Для изготовления некоторых деталей самолета выбран сплав АЛ2. Указать состав сплава и способ приготовления из него деталей.
Министерство науки и высшего образования Российской Федерации
Федеральное государственное бюджетное образовательное
учреждение высшего образования
“Ивановский государственный энергетический университет
им. В.И. Ленина”
Кафедра технологии автоматизированного машиностроения
Контрольная работа
по курсу
“Материаловедение”
Вариант 13
Выполнил:
Иваново 2021
1. Вычертить диаграмму состояния системы «алюминий – медь». Указать линии ликвидуса и солидуса, а также структурно-фазовый состав областей диаграммы. Для сплава, содержащего 10% Cu , построить кривую охлаждения и описать происходящие при охлаждении превращения. Для заданного сплава определить количественное соотношение и состав фаз при температуре 600º С. Зарисовать и описать структуру сплава.
Рисунок 1 – Диаграмма состояния системы «алюминий – медь»
Фазовые превращения протекают в двух компонентной системе: “алюминий” (А) и “медь” (В), которые образуют друг с другом твердые растворы ограниченной растворимости α и β: α — твердый раствор компонента В в А; β — твердый раствор компонента А в В.
Максимальное число фаз — три (Ф = 3): жидкий раствор (Ж), α и β — твердые растворы.
Линии на диаграмме: АЕВ — ликвидус; ADECB — солидус; DF — предельной растворимости компонента В в A; CG — предельной растворимости компонента А в В; DEC — эвтектического превращения; точка С — эвтектическая точка.
|
|
Эвтектика представляет собой мелкозернистую механическую смесь кристаллов α - и β -твердых растворов.
Растворимость компонентов В в А переменная в зависимости от температуры. Чем ниже температура, тем меньше может раствориться компонента В в кристаллической решетке компонента А. Поэтому по мере охлаждения в сплавах, с концентрацией компонентов правее точки F, будут выделяться вторичные кристаллы β, которые обозначаются символом βII в отличие от первичных кристаллов β (βI), выделяющихся из жидкой фазы. Точка D показывает максимально предельную растворимость компонента В в А, а точка F — максимальную растворимость при комнатной температуре.
Растворимость компонента А в В постоянна и не зависит от температуры (линия CG — вертикальная), выделения вторичных α -кристаллов по мере охлаждения сплавов не происходит.
Кривая охлаждения представлена на рисунке 1. Выше точки 1 сплав находится в жидком состоянии. В точке 1 начинается процесс кристаллизации сплава образованием α-твердого раствора. В точке 2 процесс кристаллизации останавливается. Ниже точки 2 α-твердый раствор является пересыщенным и выделяются избыточные кристаллы βII -твердого раствора.
|
|
Для сплава, находящегося при температуре 600º С, жидкая фаза состоит из 60% Al и 40% Cu (проекция точки N на ось абсцисс), а твердая – из 92% Al и 8% Cu (проекция точки М на ось абсцисс).
Количество твердой Qт и жидкой Qж фаз сплава определяется следующим образом:
Таким образом, сплав состоит из 63% кристаллов твердого раствора и 37% жидкой фазы, имеющей состав точки N (60% Al и 40% Cu).
Рисунок 2 – Структура доэвтектического сплава системы Al-Cu
2. Вычертить диаграмму состояния « Fe – Fe 3 C ». Указать структурно-фазовый состав областей. Построить кривую охлаждения и описать происходящие при медленном охлаждении превращения для сплава, содержащего 1,6% С. Зарисовать и описать структуру сплава.
Первичная кристаллизация сплавов системы железо-углерод начинается по достижении температур, соответствующих линии ABCD (линии ликвидус), и заканчивается при температурах, образующих линию AHJECF (линию солидус).
При кристаллизации сплавов по линии АВ из жидкого раствора выделяются кристаллы твердого раствора углерода в α-железе (δ-раствор). Процесс кристаллизации сплавов с содержанием углерода до 0,1% заканчивается по линии АН с образованием α (δ)-твердого раствора. На линии HJB протекает перитектическое превращение, в результате которого образуется твердый раствор углерода в γ-железе, т. е. аустенит. Процесс первичной кристаллизации сталей заканчивается по линии AHJE.
|
|
При температурах, соответствующих линии ВС, из жидкого раствора кристаллизуется аустенит. В сплавах, содержащих от 4,3% до 6,67% углерода, при температурах, соответствующих линии CD, начинают выделяться кристаллы цементита первичного. Цементит, кристаллизующийся из жидкой фазы, называется первичным. B точке С при температуре 1147°С и концентрации углерода в жидком растворе 4,3 % образуется эвтектика, которая называется ледебуритом. Эвтектическое превращение с образованием ледебурита можно записать формулой ЖР4,3→Л[А2,14+Ц6,67]. Процесс первичной кристаллизации чугунов заканчивается по линии ECF образованием ледебурита.
