Технические характеристики комплексов.
АУК.2М | АУК.1М | АУК.1МУ | |
Общее количество функций | 32 | 42 | 53 |
Максимальное значение настраиваемой выдержки времени, с | |||
На запуск линии | - | 90 | 120 |
На запуск конвейера | 25 | 25 | 60 |
Максимальное сопротивление линии управления и сигнализации, Ом | 20 | 60 | 60 |
Удельная масса, кг на функцию | 11,6 | 8,8 | 7 |
Удельная потребляемая мощность, ВА на функцию | 2,5 | 2,38 | 2,3 |
Концепция автоматизированного управления в АУК.2М осталась неизменной в сравнении с таковой в АУК.1М.
В АУК.2М управление конвейерной линией может осуществляться также в режиме автоматического управления от технологических датчиков контроля уровня заполнения бункера. Работа конвейерной линии в этом режиме происходит циклично: включение - при достижении горной массы в бункере ниже датчика нижнего уровня, а отключение - при достижении уровня горной массы датчика верхнего уровня.
В конце линии (под лавой) расположен кнопочный пост, с помощью которого оператор механизмов лавы при необходимости замыкает и блокирует кнопку “Стоп”, выдавая сигнал запрета работы конвейерной линии. При деблокировке упомянутой кнопки выдаётся сигнал разрешения работы конвейерной линии; запуск осуществляется при условии, что исправны все датчики системы автоматического контроля, а от датчиков бункера выдаётся команда на включение ПУ. Аналогично описанному процессу автоматического управления от технологических датчиков бункера в АУК.2М предусматривается режим автоматического управления линией от сигналов датчика контроля работы магистральной конвейерной линии. В этом случае к ПУ участковой линии подключается датчик контроля скорости ДС, который устанавливается на конвейере магистральной линии.
|
|
При работе магистральной линии сигнал от датчика ДС подаёт команду включения участковой линии, она включается и работает до тех пор, пока не отключится магистральная линия, либо не поступит сигнал отключения от датчиков средств контроля и защиты.
Для обеспечения возможности включения участковой линии вне зависимости от работы магистральной, например, при ремонтах и наладке, предусматривается деблокировка, осуществляемая с прибора-указателя пульта(ВПУ).
Комплекс автоматизированного управления конвейерными линиями УКЛ.1 предназначен для централизованного управления разветвлёнными и неразветвлёнными конвейерными линиями угольных шахт, в том числе опасных по газу и пыли, с числом конвейеров в линии до 30 и числом ответвлений до 6, обеспечивает также автоматизированное управление отдельными конвейерами, не входящими в состав конвейерной линии. Устанавливается в конвейерных выработках или в диспетчерской.
|
|
Структурная схема комплекса УКЛ.1 приведена на рис.. Комплекс состоит из пульта управления ПУ, источников питания ИП-1 и ИП-2, блока управления конвейером БК, генератора сигналов ГС, линейного усилителя ЛУ, микротелефона МТ, громкоговорителя ГР и стенда для проверки блока управления. Составные части, входящие в комплект поставки пульта и блока управления, а также линейного усилителя, и их назначение приведены в табл. 4.
Комплекс УКЛ.1 обеспечивает выполнение следующих функциональных требований:
управление разветвлёнными и неразветвлёнными конвейерными линиями, а также отдельными конвейерами; местное автоматизированное управление конвейером, осуществляемое с блока управления;
централизованное автоматизированное управление конвейерной линией, осуществляемое с пульта управления; пуск конвейерной линии (части линии) по командам от оператора или технологических датчиков в последовательности, исключающий завал мест перегрузок и осуществляемый путём включения каждого подающего конвейера только после установления рабочей скорости смежного принимающего (пуск против грузопотока); оперативный останов конвейера, осуществляемый по управляющим командам от оператора, обслуживающим персоналом на месте или от технологических датчиков путём наложения тормозов при скорости ленты ниже 0,5 м/с; аварийный останов конвейера при скорости ленты ниже 0,5 м/с и защитных отключениях;
|
|
экстренный останов с наложением тормозов одновременно с подачей команды на отключение привода конвейера при защитных отключениях;
останов конвейерной линии (части линии) по сигналам от оператора или технологических датчиков.
Кроме того, комплекс обеспечивает автоматическую подачу предупредительного звукового сигнала длительностью не менее 5с перед запуском конвейера (конвейерной линии);
запрет исполнения пусковой команды в случае отсутствия воспроизведения предупредительного сигнала звуковым сигнализатором, расположенным у приводной головки;
выбор вида управления (местное, автоматизированное, централизованное) на блоке управления конвейером;
автоматический контроль исправности цепей датчиков завала, схода ленты, экстренного останова, ограждения, а также цепи ретрансляции пуска при сопротивлении линии связи до 160 Ом;
|
|
регулируемую выдержку времени на останов конвейера в пределах от 1 до 6 с при срабатывании датчиков контроля завала или схода ленты; контроль номинальной скорости в диапазоне скоростей ленты конвейера от 1 до 5 м/с.
Комплекс также обеспечивает сигнализацию на пульте управления, блоке управления конвейером с много двигательным приводом путём подачи сигналов на поочередное включение двигателей и диагностики схемы пульта управления от встроенного устройства контроля; выполнение всех функций по управлению конвейерной линией при сопротивлении утечки между жилами не менее 12 кОм; двухстороннюю телефонную связь с селективным вызовом между оператором и пунктами установки блоков управления конвейерами и устройствами звуковой сигнализации и др.
Принцип работы комплекса УКЛ.1 не отличается от принципа работы заменяемой им аппаратуры типа ЦИКЛ.
В результате повышения надёжности источников питания и перевода питания цепей датчиков с автоматическим контролем линии связи с 4 на 50 Гц существенно повышена эксплуатационная надёжность комплекса УКЛ.1. Внедрение комплекса УКЛ.1 по сравнению с существующими комплексами управления конвейерными линиями позволяет расширить области применения и функциональные возможности, увеличить пропускную способность конвейерных линий за счёт сокращения времени простоев, что является основными источниками его экономической эффективности.
Однако, внедрение УКЛ связано с дополнительными затратами , связанными с конструктивной несовместимостью оболочек корпусов АУК и УКЛ.
6.2. Автоматизация электровозного транспорта
В функции технических средств автоматизации (ТСА) электровозного транспорта входят обеспечение:
- систем СЦБ ( сигнализации ,централизации и блокировки)
- систем оперативной связи диспетчера ,машинистов , пунктов погрузки
-контроля местонахождения и направления движения поездов
- дистанционное управление стрелочными переводами с движущихся электровозов
- дистанционное управление электровозами в пунктах погрузки и разгрузки
- автоматизированное управление движением электровоза на маршруте
- автоматическое управление движением поездов (подсистема АСУ ТП ).
Система сигнализации обеспечивает информацию о занятости участка пути и о положении стрелок. Нормальное состояние светофора - красный свет, при запросе занятости свободного участка на момент вода стрелок загорается мигающий зелёный , после перевода стрелки спокойно горящий зелёный . После въезда на участок - красный. Информация о получении запроса - мигающий красный (занятый участок).
Жёлтый и синий сигналы используются для сигализации о положении стрелок.
Устройства централизации служат для управления сигналами и стрелочными переводами из центрального пункта.
Устройства блокировок выполняют контроль занятости блок-участков путей, положения стрелок и обеспечивают безопасность движения.
Эти функции выполняются аппаратурой АБСС-1М. Комплектация:
-два блока автоматического управления маршрутами (БАУМ.1)
-блок автоматического управления стрелками (БАУС.1)
-передатчики сигналов локомотивные ЛПС.1
- приёмники сигналов управления НПУ-2
- приводы стрелочные ПМС-4
-сигнальные указатели ССУ-2.
Датчики запроса ДЗ, перемены ДП, отбоя ДО - приёмные антенны НПУ. Аппаратура АБСС.1М позволяет управлять восемью маршрутами и четырьмя стрелочными переводами. При этом скорость движения электровоза не более 30 км/ час.
В сравнении с АБСС аппаратура КУВЭТ дополнительно обеспечивает ряд дополнительных возможностей. Так, обеспечивается возможность установления блокировочной зависимости с маршрутами другого узла путевого развития или других шахтных устройств, получения на диспетчерском пункте информации о состоянии аппаратуры и занятости блок-участков и т.д. Предусмотрена возможность активного участия диспетчера (дистанционно) в управлении движением на блок-участках.
Функции АБСС.1М (КУВЭТ), а также возможность автоматического контроля местонахождения и направления движения поездов осуществляет аппаратура НЭРПА.
Широкое использование комплексов НЭРПА сдерживается отсутствием входящих в комплект поставки или встроенных локальных средств передачи и представления собранной информации о месте нахождения электровозов. В аппаратуре НЭРПА отсутствует согласующий блок для обеспечения обмена информацией с ЭВМ подсистемы АСУТП “Локомотивный транспорот” на поверхности шахты.
Эти недостатки учтены в комплексе КРДТ, выпускаемом взамен комплекса НЭРПА.
В КРДТ используются собственные локальные системы телемеханики. Для передачи информации используется зарекомендовавший себя помехоустойчивым в шахтных условиях принцип формирования и передачи сигнала. содержащий коды номера электровоза и команды управления в виде амплитудно- модулированных сигналов высокой частоты. В зависимости от объёма требуемых функций комплекс КРДТ выпускается в трёх модификациях, причём КРДТ-3 выполняет все функции, включая передачу информации в вычислительный комплекс диспетчера.
Для сбора, формирования и передачи информации о прохождении вагонеток в четырёх точках контроля в подсистему АСУ ТП (АСТРА) применяется устройство УФИ.
Автоматизированное управление рудничными аккумуляторными электровозами (АРП-14_900, АРП28-900) может выполняться с помощью тиристорной регулирующей аппаратуры ТЭРА-1.
Основные функции:
- плавный разгон и регулирование скорости
- плавное электродинамическое торможение при скорости от 0.6 до 2 м в с
- ограничение тока тяговых двигателей в разных режимах
-включение эл. магнитных рельсовых тормозов при экстренном торможении
- измерение и индикацию скорости движения электровоза
- возможность работы с аппаратурой НЭРПА ,КРДТ;
-управление одно- и двухсекционными электровозами, а также электровозами работающими на повышенной частоте.
Для управления с пульта машиниста приводом и вспомогательным электрооборудованием контактных электровозов КТ14-900 и КТ28-900 разработана аппаратура УКТН.
В сравнении с аппаратурой ТЭРА.1 УКТН дополнительно выполняет функции:
бесступенчатое задание и стабилизацию скорости электровоза в пределах от 0.6 до 8 м/с;
контроль наиболее характерных неисправностей и др.
ТСА погрузочных и разгрузочных пунктов включают следующее оборудование.
Для обработки и оперативного представления диспетчеру на поверхности шахты информации о расстановке вагонеток на порожняковой и грузовой ветвях погрузочных и разгрузочных пунктов используется аппаратура ИРП.1М.
ИРП.1М (индикатор работы погрузочного пункта шахты) может использоваться в составе АСУТП (подсистема АСТРА). Индикатор работает совместно с аппаратурой счёта вагонеток УФИ и отображает в удобной для восприятия форме количество вагонеток, загруженных с начала смены.
Автоматизированные комплексы погрузочных пунктов КАП служат для контроля заполнения шахтных вагонеток, передвижения поезда гидротолкателем и управления средствами загрузки.
Для механизации и автоматизации обмена вагонеток в клети применяют агрегаты АЦ и АЦМ ( с электрическим ) и АПГ ( с пневмогидравлическим приводом).
