мощные предприятия черной металлургии с полным производственным циклом (чугун – сталь – прокат), а также ряд заводов цветной металлургии (ртутный комбинат, цинковый завод и др.). Большинство металлургических гигантов региона тесно связаны с коксохимическими и химическими производствами. В структуре металлургического комплекса Донбасса абсолютно преобладали предприятия черной металлургии, которые производили почти половину всего металла Украины.
Анализируя изменения, которые происходили в металлургическом комплексе региона в послевоенные годы, следует отметить, что в целом восстановление отрасли проходило достаточно успешно. Основные усилия были направлены на восстановление инфраструктуры металлургического производства, увеличение выплавки металла, и дальнейшее развитие отрасли.
За годы войны почти все металлургические заводы были разрушены: значительная часть оборудования была вывезена во время эвакуации в восточные районы страны, а что осталось – было уничтожено, разграблено и вывезено в Германию. Производство основных видов продукции металлургической промышленности значительно сократилось.
Данные таблицы свидетельствуют, что основные мощности металлургического комплекса региона были сосредоточены в Донецкой области. Здесь действовали такие заводы-гиганты, как Сталинский, Макеевский, Енакиевский металлургические заводы, «Азовсталь» и др. предприятия. За годы войны производство основных видов металлургической промышленности области сократилось примерно в 3-4 раза. Металлургический комплекс Ворошиловградской области в эти годы пострадал значительно больше: выпуск некоторых видов продукции уменьшился в десятки раз. Так, в 1945 г. в сравнении с 1940 г. выплавка стали в Ворошиловградской области сократилась в 35 раз, производство проката – более чем в 82 раза, стальных труб – в 6 раз.
По сути, необходимо было создавать новый металлургический комплекс. Отдельные промышленные объекты области были восстановлены еще в годы войны. Однако основные работы начались в четвертой пятилетке: планом предполагалось ввести в эксплуатацию в Донбассе и Приднепровье 30 доменных печей общей мощностью 9 млн. т чугуна в год, сталеплавильные агрегаты мощностью 8,4 млн. т стали, 58 прокатных станов мощностью 6,5 млн. т готового проката [142]. На решение этих задач государство инвестировало почти 724 млн. руб., что составило 17,9% капиталовложений в промышленность республики [143].
С целью организации и координации восстановления металлургических предприятий Донбасса в 1946 г. было сформировано специальное Главное управление по строительству предприятий черной металлургии Донбасса (Главчерметстрой), в состав которого вошли пять строительно-монтажных трестов: Азовстальстрой, Макстрой, Сталинметаллургстрой, Ворошиловскстрой и Енакиевтяжстрой, которые ранее подчинялись Главюжстрою. Всего в строительно-монтажных организациях в 1950 г. работало свыше 26 тыс. рабочих [144].
Именно эти организации выполняли основные работы по восстановлению черной металлургии. Создание централизованной организации, которая занималась восстановлением отрасли, позволило значительно расширить масштабы работ, изменить их характер. В первые послевоенные годы основными были не ремонтные, а строительно-восстановительные работы. Восстанавливалось энергетическое хозяйство предприятий, водоснабжение, внутризаводской транспорт, но главное внимание было сосредоточено на цехах основного металлургического производства. Строителям нужно было заново восстанавливать полностью разрушенные мощные металлургические агрегаты со сложным технологическим оборудованием и большим вспомогательным хозяйством.
Впрочем, несмотря на трудности, уже в первые послевоенные годы отдельные металлургические предприятия стали оживать. Достаточно успешно проходило восстановление одного из гигантов металлургии Донбасса – завода «Азовсталь». Уже в январе 1946 г. здесь была введена в эксплуатацию мартеновская печь №2, в сентябре этого же года – доменная печь №4. В последующие годы темпы восстановительных работ ускорились, причем одновременно с восстановлением старого металлургического фонда строились и новые объекты. В 1948 г. были введены в действия два крупнейших в Европе прокатных стана (блюминг и реечно-балочный), которых здесь до войны не было. Вследствие этого завод стал предприятием с полным металлургическим циклом. К концу 1949 г. предприятие в основном было восстановлено. Достаточно интенсивно восстанавливались Макеевский, Енакиевский, Сталинский и другие крупные металлургические предприятия.
Анализируя восстановительные работы в металлургической отрасли, необходимо отметить, что среди наиболее характерных трудностей, на наш взгляд, были: во-первых, нехватка квалифицированных специалистов и рабочих. Так, в 1947 г. в тресте «Макстрой» работало примерно 5 тыс. чел., что составляло половину штатного состава. Причем, обычно это были сельские жители, направлены на восстановление Донбасса по оргнабору или через систему заключения индивидуальных договоров. В частности, в 1950 году трестами Главчерметстроя Донбасса с помощью этих форм пополнения строительных коллективов было принято почти 85,6% рабочих. Среди них преобладали неквалифицированные рабочие, которые не имели опыта строительных работ, многие из них относились к строительству как к временному местопребыванию. В трестах Главчерметстроя Донбасса только в течение 1947 г. выбыло по различным причинам более 17 тыс. рабочих, из них 7,4 тыс. – самовольно [145]. Неквалифицированный состав рабочих, большая текучесть рабочей силы, конечно, негативно сказывались на производственных показателях: довольно часто несвоевременно и некачественно выполнялись производственные задания, допускали большие потери рабочего времени.
Во-вторых, очень острой проблемой была нехватка строительных материалов, техники, оборудования. В этих условиях при проведении восстановительных работ широко использовались уцелевшие фундаменты, стены заводских зданий, арматура, другие строительные конструкции, максимально применялись местные, однако часто некачественные, строительные материалы. При этом лозунгом – как можно быстрее выйти на довоенный уровень – руководствовались не только при проведении строительных, но и монтажных работ. Достаточно часто для ускорения темпов восстановительных работ или же в случае отсутствия необходимого оборудования прибегали к максимальному сохранению поврежденных конструкций: их исправление и ремонт происходили без разборки и демонтажа, нередко использовали материалы, найденные в завалах.
Конечно, такой подход к восстановлению, особенно учитывая степень послевоенной разрухи, в какой-то мере можно понять. Однако, на наш взгляд, нельзя полностью соглашаться с авторами, которые считают этот подход «удачным решением», одним из «новых и важных методов восстановления». Возрождение предприятий по такой схеме на долгие годы консервировало устаревшую технику, оборудование, технологии. Таким способ можно было решить первостепенные задачи, но в целом это был бесперспективный подход: он закладывал основу для отставания отрасли в будущем.
В-третьих, на очень низком уровне находилась механизация восстановительных работ. В послевоенные годы парк строительной техники практически не обновлялся, а то оборудование, что осталось, было разукомплектовано, физически изношено, поэтому большая часть работ выполнялась вручную. Естественно, все это приводило к снижению качества восстановительных работ, низкой производительности труда, сдерживало темпы восстановления. Так, в 1949 г. ни один из трестов Главчерметстроя Донбасса не выполнил плановые задания [146].
Впрочем, надо отметить, что одновременно с восстановлением разрушенных предприятий предпринимались попытки технической модернизации отдельных производств. В течение 1946-1952 годах в металлургии было проведено пять так называемых обязательных минимумов по малой механизации (в 1946-1948, 1950 и 1952 годах). Каждый из них включал перечень мероприятий (с техническим решением) по механизации трудоемких работ и обязательные сроки внедрения на всех металлургических предприятиях. При этом в каждый следующий минимум включалось больше мероприятий, чем в предыдущий, и охватывалось больше структурных подразделений (сначала основные цеха, а затем и вспомогательные). Сами мероприятия постепенно усложнялись. Уже в 1948 г. значительная часть из них предусматривала внедрение автоматизации и полуавтоматизации производства, а в 1950 году был разработан ряд мер по комплексной автоматизации. Под эти проекты выделялись средства [147].
Конечно, это можно считать образцом административного подхода к решению сложного вопроса. Многое из запланированного не исполнялось, потому что не хватало ни соответствующих средств, ни материально-технического, кадрового и научного обеспечения. Однако они сыграли определенную роль в повышении уровня механизации отрасли. В реалиях жизни эти минимумы использовались как ориентиры в проведении технической политики, и это было положительным моментом. Вместе с тем, сам процесс модернизации металлургического производства включал преимущественно меры, направленные на частичную механизацию основных цехов, усовершенствование технологии, автоматизацию отдельных операций. При этом конкретные меры были обусловлены особенностями технологических процессов, условиями производства, наличием соответствующих ресурсов на отдельных заводах. Общим было то, что все эти меры предусматривали, прежде всего, совершенствование основных звеньев металлургического производства – доменного, мартеновского, прокатного. Так, в доменных цехах «Азовстали», Макеевского, Сталинского и других заводов была проведена механизация засыпных агрегатов печей, усовершенствованны разливочные машины, осуществлены другие мероприятия. В мартеновских цехах механизировалась завалка и заправка мартеновских печей. Завалочные машины действовали на Енакиевском заводе, «Азовстали» и других предприятиях.
Уже в первые послевоенные годы все мартеновские печи завода «Азовсталь» начали оснащать автоматическими комплексами, с помощью которых происходило автоматическое регулирование отдельных технологических процессов и операций. Всего к 1951 г. уровень механизации в мартеновских цехах металлургических предприятий составлял на разных участках примерно 60-99 % [148]. В прокатных цехах принимались меры по механизации обжимных, крупносортных и других станов. Коренной модернизации подвергся блюминг Макеевского завода, новыми механизмами и приборами было оборудовано блюминг «Азовстали», многочисленные механические устройства были смонтированы на рельсобалочных станах Енакиевского, Краматорского и других заводах региона [149].
Всего в течение 1946-1950 годов была проведена значительная работа по восстановлению производственных мощностей черной металлургии. За эти годы в республике было введено в действие 22 доменные и 43 мартеновские печи, 46 прокатных станов, большое количество других агрегатов. В связи с этим мощности по выплавке чугуна выросли почти на 8,3 млн. т, стали – на 5,3 млн. т, по производству проката – на 4,4 млн. т [150].
Улучшились технико-экономические показатели. На начало 1951 года средний полезный объем одной доменной печи увеличился до 823 м3 против 716 м3 в 1940 г. Повысился коэффициент использования полезного объема доменных печей, возросло среднемесячное снятия стали с квадратного метра мартеновских печей. Наибольших успехов по этому показателю достигли мартеновцы завода «Азовсталь», которые в 1950 г. получали в среднем за одни сутки с каждого квадратного пода печи по 6,78 т (по республике – 5,37 т) стали [151]. Возросла производительность прокатных станов. Общая производительность труда в черной металлургии Украины в 1950 г. возросла по сравнению с 1940 г. на треть [152].
Достаточно успешно наращивались мощности металлургии региона. В 1950 г. металлургическая промышленность Донбасса превзошла довоенные показатели по выплавке чугуна, стали, производства другой продукции. Металлурги Донбасса уже в 1950 г. производили чугуна больше, чем в 1940 году на 8,3 %, стали – на 2,3 %, проката – на 13,9 %, стальных труб – на 19,3 %.
За послевоенную пятилетку выплавка металла в регионе увеличилась в разы. В Сталинской области в 1950 г. в сравнении с 1945 г. чугуна и стали выплавлялось в 4 раза больше, производилось проката черных металлов – почти в 5 раз больше. Заводы области достигли наиболее высоких показателей не только в регионе, но и в целом среди металлургических предприятий Украины. Завод «Азовсталь» первый в республике превысил довоенный уровень производства чугуна и стали, здесь впервые (в 1948 г.) началось производство проката. В 1950 г. превзошли довоенные показатели Сталинский, Енакиевский, Коммунарский и другие металлургические заводы. В Ворошиловградской области за счет введения новых мощностей, обновления производства за этот же период выплавка чугуна и стали увеличилась более чем в 8 раз, производство проката – в 13 раз. Все это свидетельствовало о достаточно успешном восстановлении отрасли.