Таким образом, структура чугунов ниже 1147°С будет: доэвтектических — аустенит + ледебурит, эвтектических — ледебурит и заэвтектических — цементит (первичный)+ледебурит.
Превращения, происходящие в твердом состоянии, называются вторичной кристаллизацией. Они связаны с переходом при охлаждении γ-железа в α-железо и распадом аустенита.
|
|
Линия GS соответствует температурам начала превращения аустенита в феррит. Ниже линии GS сплавы состоят из феррита и аустенита.
Линия ЕS показывает температуры начала выдел пня цементита из аустенита вследствие уменьшения растворимости углерода в аустените с понижением температуры. Цементит, выделяющийся из аустенита, называется вторичным цементитом.
В точке S при температуре 727°С и концентрации углерода в аустените 0,8 % образуется эвтектоидная смесь состоящая из феррита и цементита, которая называется перлитом. Перлит получается в результате одновременного выпадения из аустенита частиц феррита и цементита. Процесс превращения аустенита в перлит можно записать формулой А0,8→П[Ф0,03+Ц6,67].
Линия PQ показывает на уменьшение растворимости углерода в феррите при охлаждении и выделении цементита, который называется третичным цементитом.
Следовательно, сплавы, содержащие менее 0,008% углерода (точкаQ), являются однофазными и имеют структуру чистого феррита, а сплавы, содержащие углерод от 0,008 до 0,03% – структуру феррит + цементит третичный и называются техническим железом.
Доэвтектоидные стали при температуре ниже 727ºС имеют структуру феррит + перлит и заэвтектоидные – перлит + цементит вторичный в виде сетки по границам зерен.
В доэвтектических чугунах в интервале температур 1147–727ºС при охлаждении из аустенита выделяется цементит вторичный, вследствие уменьшения растворимости углерода(линия ES). По достижении температуры 727ºС (линия PSK) аустенит, обедненный углеродом до 0,8% (точка S), превращаясь в перлит. Таким образом, после окончательного охлаждения структура доэвтектических чугунов состоит из перлита, цементита вторичного и ледебурита превращенного (перлит + цементит).
Структура эвтектических чугунов при температурах ниже 727ºС состоит из ледебурита превращенного. Заэвтектический чугун при температурах ниже 727ºС состоит из ледебурита превращенного и цементита первичного.
![]() |
![]() |
Правило фаз устанавливает зависимость между числом степеней свободы, числом компонентов и числом фаз и выражается уравнением:
C = K + 1 – Ф,
где С – число степеней свободы системы;
К – число компонентов, образующих систему;
1 – число внешних факторов (внешним фактором считаем только температуру, так как давление за исключением очень высокого мало влияет на фазовое равновесие сплавов в твердом и жидком состояниях);
Ф – число фаз, находящихся в равновесии.
Сплав железа с углеродом, содержащий 1,6% С, называется заэвтектоидной сталью. Его структура при комнатной температуре цементит (вторичный) + перлит.
Рисунок 4 – Микроструктура заэвтектоидной стали (перлит + сетка цементита)
В системах топливоприготовления ТЭС для измельчения угля используют шаровые мельницы. Мелющие тела (шары) изготавливают из стали Г13Л. Указать состав и определить группу стали по назначению. Назначить и обосновать режим термической обработки.
Г13Л – высокомарганцовистая сталь для отливок легированная с особыми свойствами, содержащая около 1% углерода С и 13% марганца Mn.
Сталь Г13Л аустенитного класса для изготовления деталей, которые работают на износ в условиях скольжения, а так же трения, и высоких ударов и давлений: щеки дробилок, била, траки гусеничных машин, коронки трамвайных путей и землеройных машин. Сталь Г13Л в исходном состоянии после осуществления закалки приобретает так называемую аустенитную структуру, которая имеет твердость 250НВ , а так же обладает высокой вязкостью. Под воздействием различных динамических нагрузок и под воздействием холодной деформации сталь Г13Л становится прочнее до твердости 600НВ. В случае, если детали регулярно работают в условиях высоких давлений и нагрузок от удара, которые вызывают наклеп, то износостойкость и твердость эффективно возрастают, т.е сталь обладает такой уникальной характеристикой, как самоупрочнение.
Высокая износостойкость стали достигается не только деформационным упрочнением аустенита, но и образованием мартенсита с гексогональной (ε) или ромбоэдрической (ε´) решеткой. Структура литой стали представляет собой аустенит с выделившимися по границам зерен избыточными карбидами марганца (Mn3C), снижающими прочность и вязкость материала. Для получения однофазной аустенитной структуры отливки закаливают в воде при температуре 1050…1100º С. В таком состоянии сталь имеет высокую пластичность δ = 34…53%, ψ = 34…43%, низкую твердость 180…220 НВ и невысокую прочность σв = 654…830 МПа.
Рисунок 5 – График технологического режима термической обработки стали Г13Л
На изделиях из стали 15 требуется получить слой высокой твердости. Обосновать выбор метода химико-термической обработки, описать его технологию и структуру стали после окончательной термообработки.