В составе перечисленного выше автоматизированного оборудования применяются различные датчики контроля заполнения вагонеток, датчики контроля положения подвижных объектов ( в том числе концевой защиты их) -ДКПУ,УКП , ДПМГ и другие. Они обеспечивают искровзрывобезопасный контроль оборудования, высокую надёжность и длительный срок службы.
Для дистанционного управления аккумуляторными электровозами используется система СТАРТ- 1. С её помощью обеспечивается двусторонний обмен информацией между электровозными и путевыми приёмопередатчиками. Для передачи на электровоз на частоте 72 кГц используют 4 модулированных по амплитуде сигнала, для передачи с электровоза на частоте 150 кГц- два модулированных по амплитуде сигнала.
В аппаратуре СТАРТ-1 выполняются функции рассмотренных выше аппаратов. Она может входить в состав подсистемы АСУТП шахты.
Канатная откатка относится к разновидности рельсового транспорта и применяется в выработках с углом наклона более 6 градусов для обеспечения обратного движения вагонов под действием собственного веса. Профиль пути выработки имеет переменный угол. В связи с этим задачей автоматизации является контроль и регулирование скорости в соответствии с рациональными нагрузками на электродвигатель лебёдки. Нагрузка на двигатель может меняться от 20 до 130% номинальной. Во время основного рабочего цикла задаются максимальная 3-5 м/ с и малая 0.5 м/ с (при вытягиваниии вагонеток с приёмного горизонта, при прохождении закруглений). Монорельсовые и моноканатные подвесные дороги для транспорта людей и оборудования автоматизируют с помощью аппаратуры УМД.
6.3. Автоматизация шахтных подъёмных машин
Шахтные подъёмные установки являются одними из наиболее ответственных и сложных составляющих элементов угольных шахт. Задачи их безопасной и безаварийной эксплуатации не могут быть выполнены без оснащения их средствами автоматического контроля , управления и связи.
Наиболее развитые системы автоматики реализованы на скиповых шахтных подъёмных установках или комплексах (СШПУ). Системы автоматики включают средства автоматического управления, защиты, контроля и сигнализации.
СШПУ должны оснащаться защитами, вызывающими предохранительное торможение машины:
от переподъёма (два конечных переключателя на копре и два дублирующих путевых выключателя в аппарате задания и контроля хода или на колонке указателя глубины;
от превышения максимальной скорости на 15% и скорости подхода к разгрузочным кривым более 15%,(два независимых ограничителя скорости, причём один из них может иметь общий привод с аппаратом задания и контроля хода, а второй - независимый);
от зависания и напуска каната;
от недопустимого износа тормозных колодок;
от превышения на 50% заданного времени разгона и замедления;
от понижения давления в цилиндрах тормозов и в сети воздухопровода;
от обратного хода машины;
от неисправности электрических цепей управления рабочим тормозом;
от обрыва цепей эл. ограничителя скорости;
от неполного растормаживания рабочего тормоза;
от повреждения затвора дозатора при его случайном открывании во время движения скипа;
максимальная токовая защита эл. двигатиля и источников постоянного и переменного тока;
нулевая защита двигателя.
Защитные блокировки, допускающие завершение цикла с запретом очередного пуска:
при недопустимом снижении уровня изоляции цепей сигнализации;
при перегреве подшипников, редуктора, обмоток эл. двигателей;
при перегреве воздуха компрессора тормозной системы;
при прекращении работы маслонасоса, снижении давления масла или при недостаточном уровне его в маслосборнике;
при недопустимом снижении уровня изоляции цепей управления;
Защитные блокировки, обеспечивающие:
возможность включения эл. двигателя после переподъёма или зависания скипа только в сторону его ликвидации;
невозможность снятия предохранительного тормоза, если рукоятка рабочего тормоза не находится в положении “заторможено“, а рукоятка управления двигателем - не в нулевом положении и другие блокировки и защиты.
Срабатывание защит вызывает обесточивание контакторов, приводящих к предохранительному торможению.
Рассмотрим упрощённую схему расположения датчиков и аппаратуры СШПУ.
Контроль зависания скипа в стволе производится по сигналам магнитоупругих индуктивных датчиков устанавливаемых под корпусами подшипников копровых шкивов с помощью аппаратуры АЗСП-2.
Защита от переподъёма скипа датчиками положения на копре и концевыми выключателями на пульте управления в блоке указателя глубины.
Подход скипа к месту разгрузки на копре и месту загрузки в стволе контролируется взрывобезопасными датчиками положения и выключателями
Уровень заполнения бункеров контролируется, например, взрывозащищёнными гамма- реле.
Весоизмерительное устройство дозатора воздействует на ИМ загрузочного устройства и передаётся информация в схему управления ПМ.
Износ тормозных колодок контролируется двухступенчатым устройством, где 1-я ступень - предупредительный сигнал , 2- я отключение ПМ.
Аппарат программирования и контроля хода
Пульт управления ПМ, например ПШП, который изготовляется в двенадцати вариантах по набору сигнальной и коммутирующей аппаратуры.
В качестве датчиков положения скипа, а также затворов скипа и бункеров применяют аппараты ДКПУ, ДПМГ, ДКПМ, для контроля уровней ИКУ, РКУ 1М.
Кроме перечисленных средств контроля можно указать следующие:
- реле РВКД и РКД совместно с реле давления РД применяют для защиты от понижения давления в тормозных цилиндрах;
- реле РОХ в комплекте с другими -для защиты от обратного хода ПМ;
- реле РВКТР и РКТР осуществляют защиту от неисправности эл. цепей управления рабочим тормозом;
- реле РКРМ предназначены для защиты от неполного растормаживания тормоз при пуске ПМ .
Эти и целый ряд других элементов входят в состав комплектов средств автоматизации ПМ.
Технические средства автоматики ТСА расположеные на копре , в машинном здании и в районе загрузочного устройства выполняют функции контроля, защиты, сигнализации и регулирования скорости движения подъёмного сосуда в стволе.
Основная задача ТСА СШПУ обеспечение заданной тахограммы скорости движения сосуда в стволе в зависимости от местонахождения скипа. Задание требуемой скорости осуществляется специальным программным устройством. В случае отклонения от задания по скорости, а также при возникновении аварийных ситуаций (переподъём, зависание скипа и другие) включаются тормозные устройства.
Тормозные устройства обеспечивают:
- рабочее (в большинстве случаев регулируемое) торможение, в процессе которого происходит плавное изменение тормозного момента для выполнения расчётной тахограммы, а также остановка (стопорение) машины в период пауз между циклами. Осуществляется машинистом с пульта или в автоматическом режиме управления с использованием механического подтормаживания;
- предохранительное торможение - наложение тормоза в случае аварийной ситуации. Осуществляется либо машинистом подъёма, либо автоматически - при срабатывании средств защиты подъёмной установки.
Тормозное устройство управляется комплексом аппаратуры управления тормозом по командам, поступающим от машиниста либо от автоматической системы управления СШПУ. В зависимости от конструкции машины (барабанные, со шкивами трения и т.д.), скоростей движения сосудов и т. п. системы автоматического регулируемого торможения (САРТ) выполняют одно- и двухступенчатыми.
В зависимости от алгоритма управления различают разомкнутые параметрические (РП), разомкнутые избирательные (РИ) и замкнутые следящие (ЗС) системы управления тормозом.
В РП системах происходит поочерёдное включение первой и второй ступеней торможения, при этом конечный результат торможения системой не контолируется.
В РИ системах с помощью датчиков определяют режим работы (подъём или спуск) и в зависимости от этого сразу включают первую или вторую ступень. Такой принцип более эффективен, однако система не может автоматически увеличивать момент при необходимости.
ЗС поддерживают в процессе торможения заданное замедление.
В ряде случаев невозможно уложиться в рамки допустимых замедлений при двухступенчатом замедлении и применяют трёхступенчатое со следящей системой управления.
Поддержание требуемой скорости движения сосуда на практике осуществляется совместным действием тормозов и регулируемого электропривода.
В настоящее время большая часть СШПУ на угольных шахтах оснащена асинхронным (АД) приводом мощностью до 1000 квт в однодвигательном исполнении и до 2000 квт в двухдвигательном. Однако низкая управляемость АД требует применения различных средств для регулирования хода СШПУ в разные периоды цикла подъёма. Выбор средств для обеспечения периодов замедленияи дотягивания в общем случае определяет принцип и схему автоматизации.
Применяются схемы с использованием регулируемого механического и динамического торможения при заданном пути замедления и с выбором
точки начала замедления;
схемы свободного выбега и специальные средства для осуществления дотягивания (каскадные. с микроприводом, с преобразователями частоты) или обеспечение дотягивания в импульсном режиме.
схемы с регулируемым динамическим торможением.
Наиболее перспективны схемы с использованием регулируемых тормозов, для которых аппаратура выпускается серийно(АУГТ- для гидротормозов , КУПТ для управления пневмотормозными системами, комплекс аппаратуры автоматического регулируемого предохранительного торможения АРПТ и др).
Общим конструктивным принципом всех тормозных систем ПМ является следующий: тормозные усилия обеспечиваются специальными грузами через тормозные колодки. Расторможенное состояния обеспечивается давлением газа или жидкости в цилиндрах, воздействующего на шток поршня, связанного с грузами тормозов. При торможении газ или жидкость выпускаются через регулируемые отверстия и приводятся в действие силой тяжести грузов тормозные устройства. Снижение давления в цилиндрах с помощью регуляторов производится по определённому закону. Грузовые тормоза приводятся в действие ослаблением взведённой пружины.
Аппаратура АУГТ в зависимости от типа тормозного привода и условий эксплуатации выпускается четырёх модификаций. Например, АУГТ-1 предназначена для подъёмных машин с гидрогрузовым приводом тормоза, работающих на поверхности шахт. В комплект АУГТ-1 входят: регулятор давления унифицированный гидравлический типа РДУГ, блок управления тормозом БУТ, командоаппарат сельсинный, устройство обратной связи УОС, стабилизатор напряженния С-0.75.
Аппаратура КУПТ для дистанционного и автоматического управления в трёх модификациях. КУПТ- 1- для новых подъёмных машин устанавливаемых на поверхности шахты включает: регулятор давления унифицированный РДУ-1, блок управления тормозом, стабилизатор напряжения С-0.28.
Комплекс АРПТ предназначен для поддержания заданного уровня замедления независимо от величины статической нагрузки и направления движения сосуда. Применим для различных типов машин, может использоваться с дисковыми и радиальными тормозными устройствами вертикальных и наклонных подъёмов. В состав комплекса входят аппарат управления АУ, датчик путевой импульсный ДПИ и тормозная панель электроклапанов ЭПК или электрогидроклапанов ЭГК (исполнительные органы).
Датчик ДПИ во время работы машины формирует два сдвинутые по фазе на 90 град. прямоугольные импульсы, пропорциональные скорости движения сосуда.
Используя эту информацию, оба канала в блоке управления осуществляют:
измерение величин скорости и ускорения движения;
задание уставок минимальной скорости стопорения,порога включения и отключения каждого из ЭПК и порога отключения каждого ЭГК;
сравнения величины действительного замедления с уставками и формирования команд управления исполнительными органами.
Для реализации схем управления асинхронными приводами разработана комплектная аппаратура АГП-61, АГП-2. Схемы аппаратуры построены на принципах:
вывод скипов из загрузочного и разгрузочного устройств с малой скоростью под контролем регулируемого механического тормоза;
разгон до максимальной скорости в функции тока и времени;
замедление в режиме свободного выбега или динамического торможения с автоматическим выбором (или без выбора) точки начала замедления;
дотягивание с малой скоростью под контролем регулируемого механического тормоза.