Вместе с тем, уже в первые послевоенные годы проявилась очень тревожная тенденция в развитии металлургической промышленности: рост количественных параметров, наращивание валовых показателей сопровождались низкой экономической эффективностью, многие заводы отрасли работали нерентабельно. Например, в 1950 г. через частые простои металлургических агрегатов, перерасхода руды (46,5 тыс.т), кокса (50 тыс.т) металлурги Ворошиловградской области понесли убытки почти в 10 млн. руб. [153]. Похожая ситуация была характерна и для металлургии Сталинской области.
Машиностроение является важной отраслью в структуре промышленного комплекса Донбасса. Оно исторически формировалось как сложная, многоотраслевая система, ведущее место в которой занимало тяжелое машиностроение. Подавляющее большинство предприятий отрасли непосредственно ориентировались на обеспечение промышленных нужд Донбасса определенными видами машин или оборудования. Здесь преимущественно было сосредоточено металло- и энергоемкое производство горно-шахтного и металлургического оборудования, тяжелых станков, локомотиво- и вагоностроение и другое тяжелое машиностроение.
Масштабные восстановительные работы в машиностроении начались, как и в других отраслях, в первые послевоенные годы. Анализ этого процесса показывает, что, во-первых, машиностроительная промышленность восстанавливалась достаточно интенсивными темпами. Несмотря на огромные разрушения, вызванные войной, машиностроительные предприятия республики уже в конце 1940-х годов в целом были отстроены. В Донбассе одним из первых среди крупных предприятий стал в строй Ворошиловградский машиностроительный завод (1946 г.), в 1949 г. возобновил свою работу Ворошиловградский паровозостроительный завод, а в следующем году – Новокраматорский машиностроительный завод.
В первые послевоенные годы в ходе восстановительных работ на многих заводах осуществлялось расширение производственных площадей, перестройка отдельных цехов с учетом потребностей производства. Так, на Дзержинском (с 2016 г. – Торецком) машиностроительном заводе в процессе восстановления площадь механосборочного цеха была расширена более чем вдвое, значительно расширился сталелитейный цех. На Новокраматорском машзаводе в результате переоборудования старых и строительства новых цехов, мощности по выпуску механических изделий в 1950 году увеличились, по сравнению с довоенным уровнем, в 2,6 раза [154]. Подобные работы проводились и на других машиностроительных заводах региона.
Во-вторых, уже в первые послевоенные годы машиностроительные заводы не только возобновили выпуск довоенной номенклатуры продукции, но и достаточно активно осваивали новые образцы машин и оборудования. Одним из важнейших достижений машиностроительного комплекса Донбасса послевоенных лет было освоение серийного производства угольных комбайнов. Непосредственное участие в создании этой новой высокопроизводительной техники взял Горловский машиностроительный завод, на котором в 1947 г. были изготовлены опытные образцы комбайна ГУК-1. В следующем году на базе этого комбайна совместными усилиями заводских специалистов и ученых института «Донгипроуглемаш» была создана опытную партию комбайнов «Донбасс», первая серия которых поступила на шахты в 1949 г. Это была довольно удачная для своего времени машина, которая позволила механизировать один из наиболее трудоемких процессов угледобычи – навалоотбойные работы.
Позже были созданы еще несколько специализированных машин: комбайн для разработки тонких пластов, комбайн для крутопадающих пластов и другие виды машин. Горловский машиностроительный завод уже в первые послевоенные годы стал главным производителем угольных комбайнов не только для донецкого региона, но и для всей страны. Так, если в 1946 г. завод выпустил только два комбайна, то уже в 1950 г. – 344. В последующие годы комбайновая техника постоянно модифицировалась, а в первой половине 1960-х годов появились более совершенные модели. Кроме того, завод изготовлял шахтные насосы, вентиляторы главного проветривания, корпуса электродвигателей, запасные части к горно-шахтному оборудованию [155]. Существенное обновление ассортимента производимой продукции происходило и на других заводах.
В-третьих, характерной чертой развития машиностроения региона было проведение дальнейшей специализации производства. Важно отметить, что в целом эта отрасль формировалась для обслуживания преимущественно тяжелой промышленности Донбасса. Постепенно в структуре машиностроительного комплекса региона сформировалось несколько главных направлений: производство горно-шахтного оборудования для угольной промышленности; металлургическое машиностроение и транспортное.
Одной из важнейших составляющих этого комплекса было горно-шахтное машиностроение. Оно было сосредоточено в основном на шести заводах: Сталинском, Горловском, Краснолучском, Дзержинском машиностроительных заводах, а также на Ворошиловградском заводе угольного машиностроения и Ясиноватском заводе горнопроходческого оборудования, на которых выпускались почти все машины и оборудование, которые использовались в угольной промышленности. Впрочем, надо добавить, что внутриотраслевая специализация в горно-шахтном машиностроении проводилась уже в первые послевоенные годы. Так, Сталинский машиностроительный завод, который выпускал различные виды продукции (лебедки, подъемные машины, обогатительное оборудование, запасные части к горно-шахтному оборудованию, вентиляторы, конвейеры, редукторы и многое другое оборудование), стал специализироваться на выпуске преимущественно лебедок и подъемных машин, что позволило значительно увеличить объемы производства необходимого оборудования, повысить их качество [156]. В конце 1950-х годов удельный вес стоимости этой продукции в общем объеме производства завода составила почти 58%, на предприятии производилось 73,6% общесоюзного производства подъемных машин [157].
Впоследствии и на других заводы горно-шахтного машиностроения была проведена определенная специализация. Так, Ворошиловградский завод угольного машиностроения изготавливал обогатительное и транспортное оборудование для обогатительных фабрик, а также угольные комбайны, струги, редукторы. Однако главным видом его продукции было обогатительное оборудование. К концу 1950-х годов удельный вес стоимости указанной основной продукции в общем объеме производства данного предприятия составляла почти 94 % [158]. Краснолучский машзавод специализировался на выпуске горного инструмента, изготовлял также буровое оборудование, вагонетки для перевозки людей [159]. Горловский машиностроительный завод специализировался на выпуске угольных комбайнов, Дзержинский завод изготавливал электровозы. Производство оборудования для металлургической, энергетической промышленности сосредоточивалось преимущественно на Новокраматорском и Старокраматорском машиностроительных заводах. На Новокраматорском заводе в 1948 г. был выпущен первый послевоенный отечественный блюминг для прокатки специальной стали производительностью 1,5 млн. т проката в год. Это был современный на тот момент агрегат, в котором все рабочие процессы прокатки были механизированы, а управление – автоматизированное. В 1950 г. завод впервые в стране произвел трубозаготовительный стан новейшей конструкции, который предназначался для производства высококачественной катаной трубной заготовки. Кроме металлургического машиностроения, новокраматорцы выпускали такую специфическую продукцию, как валы гидрогенераторов, цельнокованые барабаны для котлов высокого давления, кузнечно-прессовое оборудование. Это, конечно, были уникальные, преимущественно штучные изделия, которые изготавливались по заказу конкретных предприятий. В 1948 г. на заводе началось производство мощных экскаваторов с ковшом емкостью 3м3. В следующем году было начато проектирование шагающих экскаваторов [160].
Транспортное машиностроение Донбасса было сосредоточено на Ворошиловградском паровозостроительном заводе. Это было одно из ведущих предприятий не только региона, но и всей страны по производству локомотивов. Накануне войны завод выпускал почти половину всех паровозов страны. В послевоенные годы на предприятии велась активная работа по модернизации и совершенствованию техники. В 1949-1951 годах на заводе был спроектирован мощный грузовой паровоз типа 1-5-1. В начале следующего года завершено строительство очередной серии локомотивов – паровоза 1-5-2. На нем впервые в мировой практике паровозостроения были использованы оригинальные паровые машины, которые повышали мощность машины, упрощали ее обслуживание. Одновременно разрабатывались и другие перспективные типы локомотивов.
Таким образом, восстановление машиностроительного комплекса Донбасса, как и в целом Украины, в послевоенные годы проходило достаточно успешно.
Как свидетельствуют материалы таблицы, в течение четвертой пятилетки количественные объемы производства машиностроительной промышленности Сталинской области не только достигли довоенного уровня, но и были превзойдены. В области особенно интенсивно развивалось производство машин и оборудования для тяжелой промышленности. В 1950 году производство угольных комбайнов увеличилось по сравнению с 1940 годом в 15,6 раза, металлорежущих станков – в 4 раза, металлургического оборудования – в 1,5 раза. Подобная ситуация характерна и для Ворошиловградской области, особенно в станкостроительной отрасли: в 1950 году металлорежущих станков было произведено в почти в 25 раз больше, чем в 1945 г.
Вместе с тем, несмотря на положительную динамику восстановления машиностроительного комплекса, в отрасли существовал ряд серьезных проблем. В послевоенные годы в индустриально перегруженном регионе, по сути, было сосредоточено почти все тяжелое машиностроение республики, что значительно увеличило техногенное воздействие на экологическую и социальную системы региона. В машиностроении, как и в других отраслях, основное внимание уделялось не качественным, а количественным показателям. Конечно, ассортимент продукции, постепенно обновлялся, некоторые образцы освоенной продукции по своим технико-экономическим показателям даже достигли мирового уровня, однако в целом, в условиях плановой экономики, организационной и технологической неустроенности, отсутствия конкуренции, качество машиностроительной продукции была невысоким.
Главным критерием оценки деятельности машиностроительных заводов, как и других предприятий, оставалось своевременное выполнение количественных, валовых плановых показателей. Более того, иногда эти критерии, на наш взгляд, были абсурдными. Например, производство металлургического и некоторого другого оборудования оценивалось в тоннах. Подобный подход приводил к тому, что производители не были заинтересованы в снижении материало- и энергоемкости продукции. Так, в целом по стране средний вес станков увеличился с 1,92 т в 1940 г. до 2,85 т – в 1950 г. [162]. Оставалась нерешенной и проблема механизации трудоемких процессов в машиностроении. В 1950 г. больше половины рабочих машиностроительных заводов были заняты ручным трудом. На большинстве предприятий удельный вес времени станочных операций в общем количестве затраченного времени колебалась от 25 до 50%, а удельный вес ручного труда – от 50 до 75% [163]. При малосерийном и штучном производстве, характерном для многих машиностроительных заводов Донбасса, удельный вес ручного труда, естественно, значительно повышалась. Например, при изготовлении паровозов на Ворошиловградском паровозостроительном заводе ручной труд составлял более 55% общей трудоемкости этой машины [164]. Кроме того, на многих предприятиях оставались нерешенными многочисленные организационно-технические вопросы: достаточно часто нарушались трудовая и производственная дисциплина, неудовлетворительной была организация производства, наблюдалась неритмичность в работе, не хватало инструмента, оборудования.
Химическая промышленность наряду с топливно-энергетическим комплексом и металлургией, является одной из ведущих в структуре экономики Донбасса. От ее развития в значительной степени зависит уровень научно-технического прогресса, она существенно влияет на работу всех основных отраслей промышленности, транспорта, сельского хозяйства, бытового обслуживания и другие сферы экономики.
Анализ развития этой отрасли свидетельствует, что структура химического комплекса Донбасса была достаточно сложной. В его состав входило ряд специализированных отраслей, которые используют разное сырье, изготовляли очень широкий ассортимент продукции и объединялись между собой общей технологией. В течение послевоенного периода комплекс химических подотраслей и производств, их состав и экономическая группировка под влиянием научно-технического прогресса, ускоренных темпов развития, специализации и других факторов, постоянно менялись, что, кстати, значительно усложнило изучение эволюции химической промышленности.