Для получения необходимого комплекса эксплуатационных свойств (высокая износостойкость поверхности при достаточно высокой усталостно-изгибочной прочности) сталь 15 подвергают цементации, закалке и последующему низкому отпуску. Цементация повышает не только поверхностную твердость, но, как правило, и прочность детали. Цементацией стали называется процесс диффузионного насыщения поверхности стальных изделий углеродом при нагревании в науглероживающей среде. Назначение цементации и последующей термической обработки – придать поверхностному слою высокую твердость и износостойкость. Эти свойства достигаются обогащением поверхностного слоя стали углеродом доэвтектоидной, эвтектоидной или заэвтектоидной концентрации и последующей термической обработкой, сообщающей поверхностному слою стальных изделий структуру мартенсита или мартенсита с карбидами и небольшим количеством остаточного аустенита.
Термическая обработка заключается в газовой цементации при температуре 920 – 950º С. Структура слоя при температуре насыщения – аустенит, после медленного охлаждения в атмосфере агрегата перлит + цементит. Структура сердцевины при температуре насыщения – аустенит, после медленного охлаждения – феррит + перлит.
Для гарантированного получения мелкоигольчатого мартенсита детали после цементации охлаждают до температуры ниже температуры 600º С, а затем нагревают под закалку до температуры 800 – 820º С. Температуру нагрева под закалку выбирают для цементованного слоя. Температура AC3 для данной стали составляет 850º С. Закалку для стали 15 производят в воде.
Охлаждение в воде заготовок обеспечивает скорость охлаждения цементованного слоя выше критической. Структура поверхностного слоя после закалки – мартенсит, структура сердцевины зависит от размеров детали. Для небольших изделий получаем сквозную прокаливаемость. Структура мартенсит по всему сечению. С увеличением размеров изделия от поверхности к сердцевине получаем мартенсит → троостит → сорбит → перлит + феррит. Низкий отпуск проводим при температуре 180 – 200º С. Более высокие температуры применять не следует, так как это приводит к снижению твердости, статической и усталостной прочности, износостойкости цементовано-закаленных изделий. Охлаждение после отпуска на воздухе. Структура поверхностного слоя – отпущенный мартенсит. С увеличением размеров изделия от поверхности к сердцевине получаем отпущенный мартенсит → троостит → сорбит → перлит + феррит.
Твердость поверхности готового изделия 56 – 61 HRC.
Механические свойства стали:
σв = 38 кгс/мм2, σ0,2 = 23 кгс/мм2, δ = 27%, ψ = 55%.
Рисунок 6 – График технологического режима термической обработки стали 15
Для изготовления некоторых деталей самолета выбран сплав АЛ2. Указать состав сплава и способ приготовления из него деталей.
АЛ2 – алюминиевый литейный сплав, содержащий около 90% алюминия и 10% кремния.
Этот сплав, силумин, близок по составу к эвтектическому, поэтому отличается высокими литейными свойствами, а отливки – большой плотностью. Также сплав обладает высокой коррозионной стойкостью. Содержит в структуре эвтектику α + Si. Кремний при затвердевании эвтектики выделяется в виде грубых кристаллов игольчатой формы, которые играют роль внутренних надрезов в пластичном α-твердом растворе.
Сплав АЛ2 не подвергается упрочняющей термической обработке, сравнительно легко обрабатывается резанием. Заварку дефектов можно производить газовой и аргонодуговой сваркой.
Список литературы
1. Лахтин Ю.М., Леонтьева В.П. Материаловедение: Учебник для машиностроительных вузов – 2-е изд., перераб. и доп. – М.: Машиностроение. 1980. – 493 с., ил.
2. Гуляев А.П. Металловедение: Учебник для студентов высших технических вузов – 5-е изд., перераб. и доп. – М.: Металлургия. 1977 – 649 с., ил.
3. Арзамасов Б.Н., Сидорин И.И., Косолапов Г.Ф. и др. Материаловедение: Учебник для высших технических заведений. – 2-е изд., испр. и доп. – М.: Машиностроение, 1986. – 384 с., ил.
4. Мутылина И.Н. Технология конструкционных материалов: учеб. пособие / И.Н. Мутылина. – Владивосток: Изд-во ДВГТУ, 2007. – 167 с.
Дата добавления: 2021-11-30; просмотров: 53; Мы поможем в написании вашей работы! |
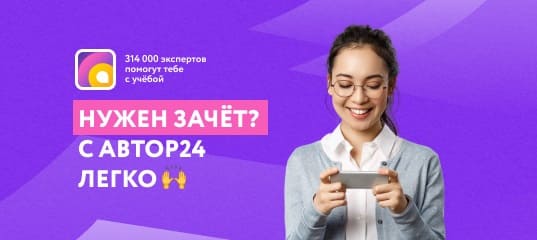
Мы поможем в написании ваших работ!