Развитие силовой полупроводниковой техники позволяет применять каскадные схемы регулирования и частотное регулирование. Системы асинхронно - вентильного каскада (АВК) для плавного регулирования скорости АДФР обеспечивают высокую управляемость и экономичность.
Частотное регулирование сдерживалось отсутствием преобразователей частоты достаточной мощности, которые в последние годы разработаны рядом организаций.
Основной аппаратурой, применяемой для программирования циклов до настоящего времени, является АЗК-1. Принцип их работы базировался на использовании следящей сельсинной передачи. Последняя отслеживала угол поворота вала машина. Задание по скорости определялось профилем ретардирующего диска. Для выдачи аварийного сигнала в цепь защиты в случае превышения максимальной скорости на 15% или подхода нормальному верхнему положению сосуда со скоростью свыше 1,5 м в сек предназначаются электрические ограничители скорости ЭОС- 2. Аппарат АКХ также, как АЗК привязаны к коренному валу ПМ. Вследствие фрикционной связи канатов и канатоведущего шкива они имеют определённую погрешность, несмотря на наличие корректирующих устройств, включаемых по окончании цикла подъёма.
Элементы АЗК и АКХ модернизировались (ЭОС-1 на ЭОС-2, -3). Однако, в основном, принцип их работы был прежним.
В настоящее время разработаны новые аппараты контроля хода. Так, вместо ЭОС-3 применяется двухканальный электронный ограничитель скорости ОСПМ.
Разработаны аппараты программирования (“Горизонт, Скип”) с привязкой непосредственно к подъёмным канатам - путём нанесения на них магнитных меток. В этом случае проскальзывание или переползание канатов не оказывает никакого влияния на точность работы аппарата.
Магнитная метка на канате может быть получена в виде постоянного магнита, расположенного вдоль оси каната. Метка наносится на канат при помощи записывающей головки. Полюса сердечника этой головки прижимаются к канату. Через обмотку записывающей головки пропускается импульс тока, в результате на канате остаётся магнитная метка. На расчётном расстоянии от записывающей головки установлен блок воспроизведения( по аналогии с магнитофоном) .
В аппарате с использованием магнитной записи на канате применяется система “магнитная запись - шаговый двигатель”(МЗ-ШД). Система МЗ-ШД предназначена для преобразования линейного перемещения по стволу сосудов в соответствующий по величине и направлению угол поворота ротора шагового двигателя (ШД) независимо от взаимного положения подъёмных канатов и канатоведущего шкива.
Направление вращения ШД определяется направлением перемещения каната, при этом каждому шагу двигателя соответствует одно и то же перемещение каната. Вращение от ШД через редуктор передаётся:
путевым выключателям, предназначенным для выдачи эл импульсов в цепь управления в отдельных точках пути движения сосудов в стволе
сельсин-датчикам указателей глубины и ограничителя скорости для выдачи сигналов заданной скорости, которые в электрическом ограничителе скорости сравниваются с сигналом фактической скорости, поступающим от тахогенератора. Сигнал рассогласования эл ограничителя скорости поступает в цепь защиты.
Исключить промежуточное преобразование информации можно за счёт установки микропроцессора, на вход которого будут поступать сигналы от блоков воспроизведения в дискретной форме. С выхода микропроцессора будут выдаваться сигналы в систему управления подъёмной машиной.
В аппаратуре “СКИП” предусмотрена цифровая аппаратура управления и защиты, выполненная в виде набора блоков логических элементов. Счёт импульсов от магнитных меток выполняется с помощью реверсивного счётчика. В составе аппаратуры управления и программирования логические схемы и дешифраторы, выдающие сигналы в зависимости от задания и отработки системой тахограммы ПМ. Глубину ствола определяет заданное количиство импульсов на счётчике при подъёме производится пропорциональное вычитание импульсов со счётчика. Скорость движения сосуда определяется дифференцированием сигналов путевых импульсов.
Системы автоматического регулирования электроприводов ПМ часто строятся по многоконтурным схемам, в частности по принципу подчинённого регулирования, рассматриваемому в курсе ТАУ. Реализация систем подчинённого регулирования выполняется на базе использования универсальной блочной системы регулирования УБСР различных модификаций.
Кроме асинхронных приводов на ПМ применяют электроприводы постоянного тока. Последние имеют, несмотря на недостатки, несколько лучшие регулировочные характеристики.
В тиристорных системах электропривода КТЗУ, а также в автоматизированных комплектах асинхронного привода подъёма КАУП (Донецкий энергозавод, Александрийский эл.маш завод) предусмотрена поставка задатчиков интенсивности вместо механических ретардирующих устройства.
Для комплексного отображения параметров движения сосудов и формирования предупредительного сигнала о необходимости снижения фактической скорости при её приближении к заданной применена аппаратура УКД, где информация о скорости вращения вала ПМ поступает от датчика - щелевого модулятора, расположенного на боковине барабана ил шкива трения ПМ.
Замена ПМ машины и сопутствующего оборудования производится крайне редко. Аппаратура автоматики часто монтируется из отдельных подходящих блоков. Кроме вышеупомянутых в числе современных элементов автоматизации можно назвать следующие.
Станция предохранительного тормоза СТП-1В предназначенная для питания и контроля цепей управления тормозным приводом ПМ с барабаном до 3м с системой регулируемого предохранительного торможения (АРПТ) с пружинно-гидравлическим или с пружинно-пневматическим приводами тормоза.
Ограничитель скорости ОСП-1 предназначен для защиты от превышения скорости ПМ. Комплект ОСП-1 состоит из:
блока сравнения и контроля ограничителя БСКО-1, трёх путевых импульсных датчиков ДПИ-1, блока питания БП-2.
Аппаратура шахтной стволовой сигнализации и связи вертикальных подъёмных установок ШСС-1 предназначена для координации действий обслуживающего персонала при выполнении операции по спуску - подъёму людей, грузов и оборудования. ШСС-1К для клетевых подъёмов,
ШСС-1С - для скиповых.
ШСС-1С обеспечивает:
рабочую световую (в сопровождении звуковой) сигнализацию и громкоговорящую связь для подъёмов высотой до 2000 м и числом горизонтов до трёх;
подачу в машинное отделение из горизонта рабочих сигналов;
подачу в машинное отделение сигналов об уровне угля в бункере, положении дозатора;
предупредительную сигнализацию перед пуском ПМ.
На эффективность работы скиповых подъёмов большое значение оказывает способ загрузки и разгрузки , а также конструктивные особенности загрузочнных и разгрузочных устройств (ЗУ и РУ). Автоматизированные З и РУ должны обеспечивать выполнение ряда требований:
невозможность открывания затвора дозатора, если нет скипа под загрузкой и повторного открывания затвора дозатора, если скип загрузился.
защиты от перегрузок и КЗ двигателей
конроля полной загрузки и разгрузки скипов и уровня заполнения бункеров
контроль верхнего и нижнего уровней угля в приёмном бункере
контроль положения затворов дозаторов загрузки и прихода скипов под загрузку и другие требования.
Загрузочные устройства, применяемые на шахтах имеют различные конструкции затворов и способов их открывания.
Наиболее эффективным способом является способ дозирования угля в скип по весу. Под дозатором устанавливается весоизмерительный датчик (тензометрический, магнитоупругий или гидравлическое взвешивающее устройство), при этом точность загрузки до ±5%, в результате чего снижаются требования к системе регулирования хода ПМ.
Способ разгрузки определяется конструкцией скипов: сдонной разгрузкой при отклоняющемся кузове с секторным затвором, опрокидывающиеся, скипы с боковой разгрузкой при неподвижном кузове и обращённым механизмом открывания- закрывания секторного затвора с помощью индивидуального привода, установленного на копре. Последние выгодно отличаются незначительными динамическими нагрузками на разгрузочные кривые и копёр, малой длиной дотягивания, высокой допустимой скоростью полхода скипа. Очевидно, что по этим параметрам такие скипы наиболее пригодны для создания надёжных систем автоматизации.
В настоящее время изготавливается взрывоопасная аппаратура весовой дозировки скипов КДС. КДС выполняет следующие функции:
автоматически включает и выключает питатель дозатора, подаёт световую сигнализацию о наличии угля в дозаторе и подготавливает цепь загрузки скипа.
КДС состоит из двух датчиков дозировки скипов ДДС с воспринимающими элементами ( наклеенными на упругий стержень тензодатчиками ТПА, включенными по мостовой схеме ) и взрывобезопасного аппарата дозировки скипов типа АДС, включающего два линейных усилителя ЛУН, выполненных на базе преобразователя ПТ-ТП -68 с унифицированным выходом 0-5ма, двух релейных усилителей мощности РУМ и источника питания ИП.
Комплектная аппаратура для установок с асинхронными приводами развивается в направлении применения тиристорной силовой техники, высоконадёжных полупроводниковых устройств и герметизированных реле, а также разработки блочных конструкций, обеспечивающих высокую надёжность и удобство эксплуатации аппаратуры.
Пример такой разработки АГП-2 (вместо АГП61). В её основе следующие принципы:
реостатное управление разгоном двигателя в функции ускорения с корректировкой по фактическому току нагрузки;
замедление и дотягивание при питании двигателя от тиристорного преобразователя низкой частоты( например типа УКПЧ, Харьковского электромехзавода). Система автоматизации предусматривает возможность кнопочного управления для проведения ревизий каната и ствола.
Для проведения контроля износа канатов и регистрации результатов применяется аппаратура ИИСК-5.
7. Автоматизация проветривания горных выработок
7.1. Автоматизация вентиляторных установок
Вентиляция подземных выработок угольных шахт является важнейшим технологическим процессом и обеспечивается большим комплексом оборудования и мероприятий.
В составе комплекса подача и подогрев атмосферного воздуха в шахту , распределение требуемого количества воздуха по выработкам,
контроль качественного и количественного состава, процессы дегазации и т.п. Основное оборудование - вентиляторы главного проветривания (ВГП), калориферные установки, регуляторы подачи воздуха в выработки, шлюзы, вентляторы местого проветривания (ВМП), аппаратура контроля сблокированная с системой сигнализации и электроснабжения.
Только совместная, синхронизированная работа всех элементов перечисленного оборудования может обеспечить снабжение выработок достаточным количеством качественного воздуха и удалить отработанный воздух. Под качественным понимается воздух, содержащий по объёму не менее 20% кислорода, не более 0.5% углекислого газа и содержащий в отработанной струе добычного участка не более 1%.
Вентиляторы главного проветривания должны оборудоваться двумя одинаковыми вентиляторами, с включением резервного не более чем через 10 мин после отключения рабочего.
Различают центральную и фланговую схемы проветривания шахты.
Способы проветривания: всасывающий (наиболее распространённый),
нагнетательный и комбинированный.
Вентиляторы: центробежные (типов ВЦ, ВЦД, ВШЦ), осевые (ВОД).
Для реверсирования струи могут использоваться реверсивные и нереверсивные ВГП. Последние для осуществления реверса оборудуются специальной системой обводных вентиляционных каналов с перебрасываемыми лядами (переключающимися перегородками).
Электропривод ВГП должен:
-работать в длительном режиме с номинальной нагрузкой
- обеспечивать запуск и разгон вентилятора с большим динамическим моментом инерции до номинальной частоты вращения
- обладать возможностью реверса (при соответствующей схеме)
- иметь низкую синхронную скорость вращения при безредукторном подключеннии к вентилятору
- обеспечивать возможность регулирования подачи вентилятора в диапазоне 2:1.