Ведущее место в химической индустрии региона в исследуемый период занимали предприятия основной химии, которая включала в себя такие подотрасли, как азотную, фосфатных удобрений, содовую, хлорную, а также производство другой продукции органической и неорганической химии. Кроме того, важную роль в химическом комплексе занимали предприятия по изготовлению синтетических красителей, лако-красочных, пластмассовых изделий. Нефтехимическую промышленность представляли заводы по изготовлению сажи, резиновых изделий, фенола и другой продукции.
При этом стоит отметить, что химические предприятия обычно производили неоднородную продукцию, поэтому в классификации отраслей промышленности они принадлежали к той отрасли (подотрасли), которой соответствовала большая часть производимой продукции в стоимостном выражении [165]. Поэтому, несмотря на это, мы должны подчеркнуть, что структурное деление подотраслей химической промышленности, является несколько условным.
Анализируя развитие химической промышленности региона в послевоенные период, следует отметить, что в эти годы происходило восстановление инфраструктуры химической промышленности, налаживался выпуск преимущественно производимой до войны продукции; восстанавливалось и внедрялось в действия то производство, которое действовало до войны, а также осваивался выпуск новой продукции.
Учитывая потребности сельского хозяйства, особое внимание уделялось восстановлению производства минеральных удобрений, прежде всего азотных, фосфатных. Первым предприятием, которое возобновило выпуск химической продукции, был Горловский азотнотуковый завод (с 1975 года – ПО «Стирол»): уже с апреля 1944 г. на заводе началось производство кислорода, с ноября – аммиака, а с марта 1945 г. – азотной кислоты и аммиачной селитры [166].
Несколько медленнее происходили восстановительные работы на Лисичанском (с 1951 г. – Северодонецкий, позже – ПО “Азот”) химическом комбинате, основное оборудование которого в начале войны было демонтировано и вывезено, как и других заводов в восточные районы страны, а то, что осталось – разрушено во время оккупации. Учитывая необходимость значительного расширения производства удобрений и другой химической продукции для сельского хозяйства, постановлением Пленума ЦК ВКП (б) (февраль 1947 г.) Совету Министров СССР специально поручалось «принять меры по обеспечению ускоренного строительства Лисичанского химкомбината в 1947 г.» [167]. После этого решения строительно-монтажные работы значительно ускорились, и в 1951 г. предприятия комбината начали выпускать первую промышленную продукцию – азотную кислоту и аммиачную селитру [168]. Первые два года завод использовал для изготовления продукции аммиак, привезенный с других предприятий, что, конечно, усложняло процесс производства. Однако уже в 1953 г. на комбинате был построен собственный завод синтетического аммиака, который добывался с помощью газификации коксующегося угля [169]. Это позволило комбинату значительно расширить номенклатуру продукции: был налажен выпуск углеаммонийной соли, натриевой селитры, формалина. Особое значение имело освоение выпуска метанола, который широко использовался при изготовлении синтетических смол, пластмасс, в лакокрасочной промышленности, при производстве клея, ядохимикатов, каучука и другой химической продукции.
Уже в первые послевоенные годы возобновилось производство фосфатных удобрений на Константиновском химическом комбинате. Следует добавить, что в годы войны завод был почти полностью разрушен, поэтому, по сути, он не просто восстанавливался, а создавался заново. Предприятие изготавливало преимущественно серную кислоту и суперфосфат. Производство последнего значительно расширилось за счет освоения огромных месторождений фосфатного сырья – фторапатитов на Кольском полуострове.
В течение первой послевоенной пятилетки в регионе почти полностью восстановилось содовое производство. Уже с 1944 г. начали работать Донецкий (Лисичанский) и Славянские (Старо – и Новосодовый) содовые комбинаты [170], в 1948 г. на базе Славянских заводов было создано единое предприятие. Концентрация производства позволила более рационально использовать производственные и трудовые ресурсы, снизить административно-управленческие расходы, а также создать условия для совершенствования техники и технологии производства. Так, производство соды в течение 1945-1950 гг. возросло, в частности, в Ворошиловградской области в 3,3 раза.
Достаточно быстрыми темпами, восстанавливалось производство синтетических красителей, которое было сосредоточено на единственном в Украине производителе этих химических веществ – Рубежанском химическом комбинате (позже – ПО «Краситель») [171]. Накануне войны завод производил 14 марок синтетических красителей и был одним из ведущих предприятий в своей отрасли. Однако в годы войны, как и многие другие предприятия, он был почти полностью разрушен, поэтому восстановительные работы сопровождались строительством новых производственных комплексов, что способствовало расширению ассортимента продукции завода. В частности, в первые послевоенные годы здесь был освоен выпуск полупродуктов, а также новых видов красителей (азотолей, индиго и других). В 1956 г. на комбинате был введен в строй первый в стране цех по выпуску высококачественных водорастворимых форм кубовых красителей. Это был очень сложный многостадийный процесс, в результате которого создавались яркие и стойкие синтетические красители.
Довоенный уровень производства синтетических красителей в регионе был превзойден уже в четвертой пятилетке, а к концу 1950-х годов их производство удвоилось.
Одновременно с восстановлением химического производства происходило перепрофилирование и специализация предприятий. В частности, уже в первые послевоенные годы в регионе на базе как действующих, так и новых мощностей, началось производство химических реактивов, фармацевтических и других химических препаратов. Так, Сталинский азотный завод, который ранее специализировался на производстве азотной кислоты, в послевоенные годы почти полностью изменил номенклатуру производимой продукции: в процессе восстановления, по сути, был создан новый завод по изготовлению химических реактивов, который в дальнейшем стал ведущим производителем этой важной химической продукции в регионе. До конца 1950-х годов завод освоил и выпускал сотни (в 1958 г. – 260) различных химических реактивов, которые стали его основной продукцией [172]. В эти годы некоторые химические реактивы выпускал также Рубежанский химический комбинат.
В ходе специализации предприятий значительные изменения произошли на Горловском азотнотуковому заводе. Здесь в 1952 г. был построен цех этилбензола – основного вида сырья для получения стирола. По сути, со строительства этого цеха началось перепрофилирование всего производственного процесса на предприятии: до конца 1950-х годов завод освоил и наладил выпуск стирола и его сополимеров, а также полистирола, поропластов и другой сопутствующей химической продукции. Позже она стала основной в ассортименте заводской продукции.
В послевоенные годы, в условиях восстановления хозяйства, значительно возросли потребности в лакокрасочной продукции. Для развития этой отрасли в Донбассе было необходимое сырье (стирол, фталевый ангидрид, растворители и другие материалы). Производство лаков и красок сконцентрировалось преимущественно на двух предприятиях – Сталинском и Ворошиловградском заводах красок, хотя в целом эту продукцию производили 10 предприятий региона [173].
Фармацевтическое производство Донбасса было сосредоточено на Ворошиловградском химико-фармацевтическом заводе и Сталинском заводе химических реактивов. Отдельные медицинские препараты производились также на других химических заводах.
Для химической промышленности Донбасса в послевоенные годы была характерна еще одна тенденция: одновременно с восстановлением производства происходило совершенствование технологии, модернизация оборудования, а также механизация и автоматизация производственных процессов. Следует подчеркнуть, что необходимость постоянного технологического усовершенствования в значительной степени была обусловлена спецификой химического производства, особенностями изготовления конкретных видов продукции. В этой области, в отличие от других промышленных производств, много процессов происходило автоматически, что требовало постоянного контроля и управления ими, поэтому эта отрасль промышленности была одной из наиболее наукоемких, а производство – наиболее механизированным. Показательным в этом отношении было содовое производство, в котором уже в послевоенные годы произошло значительное усовершенствование технологии. Так, внедрение в производство кальцинированной соды предварительной карбонизации аммонизированного рассола, а позже – глубокой карбонизации способствовали снижению простоев оборудования, уменьшению затрат сырья и сопутствующих материалов и, как следствие – увеличению выпуска соды. Ряд технических усовершенствований, в частности, внедрение предварительной очистки рассола способствовали повышению качества кальцинированной соды [174]. Такие же процессы происходили и в других производствах химической отрасли.
Анализ развития химического комплекса Донбасса во второй половине 1940-х – начале 1950-х годах позволяет утверждать, что в целом в отрасли происходили позитивные изменения: почти во всех основных производствах возрос выпуск валовой продукции, особенно характерно это было для азотной промышленности, производства синтетических красителей, химических реактивов и другой продукции. Улучшились в целом и экономические показатели, о чем свидетельствует опыт ведущих предприятий отрасли: довольно высокими были темпы роста производительности труда, фондоотдачи, значительной оставалась рентабельность производства, ведущие предприятия работали прибыльно [175]. Вместе с тем, следует подчеркнуть относительность этих успехов. Бесспорно, сделано было много, но оно не соответствовало даже тогдашним, заниженным потребностям общества. Подобный разрыв между желаемым и имеющимся, на наш взгляд, был обусловлен, прежде всего, очень низким начальным уровнем развития отрасли, значительным ее общим отставанием от промышленно развитых стран.
Со значительными трудностями происходило послевоенное возрождение и развитие энергетического хозяйство Донбасса, которое в годы войны понесло огромные разрушения. В Ворошиловградской области, например, в 1945 г. было выработано электроэнергии лишь 25,6% довоенного уровня [176]. Учитывая огромную потребность в электроэнергии, тепловые электростанции начали восстанавливать уже с конца 1943 г. При этом основой, исходным положением восстановительных работ, как и в других отраслях, была идея скорейшего восстановления того, что было до войны. В этих условиях обычной практикой была замена лишь отдельных узлов, агрегатов, их ремонт без кардинальной реконструкции. Надо отметить, что во время этих работ действительно часто принимались неординарные решения, специалисты и рабочие проявляли творческий подход к решению сложных технических проблем.
Масштабные восстановительные работы начались в послевоенное время. Четвертым пятилетним планом мощность электростанций Украины планировалось увеличить на 2574 тыс. кВт и довести выработку электроэнергии до 13,7 млрд. кВт, что на 15 % превышало довоенный уровень [177]. Важную роль в решении эти задач должна была играть система “Донбассэнерго”, которая объединяла энергосистемы Сталинской и Ворошиловградской областей. Уже в первые послевоенные годы в целом были отстроены все крупнейшие тепловые электростанции региона. К концу четвертой пятилетки завершилось восстановление Зуевской, Штеровской, Северодонецкой, Кураховской электростанций. В 1949 г. началось строительство Мироновской теплоэлектростанции. Именно на этих электростанциях начали устанавливать новые, более мощные турбины и котлы, которые работали под повышенным давлением пара (100 атм.) и температурой перегрева (до 5000 С). Внедрение в эксплуатацию нового, более совершенного оборудования позволило повысить довоенную мощность станций примерно на 15% [178], в то же время сокращались расходы топлива на производство электроэнергии [179]. Все это способствовало достаточно интенсивному наращиванию энергетических мощностей. Так, в течение 1945-1950 годов производство электроэнергии в Ворошиловградской области увеличилось в 3 раза [180], хотя довоенного уровня еще не было достигнуто.
Отмечая позитивные изменения в отрасли, вместе с тем, подчеркнем, что в условиях затратной экономики, ориентированной на наращивание, прежде всего количественных показателей, почти не уделялось внимание рациональному использованию электроэнергии. Ее основными потребителями, как и раньше, были промышленность и строительство, которые в 1950 г. использовали 71,4 % потребленной электроэнергии в народном хозяйстве республики [181]. При этом довольно часто наблюдалось бесхозяйственное отношение к энергетическим ресурсам, что было обусловлено их непроизводительными расходами и потерями из-за неполной загрузки оборудования, неправильным ведением технологических процессов, плохим состоянием оборудования и сетевого хозяйства. Особенно большие потери допускались в металлургической и угольной промышленности. Например, на заводе «Азовсталь» и других металлургических предприятиях главные приводы и вспомогательное оборудование при длительных остановках прокатных станов часто не отключались, что приводило к значительным непроизводительным затратам электроэнергии. Миллионы киловатт-часов электроэнергии перерасходовались вследствие нарушений технологического процесса выплавки металла. Подобная ситуация была и в угольной промышленности. Так, на шахте им. Орджоникидзе треста «Макеевуголь» только через применение привода вентилятора электродвигателя завышенной мощности ежегодно тратилось непродуктивно 700 тыс. кВт. час. Довольно значительные потери допускались также в сетях общего пользования: ежегодно они составляли примерно 7 % от всей использованной электроэнергии промышленностью республики [182].