В качестве электродвигателей мощностью более 200 квт применяют синхронные (до 350 квт низковольтные, свыше 350 квт высоковольтные).
При маломощных сетях или по другим причинам используют асинхронный вспомогательный двигатель для запуска СД. Асинхронный двигатель может служить для привода вентилятора в выходные и ремонтные дни или в начальный период эксплуатации шахты.
При нерегулируемом приводе регулирование режима работы вентилятора может осуществляться:
- изменением сопротивления вент сети ( дросселированием)
- изменением угла наклона лопаток направляющих аппаратов
- изменением угла установки лопаток рабочего колеса – для осевых вентиляторов.
Различают регулируемый привод ВГП со ступенчатым, а также с плавным изменением частоты вращения.
Ступенчатое регулирование может быть обеспечено: использованием двух двигателей разной частоты вращения или многоступенчатых двигателей,
или применением преобразователей частоты.
В первом случае могут использоваться два асинхронных двигателя или синхронный и асинхронный двигатели. В качестве многоступенчатых могут применяться двухскоростные АД с КЗ ротором при мощностях до 1400 кВт. Плавное регулирование подачи вентиляторов может быть обеспечено применением: асинхронного машинно - вентильного каскада (АМВК),
асинхронного вентильного каскада (АВК), асинхронного двигателя со статическим преобразователем частоты, комбинированного машинно-вентильного каскада (КАМВК). Последний применяется для ВЦД-47.5 “Север” и позволяет производить запуск АД без пусковых сопротивлений.
Комплексы автоматизации ВГП обеспечивают контроль и управление основным (электропривод) и вспомогательным оборудованием ВГП.
В разные годы и применительно к различному основному оборудованию ВГП разработана и применяется комплектная аппаратура автоматизации :
УКВГ, ЭРВГП, АДШВ, УКАВ, УКАВ-2. В настоящее время для этих целей выпускаются комплексы УАВШ, УКАВ-М. Последние являются унифицированными и могут в зависимости от требования заказчиков поставляться в модификации для различных типов вентиляторов, электроприводов, систем управления электроприводами, расстояний от диспетчерского пункта, способа реверсирования струи и т.п.
Так , УКАВ- М представляет собой набор шкафов закрытого исполнения и пульт дистанционного управления .
Процесс управления ВГП включает следующие операции:
- подготовка ВГП к пуску ( включение цепей высокого и низкого напряжения, выбор способа управления конкретным ВГП : авт., ручн., дист., местн.) и вспомогательным оборудованием (лядами : авт. или ручн.,
режим проветривания: норм. или реверсивный);
пуск (импульс пуска из помещения машинного зала либо из диспетчерской) в автоматическом режиме осуществляется по командам блока микропрограммного автомата БМА. Последний начинает отработку команд в соответствии программой, записанной в ПЗУ. В процессе работы БМА опрашивает состояние входов и формирует выходные сигналы управления электрическими аппаратами и приводами механизмов вентилятора. Между подачей команды и её выполнением задаётся выдержка времени. Если в течение её не поступит сигнал о выполнении команды, то пуск прекращается, все элементы ВГП приводятся в исходное состояние, включается сигнализация и автоматически производится АВР аварийное включение резервного вентилятора.
- регулирование подачи ВГП или автоматическая её стабилизация;
- аварийное или оперативное отключение ВГП.
К вспомогательному оборудованию относят приводы ляд и дверей для реверса воздушной струи ВГП. направляющих и спрямляющих аппаратов, приводы маслосистем и тормозной системы.
Положение ляд, дверей и тормозов контролируется магнитными включателями, датчиками ДПМГ, ДКПУ.
Для контроля нормальной работы ВГП предусмотрена система датчиков и приборов (КИП).
Температура подшипников контролируется аппаратами КТТ-1, АКТ, ДКТ3-8М. В станциях управления ШГС используют КТТ-1 с 8 термодатчиками ТД, аппаратом контроля температурыАКТТ-1 и сигнальным табло ТКТ-1.
Наиболее важными параметрами работы ВГП являются расход воздуха и подача (напор). Их измеряют, используя зависимость динамического давления воздуха в канале от скорости потока воздуха. Установив приёмники давления в различных по площади сечениях вентиляционного потока F1, F2 и измерив перепад давлений между этими приёмниками dH получим зависимость для определения подачи:
Очевидно, что для определения расхода Q необходимо из величины импульса dH извлечь корень, для этой цели используют различные инструментальные методы.
Для контроля подачи и давления в ВГП использовались дифманометры ДМ, ДМИ ( ДМИ-Р - расходомер, ДМИ-Т -например) со вторичными регистрирующими приборами ВФС. В настоящее время их заменяют на более надёжную и современную аппаратуру с тензометрическими преобразователями типа САПФИР, для контроля производительности вводится приставка извлечения корня Ореол-Пик. Для регистрации уровней давления и производительности может быть применен прибор технограф.
Для контроля давления масла в циркуляционной системе применяют, например, двухпозиционные электроконтактные манометры типа ЭКМ.
7.2. Автоматизация калориферных установок
Воздух, подаваемый в шахту в холодное время подогревается в калориферных установках. Оптимальная температура подогретого воздуха, при которой практически не происходит размораживания грунта устьев стволов (в северных широтах) и не происходит обмерзания стволов +2 ,+4 градуса. При этом устанавливается минимальное энергопотребление.
Регулирование температуры воздуха подаваемого в шахту производится изменением соотношения холодного и подогретого воздуха
перемещением перегородки (ляды) перед смесительной камерой, а также изменением количества теплоносителя (пара, перегретой воды) в калориферы. Система автоматики отслеживает также температуру конденсата на выходе каждой секции калорифера и, при недопустимом понижении отключает секцию, включая резервную.
Комплексы автоматизации калориферных установок АКУ-63. АКУ-3.
( более детально на лабораторной работе).
Основные функции АКУ-3 состоят в контроле температуры воздуха в стволе за счёт изменения положения поворотной ляды (контур 1) и поддержания на постоянном уровне температуры теплоносителя на выходе из калорифера путём изменения его расхода через калорифер (контур регулирования 2). Кроме того, во избежание обмерзания отдельных секций при нарушении герметичности секций, контролируется температура на выходе из секций и при понижении температуры конденсата на выходе секции должно производиться отключение повреждённой секции и включение резервной. Схема станции управления аппаратуры АКУ-3.
Станция управления СУРК-3 состоит из блоков:
-преобразователей сигналов датчика температуры воздуха
- преобразователей сигналов датчиков температуры отработанного теплоносителя
- контроля температуры секций;
- все сигналы о температуре (аналоговые сигналы с термосопротивлений) преобразуются в стандартные дискретные сигналы, где количество импульсов равно численному значению измеряемой температуры. Схемы блоков преобразователей включают линейный преобразователь температуры в постоянный ток, на его выходе сигнал постоянного тока ( 0- 5мА), АЦП, преобразователь цифровых кодов, реверсивный двоично-десятичный счётчик , мультивибратор, триггер, схемы совпадения (И- функции) и импульсный распределитель.
(более детально на лабораторной работе).
7.3. Аппаратура управления распределением воздуха (АУРВ)
АУРВ состоит и следующих блоков:
-блок управления участковым регулятором распределения воздуха участковым РРВ
-блока управления групповым РРВ
-блока питания
- блока управления подачей ВГП.
РРВ полидиафрагменный (РРВП) предназначается для оперативного регулирования расхода воздуха в вентиляционной сети шахт на основе информации, получаемой от датчиков информации, получаемой от датчиков [CH4], скорости воздуха с целью повышения эффективности проветривания и безопасности ведения горных работ.
В состав аппаратуры входят технические средства (ТС) контроля скорости воздуха в выработках и контроля состава атмосферы.
По заданным сечениям и длине выработок составляют системы моделирования проветривания шахт. В модели вводятся конкретные параметры, на ПЭВМ производится расчет требуемых параметров по скорости воздуха и по концентрации метана и других составляющих газовой атмосферы. На основании замеров фактических параметров с помощью соответствующих ТС вводят в систему корректирующие воздействия с помощью соответствующих регулятотров.
7.4. Аппаратура контроля шахтного воздуха
Для обеспечения безопасности труда подземных рабочих состав рудничного (шахтного воздуха ) должен контролироваться.
Основные требования:
-содержание кислорода не менее 20%
-углекислого газа на рабочих местах и в исходящих струях участков не более 0.5 %, а исходящим выработкам шахт 0.75%
-содержание метана, исчисляемое как средняя концентрация в поперечном сечении вент струи не должна быть более:
=1% на исходящей струе очистных и подготовительных выработок и участков;
=0.75% на исходящей струе крыла или шахты в целом;
=0.5% на свежей струе, поступающей в очистные выработки, к подготовительным забоям и в камеры;
=не более 2% в местных скоплениях в какой либо точке выработок.
Для точного, дискретного контроля состава воздуха применяют различные ТС: интерферометры,ШИ-6,( О2,СН4, СО2), ШИ-- 10(СН4 , СО2).
Для непрерывного индивидуального автоматического контроля [CH4]
непосредственно на рабочих местах применяют переносные метан- реле с автономным питанием.
Для контроля и автоматического отключения электропитания в выработках при достижении опасных концентраций в местах газовыделений из пласта при отбойке угля (в зоне работы шнеков добычного комбайна) разработано метан- реле типа ТМРК-3, отключающее подачу электроэнергии комбайна при достижении [CH4 более 2%].
К стационарным ТС относят аппаратуру, блокирующую подачу электроэнергии в выработку при достижении предельной для данной точки выработки концентрации, осуществляющей сигнализацию и передачу аналогового сигнала, пропорционального [CH4] на пульт диспетчера газовой службы с его регистрацией. В настоящее время это аппаратура
МЕТАН. (Более детально об аппаратуре МЕТАН - на лабораторной работе)
7.5. Автоматизация проветривания тупиковых выработок (АПТВ)
Для обеспечения непрерывного контроля за поступлением воздуха в тупиковые выработки, проветриваемые вентиляторами местного проветривания ВМП, в настоящее время применяется аппаратура АПТВ.
Основные функции:
-включение ВМП импульсами регулируемой длительности и количества, в зависимости от длины вентиляционного “рукава”
-немедленное включение резервного вентилятора при остановке рабочего
-задание уставки величины скорости воздуха пропорционального требуемому количеству воздуха для обеспечения выработки
-отключение электроэнергии в выработке при снижении скорости воздуха
ниже заданной (уставки) и другие.
(Детальное изучение АПТВ на лабораторной работе).
7.6. Автоматизация и контроль шахтных дегазационных систем
Необходимость дегазации, как средства поддержания допустимых концентраций метана в выработках, очевидна. При современных нагрузках на забой, высокой газообильности шахт обеспечение безопасных условий только за счёт способов и средств вентиляции невозможно.
Для систем дегазации характерно наличие трубопроводов ,по которым метан удаляется за пределы дегазируемого участка. В дегазационных трубопроводах для повышения безопасности эффективности в большинстве случаев создаётся разрежение с помощью вакуум-насосных установок (станций ВНС). ВНС, газопроводы, скважины, а также вся регулирующая, запорная и предохранительная аппаратура совместно со средствами контроля и управления образуют дегазационную систему шахты.
К средствам контроля и автоматизации ВНС предъявляются очень серьёзные требования по обеспечению безопасности, надёжности, систем блокировок и защиты.
В настоящее время наиболее известна автоматическая информационная система контроля параметров шахтных дегазационных установок, включающая и регуляторы ДИСК.