Конечно, неэффективное использование электроэнергии требовало постоянного наращивания ее производства, что, в свою очередь, приводило к непроизводительным затратам угля и другого сырья и материалов. Впрочем, расточительство было общей проблемой плановой экономики, ориентированной не на качественные, а на количественные показатели.
Таким образом, восстановление разрушенного во время войны промышленного комплекса Донбасса в основном завершилось к началу 1950-х годов. Несмотря на значительные разрушения, наращивание промышленного потенциала происходило высокими темпами, особенно это было характерно для металлургической и угольной отраслей, в меньшей степени – для химической промышленности. Ускоренное развитие базовых отраслей реальной экономики было обусловлено прежде всего их значимостью и ролью в общегосударственном хозяйственном комплексе.
Вместе с тем, в условиях форсированного возрождения предприятий часто преобладал принцип «сделать так как, как было до войны», при этом не уделялось должного внимания внедрению новой техники и технологий. Основной акцент, как и в прежние годы, был сделан на развитии тяжелых отраслей промышленности, усугубляя тем самым экологическую ситуацию в регионе.
Тема: Донбасс во второй половине 1970-х – середине 1980-х
Во второй половине 1960-х-первой половине 1980-х годов в Донбассе в результате сложившегося общесоюзного разделения труда, как и прежде, ведущими оставались сырьевые отрасли: угольная и металлургическая, важным сегментом экономики были также машиностроение, энергетика, химическая промышленность.
В производственном комплексе Донбасса ведущую роль продолжала играть угольная отрасль. В эти годы, по сути, начался процесс реструктуризации угольной промышленности: закрывались убыточные предприятия, добыча угля концентрировался на крупных предприятиях, наряду со строительством новых, реконструировались действующие шахты. За два десятилетия (1960-1980 гг.) в Украине было закрыто более 200 старых, нерентабельных шахт. Одновременно, чтобы не снижать объемов угледобычи, вводились в действие новые шахты. С середины 1960-х до конца 1970-х годов объем введенных новых мощностей составил почти 61 млн. т, а «чистый» прирост (с учетом потери мощностей закрытых шахт) был равен около 40 млн. т. угля.
В условиях концентрации производства на крупных предприятиях с 1960 до 1979 года количество шахт сократилось с 582 до 323. В Донбассе в 1970-е годы были введены в эксплуатацию такие крупные шахты, как «Южнодонбасская» №1, им. Скочинского, «Ясиновская-Глубокая», «Ждановская-Капитальная», первая очередь крупнейшей в Украине шахты «Красноармейская-Капитальная» (мощностью 1700 тыс.т. угля ежегодно) и другие. В целом в течение только 1971-1975 гг. было введено в действия производственных мощностей по добыче угля на 29 млн. т ежегодно [64]. В следующей пятилетке темпы обновления шахтного фонда даже несколько ускорились по сравнению с предыдущим пятилетием.
Осуществлялись мероприятия по улучшению технического оснащения шахт. Шахты начали получать комплексы с механизированным креплением, узкозахватные проходческие комбайны, роторные экскаваторные комбайны и другое более совершенное оборудование. Например, на шахтах Донецкой области за период с 1970 г. по 1985 г. количество передвижных механизированных креплений увеличилось с 75 до 483 единиц (почти в 6,5 раз), проходческих комбайнов – с 84 до 488 единиц (в 5,8 раза) [65]. К концу 1970-х годов уровень механизации наиболее трудоемкого процесса – навалки угля в лавах был доведен до 98%. Полностью были механизированы откатка угля и породы, а также погрузка угля в железнодорожные вагоны. На шахтах Донбасса впервые в мировой практике были внедрены угледобывающие комбайны на тонких крутопадающих пластах. Однако все эти попытки дать импульс дальнейшему развитию угольной промышленности, придать второе дыхание ведущей отрасли региона особого успеха не имели.
Как видно из материала таблицы, в начале 1970-х годов шахты Донбасса добывали рекордное количество угля, но с середины десятилетия объемы добычи неуклонно снижались. Если в Донецкой области в 1971 году было добыто 107,1 млн. т, то в 1990 году – только 80,5 млн. т угля [67], в Ворошиловградской области угледобыча снизилась соответственно с 74 до 51,6 млн. т [68].
Анализ архивных и опубликованных материалов, статистических данных свидетельствует, что на ухудшение ситуации в угольной промышленности влияли как объективные, так и субъективные факторы. Снижение угледобычи было обусловлено в значительной степени ухудшением горно-геологических условий на шахтах Донбасса. С середины 1970-х годов в регионе началось широкомасштабное освоение месторождений угля на больших глубинах. Если в 1975 г. средняя глубина разработки составляла 540 м, в 1980 г. – 590 м, то в 1985 г. – 620 м, а на некоторых шахтах уголь добывали на глубине 1-1,2 км. На такой глубине резко возрастали температура, газоносность, горное давление и опасность внезапных выбросов угля и газа. В конце 1980-х годов 87 % шахт были газоопасными [69]. Ситуация осложнялась и тем, что уголь добывали преимущественно из чрезвычайно тонких пластов. В середине 1970-х годов в донецком регионе почти 14 % угля добывалось из пластов мощностью до 0,7 м, для выемки которых не было эффективных средств механизации, а 43 % – из пластов мощностью до 1 м. В других угольных регионах СССР и зарубежных странах подобные пласты редко или совсем не разрабатывали [70].
Не способствовала развитию угольной промышленности Донбасса и государственная инвестиционная политика. Хотя в абсолютных показателях капиталовложения в отрасль увеличивались, однако они не соответствовали ее потребностям. Более того, даже запланированные и предусмотренные на реконструкцию отрасли средства постоянно сокращались. На 1971-1975 годы инвестиции в угольную промышленность республики намечались в сумме 4,6 млрд. руб., а фактически отрасль получила лишь около 4,1 млрд. руб., то есть недофинансирование составило почти 11 % [71]. Подобная ситуация сложилась и следующей пятилетки: из запланированных на 1976 – 1980 годы 5,5 млрд. руб. капиталовложений угольная промышленность получила лишь 5,2 млрд. руб., тогда как, по подсчетам специалистов, для модернизации угольных шахт нужно было не менее 7 млрд. руб. [72]. При этом удельный вес государственных капиталовложений в объеме общих инвестициях в отрасль постоянно уменьшался.
Недостаточное инвестирование угольной промышленности во многом обусловило замедление темпов шахтного строительства. В первой половине 1970-х годов были заложены 4 шахты общей мощностью 9 млн. т, что составляло около половины от запланированных показателей. В последующие годы темпы обновления шахтного фонда еще более замедлились. Сроки сооружения новых шахт, вместо 5-7 лет, согласно нормам, затягивались до 15-20 лет, в 2-3 раза превышая нормативные требования и сроки реконструкции шахт. В 1970-е годы ни одна шахта Донбасса не была построена вовремя, а начале 1980-х годов шахтное строительство было фактически свернуто. На 1981-1985 годы на строительство были выделены мизерные средства – 12 % от общей суммы инвестиций в угольную отрасль, однако даже и эти средства не были освоены. По плану одиннадцатой пятилетки (1981-1985 гг.) предусматривался прирост мощностей за счет нового строительства на 21 млн. т, который фактически составил в 10 раз меньше – 2,1 млн.т. В 1981-1985 годах, впервые за послевоенные годы было введено мощностей меньше, чем выбыло. Как и ранее, значительно затягивались сроки ввода в эксплуатацию строящихся шахт. Так, шахты «Самсоновская Западная», «Суходольская-Восточная» (Луганская обл.) строились более двух десятилетий, причем за этот период на их строительство было выделено лишь 40 % необходимых средств, на шахте им. Гагарина реконструкция велась так медленно, что для ее завершения и освоения, предусмотренных на эти цели средств потребовалось бы 125 лет, а на шахте «Украина» сроки завершения реконструкции неоднократно переносились с 1985 на 1995 год [73].
В 1970 – начале 1980-х годов значительно снизилась эффективность модернизационных работ. Как справедливо подчеркнула исследовательница этой проблемы З. Г. Лихолобова, «главная трагедия была не в сокращении шахтного фонда, а в ухудшении состояния действующих шахт» [74]. Надо отметить, что, на первый взгляд, обновление имеющегося производственного фонда происходило достаточно интенсивно: вводились в действия новые угольные горизонты; строились новые шахтные стволы или реконструировались действовавшие; мелкие шахты объединялись в одно производственное предприятие; модернизировались схемы шахтного транспорта, ликвидировалась его многоступенчатость; внедрялись более совершенные и прогрессивные способы подготовки и обработки пластов, предпринимались и другие меры.
Кроме того, в процессе модернизации на многих шахтах проводились локальные мероприятия по техническому переоснащению отдельных комплексов и узлов. В первой половине 1980-х годов на техническое переоборудование и поддержку имеющегося шахтного фонда было использовано 71 % общего объема капиталовложений, направленных на развитие угольной промышленности [75].
Но, как показывает опыт, результативность модернизационных усилий оказалась незначительной. Это было обусловлено, прежде всего, не комплексным, выборочным подходом к обновлению основных фондов. Модернизация и техническое переоборудование только отдельных звеньев производственного процесса, как это обычно делалось, приводили лишь к кратковременному положительному результату. Эффективность этих мер практически исчерпывалась уже через несколько лет. Но даже эта частичная, не комплексная модернизация проводилась очень медленно. Из-за отсутствия достаточных средств, ошибок, допущенных при разработке проектов модернизации шахт, недостаточной мощности шахтостроительных организаций, организационно-технические неурядицы обновление производства затягивалось на долгие годы.
Более того, похожая ситуация была и с освоением мощностей реконструируемых предприятий: ни одна из реконструированных в 1970-е годы шахт не достигла к 1980 г. запланированной мощности. В целом, несмотря на усилия по модернизации отрасли, состояние шахтного фонда неуклонно ухудшалось. Если в 1970 г. шахты, которые работали без технической реконструкции более 20 лет, составляли 36 %, то в 1985 году – 72 % [76].
Значительно повлияла на снижение темпов угледобычи в Донбассе недостаток прогрессивной высокопроизводительной техники. Надо отметить, что со второй половины 1960-х годов в очистных забоях парк машин за счет широкого применения узкозахватных проходческих комбайнов, струговых установок, конвейеров и других новых, более совершенных средств механизации и автоматизации ощутимо обновился, однако довольно часто эта техника не была приспособлена к условиям Донбасса, а потому использовалась неэффективно. Так, в начале 1970-х годов комплексом КМК-97, кстати, это был единственный угледобывающий комплекс для тонких пластов мощностью до 1,2 м, можно было добывать не более 20 % угля из подобных пластов.
В целом же фактический уровень комплексной механизации на этих пластах составлял лишь 11 %. Технический уровень очистных работ на маломощных пластах (менее 0,7 м) мог быть повышен при освоении серийного производства узкозахватных комбайнов типа 2УК («Луч»), БКТ, К-102, предназначенных для разработки пластов мощностью 0,55-0,8 м, но работы по созданию этой серии комбайнов, которые начались еще в середине 1960-х годов, затормозились, в результате чего к концу 1970-х годов этой техники на шахтах так и не было [77].