7.7. Автоматизированные системы управления проветриванием горных выработок (АСУПВ)
АСУПВ предназначена для автоматического оперативного управления газовой обстановкой в действующих выработках шахт с целью снятия ограничений на производительность выемочных участков и шахты по газовому фактору, экономии электроэнергии на проветривание и обеспечение высокого уровня безопасности горных работ.
В технической части система представляет собой совокупность ТС контроля концентрации метана и измерителей скорости воздуха(ИСВ-1), средств передачи информации в центр управления, средств обработки данных, выработки управляющих воздействий(УВК), исполнительных устройств(АУРВ, РРВП), аппаратура автоматизированного управления вентиляционными дверями (АШУ), управляемый привод ВГП.
Система позволяет:
=непрерывно контролировать концентрацию метана и скорость движения воздуха в выработках;
= осуществлять оперативную статистическую обработку контролируемых параметров с интервалом отбора данных в 1 мин;
=осуществлять оперативный расчёт требуемых приращений расходов в выработках;
=обеспечивать приращения расходов в выработках и по шахте в целом с интервалом 5-20 мин.
Применение системы позволяет автоматически снимать с помощью регулирования вентиляционного режима до 85-100%. загазирований технологического и аварийного характера при снижении расхода эл. энергии по шахте на 5- 7%.
8. Автоматизация процесса водоотлива
8.1. Водоотливная установка как объект автоматизации
Водоотливные установки горных предприятий, отрабатывающих обводненные месторождения, представляют сложный энергомеханический комплекс, включающий: насосные агрегаты различной производительности, трубные коллекторы, систему электроснабжения и аппаратуру автоматизации.
Основная задача автоматизации этих объектов заключается в высвобождении обслуживающего персонала и обеспечении надежного и экономичного функционирования процесса водоотлива, чтобы исключить затопление горных выработок и создать нормальные условия для ведения горных работ.
Для обеспечения заданного уровня безотказной работы водоотлива его проектируют с запасом по емкости водосборника и резервом насосных агрегатов. Кроме того, на главных водоотливных установках предусматривается резервирование электроснабжения и дублирование трубопровода для откачки воды на поверхность.
Водоотливные установки работают, как правило, в цикличном режиме. Их включение и отключение производят в функции уровня воды в водосборнике.
Аппаратура автоматизации водоотлива должна обеспечивать:
автоматическую контролируемую заливку насосов перед их пуском в работу;
автоматическое включение в работу очередного насоса при достижении водой верхнего уровня и непрерывную работу его до нижнего уровня;
автоматический контроль за работающим насосом и аварийное отключение его, если он не развил заданной производительности или в установке возник отказ (перегрев подшипников, короткое замыкание и др.);
автоматическое включение в работу резервного насоса, если отказал первый насос или он не справляется с притоком и вода достигла повышенного или аварийного уровня. Может предусматриваться одновременное включение нескольких насосов;
обезличенную звуковую и световую сигнализацию на пульт диспетчера о состоянии установки (работа, отказ) и аварийном уровне воды, а также сигнализацию в камере об отказавшем насосе;
возможность дистанционного включения установки с пульта диспетчера и перевод ее на ручное управление;
возможность применения различных способов заливки (погружной насос, баковый аккумулятор, сифонный способ и др.);
блокирование от включения отказавшего насоса без вмешательства обслуживающего персонала;
автоматическое управление работой задвижек на трубопроводах, а также работу с постоянно открытой задвижкой при небольших глубинах.
Учитывая многообразие типов водоотливов, разнообразие гидрогеологических, горнотехнических условий шахт и рудников, для автоматизации этого процесса используется различная серийная аппаратура, обеспечивающая с той или иной полнотой реализацию рассмотренных требований. В ряде случаев автоматизация водоотлива выполняется по индивидуальным проектам.
8.2. Автоматическое управление водоотливными установками
Для автоматического управления водоотливными установками применяется следующая аппаратура:
АВО-3 для установок, оборудованных одним насосом с короткозамкнутым асинхронным электродвигателем до 120 кВт;
АВН-1М (в настоящее время выпуск аппаратуры прекращён) для установок, оборудованных тремя насосами с низковольтными асинхронными короткозамкнутыми электродвигателями;
УАВ для установок, оборудованных насосами с высоковольтными и низковольтными асинхронными короткозамкнутыми электродвигателями.
Унифицированная аппаратура УАВ имеет нормальное исполнение и может укомплектовываться для автоматизации 16 насосов.
ВАВ для установок, .оборудованных насосами (до девяти) с высоковольтными и низковольтными асинхронными короткозамкнутыми электродвигателями. Аппаратура имеет взрывозащищенное исполнение и может использоваться в шахтах, опасных по газу или пыли.
К важнейшим операциям по управлению водоотливной установкой относится заливка насоса перед включением его в работу. В настоящее время наибольшее распространение получил способ заливки при поморий заливочного погружного насоса ЗПН, который находится в водосборнике ниже нижнего уровня и постоянно залит водой.
Другие способы заливки: подача воды из нагнетательного става, применение баковых аккумуляторов, сифонный способ, использование заглубленных насосных камер получили в угольной промышленности малое распространение. В горнорудной промышленности заглубленные насосные камеры применяют широко, так как они обеспечивают наиболее благоприятные условия работы насосов и существенно упрощают схему автоматизации.
![]() |
Рис. 8.1. Схема автоматической водоотливной установки:
I — электродные датчики уровня; 2 — аппарат управления; 3 — электропривод задвижки ЭПЗ-1; 4 — обратный клапан; 5 — реле давления РДВ; 6 — термодатчик ТДЛ; 7 — реле производительности РПН; 8 — логружной заливочиый насос ЗПН.
Гидравлическая схема автоматической водоотливной установки приведена на рис. 8.1. Обобщенный алгоритм управления такой установкой при постоянно открытой задвижке на нагнетательном трубопроводе и отключенном электроприводе задвижки дан на рис. 8.2. В соответствии с ним функционирование водоотлива осуществляется следующим образом.
После включения в работу аппаратуры (например, УАВ) и ее программного устройства (оператор А) контролируется уровень воды в водосборнике при помощи электродных датчиков (логическое условие р). Когда вода поднимется к датчику верхнего уровня, поступает команда на включение заливочного насоса ЗПН, который подает воду в насос в течение времени, предусмотренного программным блоком. Качество заливки контролируется реле давления РДВ (логическое условие k). Если в момент контроля уровня он достиг повышенного или аварийного уровня (p=0), программный блок сначала переключает схему на включение п насосов одновременно, а лишь затем включает заливочный насос.
Когда насос (или насосы) будет залит, подается команда на ввод его в работу (оператор Аз) с последующим контролем за производительностью при помощи флажкового реле производительности РПН (логическое условие г). Если насос развил заданную производительность (г=1), то схема переключается на контроль нижнего уровня, при достижении которого насос будет отключен. Если насос по какой-либо причине не развил заданной производительности, он отключается и подается сигнал диспетчеру (оператор Л4), а аппаратура начнет новый цикл по включению в работу очередного насоса. Приведенный алгоритм отражает только порядок выполнения основных функций по включению и отключению насосов. Наряду с ними аппаратура автоматизации обеспечивает выполнение различных контрольных и защитных функций, например, контроль температуры подшипников при помощи датчиков ТДЛ (см. рис. 8.1).
![]() |
Рис 8.2. Алгоритм управления автоматической водоотливной установкой при постоянно открытых задвижках.
8.3. Автоматическое регулирование режима работы водоотливных установок
Дальнейшее повышение эффективности работы водоотливных установок может быть достигнуто при создании систем, обеспечивающих регулирование производительности насосов по заданному алгоритму или перевод их на непрерывную откачку воды (работа на «приток»). При этом:
сокращается необходимая емкость водосборников на 30—50%;
сокращается на 35—75% мощность электродвигателей насосных агрегатов и появляется возможность применять меньшие по производительности насосы;
повышается безотказность работы водоотливной установки, гак как примерно 60% отказов возникают в момент пуска насосов;
уменьшаются затраты на водоотлив за счет интенсивной откачки воды в часы минимума энергопотребления, когда тариф за электроэнергию минимален.
Автоматическое регулирование производительности центробежных насосов может производиться путём изменения окружной скорости рабочего колеса и без её изменения.
Функциональная схема САУ водоотливной установкой при использовании регулируемого привода в целях стабилизации уровня воды в водосборнике показана на рис. 8.3.
![]() |
Рис. 8.3. Функциональная схема САУ стабилизацией уровня воды в водосборнике.
Объект регулирования в САУ водоотливной установкой — водосборник В, а его выходной параметр — уровень воды Н, который необходимо поддерживать постоянным путем изменения производительности Qн насоса Н. Возмущающее воздействие в этой системе — приток воды Qпр. Дифференциальное уравнение такого объекта:
,
где dH/dt – скорость изменения уровня воды в водосборнике, м/с;
Qпр – приток воды, м3/с; kВ = 1/F – передаточный коэффициент объекта ( F — площадь водосборника, м2); Qн — производительность насоса, м3/с.
Следовательно, объект представляет собой астатическое звено первого порядка, передаточная функция которого:
.
Насос характеризуется угловой скоростью рабочего колеса w на входе и производительностью Qн на выходе. Он может быть представлен апериодическим звеном первого порядка с передаточной функцией:
.
Угловая скорость рабочего колеса насоса меняется путем изменения частоты f напряжения, питающего электродвигатель насоса. Регулирование этой частоты в САУ осуществляется тиристорным преобразователем частоты ТПЧ, сигнал управления a на который подаётся от блока управления БУ. Измерение выходного параметра объекта Н производится датчиком уровня ДУ. Знак и уровень сигнала рассогласования DU между фактическим Uф и заданным Uз значениями уровней определяет характер выходного сигнала блока управления БУ. Сигналы Uз и Uф соответственно пропорциональны Нз и Нф. Для получения непрерывного сигнала Uф используются индуктивные и реостатные датчики с поплавковым чувствительным элементом, а также другие типы уровнемеров.
Данный способ регулирования производительности насосов наиболее эффективен по сравнению с другими.
В зависимости от постановки задачи при автоматическом регулировании производительности насосных агрегатов могут быть реализованы различные алгоритмы управления: поддержание постоянного уровня воды в водосборнике; изменение уровня воды по заданной программе; выравнивание нагрузки на шинах шахтной подстанции.
9. Автоматизация компрессорных установок
9.1. Регулирование производительности компрессорных установок
Основная задача регулирования режима работы компрессорных агрегатов и станций состоит в поддержании постоянного заданного давления сжатого воздуха в пневмосети путем изменения производительности компрессоров соответственно потреблению сжатого воздуха. В общем случае такое регулирование может быть осуществлено воздействием на коммуникации, компрессор или его привод. Ниже рассматриваются основные применяемые и перспективные способы регулирования производительности компрессоров.
Регулирование перепуском с нагнетания на всасывание, применяемое на поршневых компрессорах, заключается в переводе компрессора на холостой режим работы путем соединения нагнетательной полости каждого цилиндра с полостью всасывания посредством байпаса-трубопровода, снабженного вентилем (клапаном, задвижкой), управление которым может осуществляться вручную или автоматически. Этот способ по характеру регулирования ступенчатый; он обычно применяется при пуске и останове компрессора. Использовать его для регулирования производительности компрессора при работе нецелесообразно вследствие неэкономичности.