Чрезвычайно острой оставалась проблема механизации очистных забоев крутых и наклонных пластов, особенно маломощных. В 1975 г. из таких пластов было добыто 33 млн. т. угля, из них почти 20 млн. т, то есть почти 60 % – с помощью отбойных молотков. Более того, на отдельных шахтах центрального района Донбасса основная угледобыча (70-80 %) происходила только с использованием ручного труда.
В последующие годы ситуация не улучшилась. При этом стоит заметить, что новой техники не только не хватало, но достаточно часто она оказывалась низкого качества. Это приводило к росту числа аварий, увеличению ремонтных затрат, снижению эффективности использования техники и к другим негативным последствиям. В 1985 г. на некоторых шахтах коэффициент использования угледобывающей техники составлял лишь 33 % [78].
Использование устаревших технологий и оборудования, несвоевременная модернизация производственных процессов усиливали затратный, неэффективный характер экономики. Например, в 1984 г. на шахтах Украины из-за несовершенства технологии и расточительства было перерасходовано 240 млн. кВтч электроэнергии на 2,4 млн. руб., а также 25 млн. м древесины на сумму 1,1 млн. руб.
Вообще для большинства предприятий характерно было применение завышенных норм расхода сырья, материалов, топлива, электроэнергии, что позволяло руководителям предприятий приукрашивать состояние дел на производстве [79]. Указанные причины, в совокупности с другими, обусловили постепенный упадок угольной промышленности Донбасса. Об этом свидетельствуют тенденции развития отрасли в Донецкой области.
Согласно данным таблицы, на общем фоне роста производственных фондов, капитальных вложений, численности трудовых ресурсов, фондооснащенности многие важные количественные и стоимостные показатели постепенно уменьшались. Так, с 1975 г. по 1985 г. производственные фонды отрасли увеличились на 2163,5 млн. руб., количество производственного персонала возросло на 92,1 тыс. чел., фондооснащенность увеличилась с 15,2 тыс. руб./чел. до 17,3 тыс. руб./чел. руб., капитальные вложения (в 1981-1985 гг. по сравнению с предыдущим пятилетием) – на 401, 3 млн. руб.
Однако, несмотря на эти положительные тенденции, основные производственные и экономические показатели уменьшились: производительность труда сократилась с 10,2 тыс. руб./чел. до 7 тыс. руб./чел., фондоотдача с 0,67 до 0,40 руб./руб. Особое внимание следует обратить на нерациональное, неэффективное, расточительное использование сырьевых ресурсов. При значительном сокращении угледобычи (со 105,4 млн. т в 1975 г. до 93,2 млн. т в 1985 г.) расход электроэнергии в угольной промышленности увеличился на 13,4%, топлива – в 2,1 раза.
Ухудшились и другие экономические показатели, прежде всего себестоимость и рентабельность. В Донбассе в 1960 г. себестоимость добычи одной тонны угля составляла 11,26 руб., а в 1985 г. – 26,56 руб. Уголь Донбасса стал самым дорогим в СССР. Затраты на добычу одной тонны донецкого угля превышали аналогичные показатели в Кузбассе, Караганде и Печорском бассейне примерно в полтора-два раза [81].
С середины 1970-х годов угольная отрасль Украины постепенно становилась все более убыточной. Если в 1970 г. уровень рентабельности угольных предприятий составил 7,2 %, в 1974 г. – 1,6 %, то в следующем году – минус 2,1 %, а к 1980 году уровень убыточности увеличился почти до 10 %. В 1975 году убытки шахт составили 167 млн. руб. и в дальнейшем увеличивались.
При этом качество топлива значительно ухудшилось. Удельный вес породы в донецком угле возрос с 15 % в 1960 г. до 39,5 % в 1987 г., а в антрацитах – с 19 % до 37 % [82]. Все это свидетельствовало о том, что в второй половине 1960-х-первой половине 1980-х годов так и не было найдено эффективного механизма улучшения работы угольной промышленности, ведущая отрасль региона постепенно приходила в упадок.
Во второй половине 1960-х-первой половине 1980-х годов металлургический комплекс, как и раньше, оставался одним из ведущих секторов экономики Донбасса. С 1971 г. по 1980 г. основные производственные фонды отрасли увеличились на 80 %. В течение этого десятилетия на металлургических заводах, в том числе и Донбасса, были введены в эксплуатацию ряд уникальных агрегатов. К ним можно отнести прокатный стан «3600» мощностью 1850 тыс. т стального листа в год, первая очередь которого была пущена в январе 1974 г. на заводе «Азовсталь». По производительности, сортаменту продукции, уровню механизации и автоматизации он не имел равных в Европе. В декабре 1977 г. на этом же заводе был введен в эксплуатацию кислородно-конвертерный цех, при строительстве которого учитывались новейшие достижения науки и техники [83]. На Донецком металлургическом заводе были введены в строй заготовочный стан и первая очередь электросталеплавильного цеха (июнь 1978 г.) производительностью 230 тыс. т стали в год. В июле 1974 г. на Харцызском трубном заводе была сдана в эксплуатацию первая очередь цеха по производству труб большого диаметра. Выполнялись также работы по модернизации и реконструкции существующих агрегатов и установок на других предприятиях [84].
Предпринятые меры по развитию металлургии региона позволили нарастить объемы производства основных видов продукции. В течение 1965-1985 годов металлургические предприятия региона постоянно наращивали выпуск металла и труб. Производство чугуна увеличилось в 1,4 раза, стали и проката – почти в полтора раза, стальных труб – более, чем в 1,8 раза. Вместе с тем, несмотря на достаточно успешную работу отрасли, уже с начала 1970-х годов в металлургической промышленности региона начали накапливаться негативные явления, которые своевременно не решались, что привело к обострению ситуации в отрасли, ухудшению не только количественных, но и качественных показателей производства.
Негативные тенденции в развитии отрасли были обусловлены как объективными, так и субъективными факторами. Одними из важнейших факторов негативного воздействия на работу металлургии были недостаток железорудного сырья и кокса и снижение их качества.
Ухудшение топлива и сырья было связано, прежде всего, с завершением в начале 1980-х годов отработки подавляющей части легкообогащаемым, расположенных близко к поверхности запасов железных руд в Украине. Глубина многих карьеров горно-обогатительных комбинатов достигла проектной отметки – 260-280 м, а железорудных шахт в Кривбассе – до 1000 м, и продолжала увеличиваться. В первой половине 1980-х гг. глубина карьеров ежегодно увеличивалась в среднем на 12,2 м, а железорудных шахт – на 19 м [86]. Вскрышные выработки, горное оборудование, транспортные коммуникации, подъемные средства шахт приблизились к пределу своих технических возможностей.
На большинстве шахт Кривого Рога довольно быстро сокращались рудные площади, что приводило не только к уменьшению объемов добычи руды, а и к снижению ее качества: в ней уменьшалось содержание железа, повышался удельный вес бедных руд, требующих обогащения и окускования. Так, содержание железа в переработанной сырой руде на горно-обогатительных комбинатах Кривбасса сократился с 35,4 % в 1965 г. до 33,9 % в 1985 г. и продолжало уменьшаться [87].
Некачественная руда обогащалась на агломерационных фабриках, но их мощности не удовлетворяли потребностям металлургии. Уровень получения железа из руды не только не повышался, а наоборот – снижался и составил в 1980 г. 75,4 % [88], что приводило к ежегодной потере металлургическими заводами региона примерно 500-600 тыс. т чугуна. К тому же устаревшая техника и несовершенные технологии обусловили низкое качество производимого агломерата. По подсчетам специалистов, только за счет снижения до нормы мелочи в агломерате производство чугуна можно было увеличить на 120-140 тыс. т [89].
Важным резервом повышения эффективности металлургического производства было улучшения качества и снижения расхода кокса. Производство этого основного доменного топлива с середины 1970-х годов начало сокращаться, что было обусловлено, прежде всего, устаревшими фондами коксохимической промышленности, а также дефицитом коксующегося угля.
С конца 1970-х годов в Донбасс начали завозить ежегодно более 10 млн. т коксующегося угля из Кузнецкого, Печорского и Карагандинского бассейнов. Все это негативно сказывалось на экономических показателях отрасли: расходы на кокс составляли 40 % себестоимости чугуна [90]. К тому же его постоянно не хватало.
Чрезвычайно сложной проблемой металлургической отрасли было старение основных фондов. Конечно, нельзя утверждать, что в 1970-1980-е годы вообще не проводились работы по обновлению производственных мощностей. Но единичные новостройки не могли кардинально улучшить положение в отрасли: старение основных фондов металлургических предприятий неуклонно росло. Так, в 1965 г. средний “возраст”, например, коксовых батарей составлял 12,7 года, а в 1985 г. – 21,3 года. Удельный вес коксовых батарей, которые работали более 25 лет (норма амортизации – не более 15 лет), на начало 1986 г. составляла 34,2 %. В конце 1980-х годов износ основных фондов коксохимических заводов Украины превышал 60 % [91]. Такое же положение было в доменном, сталеплавильном, прокатном и других производствах. К концу 1985 г. почти 67 % доменных печей, которые находились в эксплуатации, отработали свой ресурс, мартеновских печей – 91 %, прокатных станов – 79 % [92].
Подобные процессы происходили и на металлургических предприятиях Донбасса: если в 1980 г. износ основных фондов заводов черной металлургии региона составлял 44 %, то в 1990 г. – 61 %, и был самым высоким среди ведущих отраслей промышленности. Наиболее устаревшими были мощности на Ясиноватском коксохимзаводе – износ фондов составил 88 %, Константиновском металлургическом заводе – 87 %, Енакиевском и Мариупольском коксохимзаводов – 79 %, Макеевском металлургическом комбинате – 75 %. На устаревшем оборудовании выпускалась продукция и на других предприятиях [93].
Главной причиной старения мощностей отрасли было замедление темпов обновления имеющихся фондов. Коэффициент обновления фондов снизился с 4,8 % в 1985 г. до 3,2 % в 1988 г. При этом инвестиции, которые выделялись на развитие отрасли, почти ежегодно не осваивались: в 1986 г. было освоено лишь 83 % [94]. Такая ситуация сложилась вследствие распыления средств, недостаточной концентрации материальных и трудовых ресурсов на пусковых объектах черной металлургии.
В этих условиях совершенствование структуры основных фондов, повышение уровня их отдачи во многом зависело от реконструкции и технического переоборудования действующих предприятий. Хотя на эти цели в черной металлургии Донецкой области использовалась подавляющая часть (в 1988 г. – 75 %) инвестиций, однако эффективность реконструкции часто была незначительной, потому что она проводилась не комплектно, допускались ошибки при проектировании и утверждении технической документации, затягивались сроки модернизации, устанавливалось дефектное оборудование и тому подобное.
В целом, несмотря на техническую реконструкцию отдельных производств, отрасль по уровню технологии отставала от промышленно развитых стран. На многих металлургических заводах США, Японии, Германии к этому времени, например, уже отказались от мартеновского способа выплавки стали. На предприятиях же Донбасса он оставался преобладающим. Так, доля кислородно-конвертерной стали и электростали в общем объеме производства заводов Донецкой области составляла в конце 1980-х годов 46 %.
Отставание черной металлургии оказался и в том, что медленно внедрялись установки непрерывной разливки стали, хотя приоритет в открытии этой технологии принадлежал СССР. В 1960 г. такая установка впервые в Европе стала работать на Донецком металлургическом заводе. Однако в конце 1980-х годов удельный вес стали, разлитой на машинах непрерывного литья в США составлял 64 %, в Германии – 88 %, в Японии – 93 %, в СССР – менее 17 %, в Донецкой области – 17,2 %.
Замедление темпов обновления основных фондов, затягивание реконструкции производственных мощностей обусловили рост объемов неустановленного оборудования. Эта проблема начала проявляться уже в первой половине 1960-х годов, а в последующие годы еще больше обострилась. В течение первой половины 1970-х годов складские запасы неустановленного оборудования в Украине увеличились на 10 % и оценивались в начале 1976 г. примерно в 730 млн. руб. [95].
Большие запасы оборудования были сосредоточены, в частности, на металлургических предприятиях. В целом в 1989 г. в Донецкой области хранилось на складах оборудования для черной металлургии почти на 93 млн. руб., что составляло 40 % от суммы всего неустановленного оборудования, причем 79 % из них были импортные машины, техника, приборы, которые по несколько лет не внедрялись в производство [96]. Более того, некомплектность поставки импортного оборудования, постоянные изменения первоначальных вариантов проектов, а также их нарушения при реализации часто приводили не только к моральному и физическому старению техники, но иногда она оказывалась вообще лишней.
В то же время интенсивное использование изношенной техники приводило к ее частым поломкам, авариям, что в свою очередь приводило к росту простоев металлургических агрегатов, увеличению затрат на ремонтные работы. На протяжении 1971-1985 годов на металлургических предприятиях Украины общие затраты на рубль товарной продукции возросли на 5 %, а удельные ремонтные затраты увеличились на 54,7 %. Абсолютная сумма затрат на ремонты и техническое обслуживание фондов в целом по отрасли в 1985 г. составляла около 6 млрд. руб., что вдвое превышало стоимость таких мощных комбинатов, как Магнитогорский и Криворожский, которые производили пятую часть стали в стране [97]. Только на ремонтные работы в течение 1981-1985 годов было потрачено почти 7,7 млрд. руб. [98]. Тратить значительно больше на сохранение устаревшего, чем на внедрение нового, прогрессивного оборудования, конечно, было нерациональной и бесперспективной технической политикой.
Значительное негативное влияние на развитие отрасли оказали просчеты в проведении одного из важнейших направлений промышленной политики конца 1960-х-первой-половины 1980-х годов – концентрации производства и специализации предприятий. В металлургической промышленности концентрация производства проходила в двух направлениях: во-первых, локализация производства на все более крупных агрегатах, то есть строились агрегаты большой единичной мощности; во-вторых, концентрация производства на крупных предприятиях. В общем, это соответствовало мировым тенденциям.
Однако уже первый опыт эксплуатации мощных металлургических агрегатов показал, что многие показатели их работы были не выше, а даже ниже, чем на агрегатах меньшей единичной мощности. Так, в 1979 г., по сравнению с 1970 г., производительность доменных печей возросла на 3,6 %, при этом на печах объемом до 1600 м3 – на 6,8 %, а на больших домнах (объемом более 1600 м3) – всего на 0,5 %. За это же время на малых и средних печах расход кокса сократился на 5 %, а на больших – увеличился на 3,2 % [99]. То есть, на практике большие печи, имея лучшие технологические параметры, во многих случаях не обеспечивали прогрессивный уровень технико-экономических показателей.
Это обусловливалось многими факторами. Среди них, прежде всего, несоответствие прогрессивных проектных требований реальному качеству сырья, параметрам температурно-дутьевого режима. Некачественное железорудное сырье, с большим удельным весом примесей, несбалансированным химическим составом, значительным количеством мелочи, а также снижение температуры и давление дутья значительно осложняли работу крупных агрегатов, приводили к росту их текущих простоев.
По подсчетам специалистов, с увеличением объема доменной печи на 1000 м3 текущие простои возрастали в 1,5 раза. В свою очередь, частые простои приводили к снижению производительности агрегатов. Так, с увеличением объема доменной печи на каждые 100 м3 потери производства за время простоя возрастали на 9-11 тонн [100]. Остановка крупного агрегата, конечно, нарушала работу в целом всего металлургического цикла и имела крайне негативные последствия для экономико-производственных показателей целого завода.
Нестабильность работы многих предприятий металлургической отрасли была обусловлена также организационно-техническими факторами. Архивные документы подтверждают, что наиболее характерными среди них были: несвоевременная и неритмичная поставка сырья и материалов; нарушение трудовой и технологической дисциплины, требований государственного стандарта; необеспеченность предприятий металлоломом; нехватка рабочих основных профессий и их недостаточная квалификация и другие факторы.
Эти и другие просчеты предопределили, несмотря на отдельные достижения и успехи, постепенное затухание темпов развития металлургической промышленности региона. Снижение темпов прироста основных видов продукции отрасли началось еще в конце 1960-х – начале 1970-х годов, а с середины 1980-х годов стал наблюдаться спад производства отдельных видов продукции и в абсолютных показателях.
При этом до середины 1980-х годов продолжалось наращивание объемов производства основных видов продукции металлургии, хотя уже в первой половине 1970-х годов проявилась тенденция к снижению темпов прироста выплавки металла: если в 1966-1970 годах прирост объемов выплавки чугуна составлял 30,3 %, то в следующей пятилетке он снизился до 6,3 %, во второй половине 1970-х годов – составил 1,9 %, а в 1980-1985 годах – лишь 0,9 %.
Такая же ситуация сложилась и с производством другой продукции металлургии. Темпы прироста стали в первой половине 1970-х годов составляли 9,8 %, во второй половине – 5,9 %, а в первой половине 1980-х годов – 0,5 %. Фактически металлургическая промышленность региона, постепенно теряла динамику своего развития, вступила в период стагнации. А с середины 1980-х годов в отрасли начался спад производства основных видов продукции.
Одновременно ухудшились технико-экономические показатели предприятий и эффективность их работы. Это касалось, прежде всего, таких показателей, как фондоотдача, рентабельность. Характерны в этом отношении тенденции развития металлургической промышленности Донецкой области в 1975-1985 годах.
Материал таблицы показывает, что в 1975-1985 годах, несмотря на отдельные положительные тенденции (увеличились капиталовложения в отрасль, особенно в первой половине 1980-х годов, возрос объем средств, выделенных на развитие основных производственных фондов, улучшилась фондовооруженность), эффективность работы металлургических предприятий снизилась. Если капитальные вложения в одиннадцатой пятилетке (1981-1985 гг.) возросли в сравнении с предыдущей пятилеткой почти в 1,3 раза, основные производственные фонды увеличились с 3817 до 6116 млн. руб.( в 1,6 раза), фондовооруженность – в 1,7 раза, то фондоотдача уменьшилась с почти 1,5 руб./ руб. до 1 руб./руб. Подобная ситуация была характерна в целом для металлургии Украины. Если в 1970 г. рентабельность металлургической отрасли республики составляла 17,5 %, в 1975 г. – 12,2 %, то в 1980 г. – примерно 5%. В 1980 г. более половины (50,7 %) металлургических заводов не выполнили план по себестоимости продукции, по этому показателю был допущен перерасход на 342 млн. руб. [102], в следующей пятилетке план по прибыли не выполнен уже на 1,7 млрд. руб. [103].
Одной из ведущих отраслей промышленности региона в исследуемый период было машиностроение. В Донбассе был сформирован мощный комплекс по производству машин и оборудования преимущественно для отраслей тяжелой промышленности. Только Донецкая область обеспечивала производство более 10 % общесоюзного и 24 % республиканского сталеплавильного оборудования, соответственно – 27 % и 76 % прокатного оборудования, 94 % и 100 % экскаваторов, 99,9 % и 100 % цистерн, 86 % и 100 % шахтных подъемных машин, 30 % и 78 % шахтных электровозов [104].
Особенностью машиностроительной отрасли Донбасса являлось то, что значительная часть выпускаемой продукции предназначалась для внутрирегионального использования.
Во второй половине 1960-х-первой половине 1980-х годов машиностроение региона, в условиях господства экстенсивного подхода к развитию экономики, развивалось достаточно динамично. С точки зрения количественных показателей это был период успешного развития отрасли, о чем свидетельствуют, например, следующие статистические данные.
Материалы таблицы показывают, что машиностроение области в целом развивалось стабильно. По выпуску многих видов продукции наблюдался устойчивый рост. Подобная картина была характерна и для Луганской области: с 1965 г. по 1985 г. производство металлорежущих станков увеличилось в 1,8 раза, электродвигателей в 3 раза. Значительно возрос выпуск грузовых вагонов – в 43 раза (с 72 до 3116).
Вместе с тем, в машиностроении региона, как и в целом страны, в исследуемый период значительно обострились ряд проблем. Одна из них – необходимость обновления машин и оборудования машиностроительных заводов. В начале 1970-х годов станочный парк СССР по своему количеству значительно превосходил парк любой другой страны мира. В конце 1971 г. в стране эксплуатировалось 3,7 млн. металлорежущих станков, причем почти половина из них (49,7 %) работали более 10 лет, а к 1980 г. их количество, по расчетным данным, должно была увеличиться до 5 млн. станков [106]. При этом стоит отметить, что нормативный срок амортизации станков был довольно длительным, что также не способствовало быстрому обновлению техники. В начале 1970-х годов нормативный срок использования, например, универсальных металлорежущих станков составлял 22 года, а средний физический срок действия до выбытия – 30-32 года [107]. В то же время в экономически развитых капиталистических странах наблюдалась тенденция к уменьшению как нормативного, так и физического сроков действия машин и оборудования. При нормативном сроке действия оборудования 8,5-9 лет, его средний возраст в машиностроении и металлообработке США в 1967 г. составлял 8 лет, снизившись по сравнению с 1958 г. на 3,4 года. Около 75% технологического оборудования Японии имело срок использования 6 лет [108]. При этом в условиях ускорения темпов научно-технического прогресса сроки старения постоянно снижались. По оценкам американских специалистов, моральный износ оборудования машиностроительной промышленности в 1940-х г. наступал через 10 лет, в 1950-х – через 8 лет, а в 1970-х – через 5 лет. Поэтому, естественно, что большой нормативный срок действия оборудования на предприятиях СССР значительно замедлял процесс обновления рабочих механизмов.
В первой половине 1980-х годов на машиностроительных заводах страны устанавливалось ежегодно примерно 5,4 % новых станков, а выбывало из строя лишь 3,9 %. Подобная динамики способствовала старению оборудования, которое использовалось в производстве. Если в 1980 году металлорежущие станки в возрасте до 10 лет составляли 50,5 % всего парка станков, то в 1985 г. – 45,9 %, в то время станков старше 20 лет увеличилось с 16,3 % до 21 % [109]. Подобная ситуация наблюдалась и на машиностроительных заводах Донбасса. Если в 1970-е годы на машиностроительных предприятиях Ворошиловградской области ежегодно обновлялось около 10 % основных фондов, то в середине 1980-х годов – лишь 6,7 % [110]. В 1985 г. на машиностроительных заводах области удельный вес нового, современного оборудования не превышала 33 %, а на многих предприятиях был еще ниже. Каждый шестой станок в машиностроении работал свыше двух десятилетий и более. В Донецкой области, вследствие низких темпов обновления оборудования, износ основных фондов машиностроения и металлообработки возрос с 37 % в 1980 г. до 43 % в 1985 г. [111].
Устаревшее оборудование требовало значительных затрат на его обслуживание, проведение текущих и капитальных ремонтов. Например, на Новокраматорском и Ждановском заводах тяжелого машиностроения затраты на содержание и эксплуатацию оборудования составили более 56 % всех расходов, предназначенных на обслуживание производства и управления. Подобное состояние дел было характерно и для других заводов. По подсчетам специалистов, затраты на ремонт и содержание оборудования в машиностроении достигали 12-18 % всех цеховых затрат, или 3-4 % общей суммы затрат на производство [112]. В 1985 г. ремонт оборудования машиностроительным предприятиям Донецкой области стоил 69 млн. руб., что было на 6 % больше затрат на внедрение научно-технических достижений [113].