Регулирование дросселированием на всасывании предусматривает установку во всасывающем трубопроводе управляемого дросселирующего устройства (заслонки). Уменьшая проходное сечение дросселя, увеличивают его сопротивление и снижают давление воздуха, поступающего в первую ступень компрессора. При плавном изменении давления воздуха также плавно изменяется производительность компрессора. Такой способ регулирования производительности является основным для турбокомпрессоров (его применение на поршневых компрессорах ограничено повышением температуры сжатого воздуха до опасного для смазочных масел значения). Он прост в реализации, но неэкономичен.
Наиболее распространено для поршневых компрессоров регулирование отжимом всасывающих клапанов. Сущность этого способа заключается в следующем: всасывающие клапаны обеих ступеней удерживаются в открытом состоянии, поэтому сжатие в полости цилиндров прекращается и подача становится равной нулю. Полный отжим всасывающих клапанов для компрессоров двойного действия позволяет получить три ступени регулирования производительности: 100% —без отжима клапанов; 50% — при открытии всасывающих клапанов передней полости цилиндра низкого давления и задней полости цилиндра высокого давления; 0% — при открытии всех всасывающих клапанов обеих ступеней.
Более экономичен (по сравнению с отжимом всасывающих клапанов) способ регулирования производительности посредством подключения к цилиндру дополнительной емкости (мертвого пространства), применяемый на современных поршневых компрессорах. Сущность его состоит в том, что с увеличением объема мертвого пространства уменьшается объем свежего воздуха, засасываемого компрессором, так как воздух, ранее сжатый в мертвом пространстве, при всасывании расширяется и занимает часть полезного объема цилиндра.
Обычно регулирование производительности компрессора изменением мертвого пространства ступенчатое: к цилиндру компрессора с помощью управляемых клапанов подключают дополнительные объемы, представляющие собой отдельные полости, присоединенные к цилиндрам, или полости, расположенные непосредственно в корпусе цилиндров.
Наиболее эффективно и перспективно регулирование производительности компрессоров воздействием на их привод. Один из видов такого регулирования — периодические остановы компрессора, осуществляемые остановом двигателя или отсоединением компрессора от двигателя с помощью электромагнитных или гидравлических муфт. Регулирование производительности в обоих случаях ступенчатое. Регулирование остановом двигателя производится, как правило, на компрессорах с приводными двигателями мощностью до 300 кВт (производительностью до 50 м3/мин) и в сочетании с другими способами регулирования, например, со ступенчатым регулированием поршневых компрессоров подключением дополнительных мёртвых объёмов, а также при смешанном оборудовании компрессорной станции (турбо- и поршневые компрессоры). В последнем случае основное регулирование режима работы станции осуществляется плавным регулированием производительности турбокомпрессоров с последующим при необходимости отключением (включением) поршневых, а в некоторых случаях и турбокомпрессоров.
Плавное и экономичное регулирование производительности компрессора в широких пределах может быть обеспечено изменением частоты вращения с помощью регулируемого электропривода. При этом производительность изменяется пропорционально угловой скорости. Этот способ регулирования является перспективным для турбокомпрессоров. Для поршневых компрессоров производительностью до 50 м3/мин применение регулируемого электропривода пока не оправдано.
Автоматическое регулирование производительности компрессоров осуществляется в системах автоматической стабилизации давления сжатого воздуха. Такие системы могут быть дискретными и непрерывными и реализуются с помощью различных регуляторов общего назначения соответственно дискретного и непрерывного действия.
Если потребители сжатого воздуха при изменении нагрузки допускают отклонение давления от заданного значения в сравнительно больших пределах, то для регулирования режима работы компрессоров применяют простые двухпозицнонные (релейные) регуляторы давления, воздействующие на исполнительные органы для ступенчатого изменения их производительности. Когда по условиям технологического процесса требуется высокая точность поддержания давления при широком диапазоне расхода сжатого воздуха, используются более сложные регуляторы непрерывного действия, плавно изменяющие производительность компрессоров.
Дискретные системы регулирования применяются на поршневых компрессорах. Они, как правило, реализуются на основе электроконтактных манометров ЭКМ.-1У, воздействующих на электромагнитные клапаны, с помощью которых подсоединяются дополнительные мёртвые объёмы.
Системы непрерывного действия преимущественно применяются на турбокомпрессорах. Они строятся на основе гидравлических и электрических ПИ-регуляторов.
На рис. 9.1 представлена функциональная схема системы автоматического регулирования (системы стабилизации) давления сжатого воздуха в коллекторе, имеющая регулятор непрерывного действия. Объект регулирования — компрессор с воздухосборником Л'—В, регулируемая величина — давление р воздуха, которое должно поддерживаться постоянным с допустимой погрешностью. Сигналы ХЗ задатчика 3 и ХД датчика давления ДД, представляют собой перемещения или напряжения (в зависимости от типа регулятора), пропорциональные заданному рз и фактическому р давлению воздуха. Пропорционально-интегральный регулятор ПИ-Р воспринимает разность DХ=Хз – ХД и управляет положением m регулирующего органа (заслонки), компенсируя главное возмущающее воздействие — расход воздуха Qр путём установления производительности компрессора, равной существующему в данный момент расходу.
Компрессор с выходными емкостями как объект регулирования может быть представлен приближенно апериодическим звеном с передаточной функцией
,
где ko, Т o — передаточный коэффициент и постоянная времени объекта.
![]() |
ПИ-регулятор обеспечивает устойчивое астатическое регулирование производительности компрессора, поддерживая с высокой точностью давление на заданном уровне.
Рис.9.1. Функциональная схема системы автоматического регулирования давления
9.2. Автоматизация компрессорных агрегатов и станций
Современные рудничные компрессоры в качестве привода имеют синхронные двигатели, скорость которых не регулируется.
Автоматическая система компрессорного агрегата с нерегулируемым электроприводом может быть представлена схемой, показанной на рис. 9.2. Система содержит: датчики Д давления сжатого воздуха и теплотехнических параметров контроля агрегата (температуры, давления, расхода, уровня, положения задвижек, клапанов, заслонок и др.); электропривод компрессора ЭП (синхронный двигатель с возбудителем и пусковым устройством); исполнительный механизм ИМ, управляющий положением органа регулирования (клапанов, дроссельной заслонки) производительности Qк компрессора; вспомогательные технологические механизмы ВМ (разгрузочный клапан, маслонасосы, задвижка водяного охлаждения, вентили продувки); аппаратуру управления и регулирования АУР, осуществляющую автоматическое управление компрессорным агрегатом; пульт оператора (диспетчера) ПО с органами задания и контроля режимов работы агрегата.
Коллектор нагнетания сжатого воздуха
![]() |
Рис. 9.2. Функциональная схема автоматической системы компрессорного агрегата с нерегулируемым электроприводом.
Аппаратура автоматики, поставляемая комплектно с компрессором, обеспечивает:
автоматическое программное управление пуском и остановом компрессорного агрегата (включение и отключение в заданной последовательности вспомогательных механизмов и двигателя компрессора);
автоматический контроль режимов работы агрегата;
автоматическое регулирование производительности компрессора для поддержания заданного давления сжатого воздуха в коллекторе компрессорной станции;
автоматическую защиту электропривода компрессора (от асинхронного режима работы синхронного двигателя, короткого замыкания, перегрузки и др.), а также защиту, приводящую к отключению компрессора при верхнем пределе давления сжатого воздуха в ступенях сжатия, превышении температуры масла в системе смазки, прекращении потока охлаждающей воды и других нарушениях нормального режима работы агрегата;
сигнализацию на пульте оператора — световую о нормальной работе агрегата, световую и звуковую об аварийном отключении компрессорного агрегата.
Отклонение контролируемых параметров от заданных значений указывает на ненормальные или нерациональные режимы работы систем агрегата, а в ряде случаев может привести к аварии.
Критическим параметром безопасной работы компрессорного агрегата является температура воздуха. Перегрев воздуха особенно опасен для поршневых компрессоров, в которых смесь масла с воздухом при перегреве способна детонировать. Для контроля температуры применяют контактные термометры, термометры сопротивления, терморезисторы, манометрические термометры, термопары и др.
К числу важнейших параметров, характеризующих работу компрессора, относится производительность, контроль расхода воздуха и сравнение его с расходом электрической энергии позволяет оценить эффективность работы отдельных компрессоров и системы пневмоснабжения в целом. Расход воздуха Qр определяется обычно путем измерения перепада давления на дроссельном устройстве (сопло, диафрагма), установленном на трубопроводе, в соответствии с уравнением:
,
где k – расчетный коэффициент; Dр = р1 – р2 – перепад давления на дроссельном устройстве, измеряемый дифференциальным манометром.
Для контроля производительности компрессоров преимущественное распространение получили дифманометры и дифтягомеры ДМ, ДТ2 мембранные с дифференциальными трансформаторами, работающие с автоматическими вторичными приборами, например с приборами КСД-3.
В настоящее время наиболее перспективны для контроля расхода воздуха в пневмосети и компрессорной станции мембранные электрические дифманометры ДМЭ.
Для автоматизации шахтных компрессорных станций, оборудованных турбо- и поршневыми компрессорами, разработана унифицированная аппаратура автоматизации УКАС, основная задача которой — повысить эффективность работы автоматизированных компрессорных станций, производства и использования пневмоэнергии в результате:
применения регулируемого привода для управления режимом работы турбокомпрессоров изменением их угловой скорости;
автоматического регулирования (стабилизации) давления в коллекторе компрессорной станции;
расширения объема информации, передаваемой диспетчеру, и. обеспечения тем самым возможности работы компрессорной станции без постоянного присутствия обслуживающего персонала;
построения аппаратуры по блочно-модульному принципу с использованием герконовых реле и бесконтактных элементов, а в перспективе интегральных микросхем.
В состав аппаратуры УКАС входят:
щит управления турбокомпрессорным агрегатом УКАС-А (один на агрегат);
щит управления поршневым компрессорным агрегатом УКАС-ПА (один на агрегат);
пульт оператора (один на агрегат);
щит управления компрессорной станцией УКАС-С (один на станцию из восьми агрегатов);
тиристорное ТЕ-8 или бесщёточное БВУ возбудительное устройство (одно на агрегат);
первичные приборы теплотехнического контроля, устанавливаемые на компрессорном агрегате.
Регулирование режима работы компрессорной станции (обеспечение равенства производства и расхода сжатого воздуха) с целью поддержания заданного давления при параллельной работе нескольких компрессоров достигается как автоматическим поочередным регулированием производительности отдельных компрессоров, так и изменением числа одновременно работающих компрессоров (включением и отключением приводов).
Функциональная схема системы автоматического управления компрессорной станцией приведена на рис. 9.3. Блок БКА определяет последовательность автоматического включения, регулирования и останова агрегатов станции в соответствии с выбранными на пульте оператора номерами головного (включаемого первым), рабочих и резервных агрегатов.
Блок РД состоит из двух регуляторов давления РПИБ — рабочего и резервного, включаемого при неисправности работающего. Регулятор давления обеспечивает регулирование режима работы всех компрессоров станции для поддержания заданного давления сжатого воздуха в ее коллекторе. При отклонении давления воздуха р в пневмосети от заданного значения рз выше допустимого по сигналу регулятора РД блок ЗРП задает АУР программу индивидуального управления очередным компрессорным агрегатом. Аппаратура АУР обеспечивает управление, технологические защиты и регулирование производительности агрегата.
![]() |
Рис. 9.3. САУ компрессорной станции на базе аппаратуры УКАС:
БКА — блок задания команд и адресов программы; ЗРП — задатчик-распределитель программы работы станции; КА1—КА8—компрессорные агрегаты; АУР1—АУР8 — аппаратура управления и регулирования агрегатов; Д1—Д8 — датчики теплотехнических параметров агрегатов;
Д — датчик давления сжатого воздуха в пневмосети; РД — регулятор давления; КС — коллектор станции.