Среди главных факторов, которые приводили к значительным затратам на ремонт, кроме увеличения количества техники и рост удельного веса морально устаревшего и физического изношенного оборудования, стоит выделить также низкий уровень концентрации, специализации и организации ремонта. Так, практически каждому предприятию приходилось формировать собственную ремонтную службу. Более того, поскольку централизованное снабжение запасными частями фактически находилось в запущенном состоянии (выпуск запасных частей в продукции станкостроения СССР составлял около 1 %, тогда как в США, например, он достигал 17-20 %), предприятия вынуждены были изготавливать их полукустарно, с большими затратами ручного труда, часто недостаточно высокого качества, заменяя во время ремонтов почти все детали оборудования. К тому же, ремонт часто проводился без должной обкатки и проверки отремонтированных узлов, что, конечно, отрицательно сказывалось на его качестве. В условиях интенсификации производства первостепенное значение имело улучшение использования производственных мощностей, повышение коэффициента сменности работы и более рационального применения машин и оборудования. Однако эффективность использования оборудования в машиностроительной промышленности оставалась невысокой. По данным обследования ЦСУ, в мае 1973 г., коэффициент сменности использования производственного оборудования на машиностроительных заводах республики составлял 1,38-1,64, снизившись по сравнению с 1964 г. на 1-4%. На многих заводах даже при односменной работе коэффициент сменности был ниже единицы [114].
Подобное положение было и на заводах Донбасса. Даже уникальные металлорежущие станки значительную часть рабочего времени простаивали, особенно во второй и третьей сменах. В середине 1960-х годов простои оборудования на краматорских машзаводах составляли почти треть режимного фонда времени [115]. Не улучшилось положение и в последующие годы. Так, на Ждановском заводе тяжелого машиностроения в 1970 г. металлорежущие станки не работали почти пятую часть каждой рабочей смены. На предприятиях Луганщины в 1985 г. коэффициент сменности оборудования составил лишь 1,4 [116]. На небольших заводах и в вспомогательных цехах эффективность использования техники была еще ниже.
Основными причинами простоев оборудования были неукомплектованность заводов рабочими и недостатки в организации производства и труда, прежде всего: неисправность оборудования, длительный ремонт станков, отсутствие материалов, деталей, инструмента, технической документации, прогулы рабочих, перебои в обеспечении электроэнергией и тому подобное.
Все это приводило к непланомерной и неритмичной работы. Так, в 1985 г. в производственном объединении «Ворошиловградтепловоз» примерно 85 % месячного плана выполнялось в последние пять дней [117]. Конечно, подобная «штурмовщина» крайне негативно сказывалась на качестве изделий. Значительное количество тепловозов не соответствовала требованиям стандартов и техническим условиям, выходя из строя еще в период гарантийного срока. Только за первое полугодие 1986 г. объединение получило 59 рекламаций на поставленные тепловозы [118]. Такие же случаи довольно часто встречались и на других предприятиях машиностроительной отрасли.
Слабым звеном машиностроения оставалось заготовительное производство. Одной из главных причин недостатков в этой важной сфере машиностроения было отсутствие достаточного уровня специализации и концентрации производства заготовок. Машиностроительные заводы развивались как предприятия с замкнутым циклом производства, почти на каждом из них были маломощные, слабо оснащены техникой литейные, кузнечно-прессовые цеха, где изготавливались часто некондиционные, некачественные заготовки, что, в свою очередь, приводило к значительным нерациональным затратам электроэнергии и металла. Так, в 1985 г. на машиностроительных предприятиях Донецкой области было использовано 1,4 млн. т черных металлов, при этом образовалось 284 тыс. т (20,2 %) отходов, в частности стружки – 149 тыс. т, или 52,5 % всех отходов [119]. Чрезвычайно медленно внедрялись в машиностроении новые химические материалы и новейшие технологии. Производство и переработка пластических масс в Украине получили развитие только с конца 1950-х годов, с середины 1960-х годов начали применять метод порошковой металлургии. Однако, несмотря на рост производства пластмасс и синтетических смол, их использование в машиностроении оставалось на низком уровне
В целом во второй половине 1960-х - первой половине 1980-х годов количественные показатели машиностроения Донбасса улучшились, расширилась номенклатура производимой продукции. Машиностроение в целом развивалось опережающими темпами по сравнению с другими отраслями промышленности. Вместе с тем, в отрасли, определяющей технический прогресс в народном хозяйстве, существенного повышения технического уровня, как и качества продукции не произошло. Основное внимание уделялось экстенсивному развитию отрасли, тогда как требовалось изменение инвестиционной политики в сторону технического перевооружения и реконструкции действующих предприятий, обновление основных фондов, решение проблемы материально-технического обеспечения, укомплектования трудовых коллективов квалифицированными рабочими ведущих профессий. На невысоком уровне находилась инновационная деятельностью предприятия отрасли, на них медленно внедрялись новейшие технологии, связанные с использованием пластмасс, синтетических смол, специальных сплавов, станки с программным управлением, электронно-вычислительная техника, новые измерительные приборы.
Все это в конечном счете сказывалось на качественных показателях, экономической эффективности работы предприятий машиностроительной отрасли. Основные тенденции развития машиностроения региона во второй половине 1970-х – первой половине 1980-х годов иллюстрируют материалы следующей таблицы.
Материалы таблицы позволяют сделать вывод, что в 1975-1985 годах в машиностроении области происходили противоречивые процессы. С одной стороны, к 1985 г. в сравнении с 1975 г. существенно укрепилась производственная база отрасли (стоимость основных фондов увеличилась в 2 раза), возросли капитальные вложения, расширился в стоимостных показателях выпуск товарной продукции.
Вместе с тем, с точки зрения эффективности производства в развитии отрасли наблюдались серьезные проблемы. Прежде всего речь идет о несоответствии затрат на развитие отрасли и отдачи от них. Так, в условиях расширения капитальных вложений (в 1985 г. в сравнении с 1980 г. – в 1,3 раза), существенного укрепления производственных фондов (в 2 раза), фондовооруженности (почти в 2 раза) фондоотдача уменьшилась на 30 копеек (с 1,25 руб. в 1975 г. до 0,95 руб. в 1985 г.).
Это свидетельствовало, прежде всего, о снижении уровня эффективности использования основных производственных фондов отрасли, о нарастающем несоответствии объема получаемой от реализации изготовленной продукции со стоимостью имеющихся у организации средств труда.
Со значительными трудностями столкнулась в конце 1960-х - первой половине 1980-х годах и энергетическая промышленность. В целом она развивалась достаточно динамично, но в условиях общего затухания экономических темпов наращивание энергетических мощностей постепенно замедлялось, ухудшались качественные показатели, снижалась эффективность производства.
В течение 1970-х – в начале 1980-х годов энергетическая система Донбасса еще продолжала наращивать свои мощности. Характерной особенностью развития тепловых электростанций региона было внедрение блочных схем с использованием агрегатов большой (300 тыс. кВт и более) единичной мощности. В результате реконструкции Кураховской ГРЭС ее мощность увеличилась до 1,6 млн. кВт.
Продолжалось сооружение крупнейшей в Донбассе Углегорской ГРЭС: в декабре 1973 г. была введена в эксплуатацию первая очередь электростанции в составе четырех энергоблоков мощностью 300 тыс. кВт каждый, а к концу 1977 г. было смонтировано еще три энергоблока-гиганта мощностью по 800 тыс. кВт. С их внедрением электростанция достигла проектной мощности 3,6 млн. кВт и стала одной из крупнейших тепловых электростанций не только СССР, но и Европы.
Уникальный «восьмисоттысячник» было установлено в 1971 г. также на Славянской ГРЭС [121]. В десятой пятилетке началось строительство еще одной крупной тепловой станции – Зуевской ГРЭС-2, проектная мощность которой составляла 2,4 млн. кВт. Значительно расширилась электросеть. В 1977 г. была введена в действие линия электропередач Донбасс – Западная Украина напряжением 750 кВт, которая обеспечила надежное энергоснабжение Правобережья и западных областей Украины.
В связи со значительным приращением мощностей уже в конце 1970-х годов энергосистема “Донбассэнерго” стала крупнейшей в стране. В ее состав входило 10 крупных тепловых электростанций установленной мощностью почти 13 млн. кВт, 13 предприятий электрических сетей, 9 ремонтных и вспомогательных предприятий. В 1977 г. электростанциями «Донбассэнерго» было выработано 68,3 млрд. кВт.ч электроэнергии, что составляло около 6 % общесоюзного и 31,8 % республиканского производства. «Донбассэнерго» осуществляло централизованное энергоснабжение нескольких тысяч промышленных предприятий, железнодорожного транспорта, сельского хозяйства, сотен городов и сел Донецкой и Ворошиловградской областей.
Главными потребителями электроэнергии были угольная промышленность (28-33%), металлургия (28%) и химическая промышленность (10-11 %). Около 6-7 % всей потребляемой электроэнергии приходилось на коммунально-бытовые услуги, и еще около 20 % вырабатываемой энергии передавалось за пределы Донбасса – в соседние с ним областей, а также в центральные районы России, Поволжья, Северного Кавказа [122].
В первой половине 1980-х годов ситуация в энергетической промышленности региона постепенно стала ухудшаться, что было обусловлено как субъективными, так и объективными факторами. Во-первых, изменились акценты в энергетической политике государства: приоритет был отдан развитию атомных электростанций в европейской части СССР, и мощных гидроэлектростанций в восточных районах страны. В связи с этим в Донбассе в течение 1980-х годов не предусматривалось строительство новых тепловых электростанций, за исключением достройки Зуевской ГРЭС-2, сооружение которой началось в десятой пятилетке.
Вместе с тем в регионе планировалось построить атомную электростанцию. Еще в 1977 г. руководство «Донбассэнерго» обратилось к Министерству энергетики и электрификации СССР с предложением запланировать на 1981-1990 годы строительство в Донбассе крупной атомной электростанции установленной мощности до 8-10 млн. кВт. Главный мотив этого ходатайства – будущее сокращение генерирующих мощностей в энергетической системе Донбасса. Действительно, старение основных фондов энергетической промышленности региона было очень острой проблемой.
Только в 1971-1983 годах через полное физическое изнашивание надо было вывести 1480 тыс. кВт рабочих мощностей, в частности закрыть Зуевскую-1 и Штеровскую ДРЕС. Впоследствии, в связи с выработкой предельного ресурса, предполагалось закрыть Северодонецкую и Лисичанскую ТЭЦ, а также вывести из эксплуатации 20 устаревших турбогенераторов мощностью по 100 тыс. кВт на Старобешевской, Мироновской, Славянской и Луганской ГРЭС. Приближались сроки замены и энергоблоков мощностью 200 тыс. кВт, которые обеспечивали почти 39 % энергетических потребностей Донбасса.
В целом, по подсчетам специалистов, дефицит генерирующих мощностей в системе «Донбассэнерго» до середины 1990-х годов мог составить 3,5 млн. кВт [123]. Поэтому, по мнению энергетиков Донбасса, нужна была атомная электростанция.
Сотрудники отраслевого института «Атомтепло-электропроект» Минэнергетики СССР, которые разработали технико-экономическое обоснование по определению площадки для строительства АЭС, предложили расположить атомную электростанцию на берегу Азовского моря, близ г. Новоазовска, но руководство области не согласилось с этим предложением, мотивируя это техногенными перегрузкам на природу и человека в Донбассе, перенаселением района, необходимостью сохранения курортной зоны. На совещании в Донецке в январе 1981 г., когда уже было разработано обоснование, проектировщикам предложили другое место для атомной электростанции с удалением от Азовского моря на 20-25 км, однако оно по технико-экономическим параметрам оказалось нецелесообразным [124].
В дальнейшем, в связи с аварией на Чернобыльской АЭС, на строительство атомных электростанций был наложен мораторий. Однако альтернативных решений проблемы улучшения состояния дел в энергетической промышленности не было найдено.
Во-вторых, бедственное положение энергетики Донбасса осложнялось устаревшими основными фондами. Энергообъединение «Донбассэнерго» было одним из старейших в стране, поэтому, естественно, ряд генерирующих мощностей требовали замены. Однако на модернизацию оборудования и его обновление выделялись недостаточные средства. Более того, даже эти средства не всегда своевременно осваивались. Так, в течение 1971-1975 годов на Углегорской ГРЭС не было освоено почти 4,5 млн., Кураховской – 2,4 млн., Славянской – 1 млн. руб. [125]. При условиях неудовлетворительного финансирования отрасли, в 1980-е годы впервые выводилось из эксплуатации больше мощностей, чем вводилось. Так, в 1961-1980 годы было введено 10,7 млн. кВт генерирующих мощностей, что составило более 2,5 млн. кВт за пятилетие, в первой половине 1980-х годов – 660 тыс. кВт [126].
На многих станциях из-за физического износа пришли в негодность трансформаторы, турбины, котлоагрегаты, выключатели и другое оборудование. Требовали полной или частичной реконструкции с заменой провода почти 2 тыс. км электрических сетей. Но, если в 1966-1970 годах на эти цели было выделено 54 млн. руб., то в 1981-1985 годах – лишь 23,8 млн. руб. Основные фонды энергетической промышленности Донбасса катастрофически старели: если в 1980 г. износ промышленно-производственных основных фондов электроэнергетики Донецкой области составлял 35 %, то в 1990 г. – 53 % [127].
В-третьих, значительно усложняло работу энергетических объектов некачественное оборудование, серьезные конструктивные и монтажные недоработки. Особенно это касалось новых агрегатов. Так, энергоблок мощностью 800 тыс. кВт с двухвальним турбогенератором, установленный на Славянской ГРЭС еще в 1968 г., через пять лет использовался всего лишь на 42,9 % своей мощности. Существенные конструктивные недоделки, некачественно выполненные монтажные операции предопределяли неритмичную и ненадежную работу оборудования. Из 19 остановок в 1972 году 15 были вынуждены, вследствие чего было потеряно 1662 рабочих часа, или почти 20 % календарного времени [128].
Введение в эксплуатацию энергетических блоков и оборудования со значительными недоделками, несоблюдение всех условий, предусмотренных проектами в процессе их монтажа, приводили к частым ремонтам, досрочному износу. К тому же, часто ремонтные работы выполнялись некачественно, не в полном объеме, несвоевременно. Все это негативно сказывалось на эффективности энергетических мощностей.
В-четвертых, одной из наиболее острых проблем для энергетики Донбасса было постоянное снижение качества твердого топлива, которое поступало на электростанции. При разработке проектов новых энергоблоков предполагалось, что на них будет использоваться качественный, высококалорийный угль зольностью 17-22 % и теплотой сгорания 5800-6600 ккал/кг. Но, как свидетельствуют отчеты о работе электростанции, угольное топливо не соответствовало его проектным характеристикам. Зольность угля в среднем повысилась с 29,8 % в 1975 г. до 38,6 % в 1985 г., а теплота сгорания при этом снизилась с 4844 до 4137 ккал/кг, или почти на 15 %. А на многих электростанциях (Старобешевская, Луганская, Углегорская ГРЭС) использовался уголь калорийностью 3500-3600 ккал/кг, что почти в 1,5-1,8 раза ниже проектного уровня [129]. Рост зольности был обусловлен широким использованием на шахтах высокопроизводительной техники, с помощью которой добывалась так называемая горная масса с повышенным содержанием золы.
Восстановление первоначальных свойств угля предполагалось на обогатительных фабриках, но их мощности не отвечали потребностям энергетики. В этих условиях иногда шахты поставляли на электростанции совсем необогащенное топливо. Так, шахта №10-бис «Глубокая» производственного объединения «Донецкуголь» отправляла на тепловые электростанции уголь, который почти наполовину (44 %) состоял из золы [130]. Конечно, такое «топливо» значительно усложняло работу электростанций. Некачественный уголь приводил к снижению мощности энергоблоков, увеличению расхода топлива, необходимости использования больших объемов мазута и природного газа. Так, увеличение зольности на 1 % приводило только на Старобешевской ГРЭС к ежегодному перерасходу почти 50 тыс. т угля. Значительно возрос удельный вес мазута в топливном балансе электростанций.
В целом по Украине его совокупные ежегодные издержки на тепловых станциях превышали проектные почти на 4,5 млн. т [131]. Указанные факторы в конечном счете существенно снижали эффективность работы электростанций. Только через некачественное топливо «Донбассэнерго» теряло около 600 МВт существующих мощностей, что приводило к ежегодному недопроизводству только Старобешевской и Луганской ДРЕС более 3 млрд. кВт.час. [132].
Кроме того, использование некачественного угля приводило к интенсивному износу котельного и транспортного оборудования электростанций, увеличению расходов на транспортировку топлива, загрязнению окружающей среды, а главное – сокращалось производство электроэнергии. Если в конце 1970-х годов «Донбассэнерго» производило почти 70 млрд. кВт. час. электроэнергии, то в конце 1980-х годов – около 57- 58 млрд. кВт. час. [133].
Накопившиеся проблемы отрицательно сказывались и на экономических показателях работы отрасли. Об этом свидетельствуют, в частности, данные по Донецкой области.
Несмотря на увеличение стоимости основных фондов (в 1,4 раза), фондовооруженности (в 1,3 раза) один из важнейших показателей эффективности работы отрасли – уровень фондоотдача не увеличился. На протяжении 1975-1985 годов соотношение между объемом дохода полученного от реализации произведенной продукции (электроэнергии, теплоэнергии и др.) и стоимостью имеющихся на электростанциях основных фондов не улучшалось. Так, в 1975 г. фондоотдача составила 0,49 руб., в 1980 г. – 0,56 руб., в 1985 г. – 0,51 руб. Думается, при этом надо учитывать, что в цене продукции электроэнергетики важную роль играл социальный фактор.
Анализируя основные показатели работы химической отрасли, следует отметить, что они в целом не отличались от показателей в других отраслях. Об этом можно судить на примере развития химической и нефтехимической промышленности Донецкой области.
Как видно из материала таблицы, количественные показатели свидетельствуют о, в целом, стабильной работе отрасли. Увеличились или же незначительно уменьшились объемы почти всех основных видов производимой продукции, прежде всего, минеральных удобрений и серной кислоты.
При этом потребление основного ресурса – электроэнергии – значительно уменьшилось: в 1985 г. в сравнении с 1975 г. химические предприятия области использовали ее почти в 1,4 раза меньше. За этот период основные производственные фонды увеличились в 2,2 раза, фондовооруженность – более чем в 1,5 раза, производительность труда возросла – почти в полтора раза.
Однако по ряду основных экономических показателей, как и в других отраслях, наблюдался спад. В частности, фондоотдача уменьшилась на 35 копеек (с 1,09 руб. до 0,74 руб.). Это свидетельствовало о нерациональной организации производстве. Подобное состояние отрасли можно объяснить рядом факторов.
Во-первых, неэффективное использование основных фондов. Значительные инвестиции в отрасль в конце 1950-х – первой половине 1960-х годов позволили создать на химических предприятиях новые производственные мощности. Однако осваивались они крайне неудовлетворительно [136].
В то же время на предприятиях отрасли были сосредоточены значительные запасы неустановленного оборудования. На Рубежанском химкомбинате в начале 1976 года оставалось несмонтированым оборудования на 150 тыс. руб., которое было приобретено в Италии еще в 1965 г. На складах Северодонецкого производственного объединения «Азот» такого оборудования было на 158 тыс. руб. Значительные запасы существовали и на других предприятиях отрасли [137]. Задержки с освоением новых производств и монтажом оборудования были обусловлены рядом факторов: ошибками проектировщиков, отсутствием квалифицированных специалистов, некомплексной поставкой оборудования.
Во-вторых, с начала 1970-х годов стали проявляться негативные тенденции и в техническом развитии химической промышленности, прежде всего, произошло значительное замедление темпов обновления основных фондов. Капитальные вложения в 1976-1980 годы в химическую промышленность Донецкой области составили 427 млн. руб., а в следующей пятилетке – 309 млн. руб. Во второй половине 1980-х годов они возросли, но в целом не обеспечивали достаточного обновления производства. Соотношение между изъятыми из промышленного производства основными фондами и введенными с каждой пятилеткой все больше становилось не в пользу последних: если в 1971-1975 годах коэффициент ввода составил 44,1, а вывод – 9,2; в следующей пятилетке – соответственно 39,3 и 6,7; то в первой половине 1980-х годов – уже 30 и 6,9 [138].
Как видно, темпы обновления химического производства в регионе в течение исследуемого периода значительно сократились, а темпы демонтажа устаревшего оборудования и вывода его из технологического процесса оставались примерно на одном, причем довольно низком уровне. Конечно, все это приводило к старению основных фондов, использованию неэффективного оборудования, что в свою очередь обусловливало низкое качество производимой продукции.
В-третьих, значительно усложняли работу химической промышленности организационные неурядицы. Согласно архивным материалам, чаще всего ритмичность работы производства срывали несвоевременные поставки, к тому же иногда некачественного сырья, упаковки; нарушение технологии; использование устаревшего и неэффективного оборудования. Конечно, это негативно сказывалось как на качестве продукции, так и на экономических показателях. Как и в других отраслях, в химической промышленности Донбасса в 1970-1980-е годы основные производственные фонды, фондообеспеченность увеличивались, а фондоотдача снижалась, что указывало, прежде всего, на неэффективность производства.
В-четвертых, несмотря на значительные усилия в направлении улучшения технологического процесса, он все еще оставался на достаточно низком уровне. Химическое производство было чрезвычайно материало- и энергоемкое, к тому же использование сырья происходило крайне нерационально. Так, на Донецком содовом заводе и Славянском содовом комбинате хлористый натрий – основной вид сырья – использовался только на 63-64 %, при этом хлор полностью терялся; углекислота из другого вида сырья – известняка – использовалась на 88 %, а кальций терялся полностью. Только эти два предприятия ежегодно накапливали 1,8 млн. т отходов [139]. Впоследствии положение в этой сфере несколько улучшилось, но в целом уровень переработки сырья на химическом производстве оставался довольно низким, к тому же эта отрасль была одним из главных источников загрязнения окружающей среды.
Следовательно, можно сделать заключение, что химическая отрасль развивалась в рамках общеэкономического тренда. Здесь преобладали те же тенденции развития, которые были характерны для других отраслей. Наращивались объемы производственных фондов, увеличивался производственный персонал, повышалась фондовооруженность. Вместе с тем, эффективность работы предприятий химической отрасли снижалась.
Таким образом, анализ развития промышленного комплекса Донбасса во второй половине 1960-х – первой половине 1980-х годов показывает, что, как и ранее, ведущими составляющими промышленного сектора региона оставались топливно-энергетический комплекс, металлургическая, химическая, машиностроительная отрасли.
Продолжалось интенсивное наращивание индустриальной мощи региона, прежде всего за счет введения в действие новых предприятий, расширения новых производственных площадей. При этом количественные показатели, как и прежде, выступали главным критерием как во время планирования работы отрасли и отдельных предприятий, так и в процессе оценки результатов их деятельности.
Оценивая в целом развитие промышленного сектора, надо отметить, что в эти годы не удалось решить одну из приоритетных задач современного индустриального процесса – интенсифицировать промышленное производство на основе широкого использования достижений науки и техники, повысить уровень эффективности производства.
Дата добавления: 2021-12-10; просмотров: 235; Мы поможем в написании вашей работы! |
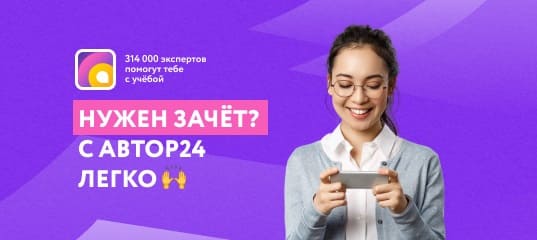
Мы поможем в написании ваших работ!