10. Автоматизированные системы управления технологическими процессами на горных предприятиях
10.1. Принцип функционирования АСУ
Под автоматизацией управления понимается замена физического и умственного труда человека, затрачиваемого на управление работой технических средств.
Автоматизация управления предприятием может осуществляться двумя методами. Первый метод заключается в разделении всей совокупности проблем управления предприятием на обособленные задачи, которые изучаются и решаются отдельно, не будучи связанными со смежными задачами. Решения, найденные для других задач, при этом во внимание не принимаются.
Задачи могут решаться в определенной логической последовательности или параллельно, в зависимости от существующих ограничений экономического, технического или организационного характера. Достоинства метода заключаются прежде всего в том, что автоматизация управления по отдельным задачам не вызывает необходимости глубокого изменения структур в системе управления. Задачи управления зачастую и выбираются так, чтобы их автоматизация не затрагивала общей структуры существующих подразделений предприятия.
Метод позволяет подразделить совокупность процедур управления предприятием на такое число задач, которое ограничивается только условием достижения наилучшего результата. Поэтому выделяются и решаются в первую очередь те задачи и в таком объеме, чтобы их решение было связано с получением прямых положительных результатов.
Такие ограничения в количестве и объеме автоматизируемых задач управления неизбежно повышают эффективность автоматизации. Преимущества метода проявляются и в самой организации решения задач автоматизации управления. Каждая задача решается одним коллективом разработчиков, который специализирован на задачах (или на одной задаче) такого типа. Отпадает необходимость работ по увязке многочисленных задач управления в единую систему. Существуют возможности оценки затрат на разрабатываемую задачу, в частности, затрат машинного времени, что позволяет точно определять расходы на ее решение.
С помощью этого метода разработчики могут тесно сотрудничать с теми подразделениями предприятия, которые наиболее заинтересованы в автоматизации решения конкретных задач, что повышает качество и эффективность разработки.
Основной недостаток метод – трудность сопряжения разработанных в отдельности задач, обеспечения взаимного обмена и координации при их эксплуатации. Большие трудности связаны с расширением задач, функционирующих изолированно друг от друга. Приходится существенно перерабатывать информационное и математическое обеспечение. В большинстве случаев речь идет практически о новом решении уже рассчитанной задачи.
Недостаток метода проявляется также в слабом влиянии на совершенствование структуры управления предприятием. Автоматизация управления предприятием обычно создает благоприятные возможности для модернизации самой структуры управления и сопровождается ее существенной перестройкой. Эти возможности в данном случае практически не реализуются.
Решение отдельных задач управления предприятием связано с использованием в разных задачах одной и той же информации в различных сочетаниях исходных показателей. Это приводит к появлению избыточных массивов данных, равно как и процедур их обработки.
Из приведенной характеристики метода можно сделать вывод, что его использование не позволяет обеспечить системное решение проблемы автоматизации управления предприятием как единым технологическим, организационным и экономическим механизмом и это является главным недостатком метода.
Второй метод – системный – заключается в автоматизации системы управления предприятием, т. е. управления по принципу системного подхода. Потоки данных всех видов, используемых в управлении, образуют сложную информационную систему. Для автоматизации ее функционирования необходимо:
а) дать описание информационной системы предприятия (отрасли);
б) разделить систему на информационные подсистемы;
в) разработать автоматизированные информационные подсистемы с учетом их взаимосвязей;
г) создать автоматизированную систему управления путем соединения отдельных информационных подсистем.
Здесь важна совместимость информационных подсистем, которая достигается путем создания некоторых общих массивов информации и обеспечения обмена информацией между различными подсистемами.
Автоматизация управления по системному методу обеспечивает интеграцию управления предприятием. Это всегда приводит к необходимости значительного изменения существующей структуры управления предприятием, так как применяются некоторые общие для всех подразделений массивы информации и однократная регистрация данных, используемых различными подразделениями.
К недостаткам метода относятся:
большая трудоемкость и длительность создания автоматизированной системы управления;
необходимость изменения сложившейся структуры управления предприятием даже в том случае, если существующая структура достаточно эффективна;
высокая стоимость автоматизированной системы управления и трудность точного определения экономического эффекта.
Таким образом, автоматизация управления по системному методу приводит к созданию автоматизированных систем управления.
Автоматизированная система управления – человеко-машинная система, обеспечивающая автоматизированный сбор и обработку информации, необходимой для организации управления в различных сферах человеческой деятельности.
В этом определении отражены две особенности, отличающие АСУ от САУ (системы автоматического управления). Первая заключается в том, что АСУ – человеко-машинная система. Здесь человек принимает основные решения, а ЭВМ отбирает и устраняет избыточную информацию, а также облегчает доведение принятых решений до исполнителя. Вторая особенность состоит в том, что в АСУ осуществляются автоматизированный сбор, обработка и хранение больших объемов информации. Поскольку информация и методы ее обработки в различных сферах деятельности человека характеризуются весьма широким спектром, в АСУ для обработки информации применяют универсальные ЭВМ, ориентированные на широкий класс задач и имеющие развитую систему команд, многоуровневую внешнюю память большого объема, систему разнообразных внешних устройств для ввода и отображения информации.
Важным отличием АСУ от САУ является время реакции на поступающие сообщения, которое может исчисляться часами, сутками и более продолжительными периодами, т. е. система работает в режиме времени, отстающем от реального.
В рамках САУ роль человека сводится к контролю процесса управления и корректировке автоматически вырабатываемых решений в сложных ситуациях.
Автоматизированные системы управления классифицируются по ряду признаков.
По уровню управления.
Общегосударственная автоматизированная система сбора и обработки информации (ОГАС) предназначена для сбора и обработки информации и решения задач управления на уровне общегосударственных органов.
Отраслевая автоматизированная система управления (ОАСУ) решает задачи управления на уровне отраслевых министерств и ведомств, а территориальная АСУ—на административно-территориальном уровне (республики, края, области, района, города) .
АСУ производственным объединением (АСУ ПО) служит для решения задач управления производственным объединением, а АСУ предприятия (АСУП)—для решения задач управления предприятием и объединением.
Перечисленные АСУ функционируют как автономно, так и в составе АСУ более высокого уровня.
По характеру объекта управления.
Автоматизированная система организационного управления (АСОУ) служит для управления всеми видами хозяйственной деятельности людей. Подобные системы называют также экономико-организационными АСУ, поскольку управление хозяйственной деятельностью осуществляется экономическими и организационными методами.
Различают автоматизированные системы, управления технологическими процессами (АСУТП) и интегрированные АСУ (ИАСУ), предназначенные для управления хозяйственной деятельностью и технологическими процессами.
По роли человека в процессе управления.
Информационные АСУ обеспечивают сбор, обработку, хранение и выдачу информации о различных аспектах хозяйственной деятельности.
Советующие АСУ наряду с выполнением функций информационных АСУ подготавливают возможные варианты решений задач управления и выдают справки по запросу.
Управляющие АСУ предназначены для оперативного управления производством и технологическими процессами, когда требуется высокая частота выдачи управляющих воздействий. В этих системах формируются управляющие воздействия и роль человека сводится к принятию наиболее важных решений, а также к контролю процесса управления.
По функциональному назначению выделяются автоматизированные системы, предназначенные для решения родственных, однородных функциональных задач управления. Таких систем достаточно много, наиболее типичные из них: АСУ планированием, АСУ материально-техническим снабжением, АСУ качеством продукции, АСУ финансовой деятельности, АСУ транспортом.
10.2. Общая характеристика ОГАС, ОАСУ, АСУП, АСУТП
Общегосударственная автоматизированная система сбора и обработки информации представляет собой информационно-вычислительную систему, увязывающую на единой методологической, информационной, организационной и технической основе отраслевые, ведомственные и республиканские АСУ для решения задач планирования и управления народным хозяйством. Она включает следующие функциональные системы:
автоматизированную систему плановых расчетов (АСПР);
автоматизированную систему государственной статистики(АС ГС);
автоматизированную систему финансовых расчетов (АСФР);
автоматизированную систему управления наукой и техникой (АСУНТ);
автоматизированную систему управления материально-техническим снабжением (АСУМТС);
автоматизированную систему труда и заработной платы (АСТЗ);
автоматизированную систему управления строительством (АСУС);
автоматизированную систему обработки информации по ценам (АСОИЦ);
автоматизированную информационно-управляющую систему стандартизации (АИУС);
отраслевые автоматизированные системы управления министерств и ведомств (ОАСУ).
Структура ОГАС отражает особенности отраслевого и территориального принципов управления, характерных для народного хозяйства страны.
Цель ОАСУ — организация управления предприятиями отрасли административными и экономико-математическими методами.
Отраслевая система управления осуществляет вычислительную и логическую обработку поступающей от предприятий информации и своевременно обеспечивает работников отраслевого аппарата управления информацией, необходимой для принятия решений по увеличению выпуска продукции и улучшению ее качества.
Функциональная структура ОАСУ отражает функциональную и организационную структуры системы управления отраслью. Общим для всех ОАСУ являются экономические принципы народного хозяйства: полный хозрасчет, использование нормативов длительного действия, совершенствование планирования и управления, наилучшее использование ресурсов, экономическая эффективность производства.
Первичным звеном ОАСУ является АСУП — комплексная система управления производственно-хозяйственной деятельностью предприятия и объединения экономико-математическими методами с использованием ЭВМ. На ее основе реализуется системный подход к управлению предприятием (объединением), достигается высокий уровень интеграции основных видов его деятельности и, как следствие, повышаются технический и организационный уровни производства.
Основные задачи АСУП сводятся к сбору, обработке и анализу информации о деятельности предприятия (объединения). Обработанная информация в необходимом объеме представляется потребителям, т. е. руководству предприятия (директору, заместителям директора), руководителям централизованных подразделений (начальникам отделов), руководителям линейных подразделений (начальникам участков, цехов, служб).
В составе АСУП различают организационный, функциональный, эксплуатационный персоналы, ЭВМ и производственную систему.
10.3. Принципы создания и функционирования АСУ
Автоматизация управления — это качественно новый уровень решения всех задач управления, переход к которому возможен и эффективен при соблюдении ряда принципов, определившихся практикой создания и эксплуатации АСУ.
Принцип комплексного (системного) подхода заключается в том, что любая АСУ, представляющая собой совокупность большого числа взаимодействующих элементов, должна рассматриваться с позиций системного анализа как самого объекта, так и системы управления им.
Системный подход, как правило, предполагает изменения, причем существенные, в организационной структуре органов управления, формах документов, видах контроля и ответственности на различных уровнях выработки и принятия решений.
Системность подхода к созданию АСУ проявляется в выделении функциональных и обеспечивающих подсистем, каждая из которых, в свою очередь, является сложной системой.
Весьма важная составная часть системного подхода—организация единой информационной подсистемы, которая создается во взаимосвязи с другими подсистемами и должна быть с ними совместима. Это означает, что создаются некоторые общие информационные массивы, используемые всеми подсистемами. Обновление общих массивов осуществляется только частью подсистем, а не всеми. Наконец, должен быть обеспечен обмен данными между подсистемами посредством использования некоторых связных массивов.
Системный подход проявляется также в формировании технических средств АСУ. Здесь основные положения сводятся к соответствию структуры технических средств структуре и условиям функционирования управляемого объекта, совместимости технических средств с учетом развития системы и расширения её возможностей, к высокому уровню надежности функционирования АСУ, проявляющемуся, в частности, в том, что существенное снижение надежности отдельных составных элементов технических средств не приводит к заметному изменению надежности функционирования всей системы.
При создании математического и программного обеспечения АСУ системный подход означает, что предполагается возможность применения программ во взаимодействии с другими программами в различных системах алгоритмов. При этом используется иерархическая структура с несколькими уровнями группирования и подчиненности программ.
Системный метод заключается также в типизации систем и подсистем управления в целях использования типовых или базовых решений при создании новых АСУ. Для систем управления предприятиями уровень типовых задач достигает 50%, а использование типовых решений позволяет сократить затраты и сроки на создание АСУ.
Принцип новых задач заключается в том, что АСУ создаются для решения не столько существовавших ранее, сколько новых задач как по содержанию, так и по методам их решения. Такие задачи не могут быть решены без использования вычислительной техники. В основном они включают задачи оптимизации (планирования, использования ресурсов, принятия решений и др.), массового обслуживания, имитационные задачи, задачи поиска и проектирования. Принцип новых задач не исключает решений в достаточно большом объеме тех задач, которые решались и ранее в управлении производством, например, задач бухгалтерского и финансового учета, материально-технического снабжения, контроля. Однако наибольшая эффективность АСУ достигается именно в применении новых методов решений задач более высокого класса. Весьма часто использование таких решений фактически сводит к новым традиционные задачи управления производством.
Принцип первого руководителя определяется как условие обязательного участия руководителя и всего аппарата управления предприятием в создании АСУ. Практикой управления предприятиями, организациями, коллективами людей выработано множество приемов и методов принятия решений. Опыт руководителей представляет собой не просто набор интуитивных удачных решений, но результат весьма глубокого анализа функционирования предприятия часто при ограниченном информационном материале. Методы принятия решений опытным руководителем невозможно просто заменить системой автоматизированной обработки и анализа большого объема информации и формальным нахождением наилучшего решения, поскольку само определение конечной цели и эффективности функционирования всех звеньев системы предприятия является часто творческой задачей, не поддающейся строгой формализации. Участие руководителя в разработке АСУ предопределяет возможности правильного сочетания выработанных практикой методов анализа ситуаций и принятия решений с современными экономико-математическими методами, реализуемыми с помощью ЭВМ. Назначение АСУ, таким образом, заключается не в замене творческого опыта и потенциала руководителя, а в существенном расширении его возможностей анализировать большее количество информации и вариантов возможных решений.
Рациональное распределение функций между человеком и ЭВМ, между уровнями и узлами системы приводит к построению рациональной структуры системы. При этом функции управления и соответствующие информационные потоки распределяются таким образом, что на низших уровнях управления решается наибольшее число задач локального характера, а на более высоких уровнях—задачи, имеющие общий, стратегический характер. Такое распределение функций упрощает проблемы обеспечения «живучести» системы, замены отдельных устройств другими того же или более высокого уровня.
В соответствии с принципом непрерывного развития системы, эволюции АСУ планируется заранее, в процессе разработки при определении очередности ввода в действие функциональных подсистем. Развитие АСУ заключается в постепенном добавлении новых функций в соответствии с намеченным планом. При разработке и вводе в эксплуатацию первых очередей системы следует тщательно продумывать их сопряжение с задачами последующих очередей.
Если под общей целью управления понимать достижение оптимального значения критерия экономической эффективности функционирования предприятия, объединения, отрасли, то очевидно, что достижение такой сложной по совокупности решаемых задач цели возможно путем разложения задач управления на задачи меньшей размерности и децентрализованного решения каждой задачи.
Такое разделение АСУ на менее сложные части называется декомпозицией системы управления, которая сама по себе представляет сложную задачу.
Основной проблемой декомпозиции системы управления является принцип разделения. Система делится на подсистемы, под которыми понимают совокупность элементов, объединенных процессом функционирования для достижения цели, поставленной перед системой в целом.
10.4. Технологические процессы горного производства как объекты управления
Важнейшей особенностью горного производства является его естественная, природная база. Разработка месторождений полезных ископаемых, их добыча всегда требовали использования совокупности многих технических приемов, которые прошли многовековой путь развития от горного искусства до современной технологии горного производства.
Природная, база каждого месторождения характеризуется совокупностью признаков, называемых горно-геологическими условиями. Эти условия определяют специфику горной технологии и, поскольку они изменяются в очень широком диапазоне, существует большое многообразие типов горнотехнологических процессов.
Таким образом, при разработке месторождения имеют дело с вероятностным характером горно-геологических факторов, и это обстоятельство определяет вероятностный характер протекания всего производственного процесса добычи полезного ископаемого, включая горнотехнологические процессы.
Другая существенная особенность горнотехнологических процессов — пространственный характер горных работ, обусловленный тем, что в рамках одного предприятия экономически целесообразно вести горные работы на нескольких пластах, рудных жилах, горизонтах, крыльях шахтного поля. Пространственность горных работ связана с необходимостью своевременной подготовки очистных забоев и одновременным ведением очистных, подготовительных и горно-капитальных работ.
Горные работы ведутся в пространстве, имеющем сотни метров по вертикали и километры в горизонтальной плоскости. В этом пространстве функционируют сотни выработок различного назначения, общая протяженность которых составляет десятки и сотни километров. На этом пространстве действуют разные технические и технологические системы и объекты.
Основные производственные зоны на подземных предприятиях — очистные и подготовительные забои, рассредоточенные в пространстве и соединяющиеся между собой и с поверхностью системой подземных горных выработок, представляющей собой уникальную инженерную систему, в которой осуществляется интенсивный производственный процесс добычи полезного ископаемого.
Важным отличительным фактором технологических процессов является непрерывность перемещения горных работ, определяющая в каждый момент времени неповторяющееся состояние производственной ситуации. Необходимость перемещения очистных и подготовительных забоев, вывода из эксплуатации старых и введения новых выработок предопределяет высокий уровень динамики производства во времени, повышает вероятностный характер многочисленных производственных параметров вследствие изменения не только геологических, но и технологических факторов.
Динамика технологических процессов обусловливает наличие переменного фронта работ. Основные технологические процессы развиваются в очистных и подготовительных забоях, перемещающихся в пространстве со скоростями, как правило, до нескольких метров в сутки. Перемещение фронта работ зачастую означает существенное изменение условий горных работ, а также требует наращивания основных и вспомогательных магистралей (энергетических, транспортных, воздушных, связи и т. п.), перемонтажа оборудования. Это нарушает технологическую непрерывность процессов и вносит постоянные помехи в функционирование отдельных систем.
Необходимость ведения горных работ при минимальных объемах выработок является серьезным ограничением для функционирования горной техники и обеспечения требуемых условий безопасности. Это ограничение лишь частично снимается при проведении выработок по крепким рудам, когда обеспечиваются условия для эксплуатации крупногабаритной мощной горной техники. В большинстве же случаев сжатие рабочего пространства снижает манёвренность горных работ, ограничивает эффективность и надёжность технологических процессов.
Опасность горных условий оказывает существенное воздействие на характер и параметры горнотехнологических процессов, а также на организацию горных работ. Это влияние сказывается на большом количестве различных ограничений на приемы, методы, способы, технику и организацию ведения горных работ, которые в совокупности формируются в действующих Правилах безопасности.
Сложность горного производства — основная причина относительно меньшего уровня механизации и автоматизации горно-технологических процессов. В настоящее время нет полностью автоматизированных технологических процессов; автоматизированы отдельные технические системы и звенья, например, шахтный подъем, конвейерный транспорт, вентиляция подготовительной выработки.
Динамика технологического процесса определяется рядом временных признаков. С точки зрения последовательности различают параллельное, последовательное и смешанное выполнение технологических операций. По длительности основных операций они делятся на короткие и длинные, по длительности производственного цикла — на операции с коротким, средним и длинными циклами. Важной характеристикой технологического процесса является перемещение составляющих производственного процесса—предметов и средств труда. По этому признаку выделяются три варианта:
перемещение предметов труда, когда средства труда находятся в одном месте, а перемещается сам объект труда (например, детали и узлы при обработке и сборке);
перемещение средств труда, когда сам объект труда неподвижен, а перемещаются средства труда (например, подъемный кран относительно строящегося здания, угольный комбайн относительно пласта);
перемещение предметов труда и средств труда (например, электровозный транспорт полезного ископаемого).
Горнотехнологические процессы классифицируются по ряду признаков:
по характеру протекания в пространстве—общешахтные (общекарьерные), участковые, локальные;
по характеру протекания процесса во времени — непрерывные и смешанные;
по отношению к добываемому полезному ископаемому — основные, обеспечивающие, вспомогательные и обслуживающие.
Основные процессы непосредственно связаны с добычей, выдачей и обработкой ископаемого.
Обеспечивающие процессы сами по себе с Действиями над продуктом труда (углем, рудой) непосредственно не связаны, их назначение — обеспечивать функционирование основных процессов. К обеспечивающим относятся процессы поддержания выработок, закладки выработанного пространства, снабжения электроэнергией, сжатым воздухом и водой, процессы вентиляции, дегазации и пылеподавления.
Вспомогательные процессы выполняются на предприятии для изготовления инструмента, мелкого оборудования, ремонта выработок, машин, механизмов, зданий и сооружений.
Обслуживающие процессы направлены на осуществление контроля основных и обеспечивающих процессов, обслуживание административно-хозяйственного комплекса предприятия.
Общешахтные — это такие горнотехнологические процессы, которые выполняются одновременно во всех (или в основных) выработках.
Для общешахтных процессов характерны: наличие разветвленной сети, в которой они протекают, централизованного механизма снабжения (подстанция, главный вентилятор, компрессор) и соответственно возможности централизованного управления процессом, а также иерархическая структура процесса, возможность расчленения процесса по нескольким составным частям и уровням управления, высокий уровень механизации процесса, высокая надежность.
Этими обстоятельствами объясняется, почему именно общешахтные процессы являются основными объектами для создания АСУТП. Здесь имеются большие возможности автоматизации управления и достижения высокой эффективности функционирования АСУТП.
Список литературы
Основная:
1. Гаврилов П.Д., Гимельшейн Л.Я., Медведев А.Е. Автоматизация производственных процессов. Учебник для ВУЗов. М.: Недра, 1985, 215с.
2. Нурлыбаев М.А. Автоматизированные системы управления технологическими процессами на карьерах. Учебное пособие для ВУЗов. М.: Недра,1985, 197с.
3. Пучков Л.А., Федунец Н.И., Потресов Д.К. Автоматизированные системы управления в горнодобывающей промышленности. Учебник для ВУЗов. М.: Недра, 1987,285с.
Дополнительная:
4. Батицкий В.А., Куроедов В.И., Рыжков А.А. Автоматизация производственных процессов и АСУТП в горной промышленности. М.: Недра, 1991, 303с.
5. Ломакин М.С. Автоматическое управление технологическими процессами карьеров. Учебник для ВУЗов. М.: Недра, 1978, 280с.
Дата добавления: 2021-12-10; просмотров: 144; Мы поможем в написании вашей работы! |
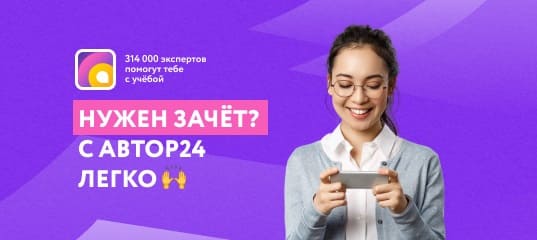
Мы поможем в написании ваших работ!